泵盖铸造工艺课程设计.docx
《泵盖铸造工艺课程设计.docx》由会员分享,可在线阅读,更多相关《泵盖铸造工艺课程设计.docx(16页珍藏版)》请在冰豆网上搜索。
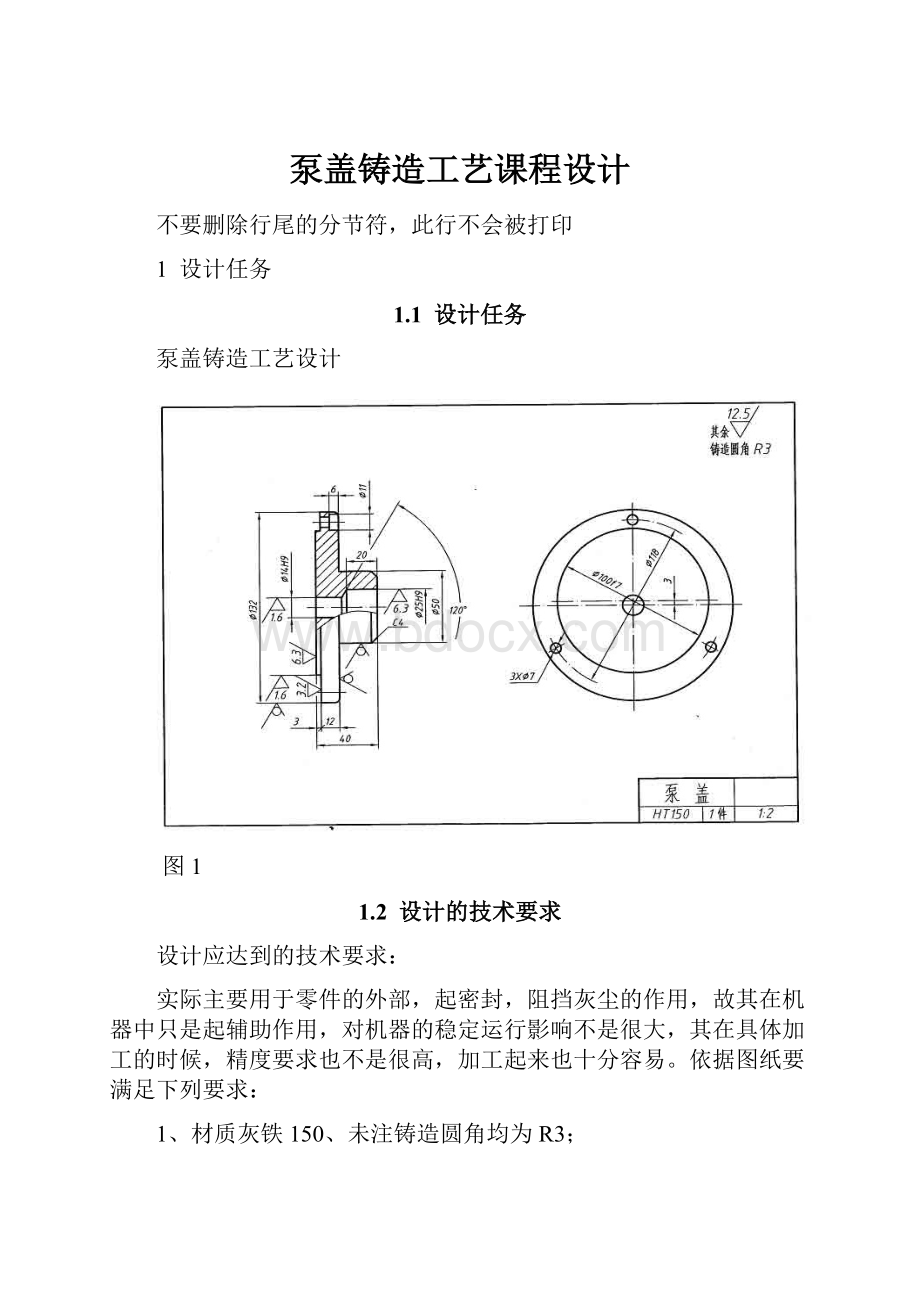
泵盖铸造工艺课程设计
不要删除行尾的分节符,此行不会被打印
1设计任务
1.1设计任务
泵盖铸造工艺设计
图1
1.2设计的技术要求
设计应达到的技术要求:
实际主要用于零件的外部,起密封,阻挡灰尘的作用,故其在机器中只是起辅助作用,对机器的稳定运行影响不是很大,其在具体加工的时候,精度要求也不是很高,加工起来也十分容易。
依据图纸要满足下列要求:
1、材质灰铁150、未注铸造圆角均为R3;
2、铸件表面不得有沙眼、缩孔等缺陷;
3、泵盖底部Φ132表面Ra为3.2,Φ100表面Ra为6.3,二者之间台阶Ra1.6。
Φ14中心孔内表面Ra为1.6,Φ25中心孔内表面Ra为6.3,其余为Ra12.5;
4、两个圆柱孔分别为中心大圆柱Φ25H9基本尺寸为Φ25mm,公差带为H8的孔;中心小圆柱Φ14H9
2铸造工艺方案的确定
2.1铸造工艺方案分析与论证
2.1.1零件结构分析
名称:
泵盖材料:
HT150
外形尺寸:
132×12×40mm体积:
2.21×102cm3
质量:
1.59kg生产批量:
中大批量生产(自定)
表面积:
3.97×102cm2密度:
7.2g/cm3
ab
图2泵盖:
三维零件图
2.1.2分型面的确定
在生产中考虑选择分型面时应注意以下原则:
1、应使铸件全部或大部置于同一半型内,以保证铸件精度。
如果做不到上述要求,必须尽可能把铸件的加工面和加工基准放在同一半型内。
2、应尽量减少分型面的数目。
分型面越少,铸件精度容易保证且砂箱数目少减少工人劳动量。
3分型面应尽量选用平面。
平直分型面可简化造型过程和模板制造,易于保证铸件精度。
4分型面通常选在铸件的最大截面处,尽量不使砂箱过高。
高砂箱,造型困难填砂、紧实、起模、下芯都不方便,劳动强度大。
5尽量便于下芯、合型和检查型腔尺寸。
6注意减轻铸件清理和机械加工量。
就本次的泵盖而言:
将铸件大部分---重要部分(泵盖圆盘底部)置于下部且分型面为最大截面。
此方案便于起模,方便下芯,保证浇注质量、能够实现顺序凝固、使其金相组织均,同时保证铸件的精度减少不必要的缺陷。
亦能减少后加工量!
图3
2.1.3浇注系统(包括冒口)的选择
浇注位置选择取决于合金的种类、铸件结构、铸件质量要求及生产条件。
确定浇注位置的主要原则有:
1.要加工面朝下或呈直立状态
2.应有利于铸件补缩
3.应保证铸件有良好的金属液导入位置,保证铸件充满
4.应使合型、浇注和补缩位置相一致
(1)、浇注系统形式的选择:
由以上分析采用:
封闭式——较好的阻渣能力、可以防止金属液卷入气体消耗金属少清理方便等;
顶注式浇注系统——容易充满,减少薄壁铸件浇不到、冷隔等缺陷,冲型后上部温度高于底部,有利于铸件自上而下顺序凝固等优点。
(2)浇注系统计算
浇注时间
经计算的浇注时间t=3.32s
液面上升速度
铸件高度/浇注时间=40/3.3=12.2mm/s,大于金属液允许最小上升速度10mm/s。
直、横、内浇道截面积的确定
跟据Osann公式可计算出浇注系统最小截面积之和。
∑A内=G/(0.31×μ×t×Hp1/2)(cm2)
式中:
∑A内---浇注系统最小截面面积之和;
G---型内铁液总重量2.27kg;
μ---流量系数,取0.5;
Hp---平均压头。
由于浇注方式为顶注式,则Hp=l×tanα=13.1732mm×tan9°=20.86mm
∑A内=2.27/(0.31×0.5×3.3×2.091/2)=2.84cm2
各浇道的截面积比为:
ΣS内:
ΣS横:
ΣS直:
=1:
1.2:
1.4
所以直浇道截面积3.41cm2;横浇道截面积3.98cm2
由此可得直浇道半径为0.3cm。
(3)冒口设计
采用模数法设计冒口:
由模数计算公式Ms=V/S,计算铸件模数Ms=0.53cm<0.75cm宜采用浇注系统当冒口,因此不用设专门的冒口。
根据实际生产情况:
采用机械化大批量生产小型铸件过程中采用一腔多模时,由于内浇道、横浇道截面积仅有几平方厘米,在造型过程中精确度不易把握,采用直浇道向型腔直接注入金属液,浇注系统亦能充当冒口功能即可满足补缩要求!
a
b
图4
2.1.4工艺参数的确定
尺寸公差
根据零件图技术要求:
其铸件尺寸公差按照GB/T6414-86《铸件尺寸公差》中灰口铸铁砂型手工造型公差等级为CT12级,尺寸公差为9mm。
重量偏差:
零件重量:
1.59kg;设铸件的工艺出品率为70%,据此估计铸件重量为:
2.27kg。
铸件收缩率
铸件材料为灰铁,收缩过程为受阻收缩,根据表3-3-7[1],中小型件得铸造自由收缩率为1.0%,受阻手缩率0.9%。
机械加工余量
根据所选尺寸公差等级CT12级,加工余量等级G级,具体数值见图。
最小铸出孔及槽
根据表3-3-8[1]查得大批量小型铸件最小铸出孔为Φ14mm。
零件中小于Φ14mm的孔不铸出,其余孔均铸出。
拔模斜度
根据已经确定的摸样高度、表面粗糙度,查表JB/T5018-91得零件的拔模斜度为1°。
a
b
图5
2.15铸造工艺简图
a
b
图6
2.2芯盒的设计
2.2.1制芯方法的确定
根据工艺方案,采用采用手工制芯。
高H=43,直径D=24H/D<2.5
砂芯尺寸如下:
图7
2.2.2芯盒选材
机械化生产为了提高砂芯的精度和芯盒的耐用性,采用金属芯盒,材质为ZL104。
2.2.3芯盒简图
图8
2.3模板的设计
2.3.1模板类型
一般模板由模底板、模样、浇冒口系统模、定位元件等组成。
2.3.2模板的选材
根据模样结构及生产要求,要有适当的强度和耐磨性,根据表3-6-4确定,模板选材为铸铁。
2.3.3模板的定位装置
采用定位销直接安装在模底板上即可满足要求。
2.3.4模板简图
简图如下:
图9上模板
图10下模板
2.4合箱图
2.4.1砂箱的选择
根据分型方法及铸件自身特点选择两箱型。
2.4.2砂箱的定位
采用定位梢
2.4.3砂箱的其它工艺参数(包括压铁、起吊等)
摸样高40mm,查表3-6-5得吃砂量最小值为32mm
2.4.4合箱简图图
图11合箱图
3铸造工艺卡
零件名称
泵盖
材质
HT150
材料
铸件重量(kg)
铸件材质
炉料
每个毛坯可切零件数
净重
毛重
浇注系统重
1.59
2.27
0.68
HT150
铁锭、废钢
3(圆孔)
造型
砂型名称
砂型类型
造型方法
砂箱编号
砂箱内部尺寸(mm)
备注
长
宽
高
上箱
树脂砂
手工
01
200
200
80
下箱
树脂砂
手工
02
200
200
50
砂型
树脂砂
射砂
干燥前
干燥后
芯撑
编号
次数
编号
次数
1
1
2
1
1
1
2
1
浇注
铁液出炉温度
(°C)
浇注温度
(°C)
每箱铁液消耗
(kg)
浇注时间(s)
冷却时间(min)
1400
1350
2.3
3.3
13
参考文献
[1]2012铸造工艺课程设计指导书
[2]王文清,李魁盛编《铸造工艺学》
........忽略此处.......