高强度放电灯用陶瓷管.docx
《高强度放电灯用陶瓷管.docx》由会员分享,可在线阅读,更多相关《高强度放电灯用陶瓷管.docx(17页珍藏版)》请在冰豆网上搜索。
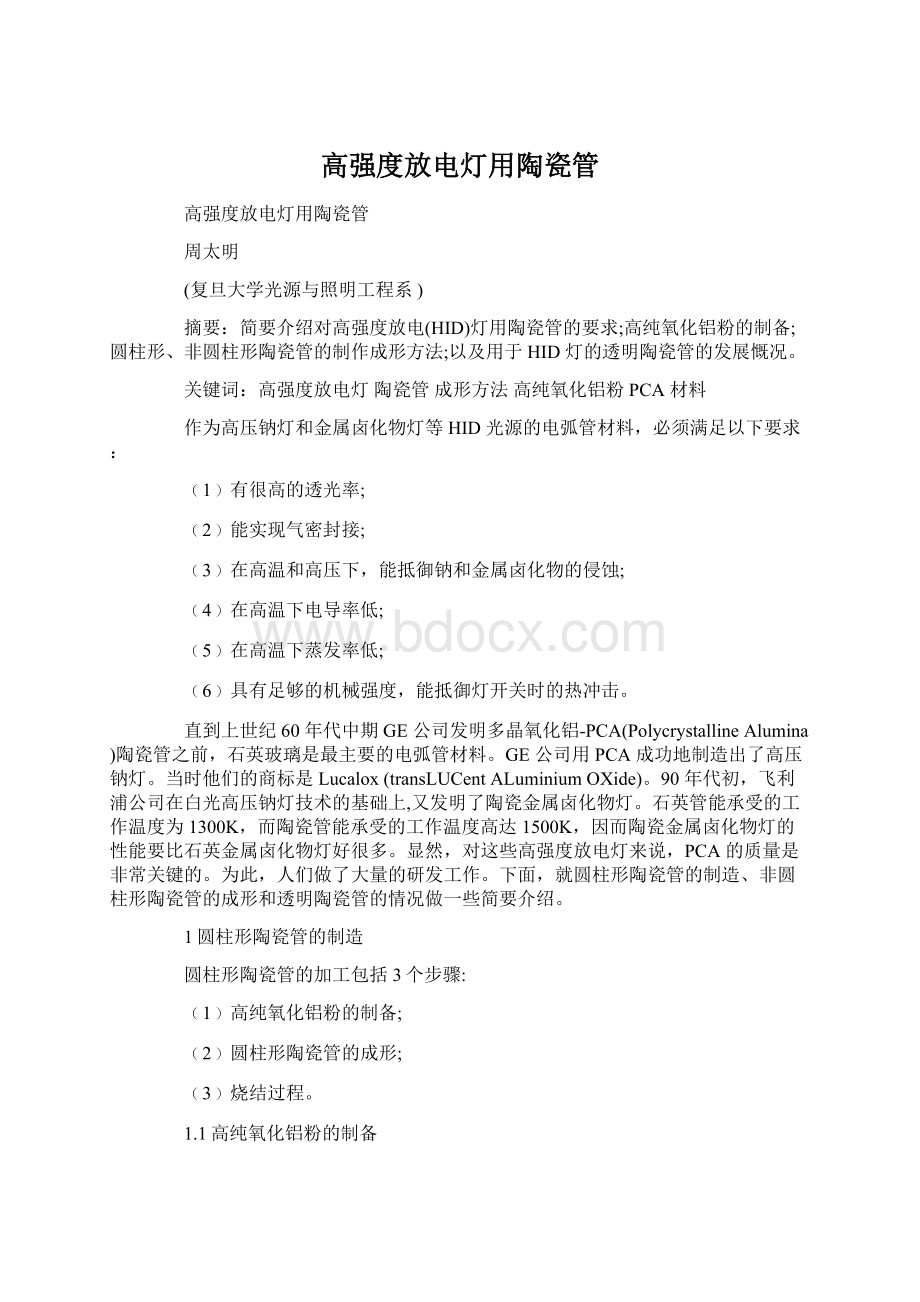
高强度放电灯用陶瓷管
高强度放电灯用陶瓷管
周太明
(复旦大学光源与照明工程系)
摘要:
简要介绍对高强度放电(HID)灯用陶瓷管的要求;高纯氧化铝粉的制备;圆柱形、非圆柱形陶瓷管的制作成形方法;以及用于HID灯的透明陶瓷管的发展慨况。
关键词:
高强度放电灯陶瓷管成形方法高纯氧化铝粉PCA材料
作为高压钠灯和金属卤化物灯等HID光源的电弧管材料,必须满足以下要求:
﹙1﹚有很高的透光率;
﹙2﹚能实现气密封接;
﹙3﹚在高温和高压下,能抵御钠和金属卤化物的侵蚀;
﹙4﹚在高温下电导率低;
﹙5﹚在高温下蒸发率低;
﹙6﹚具有足够的机械强度,能抵御灯开关时的热冲击。
直到上世纪60年代中期GE公司发明多晶氧化铝-PCA(PolycrystallineAlumina)陶瓷管之前,石英玻璃是最主要的电弧管材料。
GE公司用PCA成功地制造出了高压钠灯。
当时他们的商标是Lucalox(transLUCentALuminiumOXide)。
90年代初,飞利浦公司在白光高压钠灯技术的基础上,又发明了陶瓷金属卤化物灯。
石英管能承受的工作温度为1300K,而陶瓷管能承受的工作温度高达1500K,因而陶瓷金属卤化物灯的性能要比石英金属卤化物灯好很多。
显然,对这些高强度放电灯来说,PCA的质量是非常关键的。
为此,人们做了大量的研发工作。
下面,就圆柱形陶瓷管的制造、非圆柱形陶瓷管的成形和透明陶瓷管的情况做一些简要介绍。
1圆柱形陶瓷管的制造
圆柱形陶瓷管的加工包括3个步骤:
﹙1﹚高纯氧化铝粉的制备;
﹙2﹚圆柱形陶瓷管的成形;
﹙3﹚烧结过程。
1.1高纯氧化铝粉的制备
用于制作电弧管的氧化铝粉的原料纯度一定要高,要达到99.99%。
为什麽要这么高的纯度呢?
因为只要有杂质存在,即使其含量很少,也会造成一些不希望的影响。
比如,会引起粉变色;在烧结过程中,产生不规则的晶粒;晶界产生分离,从而使杂质容易移到晶界处,使那里的杂质浓度增加。
另外,为了得到高密度的管材,粉的烧结活性要好。
这就要求粉有特定的形态结构,具体说就是粒径要很细(约0.3μm),而且粒径分布很集中。
PCA的原料,即α-Al2O3是由灼烧含结晶水的硫酸铝氨(AlNH4(SO4)2.24H2O)而得:
AlNH4(SO4)2.24H2O→Al2O3+NH3+SOx
在1000摄氏度时,首先形成大块的Al2O3(比表面125m2/g,密度0.15g/cm3,粒径0.02μm),然后在1200~1400摄氏度下转变成α-Al2O3。
接下来,再将集团的粉分散,得到密度0.4g/cm3,平均粒径0.6μm,比表面6m2/g的α-Al2O3粉。
表1列出日本NGK公司所采用的高纯氧化铝粉原料的特性。
表1日本NGK公司所采用的高纯氧化铝粉原料的特性
1.2圆柱形陶瓷管的成形
生产圆柱形陶瓷管最常用的方法有等静压法(IsostaticPressing)和挤压成形法(Extrusion)。
将氧化铝粉、粘结剂、氧化镁等添加剂与蒸馏水充分混合,所得粉浆在专用的喷雾干燥设备中雾化、干燥成颗粒状的干粉。
然后如图1所示,将该粉末填充于空心圆柱形的橡皮模和实心的金属模之间,再从橡胶模的外部用高压液体径向施加等静压于模内的粉末,使其形成致密的圆柱形的陶瓷管坯。
图1等静压制作陶瓷管示意图
挤压成形法是将氧化铝粉末、粘结剂及添加剂与一种液态物质(或与其他附加的液态粘结剂)混合成面团状,然后被挤压穿过金属模具,形成不断伸长的空心或实心的陶瓷管或陶瓷棒。
其过程如图2所示。
这些长的管、棒可以根据要求被切割成所需的长度。
这种挤压成形的方法适宜连续大规模生产。
图2挤压成形法示意图
1.3烧结过程
成形后的陶瓷管坯料最后要进行烧结。
生产过程中通常采用二次烧结。
第一次烧结(预烧)是在比较低的温度下进行的,其目的是除去坯料中的有机粘结剂,并使其有足够的机械强度,以便其后坯料的机械加工、运输和装炉。
为了使有机粘结剂在预烧时充分挥发,预烧必须在氧化气氛中进行。
预烧的温度为1200摄氏度左右,保温2~3小时。
坯料在经过预烧后便可进行最终的高温烧结。
大规模生产时,高温烧结通常采用长约20m的隧道式氢气炉,以电加热。
在最高温度1850摄氏度左右保温5小时。
从升温到冷却的整个烧结过程约需35小时。
高温烧结后,陶瓷管的尺寸缩小20%~30%,其密度达到理论值的99.9%,成半透明状。
经过烧结,最终获得的PCA材料的物理特性列于表2。
表2PCA材料的物理特性
要获得高质量的PCA材料,烧结的温度、时间、气氛和添加剂MgO的含量都要仔细控制。
图3表明,烧结温度越高、时间越长,则密度也越高。
图4则说明,密度增加时,材料的透光率也增加。
但是,随着烧结温度的升高,晶粒的尺寸也要长大,结果其强度下降,如图5所示。
MgO是必不可少的掺杂剂,它能有效地减少气泡的数量(见图6)增加密度,减少对光的散射,其典型的含量是200~1000ppm。
现在,还在研究除MgO外再加入一些其他的掺杂剂,如Y2O、La2O3、ZrO2和CaO等。
这些阳离子半径较大的掺杂剂容易在晶界处分离,从而大大减少了金属卤化物灯内卤化物向晶界的扩散,使得灯的寿命延长不少。
图3烧结条件对PCA密度的影响
图4密度增加时透光率也增加
图5晶粒尺寸变大时强度下降
图6MgO含量增加时气泡减少
2非圆柱形陶瓷管的成形
圆柱形陶瓷管的加工精度很高,冷端温度能够得到很好的控制,因而灯的特性一致性非常好。
但是,圆柱形陶瓷管金属卤化物灯电弧管各处的温度不均匀,在其角上(即圆柱形陶瓷管与陶瓷塞的交界处)温度低,形成冷端(见图7),积存在此处的液态金属卤化物容易对陶瓷泡壳造成腐蚀。
图7圆柱形陶瓷金属卤化物灯内的温度分布
采用球形或椭球形的结构就可以比较好地克服上述缺点。
对非圆柱形陶瓷管的成形技术很多公司都进行了大量的研究。
他们采用的成形方法主要有以下几种。
2.1吹模成形法(BlowMolding)
这种方法是采用挤压出的圆柱形陶瓷管作为原料。
将陶瓷管置于模具中,该模具内表面的形状与设计的电弧管外形相同。
在高压气流的压力作用下,陶瓷管向外膨胀,直至扩大到模具的内表面,形成预定的形状,如图8所示。
这种方法对所用的圆柱形管的直径有限制,不能采用直径很细的管子作原料,否则会将管子吹破。
因此,这种方法只是用来吹制电弧管的当中部分,两边还需要再接上直径较细的陶瓷管来进行真空气密封接。
图8吹模法形成的椭球形陶瓷管
2.2注射成形法(InjectionMolding)
先将陶瓷粉与热塑性粘结剂混合。
该粘结剂在常温下是固体,但在高温下(通常低于200摄氏度)即变为液态。
再将该混合物制成丸状,并在室温下冷却,然后填入注模机中。
丸状的热塑性混合物原料经过加热融合,最后被注射入一个相对较冷的金属模具中。
在该模具中混合物重新冷却并凝固成设定的形状。
塑料桶的制作就是采用此方法。
该方法的优点是可以用来生产管壁很薄、形状又很复杂的陶瓷管。
但这种方法的缺点是较难精确控制陶瓷管的内、外直径。
一个可行的办法是采用此法生产半个陶瓷管,然后再如图9所示将两个这样的陶瓷元件结合在一起。
图9注射法制作的二体型圆形陶瓷管
2.3粉浆浇铸成形法(SlipCasting)
先将陶瓷粉末和粘结剂加入到液体(通常为水)中,形成一种低粘性的悬浮液。
再将该悬浮液倒入多孔的模具中,模具内壁的形状与目标物的外形完全一致。
由于毛细作用,悬浮液中的流体部分渗入到多孔的模具中,留下的陶瓷粉与粘结剂的混合物则附着在模具的内表面。
随着时间的增加,更多的液体进入多孔模具,而附着层的厚度也不断增加。
一定时间后,陶瓷附着层的厚度就会达到目标的要求。
这时,将多余的悬浮液排出,在模具中便留下预定形状的陶瓷坯料,如图10所示。
图10粉浆浇铸法制作的陶瓷管
2.4凝胶注模成形法(GelCasting)
凝胶注模成形法是上世纪90年代初期发展起来的,它可以用来进行精密陶瓷部件的加工。
其基本工艺流程是:
1、将陶瓷粉料分散于含有机单体和交联剂的水溶液(或非水溶液)中,加入分散剂,制成低粘度、高固相体积百分数的浓悬浮液;2、通过真空球磨,排除浆料中的气泡,降低悬浮液粘度,增加浆料的流动性,以有利于后续的注模成形;3、在依次加入引发剂和催化剂并充分混合均匀后,将悬浮液注入模具中,在一定的温度下引发单体的原位聚合,将陶瓷粉粘结在一起,形成具有一定强度和柔韧性的坯体;4、坯体脱模后,经室温干燥处理,然后进行高温脱脂、烧结,将有机凝胶在高温下分散挥发,坯体进一步致密化烧结后就成为可供加工的精密陶瓷部件。
图11NGK生产球形陶瓷管的方法
日本NGK公司采用如图11所示的方法成功制造出一体化的椭球形的陶瓷管。
在金属外模里面放了一个由低熔点聚合物材料做成的内模,二者的相对位置由金属销钉来固定。
同时,球形陶瓷管俩边的毛细管的内径也是由该金属销钉所决定。
将按前述方法混合成的悬浮陶瓷浆液注入内、外模间的空隙。
待交联反应完成并固化后,打开外模,通过加热去掉内模,就得到管子的坯件。
再经过烧结,生成球形陶瓷管。
图12则说明了该过程的各个步骤。
图12带可去除内模的凝胶注模成形法
3透明陶瓷管
除了PCA以外,还有其他一些半透明的陶瓷材料也可以用来做高强度放电灯的电弧管。
例如,尖晶石(MgAl2O4)和氧化钇(Y2O3)都可以用作电弧管的材料。
它们有更高的熔点,而且由于是立方形晶体结构,光学特性更佳。
Waymouth先生曾经采用氧化钇电弧管制作高压钠灯,得到了更高的光效,详细情况可参见《光源原理与设计》。
这几种陶瓷材料的添加物和烧结温度列于表3。
表3几种陶瓷材料的添加物和烧结条件
由于PCA是半透明的,所制作的光源不能用于诸如汽车前照灯之类的投光灯中。
在这些场合,光源必须具有清晰可见的高亮度电弧。
为了进一步提高金属卤化物灯的性能,科学家们对透明陶瓷进行了大量的研究。
研究发现,Y2O3,Y2O3-La2O3,MgAl2O4,YAG(Y3Al5O12),AlON(Al23O27N5)和Dy2O3等都是立方形晶体,在晶界处没有由于双折射而造成的散射,经抛光后可以做成透明的材料。
通过一种固体晶体转换过程(SSCC)可以将PCA转换成单晶氧化铝,即蓝宝石;通过烧结――热等静压(HIP-HotIsostaticPressing)过程,则可以形成微米级的近乎透明的多晶氧化铝。
图13给出了上述一些材料以及石英玻璃的光谱透过率曲线。
蓝宝石可以用来制作高强度放电灯,而且有不少好处。
首先,它更能抵抗钠的侵蚀;其次,可以在更高的温度下工作,用它制作的HID灯的光效能提高;再者,由于它是透明的,灯具的出光效率也更高。
但是,它有各向异性的缺点,应力容易导致破裂或漏气,封接也比较困难。
此外,蓝宝石只能制成圆柱形管,不能用来制作球形HID灯。
近年来在透明陶瓷研究方面最重要的成果之一是透明的钇铝石榴石YAG。
无论从光学还是力学性能来说,它都要比PCA优秀得多。
它已被成功地用来制灯。
但是,它抵御金属卤化物腐蚀的能力还是个问题。
为了减少被腐蚀的风险,今后需要研究在灯内填充新的物质。
氮氧化铝AlON的机械强度和热胀性能与PCA相仿,抛光的AlON的直