典型盘套零件数控铣削加工工艺分析及程序设计.docx
《典型盘套零件数控铣削加工工艺分析及程序设计.docx》由会员分享,可在线阅读,更多相关《典型盘套零件数控铣削加工工艺分析及程序设计.docx(22页珍藏版)》请在冰豆网上搜索。
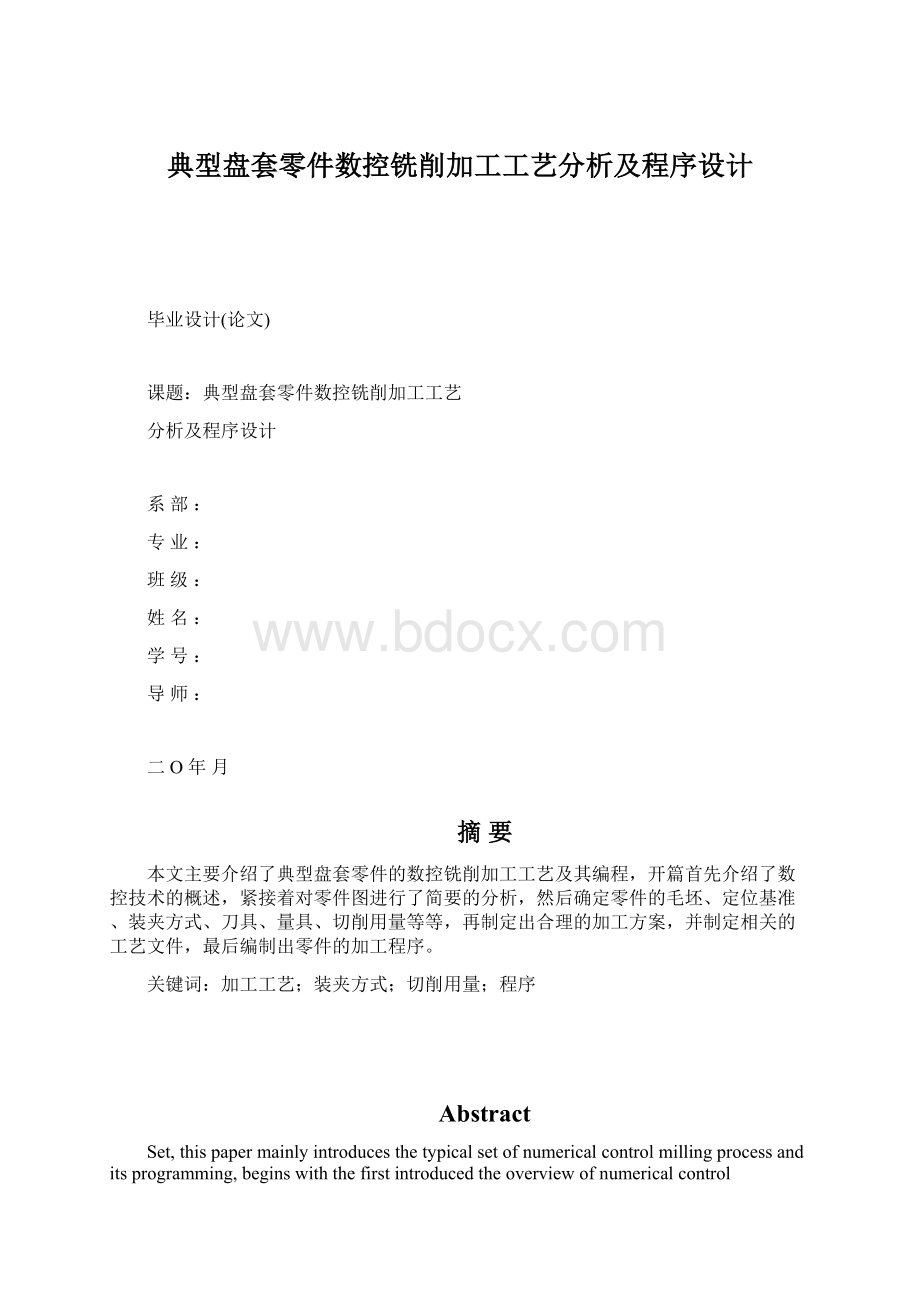
典型盘套零件数控铣削加工工艺分析及程序设计
毕业设计(论文)
课题:
典型盘套零件数控铣削加工工艺
分析及程序设计
系部:
专业:
班级:
姓名:
学号:
导师:
二O年月
摘要
本文主要介绍了典型盘套零件的数控铣削加工工艺及其编程,开篇首先介绍了数控技术的概述,紧接着对零件图进行了简要的分析,然后确定零件的毛坯、定位基准、装夹方式、刀具、量具、切削用量等等,再制定出合理的加工方案,并制定相关的工艺文件,最后编制出零件的加工程序。
关键词:
加工工艺;装夹方式;切削用量;程序
Abstract
Set,thispapermainlyintroducesthetypicalsetofnumericalcontrolmillingprocessanditsprogramming,beginswiththefirstintroducedtheoverviewofnumericalcontroltechnology,followedbyabriefanalysiswascarriedoutonthepartdrawing,andthendeterminetheblank,thelocatingdatumfortheparts,theclampingway,cuttingtools,measuringtool,cuttingdosage,etc.,todevelopreasonableprocessingscheme,andformulatetherelevantprocessdocuments,finallydevelopthepartsprocessingprogram.
Keywords:
process;Theclampingway;Cuttingparameter;Theprogram
第一章绪论
1.1数控机床的产生和发展
数控机床(NumericalControlMachineTools)是用数字代码形式的信息(程序指令),控制刀具按给定的工作程序、运动速度和轨迹进行自动加工的机床,简称数控机床。
数控机床是在机械制造技术和控制技术的基础上发展起来的,其过程大致如下:
随着电子技术的发展,1946年世界上第一台电子计算机问世,由此掀开了信息自动化的新篇章。
1948年,美国帕森斯公司接受美国空军委托,研制直升飞机螺旋桨叶片轮廓检验用样板的加工设备。
由于样板形状复杂多样,精度要求高,一般加工设备难以适应,于是提出采用数字脉冲控制机床的设想。
1949年,该公司与美国麻省理工学院(MIT)开始共同研究,并于1952年试制成功第一台三坐标数控铣床,当时的数控装置采用电子管元件。
1959年,数控装置采用了晶体管元件和印刷电路板,出现带自动换刀装置的数控机床,称为加工中心(MCMachiningCenter),使数控装置进入了第二代。
1965年,出现了第三代的集成电路数控装置,不仅体积小,功率消耗少,且可靠性提高,价格进一步下降,促进了数控机床品种和产量的发展。
60年代末,先后出现了由一台计算机直接控制多台机床的直接数控系统(简称DNC),又称群控系统;采用小型计算机控制的计算机数控系统(简称CNC),使数控装置进入了以小型计算机化为特征的第四代。
1974年,研制成功使用微处理器和半导体存贮器的微型计算机数控装置(简称MNC),这是第五代数控系统。
20世纪80年代初,随着计算机软、硬件技术的发展,出现了能进行人机对话式自动编制程序的数控装置;数控装置愈趋小型化,可以直接安装在机床上;数控机床的自动化程度进一步提高,具有自动监控刀具破损和自动检测工件等功能。
20世纪90年代后期,出现了PC+CNC智能数控系统,即以PC机为控制系统的硬件部分,在PC机上安装NC软件系统,此种方式系统维护方便,易于实现网络化制造。
我国1958年试制成功第一台电子管数控机床,从1965年开始研制晶体管数控系统,到20世纪70年代初曾研究出数控臂锥铣床、非圆插齿机、数控立铣床、数控车床、数控镗床、数控磨床和加工中心等。
20世纪80年代随着改革开放政策的实施,我国从国外引进了先进技术,并在消化、吸收国外先进技术的基础上,进行了大量的开发工作,进而推动了我国数控机床新的发展高潮,使我国数控机床在品种上、性能上以及水平上均有了新的飞跃。
1.2数控加工的特点
(1)自动化程度高,具有很高的生产效率。
除手工装夹毛坯外,其余全部加工过程都可由数控机床自动完成。
若配合自动装卸手段,则是无人控制工厂的基本组成环节。
数控加工减轻了操作者的劳动强度,改善了劳动条件;省去了划线、多次装夹定位、检测等工序及其辅助操作,有效地提高了生产效率。
(2)对加工对象的适应性强。
改变加工对象时,除了更换刀具和解决毛坯装夹方式外,只需重新编程即可,不需要作其他任何复杂的调整,从而缩短了生产准备周期。
(3)加工精度高,质量稳定。
加工尺寸精度在0.005~0.01mm之间,不受零件复杂程度的影响。
由于大部分操作都由机器自动完成,因而消除了人为误差,提高了批量零件尺寸的一致性,同时精密控制的机床上还采用了位置检测装置,更加提高了数控加工的精度。
1.3本课题的主要内容及任务
(1)主要内容
本文主要讲述了典型盘套零件的数控加工工艺中的问题,如毛坯的选择、定位基准的选择、装夹方式的选择、刀具及量具的选择、切削参数的选择等相关问题,在分析完这些问题后,制定出合理的加工方案,并制定相关工艺文件,编制出零件的数控加工程序。
(2)主要任务
1.分析加工工艺;
2.确定加工方案;
3.制订加工路线;
4.选择加工设备;
5.确定加工刀具;
6.编写加工程序;
8.编写设计说明书。
第二章零件的图样分析
2.1零件的结构特点分析
如图2.1所示零件图,从图中可以看出,该零件的结构为:
一方形板上有一规则凸台、凸台上有圆弧键槽、零件的四个角均布有4XM10的螺纹孔,这些结构形状涉及的内容坐标数值较多,在普通铣床上加工难以保证精度,而在数控铣床上加工这些结构属于易加工产品。
图2.1CAD零件图
2.2零件的技术要求分析
(1)工艺设计
1)对零件进行工艺分析
2)选择毛坯和机床
3)确定加工方案
4)选择刀具并填写工具单
5)确定零件装夹方式
6)确定粗、精铣加工切削用量
7)确定工序内容并填写工序卡
(2)编写加工程序
1)建立工件坐标系
2)基点尺寸计算与确定
3)编写加工程序
第三章零件的工艺规程设计
3.1毛坯的选择
该零件为板类零件,故其毛坯选择为板材,毛坯材料为45钢,毛坯尺寸为90mm×90mm×40mm。
3.2定位基准的选择
选择工件的定位基准,实际上是确定工件的定位基面。
根据选定的基面加工与否,又将定位基准分为粗基准和精基准。
在起始工序中,只能选择未经加工的毛坯表面作为定位基准,这种基准称为粗基准。
用加工过的表面作为定位基准,则称为精基准。
在选择定位基准时,是从保证工件精度要求出发的,因此分析定位基准选择的顺序应为从精基准到粗基准。
(1)精基准的选择原则
选择精基准时,应能保证加工精度和装夹可靠、方便,可按照基准重合、基准统一、自为基准、互为基准、便于装夹等原则进行选择。
根据其原则,确定该零件的精基准为零件的外轮廓及零件底面。
(2)粗基准的选择原则
选择粗基准要求应能保证加工面与不加工面之间的位置要求并合理分配加工面的余量,同时要为后续工序提供精基准,可按照非加工表面、加工余量最小、重要表面、不重复使用、便于工件装夹等原则进行选择。
根据其原则,确定该零件的粗基准为毛坯外边及底面,对零件的四周和上表面进行加工,再以加工的面做为精基准,加工剩余部位。
3.3装夹方式的选择
在机床上加工,为保证加工精度,必须先使工件在机床上占据一个正确位置,即定位;然后将其压紧压牢,使其在加工中保持这一正确位置不变,即夹紧。
从定位到夹紧的全过程称为工件的装夹。
经分析,该零件需要进行2道主要的加工工序方能完成零件的加工。
在第一工序装夹时为铣削零件的底面,和四周外轮廓,此次装夹时以毛坯外轮廓定位,采用平口虎钳进行装夹;第二工序装夹时加工零件的凸台、孔和螺纹,此次装夹以加工好的底面进行定位,直接用如下图3-1所示的机用平口虎钳装夹压紧已加工的外轮廓。
图3-1
3.4表面加工方法的选择
(1)上下两平面的加工方法
其表面粗糙度要求不高,故其加工方法可按照粗、精加工进行,在粗加工后留取0.5mm的余量进行精铣。
(2)侧面的加工方法
其侧面的尺寸精度和表面粗糙度要求均不高,可直接进行粗铣即可。
(3)凸台轮廓的加工方法
其表面粗糙度要求不高,尺寸精度Ra3.2um,且X、Y、Z向的加工余量较大,故其加工方法需按照粗、精加工进行,且粗加工时余量较多,需要进行分层铣削。
(5)凸台型腔键槽的加工方法
因为此型腔键槽的宽度较小,只能选用较小的刀具加工,考虑到刀具大小和长度,无形中增加难度,需要选择合理的进刀方式和切削三要素。
(6)螺纹孔及螺纹的加工方法
加工孔按照常规方法,螺纹孔直接钻即可,4XM10的螺纹则采用丝攻直接对其攻丝。
3.5加工顺序的安排
工序通常包括切削加工工序、热处理工序和辅助工序等,工序的安排与否将直接影响到零件的加工质量、生产率和加工成本。
切削加工工序通常按以下原则划分:
(1)以一次安装作为一道工序;
(2)以粗、精加工划分工序;
(3)以同一把刀具加工的内容划分工序;
(4)以加工部位划分工序。
在具有良好冷却系统的加工中心上,对于毛坯质量高、加工余量较小、加工精度要求不高或新产品试制等单件或生产批量很小的零件,可在加工中心上一次或两次装夹完成全部粗、精加工工序。
本次设计的电信盘套零件加工顺序的安排原则:
先粗后精、先面后孔、基面先行。
根据该以上原则,确定该零件的加工顺序为:
铣底面→铣四周外轮廓→翻面装夹→铣上表面→粗铣凸台→精铣凸台→粗铣凸型腔键槽→精铣凸台型腔键槽→钻中心孔→钻零件四周的4xФ8.7mm的螺纹孔,刀肩深20mm→攻丝4XM10
3.6工艺路线的确定
3.6.1可能采取的工艺路线方案
(1)工艺路线方案一
工序一:
制造毛坯90mm×90mm×40mm
工序二:
粗、精铣6个面至尺寸80mm×80mm×30mm
工序三:
工步1:
粗铣凸台轮廓,侧部留0.4mm的精加工余量
工步2:
精加工凸台轮廓
工步3:
粗铣凸台上圆弧键槽,底部和侧部留0.4mm的精加工余量
工步4:
精铣凸台上圆弧键槽
工步5:
钻螺纹孔4xФ8.7mm,刀肩深20mm
工步6:
攻丝4XM10,深12mm
工序四:
去毛刺
工序五:
检验
工序六:
入库
(2)工艺路线方案二
工序一:
制造毛坯90mm×90mm×40mm
工序二:
粗、精铣6个面至尺寸80mm×80mm×30mm
工序三:
工步1:
钻螺纹孔4xФ8.7mm,刀肩深26mm
工步2:
攻丝4XM10,深18mm
工步3:
粗铣凸台上圆弧键槽,底部和侧部留0.4mm的精加工余量
工步4:
精铣凸台上圆弧键槽
工步5:
粗铣凸台轮廓,底部和侧部留0.4mm的精加工余量
工步6:
精加工凸台轮廓
工序四:
去毛刺
工序五:
检验
工序六:
入库
3.6.2工艺路线方案比较
在数控加工中,刀具刀位点相对于工件运动的轨迹称为加工路线。
加工路线的确定原则:
(1)加工路线因保证被加工零件的精度和表面粗糙度,且效率高;
(2)使数值计算简单,减少编程工