工艺编制注意v10.docx
《工艺编制注意v10.docx》由会员分享,可在线阅读,更多相关《工艺编制注意v10.docx(17页珍藏版)》请在冰豆网上搜索。
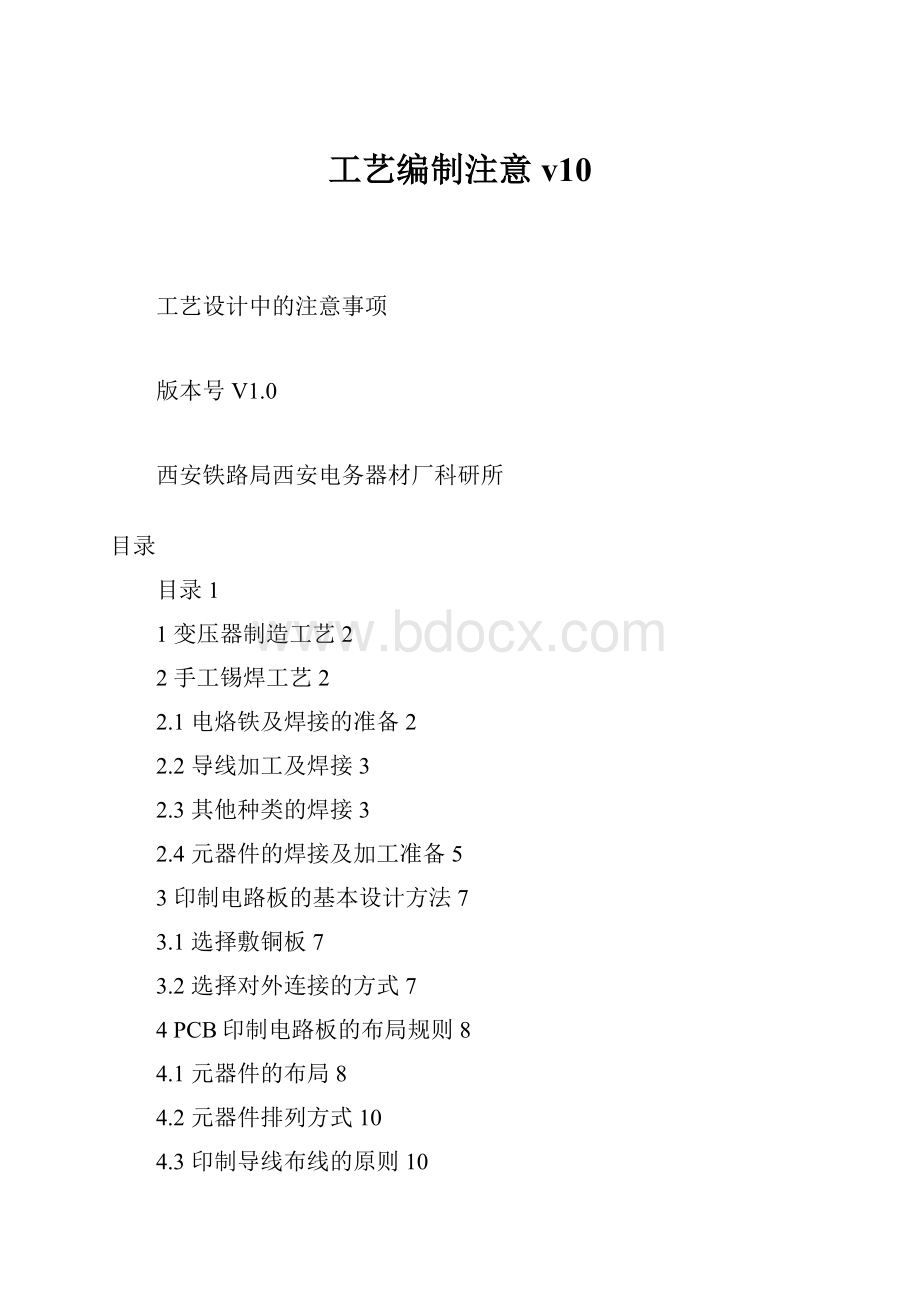
工艺编制注意v10
工艺设计中的注意事项
版本号V1.0
西安铁路局西安电务器材厂科研所
目录
目录1
1变压器制造工艺2
2手工锡焊工艺2
2.1电烙铁及焊接的准备2
2.2导线加工及焊接3
2.3其他种类的焊接3
2.4元器件的焊接及加工准备5
3印制电路板的基本设计方法7
3.1选择敷铜板7
3.2选择对外连接的方式7
4PCB印制电路板的布局规则8
4.1元器件的布局8
4.2元器件排列方式10
4.3印制导线布线的原则10
4.4印制板的排版设计应考虑的因素11
4.5印制板组装件保护涂覆准则及典型工艺技术介绍12
5接线工艺14
5.1配线14
5.2布线原则15
5.3布线方法15
5.4布线顺序16
6机械结构工艺16
6.1防止连接松动的几项措施16
6.2紧固件的安装17
6.3胶接的基本工艺17
7参考文献19
1
变压器制造工艺
1.1考虑变压器外壳的大小综合考虑铁芯的尺寸,先查询相关技术标准再根据实际提出合理的尺寸要求和公差要求。
1.2变压器采用钢带紧固时,要考虑钢带接点的位置是否影响局部装配;
1.3变压器一般本身带有固定脚,安装时把固定脚插入印制板上的对应孔位,然后焊接即可;
1.4中频变压器要与底板吻合;
1.5大型的电源变压器一般都不放在电路板上,如果需要放在电路板上则要用螺钉将其固定,螺钉要加弹簧垫圈。
这类变压器的插孔在设计时一般要放在电路板的边上,最好靠近电路板的固定处,否则电路板受压过大,易被折断。
2手工锡焊工艺
2.1电烙铁及焊接的准备
1)电烙铁的选择和使用。
烙铁头的形状要适应被焊物面的要求和焊点及元器件密度,功率大的电烙铁,烙铁头的体积也大。
常用的外热式电烙铁的头部大多制成錾子式样,,焊接密度较大的产品时,可用头部窄小的烙铁头。
内热式电烙铁常用圆斜面烙铁头,适用于焊接印刷版和一般焊点。
2)电烙铁的握法,如图2.1所示。
图2.1
2.2导线加工及焊接
1)工具材料准备:
塑料绝缘导线(包括单芯和多芯)、电烙铁及烙铁架、剥线钳、斜口钳、尖嘴钳、接线端子等。
2)绝缘导线加工工序:
剪裁→剥头→清洁→捻头(对多股线)→浸锡。
3)屏蔽导线加工步骤:
剥掉最外层绝缘层→用镊子把金属编织线根部扩成线孔→剥出一段内部绝缘导线→把根部的编织线捻紧成一个引线状→剪掉多余部分→切掉一部分内绝缘体,露出导线(注意在切除过程中不要伤到导线)→给导线和金属编织网的引线上锡。
4)导线线头处理情况
小股线线头只留2~3mm,焊时简洁、牢靠,特别对多束线应捻后上锡。
5)连线要留有维修余量。
2.3其他种类的焊接
1)绕焊(网绕可靠性最好,用于可靠性要求高的地方)。
导线和接线端子的绕焊,是经过上锡的导线端头在接线端子上绕一圈,然后用钳子拉紧缠牢后进行焊接。
如图2.2所示是常用网绕示例。
在缠绕时,导线一定要紧贴端子表面,绝缘层不要接触端子。
L=1~3mm为宜。
图2.2
导线与导线的连接以绕焊为主,操作步骤如下:
a.去掉导线端部一定长度的绝缘皮;b.给导线端头上锡,并穿上合适的套管;c.绞合两条导线,施焊;d.趁热套上套管,冷却后套管固定在接头处。
网绕时导线要紧贴接点,不要出现间隙;多股导线在网绕时,不许散股,以避免焊接时出现尖刺;导线的收头不能露在焊接点的外面,要向内收紧。
2)钩焊(用于强度低于绕焊,但操作方便)。
将导线弯成钩形在接线端子上,用钳子夹紧后再焊接,如图2.3所示。
其端头的处理方法与绕焊相同。
3)搭焊(连接方便,强度及可靠性较差,不适用于正规产品中的导线焊接)。
把经过镀锡的导线搭到接线端子上施焊,如图2.4所示。
图2.3图2.4
4)插焊。
插焊常用在如针对有线话筒内插针与开关导线的连接等地方。
2.4元器件的焊接及加工准备
1)元器件装配和焊前准备。
为保证产品质量,在印制电路板上进行元器件装配时,必须严格遵守操作规程。
正常的元器件装配需要有以下流程:
元器件检测、老化帅选、元器件成型(使得元器件的引脚和印制电路板上对应孔距相配合)、元器件插装、焊接和成品调试等。
绝大多数元器件出厂前引脚已做镀层处理,这样的元器件不必再刮脚,可直接插焊。
若元器件引脚和裸露导线的表面有杂质、易氧化,并有明显污垢,一般需用小刀或断锯条等锋利工具,将引脚认真刮净、烫锡。
但注意不要把引线、导线等弄断,也不要把原来的图层刮掉。
①元器件的引脚成型。
板装工艺中的元器件插孔时根据元器件的封装形式(如形状、尺寸等)和电气规则来安排的,在元器件插装时应做一些适当调整。
大规模生产时,元器件成型多采用成型模具。
平常的一般整机产品板装中,可以用尖嘴钳或镊子成型。
如下图所示为元器件的成型示意图。
基本原则:
引线成型后,元器件体不应破裂,表面封装不应损坏,引线弯曲部分不允许出现模印(专用磨具造成)、压痕和裂痕。
而在手工成型过程中任何弯曲处应有一定的弧度,不许出现直角,否则会使得折弯处的导线截面积变小,时电气特性变差。
标准规定:
引线弯折处距元器件引脚根部距离大于2mm,引脚弯曲半径r应大于引脚直径的两倍,如下图(b)时在元器件和插孔不符的情况时采用的一种方法,这种做法一般是在维修或自己制作时采用,正规产品不能出现。
下图(c)适用于焊接时对热敏感、易损的元器件,如晶体管等。
如下图(d)时元器件立式插装的成型方法,一般在电路板元器件密集度较高时采用,要求h、A均大于2mm,r大于元器件直径。
下图(e)时集成电路成型方法,A大于5mm。
②元器件的插装和排列
a.插装。
元器件的插装一般有卧式和立式。
电阻器、轴向电容器、半导体二极管常采用卧式插装。
板装工艺中,应根据元器件的散热要求,适当地调整元器件离板面间隙。
一般情况下,功率越大的间隙越大。
图2.5
b.排列。
为便于检验员或维修人员目视,要求元器件体有数据字符的面向上或向外,且要求位置上下、水平、垂直对称。
同一类元器件应高低一致。
一般的单面板的插孔只具有水平和垂直方向,那样只要给每个面指定一个排列方向即可。
③元器件插装后的引脚处理。
引脚不同处理会使得焊接所能过承受的机械强度不同。
2)大的发热器件焊接时离开板子;大功率器件焊接时必须悬空,小器件不能悬空。
焊接大电容时,必须卧倒紧固;较大的电容是用散热板或弹性夹固定在电路板上。
3印制电路板的基本设计方法
3.1选择敷铜板
1)选择板材主要依据是:
电路中有无发热元器件(大功率元器件)及电路的工作频率;结构要求印制电路板在电路中的放置方式(垂直或水平)及板上有无质量较重的器件;是否工作在潮湿、高温的环境中。
2)在选择板的厚度时,主要依据印制板尺寸和所选元器件的重量及使用条件等因素确定。
例如,印制板连接采用直接式插座连接时,板厚一般选1.5mm。
3)印制板的形状通常与整机外形有关,一般采用长宽比例不太悬殊的长方形,可简化成型加工。
印制板尺寸的确定要考虑到整机内部结构和板上元器件数量,尺寸及安装方式,板上元器件的排列彼此间应留存一定的间隙,尤其在高压电路中,要注意留存足够的间距。
4)在考虑元器件所占面积时,要注意发热元件需安装散热板的尺寸,在确定印制板的净面积后,还应向外扩出5~10mm(单边)物理距离,以便于印制板在整机安装中固定。
3.2选择对外连接的方式
印制板的对外焊接导线的焊盘应尽可能在印制板边缘,并按统一尺寸排列,以利于焊接与维修;为提供导线与板上焊盘的机械强度,引线应通过印制板上的穿线孔,再从印制板的元器件面穿过焊盘;将导线排列或困扎整齐,通过线卡或其他紧固件将导线与印制板固定,避免导线移动而折断。
印制板间的互连或印制板与其他部件的互连,可采用插头座、转接器或跨接导线等形式,一般采用插头座互连和导线互连的方法
1)插接器互连。
印制板电路的互连,可采用簧片式插头、插座和针孔式插头、插座连接方式进行。
2)导线互连。
采用导线互连时,为加强互连导线在印制板上连接的可靠性,印制板上一般设有专用的穿线孔,导线从被焊点的背面穿入穿线孔。
采用屏蔽线做互连导线时,其穿线方法与一般互连导线走线相同,但屏蔽线不能与其他导线一起走线,避免互相干扰,屏蔽导线与印制板的互连如下图所示。
图3.1
4PCB印制电路板的布局规则
4.1元器件的布局
元器件在印制板上布局时,要根据元器件确定印制板的尺寸。
在确定PCB尺寸后,在确定特殊元器件的位置。
最后,根据电路的功能单元,对电路的全部元器件进行布局。
1)元器件的布局原则
1元器件在整个面板上布局均匀,疏密一致,元器件不要占满板面,四周留有物理边距,便于安装固定。
2通常情况下,所有元器件均匀布置在印制板的一面,每个引脚单独占用一个焊盘。
3元器件的布设不可上下交叉,相邻元器件之间保持一定的间距,不得过小或碰接。
4元器件安装高度应尽量低,以提高稳定性和防止相邻元器件碰接。
5元器件两端跨距应稍大于其轴向尺寸,弯管脚应留出一定的距离,防止齐根弯曲损坏元件。
2)特殊元器件的布局原则
1高频元器件之间的连线应尽可能缩短,以减少他们的分布参数和相互间的电磁干扰,易受干扰的元器件之间不能距离太近。
2对某些电位差较大的元器件或导线,应加大他们之间的距离,以免放电导致意外短路。
带高压的元器件应尽量布置在调试时手不易触及的地方。
3重量较大的元器件,安装时应加支架固定,或应装在整机的机箱底板上。
对一些发热元器件应考虑散热方法,热敏元件应远离发热元器件。
4对可调元器件的布局应考虑整机的结构要求,其位置布设应方便调整。
5在印制板上应留出定位孔及固定支架所占用的位置。
3)全部元器件的布局原则
①按照电路的流程安排合格功能电路单元的位置,使布局便于信流通,并使信号尽可能保持方向一致。
②以每个功能电路的核心元器件为中心,围绕他来进行布局。
③在高频下工作的电路,要考虑元器件之间的分布参数。
4.2元器件排列方式
元器件在印刷板上的排列方式分为不规则和规则两种方式。
1)不规则排列:
一般元器件以立式固定为主,元器件排列无一定规则。
虽然看起来杂乱无章,但印制导线布线方便,元器件间连接线短而少,这样线路板的分布参数减少,抑制干扰能力强,特别适用于高频电路设计。
2)规则排列:
元器件排列方向一致,轴线方向与印制板四边平行或垂直。
一般元器件以卧式固定为主,这种排列整齐,常用于板面较大、元器件种类相对较少而数量较多的低频电路中。
4.3印制导线布线的原则
1)地线和电源线尽量布宽一些。
2)印制导线的拐弯处一般取圆弧形,另可加包络线和“补泪滴”(在焊盘和过孔与走线相连的位置上增大线径,由于连接的形状像水滴,这种操作哟普称“补泪滴”),这样焊盘和导线的附着力强,可提高焊盘、过孔与网络的连接的可靠性和抗干扰能力。
3)高频电路应采用岛型焊盘,并采用大面积接地布线,如图4.1所示。
图4.1
4)当双面板布线时,同一层面上的导线方向尽量一致,保持水平方向或者垂直方向;双面的导线宜相互垂直、斜交或弯曲走线,避免相互平行,以减少寄生耦合。
两个层面的导线连接必须通过过孔。
5)电路中输入及输出印制导线应尽量避免相邻平行,最好加线间地线,以免发生反馈耦合。
6)充分考虑可能产生的干扰,并同时采取相应的抑制措施。
7)印制板导线的宽度要满足电流的要求且布线应尽可能短,在高频电路中更应如此。
导线的最小宽度主要由导线与绝缘基板间的黏附强度和流过它们的电流所决定。
一般导线的宽度可取0.3~1.5mm。
电源线、接地线一般取1.5~2mm,线间最小间隙距离大于0.3mm,一般宽度与间隙大于1mm。
对于集成电路,尤其是数字电路,通常选0.02~0.3mm导线宽度。
根据经验值,当铜箔厚度为0.05mm时,导线宽度的毫米数值等于负载电流的安培数。
4.4印制板的排版设计应考虑的因素
1)地线的干扰及抑制。
产生此类干扰的原因在于两个或两个以上回路共用一端地线。
设计印制板时,应尽量避免不同回路电流流经某一段共同地线。
1并联分路式接地:
如图4.2(a)所示,将印制板上几部分地线分别通过各自地线汇总到线路的总接地点。
公共地线一般都设在印制板的边缘,并较一般导线宽,各级电路就近并连接地。
对低频信号接地线,采用“一点接地”(同级电路的几个接地点要尽量集中)的原则。
2大面积覆盖接地:
如图4.2(b)所示,在高频电路中,可采用扩大印制板的地线面积来减少地线中的感抗,同时对电场干扰起屏蔽作用。
图4.2
3地线的分线:
同一块印制板上,例如,布设模拟电路和数字电路,两种电路地线应完全分开,供电也要分开,以抑制相互干扰。
4印制板地线一般布设最边缘。
高频电路宜采用多点接地,在高频电路中应尽量扩大印制板上的底线面积,这样可以有效减少地线的阻抗。
2)电源干扰的抑制。
布线时,交直流回路不能彼此相连,电源线不要平行、大环行走线;电源线与信号线不要走进,且避免平行。
3)磁场干扰的抑制。
布设时,尽量减少磁力线对印制导线的切割;应使两磁性元件磁场相互垂直,以减少相互耦合;对干扰源进行磁屏蔽,屏蔽罩应良好接地。
4)热干扰抑制。
布局时,电源变压器、功率器件、大功率件、大功率电阻等发热元器件(即热源)应留有安排其散热的位置,尽量把他们散开安置;怕热及温度敏感元器件应远离热源,并加装散热片屏蔽。
为提高电子设备的性能和可靠性,在电子设备结构设计时,必须对设备和元器件的热特性进行分析和讨论,采取各种结构措施控制电子设备的温度。
4.5印制板组装件保护涂覆准则及典型工艺技术介绍
1)准则
印制板组装件(简称印制板)的保护涂覆目的是使印制板电路板在工作或贮存期间,能抵御恶劣环境对电路和元器件的影响,由于元器件通过涂层与底板粘接而增加机械强度和可靠性能。
达到长期防潮、防霉、防盐雾侵蚀的作用。
并能防止由于温度周边所引起的“凝露”使印制导线或焊点间漏导增加,短路甚至击穿。
对于高电压的印制电路导线或在低气压下工作的印制电路组件进行保护涂覆后,可以有效地避免导线之间爬电、击穿现象,从而提高产品的可靠性。
工作在湿热条件下的PCB板,必须选用高性能的基板材料(例如FR-4)在进行保护涂覆。
2)典型工艺技术
①工艺过程
准备→清洗→保护→驱潮→涂覆→滴漆→检查→聚合→检验
②清洗工艺
【污染物】清洗实际上示一种去污染的工艺,污染物及其类型。
焊接后,基板表面留下的各种残留物,一般可分为三类:
粒状物、非极性和极性物,必须彻底清洗干净,目的是防止由于电子迁移而导致电路损坏。
表4.1各种污染物对PCB组装板的影响。
表4.1各种污染物对PCB组装板的影响
污染物
对PCB影响
极性物或离子型(氯化物、活化剂)
降低绝缘电阻,漏导电阻,元件或电路板被腐蚀,吸湿性增加
非极性物或非离子型(松香、油脂)
外观差,可通过尘埃吸附极性污染物或保护涂覆层粘接力差,粉化
【选择溶剂的主要因素】
非极性污染物和极性污染物的清洗分别用极性溶剂和非极性溶剂清洗。
溶剂的选择包括下列因素:
使用的经济性;底板元件的兼容性;操作性;安全性(无毒、不燃、不爆);环境兼容性;污染物容量;表面张力;斑痕特性等因素;污染物和溶剂的一般分类见表4.2:
表4.2污染物和溶剂的一般分类
污染物
溶剂
极性污染物(离子型)
极性溶剂水或乙醇
非极性或非离子型污染物
*非容性溶剂1.1.1-三氯乙烷
*属禁用范围
大多数的污染物都是极性和非极性物质的混合物,为了保证将其完全除去,需采用极性与非极性溶剂配成的共沸夜,共沸(恒沸)的含义是沸腾时组成不变,共沸物时两种或多种溶剂的混合物,它能表现出单一溶液的特性,有一个固定的沸点,但沸点比组成物中任何一个都低,因此,共沸物的组分不能用蒸馏的方法分离。
在清洗机使用过程中,其蒸气也用做清洗介质。
最常使用的F113中加有2.8%~6.1%的乙醇,使组成中非极性和极性溶液,还加有少量(0.2%)稳定剂如硝基甲烷等以防止金属表面腐蚀。
清洗剂的组成有众多的商品编号,但基本组成大同小异,醇类中主要选用甲醇,乙醇和异丙醇,用于除去离子型污物。
保护工艺
凡不准涂漆的部位,都需要局部保护,通常局部保护的器件图纸上应标明;或电路设计师面授,并应写在图纸上,而另一些器件则属操作者应掌握的。
例如印制插头,微调磁芯,微调电容,电位器等凡不准涂覆的部位,必须保证不涂上漆。
5接线工艺
5.1配线
1)线径的测量——千分尺;
2)工作电流
线的容量选取20A/mm2,线的冗余为15%~20%;计算公式如下所述:
导线的线芯截面大小由流过的电流大小决定,并考虑环境温度和导线绝缘层的耐热程度。
一般整机选用的绝缘导线的电流密度为2~3A/mm²,最大为5A/mm²,敞开在机内的无绝缘敷层的裸铜线印制导线的电流密度20A/mm²。
电流密度确定后,工作电流越大,芯线的截面也越大。
电流密度与截面的关系式为
式中:
d—线芯直径(mm);J—电流密度(A/mm²);I—工作电流(A)
根据家用电子产品的安全要求,电网电源导线的线芯截面积应不小于0.75mm²,保证在正常工作条件或短路故障条件下,不会发生导线过热而破坏绝缘层的现象。
3)连接线的颜色要丰富,便于区别、装配和维修。
5.2布线原则
1)不同用途的、不同电位的连接线不要扎到一起,应相隔一定距离,或相互垂直交叉走线,以避免和减少相互干扰。
2)连接线要尽量缩短,使分布电感和分布电容减至最小,尽量减小或避免产生导线间的相互干扰和寄生耦合。
高频高压的连接线更应该注意此问题。
3)电路中同时存在的高低频率不同性质的电路或交直流反馈电路的复杂情况时,电路的接地线要尽量短而粗,且接地线要按照就近接地的原则,本级电路的接地要尽量在一起。
5.3布线方法
1)对于板内飞线敷设尽量紧贴底板,以利于固定;
2)对于两根以上且长度超过10cm相互靠近的平行导线在不影响电性能的情况下,可以整理成束,并用线夹固定;
3)对于高压连接线和流过高频电流的导线,应在连接线上套一个支撑环或把导线支撑的塑料支柱上架空布线,并进行隔离。
5.4布线顺序
从左到右、从上到下、从纵深到外围、从板内到板外。
6机械结构工艺
6.1防止连接松动的几项措施
1)摩擦放松
1对顶螺母
结构简单、适用于平稳、低速重载的固定装置上的连接,一般在机箱连接线板上用的较多,如图6.1所示;
2弹簧垫圈
结构简单、使用方便,冲击、振动工作条件下放松效果较差,常用于紧固部位为金属的元器件,如图6.2所示;
3自锁螺母
结构简单,放松可靠,可多次装拆而不降低放松性能,如图6.3所示。
图6.1图6.2图6.3
4橡皮垫圈起止动作用。
5靠加弹簧垫圈同时在螺孔内涂紧固漆起止动作用。
6靠加弹簧垫圈及在露出的螺钉上涂漆来止动的,涂漆处不少于螺钉半周及两个螺纹高度。
这种方法在一般安装件上常用。
2)机械放松
1(适用于较大冲击、振动的高速机械中运动部件的连接,多用于有特殊要求器件的大螺母上,如图6.4所示;
2止动垫圈(结构简单,使用方便,放松可靠)如图6.5所示;
3串联钢丝(适用于螺钉组连接,放松可靠,但拆装不便)如图6.6所示。
图6.4图6.5图6.6
6.2紧固件的安装
1)为了统一螺丝的紧固松紧程度,采用力矩扳手;
2)设计时,螺丝的大小尽量选取标准件;
3)弹簧垫圈应压平,无开裂;螺钉凸出螺母的长度为2~3扣为宜。
6.3胶接的基本工艺
1)胶接件胶接表面的制备
胶接表面一般需要经过除油处理、机械处理及化学处理,以便清除表面油污及氧化层,改造表面粗糙度,使其达到最佳交接表面状态。
表面粗糙度Ra一般应为3.2~1.6,过高或过低都会降低胶接的强度。
2)胶粘剂配备
因大多数胶粘剂是“多组分”的,在使用前应按规定的程序及正确的配方比例妥善配制作。
3)涂胶
采取适当的方法涂布胶粘剂(如喷涂、刷涂、滚涂、浸渍、贴膜等),以保证厚薄合适、均匀无缺、无气泡。
4)清理
在涂胶装配后,清除胶接件上多余的胶粘剂。
5)固化
根据胶接件的使用要求、接头形式、接头面积等,恰当选定固化条件(温度、压力及保持时间),使胶接域固化。
6)质量检验
7
参考文献
[1]赵静月.变压器制造工艺.北京:
中国电力出版社,2009.
[2]王全保.实用电子变压器材料器件手册.沈阳:
辽宁科学技术出版社,2003.
[3]朱向阳,电子整机装配工艺实训.北京:
电子工业出版社,2007.
[4]王天曦,王豫明.现代电子工艺.北京:
清华大学出版社,2009.
[5]王健石,朱炳林.电子工艺实用技术手册.北京:
中国标准出版社,2010.
[6]濮良贵,纪明刚.机械设计.8版.北京:
高等教育出版社,2006.