特种加工作业.docx
《特种加工作业.docx》由会员分享,可在线阅读,更多相关《特种加工作业.docx(16页珍藏版)》请在冰豆网上搜索。
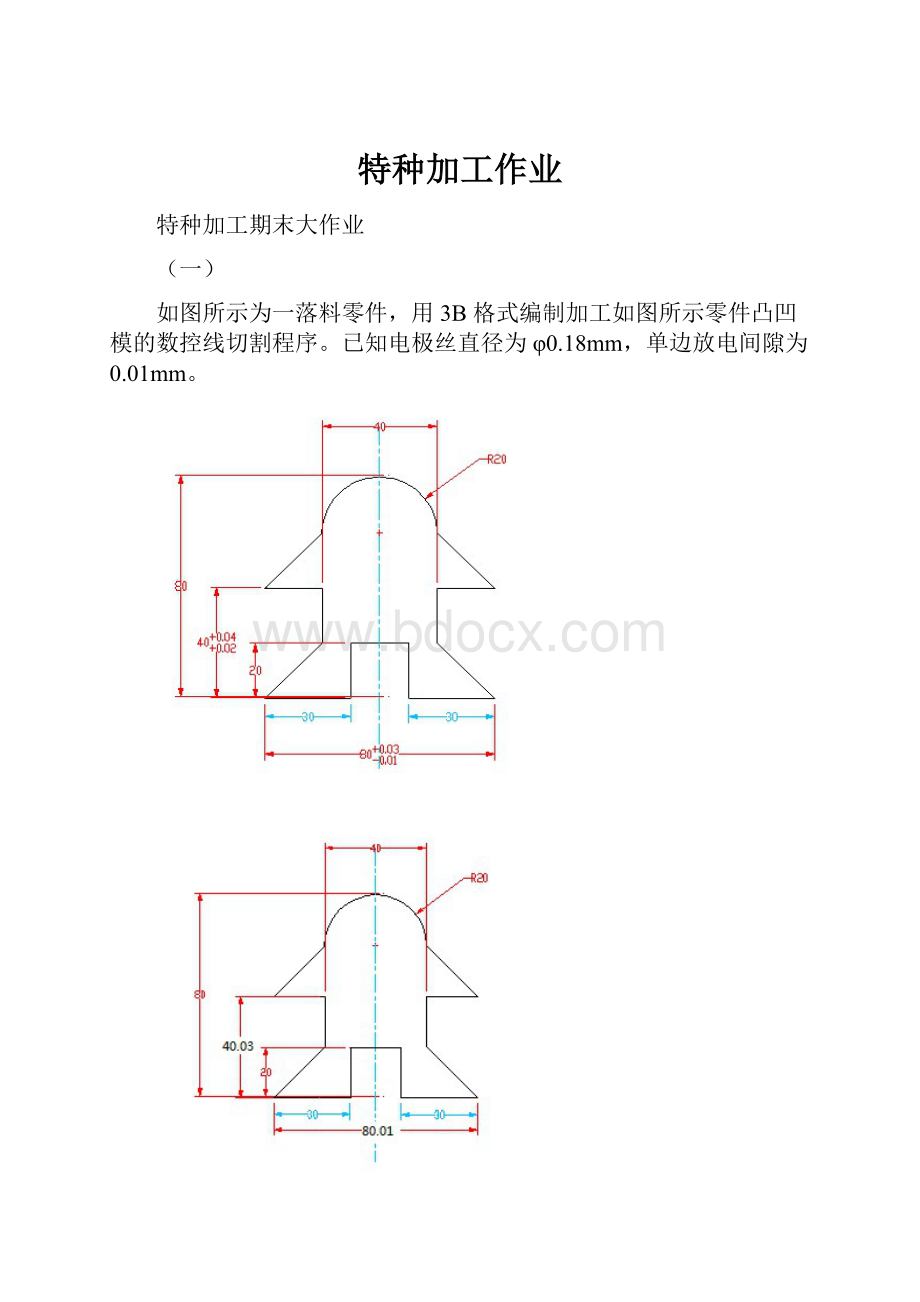
特种加工作业
特种加工期末大作业
(一)
如图所示为一落料零件,用3B格式编制加工如图所示零件凸凹模的数控线切割程序。
已知电极丝直径为φ0.18mm,单边放电间隙为0.01mm。
零件图零件图(平均尺寸)
工艺分析1右图图示尺寸为平均尺寸,故作相应偏移就可按此尺寸编程
2凸模在模具中起着很重要的作用,它的设计形状、尺寸精度及材料硬度都直接影响模具的冲裁质量、使用寿命及冲压件的精度。
在实际生产加工中,由于工件毛坯内部的残留应力变形及放电产生的热应力变形,故应首先加工好穿丝孔进行封闭式切割,尽可能避免开放式切割而发生变形。
3凸模的轮廓线与毛坯边缘的宽度应至少保证在毛坯厚度的1/5。
4凹模在线切割加工前,模板已进行了冷加工、热加工,内部已产生了较大的残留应力。
因此,模板在线切割加工时,随着原有内应力的作用及火花放电所产生的加工热应力的影响,将产生不定向、无规则的变形,使后面的切割吃刀量厚薄不均,影响了加工质量和加工精度。
针对此种情况,对精度要求比较高的模板,通常采用4次切割加工。
第1次切割将所有型孔的废料切掉,取出废料后,再由机床的自动移位功能,完成第2次、第3次、第4次切割。
这种切割方式能使每个型孔加工后有足够的时间释放内应力,能将各个型孔因加工顺序不同而产生的相互影响、微量变形降低到最小程度,较好地保证模板的加工尺寸精度。
5预先在毛坯的适当位置用穿孔机或电火花成形机加工好Φ1.0—Φ1.5mm穿丝孔,穿丝孔中心与凸模轮廓线间的引入切割线段长度选取3mm。
零件在毛坯上的定位
凹模电极丝中心轨迹凸模电极丝中心轨迹
凹模凸模
确定补偿距离电极中心轨迹如图中双点划线所示。
补偿距离为:
△R=(0.18/2+0.01)mm=0.1mm
一、凹模
切割路线的选择
加工路线的选择
在加工中,工件内部应力的释放要引起工件的变形,所以在选择加工路线时
应尽量避免破坏工件或毛坯结构刚性。
合理地选择切割路线可简化编程计算,提高加工质量。
根据分析,选择穿丝孔在1
顺时针走刀切割顺序按1→2→3→4→5→6→7→8→9→10→11→12→13→14→15→1
计算交点坐标将电极丝中点轨迹划分成单一的直线或圆弧段(每点坐标以其前一点为坐标原点,圆弧则以圆心为坐标原点).即点2的坐标值以坐标轴x1-y1来计算,点3的坐标以x2-y2来计算……
2(-22850,0)3(19859,0)4(19900,0)5(19859,-19859)6(-19859,0)7(0,-20171)8(19859,-19859)9(29659,0)10(0,20000)11(-20210,0)12(0,-20000)13(-29659,0)14(19859,19859)15(0,20171)
3B程序编制
◆B20359GxL3;
(2)
◆B1B1B19859GxL1;(3)
◆B39800GySR3;(4)
◆B1B1B19859GxL4;(5)
◆B19859GxL3;(6)
◆B20171GyL4;(7)
◆B20000GyL2;(8)
◆B29659GxL3;(9)
◆B20000GyL2;(10)
◆B20210GxL3;(11)
◆B20000GyL4;(12)
◆B29659GxL3;(13)
◆B1B1B19859GxL1;(14)
◆B20141GxL2;(15)
◆B3000GxL1;
(1)空走
二、凸模
切割路线的选择合理地选择切割路线可简化编程计算,提高加工质量。
根据分析,选择穿丝孔在1点,切割顺序按1→2→3→4→5→6→7→8→9→10→11→12→13→14→15→1
计算交点坐标将电极丝中点轨迹划分成单一的直线或圆弧段(每点坐标以其前一点为坐标原点,圆弧则以圆心为坐标原点)。
即点2的坐标值以坐标轴x1-y1来计算,点3的坐标以x2-y2来计算……
2(20459,20495)3(0,19925)4(-20141,0)5(20141,20141)6(20100,0)7(20141,-20141)8(-20141,0)9(0,-19925)10(20141,-20141)11(-30341,0)12(0,-20000)13(-19810,0)14(0,-2000)15(-30341,0)
3B程序编制
◆B22895GxL1;
(2)
◆B19925GyL2;(3)
◆B20171GxL3;(4)
◆B1B1B20171GyL1;(5)
◆B20100GxSR3;(6)
◆B20141GxL4;(7)
◆B20141GxL3;(8)
◆B19925GyL4;(9)
◆B1B1B20141GxL4;(10)
◆B30341GxL3;(11)
◆B20000GyL2;(12)
◆B19925GxL3;(13)
◆B20000GyL4;(14)
◆B30341GxL3;(15)
◆B1B1B3000GxL3;
(1)
装夹方法
装夹工件时,必须保证工件的切割部位位于机床工作台纵向、横向进给的允许范围之内,以避免超出极限,同时应考虑切割时电极丝的运动空间。
夹具应尽可能选择通用(或标准)件,所选夹具应方便装夹,以便于协调工件和机床的尺寸关系。
选用桥式支撑方式装夹。
如图所示,在通用夹具上放置垫铁后再装夹工件,装夹方便,这种方式对大、中、小型工件都适用。
(二)
下图所示型腔表面粗糙度Ra1.25
(1)设计加工型腔的精加工工具电极(不采用平动修整的工艺方法)。
(2)根据工艺参数曲线图表确定峰值电流、脉宽及脉间。
并说明该规准所能达到的加工效率、电极损耗率及单边侧面放电间隙。
型腔形状、位置尺寸如下图所示:
型腔内部轮廓图:
一、工具电极形式选择
根据电极外形尺寸的大小与复杂程度、电机结构的工艺性等因素综合考虑,可分为:
整体式电极、组合式电极、镶拼式电极。
组合式电极:
在同一个凹模上有多个型孔时,可将多个电极组合在一起,一次穿孔完成各型孔的加工,这种电极称为组合式电极。
镶拼式电极:
形状复杂,整体加工困难的电极,可采用镶拼式结构。
根据工具电极的部分参数及相关要求,择优选择电极形式为整体式电极
二、选择电参数
在型腔精加工时,需按表面粗糙度(见书本图2-36)来选择脉宽和峰值电流。
而表面粗造度应优于R1.25µm,一般都选用窄脉宽和小峰值电流进行加工,从而再可根据图(见书本图2-35,图2-37和图2-38)来查出相应参数选择,如放电间隙、腐蚀速度和电极损耗。
相应参数选择归纳如下表:
i峰值
4.3
5.4
10
13
16
21
27
t0脉冲宽度
110
25
7
4
2.7
2.3
2
V单边间隙
0.020
0.025
0.025
0.025
0.020
θ%蚀除速度
3.5
4.5
5
7
8
8
10
S电极损耗
1.2
12
70
80
型腔模的加工比较困难,因为是不通孔加工,工作液循环和电蚀产物排除条件差,工具电极损耗后无法靠主轴进给补偿精度,金属蚀除量大,其次是加工面积变化大,加工过程中店规准的变化范围大,并由于型腔复杂,电极损耗不均匀,对加工精度影响大。
因此对型腔模电火花加工,既要求蚀除量大,加工速度高,又要求电极损耗低,并保证所要求得精度和表面粗糙度。
依据精加工的电参数,最主要应注意的是:
表面粗糙度、精度(放电间隙)、生产效率和电极损耗。
应尽量使腐蚀速度快,电极损耗小,峰值电流小(与尖角有关),所以择优选择第一组数据,i峰=4.3,t0=110,v=0.02,θ%=3.5,s=1.2。
三、电极尺寸计算
电极尺寸与所加工模具的大小、形状、复杂程度有关;与电极材料、电加工参数、深度、余量及间隙有关。
水平尺寸确定:
计算公式为a=A±kb
其中:
a为电极水平方向尺寸,b为电极单边缩放量(单边火花放电间隙),K为系数,A为型腔图样上的名义尺寸
设计电极水平尺寸时注意:
1)型腔图样上的名义尺寸A应取中值尺寸。
2)计算出的电极尺寸应规定公差,一般可取凹模型孔公差的1/2—1/3
单边放电间隙S=0.02a为取相应尺寸的中值尺寸
a1=40.02-0.02=40
c=20
a3=100+2X0.02=100.04
a4=20.01-2X0.02=20.97
a5=19.99+2X0.02=20.03
a6=80+2X0.02=80.04
R1=20+0.02=20.02
R2=20-0.02=19.98
将上述尺寸进行标注,而公差可取型腔的1/2,电极零件形状图如下图所示:
根据粗糙度的要求,电极的Ra值要比型腔的Ra值高一档次,故而可取电
电极高度方向尺寸确定
高度方向尺寸设计时应考虑型腔深度、压板余量、夹板尺寸等等诸多因素。
型腔深度20cm,压板余量留2cm,电极放电间隙 s=0.03mm。
电极总高度H的确定:
H= L1+L2
L1:
电极每加工一个型腔,在垂直方向的有效高度,包括型腔深度和电极端面损耗量,并扣除端面加工间隙值。
L2:
考虑到加工结束时,电极夹具不和夹具模块或压板发生接触,以及同一电极需重复使用而增加的高度。
总高度 H= L1+L2=20-0.02+20=39.98mm
四、校核电流密度
加工面积小时不宜选择过大的峰值电流,否则放电集中,易于拉弧。
一般小面积时以保持3-5A/cm2,大面积时以保持1-3A/cm2的视在电流密度为宜。
依据这个我们可以知道电流密度适宜。
五、防止产生塌角
考虑到其他因素的影响,如排气孔,充油孔,脉肩等,应在电极相应部位进行适当的加工,尤其是尖角部位,要防止塌角的产生。
处理后的电极工具如下图所示:
六、排气孔和冲油孔的设计
当型腔加工时应及时将电加工过程中产生的气体排出,否则,容易出“放炮”现象。
放炮造成的震动容易使工件错位。
而且考虑到电火花加工时对工作液的要求,
为了保证加工零件的精度,有时我们还应该适度的开设冲油孔保证工作液,及时进行排屑。
型腔加工一般为盲孔加工,排气、排屑比较困难,会影响加工速度、定性和表面质量。
在不易排屑的拐角、窄缝处开冲油孔。
但冲油孔冲、抽油时应该注意压力不能过大,冲抽油压力一般为20KPA左右,可随深度的增加而增加。
冲油压力增加,电极损耗也增加。
在蚀除面积较大以及电极端部有凹入的部位开排气孔,孔径一般为φ1-φ2。
若为一个孔以上,则孔距一般20-40左右,孔要适当错开。
七、装夹方式确定与校正
根据设计电极参数,考虑到为了方便有效调节电极相对位置等因素,我们可采用如图所示装夹形式。
电极装夹好后必须进行校正才能加工,不仅要调节电极与工件基准面垂直,而且需在水平面内调节、转动一个角度,使工具电极的截面形状与将要加工的工件型孔或型腔定位的位置一致。
校校正常用的几种方法如下:
1、当电极直臂面较长时,可用精密角尺对光校正或百分表校正。
2、可按电极或电极上固定板端面作辅助基准校正电极,这是使用百分表检验电机与工作台平行度。
3、对没有直臂面的电极,在校正时是比较困难的,只有采用精规准、小电流放电打印法,使用电极与工件四周火花放电均匀,已完成校正和找正工作。
下图为所设电极三维造型图: