多层共挤膜.docx
《多层共挤膜.docx》由会员分享,可在线阅读,更多相关《多层共挤膜.docx(11页珍藏版)》请在冰豆网上搜索。
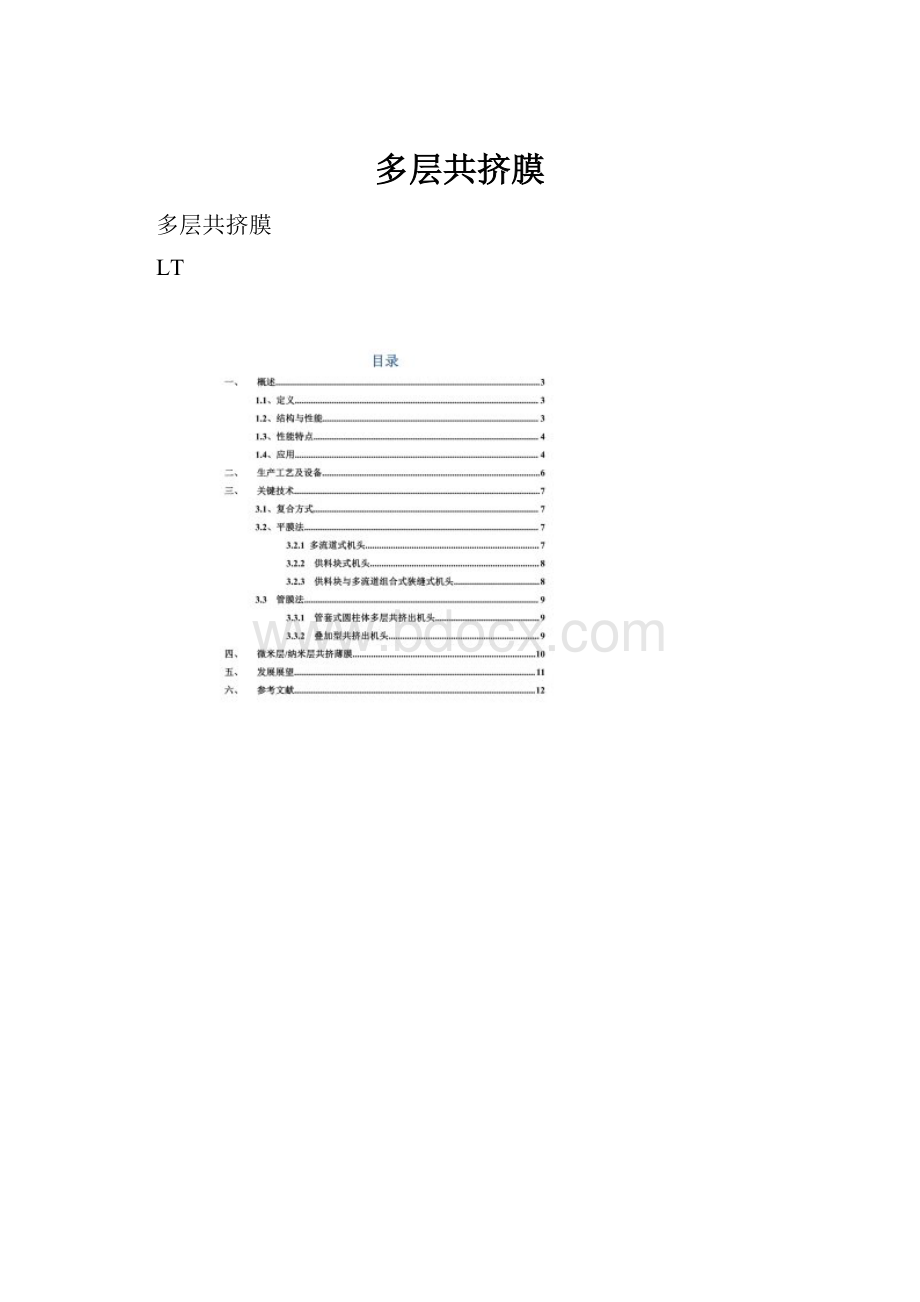
多层共挤膜
多层共挤膜
LT
层共挤膜为例介绍其结构,典型的五层共挤膜为ABCBA结构,其结构如下图所示:
据图可知,多层复合膜的对称结构层一般分为三类:
阻隔层、粘结层以及支撑层
阻隔层:
阻隔层对产品整体性能起着主导作用,它一般处于共挤膜中间层,两面均有支撑层保护,阻隔层树脂一般都较贵,因此如何确定这一层厚度显得很重要。
阻隔层树脂有极好的阻气性、阻湿性,因此特别适用于食品、饮料和药品的包装。
支撑层:
支撑层有两个作用,一面用于热封,称热封层,一面用于印刷,称印刷层。
印刷层可以薄一些,一般在巧仁左右。
支撑层要求有良好的机械强度、热封性、阻隔性、透明性和印刷性,这层一般选用LDPE或LDPE/LLDPE共混材料较多。
粘结层:
粘结层有两层,一层粘住阻隔层和热封层,另一层粘住阻隔层和印刷层,其厚度取决于粘结强度,粘结强度不够共挤膜就会脱层,严重影响产品质量。
粘结层的树脂主要有:
改性EVA树脂、离子型树脂、EVOH树脂。
1.3、性能特点
多层共计复合膜能够充分利用各种不同性能的塑料原料,根据需要进行复核,可得到优良的性能:
阻隔性好、强度和耐穿刺性高、热封性好、粘结性强、有良好的防雾性、防滑性、着色性等等。
1.4、应用
多层共挤出技术作为一种特殊的生产技术,正是利用材料的特点优势互补,大大改善了制品的各项性能,如阻隔、密封、耐腐蚀、耐高温、耐低温、抗菌、无毒、保鲜等性能。
目前多层共挤膜主要用于生产高阻隔性包装膜、收缩膜、中空保鲜膜、土工膜、输液袋……
一、生产工艺及设备
多层共挤膜按挤出工艺和机头口模形状分,共挤出复合分为平膜法和管膜法。
平膜法用于共挤出流延薄膜,所用机头称为共挤出流延薄膜机头。
平膜法用于共挤出流延薄膜,所用机头称为共挤出流延薄膜机头。
平膜法和管膜法的生产工艺大致相同,只是在冷却系统和牵引旋转器结构不同,其工艺主要有一下几个方面:
塑化、机头口模成型、冷却定型、卷取。
塑化:
粒料经料斗进人挤出机内,树脂熔化而呈熔融滚流动状态,在螺杆的推动作用下,塑料熔体以旋转流动方式通过滤网,并滤去未塑化的物粒和不熔的杂质,变熔体旋转为平直流动。
与单层挤出不同,共挤薄膜机械要求各层挤出机在塑化质量、塑化效率等方面,与多层复合机头具有一定的协调性
机头口模成型:
不同原料的熔体通过各自的流道,以相同的速率,不同的排列顺序,平衡地导入模头复合成型,经过可以调节的模唇流出。
卷取:
收卷,最后包装入库,即为多层共挤膜产品。
切边下来的边角料经回收系统处理后可回收使用。
冷却定型:
由模唇流出的薄膜至冷却辊或风环冷却定型,再经过牵引系统以一定的速度引出。
多层共挤薄膜生产中,冷却对产量及产品质量影响很大。
冷却不均匀,会影响薄膜的厚度、透明度、表面光泽等。
共挤膜在冷却成型后,自动测厚系统对其进行厚度测定,将信息反馈给执行机构,调整挤出机螺杆转速及牵引速度,以控制成膜的质量。
目前的冷却技术是采用外冷和内冷。
外冷法是采用风环冷却,最新的外冷系统为双唇环冷却。
双唇环冷却是在口模上安装一个附加风环,二次气流将部分冷却的膜泡快速向上引导,冷却气体采用制冷的空气。
最先进的内冷系统是膜泡内冷技术(IBC)。
IBC技术可以达到内部冷却介质定量、低温、恒压、动态平衡的要求,使膜泡进入夹平辊之前充分冷却,提高薄膜的生产效率及产品质量。
二、关键技术
机头是共挤出设备中的核心装置,其结构决定着复合塑料薄膜的性能,目前关于多层共挤膜的研究也多集中于机头口模的设计。
近年来,为了满足对薄膜性能不断提高的要求,多层共挤出流延薄膜机头和多层共挤出吹塑薄膜机头在结构和共挤出薄膜层数及物料的适应性、薄膜厚度控制精度等方面都有很大发展。
3.1、复合方式
根据薄膜层复合方式可分为三种类型:
模前复合、模内复合以及模外复合。
第一是模前粘接式,又分层流分布法、组合喂料法及快速调换法。
各挤出机挤出的熔融树脂在进入模具之前的入口处进行复合。
第二是模内粘接式,在T形模共挤出的场合亦称为多歧管法,其特点是挤出的各熔融树脂分别导入模内各自的流道在离开模口之前复合。
第三为模外粘接式,亦称多缝式,是在树脂离开模口后复合的。
这三种方式各有长处和短处,从国内复合薄膜的生产工艺来看,采用模内复合的情况较多。
3.2、平膜法
共挤出平膜法所用机头为狭缝式机头,主要有多流道式机头和供料块式机头以及二者的组合式。
3.2.1多流道式机头
多流道式机头具有和层数相对应的、与薄膜宽度等长的槽,通过各自的槽,熔体流扩宽后通过阻流条控制各层的速度和流量并合流,然后从模唇挤出
3.2.2 供料块式机头
这种机头的优点是体积较小,易变换层数,但和多流道式机头相比,供料块式机头制得的薄膜各层膜厚的均匀性较差。
3.2.3 供料块与多流道组合式狭缝式机头
组合式机头将供料块式和多流道式机头取长补短,喂料块恰到好处地伸到多流道式机头中,缩短了熔体流动行程,具有较好的综合性能,比较适用于复合4层以上或含热敏性物料的薄膜
3.3 管膜法
共挤出管膜法,即挤出吹塑薄膜法,所用机头为圆柱体机头,结构有多种,主要有套管式圆柱体多层共挤出机头、叠加型圆柱体多层共挤出机头
3.3.1 管套式圆柱体多层共挤出机头
管套式共挤复合机头是每层流道同芯装在一起,即每层流道是并联的,管套式复合机头的主要特点是结构紧凑,流道长度小,熔体停留时间短。
缺点是各层温度难以单独控制,每层流道的流量、压力、速度的平衡性设计较困难。
3.3.2 叠加型共挤出机头
叠加型共挤出机头一般采用侧进料,熔体以中心轴对称,在每层的叠加面(平面和锥面)流动,而不是传统的筒状流动。
叠加型机头的最大优点是机头层数可以任意组合,而且每层温度可以单独控制,这样可以根据不同的需要分别控制每层的温度,而且物料的停留时间较常规的机头要短而且均一,所以可以有效防止物料降解。
三、微米层/纳米层共挤薄膜
聚合物微米层/纳米层共挤出技术是指将两种或两种以上聚合物共挤出形成几十层乃至上千交替层的复合薄膜,所得挤出层的厚度可以是微米级甚至达到纳米级。
该结构最早是由道化学公司以彩虹膜的形式提出来的,其关键技术就是供料块。
由于该技术不仅可以获得普通多层共挤出(通常只有3~7层)无法比拟的力学、光学、阻透及电性能等,而且因其具有很大的比表面积及良好的均匀性,特别是二维的结构,为研究聚合物两相间的粘结、扩散及结晶等基础理论提供了可靠的模型体系,从而备受研究者们的青睐。
下图是微米层/纳米层共挤出的工作原理图,该共挤装置是由两台单螺杆挤出机、两个熔体泵、共挤模块及多层化口模组成。
熔体泵控制熔体流向喂料区形成两平行流层,然后流经一系列的分层单元。
在分层过程中,层的结构经历垂直分成二料流、水平展开及重新合并,从而使层的数量增倍。
很明显n个分层单元将形成22n+1共挤层。
该装置已成功地现4096层、单层厚度低于100nm的纳米层共挤出。
四、发展展望
近年来随着对塑料薄膜性能要求的不断提高以及机械制造技术的发展、自动化控制技术和CAD/CAM/CAE技术的广泛应用,多层共挤出薄膜多层共挤薄膜技术得到了良好的发展,但是仍然存在许多不足,比如“重主机,轻辅机”问题、国内最多薄膜层数为七层,远远落后于国外,等等。
以下是我认为以后我国共挤薄膜的一些发展趋势:
1、大型化发展趋势。
国内已开发出宽幅20米三层共挤薄膜设备,国外已有24米宽幅的共挤薄膜设备。
该类设备主要用于生产温室大棚和土工膜。
2、高质量的薄膜生产要求。
用于食品等包装的多层共挤薄膜外观光泽、平整度、壁厚均匀性、印刷性能要求越来越高。
3、共挤薄膜层数向更多化发展。
国外最多做到12层。
折径5米以上的大型单层设备几乎无人过问。
层数越多,功能性越强。
4、共挤设备向更高效率、节能化发展。
由于市场竞争激烈,薄膜生产商非常重视生产成本,高效、节能的挤出机及辅机是提高市场竞争力的关键。
五、参考文献
[1]张留城,张之栋.共挤出法多层聚合物膜和片材[J],塑料工业.1983,1。
33-38.
[2]占国荣,周南桥.国外多层共挤吹塑薄膜技术[J],塑料制造.2007,10
(2):
107-111.
[3]韩巧玲,张浩翔.三层共挤土工膜生产设备及工艺[J],橡塑技术与装备.2003,29(6):
32-35
[4]苗立荣,张玉霞,薛 平.多层共挤出塑料薄膜机头的结构改进与发展[J],中国塑料.2010,24
(2):
11-20.