四川宜宾长庆电泳涂装线设计说明.docx
《四川宜宾长庆电泳涂装线设计说明.docx》由会员分享,可在线阅读,更多相关《四川宜宾长庆电泳涂装线设计说明.docx(20页珍藏版)》请在冰豆网上搜索。
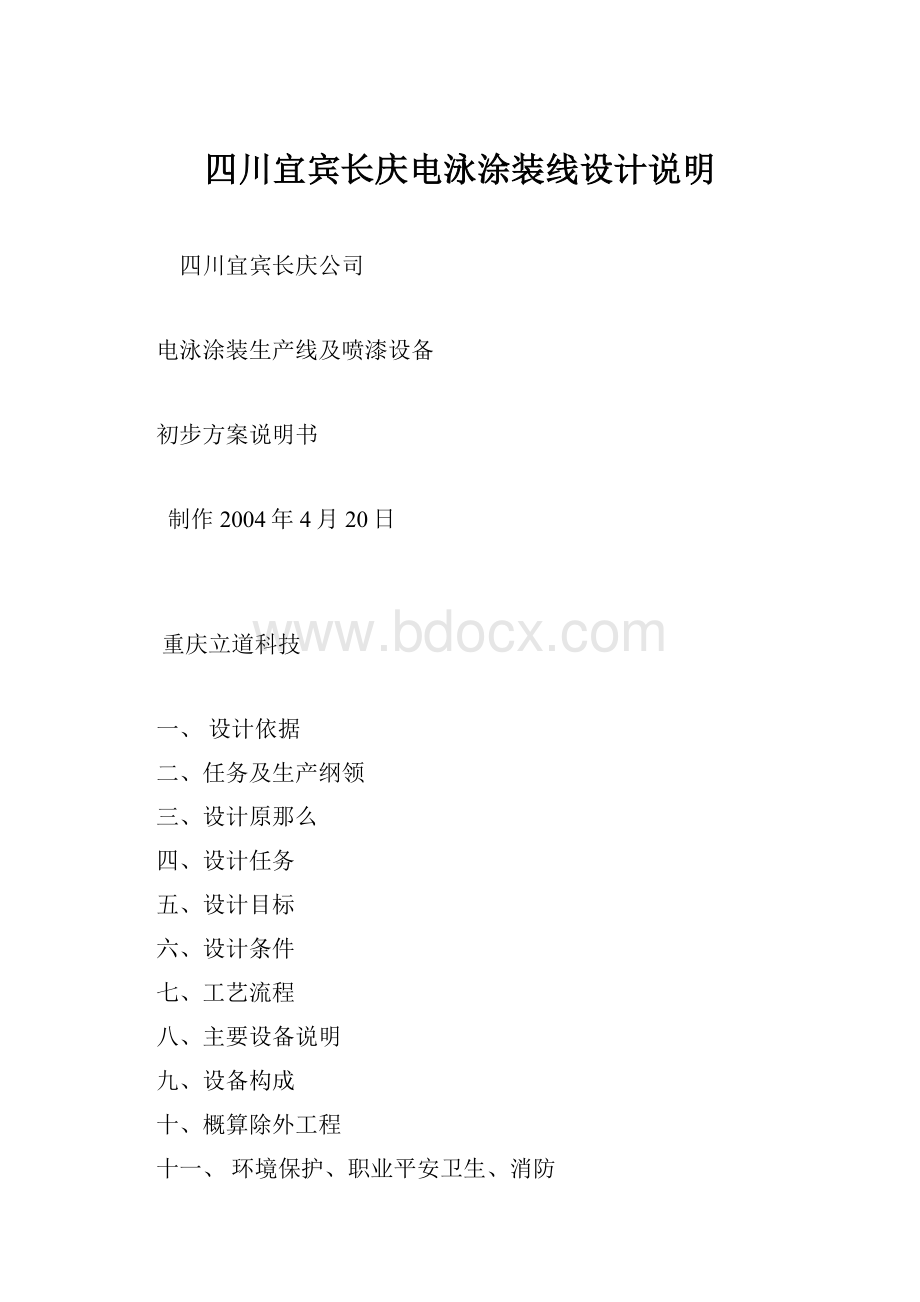
四川宜宾长庆电泳涂装线设计说明
四川宜宾长庆公司
电泳涂装生产线及喷漆设备
初步方案说明书
制作2004年4月20日
重庆立道科技
一、设计依据
二、任务及生产纲领
三、设计原那么
四、设计任务
五、设计目标
六、设计条件
七、工艺流程
八、主要设备说明
九、设备构成
十、概算除外工程
十一、环境保护、职业平安卫生、消防
十二、设计方案图
十三、设备投资概算表
一、设计依据
本规格说明书是我公司根据贵公司的要求,遵循以下原那么设计的。
1.1公司提供的有关的初步设计资料。
1.2公司提出的工艺要求。
1.3涂装作业平安规程。
1.4劳动保护及环境保护相关技术标准。
二、任务及生产纲领
2.1工件:
甲方已定。
2.2生产纲领:
甲方已定。
2.3工件参数:
甲方已定。
2.4工作制度:
甲方已定。
2.5现有能源情况:
2.5.1动力电源:
AC380V±10%三相四线制50Hz。
2.5.2照明电源:
AC220V±10%50Hz。
2.5.3车间设备电容量:
约300KW
2.5.4空气用量:
1m3/min,供气压力≥pa,进入车间的空气不能有油和水。
2.5.5用水量:
2T/h。
2.5.6加热用能源:
采用燃油加热方式。
三、设计原那么
3.1满足产量,保证产品质量,改善劳动环境,提供宽阔明亮的操作空间;
3.2采用成熟先进的工艺形式,方案可靠合理;
3.3主要配套件及电控元件,选用国内知名企业产品;
3.4执行国家在消防平安、环境保护、工业卫生等方面要求。
3.5设备的投资省,运行费用较低,操作维护方便。
3.6环保、劳保、平安设计满足如下要求:
3.6.1“废气、废水〞排放环保要求。
国家现行排放标准GB16297-1996、GB8978-1996。
3.6.2设备的平安符合
GB7692—1987?
涂装作业平安规程-涂漆前处理平安规程?
GB14443—1993?
涂装作业平安规程-涂层烘干室平安技术标准?
四、设计任务
按照产品的特点,采用阴极电泳涂装工艺,遵循设备先进,保证品质的原那么,对零〔部〕件的前处理、阴极电泳、电泳后清洗、电泳漆烘干、喷漆、烘干等工序进展工艺及设备设计。
五、设计目标
本车间系根据贵公司提供的相关参数,在新建车间内布置车轮的前处理、阴极电泳、电泳后清洗、电泳漆烘干、面漆喷涂、烘干及其附属设备,按照保证产品质量和节约投资的原那么,采用及优化目前具先进水平的涂装工艺和涂装设备。
本涂装生产线涂装工序完善,工艺设备先进,完全能满足车轮的涂装要求,在新建车间场地内力求到达物流畅通,设备布置协调、整齐、美观,操作平安、维修方便,其水平可到达同期一样涂装产品的优良品质。
六、设计条件
1
处理物
名 称
尺寸
重量
Max
250Kg/单钩
吊下距离
1100
吊挂尺寸
设计值
1100×450×350mm
2
生产
操作条件
工作日数
306
工作班数
2
工时
16
年时基数
Φ=4896h
工时效率
η=85%
3
动力源规格
电气
动力
AC220/380V1Φ/3Φ50Hz
控制
AC220V1Φ50Hz
照明
AC220V1Φ50Hz
工作指示
AC220V1Φ50Hz
水
工业用水2t/h,纯水0.5t/h
热源
天然气
4
其他
气象条件
气温
设计值
Max:
(车间内)36℃
Min:
(车间内)3℃
厂房
面积
42×10m
梁下高
8.5m
№
项目
数值
备注
1
吊挂间距
平均间距600mm〔T〕
2
当量挂数
3268挂/天
1634挂/班
3
悬链速度计算
4
悬链速度
计算:
2.4m/min
采用:
2.5m/min
5
输送装置
XT通用悬挂输送机
6
产量计算
车轮3268只/天
6.3根本领项
№
项目
内容
1
装置地点
贵公司指定车间内
2
施工期限
照合约期限
3
合约范围
设计、制作、安装、调试
4
动力源配置
各必要位置,请贵厂配合
5
风管工程
各排风管超过屋顶,并与墙保持以上距离
6
电气工程
各必要位置一次侧配置,请贵厂配合
7
设备涂装
设备涂底漆一道,面漆一道,色泽可由贵厂确定
8
安装
工程合约内包含之主体、附件设备的安装
9
调试
工程竣工后,立即进展调试
10
验收
调试完毕,贵厂配合验收
11
保证
验收后一年内,明显为本公司设计或制造上疏忽所致之损坏,由本公司尽免费修复之责
七、工艺流程
在进展多方案分析比较根底上,根据贵公司所提供的初设方案,拟定以下方案设计:
7.1前处理、电泳共线,采用直线龙门式PLC程控自动生产,同时使用计算机作为PLC的上位机〔DMS〕对系统进展控制、监视和记录。
设备运行可靠,除上下件人工操作外,其他主要工序全部自动化进展。
电泳漆烘箱采用步进式输送方式;面漆喷涂及烘箱设备单独摆放,这样可使整个生产线自动化程度提高,占地面积变小,投资省,管理更为方便。
7.2整个前处理、电泳和后清洗过程中,采用浸渍方式,充分考虑工件清洗得更彻底干净的前提下,节省了用电,降低了运行能耗。
7.3烘干室为通过式燃油对流桥式〔或直通式〕烘干室,其运行费用约为电加热的1/3。
7.4本生产线适用全钢件和钢铝复合件的混线生产。
7.5工艺流程表
№
工艺名称
方式
工艺参数
备注
温度℃
时间min
1
上线
手动
2
脱脂
浸渍
60-70
2
3
热水洗1
浸渍
80-90
1.0
4
电解除油
浸渍
60-70
5
5
热水洗2
浸渍
RT
0.8
6
水洗3
浸渍
RT
0.8
7
酸洗
浸渍
RT
3
8
水洗4
浸渍
RT
1
9
水洗5
浸渍
RT
1
建议:
酸洗除锈工序最好不放在线上,以免酸雾污染腐蚀程控行车;可考虑其他的线下除锈方式,如:
喷丸〔砂〕
10
外表调整
浸渍
RT
1.0
11
磷化
浸渍
45
3
12
水洗5
浸渍
RT
1.0
13
水洗6
浸渍
RT
14
纯水洗
浸渍
RT
1.0
15
新鲜纯水洗
喷淋
RT
0.3
16
沥水
17
电泳
浸渍
28±2
3.0
18
#1UF水洗
浸渍
RT
1.0
19
#2UF水洗
浸渍
RT
20
纯水洗
浸渍
RT
0.8
21
新鲜纯水洗
喷淋
RT
0.3
22
沥水
23
烘干
自动
190-210
30
24
冷却
自动
RT
5
25
准备
手动
RT
1-2
26
面漆
手动
RT
2-3
27
流平一
自动
RT
6
28
烘干
自动
150
30
29
冷却下线
手动
RT
八、主要设备说明
8.1电泳及前处理设备〔1套〕:
8.1.1.设备类型:
全密闭通过浸渍式设备。
8.1.2设备组成:
由棚体、供液系统、槽体、喷淋系统、槽液加热系统、排风系统、磷化除渣系统等组成。
8.1.3.设备说明:
8.1.3.1机组为全封闭构造,棚体双侧面设有检修门及平台。
8.1.3.2各加热槽设无油空气搅拌系统,可采用无油汽泵设备实现。
8.1.3.3加热槽侧设抽风装置,设气封防蒸汽溢出。
8.1.3.4各段之间设有过渡段及接水盘,防止工位间液体外溢污染环境。
8.1.3.5纯水喷淋采用立式液下泵,防止泄漏。
8.1.3.6采用夹扣式喷嘴,易撤换,喷射角度可调,喷淋压力设计能力5Mpa。
8.1.3.7采用旁路泄压保证喷淋压力、流量可调,以到达最正确工艺参数。
8.1.3.8同药液槽工位采用水流逆补技术,从而节省用水量,降低废水处理量,减少药量消耗,提高清洗质量。
8.1.3.9脱脂采用蒸汽加热,槽内布置蒸汽列管式换热器。
8.1.3.10磷化采用槽外板式换热器加热,防止结渣,便于清理。
系统包括热水槽、循环泵、蒸汽加热系统、板式换热器,硝酸反冲洗系统及除渣系统设备等。
8.1.3.11硝酸反清洗系统皆为不锈钢材料制造,可定期对板式换热器中所产生的磷化垢进展清洗。
8.1.3.12所有的棚体均采用镀锌钢板制造,棚体侧面设有玻璃观察窗,室内设照明装置。
前处理及后水洗槽体中除纯水、电解除油、磷化槽采用不锈钢材料制造外,其余槽体均采用碳钢板制作,内外表敷设1-2mm厚玻璃钢。
8.1.3.13脱脂、热水洗槽、电解除油槽、磷化槽体均采用岩棉保温,岩棉厚度50mm。
8.1.3.14槽体采用双面焊构造,不得有渗漏现象;
8.1.3.15除磷化加热采用槽外板式换热器外,其余槽液加热采用槽内不锈钢蒸汽加热器。
采用温控仪控制电磁阀实现槽液控温。
温控仪采用进口产品,电磁阀采用国内知名品牌产品,确保使用性能。
8.1.3.16各槽排水管均设不锈钢过滤网,防止排水管堵塞;
8.1.3.17磷化段设连续高位斜板沉降式除渣装置,以不断过滤槽液中的磷化结渣;
8.1.3.18磷化处理时由于化学转化的作用,会产生结渣现象。
磷化液中有一定比例的磷化渣不会对磷化效果产生影响,但当比例过大时,将会产生挂灰等磷化缺陷,所以必须对磷化液中的结渣进展清理。
8.1.3.19采用连续式高位沉降槽对磷化渣进展清理,循环沉降泵将含渣槽液从底部泵入高位沉降槽中,利用截面积的突然增大使槽液流速迅速降低,当其流速低于时,已经远远低于磷化渣的上升速度,磷化渣缓慢沉降,再利用槽内斜板的作用防止细微颗粒的磷化渣上浮。
清洁的槽液从槽体上部流入磷化槽。
底部沉渣到达一定高度时,翻开排渣阀,放入接渣小车中直接外运处理或采用板框压滤机处理后外运。
本设备由高位沉降槽、沉降泵、接渣小车、管路系统等组成。
8.1.3.20工件在进入电泳槽以前的最后一道前处理工序采用纯水浸渍,新鲜纯水喷淋一次;
8.1.3.21外配管路系统:
系统包括给水管路、排水管路、溢流管路等。
其中电泳、磷化、UF及纯水洗工位管路系统材质为SUS304不锈钢,其余管路系统材质为碳钢。
8.1.3.22电气控制系统包括对加热系统、循环水泵、排风风机、温控仪表、电磁阀等的控制。
槽液控温采用铂热电阻传感器测温,数显式温控仪控制电磁阀或循环水泵,以稳定控制槽液温度。
8.1.3.23风机与棚体的连接处、水泵与槽体的连接处采取减、隔振措施以减少振动及噪音。
使用时按国家标准规定的测试方法整机噪音不得超过85dB;
8.1.3.24主要部件
A.前处理棚体及槽体
前处理及电泳装置棚体:
尺寸〔L×W×H〕24000×3500×4100mm
前处理及电泳棚体由1.5毫米镀锌钢板制作,内以矩形钢管和其他型材作龙骨,强度可靠。
棚体内部设照明灯,侧面开有玻璃窗,保证光照。
在加热工位设计有排风装置,减少室内水蒸汽对工件的影响。
室体顶部有一定坡度防止冷凝水滴下,在电泳槽上方设有强制排风系统,排走挥发的助剂。
电泳槽两侧设有操作通道;设备侧面设操作平台。
脱脂槽的油水别离装置、磷化除渣装置、纯水装置、冷水机组等设备放在电泳线旁的附属设备间内。
所有水洗槽设置溢流槽,溢流槽设置排液溢流口。
B.预脱脂工位:
采用热脱脂液浸渍,将油污在热水浸泡下松脱,以便于脱脂处理。
工作过程中产生的水蒸气由排风机排出,槽液温度达55~70度。
槽体尺寸:
800×1500×1800mm.
油水别离装置:
一台
C.热水洗工位:
槽液温度达70~90度,用热水可保证将油污清洗得更彻底。
槽体尺寸:
700×1500×1800mm.
D.冷水清洗:
为确保下道工序的效果而设立,可彻底去除工件外表的残液,为下道工序做好准备。
槽体尺寸:
700×1500×1800mm.
双联槽:
1400×1500×1800mm.
E.表调工位:
表调的目的是为使磷化膜在工件的外表产生更好的附作力,通过化学制剂的作用,使外表发生化学反响,在金属外表形成大量极细的微小结晶颗粒,从而加速磷化反响,有利于磷化膜的形成。
槽体尺寸:
700×1500×1800mm.
F.电解除油工位:
可彻底出去工件外表残留油污,槽液温度60~70度。
槽体尺寸:
800×1500×1800mm.
配整流电源一台:
电压12V(24V),电流按6A/dm2设计。
G.酸洗工位:
可除去工件外表锈迹。
该工序为甲方所设计,本公司认为酸洗工位设置在线上不太合理,尽管设置有槽边抽风装置,但仍有局部酸雾将会弥漫在棚体中,这样会造成行车腐蚀。
槽体尺寸:
700×1500×1800mm.
H.磷化工位:
磷化的意义在于钢铁件在含有锌铁锰的磷酸盐溶剂中,由于金属和药液在界面上发生化学反响,产生难溶于水的磷酸盐,使钢铁外表形成一层良好的保护膜,起到防锈的效果。
槽体尺寸:
1000×1500×1800mm.
配高位除渣系统一套;
板式换热加热系统一套;
硝酸反清洗系统一套;
I.冷水清洗〔2道〕:
双联槽:
1400×1500×1800mm.
J.纯水洗:
纯水槽体尺寸:
700×1500×1800mm.
反渗透纯水制备设备:
1套流量1吨/h。
K.吹水检查工位:
高压空气喷头一套,人工定期检查一下工件前处理的效果。
8.2阴极电泳设备:
本工序设有6个工位,包含阴极电泳,UF水洗两道,纯水洗,电泳烘干,冷却。
阴极电泳采用国内先进的涂装技术,通过电极作用于漆液,在工件上沉积形成漆膜,成膜均匀,外观光整。
电泳主槽体设有溢流槽,用以控制液面高度;设有漆液补充槽,以保证槽体内漆液得以及时补充。
为防止漆液沉淀,设计有循环搅拌装置.
8.2.1设备组成:
由棚体、抽风装置、槽体、阳极液系统、循环搅拌系统、过滤和超滤系统、热交换系统、直流电源和集电系统、电泳液转移槽等组成。
8.2.1.1棚体由外罩、人行走道组成,材料为碳钢型材和镀锌板。
棚体内上侧部设照明灯。
棚体顶部设抽风装置,将不洁空气抽出室外排放。
8.2.1.2槽体为5mm厚碳钢制作,内涂5层玻璃钢,槽体倒圆角,使电泳槽液无循环死角。
电泳槽尺寸为:
L1200xW1500xH1800mm;
走道宽度:
800mm;
电泳槽槽体为全焊构造,槽体骨架及槽板均为碳钢钢,槽底有一定斜度,槽一端设置副槽,槽内设置过滤网,槽底内侧边角为圆弧型。
内外表涂玻璃钢。
击穿电压20000伏。
副槽上配置超滤水喷淋管路,管路材料为不锈钢。
电泳槽与一次超滤水槽之间设置转移管路。
m3,副槽350Kg。
m/s。
电泳漆过滤不低于4次/小时,由槽内搅拌管及外部管路系统组成,搅拌管上安装文丘里喷嘴,喷嘴布局合理,无搅拌死区,保证电泳漆不沉淀。
管路系统中采用双机械密封泵,设置袋式过滤器,泵、阀、管路材料均为不锈钢。
8.2.1.4主循环、超滤循环及UF1循环设袋式过滤器。
超滤器为美国AMT或星达公司卷式超滤器超滤系统:
由卷式超滤器、袋式过滤器、泵、阀、管路、超滤器清洗装置组成,材料均为不锈钢,采用机械密封泵。
超滤膜采用美国进口产品,超滤量为200L/h;
主循环量:
100t/h,循环压力:
0.3-0.4MPa;
温度限制:
32℃,PH值限制:
6~11
8.2.1.5热交换系统设冷热调温水槽和板式换热器,用冷冻水〔8~12℃〕冷却电泳槽液。
热交换系统:
采用板式热交换器冷却电泳漆,管路系统中采用单机械密封泵,油漆管路中设置温度传感器,设置袋式过滤器,泵、阀材料均为不锈钢。
冷却水管路中设置Y型三通电工调节阀,通过温控系统能自动调节电泳漆的温度。
过滤器:
袋式。
冷冻机:
15000Kcal/h
冷却水泵浦:
1.1KW;
漆液温度:
28±2℃
8.2.1.6选取直流电源容量为:
直流电压:
300V;直流电流:
250A,电源:
380V×50Hz
操作方式:
连续方式;
冷却方式:
气冷式。
0-180V、180-240V阶梯线性升压,波纹系数小于5%,阴极接地。
电泳导电装置:
由于电泳电流较大,在电泳槽上自动接电,电泳槽上方设置导电排,工件进展到电泳槽上方导电排接电,通过电控系统实现工件入槽后通电,出槽后断电,使用平安、可靠。
8.2.1.7阳极系统:
由阳极液槽、管式阳极、泵、阀、管路组成,每只阳极管配流量计,流量可调,电导率自动控制。
阳极系统采用进口膜别离技术
阳极管:
Tas-1.2;10只。
极液泵浦:
CDL2-30,极液槽体容量:
500公斤,电极巢数量:
5组
8.2.1.8电泳漆转移槽由槽体、循环泵〔输送泵〕、搅拌管路组成。
槽体容积与电泳槽一样,内衬三层防腐玻璃钢。
8.2.1.9电泳后清洗UF1采用袋式过滤器进展过滤,过滤精度20~50μUF水洗工位:
超滤水槽及管路系统:
超滤水槽槽体为全焊构造,槽体骨架及槽板均为低碳钢,内外表涂玻璃钢〔或用不锈钢〕,槽底部有一定斜度至排水口;排水口处设置排水阀门;槽上有去离子水加水口;槽内设置循环搅拌管路,泵、阀、管路均为不锈钢制造,采用液下单机械密封泵。
管路中设置电控阀,可将一次超滤水转移至电泳槽。
8.2.1.10去离子水槽及管路系统:
去离子水槽槽体为全焊构造,浸渍槽体骨架及槽板均为低碳钢,内外表涂玻璃钢,喷淋槽体采用不锈钢材质,槽底部有一定斜度至排水口;排水口处设置排水阀门。
8.3电泳烘干室
8.3.1设备类型:
连续通过式燃油热风循环桥式烘干室。
8.3.2设备组成:
由炉体、热风循环系统、过滤系统、燃油加热系统、排气系统和自动温控系统等组成。
8.3.3设备构造特点:
8.3.3.1利用热空气上升的原理,采用下送上回的方式,使炉内温度均匀。
8.3.3.2采用拼装式壁板构造,内、外板间热桥少,减少热损失。
8.3.3.3采用轻质岩棉板,隔热性能好,隔热层厚度150毫米。
设备外外表温度不高于车间温度10℃。
室体壁板为自承重插接式构造,节省骨架材料,且可很好解决由温度变化引起的热伸缩给设备构造造成的危害;壁板插接处涂耐热密封胶,防止热泄露。
8.3.3.4内外壁板均采用镀锌板折弯后制成。
8.3.3.5送风管中设有调节板,保证炉内温度场的均匀,便于调节。
8.3.3.6加热系统和循环风机均有保温层,减少了管道的热损失。
8.3.3.7循环风机采用国产耐温、低噪音风机。
风机平台骨架为普通型钢和钢板焊接而成。
8.3.3.8送风管出口处设空气过滤器,以确保空气的干净度。
内、外风管均采用镀锌钢板制造,整体构造美观大方。
燃气油热风装置四元体放置于室体顶部,便于桥式炉底部可成为通道。
8.3.3.9热源采用轻质柴油燃烧进展加热,采用进口燃烧器,设有自动点火和检测系统。
〔四元体〕加热燃烧换热单元、废气单元、过滤单元、循环风机单元。
8.3.3.10整个烘干室有一套热风循环系统,废气可通过风机抽送到车间外。
主要部件:
烘道棚体1座;L18000xW2500xH2200mm;
燃油四元体供热装置1套供热量55万大卡/小时,废气处理量:
2500m3/h;
温度控制系统1套
耐热风机1套
废气排放装置1套
循环热风管道1套
超温报警装置1套
热风循环过滤系统1套
烘道出入口排热气系统2套
九、设备构成
十、概算除外工程
No:
项目
含
除外
内容
1
根底
工程
√
根底地面PIT,排水沟等土木建筑工程
√
设备安装时必要之水泥土木工事
2
厂房建
筑工程
√
厂房建筑工程
√
厂房的打洞,修补,增强工程
√
厂房内隔间工程
√
厂房内照明工程
√
厂房内换气及空调工程
3
现场
安装
√
现场临时办公室
√
工程用材料堆放场地
√
工厂平安及防火设备
√
工程安装用动力
√
废弃物运出
4
一次侧动力
电气
√
各操作台一次侧电力及配线
√
接地工程
√
工厂配电,发电设备
水
√
工业用水及配管、管路、管件、水塔等
√
排水沟工事及设备3m以外之给排水配管
5
其他
√
配套环保设备及设施
√
三废处理设备
√
试车用药液及电泳漆等材料消耗
√
蒸汽锅炉及蒸汽配管设施
√
天然气输送及降压设施
√
空压机设备
√
紧急发电机
√
抛丸除锈设备
√
工作物吊挂具
√
废水处理场设施
√
车间消防设施
十一、环境保护,职业平安卫生,消防
11.1引用技术标准,标准等。
a.工业企业设计卫生标准TJ36-79
b.工业企业照明设计标准TJ34-79
c.电气设备平安设计导那么GB4064-83
d.固定式钢梯,台,栏GB40531-4-83
e.涂装作业平安规程GB6514,GB6515-86
GB7691-93-87
f.工业企业噪声卫生标准〔1979〕试行
g.重庆市污染物排放标准川印356-82〔1983〕
h.污水综合排放标准GB8978-88
i.大气环境质量标准GB3095-82
j.爆炸和火灾危险环境装置设计标准标准GB50058-92
本车间生产过程中排放的污染物质中,采取的治理措施说明如下:
1、前处理、电泳在生产过程中所产生的废水,排至废水处理站进展处理,达标后排放。
2、在前处理预脱脂、脱脂、表调、磷化槽体处安装抽风罩,通过离心风机把产生的有害气体及时排除,保证车间的空气质量,因此最大限度地减少了对生产工人的危害。
3、对于生产过程中如风机、水泵等产生的噪声,设计中采用了减震措施,选用转速较低,质量较好的产品,使噪声不超过85分贝。
4、加热管道及加热设备均设保温隔热层,以防工人烫伤。
5、但凡高压电场所,均有明显的“警示〞标志。
6、车间设计考虑平安门及疏散通道,以便车间发生火灾时及时撤离。
7、工人在操作过程中应穿好工作服,严禁在车间内吸烟。
8、对喷漆时所产生的废气,由于浓度较低,采用高空排放,排放高度为离地面15M;烘干时所产生的废气采用催化燃烧或活性碳吸附处理。
11.2消防:
〔车间消防不在本工程范围内〕
在车间适当位置设置平安门及疏散通道,以便车间发生紧急情况时及时撤离。
十二、设计方案图〔附后〕
电泳、喷漆涂装线平面布置图
如有侵权请联系告知删除,感谢你们的配合!