水泥窑余热电站投入运行后电站及水泥窑生产过程中容易Word文档格式.docx
《水泥窑余热电站投入运行后电站及水泥窑生产过程中容易Word文档格式.docx》由会员分享,可在线阅读,更多相关《水泥窑余热电站投入运行后电站及水泥窑生产过程中容易Word文档格式.docx(17页珍藏版)》请在冰豆网上搜索。
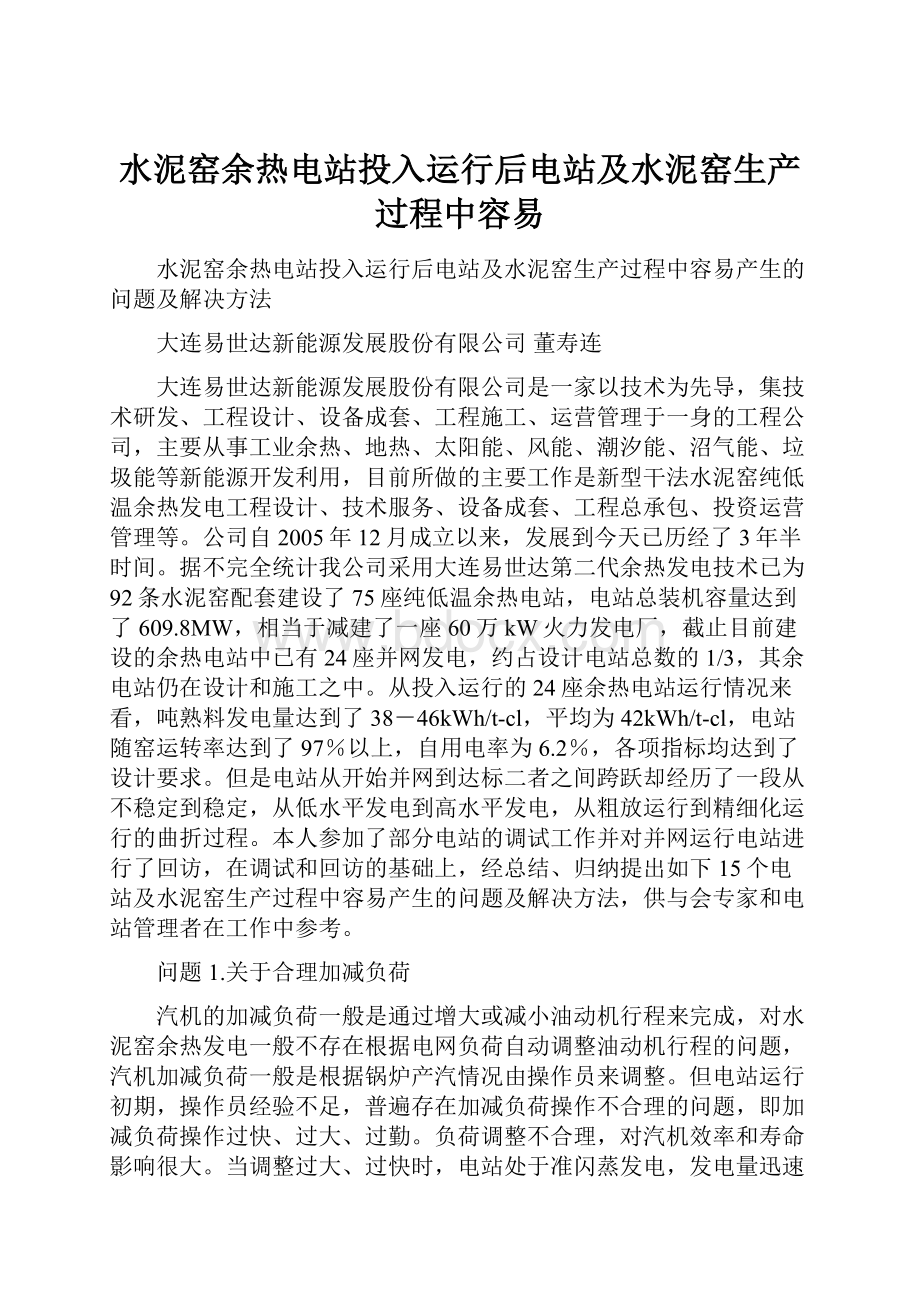
汽机真空降低一般与汽轮发电机密闭性、射水抽汽器特性、凝汽器铜管胀口完好性,冷却水温和冷却水量以及凝汽器铜管表面热阻有关,当检查排除汽轮发电机密闭性、射水抽汽器性能因素后,重点通过加强操作维护来提高汽机真空。
如某厂为降低自用电率,只开一台循环水泵,循环水量不足导致汽机真空降低,排汽温度升高。
还有某厂原水杂质多,过滤不严格导致铜管表面结垢,热阻增大,真空降低,排汽温度升高。
还有某厂循环水加药不严格导致铜管表面粘挂微生物导致热阻增大,真空降低,排汽温度升高。
我们回访中发现这一问题很严重,讲明原因,危害及处理办法后。
这些电站很重视,均采取了行之有效的解决办法。
如山东济南某厂对冷凝器进行酸洗后,每天再用胶球清洗装置做一次清洗,现汽机真空已由过去的0.01MPa(表压-0.090MPa)达到0.006MPa(表压-0.094MPa),提高0.004MPa;
排汽温度由45.8℃降为38℃,下降了7.8℃;
发电量提高450kW左右,由于效果显著许多厂前去学习参观,目前山东平阴某厂、安丘某厂等均采用了酸洗和胶球清洗装置,均收到了预期效果。
问题3.关于SP炉低压调温蒸汽段
自从水泥窑配套余热锅炉后,余热的合理使用问题应当是一个首要问题,如何做到合理使用水泥窑余热呢?
我们的指导思想是:
一个根据和一个坚持。
一个根据是:
根据梯级利用原理,即根据水泥窑余热分布,做到高能高用,低能低用,即将450~550℃高温余热用于生产过热蒸汽,将210~400℃中温余热用于生产饱和蒸汽,将160~220℃低温余热用于生产低压蒸汽和原料烘干,将价值很低的150℃以下的低品位余热用于循环风。
一个坚持是:
坚持“能”尽其材,“量”尽其用。
按照这一原理我们利用窑头冷却机前部500℃高温余热,设计了独立过热器,利用窑头电收尘排出的100℃低温余热,设计了篦冷机循环风系统,利用窑尾烘干温度在170~220℃变化的实际,设计了SP炉低压调温蒸汽段,通过调节SP炉低压调温蒸汽段的低压蒸汽产量使出SP炉废气温度从170~220℃变化,以满足不同烘干要求。
但是一些刚并网发电单位甚至有些运行已很长时间的单位,如:
最近并网的湖北某电站,浙江绍兴某电站,对这一指导思想仍未完全理解。
表现比较突出的就是SP低压调温蒸汽段使用问题。
这些单位只利用了它的产汽功能,而忽略了它的调节功能。
当原料温度降低、水分增大,需要较高的烘干温度时,不是通过调节SP低压调温蒸汽段的低压蒸汽产量的方式来解决,而是通过开启旁通阀门的方式来完成。
采取后一方式调节是严重损失发电量的,而采用前一方式调节其电量损失较少。
通过计算,采用前一方式调节其电量损失:
对2500t/d水泥窑余热电站为0~320kW,平均为160kW;
对5000t/d水泥窑余热电站为0~650kW,平均为325kW;
而用后一方式调节其电量损失:
对2500t/d水泥窑余热电站为0~880kW,平均为440kW;
对5000t/d水泥窑余热电站为0~1990kW,平均为995kW;
与前一方式相比,电量损失:
对2500t/d水泥窑余热电站平均增加280kW;
对5000t/d水泥窑余热电站平均增加670kW;
目前以第一代余发电技术设计的水泥窑余热电站,因无调温低压蒸汽段,只能采取后一方式调节烘干废气温度。
因此余热的利用不够合理,浪费仍比较严重。
通过我们回访和现场讲解,逐步纠正了一些单位的错误操作,发电量明显得到提高,如湖北某电站,纠正前平均发电量为8500kW,纠正后为平均发电量为9300kW,平均提高800kW;
再如浙江绍兴某1000t/d水泥窑电站,纠正前平均发电量为2200kW,纠正后为平均发电量为2400kW,平均提高200kW;
事实上,SP炉低压调温蒸汽段除具有以上调温功能外,还具有调湿功能。
如窑尾采用电收尘器,SP炉投运后收尘效果会受到影响,为了不影响收尘效果,将SP炉生产的低压蒸汽用于废气增湿(相应的减少发电量),这样可解决余热电站对窑尾收尘效果的负面影响问题。
目前一些单位没有使用好SP炉低压调温蒸汽段另一主要原因是培训工作还没有完全到位,操作员对余热的质和量的概念没有完全理解,对SP炉低压调温段设置的作用和目的还不清,对SP炉低压调温蒸汽段的操作要领还没有掌握。
因此要加强对电站操作管理人员技术培训。
问题4.篦冷机操作与管理
篦冷机作为熟料烧成过程中重要机组,担负着熟料冷却和热量回收任务。
1370℃不同粒径的高温熟料从喂料端进入冷却机并平铺在篦床上,在篦板推力的作用下向出料端移动,在移动过程中篦下冷却空气源源不断地通过篦板穿过料层,与热物料进行热交换,热交换结果是熟料被冷却,空气被加热。
熟料的冷却可近似地看作为一维不稳态冷却过程,过程中冷却时间基本一定,冷却风量基本一定,因不同时段的传热温差不同,传热速度也不一样,开始阶段非常快,以后迅速减慢,前1/3时间段几乎完成了全部换热量的60~70%。
由于出窑熟料的温度、液相量、颗粒级配、比热、产量、布料均匀性时常变化,而传热又对熟料温度、液相量、颗粒级配、比热、料量、布料等非常敏感,因此前期传热特点是快速而多变。
由于影响因素多,操作参数相关性差,因此熟料冷却只能模糊控制。
这种控制对熟料烧成影响不大。
但对窑头余热锅炉影响却十分大,表现比较明显的是,窑工艺状况虽未发生异常,但进ASH和AQC炉的却做出了较大的反应。
为减弱上述影响,可通过以下操作解决。
1.密切关注二次风温、三次风温及其它们的温差。
一般出窑熟料物性参数变化对二次风温影响不大,但对三次风温影响较大。
此时可通过观察三次风温和三次风温与二次风温差值变化来判定窑况的改变,并及时采取应对措施。
一般当三次风温升高或三次风温与二次风温差值变小时,可减慢篦速,或减小鼓风风压,或减慢篦速和减小鼓风风压同时进行。
反之,当三次风温降低或三次风温与二次风温差值变大时,可加快篦速,或增加鼓风风压,或加快篦速和增加鼓风风压同时进行。
2.密切关注各风室鼓风机的风门开度、转速及电流。
目前操作员只注意鼓风机的风门开度和转速,却忽视了鼓风机的电流。
因为当出窑熟料物性参数发生变动后,各风室通风阻力将会发生微弱的变化,进而引起鼓风量变化,因此风机电流或风机功率将有所变化。
当电流或功率有减小趋势时,应有意识的开大风门或增大转速,并将电流或功率控制在更高的参数值上。
反之,当电流或功率有增高趋势时,应有意识的减小风门或降低转速,并将电流或功率控制在更低的参数值上。
上述操作应与三次风温或三次风温与二次风温差值变化相兼顾,操作中尽量采用调风量的办法,最好不要调篦速,调篦速会导致更多因素变化,使篦冷机更难控制。
篦速控制要与下料量和窑速保持一致。
3.加强篦板使用与维护,做到同室同期,严禁同室新老混用,尤其是高温室和中温室。
我们知道不同龄期的篦板,孔隙率不同,新篦板孔小,老篦板孔大,同用一个室会导致上风不均匀,熟料冷却不好,废气温度降低,热效率下降。
4.加强配料,加强均化,加强热工检测,定期对计量设备进行标定,稳定窑的热工制度。
5.定期开门检查篦冷机内熟料结粒情况,布料情况,红河情况等。
6.两个余风风门的开启,破碎上部的余风烟囱常开,篦冷机的余风根据排气温度来开户启。
问题5.关于过热器积灰(结皮)堵塞
在并网运行的电站中了解到,由于过热器工作温度的关系(设计在500~550℃,有些电站实际高达600~700℃),因此不同程度地存在着过热器堵塞问题(06年及07年先期投产的余热电站中有个别电站余热过热器存在积灰堵灰问题,由于发现堵灰问题后修改了过热器的结构设计,因此近年投产的电站已不存在这个问题)。
过热器堵塞主要发生在进口2~4排换热管的翅片的间隙中,密实、坚固,不易清除。
过热器堵塞影响过热器通风,影响蒸汽过热度,影响发电量,情况严重时还危及电站安全运行。
从形成过热器堵塞物质来看:
一种是黄料粉,另一种是熟料粉。
前者是因窑串料,大量生料粉串入冷却机并在冷却机鼓风作用下分散悬浮进入过热器,导致过热器堵塞。
这种情况下形成的堵塞,速度快,分布均匀,阻力大,但质地比较松软,比较容易清除。
后一种情况形成的堵塞是逐渐形成的,与温度有直接关系,温度低时形成速度比较慢,温度高时形成速度比较快,堵塞物质是水泥熟料,其与换热管和换热管的翅片结合紧密、坚固,很难清除。
前一种情况形成的堵塞比较容易理解,主要与高温度和大粉尘浓度有关。
后一种情况形成的堵塞比较复杂,从形成过程和现象分析,后一种堵塞与熟料成分和操作温度有关。
高温熟料含有液相粘性物质和挥发性物质,这些物质遇温度较低的换热管和换热管的翅片后并在其上冷凝结晶,粘挂,从而形成坚固堵塞物质。
过热器堵塞一旦形成,很难彻底清除,因此过热器堵塞本着预防为主,定期清理为辅,主辅兼备的办法加以控制。
措施主要有:
⑴严格控制过热器进口烟气温度
蒸汽过热不仅需要较高的烟气温度,还要有一定烟气数量。
由于冷却机内高温风数量有限,当少量提取时,温度高,流量小;
当大量提取时,温度低,流量大;
因此可通过调整高温风流量的办法来调整过热器温度。
具体操作时以高温Ⅰ为主,以高温Ⅱ作为补充,适当增大过热器通风量,以确保进入过热器的烟气温度不至太高,又不影响蒸汽过热。
为便于操作,过热器进口烟气温度控制在500℃,最高不应超过550℃。
⑵将进口几排翅片管改成光管
由于光管的附着力差,不易结皮积灰,它的换热可使烟气降温,便利进入翅片管烟气温度降至500℃以下。
因此可大大减轻过热器堵塞问题。
⑶在进口适当位置装设吹扫装置
目前普遍采用的过热器堵塞清扫装置主要有:
超声波除灰器,乙炔爆燃吹灰器,蒸汽吹灰器等。
从使用情况看均有一定的效果,超声波除灰器价格较贵,乙炔爆燃吹灰成本较高,比较好的是蒸汽吹灰。
建议在过热器进口装设蒸汽吹灰装置。
⑷定期更换备用管束
由于每次停机时间短,不能对过热器进行彻底清理,因此在大修时,用备用管束替换工作管束,然后对换下的工作管束进行下线清理。
清理干净后,留作备用管束备用。
⑸加强与水泥中控配合,发现水泥窑串料及时关闭过热器进口阀门,同时打开放汽阀门。
问题6.关于生料磨操作调整
生料制备一般都采用烘干兼粉磨工艺,按主机设备不同分为管磨生料制备系统和立磨生料制备系统。
该系统可使最大入磨水分5%的配合物料,经烘干后达到出磨水分0.5%。
所需热源由窑尾C1筒提供,废气温度通过预增湿调整到入磨要求温度。
一般管磨烘干用风较少,但要求烘干温度较高,一般为250~280℃,控制出磨废气温度80℃;
而立磨烘干用风较多,但要求烘干温度较低,一般为210~250℃,控制出磨废气温度90℃。
考虑原料入磨系统均使用了三道锁风装置,漏风较少;
再有实际入磨物料水分不高,一般在2.0~3.5%之间,因此实际入磨温度:
管磨为190~230℃;
立磨为180~220℃。
出磨温度:
管磨为80℃;
立磨为90℃。
所需烘干用出C1出口废气需阶段增湿降温后再入磨。
当由SP余热锅炉降温取代阶段增湿降温后,由于前者含水量极少,后者含水量较高。
因此同样温度条件下的废气,前者干燥能力较强,后者较差。
换句话说,对同样烘干能力废气,前者废气温度较低,后者温度较高。
根据我们的经验,出SP余热锅炉温度调整为:
管磨为170~210℃;
立磨为160~200℃。
出磨控制温度调整为:
管磨为70℃;
立磨为80℃。
问题7.关于煤磨热风管道改造与操作调整
煤磨烘干热源一般取自篦冷机中部靠前位置,提取温度一般为300~400℃,而煤磨烘干用废气温度一般为200~250℃,因此热风在入磨前需配入大量冷风。
这样将造成大量高品位余热资源浪费,为减少浪费,增加收益,一般采取高低温风搭配的办法加以解决。
高温风仍从原取风口提取,低温风从原余风排出管道抽取。
两股热风汇合后入磨,两股热风调整由中控员通过遥控设在两股热风管道上的电动蝶阀来完成。
控制参数:
高温风:
300~400℃高温阀:
55~28%
低温风:
120℃低温阀:
45~72%
入磨风:
200~250℃
出磨风:
70℃
问题8.关于耐火浇注料的使用维护
在冷却机经过热器到AQC锅炉及冷却机到AQC锅炉的联接管道及沉降室中使用耐火浇注料。
耐火浇注料的使用与维护水泥厂都很有经验,主要把握三点:
1.选料合理:
即根据使用部位的技术要求进行选料,对冷却机经过热器到AQC锅炉及冷却机到AQC锅炉的联接管道及沉降室,由于温度不高,废气中化学成分稳定,含尘浓度不高,因此选用GT-13N普通耐碱浇注料即可。
2.施工规范:
⑴把钉按图纸要求加工,焊接要牢固,间隔尺寸符合图纸要求,表面涂沥青,沥青厚度均匀。
⑵硅酸钙板粘贴做到灰浆饱满,灰缝均匀,不超过2mm,硅酸钙表面要刷防水漆。
⑶模板支护要符合要求。
⑷浇注料必须在搅拌机中搅拌,先干混,后加水,水灰比控制在6~8%,同一锅料要求30分钟内用完。
⑸浇注时要用振捣棒振捣密实。
⑹按图纸要求预留膨胀缝,膨胀缝应留设在锚固件间隔的中间位置。
3.严格的烧烤养护制度:
根据设计要求绘制的升温曲线,对浇注料进行烧烤养护。
烧烤中防止升温过快发生爆裂,确保水分正常排出。
问题9.关于旁路阀漏风
SP旁路阀门的漏风对发电量影响很大,旁路阀门每漏风1%,发电量下降0.6%,因此必须严格控制,设计要求旁路阀漏风率为2%,最大不应超过3%,当漏风率超过3%时,可能阀板变形或阀轴活动,当经过详细检测、检查之后,应采取措施修复。
问题10.关于余风分离和甩风
水泥窑配套余热电站后,冷却机后部形成的占冷却机30~40%、温度约90~150℃左右废气必须及时分离,并经冷却机余风管道排掉,否则将严重影响系统发电效率。
对2500t/d水泥窑,若低温废气分离不净,排气温度每上升1℃发电量下降5.8kW。
对5000t/d水泥窑,若低温废气分离不净,排气温度每上升1℃发电量下降11kW。
对2500t/d水泥窑,当高温废气无法分离随即排出,每多排出200~250℃热风10000Nm3/h,发电量将下降102kW;
对5000t/d水泥窑,当高温废气无法分离随即排出,每多排出200~250℃热风10000Nm3/h,发电量将下降131kW。
事实上,由于无法分离多排出的热风不只10000Nm3/h。
如5月18日对黄石某电站标定:
余风温度为180℃,余风风量为130000Nm3/h,相当于多排200~250℃热风67000Nm3/h,由此导致发电功率下降为897kW。
导致余风温度偏高,风量偏大的主要原因是冷却机内的高温气层运动,个别厂还有206阀、207阀失灵等原因,解决措施可通过在冷却机加设挡风板,以及对206阀、207阀进行修复来完成。
问题11.关于篦冷机使用循环风后的操作调整
篦冷机使用循环风后,由于鼓风温度提高了50~70℃,同等条件下,风机特性发生改变,鼓风量将会减少。
为获取同样的冷却效果,就必须增大冷却风量(质量流量);
为使循环风顺利通过篦床冷却熟料,就必须增大体积流量。
因此要求在操作上适当提高风机转速或风门开度,适当增大篦下鼓风压力控制或鼓风机轴功率控制。
下表1是山东安丘某厂篦冷机使用循环风前后,篦下风机控制参数和调节参数的变化情况。
表1:
使用循环风前后各风机控制、调节参数变化情况表
阶
段
参数内容
单位
二段篦床下鼓风机
三段篦床下鼓风机
57.18
57.19
57.20
57.21
57.22
57.23
57.24
无
循
环
风
进风温度
℃
20
篦下控制压力
Pa
6600
5500
6200
4500
3500
3300
篦速
r/m
470
606
风门开度
%
67
66
风机电流
A
96
153
69
169
168
87
113
有
70~90
6900
6000
6500
5800
4000
3700
77
75
76
105
81
190
185
127
表中看出:
使用循环风后篦速未改变,但各室鼓风压力提高300~500Pa,提高5~10%,风门开度增大10%,鼓风电流提高约10%。
问题12.关于主蒸汽温度偏低处理
第二代水泥窑余热发电技术使水泥窑余热资源得到了有效的开发利用,设置了独立过热器,主蒸汽温度较第一代技术得到了明显提高和稳定,一般情况下不会出现主蒸汽温度偏低问题。
但在窑生产不正常、过热器堵塞、高温烟道阀门故障等特殊情况下仍会出现主蒸汽温度偏低或波动问题。
如山东某电站因过热器经常堵塞,清理前主蒸汽温度不足300℃,清理后温度迅速升高到380℃,之后,又因过热器慢慢堵塞逐渐降低到300℃;
又如四川某电站,单炉运行时过热度正常,但当窑头、窑尾二炉同时运行时主蒸汽温度降低且变化不大,检查发现是高温Ⅰ阀门故障所致。
主蒸汽温度偏低会导致汽机效率和寿命下降,严重时将引起汽机设备故障。
因此必须格外重视,发现主蒸汽温度降低,应及时采取措施进行处理。
如属过热器堵塞引起主蒸汽温度降低,问题处理详见“问题5.关于过热器积灰(结皮)堵塞”。
如属高温Ⅰ阀门故障引起主蒸汽温度降低,应及时处理,如属阀轴弯曲或卡死故障应采取停机处理措施。
如属水泥窑生产不正常引起主蒸汽温度降低,问题轻者采取开大高温Ⅱ阀门,关小高温Ⅰ阀门来处理,问题比较严重时可采取开大高温Ⅱ阀门,关小高温Ⅰ阀门的同时增大余风阀门开度,适当开大中温阀门开度的作法加以解决。
如主蒸汽温度过低,在采取以上措施仍无法解决时,应立即退炉停机,待问题处理后再起炉。
问题13.关于高温风机调整
许多人都曾思考,系统串入SP锅炉后高温风机能力够不够的问题,现在可以明确回答,系统串入SP锅炉后,高温风机能力不仅够,而且还会有富裕,为什么呢?
这可用风机的轴功率计算公式进行说明。
因为
N1=HS1Q1/(1000ηS1)………………………………………………
(1)
式中:
N1—串前风机轴功率,m3/s;
HS1—串前风机进口静压,Pa;
Q1—串前风机进口风量,m3/s;
ηS1—串前风机进口风量,m3/s;
N2=HS2Q2/(1000ηS2)……………………………………………
(2)
N2—串后风机轴功率,m3/s;
HS2—串后风机进口静压,Pa;
ηS2—串后风机进口风量,m3/s;
Q2—串后风机进口风量,m3/s;
可用下式计算
Q2=(273+t2)/(273+t1)(P0-HS1)/(P0-HS2)Q1………………………(3)
t2—串后进风机烟气温度,℃;
t1—串前进风机烟气温度,℃;
P0—当地大气压力,Pa;
一般串入SP锅炉后风机进口静压将增加1000Pa左右,即由串前的6000Pa左右增至7000Pa左右;
又因为串入SP锅炉后烟气温度由300℃左右降至170~210℃,平均降至190℃,考虑3%SP锅炉漏风并设ηS1=ηS2后,进入风机的风量变为:
Q2=(273+t2)/(273+t1)(P0-HS1)/(P0-HS2)Q1
=0.8411Q1
(1)/
(2)得:
N2/N1=(HS2/HS1)(Q2/Q1