产品尺寸检验作业指导书.docx
《产品尺寸检验作业指导书.docx》由会员分享,可在线阅读,更多相关《产品尺寸检验作业指导书.docx(11页珍藏版)》请在冰豆网上搜索。
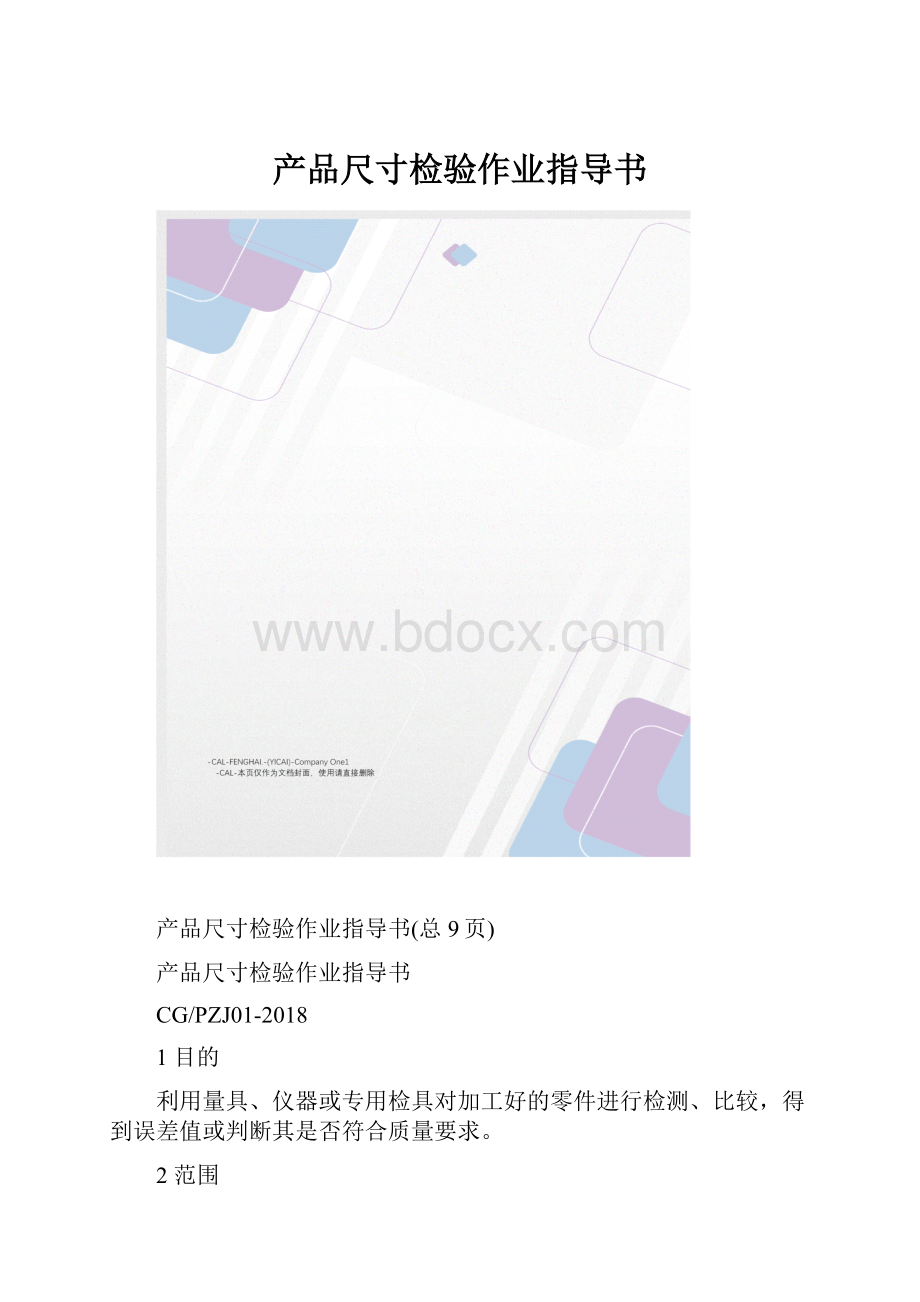
产品尺寸检验作业指导书
产品尺寸检验作业指导书(总9页)
产品尺寸检验作业指导书
CG/PZJ01-2018
1目的
利用量具、仪器或专用检具对加工好的零件进行检测、比较,得到误差值或判断其是否符合质量要求。
2范围
适用于对机械加工产品的几何量误差进行检测。
3依据
GB/T3177-2009产品几何技术规范(GPS)光滑工件尺寸的检验
GB/T10610-2009产品几何技术规范(GPS)表面结构轮廓法评定表面结构的规则和方法
GB/T1958-2004产品几何量技术规范(GPS)形状和位置公差检测规定
GB/T11336-2004直线度误差检测
GB/T11337-2004平面度误差检测
GB/T4380-2004圆度误差的评定两点、三点法
JB/T7557-1994同轴度误差检测
4职责
(1)检验人员负责选择方法并进行检测。
(2)技术负责人负责组织特殊情况下产品的方法选择。
5作业方法
5.1检验前的准备工作
检验人员依据《产品检验委托单》、技术文件和产品标准的要求确定检验项目,并选择适宜的检具和辅助工具,选择适合的检测方法,按照选择的方法进行检测,并做好记录。
使用的检具与辅助工具英语被测工件放置在同一环境条件下,并达到相同状态。
遇到特殊情况由技术负责人组织确认。
5.2尺寸误差检测(直径、长度、厚度等检测)
5.2.1轴径及其误差的常见检测方法
用卡尺、千分尺、专用量表等普通计量器具进行检测,测量的位置及点数应按标准、规范及图纸的要求进行。
5.2.2孔径及其误差的常见检测方法
用卡尺、内径千分尺、内径规、内径摇表、内测卡规等普通量具、通用量仪进行检测,测量的位置及点数应按标准、规范及图纸的要求进行。
。
5.2.3长度、厚度误差的检测
(1)长度尺寸一般用卡尺、千分尺、专用量表、测长仪、比测仪、高度仪、气动量仪等进行测量。
(2)厚度尺寸一般用塞尺、间隙片结合卡尺、千分尺、高度尺、量规等进行测量。
(3)壁厚尺寸使用超声波测厚仪、壁厚千分尺来测管类、薄壁件等的厚度。
(4)其它尺寸用偏心检查器检测偏心距值,用半径规检测圆弧角半径值,用螺距规检测螺距尺寸值。
用孔距卡尺测量孔距尺寸。
测量的位置及点数应按标准、规范及图纸的要求进行。
5.3表面粗糙度误差检测方法
5.3.1目视检查法
操作者根据加工纹理和加工表面特征,通过视觉经验,结合手感(用指甲轻划或手摸)或其他方法进行比较,对被测表面的粗糙度进行评定的方法。
目视检查的特征参见下表:
Ra(um)
表面特征
Ra(um)
表面特征
50~12.5
可见粗糙刀痕
0.05
光泽表面
6.3~1.6
可见刀痕
0.025
亮光泽表面
1.8~0.2
可见加工痕迹方向
0.012
雾状镜面
0.1
仔细辨认可见加工痕迹方向
0.005
镜面
5.3.2比较法
操作者将表面粗糙度比较样块与被测工件表面靠在一起,用目测或借助放大镜、比较显微镜等直接进行比较,或用手感(摸,指甲滑动的感觉)来判断表面粗糙度。
还可以用油滴在被测表面和表面粗糙度标准样块上,用油的流动速度(此时要求样块与工件倾斜角度与温度相同)来判断表面粗糙度。
流动速度快的表面粗糙度数值小。
5.3.3针描法
利用金刚石触针在被测表面滑行而测出表面粗糙度值的一种方法,使用的是粗糙度仪,可直接显示Ra值,测量范围Ra0.025~6.3um。
5.4角度误差检测方法
5.4.1角度测量的内容
包括矩形零件的直角、锥体的锥角、零部件的定位角、零件结构的分度角以及转角等。
5.4.2角度测量的方法
直角尺用于检验直角和划线。
光学分度头主要用来测量工件的圆周分度或对精密工件进行划线。
精度要求不高的常用样板、角尺、万能角度尺直接测量。
水平仪用来测量工件表面的水平位置及两平面或两轴线的平行度。
5.5形状误差检测方法
5.5.2形位误差检测原则依据GB/T1958-2004执行。
5.5.3直线度误差检测按照GB/T11336-2004进行。
光隙法是将平尺(或刀口尺)与被测要素直接接触,并对准光源,摆动工件或平尺,使最大间隙为最小。
用此方法应多测几次,取最大误差值作为被测件的直线度误差。
光隙法检验一般间隙为0.5um(0.5~3um为有色光,3um为白光)。
间隙偏大时可用塞尺配合测量。
钢丝法是用直径0.1~0.2mm钢丝拉紧,用V型铁上垂直安装读数显微镜检查直线度。
5.5.4平面度误差检测按照GB/T11337-2004执行。
5.5.5圆度误差检测按照GB/T4380-2004执行。
5.5.6圆柱度误差检测方法
(1)两点法。
将工件放在平板上并靠紧方箱,用千分表测若干个截面的最大与最小读数,取所有读数中最大与最小读数差之半为该工件的圆柱度误差。
(2)三点法。
将工件放在V形块内(V形块长度应大于被测工件长度),工件转动用千分表测出若干个截面的最大与最小读数。
取各截面所有读数中最大与最小读数之半为该工件圆柱度误差。
V形块夹角a,推荐使用a=90和a=120两种,见下图。
(3)指示器法(打表法)。
将零件顶在仪器的两个顶尖上轴线定位,在被测圆柱面的全长上,测量若干个截面轮廓,每个轮廓上可选取若干个等分点,得到整个圆柱面上各点的半径差值。
(见下图)
5.5.7线轮廓度误差的检测
采用样板光隙法。
用制作精确的检验样板检测工件,测量样板与工件的间隙来确定工件线轮廓度误差。
5.5.8面轮廓度误差检测方法
方法等同5.5.7,但最好将样板做成框架结构。
5.6位置误差检测的方法
5.6.1平行度误差检测方法
(1)指示器法
将工件基准面放在平板上,用千分表测被测表面,读出最大与最小数值之差即为平行度误差。
如下图,三种检测均应将所测得数据换算到工件实际长度上,即△=L1/L2|M1-M2|。
(2)水平仪法
将工件放到平板上,将基准面找平,分别测出基准面与被测面的直线度后,即获得平行度误差。
具体见下图。
5.6.2垂直度误差检测方法
(1)光隙法
使用直角尺或标准圆柱在平板(或直接放在工件的基准面)上,检查直角尺的另一面与工件被测面的间隙,用塞尺检查间隙的大小。
(2)坐标转换法
将工件基准面固定到直角座或方箱上,在平板上用测平行度的方法测垂直度误差。
(3)打表法
参照下图线对线垂直度测量。
基准轴线与被测轴线由心轴模拟,转动心轴轴线,在测量距离L2的两个位置上测得读数为M1何M2,出制度误差为△=L1/L2|M1-M2|。
5.6.3倾斜度误差检测方法
倾斜度误差检测中,一般将被测要素通过标准角度块、正弦尺、倾斜台等转换成与测量基准平行状态,然后在用测量平行度的方法测量倾斜度误差,参见下图。
5.6.4同轴度误差检测方法
(1)壁厚测量法
用量具直接测量壁厚均匀性,取厚度差最大值的1/2为同轴度误差。
该方法适用于板形、筒形工件内外圆同轴度测量。
(2)指示器法(心轴打表法)
将工件基准圆柱放在等高刃口形V型架上,转动工件,读出千分表指针指示的最大与最小读数差的1/2即为同轴度误差。
若基准指定为中心孔,则测量时应将中心孔在中心架上测量。
此方法适用于测量圆度误差较小的工件,见下图。
5.6.5跳动误差检测方法
跳动误差的测量只限于被测件上的回转表面和回转端面,如圆柱面、圆锥面、回转曲面、与回转轴心垂直的端面等。
它的测量项目有径向全跳动误差、径向圆跳动误差、斜向圆跳动误差、端面圆跳动误差等,见下图。
跳动误差的测量一般有三种方式:
径向圆跳动与径向跳动测量、端面圆跳动与端面全跳动测量、斜向圆跳动测量。
可采用顶尖、心轴、套筒、V形块等装置配合千分表进行测量。
5.6.7对称度测量方法
(1)打表直接检测法
将被测工件置于平板上,用百分表(或千分表)测量被测表面与平板之间的距离;将被测工件翻转,再测量另一被测表面与平板之间的距离。
取各剖面内测得的对应点最大差值作为对称度误差,见下图。
(2)打表间接检测法
将被测件置于两块平板之间。
以定位块模拟被检测中心面,再分别测出定位块与两平板之间的距离a1和a2,对称度误差为:
△=|a1-a2|max,见下图。
(3)综合检测法
将零件的基准圆柱面用心轴支撑在等高V形块上,并将被测基准表面调整与平板平行,测出读数;在同一剖面内,将被测件旋转180测量,百分表(或千分表)最大与最小读数之差则为该剖面对称度误差。
再选其他剖面进行测量,各剖面所得测值得最大极限尺寸者,即为该零件的对称度误差,见下图。
5.7测量要求
试验一般在10℃~35℃室温下进行,测量时工件与计量器具保持相同的温度,如偏离或有更高要求要记录。
选择计量器具时按照GB/T3177规定选取。
5.7.1尺寸误差检测
观察所要测试的工件,根据工件具体情况及标准、图纸等的要求选择检具、测量位置、测量点数,按照要求予以判定。
5.7.2表面粗糙度误差检测
(1)使用粗糙度测量仪测量时,每个判定区域测量3处,按照要求予以判定。
(2)使用粗糙度样块比对时,整体观测,选择判定区域,按照要求予以判定。
5.7.3角度误差检测
根据所检工件不同,选择不同的检测方法,依据工件的不同,选择评测区域检测,并按照要求予以判定。
5.7.4形状误差检测
根据所检工件不同,选择不同的检测方法,依据工件的不同,选择评测区域检测,并按照要求予以判定。
5.7.5位置误差检测
根据所检工件不同,选择不同的检测方法,依据工件的不同,选择评测区域检测,并按照要求予以判定。
5.8检验报告
检验报告至少应包括以下内容:
a)所选择的检验方法(必要时);
b)与工件有关的标准、图纸等详细资料;
c)所使用的主要计量器具;
d)特殊环境下的检测温度;
e)影响检验结果的各种因素。