数字化设计与并行工程在摩托车研发中的应用Word文件下载.docx
《数字化设计与并行工程在摩托车研发中的应用Word文件下载.docx》由会员分享,可在线阅读,更多相关《数字化设计与并行工程在摩托车研发中的应用Word文件下载.docx(12页珍藏版)》请在冰豆网上搜索。
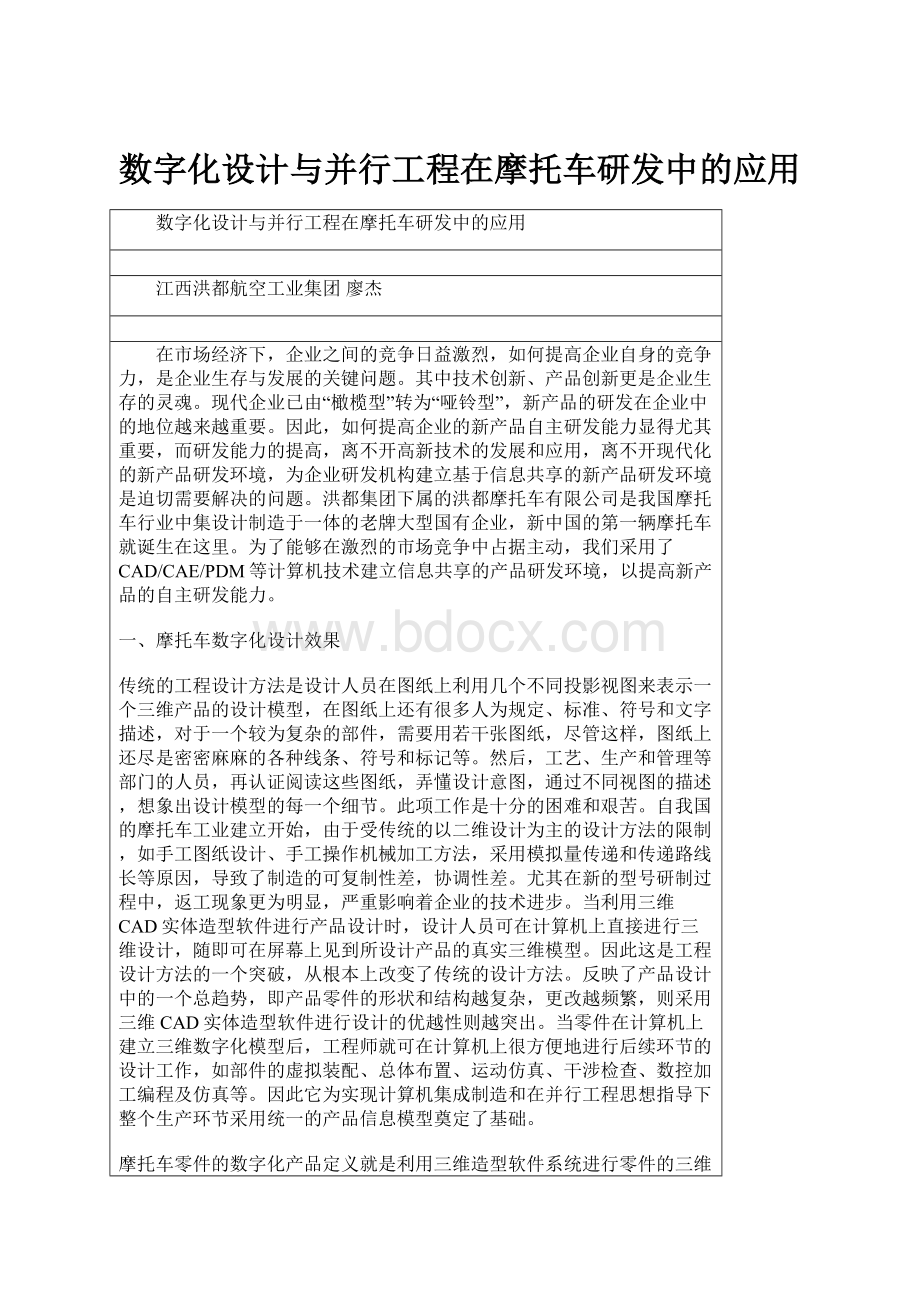
当利用三维CAD实体造型软件进行产品设计时,设计人员可在计算机上直接进行三维设计,随即可在屏幕上见到所设计产品的真实三维模型。
因此这是工程设计方法的一个突破,从根本上改变了传统的设计方法。
反映了产品设计中的一个总趋势,即产品零件的形状和结构越复杂,更改越频繁,则采用三维CAD实体造型软件进行设计的优越性则越突出。
当零件在计算机上建立三维数字化模型后,工程师就可在计算机上很方便地进行后续环节的设计工作,如部件的虚拟装配、总体布置、运动仿真、干涉检查、数控加工编程及仿真等。
因此它为实现计算机集成制造和在并行工程思想指导下整个生产环节采用统一的产品信息模型奠定了基础。
摩托车零件的数字化产品定义就是利用三维造型软件系统进行零件的三维建模,其最突出优点是:
可以建立摩托车零件的三维实体模型,并可方便地通过在计算机上进行虚拟装配来检查零件的干涉和配合协调情况;
可准确地进行重量、平衡和应力分析;
很容易从三维实体模型中提取它的截面图,便于数控加工的程序设计,产品的三维分解图也很容易建立起来。
所有零件的三维设计结果是唯一的权威性数据集,可供所有的后续环节使用,二维图纸按三维数模生成。
用户评审的唯一依据是三维数模和相应生成的二维图纸。
对于数控加工,可利用三维的线框和表面模型数据。
这样的技术思路决定了数字化协同设计平台要以应用为中心,其核心是协同设计平台支持下的三维CAD技术,既以CAD系统为第一选型目标,CAD系统确定之后,再根据CAD软件的要求,配置相应的硬件、系统软件、网络系统及其它应用软件,构成一套较为完整的数字化设计系统。
为确保在研制中全面采用三维CAD设计技术,必须建立一套较完整、先进、实用性强的协同设计平台,因此,我们选择了PDM(产品数据管理)系统。
二、PDM系统的结构特点
PDM系统工程紧紧围绕着建立信息共享、产品研发环境展开,立足于公司的实际情况,充分考虑系统的先进性、成熟性、经济性和可扩展性,最大可能地保护我公司的现有投资。
系统运行环境采用基于“client/server”的体系结构,把客户机、服务器、操作系统、数据库、研发工具等系统软硬件有机地联系在一起,建立一个完整、良好的运行环境。
1.系统硬件配置
采用IBMAIX系统服务器和IBM、DELL零件级图形工作站WindowsNT系统客户机。
2.系统软件配置
软件采用UGS公司的UGNX和TeamcenterEngineering软件。
3.系统的网络拓扑图
本公司PDM系统的网络拓扑图见图1所示。
图1系统的网络拓扑图
三、PDM系统的应用情况
1.成立IPT项目组
(1)IPT项目组成员
IPT项目组的成员由来自结构、重量、分析、CAD/DPA(数字化预装配)支持等部门人员组成。
他们是各功能室的全权代表,并且在同一地点工作。
(2)IPT项目组的作用和职责
由于并行产品定义是一项新工作,为了使每一个人、每一件事都有章可循,公司管理并行产品定义的主要方法之一是,对与项目有关的每一个工作和职责都有一整套明确的定义。
并行产品定义的工作过程是基于公司职能部门和IPT之间清楚的通信交流,以及IPT项目组内成员之间清楚的信息交流。
因此,必须明确阐明他们的作用和职能,而且可以方便地利用项目的每一个成员。
其主要作用和职责如下:
·
在整个工作中采用连续工作环境中协调解决的方法,而不是会议驱动方式;
完成IPT要求的项目的需求分析、设计定义、制造生产和支持服务;
拟订计划并保证质量达到预期的目标;
应用某种度量来估价工作进展,且提供足够数据后才能作更改;
通过协调来支持交叉功能之间的通信交流;
对数字化技术活动做出决策;
理解和使用并行产品定义的优化工作方法;
拟订人员培训要求。
(3)项目机构
项目机构见图2所示。
图2项目机构
2.人员培训
人员培训是PDM系统实施应用成败的关键,因此企业一开始就非常重视人员的培训。
先后进行了多次计算机基本知识、CAD三维、二维使用培训。
其中较为有效的一种方法是通过PDM项目组成员先对洪都集团PDM系统的系统管理员进行全面的培训,然后利用这些系统管理员对所有相关人员进行分角色、分批次培训的形式使企业的所有人员去了解PDM,并制订完善的操作手册和相应的标准在公司内网主页上和PDM系统中共享,用以指导应用者更好地使用PDM系统。
3.设计工作流程
通过PDM系统的应用,规范管理整个设计协同环境,一方面进行设计资源的共享、设计任务的分配和基于WAVE的自顶向下和基于装配的自底向上设计,并且对整个设计过程进行实时监控;
另一方面通过图样/文件审批发放流程,完成研发部设计图样的自动归档和发放。
设计员得到任务后,打开所需设计的数据集文件(UG文件),此时系统将调用基于企业标准的已由系统管理员定义好的三维、二维种子文件(seedpart),然后开始三维设计或二维图纸的生成。
(1)产品结构的建立
根据自顶向下的协同设计要求,顶级的产品设计结构由项目组组长来构建,然后再由各级小组组长和设计人员根据上级组长分配的产品零部件任务来完成底层的产品结构,最后随着各级设计人员工作的结束,整个产品结构自然形成了。
在研发部里,可以将整体系统分解为多级分系统,分别构建顶级BOM和分级BOM。
产品结构见图3所示。
图3产品结构
(2)基于产品结构(BOM)的设计任务分配系统
产品结构搭建完毕后,由项目组组长(任务调度员)来进行设计任务的分配。
首先选中需要进行任务分配的零部件,新建“设计任务分发流程”;
启动该流程后,项目组组长需要指定具体的小组组长或设计人员;
随即在他们各自的任务收件箱中收到这项任务。
如图4、图5所示。
图4基于产品结构的任务分配
图5指定人员
(3)审批发放流程
在TeamcenterEngineering系统中建立各类标准流程,使产品/项目的研发各阶段、各部门的设计和审批流程都在系统的控制下规范地进行。
领导层根据PDM的权限管理可在任何时候实时查询正在进行的和已经完成的工作流程,了解项目研发的进展情况。
所有设计和审批流程的操作都有权限控制,并在系统中纪录,以便分清职责和人员绩效考核。
研发部的流程中的研发部图样发出审批流程模板。
见表1、图6所示。
表1研发部图样发出审批流程模板
图6研发部图样发出审批流程模板
其中在该流程完成后,各个阶段的电子签名自动在图样上添加。
而且各个阶段的审批人员只有查阅功能,不能进行任何修改。
在某个组件的零件设计初步完成后,由小组组长来启动该流程。
在审批发放流程进行过程中,后面的任何阶段如发现有问题,通过系统的批注功能,直接在零部件的下面生成一个或者多个批注文件(*.Jpg文件),并且直接返回到设计者那里,设计修改完成后再次由小组组长递交,继续流程的审批发放,直到最后的部内设计完成的完成状态为止。
批注文件见图7所示。
图7批注文件
(4)更改管理
首先由设计员根据问题的具体情况和初步更改方案提出更改申请给所在小组组长,小组组长收集需要更改的所有图样,并且修订出各相应现有版本图样的升版图样,然后把升版的图样通过更改所有权更改为将要修改设计的设计人员。
然后在TeamcenterEngineering系统中创建一个更改单,编号由系统自动编号产生,同时把需要更改的图样现有版本和升级版本分别放到系统的问题文件夹ProblemItems和结果文件夹AffectedItems中去,随后启动更改单和新版图样的设计、审批流程。
CO创建界面和产生的效果分别见图8和图9所示。
在流程开始后,小组组长必须指定设计、审批的具体人员,在第一阶段指定将要进行修改设计的人员,由他来完成更改单的填写,新版本图样的修改设计,完成后同意递交,随后进入流程中后续的各个不同阶段进行不同级别的审批。
整个流程完成后,该新版图样就处于冻结状态,可以进行归档晒图。
图8TeamcenterEngineering系统的更改管理创建界
图9更改单生成后的内容
四、CAD/CAE的应用情况
1.基于WAVE技术的并行三维设计
运用自顶向下的产品设计研发技术,能够为企业的产品研发带来极大的好处。
设计资源的唯一性可以得到保证并按权限控制(ACL)来实现共享,因为高层设计和细节设计的内容分别在不同的UGPART中构建,而它们在PDM系统中共享信息(如设计基准控制文件),所以基于PDM的权限管理,使得不同部门、不同专业、不同的设计组之间实现并行工程。
此外,控制信息传播途径清晰,设计任务与责任范围分明。
当需要对设计资源(如设计基准等)信息进行更改时,零部件的详细设计能够按照系统通知来响应更改,做相应调整。
运用WAVE的CopyGeometrytoPart的功能,将设计基准控制文件(有些部件可能只有一个控制零件文件而没有控制结构文件)或某个产品零件中的设计基准或几何体链接到各产品零件中。
此时不存在从上一级发送到下一级或平级发送等概念。
只有将设计基准控制文件中的几何信息从设计基准控制文件中发送到具体产品零件中。
基于单一产品设计基准控制文件的自顶向下的产品结构体系如图10所示。
图10产品结构体系
2.整车采用数字化虚拟装配
采用自顶向下和自底向上相结合的设计方法,利用装配功能将摩托车各零部件模型按照实际定位关系进行虚拟装配,可实现在零件进行加工前就通过UG系统功能检查零部件之间的配合⒏缮妫姓敌阅堋⒔峁狗治觯栽硕悴考谢狗治觯约奥壑ち慵目砂沧昂涂刹鹦缎裕股杓埔季×
慷啪诓飞杓平锥危跎傩虏肥灾剖钡姆倒ぃ档蜕杓聘某杀荆醵绦虏返难蟹⒅芷凇S辛苏的P秃螅箍梢源蟠笏醵瘫湫瘟悴考难蟹⑸杓浦芷凇?
PortalView是在TeamcenterEngineering系统中集成的可视化插件,它用来浏览TeamcenterEngineering中各类UG数据相对的JT格式的可视化文件,UG在TeamcenterEngineering中将自动生成其相应的JT可视化文件。
这种文件类是一个数据量极小,可以快速浏览的的文件,无须运行本地的UG系统即可让整个企业一起查看。
源文件和可视化文件(JT格式)自动相连,并储存在产品结构中。
这些可视文件虽然非常简单,但却可用于测量、交叉截面、清晰度检测、动画效果、干扰度检测、以及用于研究其他包装的问题。
JT可视文件使可以我们轻松地装配由不同CAD系统产品设计的产品。
有时这被称为数字模拟装配。
3.关键部件的运动分析
后轮、后摇架、后减震的运动分析过程如下:
(1)对零部件进行实体建模,并在UG软件中进行虚拟装配;
(2)定义“连杆”和“运动副”;
(3)定义运动“驱动”;
(4)给运动分析方案加力、力矩、弹簧、阻尼、减振块和接触运动副;
(5)设置标记及其他封装分析选项(PackagingOption),从而可以对标记、组件进行跟踪,分析其临界状态,并进行干涉检查等;
(6)利用电子图表进行运动仿真分析;
(7)查询运动分析方案的信息,修改编辑模型及运动分析方案的特征。
4.连杆的有限元分析
有限元分析一般要经过以下步骤:
(1)对零件进行实体建模;
(2)对模型进行的简化;
(3)对模型进行网格划分;
(4)对模块进行加载荷及约束;
(5)利用解算器对网格化的模型连杆进行计算;
(6)利用UG软件有限元分析模块中的后处理功能对连杆进行结果分析。
有限元分析的关键是载荷分析与有限元模型的建立,一旦建立了模型,今后基本参数若有变动,只需修改基本输入参数与加载荷即可。
分析结果见图11所示。
图11连杆的有限元分析结果
5.外形件的设计
燃油箱的设计过程如下:
(1)利用三坐标测量仪测量油泥模型,将截面数据点文件(*.dat文件)读入到UG软件中,并生成相应的“样条”曲线;
(2)数据处理,即根据曲线情况将误差大的数据点删除,使生成的样条曲线光顺;
(3)采用正向设计与逆向设计相结合的方法对样条数据进行编辑构造曲面;
(4)利用三维数据在快速成型机上制作样件,检查与摩托车车架、座垫的配合情况,若是不理想则执行步骤
(2)直到效果满意为止。
由于在设计阶段严格把关,使得模具制作周期大大地缩短、制作质量大幅度地提高。
五、结束语
由上述可知,在UGS公司工程师的大力支持下,洪都集团摩托车有限公司研发部已基本建立了信息共享的新产品研发环境,培养了一批掌握现代设计工具的技术队伍。
利用此研发环境提高了新产品研发的质量、缩短了新产品的研发周期,提高了产品数据的管理水平。