自动化仪表与过程控制实验讲义.docx
《自动化仪表与过程控制实验讲义.docx》由会员分享,可在线阅读,更多相关《自动化仪表与过程控制实验讲义.docx(24页珍藏版)》请在冰豆网上搜索。
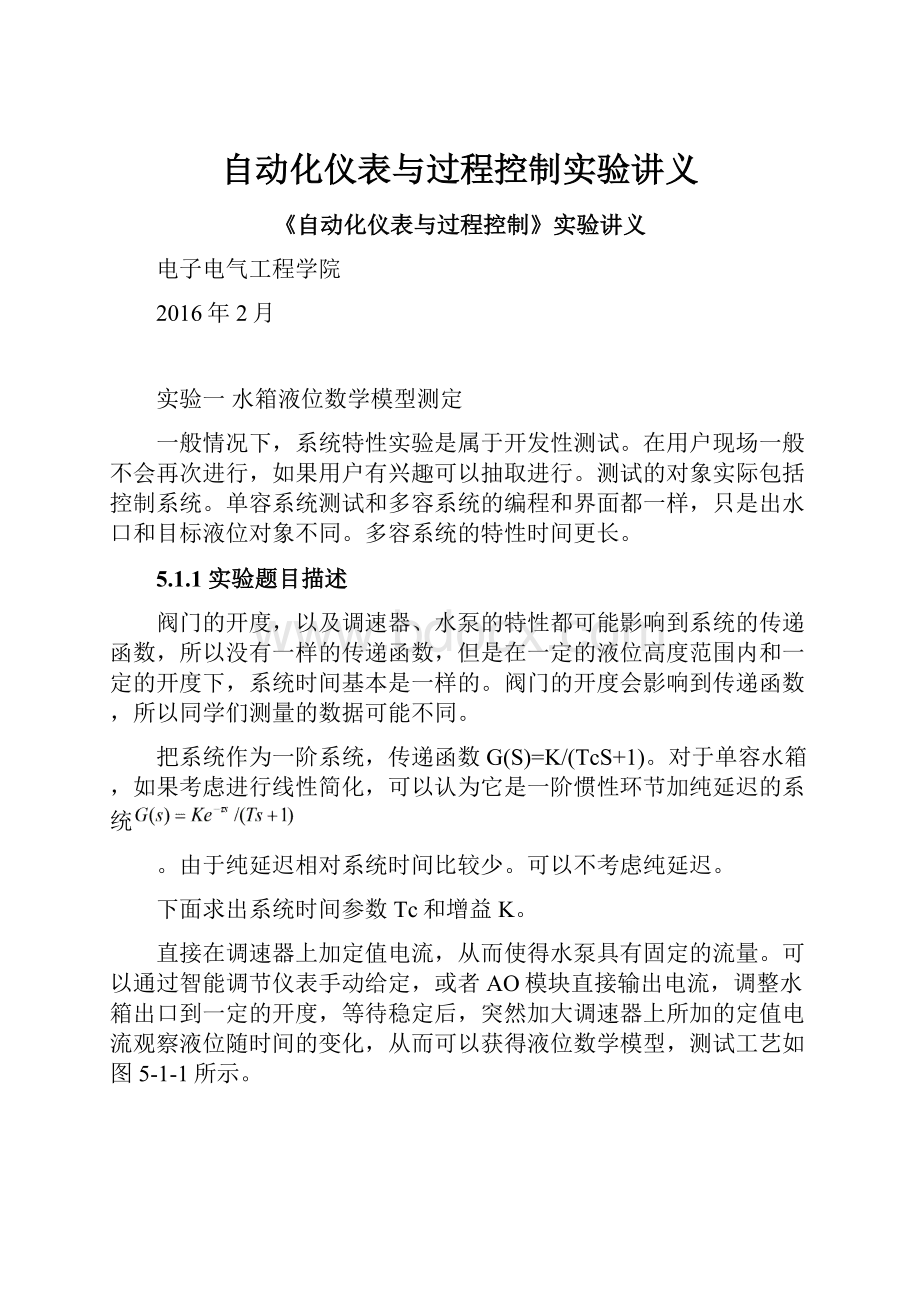
自动化仪表与过程控制实验讲义
《自动化仪表与过程控制》实验讲义
电子电气工程学院
2016年2月
实验一水箱液位数学模型测定
一般情况下,系统特性实验是属于开发性测试。
在用户现场一般不会再次进行,如果用户有兴趣可以抽取进行。
测试的对象实际包括控制系统。
单容系统测试和多容系统的编程和界面都一样,只是出水口和目标液位对象不同。
多容系统的特性时间更长。
5.1.1实验题目描述
阀门的开度,以及调速器、水泵的特性都可能影响到系统的传递函数,所以没有一样的传递函数,但是在一定的液位高度范围内和一定的开度下,系统时间基本是一样的。
阀门的开度会影响到传递函数,所以同学们测量的数据可能不同。
把系统作为一阶系统,传递函数G(S)=K/(TcS+1)。
对于单容水箱,如果考虑进行线性简化,可以认为它是一阶惯性环节加纯延迟的系统
。
由于纯延迟相对系统时间比较少。
可以不考虑纯延迟。
下面求出系统时间参数Tc和增益K。
直接在调速器上加定值电流,从而使得水泵具有固定的流量。
可以通过智能调节仪表手动给定,或者AO模块直接输出电流,调整水箱出口到一定的开度,等待稳定后,突然加大调速器上所加的定值电流观察液位随时间的变化,从而可以获得液位数学模型,测试工艺如图5-1-1所示。
图5-1-1单容液位特性测量流程图
相关理论计算可以参考清华大学出版社1993年出版的《过程控制》,金以慧编著。
实验方案连线如表5-1-1所示。
表5-1-1实验连线
测量或控制量
测量或控制量标号
控制系统端口
水箱液位
LT101
AI0
调速器
U101
AO0
5.1.2实验步骤和数据记录
步骤如下:
1、JV12全开,JV16打开45度左右(由于开度不同,特性也有差异),其余阀门关闭。
2、将LT101连到AI0输入端,AO0输出端连到U101(手动输出)。
3、工艺对象上电,控制系统上电,调速器U101上电,启动P101。
4、启动组态软件,设定U101控制40%,等待系统稳定。
液位和流量稳定在某个值。
注意观察液面,不能太低,否则不算稳定。
5、设定U101控制45%,记录水位随时间的数据,到新的稳定点或接近稳定。
如果阶越太大,可能导致溢出。
6、抓图,修改U101控制量,然后获得一个新的稳定曲线。
7、可以修改JV16开度,重复4和6步。
8、关闭系统,分析数据。
5.1.3实验结果
单容水箱水位阶跃响应曲线,如图5-1-2所示。
图5-1-2单容测试飞升特性曲线
传递函数G(S)=K/(TcS+1)。
控制量从20%上升到25%,液位从27.1%上升到61.2%。
按照63.2%变动,则从54.6%高度画线。
从开始变化到70.6%变动范围时间Tc就是178秒。
增益K=(70.6-27.1)/(25-20)=8.7
传递函数G(S)=8.7/(178S+1)。
实验二液位PID单回路控制
同样的程序和界面,可以用于单容、水平双容、垂直双容和水平三容的液位控制。
只是管路有所不同,目标液位不同,我们选择单容来进行描述。
5.2.1实验题目描述
单容水箱液位PID控制流程图如图5-2-1所示,采用右边支路进行实验,左边支路也是一样的。
图5-2-1单容水箱液位调速器PID单回路控制
测点清单如表5-2-1所示。
表5-2-1单容水箱液位调速器PID单回路控制测点清单
序号
位号
设备名称
用途
原始信号类型
工程量
1
U101
电动调速器
阀位控制
2~10VDC
AO
0~100%
2
LT103
压力变送器
水箱液位
4~20mADC
AI
3.5kPa
水介质由泵P102从水箱V4中加压获得压头,经由调速器U101进入水箱V3,通过手阀JV26回流至水箱V4而形成水循环;其中,水箱V3的液位由LT103测得,用调节手阀JV26的开启程度来模拟负载的大小。
本例为定值自动调节系统,U101为操纵变量,LT103为被控变量,采用PID调节来完成。
5.2.2操作步骤和调试
1、编写控制器算法程序,下装调试;编写实验组态工程,连接控制器,进行联合调试。
2、在现场系统上,打开手阀JV22,调节JV26开度(如果你希望控制量范围50-70%,则要开很大,否则开少一些),其余阀门关闭。
3、在控制系统上,将IO面板的水箱液位输出连接到AI0,IO面板的电动调速器控制端连到AO0。
注意:
具体哪个通道连接指定的传感器和执行器依赖于控制器编程。
对于全连好线的系统,例如DCS,则必须按照已经接线的通道来编程。
4、打开设备电源。
5、启动计算机组态软件,进入实验项目界面。
启动调节器,设置各项参数。
启动右边水泵P102和调速器。
6、系统稳定后可将调节器的手动控制切换到自动控制
7、设置比例参数。
观察计算机显示屏上的曲线,待被调参数基本稳定于给定值后,可以开始加干扰实验。
8、待系统稳定后,对系统加扰动信号(在纯比例的基础上加扰动,一般可通过改变设定值实现,也可以通过支路1增加干扰,或者临时改变一下出口闸板的高度)。
记录曲线在经过几次波动稳定下来后,系统有稳态误差,并记录余差大小。
9、减小P重复步骤6,观察过渡过程曲线,并记录余差大小。
10、增大P重复步骤6,观察过渡过程曲线,并记录余差大小。
11、选择合适的P,可以得到较满意的过渡过程曲线。
改变设定值(如设定值由50%变为60%),同样可以得到一条过渡过程曲线。
注意:
每当做完一次实验后,必须待系统稳定后再做另一次实验。
12、在比例调节实验的基础上,加入积分作用,即在界面上设置I参数不是特别大的数。
固定比例P值(中等大小),改变PI调节器的积分时间常数值Ti,然后观察加阶跃扰动后被调量的输出波形,并记录不同Ti值时的超调量σp。
13、固定I于某一中间值,然后改变P的大小,观察加扰动后被调量输出的动态波形,据此列表记录不同值Ti下的超调量σp。
14、选择合适的P和Ti值,使系统对阶跃输入扰动的输出响应为一条较满意的过渡过程曲线。
此曲线可通过改变设定值(如设定值由50%变为60%)来获得。
15、在PI调节器控制实验的基础上,再引入适量的微分作用,即把软件界面上设置D参数,然后加上与前面调节时幅值完全相等的扰动,记录系统被控制量响应的动态曲线。
15、选择合适的P、Ti和Td,使系统的输出响应为一条较满意的过渡过程曲线(阶跃输入可由给定值从突变10%左右来实现)。
5.2.3实验结果
测试结果如图5-2-2和如图5-2-3所示。
由于手阀的开度不同,有不同的控制情况,所以各个用户的测试数据不一定相同。
图5-2-2单容水箱液位调速器PID单回路控制曲线1
图5-2-3单容水箱液位调速器PID单回路控制曲线2
实验三流量PID单回路控制
5.3.1实验题目描述
流量调速器控制流程图如图5-3-1所示。
采用右边支路进行实验,左边支路也是一样的。
图5-3-1流量调速器PID单回路控制
测点清单如表5-3-1所示。
表5-3-1流量调速器PID单回路控制测点清单
序号
位号
设备名称
用途
原始信号类型
工程量
1
FT102
电磁流量计
给水流量
4~20mADC
AI
0~3m3/h
2
U101
电动调速器
阀位反馈
2~10VDC
AO
0~100%
水介质由泵P102从水箱V4中加压获得压头,经由流量计FT102、调速器U101进入水箱V3,通过手阀JV26回流至水箱V4而形成水循环;其中,给水流量由FT102测得。
本例为定值自动调节系统,U101为操纵变量,FT102为被控变量,采用PID调节来完成。
上位组态,实验要求的组态流程图界面(要求复显),如图5-3-2所示。
图5-3-2组态流程图界面
组态控制点清单如表5-3-2所示。
表5-3-2组态控制点清单
名称
描述
数据格式
控制器中对应变量
U101
流量控制,PID百分比输出
FLOAT
PD9:
0.CVP
FT102
流量信号
FLOAT
F8:
0
SP
调速器设定值
FLOAT
F8:
10
P
PID比例
FLOAT
PD9:
0.KC
I
PID积分
FLOAT
PD9:
0.Ti
D
PID微分
FLOAT
PD9:
0.Ti
手/自动
手自动切换
BYTE
PD9:
0.AM
调速器输出
调节器手动状态下,点击则弹出输入对话框(改变调节器输出值),自动状态跟随调节器输出值。
FLOAT
PD9:
0.CVP
5.3.2操作步骤和调试
1、编写控制器算法程序,下装调试;编写实验组态工程,连接控制器,进行联合调试。
2、在现场系统上,将手阀JV22,JV26完全打开,其余阀门关闭。
水箱容器只是作为水介质流通回路的一个部分。
3、在控制机柜上,把IO面板的FT102流量计信号端子通过实验连接线连到AI0端,面板上的U101调速器控制端连接到控制器AO0端。
注意:
具体哪个通道连接指定的传感器和执行器依赖于控制器编程。
对于全连好线的系统,例如DCS,则必须按照已经接线的通道来编程。
4、打开设备电源,包括调速器,流量计电源。
接通水泵P102电源。
5、连接好控制系统和监控计算机之间的通讯电缆,启动控制系统。
6、启动计算机,启动组态软件,进入实验项目界面。
7、启动调节器,设置到手动状态,把输出值设定到比较大的状态,同时检测流量计的流量测量。
经过1分钟后,流量计测量准确后开始实验。
8、把调节器切换到自动控制。
9、设置PID控制器参数,可以使用各种经验法来整定参数。
5.3.3实验结果及记录
参考的控制曲线如图5-3-3所示。
图5-3-3调速器流量控制曲线
曲线中PI参数设定如下P=2,I=20,小数值D的影响不大。
实验四压力PID单回路控制
5.4.1实验题目描述
压力调速器控制流程图如图5-4-1所示,采用右边支路进行实验,左边支路也是一样的。
图5-4-1压力调速器PID单回路控制
测点清单如表5-4-1所示。
表5-4-1压力调速器PID单回路控制测点清单
序号
位号
设备名称
用途
原始信号类型
工程量
1
PT102
压力变送器
给水压力
4~20mADC
AI
150kPa
2
U101
电动调速器
调速器控制
2~10VDC
AO
0~100%
水介质由泵P102从水箱V4中加压获得压头,经由调速器U101进入水箱V3,通过手阀JV26回流至水箱V4而形成水循环;其中,给水压力由PT102测得。
本例为定值自动调节系统,U101为操纵变量,PT101为被控变量,采用PID调节来完成。
位组态要求,实验要求的组态流程图界面如图5-4-2所示。
图5-4-2组态流程图界面
组态控制点清单如表5-4-2所示。
表5-4-2组态控制点清单
名称
描述
数据格式
控制器中对应变量
U101
流量控制,PID百分比输出
FLOAT
PD9:
0.CVP
PT102
压力信号
FLOAT
F8:
0
SP
调速器设定值
FLOAT
F8:
10
P
PID比例
FLOAT
PD9:
0.KC
I
PID积分
FLOAT
PD9:
0.Ti
D
PID微分
FLOAT
PD9:
0.Td
手/自动
手自动切换
BYTE
PD9:
0.AM
调速器输出
调节器手动状态下,点击则弹出输入对话框(改变调节器输出值),自动状态跟随调节器输出值。
FLOAT
PD9:
0.CVP
5.4.2操作步骤和调试
1、编写控制器算法程序,下装调试;编写实验组态工程,连接控制器,进行联合调试。
2、在现场系统上,将手阀JV22,JV26完全打开,其余阀门关闭。
水箱容器只作为水介质流通回路的一个部分。
调速器打开一半。
3、在控制机柜上,把IO面板的管道压力(PT102)信号端子通过实验连接线连到AI0端,面板上的调速器(U101)控制端连接到控制器AO0端。
4、打开设备电源,包括调速器电源。
5、连接好控制系统和监控计算机之间的通讯电缆,启动控制系统。
6、启动计算机,启动组态软件,进入实验项目界面。
7、启动水泵P102电源。
8、启动调节器,把调节器切换到自动控制。
注意:
控制器必须是正作用的,因为要想压力增加,必须减少调速器开度,而不是增加调速器开度。
9、设置PID控制器参数,可以使用各种经验法来整定参数。
5.4.3实验结果及记录
参考的控制曲线如图5-4-3所示。
给定值跳变到60%,操作值逐步下降,控制量快速跟踪到给定值,没有什么超调量。
图6.4.3调速器压力控制曲线
实验五液位和进口流量串级控制实验
5.6.1实验题目描述
液位和进口流量串级控制流程图如图5-6-1所示。
采用右边支路进行实验,左边支路也是一样的。
图5-6-1液位和进口流量串级控制流程图
液位和进口流量串级控制测点清单如表5-6-1所示。
表5-6-1液位和进口流量串级控制测点清单
序号
位号
设备名称
用途
原始信号类型
工程量
1
FT102
2#流量计
管路2流量
4~20mADC
AI
0-3m3/h
2
LT103
V3液位
测量液位
4~20mADC
AI
0-3.5kPa
3
U101
调速器
控制流量
2~10VDC
AO
0~100%
水介质由泵P102从水箱V4中加压获得压头,经流量计FT102、电动阀U101、水箱V3、手阀JV26回流至水箱V4而形成水循环,负荷的大小通过手阀JV26来调节;其中,水箱V3的液位由液位变送器LT103测得,给水流量由流量计FT101测得。
本例为串级调节系统,调速器U101为操纵变量,以FT102为被控变量的流量控制系统作为副调节回路,其设定值来自主调节回路―以LT103为被控变量的液位控制系统。
以FT102为被控变量的流量控制系统作为副调节回路―流量变动的时间常数小、时延小,控制通道短,从而可加快提高响应速度,缩短过渡过程时间,符合副回路选择的超前,快速、反应灵敏等要求。
水箱V3为主对象,流量FT102的改变需要经过一定时间才能反应到液位,时间常数比较大,时延大。
由上分析知:
副调节器选纯比例控制,反作用,自动。
主调节器选用比例控制或比例积分控制,反作用,自动。
副回路干扰量通过手阀J21的调节来实现,该阀门直接影响流量,而主回路的干扰可以通过J26来实现,或者直接打开J25一会,再关上。
流程图界面,如图5-6-2所示。
图5-6-2组态流程图界面
组态控制点清单如表5-6-2所示。
表5-6-2组态控制点清单
名称
描述
数据格式
控制器中对应变量
U101
流量控制,PID百分比输出
FLOAT
PD9:
0.CVP
LT103
液位信号
FLOAT
F8:
0
FT101
流量信号
FLOAT
F8:
1
SP
主调节器设定值
FLOAT
F8:
10
P
主调节器比例系数
FLOAT
PD9:
0.KC
副调节器比例系数
FLOAT
PD9:
1.KC
I
主调节器积分系数
FLOAT
PD9:
0.Ti
副调节器积分系数
FLOAT
PD9:
1.Ti
D
主调节器微分系数
FLOAT
PD9:
0.Td
副调节器微分系数
FLOAT
PD9:
1.Td
手/自动
主回路手自动切换
BYTE
PD9:
0.AM
副回路手自动切换
BYTE
PD9:
1.AM
主回路调节器输出
手动状态下可改写
FLOAT
PD9:
0.CVP
主回路调节器输出
手动状态下可改写
FLOAT
PD9:
1.CVP
5.6.2控制算法和编程
串级控制系统方框图如图5-6-3所示。
以串级控制系统来控制水箱液位,以支路流量为副对象,水泵直接向水箱注水,流量变动的时间常数小、时延小,控制通道短,从而可加快提高响应速度,缩短过渡过程时间,符合副回路选择的超前,快速、反应灵敏等要求。
水箱为主对象,流量的改变需要经过一定时间才能反应到液位,时间常数比较大,时延大。
将主调节器的输出送到副调节器的给定,而副调节器的输出控制执行器。
由上分析副调节器选纯比例控制,反作用(要想流量大,则调速器开度加大),自动。
主调节器选用比例控制或比例积分控制,反作用(要想液位高,则调速器开度加大),自动。
5.6.3操作步骤和调试
1、编写控制器算法程序,下装调试;编写实验组态工程,连接控制器,进行联合调试。
2、在现场系统上,打开手动调速器JV22。
调节JV26具有一定开度,其余阀门关闭。
3、在控制系统上,将流量计(FT102)连到控制器AI0输入端,水箱液位(LT103)连到控制器AI1输入端,调速器U101连到控制器AO0端。
4、打开设备电源,包括调速器电源。
5、连接好控制系统和监控计算机之间的通讯电缆,启动控制系统。
6、启动计算机,启动组态软件,进入实验项目界面。
启动调节器,设置各项参数,将调节器切换到自动控制。
7、启动水泵,工频运行水泵P101。
系统开始运行。
8、首先,利用主回路,做一个单回路液位实验。
确定P、I值(D=0)设定一个SP值A1,并记录稳定时的流量计FT101的测量值A2
9、调节JV21从90度变动到50度,并记录系统超调量。
10、将主调节器置手动状态,调整其输出为A2,将A2作为副调节器的SP值。
11、在上述状态下,整定副调节器的P参数。
调整整个系统至稳定(可有余差)
12、再将主调节器切换到自动状态,预置主调节器的P、I参数不变。
系统应仍然稳定。
13、调节JV21从90度变动到50度,并记录系统超调量。
副调节器:
一般纯比例(P)控制,反作用,自动,KC2(副回路的开环增益)较大。
主调节器:
比例积分(PI)控制,反作用,自动,KC1〈KC2(KC1主回路开环增益)。
14、通过反复对副调节器和主调节器参数的调节,使系统具有较满意的动态响应和较高的静态精度。
15、再次通过JV21增加副回路干扰进行测试,记录超调和稳定时间。
16、通过JV26的变动增加主回路干扰,记录超调和稳定时间。
5.6.4实验结果及记录
实验曲线如图5-6-4所示。
图5-6-4液位流量串级控制曲线
实验五水箱液位数学模型测定
一般情况下,系统特性实验是属于开发性测试。
在用户现场一般不会再次进行,如果用户有兴趣可以抽取进行。
测试的对象实际包括控制系统。
单容系统测试和多容系统的编程和界面都一样,只是出水口和目标液位对象不同。
多容系统的特性时间更长。
5.1.1实验题目描述
阀门的开度,以及调速器、水泵的特性都可能影响到系统的传递函数,所以没有一样的传递函数,但是在一定的液位高度范围内和一定的开度下,系统时间基本是一样的。
阀门的开度会影响到传递函数,所以同学们测量的数据可能不同。
把系统作为一阶系统,传递函数G(S)=K/(TcS+1)。
对于单容水箱,如果考虑进行线性简化,可以认为它是一阶惯性环节加纯延迟的系统
。
由于纯延迟相对系统时间比较少。
可以不考虑纯延迟。
下面求出系统时间参数Tc和增益K。
直接在调速器上加定值电流,从而使得水泵具有固定的流量。
可以通过智能调节仪表手动给定,或者AO模块直接输出电流,调整水箱出口到一定的开度,等待稳定后,突然加大调速器上所加的定值电流观察液位随时间的变化,从而可以获得液位数学模型,测试工艺如图5-1-1所示。
图5-1-1单容液位特性测量流程图
相关理论计算可以参考清华大学出版社1993年出版的《过程控制》,金以慧编著。
实验方案连线如表5-1-1所示。
表5-1-1实验连线
测量或控制量
测量或控制量标号
控制系统端口
水箱液位
LT101
AI0
调速器
U101
AO0
5.1.2实验步骤和数据记录
步骤如下:
1、JV12全开,JV16打开45度左右(由于开度不同,特性也有差异),其余阀门关闭。
2、将LT101连到AI0输入端,AO0输出端连到U101(手动输出)。
3、工艺对象上电,控制系统上电,调速器U101上电,启动P101。
4、启动组态软件,设定U101控制40%,等待系统稳定。
液位和流量稳定在某个值。
注意观察液面,不能太低,否则不算稳定。
5、设定U101控制45%,记录水位随时间的数据,到新的稳定点或接近稳定。
如果阶越太大,可能导致溢出。
6、抓图,修改U101控制量,然后获得一个新的稳定曲线。
7、可以修改JV16开度,重复4和6步。
8、关闭系统,分析数据。
5.1.3实验结果
单容水箱水位阶跃响应曲线,如图5-1-2所示。
图5-1-2单容测试飞升特性曲线
传递函数G(S)=K/(TcS+1)。
控制量从20%上升到25%,液位从27.1%上升到61.2%。
按照63.2%变动,则从54.6%高度画线。
从开始变化到70.6%变动范围时间Tc就是178秒。
增益K=(70.6-27.1)/(25-20)=8.7
传递函数G(S)=8.7/(178S+1)。