第二篇物料控制Word文档下载推荐.docx
《第二篇物料控制Word文档下载推荐.docx》由会员分享,可在线阅读,更多相关《第二篇物料控制Word文档下载推荐.docx(22页珍藏版)》请在冰豆网上搜索。
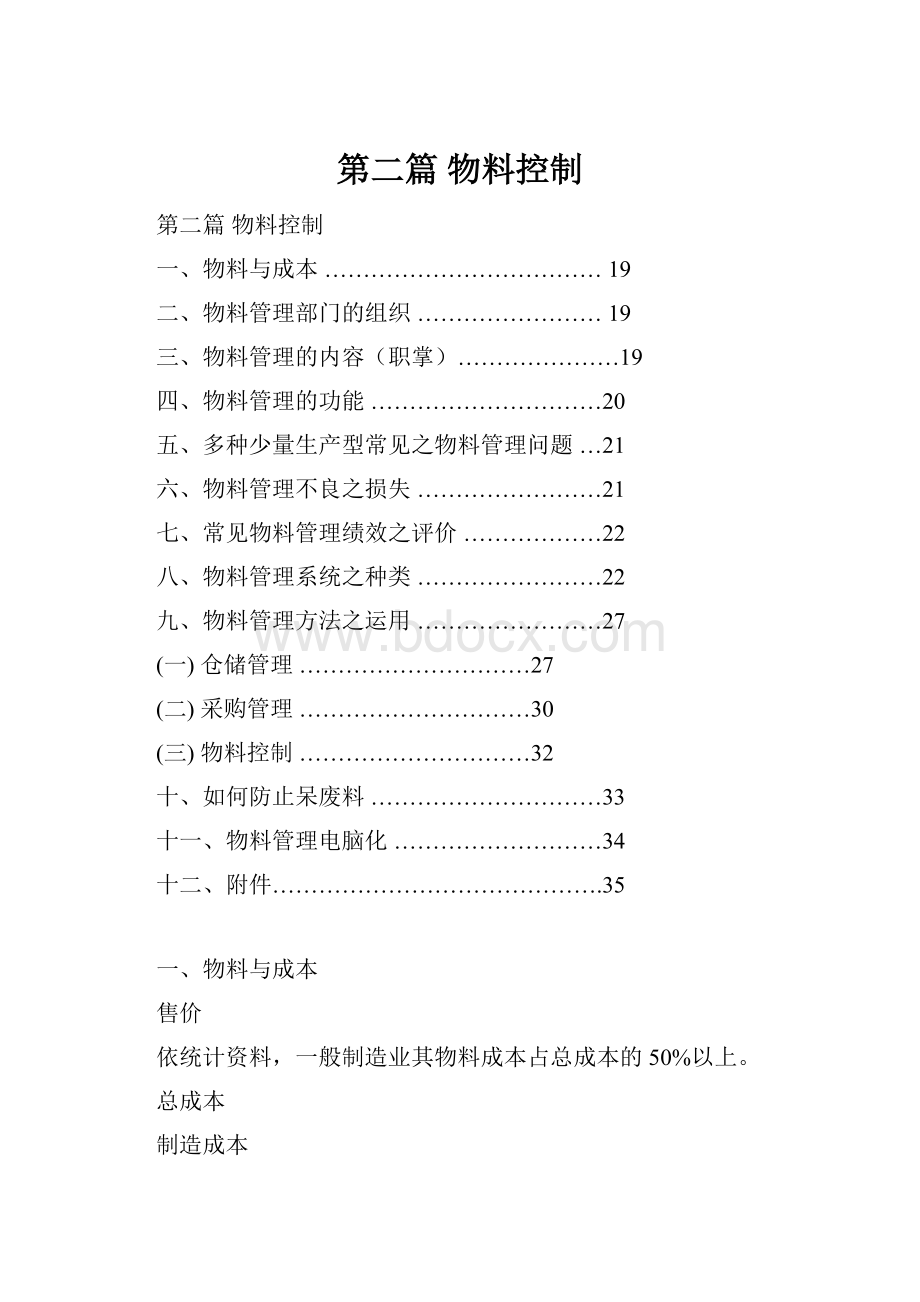
1.紧急订单或变更多、物料准备紊乱、成本高;
2.短期订单多;
3.用料分析失误,未能配合生产计划;
4.供应厂商未能如期交货;
5.物料品质不良;
6.库存过多,积压资金;
7.呆废料多,未定期清理;
8.料帐不一致,作业依据失误;
9.仓库紊乱,浪费寻找时间;
10.收发料缺乏制度规范。
六、物料管理不良之损失
(一)显在的浪费与困扰
●仓储料品经时变坏,变成废品
●储存过多,形成呆料,积压资金
●停工待料,生产紊乱,交期延误
(二)潜在的浪费与困难
●呆料积存的风险,因产品变更而不能使用
●用料浪费,使成本无法控制
●搬运增多,增加管理上的浪费
七、常见物料管理绩效之评价
当期材料使用金额
1.物料周转率=×
100%
(期初材料库存金额+期末库存金额)/2
2.呆废料处理损失=(各项物料原价×
数量)—变卖价
3.紧急采购或断料停工之损失
4.采购价差=前月价格—本月价格(针对采购)
八、物料管理系统之种类
(一)订单订购型
A/R法(AsRequired)
MRP法(MaterialRequirementPlanning)
1.适用:
●多种少量之订单
●单价高
●不重复性、无共用性之物料
●料品易变质者
●能因应订单及设计变更的变化
2.做法:
依据订单(或生产计划)分析物料需求,做订购依据。
注:
A/R法:
毛需求
MRP法:
净需求
3.操作流程:
如附件5
4.步骤说明
1确定订单或生产计划
2区别各项物料之订购模式
是使用订单订购还是存量订购。
3物料用量分析(使用物料分析表)
依产品之材料表(BOM)及生产量计算各项物料需求量.
注:
物料毛需求量应加上备用率
备用率=(进料不良率+制程不良率)×
1.2~1.5
4调整库存量(属于订单订购之MRP法)
毛需求量±
调整库存量=净需求量
调整库存量包括已订购未入量及已指定使用未领量。
5申购
依需求量提出申购单。
6订购
●向供应厂商提出订购单;
●控制交货进度(订货追踪表)。
7供应厂商交货
●核对订购单;
●来料点收(收料单)。
8品质验收
●区别验收方式:
全检、抽检、免检;
●使用验收标准书。
9合格料品入库
●将合格料移入物料仓,并通知采购、生管、会计;
●过帐物料管理卡。
(二)存量订购型
1存货生产型产品之物料(少种多量或中种中量);
2重复性或共用性之物料;
3购备时间较长之物料;
4市场性较差之物料;
5资金影响较低之物料。
2.订购时机
依库存量订购点(定量订购法),不与订单直接挂上关系。
3.优点
1生产无备料时间、缩短交期;
2管理简单、管理成本低;
3隐藏成本少;
4品质较易控制。
4.操作方法:
如附件6
订购前先确认
a.材料是否继续使用或可被其他产品替用;
b.月平均每日用料量;
c.材料标准购备时间;
d.前进料品质记录;
e.料帐是否正确。
5.运作点说明
a.安全存量
为因应每日使用量及购备期的变动而准备的存量(缓冲存量)。
①概算:
安全存量=(平均购备迟延日数×
1.5)×
每日用料
②精算:
安全存量=平均预测误量×
服务水准(安全系数)
参照附件7
耗用量
平均
用量
缺料率
安全存量
期间
b.订购点=(每日用料量×
购备时间)+安全存量
购备时间=(供方生产时间+运输时间)+
(购方订购事务时间+检验时间)
c.一次订购量=(最高经济存量–安全存量)或
经济订购量(EconomyOrderQuantity)
2DS
经济订购量(EOQ)=
IC
D:
年间总需用量
S:
每次订购费
订购费用包括:
a.订购作业事务费用
b.差旅费用
c.运输费用
I:
年间库存费用占单价百分比%
年间库存费用占单价百分比一般以20~30%设定。
其中利息13~20%
陈腐化5~8%
保管费1~3%
C:
单价
订购费用曲线
(三)存量订购型与订单订购型之比较
存货订购型与订单订购型之比较
项目
存量订货型
订单订货型
适
用
类
别
●占用金额较少(C类及大部分B
类)
●购料不易,购备时间长
●重复性之物料
●共用性(或可替代)
●属于存货生产型产品之物料
●占用金额大(A类及少部分B
●规格多变化(特殊规格)
●多种少量之物料
●不常使用之物料
●采购方便之物料
优
点
●不会断料
●产品交期短
●管理简单
●品质控制易
●易赢取顾客
●风险较小
理论上
●不呆料、囤料
订购时机
以库存量的需要(订购点)为订购依据
以订单或生产计划展开需求
订购量
最高经济存量-安全存量
订单用量×
(1+备用率)
简
要
图
示
最高存量
订购点
安全存量
表示订购量
订购量
订单用量
表示备用量
选择物料管理模式应有之认识:
1.要适合自己的产销型态;
2.要考虑料品价值与管理难易度;
3.不妨“一厂两制”,不同的物料,选用不同的管理方法。
九、物料管理方法之运用
(一)仓储管理
1.物料编号
将材料、零件、组件予以编号,一料一号,以便于管理及电脑化。
例:
○○—○○○○—○○—○
变更号
序号
规格
材质
产品类别
2.仓储规划
1建立平面布置图,明示料品储放区;
2尽量利用立体空间;
3依不同性质料品规划储放区;
4规划搬运工具及搬运路线。
3.包装材力求统一及明确标示
内装袋及外装箱要求统一,标示应统一位置,便于点收及管理。
4.仓储环境整顿
1使呆料浮现;
2使料帐易于稽核;
3使先进先出易执行;
4使仓库空间更有效利用;
5不良品的隔离。
5.物料先进先出(FIFO)
1理由
●有保存时限的要求者;
●设计变更品(EC)之加速处理;
●交货批次品质差异之控制;
●零头存量之优先取用;
●迫使现有呆料加速处理。
2方法
●移仓法;
●标签法;
●颜色管理法;
●电脑条码法(自动仓储系统)。
6.物料盘点
1目的
a.矫正料帐不一致;
b.评价物料管理绩效;
c.呆、废料之及时处理。
2频度
一般一个月一次。
3使用表单
a.盘点签;
b.盘点表。
4盘点方法
a.初盘:
仓库管理者;
b.复盘:
指定复盘人员。
7.料帐准确的方法
a.严密的入出库凭证;
b.严密的仓库门禁管制;
c.入库时的确实点收;
d.即时或当日的登帐作业;
e.料品使用标准容器;
f.经常性的储位整顿;
g.运用常时盘点。
(二)采购管理
建立正确的观念,供应商(协力厂)=成长的伙伴
Ⅰ、甄选合格供应厂商(QualifiedVendor)
1.优良供应厂商之条件
1经营理念优秀的企业主管;
2优秀的干部群;
3忠诚稳定的基层员工;
4好的管理制度;
5好的开发及制程技术;
6好的机器设备;
7品质能力;
8生产能力;
9好的供应厂商;
10好的财务状况;
⑾好的客户。
2.供应厂商甄选之步骤
1成立评选小组(采购、品管、技术);
2制订评选项目
如上述评选项目,针对不同项目的重要性给予不同的权数。
3推荐供应厂商;
4供应厂商基本资料审查;
5评选小组实地评鉴;
6评鉴合格供应商;
7决定来往厂商;
8供应厂商管理及辅导;
9供应厂商考核;
10供应厂商奖惩。
Ⅱ、供应商管理库存(VendorManagedInventory,VMI)
这是在要求快速交货的环境下,形成新的管理做法。
做法:
由供应商建立料品的适当库存,在中心厂通知交货时可以迅速供应。
条件:
1中心厂商与供应厂商讯息共享;
2长期或重复性使用之料品;
3料品较少的设计变更者。
(三)物料控制
Ⅰ、ABC分析法之运用
源自于Parato之重点管理技术
定义:
掌握问题之重要的关键少数。
1.实施的步骤
1计算期间(通常以半年或季度)各项材料的耗用量;
2各项材料用量换算成金额;
3重新依金额大小的顺序排列;
4依序计算各项金额占总额的百分比(影响度)及累计影响度;
5绘制柏拉图;
6决定ABC分类。
一般的分类方法:
累计影响度
分类
0~60%
A
60~85%
B
85~100%
C
2.运用ABC分析法于物料管理
A类(严密管制):
●尽量采用订单订购法;
●预测精度要高;
●采保守策略,必要时与其呆存不如缺料;
●尽可能协助供料厂商压缩供料购备时间;
●原则上每月盘点一次;
●列为VA/VE降低成本;
●采购权限往上移。
B类(中度管制)
●原则上采用存量订购方式,容许少量的库存与呆料风险;
●采取经济批量的观念决定订购量或生产批量。
C类(宽松管制)
●采用存量订购方式;
●原则上采取“双堆法”(TwoBinsSystem)
●不妨大量库存、大量订购以换取价格优惠。
十、如何防止呆废料
1.呆料的产生与防止
a.因客户订单的取消或规格变更或减订而产生
●同客户协商因订单取消、减订或规格变更之旧料处理办法。
b.因设计变更或制程变更而产生
●制订设计变更管理规定,对旧料提出处置方法。
c.由于销售预测的失误而产生
●实施滚动或销售预测,经常调整安全存量。
d.材料点收未依据订购单而产生
●严格执行进料检验制度。
e.因呆料未予处置而继续保留
●呆料应尽速处置。
2.废料的产生与防止
a.由呆料转成的废料
●呆料应尽速处理。
b.仓储环境之经时变坏
●做好仓库环境整理整顿;
●贯彻物料先进先出。
c.进料不良或制程不良
●加强进料检验;
●不良品尽速处理。
d.超过使用期限逾期变成废品
●控制库存量;
●执行先进先出。
十一、物料管理电脑化
因应产业环境的变化,物料管理电脑化是必然的趋势。
1.把事务性、重复性的工作交给电脑;
2.减少人为的错误,而造成管理上的误判(品质);
3.快速作业,大幅减少作业时间(效率);
4.使库存量大幅降低(成本)。
附件1
资料统计员
生管组织
中型企业组织架构范例
附件2
订货生产型生产系统
流程
责任者
依据资料
形成表单
备注
订单受理
产销协调
生产计划
用料分析
采购计划
入库
产前查核
生产
业务部
生管课
制造部
物控
采购
物料仓
生管员
成品仓
客户订单
出货计划(案)
库存量
产能负荷分析
出货计划
订单
材料表
库存表
申购单
订购单
收料单
制造单
途程计划
入库单
出货计划表(案)
物料分析表
订购追踪表
验收单
查检表
移交单
库存日报表
存货管制卡
每月、周实施
协调制造部
验收单分送
采购、品管、会计
存货生产型
投产点
一
次
投
产
量
生产时间
存
零库存
最高存量
时间
附件3
附件4
部门:
装配组
日期:
2001.3.31
生产日报表
Ⅰ、应有时间=(1+2+3)-4
Ⅱ、缺勤时间=1+2
项次
项目
时间
1
出勤人数
480分×
32人=15360分
缺勤
1人=480分
2
加班时间
120分×
26人=3120分
迟到、早退
12分×
1人=12分
3
借入时间
600分×
1人=600分
4
借出时间
分×
人=分
合计
19080分
492分
实勤时间=Ⅰ-Ⅱ=18588分
Ⅲ、除外时间
(一)例行事务
(二)业务损失
早会
5分×
32人=160分
计划异常
20分×
33人=660分
开会
分×
人=分
材料异常
教育
30分×
32人=960分
设备异常
盘点
制程异常
10分×
33人=330分
5
清扫
机种变更
40分×
33人=1320分
6
公出
1120分
2310分
(三)意外事故
除外时间合计=
(一)+
(二)+(三)
=3430分
停电
0分
稼动率=%
作业实绩
型号
生产数
良品数
标准时间
实用时间
作业能率
1010
1005
5.43’
5540分
%
2322
2296
3.18’
6555分
808
801
3.46’
2520分
4140
4102
14615分
综合效率=稼动率×
作业能率=%
附件5
物料订单订购流程
备注
订购方式判别
NO
YES
订单订购
物料分析
调整备料率
申购
订购
入库
存量管制
营业部
生管
物控
采购
仓管
销售计划
订单
订购模式一览表
备料率一览表
制造命令单
进度追踪表
物料管理卡
附件6
存量订购法
一次订购量
存量
订购点
零存量
购备时间
附件7
平均预测误差量
月份
预测需求量
实绩需求量
预测误差
绝对误差
25
31
-6
20
+5
41
-16
16
30
-5
19
+6
7
34
-9
9
8
21
+4
合计
56
合计绝对误差
预测期数
平均预测误差=
=
=7