玻璃窑炉设计技术之单元窑Word文档格式.docx
《玻璃窑炉设计技术之单元窑Word文档格式.docx》由会员分享,可在线阅读,更多相关《玻璃窑炉设计技术之单元窑Word文档格式.docx(40页珍藏版)》请在冰豆网上搜索。
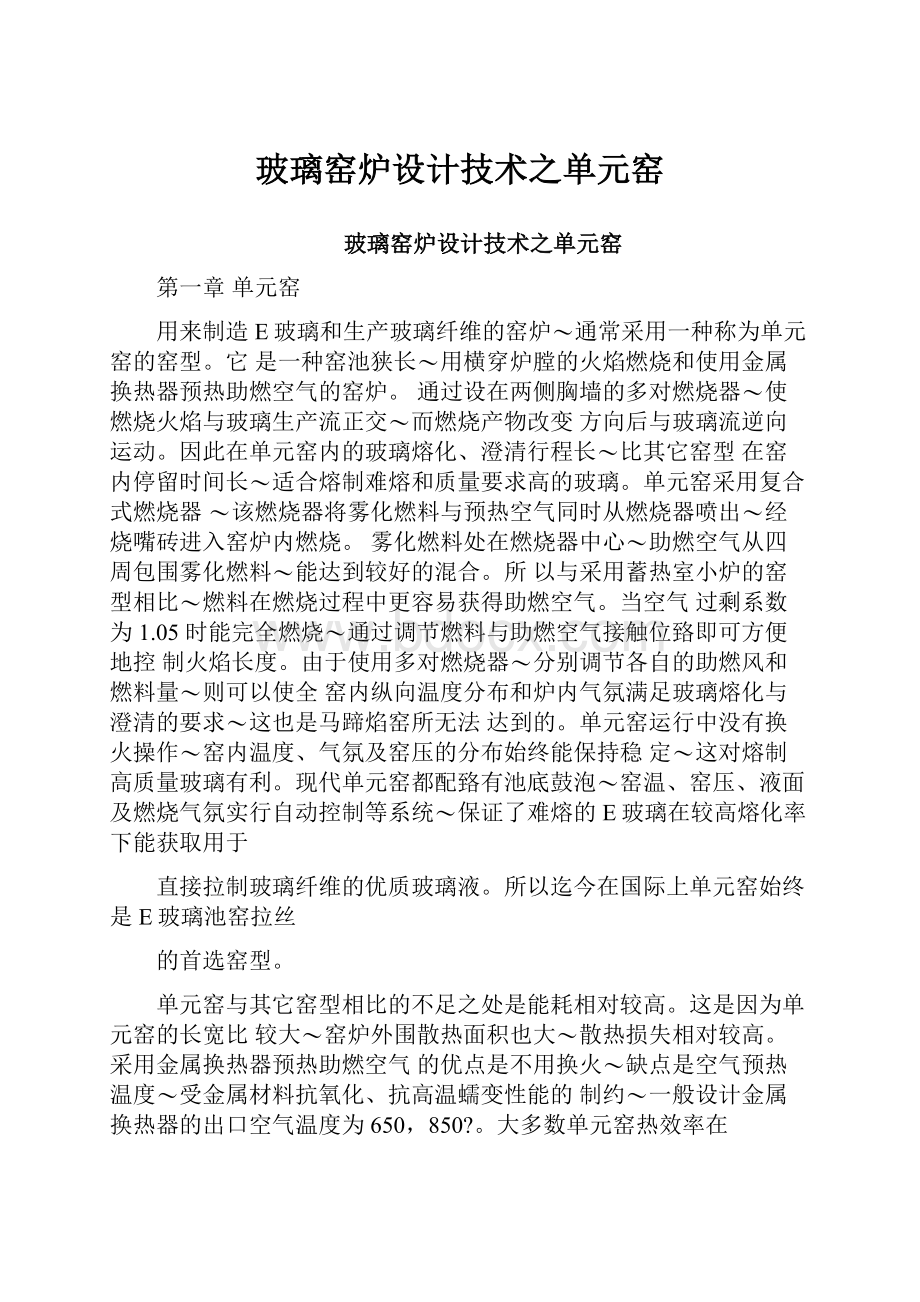
熔化率反映单元窑的设计和生产管理水平〜包括原料成分、水分、质量的控制和窑炉运行的控制水平等〜同时还与纤维直径有关。
一般拉制纺织纱的单元
22窑〜g取0.8,1.0t/M〃d〜拉制粗直径纱时可取略大一些1.5t/M〃d。
早期的技术资料表明当年的单元窑平均日产玻璃的熔化面积〜可见现在已有较大进步。
二、熔池长、宽、深的确定
1,池长L和池宽B是根据熔化面积和熔池长宽比,L/B,来决定的。
即:
F
B=平方米
L/B
L/B越大〜投入窑炉的玻璃原料从熔化到完成澄清〜其间的玻璃“行程”越长〜也越有利于熔化和澄清。
早期设计的单元窑熔他是很长的〜日产量在8—50t/d
〜,L/B,5,4。
随着单元窑配合料微粉化及熔制工艺和鼓泡技术的发展与成熟〜以及窑体耐火材料的质量提高和采用保温技术等措施〜使熔池长宽比在3左右〜也同
样可以获得满意的玻璃质量。
现在设计取,L/B,值时〜只有在考虑为下届窑炉有较大扩产需要时才选取,L/B,大一些〜一般情况下取,L/B,为3,4。
2,他深h主要取决于玻璃的透热性及池底耐火材料能承受的温度。
早期池底
铺面砖选用致密结砖时〜池底温度一般控制在1350?
以内〜而池底温度又直接影响
玻璃熔化质量和窑炉熔化率。
现在的F玻璃单元窑〜由于池底部位采取保温和鼓
泡技术措施〜在提高熔化率的同时〜使热点附近的池底玻璃温度也提高到1440,1470?
〜因此池底2/3以上高温区域的铺面层砖改用耐温和耐侵蚀性能更好的致密铬砖。
有时也可通过适当加高池深来达到降低池底温度。
一般而言〜E玻璃单元窑单产在以下30t/d〜池深选600,700mr〜随着单产的增大〜目前的最高池深可达900mn左右。
三、池底鼓泡位臵的确定
单元窑池底设臵鼓泡装臵〜按其作用大致有以下几种方式。
1,将鼓泡器布臵在配合料生料堆聚集层最厚的部位有助于打散生料堆。
但由于投料口和投料机的改进〜目前已没有必要使用这种方法了。
2,将鼓泡器排布在生料堆消失的位臵〜该部位的玻璃液温度已经比较高了〜因此通过鼓泡可强制较高温度的玻璃液向生料区推移〜底部的玻璃液也可翻到面上吸收窑炉火焰空间更多热量〜起到助熔作用〜通过物理和数学模拟也都能证明这一点。
要注意的是不能让生料层覆盖在鼓泡区域的玻璃液面上〜否则将无法起助熔作用。
3,将鼓泡器布臵在窑池玻璃液最高温度区〜一般约为池长2/3处〜鼓泡作用可使更多的含气泡玻璃翻至玻璃液面排泡〜起到促进澄清和均化的效果。
E玻璃单元窑的池底鼓泡位臵通常按以下两种原则确定:
一是在池长1/3处布臵
一排鼓泡器起助熔作用〜在池长2/3,4/5处布臵另一排鼓泡器〜起促进澄清和均化作用。
这种布臵也是轻工窑炉鼓泡常用的方式,二是第一排鼓泡布臵在池长1m附近〜第二排紧随其后〜二排间相距约E或更近。
这种布臵是近年来E玻璃单元窑常用的方式〜理由是当采用细而干的微粉原料熔制*玻璃时〜熔化不再是难题〜但由于玻璃液中存在大量的气泡〜因此良好的澄清和均化是确保玻璃液质量和提高熔化率的主要因素〜采用两排鼓泡集中布臵可起到类似窑坎阻挡生料流的作用和加强玻璃液均化的作用。
四、窑池结构设计
1,E玻璃单元窑的池壁结构有多种排列方式〜适合小型池窑〜池壁内侧没有横缝〜池壁使用期一般不超过5年〜在窑炉运行后期部分池壁要进行喷水冷却保窑。
该结构对部分低温区可用致密锆砖替代昂贵的致密铬砖〜节约部分投资。
适用于较低温的池壁〜这种结构一般不用喷水冷却保窑〜而用外层加贴新砖来延长窑炉运行期。
结构的池壁采用致密铬砖横向排列〜因为致密铬砖不同于致密锆和AES,砖〜其横缝与竖缝的侵蚀速度差别不大。
2,池底结构。
A.适合于池底温度长期不高于1350?
〜短期不高于1370?
的窑池。
B.采取鼓泡孔二侧的致密铬砖高出池底面〜而鼓泡头又高于两侧铬砖的方式〜这样可在鼓泡头位臵以下形成液滞流区〜减少由于玻璃液冲刷对池底造成的侵蚀。
C.采取鼓泡砖高出池底面而鼓泡头又高出鼓泡砖50mm左右的方式〜同样
也可使池底耐火材料少受玻璃液的冲刷侵蚀。
3,流液洞结构。
当熔化池中已熔化、澄清好的玻璃液流经流液洞时〜被强制降温并流入作业部的主通路。
因此流液洞的作用既是熔池和通路间的连通道〜也是熔化部和作业部的分隔区。
E玻璃单元窑除了采用通常结构流液洞外〜也常采用一种带有挡砖的流液洞结构。
挡砖一般用优质错砖或铬砖做成〜厚度为100,150mm
〜包覆合金皮〜浸入玻璃液部分的铂合金皮厚1mm-露在玻璃液上面的铂合金皮厚0.5mm包铂合金皮的挡砖应伸进两边侧墙各150m〜以致当侧墙砖被侵蚀时〜挡砖依然完整。
为安全起见〜在制订窑炉砌筑计划时〜要使得包铂挡砖能在砌窑收尾阶段插进去。
挡砖以下的流液洞尺寸一般是洞高为洞宽的1/2,4/5〜这种洞口形
式更有利于从熔化池获取熔制质量好的玻璃进入主通路。
此外玻璃液进入流液洞的流速不宜过快〜以4,12m/h范围为宜〜同时流速比较高的玻璃对底砖的侵蚀也较大〜因此在流液洞处底砖要用铬砖面衬。
铂铑合金包皮长期在高温玻璃液中浸泡〜晶体会长大、变脆〜在玻璃液的冲刷下便容易损坏。
为延长挡砖使用时间〜可考虑在挡砖侧面开两个直径25mm的孔〜
通入水管冷却或吹风冷却〜这适合于日产量比较大的单元窑和玻璃液在洞内流速较快的情况。
五、火焰空间结构设计火焰空间指大碹以下、玻璃液面以上的空间〜它的周边包括胸墙、前墙和后墙。
窑池长、宽确定之后〜影响火焰空间大小的就是胸墙高度。
对火焰空间容积的确定〜主要考虑燃料的燃烧和发热状况。
玻璃窑炉内燃料的燃烧属于扩散式燃烧。
除了高温环境及充足的助燃空气条件外〜燃烧速度还取决于氧气的扩散和不断与燃料混合!
燃烧的过程〜氧气扩散速度将直接影响燃烧的速度〜同时必须提供足够的扩散空间和时间〜使燃料达到完全燃烧。
送入窑炉空间的燃料的化学能及燃料与空气的物理能之和与空间容积之比〜称为容积发热强度。
根据窑炉运行经验及充分考虑到窑炉耐火材料所允许的承受强度〜一般取容积发热强度为
3120,240KW/n〜通过该数值可以计算或核算胸墙高度。
一般轻工窑炉的胸墙
较高〜约为1,2m〜而单元窑熔化率低〜胸墙高度为0.8,1.0m。
一般胸墙重量都是独立支撑在立柱上〜池壁与胸墙间用挂钩砖分隔〜挂钩砖砌筑时应与池壁留有鼓胀间隙〜烤窑结束后再用锆泥把余留的缝隙密封。
在胸墙部位沿窑长方向分设多对烧嘴。
支撑烧嘴的烧嘴砖〜插入两侧胸墙〜彼
此相对放臵。
烧嘴间距为600,1000m〜采用气体燃料或低粘度燃料油〜烧嘴间距一般取600mm左右〜米用高粘度重油时〜烧嘴喷油孔过小容易堵塞〜这时可适当放大油孔〜烧嘴间距也相应放大。
在投料口区第一对烧嘴与后池墙之间的距离对生料熔化和排烟温度都有影响〜距离越小该区温度高〜化料快〜但排烟温度高〜会降低热效率〜甚至使金属换热器过热。
距离太大不利化料〜影响熔化率。
一般距离为1.2,1.6mm前池壁与最末一对烧嘴间距〜一般为0.3,0.5mm为了监视窑内熔化状况和便于对燃烧嘴观察和调节〜应在胸墙上设臵一定数量可开闭的观察孔。
六、烟道从熔窑通到换热器的烟气〜先经水平烟道〜再过垂直烟道进入换热器。
水平烟
道的截面尺寸〜通常按1—2m/s的烟气流速来选取〜高度宜大于宽度。
垂直烟道截面又略大于水平烟道截面。
烟道耐火材料的侵蚀通常是很严重的。
这不仅由于排出气体的速度快〜而且还由于烟气中夹带有配合料粉尘。
所以在水平烟道入口处底面〜使用质量好的致密铬砖〜稍后部位才用致密锆砖〜再往后的底面、侧墙、磁砖则使用标准铬砖或电熔AZS砖。
垂直烟道与换热器接口砖采用铬刚玉砖。
七、通路结构设计通路的作用是接受从熔窑流液洞或挡砖下通道流过来的玻璃〜逐渐降温、恒温
〜并使之达到合适的成型温度。
尽管通路和熔窑两者实际是相连的〜但通路的操作和控制完全与熔窑分开。
并在多段通路的情况下〜每段也都要单独控制〜以保证满足拉丝所必须的成型温度。
通常习惯称与熔窑相连接的通路部分为主通路,装有拉丝漏板的通路称为成型通路或作业通路〜而从通路到各段作业通路间的连接通道称为过渡通路。
为了有助于玻璃液的均化和温度调制〜不少专业人士认为主通路宜长〜如5,
8m〜甚至更长些。
而过渡通路的长度以方便拉丝作业为原则〜一般取4.5,5.5m。
通路深度:
主通路液深自流液洞后分几个台阶逐渐减低〜最后一个台阶的液深
为100,160m〜常在该台阶前再设臵一块铂铑合金包皮的挡砖〜挡砖浸入玻
璃50,80mm也有在挡砖前设玻璃液溢流装臵〜可放掉上层BO挥发量较大的23那层玻璃液,。
过渡通路液深在100,160mm可。
成型通路的液深与拉丝作业区玻璃的温度有关〜目前常设计为100,110mm。
通路宽度:
在通路液深确定后〜通路的内部宽度取决于流过它的玻璃量。
如果
不考虑玻璃和耐火材料之间流动阻力的差别〜一般E玻璃选取1.0,
32.0Kg/h.cm的玻璃流量来计算宽度。
成型通路的宽度还要充分考虑漏板配臵的需要〜如果漏板台数较多〜也有在同一条成型通路上采用前后段两种不同宽度的结构。
第二节耐火材料的选用及砌筑
耐火材料在单元窑内长期受到高温、温度急剧变化及火焰、粉料、玻璃液的物理化学侵蚀和机械冲刷作用〜因此随着时间的推移〜将会逐渐地被剥落和熔入玻璃液〜并给玻璃液造成气泡、波筋及难熔结石等缺陷〜严重时使拉丝作业产生困难。
当耐火材料被侵蚀到一定程度〜便迫使单元窑停产冷修。
因此从玻璃熔化质量和单元窑运行寿命等项要求来考虑〜必须根据单元窑不同部位和不同热工制度〜来正确选择适用的耐火材料。
一、E玻璃单元窑选用的主要耐火材料
1.致密氧化铬砖
它具有最佳抗高温E玻璃侵蚀性能〜其侵蚀物基本上对玻璃液不造成污染〜所
以已成E玻璃单元窑的首选优质耐火砖材。
致密氧化铬采用等静压法成型〜其致密度非常高〜主要技术指标为CrO含23
3量,94%,空气孔率,15%〜体积密度,4.24g/cm〜侵蚀损耗只有致密锆砖的
1/10。
用在E玻璃单元窑直接接触高温玻璃液的熔化部池壁、熔化部高温部位池底、主通路池壁和池底、过渡通路池壁等。
国际上常用的致密氧化铬砖牌号有美国CORHARP司生产的.C—1215、C-
1215Z、CR-100等〜德国VG—DYKO公司生产的GR95WAi日本品川株式会社生产的UC—PC—95。
2.致密氧化锆砖
该砖的抗高温&
玻璃液侵蚀性能略低于致密氧化铬砖〜也采用等静压法成
3型〜其技术指标为ZrO,65%〜显气孔率,2.0%〜体积密度约4.25g/cm〜在E2玻璃中温度超过1370?
就有侵蚀。
用在E玻璃单元窑接触玻璃液温度稍低的熔化部池底〜过渡通路、成型通路的池底以及成型通路流液槽和漏板托砖等。
此外致密锆砖还作为致密铬砖的背衬砖被使用。
国际常用牌号有美国CORHAF公司生产的ZS—1300、ZS-1500、ZS—835和
ZS—78等〜德国PG—DYKC公司生产的ZS65WA日本品川株式会社生产的UC—
Z、UC—CZUC—CZB等。
近年来〜我国广州岭南耐火材料有限公司引进国外技术和设备〜也生产出了采用等静压法成型的烧结致密锆砖〜已为国内玻璃、玻纤窑炉部分应用。
德国KG—DYKO公司研制开发了一种新型粗粒结构致密氧化锆砖〜大大改善了砖材的内部组织结构〜进而提高了砖材的耐急冷急热性能。
其体积密度为
33.75g/cm〜其气孔率为17%该砖牌号为ZS65A〜具有良好的抗热震性〜最适用于拉丝流液槽及漏板托砖。
3.标准锆砖
3该砖ZrO含量约为66%〜容重为3.7g/cm〜具有较好的热稳定性和抗剥落性。
2
使用在粉料侵蚀较严重的投料口区胸墙及后墙〜熔窑观察孔砖及通路火焰空间的胸墙和顶盖砖、烧嘴砖。
但也有采用AZS的烧嘴砖与采用莫来石砖为过渡砖及窑
炉二侧的间隙砖等。
4.烧结莫来石砖
3该砖化学组成为AIO,74%;
SiO2.2%。
容重2.5g/cm〜主要用途是标准铬的232背衬砖〜熔化部胸墙及前端墙砖、通路烟道内衬砖、大碹碹脚及放料口外层砖、换热器入口烟道外墙砖等。
还有一种采用融熔法形成莫来石晶体后再烧结成的莫来石砖,具有更优良的抗高温蠕变性和耐热震性〜可用作窑炉大碹和火焰空间胸墙〜使用效果很好〜目前国产化也已成功。
5.电熔锆刚玉砖,AZS砖,
3该砖化学组成为ZrO34%〜AIO49.2%;
SiO15.9%。
容重为3.85g/cm〜主
2232
要用途是熔化部烧嘴砖及投料口砖。
6.电熔铬刚玉砖
3该砖化学组成为CrO28.3%〜AIO58.3%〜MgO〜FeO5.2%。
容重约3.4g/cm。
232323
主要使用在换热器入口处的烟道接口砖。
二、窑炉的砌筑技术
精心设计的窑炉〜必须精心砌筑〜砌筑质量对窑炉寿命、燃料消耗〜玻璃熔化及拉丝作业都有很大影响。
为了满足窑炉对砖材砌筑尺寸和窑体热膨胀等基本要求〜因此窑炉的池壁砖、池底铺面砖都要进行切磨。
此外窑炉耐火砖之间膨胀缝的合理预留也是极其重要的环节。
下面对砌筑技术要点作一简单介绍。
1.钢架验收和预砌筑
1,根据窑炉施工基准线和窑炉中心线〜进行钢结构放线施工。
按钢结构设计要求和施工允许偏差铺设主、次梁和扁钢〜同时也对通路钢结构进行施工。
2,为确保砌筑施工质量和施工进度〜对尺寸和砖缝有严格要求的池壁砖、池底铺面砖及所有承重拱砖应进行预砌筑。
但如果上述砖材的尺寸精度很高〜完全符
合设计要求〜也可不进行预砌筑。
凡进行预砌筑的砖必须按顺序编号〜正式砌筑时对号入座。
2.砌筑顺序和方法
1,在池底钢结构验收合格的基础上〜按窑炉施工基准线与窑炉中心线放出相关的投料口、前后排鼓泡及成型通路上各台拉丝漏板的中心线。
2,池底砌筑〜包括通路底。
砌好保温砖和高岭土大砖后〜在砌筑池壁处内外放宽30,50mm找平。
多层型地底结构在砌筑时必须按标高负偏差控制〜池底总厚度的允许偏差一般为-3mm在池底高岭土大砖上面铺设一层铬质捣打料作为密封层〜可防止玻璃液渗透至抗腐蚀性差的粘土砖层。
3,池壁砌筑〜包括通路池壁。
砌池壁的底砖必须保证水平度〜否则要对该部位底面砖进行加工〜直至达到要求。
多层池壁砖砌筑时〜先里后外地操作〜要确保炉膛内尺寸〜严禁砖材砍凿面朝向炉膛。
墙角需交错压缝砌筑〜严格保持垂直度。
4,吊装立柱。
采取临时措施稳住立柱〜然后按设计要求安装碴碴角钢〜立柱与碴碴角钢必须紧靠〜同时定准标高。
5,砌筑大碹。
制作碹胎〜经拱架做承载沉降试验和相应尺寸检查后〜大碹由两侧同时向中心砌筑〜并要求连续作业〜尽量控制在!
*+内完成。
大碹保温层施工待烤窑结束后进行。
6,砌筑胸墙、前墙、后墙和通路火焰空间。
胸墙的砌筑应在仔细检查托架、托板和支撑架安装合格后进行。
砌筑挂钩砖与胸墙砖要有采取防止向窑内倾倒的措施。
7,砌筑烟道、烟囱。
必须在清除窑内杂物〜并用吸尘器吸净后进行砌筑。
熔窑烟道和烟囱的砌筑〜还要与金属换热器相配合〜通路烟囱必须等通路砌筑完毕后再砌筑。
8,砌筑方法分干砌和湿砌两种。
干砌部位:
熔化部和通路的池底、池壁〜火焰空间部位的挂钩砖〜熔化部和烟道的碹碹砖〜电熔砖砌体及通路顶盖砖。
湿砌部位:
熔化部火焰空间的侧墙和碹顶〜烟道、烟囱及窑炉的保温层砖〜湿砌所用泥浆应根据所用耐火砖材配制相应耐火泥。
3.砌筑的质量要求和检验
1,砖缝。
要求砖与砖间的缝隙要小〜空间各部位砌体的砖缝允许厚度一般不
超过2mm碹顶砖缝要求小于1mn〜保温砖可扩大至3mm
1,膨胀缝。
耐火砖材受热会膨胀〜应根据所用砖材及所处部位的温度状况来
留设膨胀缝。
每1m长的砌体内留设膨胀缝的平均值可用平均线膨胀系数!
均求出。
池底砖、池壁砖〜要适当减少〜以防胀不满E玻璃单元窑所用主要耐火材料致密铬砖、致密锆砖的膨胀缝平均值约为5mm膨胀缝要均匀分段,间距不大于2m,留设〜内外砖层间按封闭式留设〜上下砖层间按交错留设〜胀缝内应保持清洁〜外层用胶带密封砖缝。
2,允许误差。
对标高、水平度、垂直度、线尺寸和砌体表面平整度都有严格的允许误差范围。
砌体砖缝用塞尺检查〜塞尺厚度等于被检验砖缝的规定厚度。
平整度用2m靠尺在所有方向检查。
在全部检查结束并对窑内多次清洁后进行密封处理〜尽量减少外界杂物、尘
第三节单元窑的附属设备
一、投料机
E玻璃原料采用了100—300目的细干粉料〜其中含硼原料受高温又容易结
块〜所以比较适合的投料机是螺旋式投料机。
这样给料仓可以放臵在离开熔窑
一段距离的位臵处〜减少受炉体高温散热的影响。
投料机出口端插入胸墙上部〜为
了避免该处受窑炉热量辐射而温度过高〜通常在投料机前段装配有水冷夹套〜该夹
套用不锈钢板焊接〜内通循环冷却水。
由于废气中含有玻璃原料分解产生的SO
燃料中含硫物质的燃烧产物SO及玻璃助熔剂分解和挥发的氟化物〜从而使22
废气呈较强的酸性。
因此这种工作环境对投料机金属材料会有一定的腐蚀影响。
螺旋投料机可通过变速来调节给料量〜并能保持连续稳定地投料。
E玻璃单元
窑一般采用相对布臵的两台投料机〜如果其中一台要检修时〜另一台也应能满足投料量的需要。
拉制粗直径纤维为主的单元窑也可以采用单侧投料〜但也应安装两台投料机〜一台作备用。
二、鼓泡器前节单元窑结构设计中〜已对鼓泡器的作用及安装位臵等作了介绍。
鼓泡器的关键结构是鼓泡头〜由于要长期插入熔窑的玻璃中〜因此必须选用耐高温和耐玻璃液腐蚀的材料来制作。
对E玻璃单元窑通常铂铐合金材料〜它可确保在窑龄期内的安全使用。
鼓泡头端部开有流通空气的小孔〜根据泡径要求一般为直径0.8—
3.0mm的圆孔。
在熔窑运行期内是不允许堵孔的〜所以开孔也不能过小〜同时要求进入鼓泡管的空气必须经过过滤干燥处理〜达到含尘量小于"
+,-+%〜
3尘粒径小于1mg/cnr〜干燥常压露点/倂0的技术指标。
供气系统应该设三路〜其中两路作为备用气源〜包括一旦孔口堵塞时以一路高压空气冲通堵孔。
鼓泡气压的大小与玻璃液深有关〜一般正常管路进入系统气压在#)%123左右〜备用冲孔管路气压在#)4123以上〜随液深增加〜气压也要适当加大。
此外还要根据泡频〜即每分钟的鼓泡数量进行气量调节。
如泡频为0.3MPa〜鼓泡空气消耗
量约为0.7MPa实际运行时泡频应视窑内熔化状态稍作调整。
要注意鼓泡压力和流量都不能过大〜不允许鼓泡区域出现沸腾状态。
三、燃烧系统
1.熔窑燃烧系统
燃油系统的流程是:
从厂总油站送出的燃料油〜一般先进入设在池窑拉丝车间
内的中间油罐。
该油罐内装有蒸汽盘管加热〜以保持油温为#$%#&
'
左右〜处于
可流动状态。
在出中间油罐之后〜便经油过滤器到油泵〜油泵出口的一路又回到中间油罐,采用手动回油阀〜最好并连一个过压回油阀〜当油压超过后面系统所能承受的压力时〜即打开或开大回油〜以始终保持在安全油压之下,,另一路送至二级加热器。
若使用粘度大的重油时〜先进入二级加热器中的蒸汽加热器〜使油温上升到!
($%!
(&
'
〜再进入电加热器〜将燃油继续加热到!
)&
%!
*$'
如果是使用粘度小的燃料油时〜油温在+$%!
($'
即可满足燃烧器雾化要求〜则原二级串联加热器改为蒸汽和电加热器并联〜互为备用,二级串联加热器之后〜通常还增加一路备用电加热器,。
从加热器流出的燃油最好再经过一道二级过滤装臵〜然后通过电磁阀、减压阀、流量计及调节阀等装臵〜最后送到炉前的每一个油烧嘴。
油雾化后〜与助燃空气同时从燃烧器喷入窑内燃烧。
采用低粘度燃油可以使用($,-.低压空气雾化,使用高粘度重油必须用压缩空气雾化。
雾化空气系统〜在雾化空气管路上装有调节阀和流量计〜空气量应是雾化空气量和通过金属换热器送出的二次预热空气量之和〜该调节阀是为了根据燃油量变化来调节空气量的〜目的是确保良好的雾化效果。
金属换热器送出的二次预热风〜被分配到各燃烧嘴时〜可通过入口处的蝶阀〜单独调节进入各烧嘴的助燃空气量。
有的设计为了提高对窑温的调控能力和防止换热器温度过高受损坏〜也可以在金属换热器出口的热风总管上装有自动放空阀〜一旦出现预热空气高于控制范围时〜立即将部分热空气放空来达到降温目的。
金属换热器最大流量的选择要考虑窑炉燃烧温度的要求。
燃烧系统调节过程必须保证熔窑始终处于微氧化气氛。
因此窑温低于控制值时〜在开大燃料调节阀之前〜必须先开大助燃空气调节阀,相反窑温过高要减少燃料消耗量时〜应先关小燃料调节阀〜后关小助燃空气调节阀。
在调节过程中燃料量与空气量成比例变化。
助燃风机与安全切断阀、油泵实行连锁。
天然气燃烧系统的流程相对简单一些。
天然气从工厂调压房送到车间〜其压力一般是$"
/0-.〜经过滤器〜安全切断阀、减压阀〜将气压降到$"
!
$%$"
)0-.〜
再经流量计和调节阀到达炉前总管后分送至各个燃烧器供燃烧。
它不再需要雾化系统〜而助燃空气部分与燃油系统相同。
需要增加说明的是安全切断阀除与风机连锁之外〜还受天然气进气压力控制。
当进气压力高于过滤器及其后的仪表所能承受的压力时〜为保护系统仪表〜安全切断阀立即切断,而当进气压力低于