第十章沸腾炉工艺计算.docx
《第十章沸腾炉工艺计算.docx》由会员分享,可在线阅读,更多相关《第十章沸腾炉工艺计算.docx(15页珍藏版)》请在冰豆网上搜索。
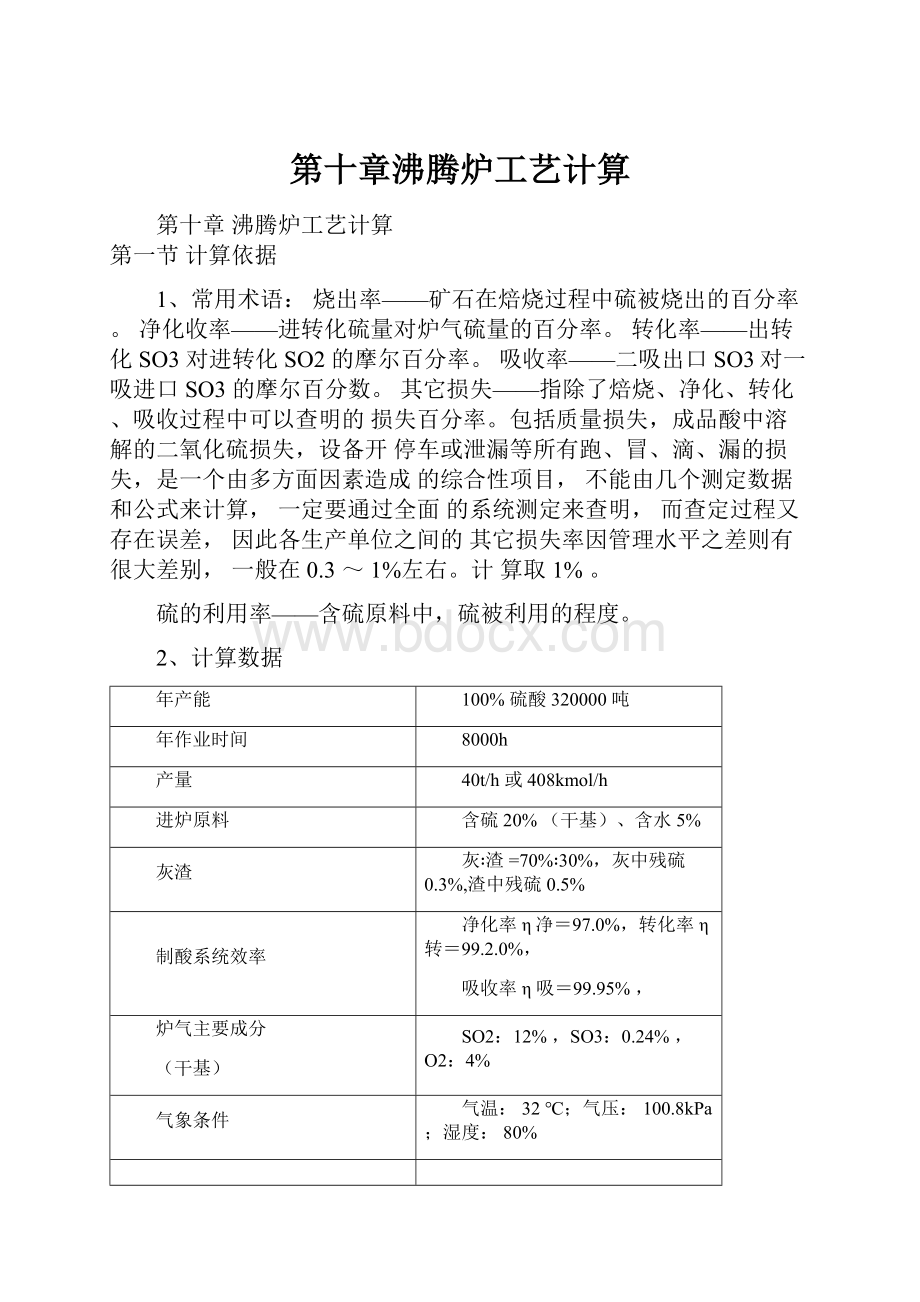
第十章沸腾炉工艺计算
第十章沸腾炉工艺计算
第一节计算依据
1、常用术语:
烧出率——矿石在焙烧过程中硫被烧出的百分率。
净化收率——进转化硫量对炉气硫量的百分率。
转化率——出转化SO3对进转化SO2的摩尔百分率。
吸收率——二吸出口SO3对一吸进口SO3的摩尔百分数。
其它损失——指除了焙烧、净化、转化、吸收过程中可以查明的损失百分率。
包括质量损失,成品酸中溶解的二氧化硫损失,设备开停车或泄漏等所有跑、冒、滴、漏的损失,是一个由多方面因素造成的综合性项目,不能由几个测定数据和公式来计算,一定要通过全面的系统测定来查明,而查定过程又存在误差,因此各生产单位之间的其它损失率因管理水平之差则有很大差别,一般在0.3~1%左右。
计算取1%。
硫的利用率——含硫原料中,硫被利用的程度。
2、计算数据
年产能
100%硫酸320000吨
年作业时间
8000h
产量
40t/h或408kmol/h
进炉原料
含硫20%(干基)、含水5%
灰渣
灰∶渣=70%∶30%,灰中残硫0.3%,渣中残硫0.5%
制酸系统效率
净化率η净=97.0%,转化率η转=99.2.0%,
吸收率η吸=99.95%,
炉气主要成分
(干基)
SO2:
12%,SO3:
0.24%,O2:
4%
气象条件
气温:
32℃;气压:
100.8kPa;湿度:
80%
第二节物料衡算
根据质量守恒定律,以生产过程或生产单元设备为研究对象,对其进出口处进行定量计算,称为物料衡算。
通过物料衡算可以计算原料与产品间的定量转变关系,以及计算各种原料的消耗量,各种中间产品、副产品的产量、损耗量及组成。
物料衡算的基础:
物料衡算的基础是物质的质量守恒定律,即进入一个系统的全部物料量必等于离开系统的全部物料量,再加上过程中的损失量和在系统中的积累量。
物料衡算是所有工艺计算的基础,通过物料衡算可确定设备容积、台数、主要尺寸,同时可进行热量衡算、管路尺寸计算等。
1、硫的烧出率
1.1灰渣平均残留率
式中,CS(残)—灰渣平均残硫率,%CS(灰)—灰中残硫量,%CS(渣)—渣中残硫量,%
1.2灰渣产率:
160CS(实)
x
160CS(残)
式中,CS(实)—矿石中硫的实际含量%
CS(残)—矿渣中的残硫量%
则灰渣产率为:
1600.36
x16020=0.877kg灰渣/kg矿
1.3硫的烧出率
式中,ηs—硫的烧出率,%
则硫的烧出率为:
20-0.8770.36×100%=98.42%
20
2、投矿量
总硫利用率:
式中,—总硫利用率,%;
—净化率,%;
—转化率,%;
—吸收率,%。
=98.42%×97%×99.2%×99.95%=94.65%则,耗矿定额(干矿):
式中,
式中,—耗矿定额,吨矿/吨酸;
—硫的摩尔质量,kg/mol;
—硫酸的摩尔质量,kg/mol
则,G耗
980.200.9465
=1.725干矿/t酸
小时投干矿量=1.725×40=69t/h
小时投矿实物量=69÷(1-0.05)
=72.63t/h。
3、灰、渣产量:
焙烧反应是较复杂的,为计算方便及实用,本计算只依据下列反应式来进行。
4FeS2+11O2=2Fe2O3+8SO2+3413KJ实际上反应后生成的Fe2O3一般约占75%,生成的Fe3O4占25%左右。
式中,—灰渣生成量,t/h
则,G灰渣=0.877×69=60.51t/h其中:
随炉气带走灰量:
60.51×70%=42.36t/h
出渣口排放渣量:
60.51×30%=18.15t/h
4、干炉气量
SO2+SO3量
=408/η净×η转×η吸=408/0.9618=424.2kmol/h出炉干炉气量
=424.2÷(0.12+0.0024)=3465.69kmol/h
或77631.46m3/h其中:
SO2:
3465.69×12%=415.88kmol/h
SO3:
3465.69×0.24%=8.32kmol/h
O2:
3465.69×4%=138.63kmol/h
N2:
3465.69―415.88―8.32―138.63=2902.86kmol/h
5、空气量
N2=2902.86kmol/h
O2=2902.86×21=771.65kmol/h
279
干空气量=
或3674.51
空气含水=
2902.86+771.65=3674.51kmol/h×29kg/kmol=106560.79kg/h3674.51×3.79=143.56kmol/h
100.8-3.79
式中:
3.79为32℃相对湿度为80%时,空气中的蒸汽分压(kPa)
湿空气量=(3674.51+143.56)×22.4
=85524.77m3标/h或3818.07kmol/h
32℃、常压下湿空气量=85524.77×(273+32)/273=95549.65m3/h。
(或1592.49m3/min)
6、炉气中水量
原料带入水=69×1000×5/(100-5)=3631.58kg/h或201.75kmol/h
空气带入水143.56kmol/h
炉气中水量=143.56+201.75=345.31kmol/h
7、炉气总量(即湿炉气量)
3465.69+345.31=3811kmol/h或85366.4m3标/h
附:
按计算公式来计算:
1、炉气生成量
式中,—炉气生成量,m
—炉气中
3/h
SO2、SO3的含量,%
G投—投矿量,kg/h
则,V气.矿=685×0.98420.269=76010.15m3/h
0.120.0024
2、炉气组分计算
2.1炉气中氧含量CO2(%体积)
按反应式4FeS211O22F2eO38SO2来进行计算,其炉气中
SO2、SO3、O2
的含量关系如下:
CSO2CSO31.375(CSO2
100
CSO3)729112CSO37291CO27291CO2
SO3212SO321O221O2
6.17CSO28.05CSO34.76CO2100
6.17128.050.244.76CO2100所以CO25.05
即CO25.05%
又CSO2CSO3CO2CN2100%
得CN2100120.245.05
CN282.71%
表3-1炉气中各气体含量表:
组分
含量%
SO2
12
SO3
0.24
O2
5.05
N2
82.71
3、空气需用量
按反应式4FeS211O22F2eO38SO2来进行计算。
生成SO2需氧量V1:
=11/8×0.12×76010.15=12541.67m3/h
生成SO3需氧量V2:
=11/8×0.0024×76010.15=250.83m3/h炉中过剩氧量V3:
=0.0505×76010.15=3838.51m3/h进炉总氧量
=12541.67+250.83+3838.51=16631.01m3/h
需要空气量V空:
V空=VO2/21%=16631.01÷21%=79195.3m3/h
=79195.3029=102529.63kg/h
22.4
随空气带入炉内水份量:
=0.01×79195.3=791.953kg/h
或=791.953÷18×22.4=985.54m3/h
式中0.01是32℃空气中含水量10g/m3
所以炉内湿空气总量:
V空=79195.3+985.54=80180.84m3/h
4、物料进出情况
沸腾焙烧反应:
4FeS211O2Fe2O38SO2(少量SO3),水、氮气未参加反应。
G水=5%G投+G气·水
=0.05×69000÷0.95+791.953
=4423.53kg/h
GN2=V空×0.79÷22.4×MN2
=79195.3×0.79÷22.4×28=78205.36kg/h
GO2=3838.51÷22.4×32
=5483.59kg/h
=76010.15×0.12÷22.4×64=26060.62kg/h
GSO3=76010.15×0.0024÷22.4×80
=651.52kg/h
于是,
∑进=G矿+GN2+GO2+G水
=69000+78205.36+23758.59+4423.53=175387.48
=4423.53+78205.36+5483.59+26060.62+651.52+60510
175334.62kg/h
∑进-∑出=175387.48-175334.62=52.86kg/h
物料平衡表
物料名称
输入kg/h
输出kg/h
投矿量(干矿)
69000
—
N2
78205.36
78205.36
O2
23758.59
5483.59
H20
4423.53
4423.53
SO2
—
26060.62
SO3
—
651.52
矿渣
—
60510
合计
175387.48
175334.62
第二节热量衡算
热量衡算的基础是能量守恒定律,在无轴功的条件下,进入系统的热量与离开热量相互平衡。
实际生产中传热设备的热量衡算可由下式表示。
Q1+Q2+Q3=Q4+Q5+Q6
式中,Q1—物料进入设备带入热量,kJ;
Q2—由加热剂或冷却剂传给设备和物料的热量,kJ;
Q3—过程热效应,kJ;
Q4—物料离开设备带出的热量,kJ;
Q5—消耗在加热设备各个部件上的热量,kJ;Q6—设备向四周散失的热量,kJ。
热量衡算的方法
热量衡算时一般建议以273K为基准温度,以液态为基准物态。
(1)物料进入设备带人热量Q1(或物料由设备带出的热量Q4)的计算
—物料质量,kg;
—物料平均等压比热容,kJ(kg?
℃)-1;
T—物料温度,℃;
T0—计算基准温度,℃。
生产过程中有相变化时还要加上相变热。
(2)过程热效应(Q3)
过程热效应包括化学过程热效应(Qr)和物理过程热效应(Qp)。
即:
式中,GA—参与反应的A物质量,kg;
—标准化学反应热,kJ·mol-1;
MA—A物质的分子量。
Qp可通过盖斯定律来计算。
消耗在加热设备各个部件上的热量(Q5)的计算:
式中,Mi—设备上i部件质量,kg;
—设备上i部件比热容,kJ·(k℃g?
)-1
T1—设备各部件初温,℃;
T2—设备各部件终温,℃。
设备向四周散失的热量(Q6)的计算
式中,A—设备散热表面积,m2;
—散热表面向四周介质的联合给热系数,
W·(m2?
℃)-1;
—四壁向四周散热时的表面温度,℃;
—周围介质温度,℃;
t—过程持续时间,s。
由加热剂或冷却剂传给设备和物料的热量的计算:
选定加热剂(或冷却剂),即可从有关手册查出该物质cp,再确定其进出口温差ΔT,则加热剂(或冷却剂)的用量为:
式中,κ—传热系数,kJ·(m2?
h·℃)-1;
A—传热面积,m2;
ΔTm—对数平均温差,℃
从上式即可计算所需的传热面积。
对不需加热或冷却的设备可不必进行热量计算,此时水、汽等消耗量的确定可从同类型的生产车间取得。
1、原始数据
炉温:
沸腾层800℃,炉气出口850℃尘、渣平均热容:
0.96kj/(kg.K)单位换算:
1cal=4.1868J
以1h为计算基准
2、带入热
2.1矿石带入热
室温32℃CP=0.45kj/(kg.K)
Q1=69000×0.45×32=993600kj/h
2.2空气带入热空气温度32℃,CP=1kj/(kg.K)
Q2=106560.79×1.014×32=3457684.51kj/h
2.3反应热Q3
4FeS2+11O2=2Fe2O3+8SO2+3413KJ
SO2+O2=SO3+99KJ
SO2:
415.88kmol/h;SO3:
8.32kmol/h
Q3=415.88×1000×3413÷8+8.32×1000×99
=178248485KJ/h
带入热总计:
182699769.5kj/h
3、带出热
3.1矿渣带出热Q4
Q4=18.15×1000×0.96×800=13939200kj/h
3.2矿灰带出热Q5
Q5=42.36×1000×0.96×850=34565760kj/h
3.3干炉气带出热Q6(硫酸工业手册314页)
SO2:
415.88kmol/hCPSO2=49.4j/(mol.K)
SO3:
8.32kmol/hCPSO3=71.97j/(mol.K)
O2:
138.63kmol/hCPO2=32.4j/(mol.K)
N2:
2902.86kmol/hCPN2=31.0j/(mol.K)
水:
345.31
kmol/hCPH2O=37.7j/(mol.K)
带出热:
SO2:
415.88×49.4×850=17462801.2kj/h
SO3:
8.32×71.97×850=508971.84kj/h
O2:
138.63×32.40×850=3817870.2kj/h
N2:
2902.86×31.00×850=95358951kj/h
H2O:
345.31×37.7×850=11065458.95kj/h
Q6=17462801.2+508971.84+3817870.2+76490361
+11065458.95
=109345463.2kj/h
3.4矿石带入水分吸收热
矿石水:
3631.57kg/h水比热:
4.178kj/(kg.K);水蒸气汽化热:
539kcal/kg;过热水蒸汽平均比热:
0.5kcal/(kg.K)Q7=3631.57×4.178×(100-32)+539×4.19×3631.57
+0.5×4.19×3631.57×(850-100)
=14939421.93kj/h
3.5空气带入水分吸收热
水:
143.56kmol/hCPH2O=37.7j/(mol.K)
Q8=143.56×37.7×(850-32)=4427189.42kj/h
3.6炉壁损失热
Q9=182699769.5×3%=5480993.085kj/h
3.7沸腾层炉气汽化冷却转移走的热量
=993600+3457684.51+178248485-13939200-34565760
-109345463.2-14939421.93-4427189.42-5480993.08
=1741.9kj/h
输入(kj)
输出(kj)
矿石带入热
993600.00
矿渣带出热
13939200.00
空气带入热
3457684.51
矿灰带出热
34565760.00
反应热
178248485.00
干炉气带出热
109345463.20
—
—
矿石带入水分吸收热
14939421.93
—
—
空气带入水分吸收热
4427189.42
—
—
炉壁损失热
5480993.08
—
—
沸腾层汽化移走热
1741.9
沸腾炉热量平衡表
总计
182699769.50
182699769.50
第二节主要设备工艺计算
1、炉床面积、
1.1炉床直径(硫酸工业手册314页)
D=4Y3210010024100098CsB
式中:
Y—小时产酸量100%,kg
η总—总采酸量,%
CS—矿石中硫的实际含量%
12%
B—焙烧强度,t/m·d焙烧硫精砂采用焙烧强度12t/m2·d
850℃下沸腾层气量:
850
Vt=V0(1+273)=85445.58(1+273)=351484.93m3/h(或=97.63m3/s)
沸腾层气量(减除二次气量):
97.63×(100%-12%)=85.92m3/s沸腾层面积:
F沸=85.92÷0.709=121.18m23、焙烧强度:
硫酸工业手册296页
UF=33700WCSO2/CSηT
式中,UF—单位生产率(焙烧强度),t/m2·d;
W—操作气速,m/s;
CS—原料含硫,%;
T—沸腾层内温度,k;
CSO2—炉气SO2浓度,%;
η—硫烧出率,%;
UF=33700×0.709×0.12/(0.2×0.9842×1123)=12.97t/m2·d
4、床面积
式中,F床—床面积,;
A—炉子日处理量,t/d
F床=6924=127.68m
12.97
对于圆形炉子,床直径:
式中,D床—床直径,m;
F床—本床面积,;
F前室—前室面积,。
F前室=0。
则,D床=1.13127.68=12.77m
5、沸腾层高度硫铁矿焙烧为放热反应,为使床层具有一定的热稳定性与流化的均匀性,参考同类型炉子的生产实践,取H层=1.3m。
炉床面积在投矿量一定的情况下,主要与沸腾层高度、炉料停留时间和烟尘率有关。
2.3沸腾层气量
沸腾层气量一般采用炉气和空气量的平均值(湿气体)
85366.485524.773=85445.58m标3/h
2标