凝胶注模工艺制备陶瓷微球.docx
《凝胶注模工艺制备陶瓷微球.docx》由会员分享,可在线阅读,更多相关《凝胶注模工艺制备陶瓷微球.docx(11页珍藏版)》请在冰豆网上搜索。
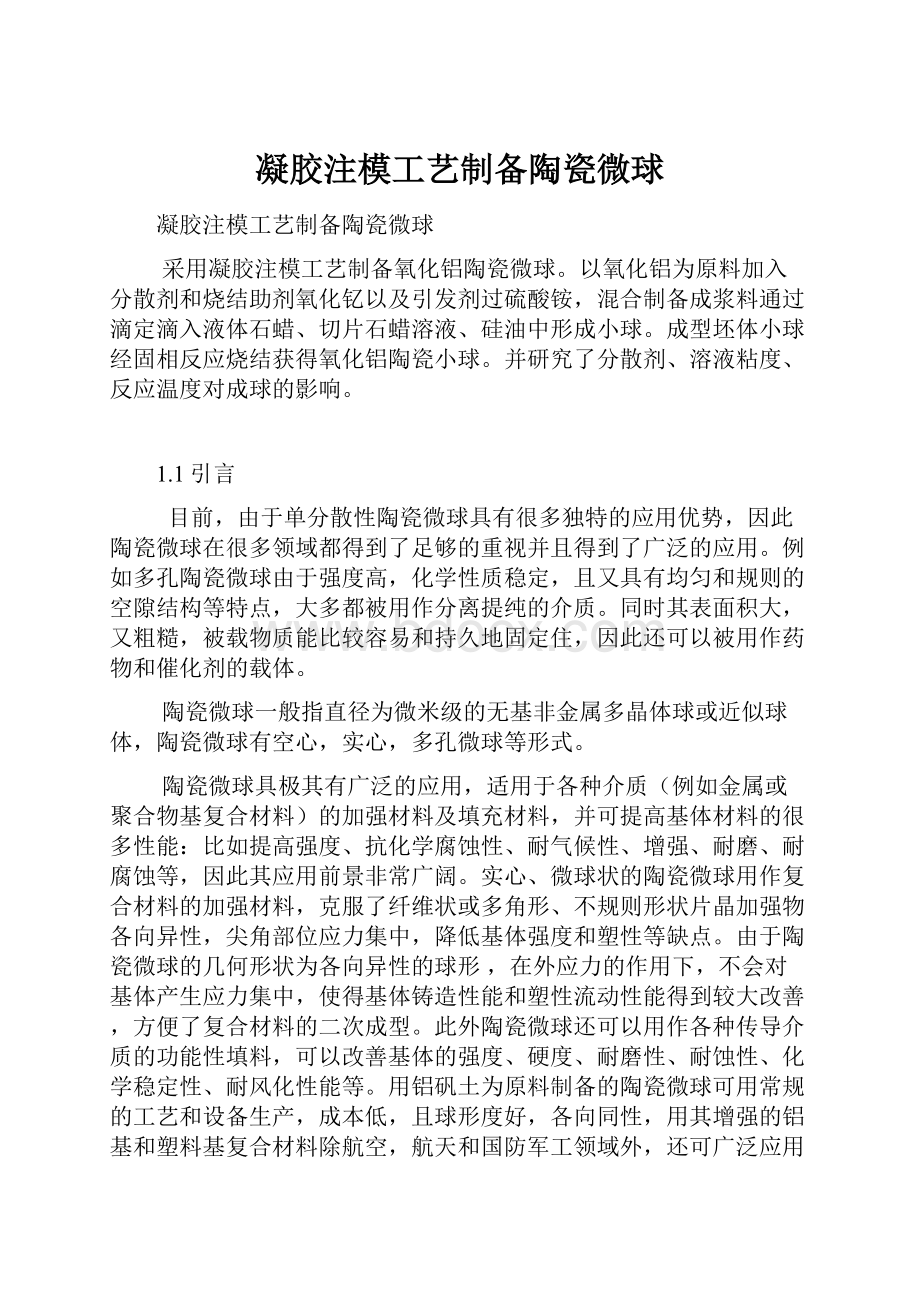
凝胶注模工艺制备陶瓷微球
凝胶注模工艺制备陶瓷微球
采用凝胶注模工艺制备氧化铝陶瓷微球。
以氧化铝为原料加入分散剂和烧结助剂氧化钇以及引发剂过硫酸铵,混合制备成浆料通过滴定滴入液体石蜡、切片石蜡溶液、硅油中形成小球。
成型坯体小球经固相反应烧结获得氧化铝陶瓷小球。
并研究了分散剂、溶液粘度、反应温度对成球的影响。
1.1引言
目前,由于单分散性陶瓷微球具有很多独特的应用优势,因此陶瓷微球在很多领域都得到了足够的重视并且得到了广泛的应用。
例如多孔陶瓷微球由于强度高,化学性质稳定,且又具有均匀和规则的空隙结构等特点,大多都被用作分离提纯的介质。
同时其表面积大,又粗糙,被载物质能比较容易和持久地固定住,因此还可以被用作药物和催化剂的载体。
陶瓷微球一般指直径为微米级的无基非金属多晶体球或近似球体,陶瓷微球有空心,实心,多孔微球等形式。
陶瓷微球具极其有广泛的应用,适用于各种介质(例如金属或聚合物基复合材料)的加强材料及填充材料,并可提高基体材料的很多性能:
比如提高强度、抗化学腐蚀性、耐气候性、增强、耐磨、耐腐蚀等,因此其应用前景非常广阔。
实心、微球状的陶瓷微球用作复合材料的加强材料,克服了纤维状或多角形、不规则形状片晶加强物各向异性,尖角部位应力集中,降低基体强度和塑性等缺点。
由于陶瓷微球的几何形状为各向异性的球形,在外应力的作用下,不会对基体产生应力集中,使得基体铸造性能和塑性流动性能得到较大改善,方便了复合材料的二次成型。
此外陶瓷微球还可以用作各种传导介质的功能性填料,可以改善基体的强度、硬度、耐磨性、耐蚀性、化学稳定性、耐风化性能等。
用铝矾土为原料制备的陶瓷微球可用常规的工艺和设备生产,成本低,且球形度好,各向同性,用其增强的铝基和塑料基复合材料除航空,航天和国防军工领域外,还可广泛应用于民用工业如轴承、活塞、缸套、自行车链、机械加工、汽车、齿轮及其他耐磨零件的制造。
正是因为陶瓷微球这些优异的性能,引起了学术界和工程界的广泛关注。
近些年来国内外学者在微球的制备和应用方面作了大量的工作。
就目前国内外的研究情况,依据微球的结构特点可以将其分为三类:
实心陶瓷微球,即整个球都是密实的;空心陶瓷微球,即球的中心部分是空的;多孔陶瓷微球,即球的表面有许多小的孔洞。
目前制备毫米级陶瓷球的方法很多,但主要有:
模具压制法,“行星式”滚动法,反相悬浮聚合法,外胶凝法,直接热解法,内胶凝法等,每种方法都有各自的优缺点,各方法的选择还应根据原料的性质而定。
而微米级陶瓷球形颗粒的制备方法主要有:
沉淀法、气流研磨法、溶胶-凝胶法、粒化-滚化法、挤压成型-滚动法、聚-诱导胶体聚集法、喷雾干燥法等。
大多数制备方法都具有操作复杂,微球制备效率低,难以大规模应用等的缺点。
不过目前陶瓷微球的制备方法大多都是用陶瓷超细粉经喷雾干燥的方法来制备陶瓷微球。
例如初小葵等对Al2O3粉料进行喷雾干燥成功制备了20~100微米的Al2O3陶瓷微球。
李志强等通过对均匀分散的SiC、C料浆进行喷雾干燥造粒制备得到了SiC陶瓷复合微球。
而马奇等对SiC-AlN复合浆料进行喷雾造粒,成功制备出了流动特性及成型性能都俱佳的SiC-AIN复合陶瓷微球。
唐文军等利用喷雾干燥技术对TiB2/A12O复合粉体进行造粒。
陆有军等通过对SiC浆料喷雾干燥得到了平均粒径50微米的SiC陶瓷微球。
Kuk Cho等通过喷雾干燥法合成了介孔CaCO3陶瓷微球。
然而人们对于用凝胶注膜工艺制备陶瓷微球方面研究较少,凝胶注模工艺制备陶瓷微球具有操作容易,仪器设备简单,实验可操作性强,成本低,实验成功率较高,制备得到的陶瓷微球形状规整,质地均匀,性能优越等特点并且可以提高生产效率,可大规模应用具有很高的经济价值。
凝胶注模(Gel—casting)成型技术是20世纪90年代初由美国橡树岭国家实验室发明的一种新的陶瓷成型工艺,其具有设备简单,可以成型复杂的零件和成本较低廉等优点,因此受到了工业界与学术界的广泛关注。
目前凝胶注模已被广泛应用于ZrO2、Al2O3、SiC和Si3N4等高致密性能结构陶瓷的制备。
其构想是将高分子化学单体聚合的思路引入到陶瓷材料的成型工艺中,通过制备低粘度、高固相含量的陶瓷浓悬浮体,浇注到模具中。
然后,在引发剂和催化剂的作用下,使悬浮体中的有机单体交联聚合成三维网络结构,从而使悬浮体原位固化成型,而得到均匀、高强度、高密度、准净尺寸的陶瓷坯体。
然后经过脱模、干燥、烧除有机结合剂后最终烧结,即得到所需的陶瓷部件。
在凝胶注模工艺制备陶瓷微球过程中浆料的制备过程中我们不可避免地会遇到粉体粒子易于聚集、难以分散的困难,因此根据粒子的特性选择适宜的分散剂是有效解决这一问题的关键。
分散剂可简单的划分为小分子型分散剂和超分子型分散剂(超分散剂)。
由于小分子型分散剂的种种局限性本文实验选用的是超分散剂。
超分散剂的分子结构特征如下:
超分散剂的分子结构按其所具有的功能和性质可分为两段:
即锚固段(A段)和溶剂化段(B段)。
超分散剂的A段是带有多个锚固基团(如-NR3+、-R2、多元醇及聚醚等)的聚合物链,为了防止超分散剂的脱附它们是通过共价键、离子键、氢键以及范德华力相互作用而紧紧地吸附在固体微粒表面。
而超分散剂的B段为聚酯、聚醚、聚烯烃以及聚丙烯酸酯等聚合物链。
它们会在纳米微粒表面形成一层吸附层,并且通过空间位阻作用对微粒的分散起稳定的作用。
超分散剂的作用机理如下:
超分散剂的作用机理是其分子结构设计的理论依据,主要包括锚固机理和稳定机理这两部分。
分散剂必须与微粒的表面形成牢固的结合这是超分散剂锚固机理的基础。
因此可以根据极性不同的纳米微粒可通过不同的锚固手段(例如“多点锚固”,“单点锚固”或“协同作用”)来进行锚固。
超分散剂的稳定机理目前已知的主要有两种理论:
即静电稳定机制和空间位阻稳定机制。
静电稳定机制是超分散剂发生电离而在纳米微粒表面形成双电层并且通过静电斥力从而使纳米微粒稳定存在于介质中。
而超分散剂在纳米微粒表面形成牢固的吸附并且具有足够的吸附层厚度(大于1~10纳米)的完整的覆盖层是空间位阻稳定的理论基础。
本文以氧化铝为原料加入分散剂和烧结助剂氧化钇以及引发剂过硫酸铵混合制备成浆料通过滴定滴入液体石蜡、切片石蜡溶液、硅油中形成小球。
成型坯体小球经固相反应烧结获得氧化铝陶瓷小球。
此方法制备的陶瓷微球具有质地均匀,高强度,高球形度等特点陶瓷微球所需原料和设备价格便宜,为陶瓷微球的制备提供了一种新方法。
第二章凝胶注模工艺制备陶瓷微球
2.1实验仪器:
10毫升量筒一个,5毫升量筒一个,分析天平,称量纸,药匙一个,棉花,100毫升烧杯一个,移液枪一个,一次性塑料移液管,超声机,磁子,2000毫升量筒一个,DF-101S集热式恒温加热磁力搅拌器,量程为100摄氏度的温度计一个,JJ-1精密增力电动搅拌器,25X25厘米玻璃板一块。
2.2实验药品:
丙烯酰胺(单体),亚甲基双丙烯酰胺,蒸馏水,聚丙烯酰铵(分散剂),氧化铝,烧结助剂氧化钇,引发剂过硫酸铵,石蜡,凡士林。
2.3实验原理:
丙烯酰胺(单体),亚甲基双丙烯酰胺在蒸馏水中溶解后,加入分散剂聚丙烯酰铵后加入烧结助剂氧化钇和氧化铝粉末搅拌半个小时后超声加入引发剂过硫酸铵制成料浆,然后用移液枪或者一次性塑料塑料移液管吸取少量的料浆缓慢滴入盛有加热了的石蜡溶液,切片石蜡溶液或硅油中,料浆液滴在粘度大的溶液中在缓慢的下降过程中由于受力均匀,会是一个球形的液滴。
液滴下降过程中由于受热会使液滴中引发剂过硫酸铵分解产生自由基引发单体聚合,从而使液滴固化成一个球形。
最终成型坯体小球经固相反应烧结获得氧化铝陶瓷小球。
2.4聚丙烯酸胺分散剂的制备
1.用一次性移液管和量程为100毫升的量筒分别量取30mL蒸馏水和30mL丙烯酸于干净烘干的100毫升烧杯中。
2.然后用分析天平称取0.126克过硫酸铵(引发剂)加入该烧杯中,用玻璃棒搅拌使其完全溶解配置成混合溶液。
3.取一个干净的量程为100毫升的三口烧瓶,用量筒量取30mL混合溶液于三口烧瓶中,然后用移液枪量取0.025毫升的异丙醇加入三口烧瓶中并将洗净烘干的磁子放入其中。
4.将三口烧瓶固定在水浴加热装置的支架上,水浴锅中加满水,调节支架使三口烧瓶浸没在水中,设定水浴加热锅的加热温度为75摄氏度,在此温度下反应15分钟。
5.反应15分钟后再将剩下的30毫升混合溶液倒入三口烧瓶上的恒压漏斗中,调节恒压漏斗上的旋钮来调节混合溶液液滴往下滴的速度,使其滴定时间为一个小时。
6.滴定完后保温反应2小时,反应结束后将反应产物聚丙烯酸装在干净的烧杯中,然后加入一定量的氨水搅拌使其反应生成聚丙烯酸胺并将其密封保存并贴上标签待用。
2.5浆料的制备
取丙烯酰胺(单体)3.0克,亚甲基双丙烯酰胺0.5克于烧杯中加10毫升蒸馏水超声使其溶解。
再加入3毫升分散剂,烧结助剂氧化钇和氧化铝粉末搅拌半个小时后超声加入引发剂过硫酸铵制成料浆。
2.6不同温度下制备陶瓷微球
用移液枪或者一次性塑料移液管吸取少量已经制备好的料浆缓慢滴入盛有加热了的石蜡溶液。
加热温度分别为110摄氏度、120摄氏度和130摄氏度,在这三种温度下制备氧化铝陶瓷微球。
在这三种温度下制备出的氧化铝陶瓷微球的样品分别如图2.6-1,图2.6-2,图2.6-3。
图2.6-1
图2.6-2
图2.6-3
2.7不同分散剂对陶瓷微球制备的影响
分别用聚丙烯酰铵和聚丙烯酸胺作为分散剂(但分散剂的用量不变)配制氧化铝浆料。
溶液为液体石蜡,加热温度为110摄氏度,实验制备得到的氧化铝陶瓷微球分别如图2.7-1和2.7-2。
图2.7-1
图2.7-2
2.8溶液粘度对实验结果的影响
1.将型号为KF-96-600CS的硅油倒入量程为500毫升的量筒中,测量硅油的液体高度为33厘米,然后滴入氧化铝浆料,其浆料小球下落的时间为24秒,同样将型号为KF-96-1500CS的硅油倒入石英管中测量其液面高度为45厘米,滴入的氧化铝浆料的小球下落时间为72秒。
2.将装有型号为KF-96-1500CS的硅油的石英管和装有型号为KF-96-600CS的硅油的2000毫升的量筒放入加了液体石蜡的油浴锅中加热,加热温度设定为为130摄氏度。
3.按照实验方案制备氧化铝浆料,但该实验用的分散剂为聚丙烯酸胺。
4.用液枪吸取少量的浆料一滴滴地滴入上述硅油中观察坯体小球下落的速度和成球情况。
图2.8-1和图2.8-2分别为型号为KF-96-600CS和型号为KF-96-1500CS的硅油中制备的氧化铝陶瓷微球。
图2.8-1
图2.8-2
2.9实验结果讨论与分析
本实验中,以丙烯酰胺(AM)作为有机单体,以N,N一亚甲基双丙烯酰胺(MBAM)作为交联剂,自己制备的聚丙烯酸胺(PAA—NH4)作为分散剂,过硫酸铵水溶液作为引发剂,制备氧化铝浆料。
在不同温度、不同分散剂、不同液体粘度下制备出的氧化铝陶瓷微球形状的规整性不同,陶瓷微球的成球率不同。
1.加热温度越高制备出的的陶瓷微球形状越接近球形,其成球率也越高。
温度越高反应越快,在成型坯体小球下落初期小球就已经烧结固化了,落到底部时不会由于冲击力而变形。
2.不同分散剂制备出的浆料其均匀性、稳定性、粘度都存在较大差异。
性质不同的浆料制备出的陶瓷的形状和其成球率都不同,分散剂的分散效果越好陶瓷的形状就越规整其成球率就越高。
3.当液体的粘度较大时,成型坯体小球下落的时间就越长因此其反应烧结过程所用的时间也越长,使得其反应更加充分在未落到底部时就固化了不会相互粘结在一起且不会因为与底部冲击而破坏其形状,得到的氧化铝陶瓷微球就成规整的球形,成球率就非常高,并且液体粘度越大效果越佳。
第三章结论与展望
3.1结论
1.料浆的pH值及不同的分散剂对粉料在介质中的高分散、高稳定性有重要影响,从而影响成型坯体小球经固相反应烧结获得氧化铝陶瓷小球的过程。
2.用液体石蜡、切片石蜡和不同型号的硅油,由于上部液体所加热的温度不同以及他们加热时的粘度差异导致成型坯体小球下落的时间差太大从而影响成型坯体小球固相反应烧结的时间和反应温度是获得的氧化铝陶瓷微球的形状规整性存在差异和成球率差别较大。
3.引发剂的加人量影响料浆的固化时间,本实验所用引发剂的量为0.02g
4.加热时上部液体的温度较高,且液体的粘度大,小球的下落时间越长,滴入的成型坯体小球的直径比较小时经烧结获得的小球形状越规整,陶瓷小球的成球率越高。
3.2展望
1.由于分散剂分散剂的不同,导致配置的浆料的性质不同从而对实验的结果产生影响,因此可以寻找更合适的分散剂分散粉体使配制的浆料更佳。
2.不同的粉体做出来的浆料有一定区别,所以可以尝试多种粉体进行试验。
3.我们所做的实验加热装置无法将容器上部的液体加热到设定温度,而且与设定温度有较大差异,由此我们可以改进加热装置或找到更先进的加热装置进行试验。
4.由于反应所需的液体环境对反应有很大影响,所以可以寻找粘度更大的且可以加热到较高温度,此外其粘滞系数随温度的变化较小,这样也可以提高成球率和所成球形状的规整性。