材料制备与加工新技术快速凝固.docx
《材料制备与加工新技术快速凝固.docx》由会员分享,可在线阅读,更多相关《材料制备与加工新技术快速凝固.docx(41页珍藏版)》请在冰豆网上搜索。
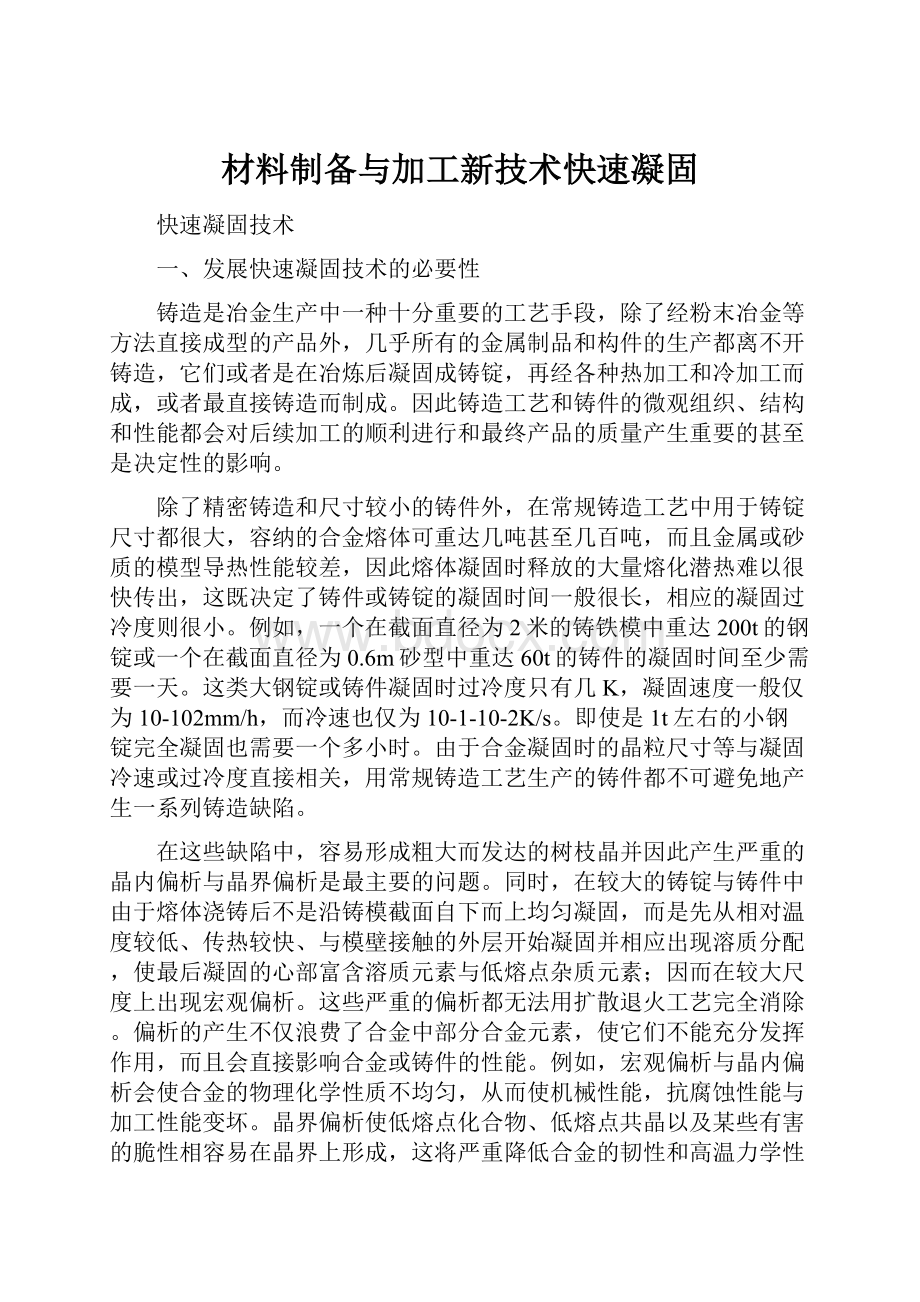
材料制备与加工新技术快速凝固
快速凝固技术
一、发展快速凝固技术的必要性
铸造是冶金生产中一种十分重要的工艺手段,除了经粉末冶金等方法直接成型的产品外,几乎所有的金属制品和构件的生产都离不开铸造,它们或者是在冶炼后凝固成铸锭,再经各种热加工和冷加工而成,或者最直接铸造而制成。
因此铸造工艺和铸件的微观组织、结构和性能都会对后续加工的顺利进行和最终产品的质量产生重要的甚至是决定性的影响。
除了精密铸造和尺寸较小的铸件外,在常规铸造工艺中用于铸锭尺寸都很大,容纳的合金熔体可重达几吨甚至几百吨,而且金属或砂质的模型导热性能较差,因此熔体凝固时释放的大量熔化潜热难以很快传出,这既决定了铸件或铸锭的凝固时间一般很长,相应的凝固过冷度则很小。
例如,一个在截面直径为2米的铸铁模中重达200t的钢锭或一个在截面直径为0.6m砂型中重达60t的铸件的凝固时间至少需要一天。
这类大钢锭或铸件凝固时过冷度只有几K,凝固速度一般仅为10-102mm/h,而冷速也仅为10-1-10-2K/s。
即使是1t左右的小钢锭完全凝固也需要一个多小时。
由于合金凝固时的晶粒尺寸等与凝固冷速或过冷度直接相关,用常规铸造工艺生产的铸件都不可避免地产生一系列铸造缺陷。
在这些缺陷中,容易形成粗大而发达的树枝晶并因此产生严重的晶内偏析与晶界偏析是最主要的问题。
同时,在较大的铸锭与铸件中由于熔体浇铸后不是沿铸模截面自下而上均匀凝固,而是先从相对温度较低、传热较快、与模壁接触的外层开始凝固并相应出现溶质分配,使最后凝固的心部富含溶质元素与低熔点杂质元素;因而在较大尺度上出现宏观偏析。
这些严重的偏析都无法用扩散退火工艺完全消除。
偏析的产生不仅浪费了合金中部分合金元素,使它们不能充分发挥作用,而且会直接影响合金或铸件的性能。
例如,宏观偏析与晶内偏析会使合金的物理化学性质不均匀,从而使机械性能,抗腐蚀性能与加工性能变坏。
晶界偏析使低熔点化合物、低熔点共晶以及某些有害的脆性相容易在晶界上形成,这将严重降低合金的韧性和高温力学性能,井使铸锭或铸件在凝固后期收缩时容易产生热裂。
除了偏析外,采用常规铸造工艺还容易出现缩孔、疏松、气泡、热应力等铸造缺陷,它们也会对铸锭或铸件的性能产生有害影响。
同时,合金元素含量高时,特别是比重小、粘度高、扩散能力差的合金元素含量增加会降低熔体的流动性、充型能力和导热性,这些问题更加严重。
这些问题不仅使现有牌号合金的铸造质量和性能很难得到保证,还限制和约束了新型合金材料的研制。
在镍基铸造高温合金中,根据实验分析和理论研究的结果可知,为了进一步提高合金的热强度与工作温度,必须增加合金的Al、Ti含量以便增加主要的弥散强化相γ(Ni3A1)的含量和提高γ的固溶温度,但在常规铸造工艺下这将产生一些无法解决的问题。
由于镍基铸造高温合金的合金元素含量很高,熔体导热率低,凝固温度范围宽、热收缩率大,本来就容易产生晶粒粗大、成分偏析、铸造应力和熔体流动性差等问题,随着Al、Ti这些轻元素含量的增加变得更加严重,特别是因为偏析容易在某些区域形成α、β等脆性相,即使经过长期退火均匀化处理也不易完全消除,使合金的性能受到很大影响甚至无法使用所以在常规铸造工艺下通常只好在增加Al、Ti含量的同时减少Cr的含量,但是Cr含量减少会减弱合金的抗氧化,抗腐蚀能力,这将使增加Al、Ti含量失去意义。
正是因为这些问题在常规铸造工艺下无法解决,所以便镍基高温合金的发展进入60年代后处于停滞状态。
在用于制造变压器芯片的Fe-Si软磁合金中,虽然已知含Si较高的Fe-6.5wt%Si合金的软磁性能比含Si少的合金好,例如磁致伸缩为零,而且铁芯损耗很小,但由于采用常规铸造工艺无法使Fe-6.5wt%Si合金根据需要在铸成钢锭后再热轧成0.3mm厚的芯片,只能采用铸造和加工性能较好的Fe-3wt%Si合金制作变压器芯片,这使变压器性能受到很大影响。
这些事实清楚地表明,常规铸造工艺存在的问题已成为改善现有合金的微观组织结构和性能与调整合金成分、研制新型合金材料的严重障碍。
特别是许多用于航空、航天、国防、能源等高技术领域,具有优异性能的合金材料一般都含有大量Cr、Ni、Co等战略元素,而这些金属原科的充分供应已日益成为一个严重的全球性问题。
显然,只有突破传统工艺的限制;采用新的技术才有可能研制出少含甚至不含这些战略元素的新型合金。
因此,这迫使人们从60年代前后在研制新型合金材料的过程中不仅从单纯的调整,改变合金成分着手,也把研究生产合金的新技术提上了议事日程。
快速凝固技术正是在这样的背景下出现并很快得到了迅速的发展。
二、金属的一般凝固过程
熔体在冷却时转变成固态的过程通常称为凝固。
由于钢锭的冷凝、铸件的成型、连续铸造、半导体和光学晶体的单晶长大、高温合金的定向结晶以及焊缝的冷凝等工艺过程都与凝固密切相关,同时,凝固组织和结构对合金的最终性能有重要影响,所以凝固过程在冶金生产和材料研制中起着十分重要的作用。
另一方面,凝固作为一种典型的相变过程也在物理冶金和凝聚态物理的理论研究中占有突出的地位。
晶态金属的凝固属于一级相变,包括形核与长大二个阶段的渐变过程。
从原子排列结构的角度考虑,晶态金属与金属熔体的重要区别在于金属晶体只有长程平移对称性或周期性,而熔体中的原子排列则不具有任何长程序,但也并不是完全无序。
x射线衍射分析的结果都表明熔体中原子的排列存在短程序,即存在着按一定规则排列的原子团。
但是这些原子团或通常所称的“晶胚”不仅尺寸很小,一般只含几十个到几百个原子,而且随热涨落而处于不断形成又不断解体的动态变化之中。
只有满足一定的热力学与动力学条件,它们才能形成可以稳定长大成为宏观晶态金属的晶核。
1.1、形核过程
形核的热力学条件是指为了使形核过程能持续进行必须具有一定的热力学驱动力。
假定形核凝固前后固、液相的吉布斯自由能分别为Gs,GL,热焓分别为HL、Hs、熵分别为SL。
SS、熔体温度为T,则凝固前后系统的自由能变化为
通常忽略H、S随熔体温度发生的变化,则当熔体温度T等于固相平衡熔点温度Tm时,ΔG=0。
因此从(1-1)式可得:
式中ΔHm是固相在平衡熔点的熔化潜热。
将上式代入(1-1)可得
式中ΔT=Tm-T为熔体的过冷度。
从(1-3)式可知,由于熔化潜热ΔHm<0,因此只有当ΔT>0,即在熔体温度低于平衡熔点温度时才能有ΔG<0,从而使形核过程具有一定的热力学驱动力。
同时,在上述分析中实际上假定了晶核的表面是平面,但由于实际凝固过程中晶核表面通常是曲面,这会使固相的实际熔点低于Tm。
因此,足够的过冷度对实际形核过程的稳定进行更是不可缺少的。
满足形核的热力学条件只是为形核过程的进行提供了必要条件或可能性,这种可能性要变成现实还必须同时满足形核的动力学条件,这些条件要通过分析形核的具体过程来导出。
假定在稳定凝固时晶核的形状是最简单的球形,半径为r。
由于在晶核形成的同时晶核与熔体之间会形成新的固液界面,这将使系统增加固液界面能,因此这时系统中总的能量变化实际上为:
式中ΔGV是单位体积固、液相自由能之差,σSL是单位面积固液界面能。
如上所述,形核的热力学条件要求ΔGV<0,为形核过程提供驱动力,而σSL>0可以看成形核的动力学阻力。
因此从能量变化的角度考虑,(1-4)式表明形核实际上是热力学驱动力ΔGV与动力学阻力σSL之间互相竞争的过程。
从(1-4)式可知,ΔG是晶核半径r的函数,图1-1分别示意地表示了ΔG、(1-4)式中体积自由能项和固液界面能项与r的关系。
从图中可以看出,只有当r>rc后,晶核继续长大时ΔG才会相应成小,即晶核才能稳定地长大。
所以、rc称为临界晶核半径。
可从(1-4)式用求极值的方法解出,然后用解出的rc代入(1-4)式,并用(1-3)式代入(1-4)式,可以求得相应的ΔGc为:
因为上式右端各项均为正值,所以ΔGc>0,通常称为形核势垒。
因此,要使晶核能稳定形成,熔体中还必须有足够大小的能量起伏或涨落以便克服形核势垒ΔGc,对合金的凝固还应该有一定的浓度起伏以满足晶核的成分要求。
这些就是稳态形核过程必须的动力学条件。
同时从(1-5)式可以看出形核势垒ΔGc主要是由固液界面能σSL产生的,这进一步表明。
σSL是形核过程中的主要阻力。
此外,从(1-5)式还可知,当r=rc时,在一定成分的熔体中过冷度ΔT越大时ΔGc越小,即在通常凝固条件下,过冷度越大时熔体越容易形核凝固。
形核过程在满足上述热力学与动力学条件稳定进行后,形核过程的快慢对凝固晶体的许多性质会产生重要影响,所以通常用形核速率I来定量表示形核过程的快慢,I的物理意义是表示单位时间内在单位体积的熔体中形成的晶核数目,即
式中Q是熔体中原子扩散激活能,k是玻尔兹曼常数,A是与固相结构有关的常数。
上式表明形核速率的大小不仅与形核势垒有关,还与熔体中原子的扩散有关。
事实上这种扩散在晶胚发展成稳定晶核的过程中起着重要作用。
结合(1-5)式与(1-6)式可以知道,形核率I直接受到过冷度ΔT的影响,对成分一定的熔体,ΔT越大,形核速率I越大。
1.2、长大过程
如果形核是新的固相在熔体中许多微小区域里从无到有的形成过程,那么长大就是这些晶核的固液界面向熔体中不断推进或熔体原子向晶核逐步扩散沉积的过程。
从图1-1可知,当晶核形成,即r>rc后,晶核的长大将伴随系统自由能的减小,因而有可能继续稳定长大。
根据固液界面结构的不同,晶体长大的方式主要有界面向前连续推进长大和通过固液界面上原子台阶侧向移动间接向前推进的不连续长大两种类型。
大多数金属晶体凝固是以连续长大的方式进行的。
在晶态金属的连续长大过程中,熔体内实际上存在着两类微观原子运动,第一类是某些因涨落面有较高能量的原子跳跃到固液界面上的运动,这类原子运动的宏观表现是固液界面局部瞬时地向前推进;第二类是固液界面上某些原子在做无规运动时又跳回熔体中,这类原子运动的宏观表现是已凝固晶体局域瞬时熔化。
当T=Tm时,这两类原子运动处于动态平衡状态,既不进一步长大也不进一步熔化。
只有当T<Tm,即具有一定的过冷度ΔT时,第一类原子运动的效果才能超过第二类原子运动的效果,长大过程才能稳定地连续进行。
所需过冷度的大小与熔体系统的传热条件有关。
如果系统向周围环境的传热速度很高,能及时传出凝固固体释放的熔化潜热而不使熔体温度升高,连续长大所需的过冷度就很小;反之,当系统的传热速度很低时,就必须有足够大的过冷度抵消熔化潜热释放后引起的熔体温度回升。
所以晶体连续长大的速度应等于上述两类原子运动速度之差,可以近似表示为:
式中DL是熔体中的原子扩散系数。
a是当一个熔体原于沉积到固液界面上时界面向前移动的距离,它实际上等于固相沿长大方向上的原子间距,ΔT是维持动态长大过程进行必须的过冷度,N是阿佛伽德罗常数。
长大速度R也称为凝固速度或固液界面移动速度。
根据上述分析并比较可知,与形核速率I类似,R除了与固、液相的结构和热力学性质有关外,还与过冷度ΔT密切相关,对一定成分的合金,过冷度ΔT越大时,凝固速度越大。
但是形核速率I通过形核势垒ΔGc与ΔT之间存在指数关系,而R受ΔT的影响则比I小。
所以ΔT的变化对形核速率I的影响要更大一些。
1.3、晶粒尺寸
当一个个晶核长大形成晶粒并通过晶界完全连接在一起时,凝固过程就完成了,因此晶粒的尺寸,形貌和成分分布都与形核,长大过程密切相关。
显然,在单位体积熔体中如果形核速率I越大,形成的晶核数目越多,则凝固后形成的晶粒数也越多,每个晶粒的平均尺才将越小;另一方面,由于在熔体中尤其是多相合金熔体中形核不一定是在同一时刻发生与结束的,所以从决定晶粒尺寸大小的角度考虑,长大速度与形核速率之间实际上存在着竞争,在形核速率—定时,先形成的晶核长大速度很高时就有可能使总晶粒数减少而增大平均晶粒尺寸。
单位体积中的晶粒数与形核率I、长大速度R之间一般有以下关系:
提高冷速T,增大过冷度ΔT对形核率I的影响比对长大速度R的影响更大,所以从上式可知,对一定成分的合金熔体,提高冷速从而增大凝固过冷度或者直接提高凝固过冷度都可以明显细化晶粒。
此外,还可以在熔体中加入形核剂,促进非均匀形核的进行,这样也可以显著提高形核率,达到细化晶粒的目的。
由于长大过程能够稳定进行的前提是界面前沿熔体中要有一定的动力学过冷度ΔT,所以固液界面在向前推进时的形状或晶粒的几何形貌更重要的是受界面前沿熔体中温度分布的影响。
对纯金属来说,当固液界面前沿熔体中存在正温度梯度,过冷度ΔT越小时,熔化潜热只能通过已经凝固的固相传出,固液界面的推进或长大只能是均匀、平稳地并且由传热速度控制。
固相沿界面出现的任何一个微小的凸起扰动都会因凸起处过冷度减小而不可能进一步发展并自行消失,所以这时固液界面是稳定的。
与此相应,凝固形成的晶粒一般是只有平直界面的晶体或等轴晶。
反之,固液界面前沿熔体中存在负温度梯度,即过冷度越大时,熔化潜热可以通过熔体向外传出,这时固相沿固液界面一旦出现微小的凸起时,它就可能进一步迅速长大使固液界面失稳,相应凝固成的晶粒形貌随固液界面前熔体中温度梯度绝对值的增大依次为胞状晶与树枝状晶。
因此,随着凝固长大时固液界面前温度分布的变化因液界面稳定性也随之相应变化,即当因液界面稳定性逐步减小时,晶粒形貌从平直界面晶粒或等轴晶变成胞状晶和树枝状晶。
合金的凝固要比纯金属的凝固更复杂一些,晶粒的形貌不仅取决于固液界面前熔体中的温度分布,还要取决于熔体中的溶质分布,所以要首先研究合金凝固时固液界面前沿熔体中出现的溶质分配现象。
三、快速凝固的产生与发展
常规铸造合金之所以会出现晶粒粗大、偏析严重、铸造性能不好等严重缺陷的主要原因是合金凝固时的过冷度和凝固速度很小,而这又是由于它们凝固时的冷速很小引起的。
因此要消除铸造合金存在的这些缺陷,突破研制新型合金的障碍,核心是要提高形核凝固时的过冷度,从而提高凝固速度。
在实际凝固过程中达到这—目的的方法主要有两种,一种可以看成是“动力学”的方法,即设法提高形体凝固时的传热速度从而提高凝固时的冷速,使熔体形核时间极短,来不及在平衡熔点附近凝固而只能在远离平衡熔点的较低温度凝固,因而具有很大的凝固过冷度和凝固进度。
具体实现这一方法的技术称为急冷凝固技术或熔体淬火技术。
另一种力法是“静力学”的力法,即针对通常铸造合金都是在非均匀形核条件下凝固,因而使合金凝固的过冷度很小的问题,设法提供近似均匀形核的条件。
在这种条件下凝固时,尽管冷速不高但也同样可以达到很大的凝固过冷度。
具体实现这种方法的技术一般称为大过冷技术。
特思布尔早在1950年后就成功地应用大过冷快速凝固技术研究了某些纯金属的固液界面能、过冷度等凝固参数和形核等凝固过程。
特思布尔当时主要采用的是大过冷技术中的熔滴弥散法,即通过使熔体弥散成小熔滴的方法消除形核媒质以形成近似均匀形核的条件。
不仅弥散熔满的方法更多、更有效,近年来还发起了无容器电磁悬浮熔化凝固技术,进一步提高了熔体凝固前可以达到的过冷度。
为了获得更高的淬火冷速并避免常规铸造工艺存在的问题,福尔肯哈根和豪夫曼在1952年首先想到把固态淬火和铸造两种工艺的优点结合起来,使熔体通过传导的方式散热,提高传热速度。
他们把熔化的铝合金滴到浸在液氮中冷却的铜模上使之迅速凝固,因而得到了很高的凝固冷速,使过渡金属元素在铝中的固溶度有了明显提高。
福尔肯哈根和豪夫曼的工作在急冷凝固技术发展的历史上是一个很大的突破,他们第一次用类似于铸造但每次凝固的熔体体积比通常的铜模体积小很多的熔滴淬火代替固态淬火。
然而,一方面由于在他们采用的方法中,滴在铜模上的熔体体积与它的散热面积之比还不够小,因而淬火冷速还不太高;另一方面也由于他们对凝固后的合金微观组织结构没有做深入的分析研究,此外,当时社会对这类新术的需求也还不是十分迫切,因此他们的工作并没有引起人们的注意。
急冷凝固技术是杜书兹(Duwez)在1960年创立的一种研制新型合金的冶金技术。
这一技术是设法把熔体分成尺寸很小的部分,并减小熔体体积和熔体与冷却介质接触的散热面积之比,从而使熔体被冷却介质迅速冷却而凝固。
应用急冷凝固技术制取的合金称为急冷凝固合金,简称为急冷合金。
杜韦兹应用急洽凝固技术第一次制取了非晶态的Au-Si合金,凝固冷速达到106-109K/s,过冷度可达102K数量级,相应的凝固速度也可达10-102cm/s数量级。
与常规铸造技术相比急冷凝固技术所达到的冷速、过冷度和凝固速度都有很大提高。
自从杜韦兹在1960年创立快速凝固技术以来,这一技术已经不断完善和系统化,并逐步从实验室研究转向工厂化生产。
60年代前后这一技术主要应用于研究与生产快速凝固非晶态合金,并把这种合金发展成一种重要的功能材料;70年代中期,这一技术进一步应用于研究用途更加广泛的快速凝固晶态合金;进入80年代中期以后,应用快速凝固技术又发现了新的、具有重要理论研究价值的准晶态合金。
快速凝固技术及其合金的不断迅速发展充分证明了这一技术在生产中的重要作用。
实验研究和实际应用的结果都表明,快速凝固合金与成分相同的合金相比,不仅微观组织结构产生了许多变化,相应性能有很大的提高,而且应用快速凝固技术还能突破常规铸造工艺的限制,研制出许多具有不同成分结构和优异性能的新型合金,从而为各个高技术领域研制急需的新材料开辟了一条新的道路。
另一方面快速凝固技术与合金的研究也为材料科学提出了许多新的研究课题,有力地推动了理论研究的发展。
正因为如此,快速凝固技术诞生以来已经引起了世界各国材料科学工作者的注意与重视,投入大量的人力,物力与财力进行研究。
经过近三十年的发展,快速凝固技术及其合金的研究已经成为材料科学和工程的一个重要分支。
据统计,世界上大多数有关的企业和大学实验室都在进行这方面的研究,现有的各种成分已定型的合金几乎全都用快速凝固技术研究过。
综上所述,可以十分清楚地看出,快速凝固技术在获得新的微观组织结构、新的合金和新的加工工艺方面几乎具有无限的潜力,它已经成为研制本世纪末和下个世纪各个工业和技术部都急需的新型合金材料的一项重要技术,而快速凝固合金则是一种正在得到广泛应用并有广阔应用前景与潜力的新型合金材料。
四、快速凝固方法—单辊法
快速凝固技术的核心是要提高凝固过程中熔体的冷速,从热传导的基本原理可以知道,一个相对于环境放热的系统的冷速取决于该系统在单位时间内产生的热量和传出系统的热量,因此对金属凝固而言,提高系统的冷速必须要求:
第一,减少单位时间内金属凝固时产生的熔化潜热,第二,提高凝固过程中的传热速度。
根据这两个基本要求,并针对常规铸造凝固时熔体在体积很大的铸模中同时凝固、热量不易迅速传出和固态淬火时主要通过对流传热冷速不高等问题,急冷凝固技术的基本原理是设法减小同一时刻凝固的熔体体积并减小熔体体积与其散热表面积之比,并设法减小熔体与热传导性能很好的冷却介质的界面热阻以及主要通过传导的方式散热。
按照上述基本原理,在采用急冷凝固技术的各种方法中,具体设备一般都包括熔化母合金的熔化装置和传出熔体热量的冷却装置,与常规铸造工艺比较,熔化装置相当于冶炼炉,冷却装置相当于铸模。
但是采用急冷凝固技术的设备还必须包括常规铸造设备所没有的、特殊的分离装置,分离装置的主要作用是在时间或空间上“分割”熔体,从而避免大量熔化潜热的集中释放和改善熔体与冷却介质的热接触状况。
分离装置是急冷凝固设备中的核心,它对所能达到的凝固冷速起着关键的作用。
先把母合金在砂轮上磨去氧化皮后装入石英管内。
合金经感应加热熔化后从石英管上端通入氩气或其它隋性气体熔体在气体压力下克服表面张力从石英管下端的喷嘴中喷到下方高速旋转的辊轮表面,熔体在与辊轮表面接触的瞬间迅速凝固并在辊轮转动的离心力作用下以蒲带的形式向前抛射出来。
在熔体旋转法中可以控制和调节的主要工艺参数有:
石英管喷嘴尺寸、石英管喷嘴离辊面距离、石英管内通入的气体压力、辊面线速度和辊轮合金成分等。
为了用熔体旋转法制成高质量的急冷凝固薄带,必须了解对急冷薄带质量的一般要求和可控工艺参数与薄带形成及其质量的关系。
首先,薄带应该是均匀、连续的。
只有保持石英管喷嘴下方辊面上熔池的稳定性才能保证从熔池中拉出的薄带均匀、连续,这就要求喷射熔体时石英管内的熔体是均匀的层流而不是紊流,喷射的流量不能过大和进入熔池后熔体的流速分布应该基本均匀。
因此气体喷射压力过大、喷嘴与辊面距离过远、辊面线速度过低或过高或者这几个工艺参数之间匹配不当时均会使熔池失稳,这样制取的薄带会出现不连续、有孔洞等问题。
此外,调节和控制这些工艺参数时还必须考虑合金熔体的粘度、表面张力等特性。
当熔体称度较大时沉应适当增加气体压力和喷嘴与辊面的距离,否则很容易出现熔体堵塞喷嘴的问题。
其次薄带应表面光滑、平整,做到这一点的关键是选择与急冷合金熔体热接触较好或润湿性较好同时又有很高导热系数的合金做辊轮材料。
例如对一定成分的镍基高温合金熔体,当分别选用与熔体成分相同的高温合金或工具钢做辊轮材料时,薄带与辊轮接触的底面和自由表面都十分光滑、平整均匀,表明熔体与辊轮的润湿情况或热接触很好,相反当选用导热性能较好的铜或铜铬合金做辊轮材料时,则因辊轮与熔体热接触不好、局域冷速下降使薄带表面质量变坏。
用扫描电镜可以看到薄带表面有许多凹凸不平之处甚至出现小孔洞。
第三,薄带的形状、尺寸应该稳定,尤其是厚度应该均匀。
薄带宽度主要是由石英管喷嘴直径决定的,薄带的厚度是由辊速、喷嘴与辊面的距离、气体压力和喷嘴直径等工艺参数决定的。
结合合金熔体的特性适当选择这些工艺参数可把薄带厚度的起伏变化限制在很小的范围内。
显然,在保证薄带质量的前提下制备凝固冷速尽可能高的薄带无论对于实验研究还是对于急冷合金的实际生产都有重要意义。
在上述与薄带厚度有关的工艺参数中辊速比较容易定量调整与控制。
当其它工艺参数一定时,辊面线速度越高,从熔池中拖拉熔体形成薄带的速度也越高,由于熔体的喷射流量和薄带宽度不变,所以凝固成的薄带厚度就会越小,相应的凝固冷速也越高。
因此一般只要在增加辊速的同时适当增加气体压力,调整喷嘴与辊面的距离以保证熔池的稳定性,就可以制成厚度小且凝固冷速高的薄带。
除了上述与薄带质量关系比较密切的工艺参数外,还有熔体过热温度、石英管喷射角、感应加热线圈的形状与尺寸、喷嘴的形状等对薄带的质量影响较小的工艺参数。
为了制取具有一定凝固冷速高质量的急冷薄带,必须根据合金的成分、熔点、粘度、表面张力等特性调整与控制工艺参数。
具体操作时一般是根据经验并通过尝试对样品合金摸索出一套最佳工艺参数组合然后固定绝大部分工艺参组只调整其中一个对薄带凝固冷速敏感的参数来控制冷速,在熔体旋转法中,一般通过改变辊面线速度来达到这一目的。
五、快速凝固中的热传输
在快速凝固过程中,正是由于固体、熔体系统内部或系统与环境之间的热传施具有与一般铸态凝固过程不同的特点,所以熔体才能以极高的速度凝固,因此热传输研究更是快速凝固理论中的核心问题。
快速凝固过程中的热流问题可以分成以下三种情况:
第一种情况是熔体与模面的热接触较差,熔体与冷模之间的界面热阻较大,同时熔体层厚度较小,熔体内部沿热流方向的温度梯度也很小,因此熔体在凝固前和凝固时的传热主要由熔体与冷模之间的界面热传递控制。
这种传热或冷却方式称为牛顿冷却;第二种情况是熔体与冷模的热接触很好,界面热阻极小,而且熔体层厚度较大,沿热流方向的温度梯度也较大,因此熔体在凝固前和凝固时的传热主要受熔体内部的传热控制,这种传热或冷却方式称为理想冷却;第三种情况是熔体中的传热过程介于牛顿冷却和理想冷却之间的中间冷却。
为了定量区别这三种传热类型,可以引入无量纲参数牛塞数N
式中h是界面传热系数,x是熔体层或快速凝固薄带、片的厚度或粉末的直径,K是金属的导热系数。
其中h是表示熔体与冷模或冷却介质之间的界面传热能力大小的重要参数,它的物理意义是在单位时间内,当界面两侧的温差是1K时通过单位面积界面传过的热量。
一般当N<0.015是牛顿冷却;当N>30时是理想冷却,而当0.015<N<30时中间冷却。
在实际的快速凝固过程中由于合金的传