制造电机定转子铁芯零件的现代冲压技术.doc
《制造电机定转子铁芯零件的现代冲压技术.doc》由会员分享,可在线阅读,更多相关《制造电机定转子铁芯零件的现代冲压技术.doc(8页珍藏版)》请在冰豆网上搜索。
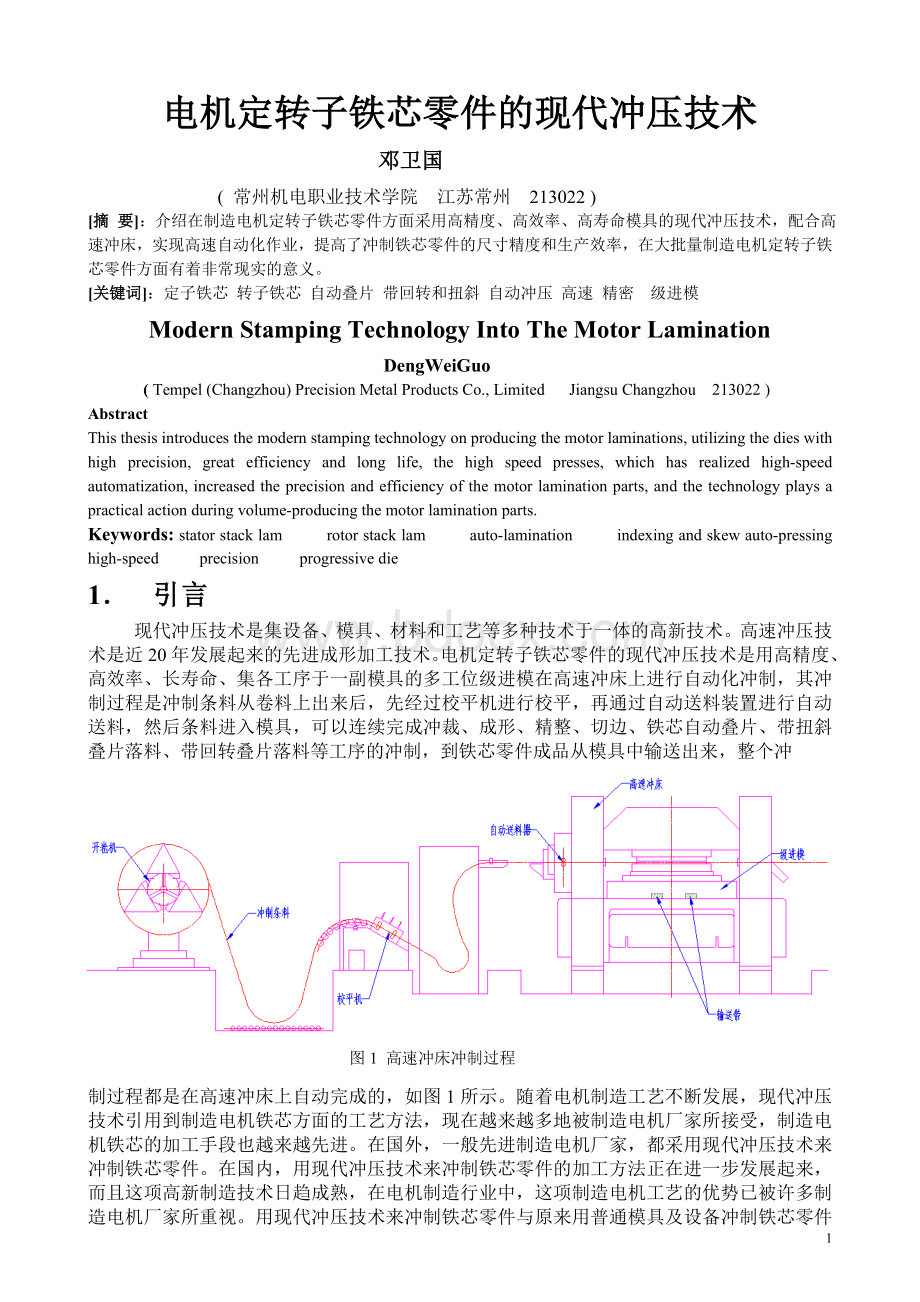
电机定转子铁芯零件的现代冲压技术
邓卫国
(常州机电职业技术学院江苏常州213022)
[摘要]:
介绍在制造电机定转子铁芯零件方面采用高精度、高效率、高寿命模具的现代冲压技术,配合高速冲床,实现高速自动化作业,提高了冲制铁芯零件的尺寸精度和生产效率,在大批量制造电机定转子铁芯零件方面有着非常现实的意义。
[关键词]:
定子铁芯转子铁芯自动叠片带回转和扭斜自动冲压高速精密级进模
ModernStampingTechnologyIntoTheMotorLamination
DengWeiGuo
(Tempel(Changzhou)PrecisionMetalProductsCo.,LimitedJiangsuChangzhou213022)
Abstract
Thisthesisintroducesthemodernstampingtechnologyonproducingthemotorlaminations,utilizingthedieswithhighprecision,greatefficiencyandlonglife,thehighspeedpresses,whichhasrealizedhigh-speedautomatization,increasedtheprecisionandefficiencyofthemotorlaminationparts,andthetechnologyplaysapracticalactionduringvolume-producingthemotorlaminationparts.
Keywords:
statorstacklamrotorstacklamauto-laminationindexingandskewauto-pressinghigh-speedprecisionprogressivedie
1.引言
现代冲压技术是集设备、模具、材料和工艺等多种技术于一体的高新技术。
高速冲压技术是近20年发展起来的先进成形加工技术。
电机定转子铁芯零件的现代冲压技术是用高精度、高效率、长寿命、集各工序于一副模具的多工位级进模在高速冲床上进行自动化冲制,其冲制过程是冲制条料从卷料上出来后,先经过校平机进行校平,再通过自动送料装置进行自动送料,然后条料进入模具,可以连续完成冲裁、成形、精整、切边、铁芯自动叠片、带扭斜叠片落料、带回转叠片落料等工序的冲制,到铁芯零件成品从模具中输送出来,整个冲
图1高速冲床冲制过程
制过程都是在高速冲床上自动完成的,如图1所示。
随着电机制造工艺不断发展,现代冲压技术引用到制造电机铁芯方面的工艺方法,现在越来越多地被制造电机厂家所接受,制造电机铁芯的加工手段也越来越先进。
在国外,一般先进制造电机厂家,都采用现代冲压技术来冲制铁芯零件。
在国内,用现代冲压技术来冲制铁芯零件的加工方法正在进一步发展起来,而且这项高新制造技术日趋成熟,在电机制造行业中,这项制造电机工艺的优势已被许多制造电机厂家所重视。
用现代冲压技术来冲制铁芯零件与原来用普通模具及设备冲制铁芯零件相比较,具有冲制铁芯零件自动化程度高、尺寸精度高、模具使用寿命长等特点,适合于冲制件的大批量生产。
由于多工位级进模是集众多加工工艺于一副模具上的冲制,减少了电机的制造工序过程,提高了制造电机的生产效率。
2.现代高速冲压设备
现代高速冲压的精密模具离不开高速冲床的配合,目前国内外现代冲压技术的发展趋势是单机自动化、机械化、自动送料、自动卸料、自动出成品,高速冲压技术目前在国内外得到了普遍发展。
电机定转子铁芯级进模的冲压速度一般为200~400次/min,多半是在中速冲压范围之内进行工作的。
冲制电机定转子铁芯带自动叠片的精密级进模对高速精密冲床技术要求是,冲床的滑块在下死点精度要求较高,因为影响到定转子冲片在模具內自动叠片形成铁芯过程的质量问题。
现在精密冲压设备正在向着高速度、高精度、稳定性好的方向发展,特别是近年来精密高速冲床发展很快,在提高冲制件生产效率方面发挥了重大的作用。
高速精密冲床在设计结构方面比较先进,制造精度又高,适合于多工位硬质合金级进模的高速冲压,可以大大提高级进模的使用寿命。
级进模所冲制材料是卷料形式,因此现代冲压设备都带有开卷机、矫平机等辅助装置,自动送料装置有:
辊式、凸轮、机械无级调节式、齿轮式、数控无级调节式送料机等结构形式,分别与相适应的现代冲压设备配套使用。
由于现代冲压设备的自动化冲制程度高,且速度快,为充分保证模具在冲制过程中的安全性,现代冲压设备都配备有在发生失误情况下的电气控制系统,如模具在冲制过程中发生故障情况,则失误信号就会立即传送到电气控制系统,电器控制系统就会发出信号使冲床立即停止工作。
目前用于冲制电机定转子铁芯零件方面的现代冲压设备主要有:
日本有:
AIDA高速冲床、DOBBY高速冲床、ISIS高速冲床,美国有:
MINSTER高速冲床,台湾有:
瑛瑜高速冲床等。
这些精密高速冲床,具有高的送料精度、冲压精度和机器的刚度、可靠的机器安全系统,其冲压速度一般多在200~600次/min范围,适合于冲制电机定转子铁芯的自动叠片和带扭斜、回转自动叠铆片的结构零件。
3.电机定转子铁芯的现代冲模技术
3.1电机定转子铁芯级进模概述
在电机行业中,定、转子铁芯是电机上的重要零部件之一,它的质量好坏直接影响到电机的技术性能。
传统制作铁芯方法是用一般普通模具冲制出定、转子冲片(散片),经过齐片,再用铆钉铆接、扣片或氩弧焊等工艺过程制成铁芯,对于交流电机转子铁芯还需用手工进行扭转出斜槽,步进电机要求定、转子铁芯磁性能和厚度方向均匀,定子铁芯和转子铁芯冲片之间分别要求旋转一定的角度,如用传统方法制作,效率低,精度很难达到技术要求。
现在随着高速冲压技术的迅速发展,在电机、电器等领域,已广泛采用高速冲压多工位级进模制造自动叠片式的结构铁芯,其中定、转子铁芯还可以带扭转叠斜槽、冲片之间带大角度回转叠铆结构等,与普通冲模相比,多工位级进模具有冲制精度高、生产效率高、使用寿命长、所冲制铁芯尺寸精度一致性好、容易实现自动化、适合大批量生产等优点,是电机行业精密模具发展的方向。
定、转子自动叠铆级进模具有制造精度高、结构先进、带有技术性要求高的回转机构、计数分离机构及安全机构等,铁芯自动叠铆、转子带扭斜叠铆、大角度回转叠铆的冲制工步都是放在定、转子冲片落料工位上完成的。
级进模上的主要零件凸模、凹模都采用硬质合金材料,每磨一次刃口可冲150万次以上,模具总寿命在1.2亿次以上。
3.2电机定转子铁芯自动叠铆技术
级进模上带自动叠铆技术就是要把原来传统制作铁芯的工艺过程(冲出散片-齐片-铆合)放在一副模具内完成,即在级进模的基础上增加了新的冲压工艺技术,除了冲定、转子上的轴孔、槽孔等冲片形状要求外,增设了定、转子铁芯叠铆需要的叠铆点及起叠铆点分离作用的计数孔的冲压工位,并将原来定、转子的落料工位改变成先起落料作用,然后使各冲片再形成叠铆过程和叠片计数分离过程(以确保铁芯厚度)的叠铆工位,如定、转子铁芯需要带扭转、回转叠铆功能的,在级进模转子或定子落料工位的下模上要带有扭转机构或回转机构,由叠铆点在冲片上不断改变或转动位置而实现这一功能的,从而满足在一副模具内自动完成冲片的叠铆和回转叠铆的技术要求。
3.2.1铁芯自动叠片形成的过程是:
在定、转子冲片适当部位上冲出一定几何形状的叠铆点,叠铆点的形式如图2所示,上部是凹陷形孔,下部是凸起的,然后将同一名义尺寸的上
一冲片凸起部分嵌入到下一冲片的凹陷形孔时,在模具中落料凹模收紧圈内自然形成“过盈”,达到紧固连接的目的,如图3所示。
在模具内铁芯形成的过程是,在冲片落料工位上使上一
片叠铆点的凸起部位正确地与下面一片的叠铆点凹形孔部位重合在一起,当上面一片受到落料凸模压力作用时,下面一片借助其外形与凹模壁摩擦所产生的反作用力使两片产生叠铆。
图2冲片叠铆点结构
图3铁芯自动叠片结构
这样,通过高速自动冲床连续不断的冲制,就可以得到一片挨着一片排列、毛刺是同一方向而且具有一定叠厚的整齐铁芯。
3.2.2铁芯叠片厚度的控制方法是,在铁芯预定的片数时,把最后一片冲片上的叠铆点冲穿,使铁芯按预定的片数分离,如图4所示。
在模具结构上设置有自动叠片计数分离装置,如图5所示。
在计数凸模上面有一个抽板机构,抽板由气缸带动,气缸动作由电磁阀控制,电磁阀根据控制箱发出的指令而动作。
冲床每一次行程信号都输入到控制箱里,当冲到所设定片数时,控制箱会发出信号,通过电磁阀和气缸,使抽板动作,从而使计数凸模达到计数分离的目的,即在冲片的叠铆点上达到计量孔被冲穿和不冲计量孔的目的。
铁芯的叠片厚度可以自行设定。
另外,有的转子铁芯的轴孔因支承结构的需要,要求冲制成有2段或3段台肩沉孔,如图6所示,级进模上要同时完成冲制这种有台肩孔工序要求的铁芯,可采用上述相类似的结构原理,模具结构如图7所示。
图4叠铆铁芯分离情况
图5铁芯叠片计数分离机构
1.气缸、电磁阀2.计数凸模
3.抽板
图6转子铁芯台肩沉孔结构
图7冲制大小轴孔计数分离机构
1.气缸、电磁阀2.计数轴孔凸模
3.抽板4.上下移动凸模垫板
3.2.3铁芯叠铆结构形式有两种:
第一种是密叠式,即叠铆成组的铁芯不需要在模具外再加压,出模即可达到铁芯叠铆的结合力。
第二种是半密叠式,出模时已叠铆的铁芯冲片之间有间隙,还需要再加压才能保证结合力。
3.2.4铁芯叠铆的设置及数量的确定:
铁芯叠铆点位置的选择应根据冲片的几何形状确定,同时考虑到电机的电磁性能及使用要求,模具上应考虑叠铆点的凸模、凹模镶块位置是否有干涉现象及落料凸模相应叠铆顶杆孔位置离边上距离的强度问题。
叠铆点在铁芯上分布应对称和均匀,叠铆点的数量及大小应根据铁芯冲片之间要求的结合力大小来确定,同时必须考虑到模具的制造工艺性。
如铁芯冲片之间带有大角度回转叠铆的,还要考虑叠铆点的等分要求等。
如图8所示。
图8铁芯叠铆点分布图
图10叠铆点过盈量示意图
图9叠铆点几何形状
3.2.5铁芯叠铆点的几何形状有:
(a)圆柱形叠铆点,适用于铁芯的密叠式结构;(b)V型叠铆点,该叠铆点的特点是铁芯冲片之间的连接强度大,适用于铁芯的密叠式结构和半密叠式结构;(c)L型叠铆点,该叠铆点形状一般用于交流电机转子铁芯的扭斜叠铆,适用于铁芯的密叠式结构;(d)梯形叠铆点,该叠铆点有园梯形和长梯形叠铆点结构之分,两者都适用于铁芯的密叠式结构,如图9所示。
3.2.6叠铆点的过盈量:
铁芯叠铆的结合力大小与叠铆点的过盈量有关,如图10所示,叠铆点凸台的外径D与内经d的尺寸差(即过盈量),由冲制叠铆点凸模与凹模的刃口间隙确定,所以选取合适的间隙是保证铁芯叠铆强度以及叠铆难易程度情况的一个重要部分。
3.3电机定转子铁芯自动叠铆的装配方法
3.3.1直接叠铆:
在一副级进模的转子落料或者定子落料工步上,将冲片直接冲入落料凹模之中,当冲片叠压于凹模和凹模下面的收紧圈内时,靠每一冲片上的叠铆凸出部位使各冲片固定在一起。
3.3.2带扭斜叠铆:
铁芯上每一冲片之间要旋转一个小角度再叠铆,这种叠铆方法一般多用于交流电机的转子铁芯上。
其冲制过程是,冲床每冲一次后(即冲片冲入落料凹模之内后),在级进模的转子落料工步上,由转子