DQ产品说明书.docx
《DQ产品说明书.docx》由会员分享,可在线阅读,更多相关《DQ产品说明书.docx(42页珍藏版)》请在冰豆网上搜索。
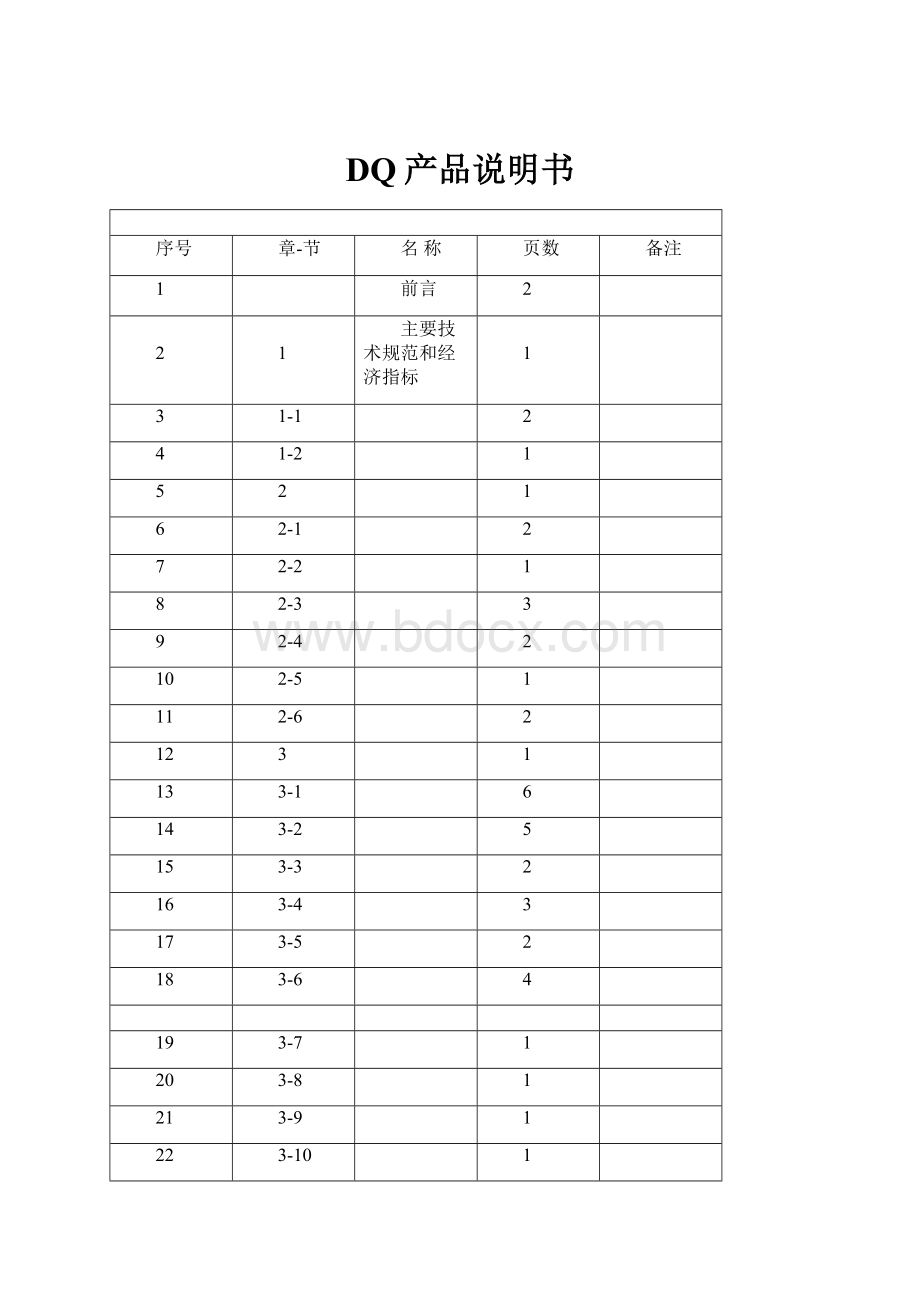
DQ产品说明书
序号
章-节
名称
页数
备注
1
前言
2
2
1
主要技术规范和经济指标
1
3
1-1
2
4
1-2
1
5
2
1
6
2-1
2
7
2-2
1
8
2-3
3
9
2-4
2
10
2-5
1
11
2-6
2
12
3
1
13
3-1
6
14
3-2
5
15
3-3
2
16
3-4
3
17
3-5
2
18
3-6
4
19
3-7
1
20
3-8
1
21
3-9
1
22
3-10
1
23
3-11
12
24
3-12
2
25
3-13
3
26
3-14
5
27
3-15
3
28
3-16
1
29
3-17
4
前言
CN310/538/538型汽轮机是我厂引进和吸收国内外先进技术设计制造的最新式亚临界350MW优化机型,为一次中间再热双缸双排汽凝汽式汽轮机,与相应容量的锅炉和汽轮发电机配套,构成大型火力发电机组,在电网中以带基本负荷为主,也可承担部分调峰任务。
本说明书主要介绍该机组总体设计和本体结构,有关辅机、调节、保安、安装、启动运行和DEH及各系统的详细介绍请参阅下列技术文件:
1交货清单
2热力特性书
3汽轮机保温设计说明书
4螺栓热紧说明书
5汽轮机本体安装及维护说明书
6汽轮机启动运行说明书
7盘车装置说明书
8辅机部套说明书
9润滑油系统说明书
10汽轮机本体及管道疏水系统说明书
11抽汽止回阀控制系统说明书
12自密封汽封系统说明书
13油系统设备安装说明书
14油系统冲洗说明书
15调节、保安系统说明书
16调节、保安部套说明书
17汽轮机安全监视装置说明书
18汽轮机电气监视保护系统说明书
19主机证明书
20辅机证明书
21调节证明书
22安全监视装置出厂证明书
23DEH的电、液所有技术文件由供货商随机提供。
本文件中热力系统的压力一律用绝对压力,油系统的压力一律用表压,并用“(表压)”或“(g)”注明,真空度和负压用文字注明,本说明书采用法定计量单位,它与工程制计量单位的换算关系如下:
力1kgf=
压力1kgf/cm2=
热量1kcal=
注:
左、右定义为:
从汽轮机朝发电机方向看去,左手侧为左,右手侧为右。
前后定义为:
靠近汽机为前,靠近发电机为后。
1主要技术规范和经济指标
1-1主要技术规范
1型号:
CN310/538/538型
2型式:
亚临界、单轴、双缸双排汽、中间再热可调抽汽凝汽式
3额定功率:
310MW(额定工况)
4最大功率:
(VWO工况)
5额定蒸汽参数
新蒸汽:
(高压主汽阀前)538℃
再热蒸汽:
(中压联合汽阀前)538℃
背压:
(设计冷却水温20℃)
6额定新汽流量:
h
7最大新汽流量:
1025t/h
8配汽方式:
全电调(阀门管理)
9转向:
从汽机向发电机方向看为顺时针方向
10转速:
3000r/min
11轴系临界转速(计算值)
第一阶:
(发电机转子一阶)1386r/min
第二阶:
(高中压转子一阶)1733r/min
第三阶:
(低压转子一阶)1773r/min
第四阶:
(发电机转子二阶)3587r/min
*电机临界转速值以电机厂提供的数据为准。
12通流级数
总共26级,其中:
高压缸:
1调节级+8压力级
中压缸:
5压力级
低压缸:
2×6压力级
13给水回热系统:
3高加+1除氧+4低加(除氧器采用滑压运行)
14给水泵拖动方式
15系统设有两台50%容量的汽动给水泵和一台30%容量的电动给水泵,每台汽动给水泵配置一台电动给水前置泵。
16汽封系统:
自密封系统(SSR)
17末级动叶片高度:
1016mm
18末级动叶片环形排汽面积:
2×
19汽轮机本体外形尺寸(长×宽×高)
18500mm×8000mm×6500mm(高度指从连通管吊环最高点到运行平台距离)
20主机重量
~630t(包括高、中压阀门及其支吊架,高、中压主汽管和主汽管支吊架及基架等)。
21最大吊装重量
~98t(安装时,低压外缸下半组合)
~(检修时,低压转子包括起吊工具)
22最大起吊高度
≈9.84m(吊装低压外缸时)
23运行平台高度:
12.6m
24汽轮机与凝汽器连接方式:
弹性
25汽轮机布置方式:
汽轮发电机组为室内纵向顺列布置。
26产品执行标准:
GB5578-85《固定式发电用汽轮机技术条件》
1-2技术经济指标及保证条件
1 符合下列条件时可发额定功率:
a)新蒸汽压力:
±新蒸汽和再热蒸汽温度:
538±5℃
b)冷却水温不超过33℃,冷却水流量不小于额定值
c)加热器按规定投入
2 汽轮机在额定工况下,计算热耗为:
7860KJ/
保证热耗以各工程<<热力特性书>>提供的数据为准。
达到这一保证的必要条件是:
a)新蒸汽和再热蒸汽参数为额定值;
b)背压不高于额定值;
c)按规定的回热系统运行;
d)主给水流量等于主蒸汽流量;
e)发电机效率不低于%;发电机功率因数。
3 如果机组投运后未及时进行热力鉴定试验,应按IEC953-2国际电工委员会参考资料进行老化折扣;汽轮机效率老化折扣如下:
a)3-12个月,每月%
b)13-24个月,每月%
热力鉴定试验的方法、测试仪表精度、测试数据的误差修正、实测热耗的计算方法应符合GB8117-87<<电站汽轮机热力性能验收试验规程>>的规定,经过误差修正的热耗试验值相对于保证热耗的允许偏差为+1%。
2总体设计
2-1机组的运行特点
1 启动状态
本机组启动状态的划分根据是高压内缸上半调节级后内壁金属温度。
冷态启动:
小于150℃温态启动:
150℃~300℃
热态启动:
300℃~400℃极热态启动:
≥400℃
2启动方式
本机组采用高压缸与中压缸两种启动方式。
3运行操作控制方式
运行人员手动方式(手动),运行人员自动方式(半自动),汽轮机自启动方式(全自动)。
4阀门管理
见2-5节。
5转子寿命管理
为了把转子热应力作为指导启动运行的主要依据,并应用寿命损耗概念对机组运行进行管理,本机组配置转子应力监控,它来自一个完整的ATS(汽轮机自动启动)模块,转子应力程序提供应力和温度计算的有关信息给ATS模块,通过这些信息即可作出汽轮机启动和升负荷的判据。
6偏周波运行
非正常周波运行的限制主要由末级叶片、次末级叶片的共振频率决定。
偏周波运行的累计时间限定见《汽轮机启动运行说明书》。
7调峰
本机组可以按定压和定-滑-定两种方式运行。
调峰运行时宜采用定-滑-定运行方式。
机组在90%额定负荷以上时采用定压运行,机组在90%~30%额定负荷时采用滑压运行,机组在30%额定以下负荷时采用定压运行。
这种运行方式能够提高机组变工况运行时的热经济性,减小进汽部分的温差和负荷变化时的温度变化,因而降低机组的低周热疲劳损伤。
若机组年运行时间平均不少于7500小时,调峰运行负荷允许稳定运行时间为:
负荷(%额定负荷) 小时/每年
100% 4500
75% 2000
40% 1000
负荷变化率
定压运行最大3%ECR/min
滑压运行最大5%ECR/min
机组最小负荷
机组最小稳定负荷应取决于锅炉的低负荷能力和机组末级动叶片振动特性,在自动控制没有投油燃烧情况下,燃煤最小稳定负荷是40%额定负荷(以锅炉厂资料为准),汽机允许最小稳定负荷是30%额定负荷。
为了保证低压末级叶片的安全,所有工况下低压缸蒸汽流量不得小于235t/h,相应的压力不得低于。
8其它
本机组在30年使用期间,带厂用电不允许超过10次,每次不允许超过15分钟。
机组甩负荷以后空负荷运行每次不允许超过15分钟。
2-2主蒸汽、再热蒸汽和回热系统
1主蒸汽及再热蒸汽系统
本机组主蒸汽及再热蒸汽系统采用单元制。
从锅炉过热器出来的主蒸汽经过两根主蒸汽管进入高压主汽调节阀,然后再由四根高压主汽管导入高压缸。
在高压缸内作功后的蒸汽通过两个高压排汽止回阀,经两根冷段再热蒸汽管进入锅炉再热器。
再热后的蒸汽温度升高到538℃,压力,再经过两根热段再热蒸汽管进入中压联合汽阀,然后由两根中压主汽管导入中压缸。
Ⅰ级旁路蒸汽从高压主汽阀前引出,经一级减温减压后,排至再热器冷段管。
Ⅱ级旁路蒸汽由中压联合汽阀前引出,再经三级减温减压后排至冷凝器。
2回热系统
本机组有八级回热加热,三个高压加热器,一个除氧器,四个低压加热器,见附图额定工况热平衡图。
除氧器采用滑压运行,工程系统设计和辅助设备选型均需满足滑压运行的要求。
额定供热工况各段抽汽参数和流量见热平衡图。
当加热器切除或新蒸汽参数降低时,为了保证叶片应力不超限,应减负荷限制流量运行。
任何工况下调节级后压力和各段抽汽压力不得超过VWO工况下相应的压力。
表2-2-1额定供热工况各段回热抽汽参数、流量汇总表
抽汽段号
1
2
3
4
5
6
7
8
抽汽器
1
2
3
4
5
6
7
8
抽汽点
(第几级后)
7
9
12
14
正反1
正2
反3
正反4
抽汽压力(MPa)
抽汽温度℃
261
流量t/h
2-3汽轮机本体辅助系统
本机组配置有高压缸预暖及夹层加热系统,以满足冷态、温态高中压联合启动对高压缸温度、胀差控制的需要。
1高压缸预暖系统
为了在冷态启动前对高中压缸进行加热预暖,保证冷态启动前高压调节级后内壁金属温度达到150℃,上下半内、外壁温差小于50℃,高压内缸上下半左右法兰内、外壁温差小于50℃,中压缸进汽处和排汽口处内壁温度超过50℃,以达到降低启动热冲击、避免膨胀不畅或胀差超标的目的,在高排止逆门前的高排管道上设置有高压缸预暖系统。
该预暖系统由高压蒸汽管路及倒暖阀(DN100电动截止阀)组成。
在汽轮机冲转前,高压旁路阀后的蒸汽或辅助蒸汽通过倒暖阀(RFV)进入高压缸。
从高中压缸之间汽封、高压主汽管疏水和高压缸疏水排出,对高压缸进行预加热,通过调整倒暖阀与疏水阀保证缸内压力在~,并按启动运行说明书要求进行保温后暖缸结束。
高压缸预暖期间打开10%高压主汽阀阀位,对高压主汽阀壳、主汽管进行预暖。
预暖蒸汽压力~,温度为200℃~250℃,并保持50℃以上过热度。
2汽缸夹层加热系统
高中压外缸下半设置有夹层加热进汽口,从夹层加热进汽联箱来的蒸汽通过阀门分别进入左右进汽口对高压内缸与高中压外缸之间的夹层进行加热以便在启动过程中对胀差及温度及时进行调整。
高压缸夹层加热系统的投入应根据高中压胀差、高压内缸外壁和高压外缸内壁温差及高压缸的温度情况决定,胀差在允许范围内可以停用高压缸夹层加热系统。
在正常运行时,高压进汽部分处在中压进汽的包围中,内外温差接近于零,高中压间汽封漏汽,正常运行时从高压漏至中压作功,见图2-3-2。
Ⅰ区蒸汽通过隔热环外沿5mm宽的环形间隙进入与高压排汽相通的Ⅱ区,随抽汽进入2#高加()。
Ⅱ区中的温度压力为高压排汽参数,Ⅰ区和Ⅱ区压力相等,在内缸壁和定位环的热幅射作用下,Ⅰ区的温度较接近内缸HP第三级后内壁温度。
高压部分采用上述结构,使得高压内外各区域保持合理的温度和压力分布,热应力和压差引起的机械应力都限制在较低水平。
3应急排放系统
当机组甩负荷时,高压缸、高压导汽管内冗余蒸汽将有可能通过高中压之间的轴封漏入中、低压缸导致机组超速。
在高中压轴封间设置应急排放装置,机组跳闸时,应急排放阀(BDV)快速开启,将大部分冗余蒸汽引入凝汽器,防止机组超速。
图2-3-1汽轮机本体辅助系统
2-4配汽
本机组控制系统具有阀门管理功能,它可以实现调节阀的顺序阀控制和单阀控制以及高、中压阀门关系的协调,以适应不同的启动和运行要求,机组在运行中可以进行两种方式的无扰切换。
两种控制方式对应两种不同的进汽方式,其中顺序阀方式可以实现机组的喷嘴调节运行;单阀方式可以实现机组的节流调节运行。
为减小启动过程中的热冲击,以单阀方式启动即采用节流配汽(全周进汽方式),避免汽缸及转子应力过大,保证机组顺利启动,在达到目标负荷且温度场趋于稳定后可切换到顺序阀方式即喷嘴配汽,保证较好的经济性。
采用喷嘴配汽(部分进汽):
高压部分共有4个调节阀,对应于4组喷嘴,喷嘴组的序号与调节阀序号对应关系见图2-4-1。
当Ⅰ、Ⅱ号调节阀阀杆开启到39.2mm(不包括预启阀行程)时,Ⅲ号调节阀开启;当Ⅲ号调节阀阀杆行程达到39.2mm时,Ⅳ号调节阀开始开启。
采用节流配汽(全周进汽):
高压部分4个调节阀根据控制系统的指令按相同的阀位开启,对应于4组喷嘴同时进汽。
再热蒸汽通过2个中压联合汽阀从汽缸下半右、左两侧分别进入中压部分,中压部分为全周进汽,因此中压调节阀仅采用节流调节方式运行。
中压联合汽阀内主汽阀和调节阀共用1个阀座,由各自独立的油动机分别控制,中压联合汽阀配置见图2-4-1。
调节阀口径Ф510mm,流量在30%以下时起调节作用,以维持再热器内必要的最低压力,流量大于30%时,调节阀一直保持全开,仅由高压调节阀调节负荷。
图2-4-1喷嘴组与高压调节阀对应关系及中压联合汽阀配置示意图
2-5阀门管理
阀门管理配汽技术的指导思想就是要求汽轮机在整个运行范围内能够随意选择调节方式并实现节流调节与喷嘴调节无扰转换。
采用节流调节方式使汽轮机快速启停和变负荷不致产生过大的热应力(减少机组寿命损耗),在正常负荷范围内采用喷嘴调节变压运行方式使机组有最好的经济性和运行灵活性。
在操作盘上有单阀---顺序阀选择按钮,运行人员能够对汽轮机的调节阀门配汽方式进行选择,配汽方式的选择要根据汽轮机的启动运行方式决定。
启动过程:
在汽轮机冲转、升速、并网、带低负荷阶段一般选用单阀节流配汽方式。
因该方式为汽流全周进入高压调节级,使汽缸和转子能均匀地加热膨胀,故能有效降低启动过程中的热应力和调节级动叶的机械应力。
正常负荷运行:
如果负荷变动频繁且变动率较大时,为使汽轮机高压缸温度变化最小,热应力最低,应选用单阀节流配汽方式。
但若机组长期在低于额定负荷稳定运行时则应选用顺序阀喷嘴调节方式以获得较高的热效率。
停机过程:
若正常停机并计划停机后检修,则采用喷嘴调节方式是有利的,因该方式停机后金属温度较低可缩短机组冷却时间。
对于停机时间只有几小时的调峰机组或其它短暂的临时停机,为了使停机后金属温度较高,有利于再次快速启动投运,通常应采用节流调节方式。
2-6旁路系统
汽轮机旁路系统是本机组重要外部系统之一,它具有改善机组启动性能,减少汽轮机寿命损耗和快速跟踪负荷等功能。
合理的旁路设置能满足机组启停时的机炉匹配。
本机组采用40%B-MCR容量的2级串联旁路加3级减温减压器的旁路系统。
高压旁路蒸汽从高压主汽门前引出,经1级减温减压后排至再热冷段;低压旁路蒸汽由中压联合汽阀前引出,经2级和3级减温减压后排至凝汽器。
旁路系统的设计容量参数:
40%B-MCR
旁路系统
进口参数
出口参数
流量
MPa/℃
MPa/℃
t/h
高压旁路(HPBV)
538
*)/
410
低压旁路(LPBV)
*)/538
**)/180
***)
注:
高压旁路流量:
1025×
=410t/h(40%THA旁路)
1025为B-MCR工况主蒸汽流量。
低压旁路流量:
高压旁路流量+高压旁路喷水流量。
*) ──按MCR工况热平衡确定。
**) ──按3级减温减压器前参数确定。
***)──高压旁路的喷水流量是假定按高压旁路通流能力15%考虑。
实际工程使用的旁路系统的容量参数应根据设计院工程设计选型最终确定。
旁路系统见图2-6-1
图2-6-1
3本体结构
本机组为双缸双排汽型式,高中压部分采用合缸结构。
因进汽参数较高,为减小汽缸应力,增加机组启停及变负荷的灵活性,高压部分设计为双层缸。
低压缸为对称分流式,也采用双层缸结构。
为简化汽缸结构和减小热应力,高压和中压阀门与汽缸之间都是通过管道联接。
高压阀悬挂在汽机前运行层下面,中压阀置于高中压缸两侧。
机组总长~18.5m,纵剖面图见附图1。
高压通流部分设计为反向流动,高压和中压进汽口都布置在高中压缸中部,是整个机组工作温度最高的部位。
来自锅炉过热器的新蒸汽通过主蒸汽管进入高压主汽调节阀,再经4根Φ273×40高压主汽管和装在高中压外缸中部的4个高压进汽管分别从上下方向进入高压内缸中的喷嘴室,然后进入高压通流部分。
蒸汽经1个单列调节级和8个压力级作功后,由高中压缸前端下部的2个高压排汽口排出,经2根冷段再热汽管去锅炉再热器,管上各装1个Dg600的排汽止回阀。
通流级第6级后设1段回热抽汽供3#高加,通流级第9级后(高压排汽)设2段抽汽供2#高加。
再热蒸汽通过2根热段再热汽管进入中压联合汽阀,再经2根Φ610×55中压主汽管从高中压外缸中部下半两侧进入中压通流部分。
中压部分共有6个压力级,第3级后有1个3段抽汽口供1#高加,中压排汽一部分从高中压外缸后端下半的4段抽汽口抽汽供除氧器(DTR),大部分从上半正中的一个Φ1400mm中压排汽口进入连通管通向低压缸。
低压部分为对称分流双层缸结构。
蒸汽由低压缸中部进入通流部分,分别向前后两个方向流动,经2×6个压力级作功后向下排入凝汽器。
在正反1级、正2级、反3级、正反4级后依次设有5~8段抽汽口,分别供4个低压加热器~。
3-1高中压外缸
1外缸结构
高中压外缸内装有高压内缸、喷嘴室、隔板套、隔板、汽封等高中压部分静子部件,与转子一起构成了汽轮机的高中压通流部分。
外缸材料为高温性能较好的ZG15Cr1Mo1铸件。
通过强度计算分析,对缸壁筒体的厚度特别是中排及高排处的厚度进行合理的选取,最大壁厚约108mm。
外缸重量~68t(不包括螺栓等附件),允许工作温度不大于566℃。
外缸中部上下有4个高压进汽口与高压主汽管相连,高压部分有安装固定高压内缸的凸台和凸缘,前端下部有2个高压排汽口,下半第7级后有1个抽汽口,通过一根Φ168×8抽汽管与高压内缸第6级后环形集汽腔室相通,抽汽供。
外缸中部下半左右侧各有1个中压进汽口,中压部分有安装1#、2#隔板套的凸缘,下半中压第3级(1#隔板套)后有1个抽汽口(供。
外缸后端上部有1个Φ1400中压排汽口,下部左右侧有2个抽汽口,供除氧器(DTR)和给水泵小汽轮机。
前后两端有安装高压和中压后汽封凹窝和相应的抽送汽管口。
高中压外缸中分面法兰等高设计,左右水平法兰螺栓全部采用GH螺纹。
为减少启动过程中螺栓与法兰温差,降低运行时螺栓的使用温度,特采用大螺栓自流冷却/加热系统,从高压内缸与外缸的定位环之前的区域引入蒸汽至螺栓孔,正常运行时冷却高温区中分面螺栓,再由1#、2#隔板套之间的抽汽口排出(见图3-1-1)。
螺栓直径从汽缸中部至中压排汽端依次递减,其中:
●前部及中部左右水平法兰(从2号隔板套凸肩至高压排汽腔室)共有36个(GH)6″×1318的特制双头螺栓,2号隔板套凸肩处左右水平法兰有2个(GH)5″×1268的特制双头螺栓,上述两种螺栓材料均为20Cr1Mo1VNbTiB,允许工作温度不大于570℃。
●中压排汽腔室两侧水平法兰有10个(GH)4″×1216特制双头螺栓,后部横向水平法兰有2个(GH)31/2″×1190特制双头螺栓和14个(GH)3″×1166特制双头螺栓,这3种螺栓材料均为25Cr2MoVA,允许工作温度不大于510℃。
与上述(GH)6″规格螺栓相配的为罩螺母,与其余螺栓相配的为特制开槽螺母。
螺栓与对应螺母一一编号,螺母与汽缸水平法兰螺柱孔刮面在总装时进行研磨,保证接触面密封良好,同时改善螺栓受力状况。
安装时螺栓需要热紧,要求必须使用汽轮机螺栓电加热器,不允许用氧乙炔火焰加热。
使用螺栓伸长测量工具对螺栓伸长进行测量。
螺栓伸长满足设计要求,即可保证螺栓预紧力的要求。
热紧数值、热紧顺序及注意事项见<<螺栓热紧说明书>>。
图3-1-1高中压外缸大螺栓自流冷却/加热示意图
2外缸的支承
外缸由下缸中分面伸出的前后左右4个元宝形猫爪搭在前轴承箱和中低压轴承箱的水平中分面上,称为下猫爪中分面支承结构,见图3-1-2。
这种结构有下列优点:
a)动静间隙不受静子温度变化的影响;
b)汽缸中分面联接螺栓受力状态和汽缸密封性好。
高中压缸与前轴承箱之间的推(拉)力靠汽缸下半前端与前轴承箱之间的“H”梁形式的推拉机构传递,为使汽缸与前轴承箱保持中心一致,“H”梁与汽缸下半前端及前轴承箱之间均采用圆柱销定位,见图3-1-3。
安装时“H”梁电机端(与汽缸下半前端联结)相对机头端(与前轴承箱联结)冷态标高高出1mm,从而得到1mm预变形以减小其在工作状态下的热变形,达到减小其在工作状态下的热应力的目的。
该推拉机构的优点在于其“H”梁本身:
a)在平行于汽缸中分面的平面内刚度较大。
借助于前轴承箱与前基架之间的导向键可保证高中压缸在受到外部管道不平衡推力以及自身左右不均匀热膨胀影响的情况下,仍能保持良好的对中。
b)在纵剖面内其刚度相对较小。
这样前轴承箱与高中压缸之间在铅垂方向客观上存在的较大胀差将不会对“H”梁本身造成过大的热应力。
高中压缸与中低压轴承箱之间的推(拉)力靠猫爪下面的横向键传递。
为使汽缸与中低压轴承箱保持中心一致,汽缸下半后端设有立键,见图3-1-4。
3高压进汽管
高中压外缸中部上、下、左、右共有4只高压进汽管,分别通过螺栓固定在内缸上,高压进汽管两端靠密封圈分别与喷嘴与外缸联结。
能吸收内、外缸及喷嘴间的胀差。
进汽管联结图见图3-1-5。
4高压第7级后抽汽管
下半第7级后有1个抽汽口,通过一根Φ168×8抽汽管与高压内缸第7级后环形集汽腔室相通,抽汽管两端靠密封圈分别与内缸与外缸联结,能吸收内、外缸间的胀差。
抽汽管通过用螺栓固定在外缸上的法兰与外部管道相联结。
抽汽管联结图见图3-1-6。
图3-1-2前、后猫爪安装图
图3-1-3汽缸推拉装置装配图
图3-1-4高中压外缸后部与中低压轴承箱立键装配图
图3-1-5进汽管联结图
图3-1-6高压第7级后抽汽管联结图
3-2高压内缸
1内缸结构和安装定位
为降低高中压外缸的使用压力,高压内缸采用整体内缸。
进汽端装有4组喷嘴室,缸内支承高压2~9级隔板,工作参数较高,因而选用材料ZG15Cr1Mo1,允许工作温度不大于540℃。
内缸外壁对应于第2级隔板处有一个定位环,其外缘的凹槽与外缸上相应位置的凸缘配合,确定内缸轴向位置,构成内缸相对于外缸的轴向膨胀死点。
内缸外壁第5级处设置隔热环,将内外缸夹层空间分为2个区域,这样可以降低内缸内外壁的温差,提高外缸温度,减少外缸与转子的膨胀差,在第6级后内外缸之间设置