完整版产品结构设计章1.docx
《完整版产品结构设计章1.docx》由会员分享,可在线阅读,更多相关《完整版产品结构设计章1.docx(11页珍藏版)》请在冰豆网上搜索。
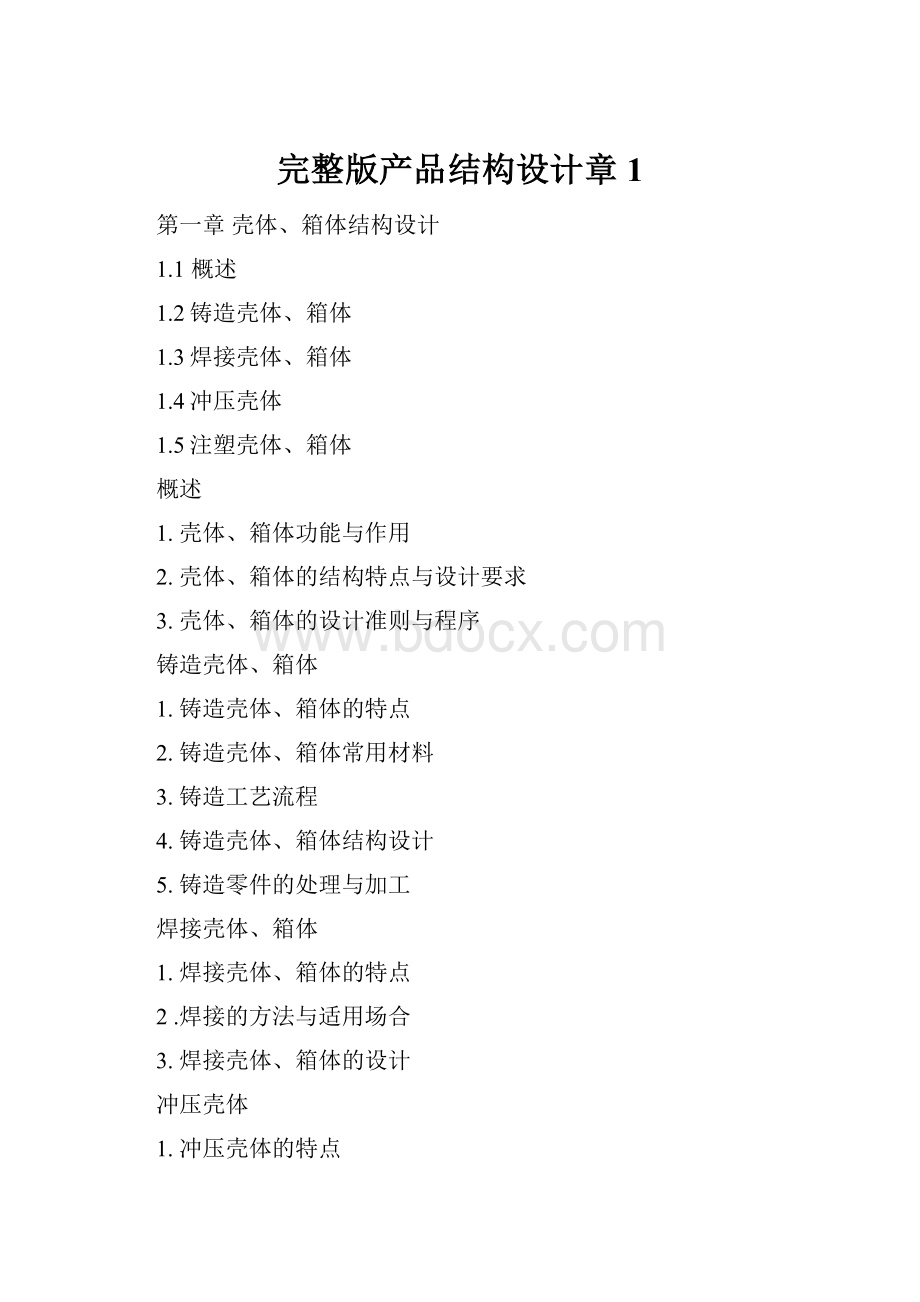
完整版产品结构设计章1
第一章壳体、箱体结构设计
1.1概述
1.2铸造壳体、箱体
1.3焊接壳体、箱体
1.4冲压壳体
1.5注塑壳体、箱体
概述
1.壳体、箱体功能与作用
2.壳体、箱体的结构特点与设计要求
3.壳体、箱体的设计准则与程序
铸造壳体、箱体
1.铸造壳体、箱体的特点
2.铸造壳体、箱体常用材料
3.铸造工艺流程
4.铸造壳体、箱体结构设计
5.铸造零件的处理与加工
焊接壳体、箱体
1.焊接壳体、箱体的特点
2.焊接的方法与适用场合
3.焊接壳体、箱体的设计
冲压壳体
1.冲压壳体的特点
2.冲压工艺与模具
3.冲压零件的设计
注塑壳体、箱体
1.注塑壳体、箱体的特点
2.注塑工艺与模具
3.注塑壳体、箱体设计
1.壳体、箱体功能与作用
壳体与箱体没有本质上的区别:
壳体:
从产品构造和结构特点上的称谓具有包容内部组成部件且厚度较薄的特征,如电视机壳。
箱体:
从零部件功能和结构方面的定义,具有包容、支撑等结构功能且相对封闭的特点,如汽车变速箱。
壳体、箱体的主要功能,以图1-1为例:
容纳、包容:
讲产品构成的功能部件容纳于内。
定位、支撑:
支撑、确定产品构成各零部件的位置。
防护、保护:
防止构成产品的零部件受环境的影响、破坏或其对使用者与操作者造成危险与侵害。
装饰、美化:
工业造型设计主要关注的问题。
其他:
依产品的功能和使用目的而定。
2.壳体、箱体的结构特点与设计要求
结构特点:
在满足强度、刚度等设计要求的基础上,通常采用薄壁结构。
设计要求:
定位零部件:
以图1-2为例,固定的零部件与运动的零部件在结构上有所不同。
便于拆、装:
考虑产品的组装、拆卸和维修、维护,箱体多设计成分体结构,各部分通过螺丝、锁扣等进行组合连接。
以图1-3、4为例,考虑拆卸的设计:
以图1-5为例,不考虑拆卸的设计。
考虑材料及加工、生产方式:
产品功能和使用目的决定外壳材料,生产成本和批量决定加工、生产方式,进而决定壳体、箱体的结构设计。
考虑装饰与造型装饰与造型的设计应结合产品的功能、构件的材料及加工、生产方式进行。
3.壳体、箱体的设计准则与程序
保证刚度、强度、稳定性及加工性的设计准则
刚度:
对于承受较大载荷及作为支撑和其他零部件定位的壳体和箱体,刚度是主要设计准则。
强度:
强度时考虑壳体、箱体的防护和保护性能进行设计的基本准则,分静态和动态两方面考虑。
稳定性:
受压及受压弯结构都存在失稳问题,特别是薄壁腹部还存在局部失稳问题,必须校核。
加工性:
铸造、注塑构件应考虑液体的流动性、填充线和脱模,冲压件应考虑材料延展性和拉伸能力,并做相应的计算。
壳体、箱体的通常设计步骤与程序
初步确定形状、主要结构和尺寸。
常规计算。
静动态分析、模型或实物试验及优化设计。
制造工艺性和经济性分析。
详细结构设计
1.铸造壳体、箱体的特点
有较高的刚度、强度:
铸造构件一般壁厚较大,适合对刚度强度要求较高的产品外壳;也可以在铸件上制作部分其他结构部件。
造型适应性强:
可制作比较复杂和变化不规则外形,以图1-6、7、8为例。
表明粗糙。
尺寸精度低。
封闭性好:
以图1-9为例。
工艺灵活性打、成本低。
其他:
铸铁材料具有减震、抗震性能和耐磨、润滑性能。
铸造成型的主要缺点:
铸造组织的晶粒比较粗大,且内部常有缩孔、缩松、气孔、砂眼等缺陷,力学性能一般不然锻件。
铸造生产工序繁多,工艺过程较难控制,废品率较高。
工作条件较差,劳动强度比较大。
2.铸造壳体、箱体常用材料
铸铁:
铸铁流动性好,体收缩和线收缩小,容易获得形状复杂的铸件,在铸造时加入少量合金元素可提高耐磨性能。
铸铁分类:
灰铸铁、球墨铸铁、蠕墨铸铁、可锻铸铁。
铸造碳钢:
铸钢熔点高、流动性差、收缩率大,吸震性低于铸铁,弹性规模较大。
铝合金:
纯铝强度低、硬度小,因此,制造产品壳体常采用铝合金材料。
常用铝合金有:
铝硅合金、铝铜合金、铝镁合金、铝锌合金。
3.铸造工艺流程
砂型铸造:
砂型铸造时应用最广泛的铸造方法,其生产过程如图1-10所示。
砂型的结构组成如图1-11所示。
砂型铸造有适应性强、生产简单等优点,但砂型铸造生产的铸件尺寸精度较低、表面粗糙、内在质量较差,且生产过程较复杂。
熔模铸造:
熔模铸造的工艺流程如图1-12所示。
与砂型铸造比较,有以下几个特点:
铸件精度及表面质量高。
能够铸造各种合金铸件。
生产批量不受限制。
熔模铸件的形状可以比较复杂。
熔模铸件的重量不宜太大。
金属型铸造:
用金属制成的铸造型腔,进行浇注获得铸件的铸造方法,如图1-13所示。
与砂型铸造比较,金属铸造有以下的特点:
实现了“一型多铸”。
铸件的力学性能提高。
精度及表面质量高。
金属型的制造成本高、周期长;铸型透气性差、无退让性,易产生冷隔、浇不足、裂纹等铸造缺陷。
压力铸造:
如图1-14所示,在高压下,使液态或半液态金属以较高的速度填充铸型的型腔,并在压力作用下凝固而获得铸件的方法。
与砂型铸造比较,有如下优点:
铸件尺寸精度、表面质量高。
铸件的强度和表面硬度高。
可铸造形状复杂的薄壁铸件。
生产效率高。
压力铸造的缺点:
设备投资大,压型成本高。
压铸高熔点合金时,压型的寿命低。
离心铸造:
如图1-15所示,将液态合金浇入高速旋转的铸型中,使金属在离心力的作用下填充铸型并凝固成型。
与砂型铸造比较,有如下特点:
工艺过程简单,节约金属和其他原材料。
铸件组织致密,无缩孔、气孔、夹渣等缺陷,力学性能好。
铸造合金的种类不受限制。
铸件的内表面质量差,孔的尺寸不易控制。
4.铸造壳体、箱体结构设计
在设计铸造壳体、箱体结构时,除考虑壳体设计的总体要求与准则,还应重点结合铸造生产的工艺特点,考虑相关的工艺性。
在此,结合一些典型设计实例进行有关讨论。
铸造时处于水平位置,易造成气孔和夹渣,如图1-16所示。
尽量减少凹凸部分,简化制造工艺,如图1-17所示。
考虑出模工艺,应在结构上设计拔模斜度,包括内腔结构,如图1-18所示。
对于砂型铸造,尽量减少活块部分,简化制造工艺,如图1-19所示。
凸台距离分型面较近时,为避免使用活块,可将凸台延长至分型面或取消凸台,如图1-20所示。
如图1-21所示,修改一些局部结构,保证砂型牢固。
如图1-22~图1-24所示,修改不合理凸台,达到保护砂型进而保证铸件质量的目的。
如图1-25、图1-26所示,修改结构避免使用型心或减少型心数量。
5.铸造零件的处理与加工
铸造零件一般存在一定内应力,经过一段时间,内应力消除,零件会产生一定变形,影响几何精度与使用性能,尺寸越大的铸件,影响越大。
一般铸件在机加工前,要经过一定处理。
铸铁铸件消除内应力的方法:
时效处理,热处理,机械振动法。
铸钢件一般都需要热处理。
壳体、箱体铸件的关键部位一般需要精加工。
主要部位包括:
壳体、箱体分离部分之间的连接部位。
壳体、箱体与内部零部件的定位与连接部位。
壳体、箱体与外部其他零部件的连接部位及地脚部位。
1.焊接壳体、箱体的特点
焊接壳体、箱体有以下特点:
适用范围广。
使用灵活。
生产周期短。
强度高。
焊接的主要缺点是:
造型能力较差。
加工精度较低。
焊接部位表面质量较差。
焊接产生一定的内应力,造成成品变形。
2.焊接的方法与适用场合
电弧焊
利用电弧作为热源的熔焊方法,称为电弧焊。
手工电弧焊:
设备简单,使用灵活、方便、通用,但对操作人员的技能要求较高。
不适宜焊接活泼金属及难熔合低熔点金属。
埋弧自动焊:
利用连续送进的焊丝在焊剂层下产生电弧而自动进行焊接的方法,如图1-27、1-28所示:
埋弧自动焊的主要特点:
生产效率高,焊缝质量好,焊接规范自动控制。
适用于大批量生产,可焊接中、厚钢板(6~60mm)。
气体保护焊:
用外加气体作为电弧介质并保护电弧和焊接区的电弧焊。
保护气体主要有两种:
惰性气体(氩气和氮气)和活性气体(二氧化碳),其中氩弧焊,应用比较广泛。
电阻焊
利用电流通过工件及焊接接触面间所产生的电阻热,将焊件加热至塑性或局部熔化状态,再施加压力形成焊接接头的焊接方法。
有电焊、缝焊、相对焊三种形式。
电焊:
其基本结构如图1-29所示,适用于焊接4mm以下薄板广泛用于汽车、飞机、电子、仪表和日常生活用品生产。
缝焊:
焊接厚度3mm以下的薄板搭接,主要应用于生产密封容器和管道等,如图1-30所示。
3.焊接壳体、箱体的设计
焊接结构材料的选择:
选用焊接性好的材料才制造焊接结构壳体、箱体。
焊接方法的选择:
根据材料的焊接性、工件厚度、生产率要求、各种焊接方法的适用范围和设备条件等综合考虑。
焊接接头工艺设计
手工电弧焊接头基本形式有四种,如图1-31所示:
除搭接接头外,其余接头在焊件较厚时需开坡口。
坡口的基本形式如图1-32所示:
焊缝布置应遵循以下原则:
便于施焊:
焊缝设置必须具有足够的操作空间以满足焊接工艺需要。
如图1-33、1-34所示。
有利于减少焊接应力与变形:
尽量选用尺寸规格较大的板材、型材。
避开最大应力区和应力集中部位。
避开或远离机械加工面。
1.冲压壳体的特点
板料冲压制造产品壳体具有下列特点:
生产率高、操作简单。
产品质量好。
材料利用率高。
造型能力强
适用广泛。
主要缺点:
集中在模具方面。
冲模设计、制造负责,成本高,且一件一模,局部更改,也要更换模具。
小批量生产成本较高,图1-35的模型就是例子。
2.冲压工艺与模具
冲压设备主要有剪床和冲床两大类。
常用小型冲床的结构如图1-36所示,冲压基本工序如图1-37所示。
冲压模具按冲床的每一次冲程所完成工序的多少划分为简单冲模、连续冲模及复合冲模。
简单冲模在冲床的一次冲程内只能完成一道工序。
如图1-38所示,简单冲模的结构简单,成本低,生产率低,主要用于简单冲裁件的生产。
连续冲模在冲床的一次冲程中,在模具的不同位置上可以同时完成两道以上的工序,如图1-39所示。
连续冲模生产率高,易于实现自动化,但结构复杂、成本高,适于大批量生产精度要求不高的中、小型零件。
复合冲模在冲床的一次冲程内,在模具的同一位置上可以同时完成两道以上的工序,如图1-40所示。
复合冲模生产效率高,零件加工精度高,但模具制造负责,成本高,适用于大批量生产。
3.冲压零件的设计
在设计冲压壳体结构时,须综合考虑产品结构需要、零件结构强度、材料特性与成型能力、冲压模具复杂性及冲压工艺等因素。
如图1-41、1-42所示。
弯曲时尽可能使弯曲线与坯料纤维方向垂直,如图1-43所示。
设计弯曲件时应加强变形部位的刚性,如图1-44所示。
在设计拉伸壳体时,应注意拉伸变形的影响,如图1-45所示。
1.注塑壳体、箱体的特点
注塑壳体、箱体有以下特点,如图1-46为例。
生产周期短,生产效率高,易于实现大批量、自动化生产。
可使用材料丰富,适应性强。
产品质量较高,一致性好、互换性强,成本低。
几何造型能力强,可生产现状、结构复杂的产品。
功能性与装饰性结合好。
明显的缺点:
注塑模具成本较高,不适于单件、小批量生产。
强度、表面硬度较低,扛冲击、磨损性能差,局部细小结构在维修过程易损坏。
材料存在老化问题,耐久性差。
2.注塑工艺与模具
典型注塑工艺过程如图1-47所示。
注塑模具在结构组成上是比较复杂的,按功能、作用分以下几个部分:
成型部分:
模具的核心部分,由可分合的两部分组成,类似于凸模和凹模。
浇注系统
排溢、引起系统
冷却系统
脱模机构
模架
3.注塑壳体、箱体设计
注塑壳体、箱体的结构设计应综合考虑产品要求、外观造型、注塑材料、各功能局部、生产加工条件及成本等因素。
壁厚设计尽可能均匀,如图1-48所示。
在壳体转弯连接处,避免使用锐角连接,如图1-49所示。
在壳体结构上,尽量避免表面凹陷,如图1-50所示。