合成气压缩操作规程1331定文档格式.docx
《合成气压缩操作规程1331定文档格式.docx》由会员分享,可在线阅读,更多相关《合成气压缩操作规程1331定文档格式.docx(65页珍藏版)》请在冰豆网上搜索。
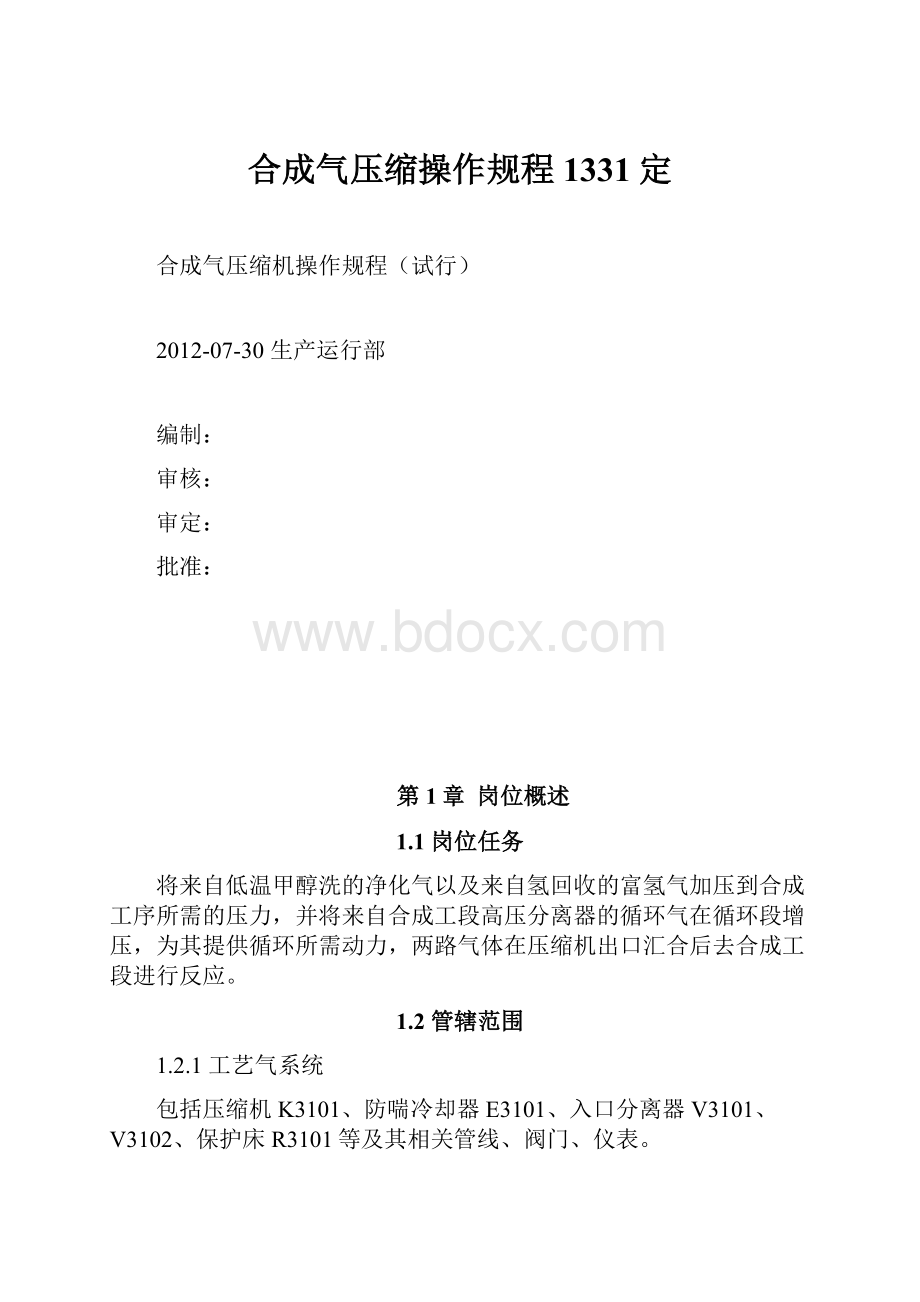
为了维持凝汽器的真空,设有两级蒸汽抽气器E3104,不凝气由一级抽气器抽出,经水冷器冷却后冷凝液经U型管送回凝汽器,未冷凝的气体被二级抽气器抽出,再经水冷器冷却,冷凝液经疏水器送回凝汽器,仍未冷凝的气体直接放空到大气,抽气器动力蒸汽为中压蒸汽(3.8MPaG,425℃)。
为防止汽轮机高压端蒸汽外泄、低压端漏入空气破坏真空,在汽轮机的轴封处注入密封汽,密封汽使用低压蒸汽。
系统所有泄漏气汇集到膨胀疏水槽最后返回凝汽器。
此外,在凝汽器的壳程设有水封式安全阀,当凝汽器超压时安全阀将起跳以防止凝汽器超压损坏。
2.3油系统
储存于油箱中的汽轮机油,经油泵P3102A/B加压后用自力式调节阀PCV3097调节油压至1.0MPa,经油冷器E3105A/B冷却、温控阀TCV3089控制油温至45℃,再经油滤器X3102A/B过滤后,一路送往汽轮机调节机构作为调速液压油;
另一路经自力式调节阀PCV3093调节油压至0.25MPa后送往机组各个轴承点作为润滑油使用,各路回油汇合后经回油总管返回油箱。
油箱设有油加热器E3106,在油系统循环前可对油箱内的存油进行加热。
另外,还设置了由事故发电机驱动的事故油泵(0.3MPa),事故油经过滤器X3102C过滤后直接送至润滑油管路,以确保全厂断电时机组各轴承所需润滑油的供给。
为保证事故油泵启动前或特殊情况下机组停机后惰走期间供油,还设置了高位油箱,正常运转中高位油箱注满油,并保持少量溢流,一旦发生意外,可通过位差向机组各轴承提供短时间润滑油,保证机组惰走期间各轴承的润滑。
2.4干气密封系统
2.4.1一级密封气流程
来自压缩机出口的工艺气体作为一级密封的气源,经过滤器F2812A/B、加热器E2800后通过限流孔板FO3035、FO3036分别进入压缩机低压端和高压端一级密封腔。
当密封气压差PDI3037低于0.23MPa时,自控系统自动打开电磁阀YV3053并保持,增压泵启动,对密封气进行增压;
当密封气压差PDI3037≥0.46MPa时,自控系统自动关闭电磁阀YV3053,增压泵停止工作。
增压系统仅在机组开、停车工况时启用。
一级密封气体绝大部分经机组迷宫返回到机内,阻止机内气体外漏污染密封,少量气体经过密封端面泄漏至第一级密封排气腔。
2.4.2二级密封气流程
0.45MPa的低压氮气经过滤器F2811A/B过滤后,分别作为二级密封气和隔离气使用。
二级密封气经调节阀PCV3027调节压力至0.35MPa后再分为两路,分别进入高、低压端二级密封腔。
此部分气体中少量通过密封端面泄漏到二级密封排气腔,到室外放空;
另外大部分气体经中间迷宫密封进入第一级密封排气腔与一级密封的泄漏气混合后排火炬。
2.4.3隔离气流程
隔离气经自力式调节阀PCV3021调节压力至0.15MPa后再分为两路,后分别进入高、低压端隔离气腔,一小部分通过后置迷宫阻止二级密封泄漏气外溢后放空。
大部分气体通过后置迷宫进入轴承箱,通过轴承放空排入大气,作用是阻止润滑油污染密封端面。
2.4.4放火炬气流程
一级密封泄漏气与大部分二级密封气混合后,经孔板FO3041、FO3040节流,通过压力控制阀PCV3042排放至火炬。
当一级密封损坏时,气体泄漏量增大,一级排气压力PI3038A/B/C或PI3039A/B/C将升高,高至0.32MPa时压缩机联锁跳车;
当二级密封损坏时,一级密封的漏气将进入二级密封腔,一级排气压力PI3038A/B/C或PI3039A/B/C将降低,低至0.11MPa时压缩机联锁跳车。
第3章开车
3.1原始开车
3.1.1开车前应具备的条件
(1)机组及其相关设备、管道、阀门等安装完毕,具备试车条件。
(2)各电气设备,由电气人员检查并确认完好,具备启动条件。
(3)工艺、仪表人员共同检查仪表、阀门、报警、联锁等并确认完好,可以正常投用。
(4)水、电、气等公用工程供给正常。
(5)蒸汽管道、工艺管道吹扫合格,油系统清洗合格。
(6)各类消防,安全防护器具齐全,现场杂物清理干净。
(7)记录报表齐全,通讯设施完备。
3.1.2油系统开车及各项试验
3.1.2.1油系统开车前的检查确认工作
(1)确认油洗时所有临时虑网、盲板已拆除,对照PID图,检查确认油系统恢复正常流程。
(2)确认油泵入口回装洁净虑网,润滑油过滤器回装新虑芯,油站主油箱V3103加油至液位计指示最大值。
(3)润滑油及控制油管路蓄能器充N2正常。
(4)将各台油泵开关打在就地位置,就地压力表及变送器根部阀打开,报警、联锁仪表设定好后投用。
(5)投用油箱电加热器E3106,控制油温在45±
2℃。
(6)打开氮气阀,向主油箱充入氮气,使油箱保持微正压。
3.1.2.2油系统开车
(1)确认以下阀门状态:
●应开阀门:
①润滑油泵P3102A/B进、出口阀;
②压力调节阀PCV3097、PCV3093以及温控阀TCV3089的前后切断阀。
③各轴承进油阀;
④油冷却器E3105A/B进油管线上连通阀,油冷却器E3105A/B排气阀;
⑤油过滤器X3102A/B进油管线上连通阀,油过滤器X3102A/B排气阀。
●应关阀门:
①油系统各调节阀旁路阀;
②各设备上导淋阀、蓄能器充油阀。
(2)稍开油冷却器E3105A/B水侧排气阀,缓开油冷却器上水阀,对油冷却器水侧排气。
排气完毕后关排气阀,全开油冷却器上、回水阀,投用循环冷却水。
(3)油系统运行前五分钟投用隔离气,并确认隔离气压力PI3022正常。
(4)联系电气,给润滑油泵P3102A/B送电,并将置于就地控制。
(5)手动盘油泵无卡涩之后,启动P3102A/B之一,待出口压力正常后打开运行泵出口阀,利用回路调节阀PCV3097调节油泵出口总管压力为1.0MPa。
(6)向油冷却器E3105、油过滤器X3102充油排气;
排完气后,关闭排气阀。
(7)打开并调整PCV3093,使润滑油总管压力稳定在0.25MPa,观察各轴承回油情况。
(8)缓慢打开蓄能器充油阀,排气后将其投入使用。
(9)打开高位油槽充油阀,观察回油管视镜,有回油后关充油阀。
(10)人为改变油冷却器回水阀开度,改变油冷却器后油温,确认温控阀TCV3089能够自动调节,控制温控阀后油温在45℃。
主泵运行正常后,检查确认辅泵进、出口阀打开,将其投自动。
(11)检查油箱液位是否下降,若低于最低工作液位应及时补油。
(12)检查各回油管线上的油视镜油流动情况,观察管线有无泄露、异常振动。
3.1.2.3油系统联锁试验及静态调试
(1)油路总管压力低报警及备用油泵自启动试验:
将备用油泵处于“自动”位置,运行泵处于“手动”位置。
缓慢开大PCV3097旁路阀,当总管油压PI3099降至0.75MPa时,控制室报警且备用泵自启动,记下PI3099的压力,最后两泵互换,再进行一次该实验。
(2)控制油管路压力低报警、低低联锁停机试验:
将工艺联锁强制切除,油系统联锁投用,中控复位。
现场打开主汽阀,切除主、辅油泵自启动联锁,蓄压器充油阀关闭。
通过控制油压力试验阀降低控油管路压力,当PI3122A/B/C低至0.75MPa时油压低报警;
当控制油压PI3122A/B/C(三选二)降至0.55MPa时联锁跳车,主汽阀关闭。
记录报警及跳车时油压数据。
(3)润滑油管路压力低报警、低低联锁停机、事故油泵自启试验:
通过PCV3093前切断阀降低润滑油管路压力,当PI3008A/B/C低至0.18MPa时油压低报警;
当润滑油压PI3008A/B/C(三选二)降至0.13MPa时联锁跳车,主汽阀关闭,同时,事故油泵自启动。
(4)蓄能器性能试验
①确认蓄能器排油倒淋阀关闭,充油阀全开,压力正常。
②停润滑油主泵,确认辅助油泵自启动时,主机未联锁跳车,说明蓄能器性能良好,否则主机因速关油压低联锁跳车,则应调整蓄能器充氮气压力。
③在机组复位条件下,进行油冷器和油过滤器的切换操作,确认主机不会因辅机切换时油压波动而跳车,说明蓄能器良好
注:
做油压试验时,关试验球阀时应缓慢,以便准确记录油泵瞬间启动值,跳车时油压、液位瞬间值;
油试验数据应在设计范围内,否则应重新整定、重新做油试验。
(5)高位油箱性能试验
①将辅油泵及事故油泵自启动联锁进行强制切除。
②现场停主油泵,记录润滑油高位油箱供油时间,以不低于机组正常的惰走时间为合格。
(6)油冷却器和过滤器运行中切换试验:
①确认油系统运行正常。
②确认备用油冷却器和备用过滤器,充油完毕。
③冷却器切换:
快速搬动油冷却器切换手柄,同时观察机组润滑油、控制油压力应稳定。
润滑油压力PI3008A/B/C≥0.25MPa,控制油压力≥0.85MPa。
④油过滤器切换:
分别快速搬动油过滤器切换手柄,同时分别观察润滑油和控制油供油压力应稳定。
(7)主汽阀关闭联锁试验:
从ITCC上将机组联锁复位,使机组具备开车条件。
复位电磁阀SV3121A/B,建立速关油压,手动打开主汽阀。
分别用现场停车按钮、ITCC停车按钮进行试验,确认主汽阀能够迅速关闭。
试验结束后将所有联锁回路恢复正常。
(8)调节汽阀行程调试:
①确认控制油压正常,联系仪表,对调节汽阀进行行程调试。
②分别在0%、25%、50%、75%、100%阀位,测量调节系统:
二次油压力和油动机阀杆位移及调节阀阀杆位移,核对三者之间关系是否符合设计要求。
③调试结速后,将所有调试状态恢复正常。
每次调试时应将实测数据与原始数据作对比,如偏差较大,开车前应检查处理。
(9)机组轴系监测系统报警及联锁试验:
1确认系统油压正常,轴系检测相关联锁投用。
2从DCS上将机组联锁复位,确认主汽阀和调速阀打开。
3联系仪表人员给汽机的轴位移一个假信号,使轴位移达到±
0.4mm时高报警,轴位移达到±
0.6mm时高高联锁,速关阀、调速阀关闭。
4试验结束后将机组恢复正常。
5用同样的方法做轴振动、轴瓦温度监测的报警及联锁试验。
(10)试验后的确认:
油系统所有试验完成后,确认仪表所有联锁,报警回路恢复到正常状态,电气电源正常,主油泵运行正常,辅油泵投自动,事故油泵已备用,机组各回油视镜回油情况正常,流速稳定。
3.1.3冷凝液系统投用
(1)投用步骤
1检查冷凝液泵P3101A/B油杯液位正常,盘车无卡涩,联轴节保护罩就位,具备启动条件。
确认两泵的进口阀全开,主泵出口阀关闭,辅泵出口阀打开。
2确认LV3142A/B前后切断阀全开,旁路阀关闭;
LIC3142置手动,LV3142A全开。
3打开凝汽器E3102脱盐水补水阀,向主冷凝器补水至热井液位50%左右,关闭补水阀。
4启动主冷凝液泵,待出口压力稳定后缓慢打开其出口阀;
并调整LIC3142,稳定后将LIC3142投自动。
5检查确认液位调节阀LIC3142能稳定控制热井液位在50%左右,注意检查在热井上涨过程中液位调节阀LV3142A逐渐关小,LV3142B阀逐渐打开,液位下降过程则反之。
6启动辅泵,停运主泵,检查辅泵运行情况。
7稍开凝汽器大气安全阀PSV3140的密封水阀,确认安全阀的密封水有少量溢流。
(2)凝液泵自动启、停联锁试验
冷凝液泵P3101运行正常后,将主泵(运行泵)和辅泵(备用泵)均投自动。
缓开脱盐水进凝汽器的阀门,使热井液位缓慢上涨,当液位涨至80%时液位高报警且备泵自启,两台泵同时运行;
控制脱盐水补入量,使热井液位逐步下降,当液位降至50%时,辅泵自动停止;
液位降至20%时主泵自动停止运行;
两泵同时停止运行后,缓慢加大脱盐水补入量,使热井液位再次上涨,当热井液位达到50%时,主泵自动启动。
主辅泵的切换可在ITCC上选择,两台泵互为主辅泵。
3.1.4汽轮机单试
3.1.4.1单试前的检查和确认
1油系统运行正常,辅油泵投自动,事故油泵处于备用状态。
2汽机手动盘车正常,无卡涩;
汽机与压缩机联轴节已脱开。
3循环冷却水、仪表空气等公用工程系统正常。
4冷凝液系统正常,辅助冷凝泵处于"
自动"
备用状态。
5确认主汽阀,调速汽阀处于关闭状态。
6打开蒸汽管线导淋阀,暖管放空阀和放空导淋,汽轮机缸体导淋阀,速关阀导淋疏水。
7机组静态调试结束。
8汽轮机部分联锁全部投用,压力、流量等仪表根部阀打开。
9润滑油高位油槽满液位且有溢流。
10蒸汽管网已建好,汽量充足。
3.1.4.2暖管
1打开3.85MPa中压蒸汽手动隔离阀前导淋对总管进行疏水。
2微开3.85MPa中压蒸汽手动隔离阀的旁路小阀。
3确认中压蒸汽手动隔离阀后的导淋阀打开,控制管路压力在0.2-0.3MPa,对其至速关阀间的管道进行低压暖管。
4当蒸汽管管壁温度升到低压蒸汽的饱和温度时(>120℃),可以升压暖管。
缓慢开大旁路小阀,并逐步打开主汽阀前去消音器SL3101的暖管放空阀,使蒸汽管道温度逐渐提高,控制管道升温速率为5-10℃/min,至旁路阀全开。
5缓慢打开手动隔离阀,关旁路阀。
6注意加强疏水,避免产生水击,同时注意检查速关阀的气密性,以防止蒸汽漏入汽轮机缸内。
7确认主蒸汽压力已经达到汽轮机启动的条件后,关小暖管放空阀,保持主蒸汽温度及压力,汽机准备启动。
3.1.4.3轴封供汽
1投用汽封冷凝器E3103循环冷却水。
2投用轴封外侧的隔离用仪表空气,以防止轴封漏汽进入油系统。
3对轴封蒸汽管线进行暖管,并引蒸汽至汽封冷凝器的抽气器S0612及轴封汽压力调节阀PCV3142,调整PCV3142将轴封汽压力控制在20KPa。
汽机冷态启动时先抽真空再投轴封汽,以防轴封蒸汽对转子局部加热而受热不均造成损伤;
热态启动时先投轴封汽再抽真空,以防冷空气进入缸体造成转子局部冷却而损伤。
3.1.4.4建立真空
1打开开工抽汽器蒸汽阀,随后打开空气阀,从PG3150检查抽真空状况。
2启动主抽汽器,注意先投第二级驱动蒸汽阀,再开第二级空气阀,然后打开第一级抽汽器出口阀,再投第一级驱动蒸汽阀,最后打开第一级空气阀,投用抽汽冷凝器疏水阀。
3待真空正常后,停开工抽汽器,关其空气阀,之后再关其蒸汽阀,注意控制主冷凝器压力在-80KPa左右。
3.1.4.5启动汽轮机
(1)启动前确认
1油系统运行正常,各项试验合格;
2真空、冷凝液系统运行正常;
3动力蒸汽压力、温度在指标内;
4汽机各处疏水阀开;
5除压缩机部分外其余联锁已投用;
6盘车已脱开。
(2)启动步骤
1通知运行主任准备启动汽轮机;
2首先发出复位指令(按下副操台上RESET-3125B或现场操作柱上RESET-3125C),ITCC调速器及203超速保护自动复位,启动指示灯开始闪烁。
3在60S内现场手动复位电磁阀SV3121A/B,建立速关油压。
速关油压建立后,ITCC界面上“mode1:
readytostart”后出现“start”按钮,按下此按钮,调速汽阀自动开到100%,同时目标转速自动设定为最低运行转速8360rpm。
此时具备冲转条件。
4冲转:
通知现场,缓开主汽阀。
主汽阀一旦打开,超速保护装置启动,同时启动指示灯由闪烁变为常亮。
随着主汽阀开度逐渐增大,机组转速开始上升,转速升至300rpm时,启动指示灯熄灭。
5低速暖机:
继续开主汽阀,将转速升至1000rpm暖机15min。
暖机期间应全面检查缸内有无异样声响;
机组轴振动、轴位移;
各轴承油压、瓦温、回油及油箱油温情况;
汽机排汽压力、温度;
汽缸热膨胀等情况。
6低速打闸停车试验:
汽轮机在1000rpm低速暖机期间,注意检查各机械参数和工艺参数正常后,在中控ITCC或现场打闸停车,检查紧急停车功能,确认打闸停车后主汽阀,调速汽阀关闭。
7升速:
按前述步骤重新启动汽机,暖机结束后,通知现场继续开主汽阀,按机组升速曲线将转速升至8360rpm。
8注意:
在此期间机组转速的调节完全由现场操作人员通过主汽阀的开度进行控制;
升速期间要避免在临界转速(3900-6270rpm)内停留,如果在临界转速区内Δn/Δt≤500rpm/min超过5s,则调速器触发跳车。
9ITCC速度控制器接管转速控制:
当机组转速一旦超过8360rpm,转速由ITCC转速控制器控制,此时机组转速大于系统设定目标转速8360rpm,所以“ITCC转速控制器”会将调速汽阀回关,回关到一定开度后,转速趋于稳定。
待转速稳定后,现场缓慢开大主汽阀,在开大主汽阀的同时,调速汽阀可能继续回关,在此过程中,要注意主汽阀的手动开大与调速汽阀的自动回关要维持机组转速稳定在8360rpm左右(一般偏差在100rpm之间)。
直到主汽阀全开,汽机进汽量完全由调速汽阀自动控制,接管完成。
“ITCC转速控制器”转速控制区间为:
8360-12540rpm之间。
注意:
如果转速达到接管转速8360rpm后,汽机转速再将至8193rpm以下超过5s,“ITCC转速控制器”触发跳车。
(3)超速保护试验
本机组超速保护跳车值有两个:
一个通过ITCC转速控制器实现,跳车值为13376rpm(定义为电子超速);
另一个通过203超速保护系统实现,跳车值为13794rpm(定义为机械超速)。
(4)电子超速试验
在汽机准备启动前将超速试验开关旋转至允许超速位置,将超速试验开关旋转至电子超速“EOST”位置,按汽机启动步骤启动汽机逐步进入mode6:
超速试验模式。
通过手动升速按钮使汽机转速逐步升至电子超速设定值13376,机组因超速联锁跳车,记录下跳车时实际转速和机组惰走时间。
(5)机械超速试验
在汽机准备启动前将超速试验开关旋转至允许超速位置,将超速试验开关旋转至机械超速“MECHA”位置,按汽机启动步骤启动汽机逐步进入mode6:
通过手动升速按钮使汽机转速逐步升至电子超速设定值13794,机组因超速联锁跳车,记录下跳车时实际转速和机组惰走时间。
●超速试验时,如果转速已超过跳闸转速而不跳车,应立即打闸停车,并找原因。
●超速跳车后,操作人员要认真记录惰走时间,并绘制惰走曲线。
(6)打闸停车
①汽轮机单试完毕后,按下停车按钮,汽轮机打闸停车,确认速关阀、调速阀均已关闭,打开DW补水阀,维持热井液位正常。
②关闭主蒸汽闸阀,缓慢开导淋阀卸压疏水,开汽机缸体各部疏水阀。
③当汽轮机转速降为0rpm,确认转子完全停止后,手动对机组进行盘车,现场确认盘车行程及转子是否正常。
④停抽气冷凝器:
关闭一级空气吸入阀,再关闭一级动力蒸汽阀;
然后再关闭二级空气阀、蒸汽阀门。
等真空降至0后,停汽封冷凝器E3102,关轴封汽切断阀,停轴封蒸汽。
⑤关补水阀,停冷凝液泵,维持油系统运行24小时后,确认汽轮机汽缸温度在65℃以下,停油泵。
⑥油泵停运10分钟后,停压缩机隔离气。
⑦各油泵断电,汽轮机与压缩机联轴节复位,准备联动开车。
3.1.5汽轮机和压缩机联动试车
3.1.5.1试车前的准备工作
(1)机组安装或大修完毕,联轴器接好,机组盘车正常、无卡涩,护罩安装好。
(2)汽机已经单试合格,具备投用条件。
(3)机组仪表部分调试合格,具备试车条件。
(4)水、电、气等公用工程供给正常;
E3101循环水已投用。
(5)干气密封系统已经调试合格,能够正常投用。
(6)试车现场清洁无杂物,管道、阀门标识清楚,消防器材齐全,消防通道畅通,现场照明合格。
(7)试车用工器具(扳手、手电、听棒、测温仪、测振仪等);
通讯器材(电话、对讲机等);
开车用资料(报表、试车方案、操作法、流程图)齐全完备。
3.1.5.2油系统开车
按3.1.2中油系统开车步骤正常将油系统正常投用。
3.1.5.3汽机部分准备
按3.1.3、3.1.4中所述步骤做好汽机启动前的准备工作
3.1.5.4压缩机工艺系统氮气置换
(1)缸体氮气置换前投用一级密封气,确认一级密封运行正常。
(2)确认UV3101、UV3102、UV3103、HV3101、LV3061、LV3068关闭;
FV3059、FV3066及其各自前后切断阀打开,HV3101前后切断阀打开。
(3)倒通开工氮气管线N3-31001-50-B01盲板,压缩机系统充压至0.45MPa。
(4)通过HV3101将系统压力泄至0.05MPa。
(5)将
(2)、(3)步骤重复数次后,通过S3103、S3105、S3106取样,当分析O2≤0.2%为合格,同时在各导淋、排放阀处适当排放,以防形成死区,置换完毕,压缩机系统保压0.45MPa。
3.1.5.5机组部分阀门确认:
(1)应开阀门:
①防喘振阀FV3059、FV3066;
②各调节阀组前、后切断阀;
(2)应关阀门:
①新鲜气进口阀UV3101、循环气进口阀UV3102及压缩机出口阀UV3103;
②压缩机出口放空阀HV3101;
③各