4转 体 梁 转 体 施 工 工 法Word格式.docx
《4转 体 梁 转 体 施 工 工 法Word格式.docx》由会员分享,可在线阅读,更多相关《4转 体 梁 转 体 施 工 工 法Word格式.docx(29页珍藏版)》请在冰豆网上搜索。
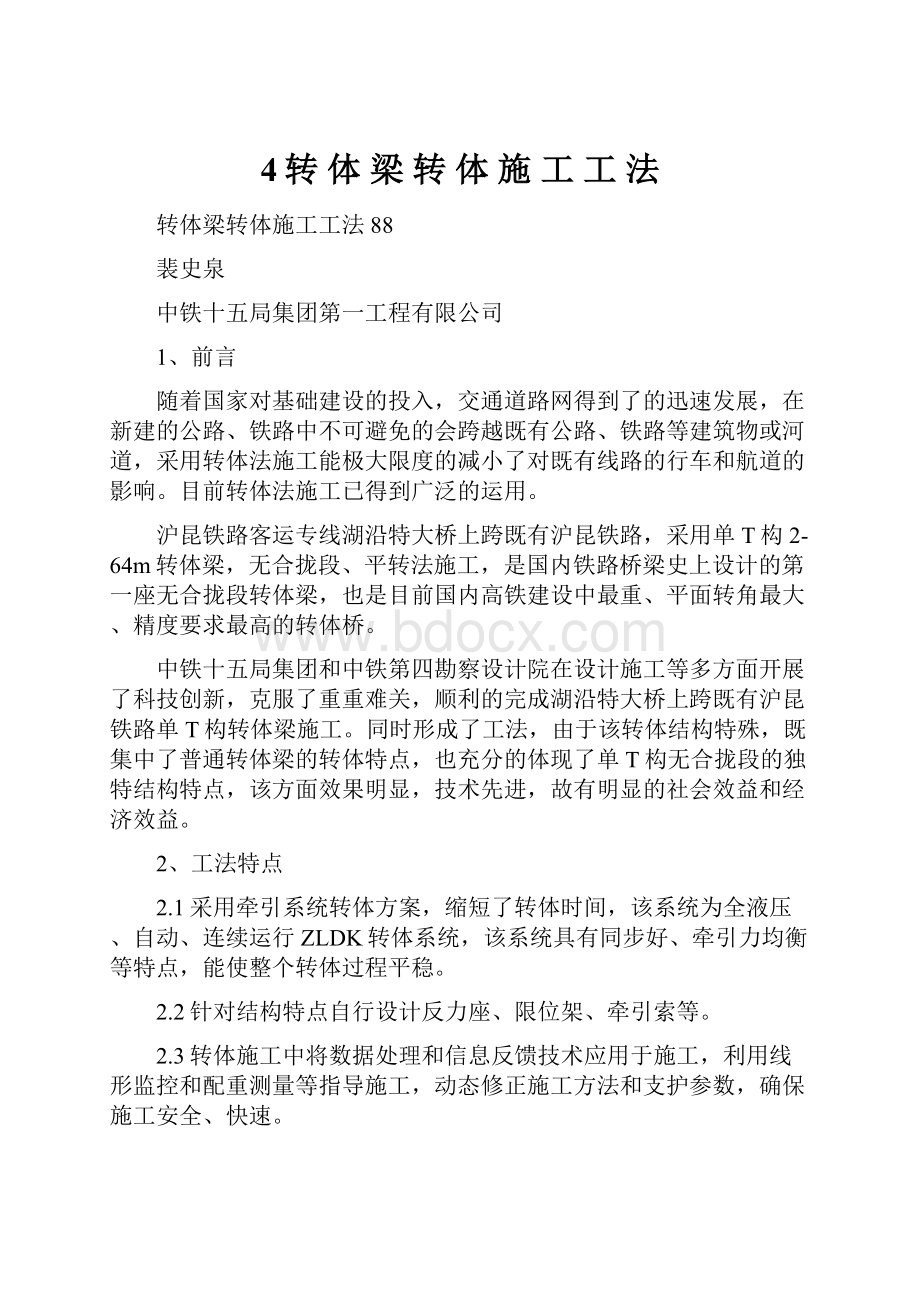
满堂支架、临时支墩
现浇0#块~4#块箱梁、养生、张拉
转体梁转体
封铰
梁端顶起至设计标高
安装支座
浇筑支撑垫石
千斤顶卸载
转体后剩余钢绞线张拉
封锚
成桥
转体前的要点等准备工作
上下承台锁定限位
垫石砼的试配
单T构转体梁施工工艺框图
滑道排气孔设计
砼施工能振捣密实。
下承台的砼分两次浇筑,在绑扎承台底和侧面四周钢筋时将预埋滑道和下球铰的定位钢架角钢安装好,然后进行第一层混凝土浇筑,定位钢架按沿滑道和下球铰四周每米布设一对,角钢预埋高度应超出第一层砼面10~15cm,距离滑道和下球铰定位钢架外边缘5~10cm。
第一层砼浇筑完成后安装滑道和下球铰定位钢架,并和预埋角钢焊接牢固,定位钢架的安装要求骨架顶面的相对高差不大于5mm,骨架中心和球铰中心重合,与理论中心偏差不大于5mm,做为初步控制,然后安装滑道和下球铰,滑道和下球铰与定位钢架之间分别设置调节螺杆,做为滑道钢板和下球铰的平面位置和高程的精调,调节后滑道钢板和球铰高程误差不小5mm、平整度不小于1mm/m,下球铰中心
轴误差顺桥向±
1mm,横桥向±
1.5mm。
精调完成后用电焊点焊牢固。
砼的浇筑是影响球铰和滑道高程和平整度的最后一道工序,在砼的浇筑过程中要充分考虑砼对已安装的下球铰和滑道的冲击力,首先浇筑砼时应尽可能的从滑道和球铰之间缓慢放料,也有利于排气;
其次振捣的时应避免振捣器碰撞球铰、滑道以及其固定支架。
在砼放料过程中,应尽量保持砼的倾斜面浇筑振捣,这样将有利于将球铰和滑道底部不易振捣部位的空气排除,同时浇筑砼过程中,应不间断的查看和清理球铰和滑道预留的排气孔,确保砼的密实。
5.2.1.2限位架的设计
限位架的设置主要有两个目的,其一是在施工上承台、墩身梁部、以及试转停止后将上下承台进行刚性连接的装置;
其二是在正式转体的精调阶段利用限位架做为控制梁体超转的装置。
限位架采用在上下承台埋设I30工字钢的方式,工字钢的埋设要充分考虑旋转的方向和角度,并精确定位,并结合转体过程中点转的测量监控相配合,防止出现过转或欠转等现象。
5.2.1.3支撑腿的安装
支撑腿是转体梁防出现不平衡中或外力作用下倾覆的一种保险支撑腿,支撑腿走板和滑道每个支撑腿为双圆柱形,下设30mm厚钢板。
双圆柱为两个φ630mm×
8mm×
1280mm的钢管,支撑腿钢管内灌注C50微膨胀混凝土。
支撑腿由工厂制造后运至工地,在下转盘混凝土浇筑完成上球铰安装就位时即安装支撑腿,并在支撑腿走板下支垫
支撑腿安装
10mm砂箱支撑底面与不锈钢板间预留10mm间隙,施工时,在支撑腿底和不锈钢板间放置由木条做成的一个方框,方框厚度为10mm,内填平石英砂,把支撑腿水平地布置在石英砂上。
滑道上布置8个砂箱,砂箱尺寸为500×
500mm,每个理论承重300t,用来支承上转盘和上部结构的重量,同时起到稳定上转盘作用,转体前抽调砂箱并在滑道面内铺装3mm聚四氟乙烯片。
5.2.1.4上球铰的安装
下承台砼浇筑完成形成强度后,即可进行上球铰的安装,安装分如下几个步骤:
(1)转动中心轴的安装
施工中要精确安装下球铰精密对位后进行锁定。
在混凝土灌注前将球铰中心轴的预埋套筒精确定位并固定,以便中心轴的转动。
下球铰混凝土灌注完成后,将转动中心轴Φ270mm钢棒放入下转盘预埋套筒中。
四氟乙烯片按装
(2)聚四氟乙烯滑动片的安装。
上球铰安装
聚四氟乙烯滑动片安装前,先将下球铰顶面清理干净,球铰表面及安装滑动片的孔内不得有任何杂物,并将球面吹干。
根据聚四氟乙烯滑动片的编号将滑动片安放在相应的镶嵌孔内。
滑动片安装完成后,各滑动片顶面应位于同一平面上,其误差≯0.6mm。
检查合格后,在球面上滑动片间涂抹黄油聚四氟乙烯粉,使黄油聚四氟乙烯粉均匀充满滑动片之间的空间,并略高于滑动片顶面,保证滑动片顶面有一层黄油聚四氟乙烯粉。
涂抹完黄油聚四氟乙烯粉后,严禁杂物掉入球铰内,并尽快安装上球铰。
(3)上球铰的吊装
转动中心轴定位后,吊装上球铰前,将锅形上球铰底面抹面用布擦洗干净,均匀涂抹少量黄油,然后进行吊装。
上球铰精确就位并临时锁定限位,上下球铰吻合面四周用胶带缠绕密封,严禁泥砂或杂物进入球铰摩擦部。
球铰安装要点:
保持球铰面不变形,保证球铰面光洁度。
(4)安装注意事项
球铰安装期间,受外界环境影响的,会附着水汽、杂物,以致表面产生锈蚀。
此外安装时的吊装过程也容易产生碰撞,致使球铰产生轻微变形、损伤。
因此在整个安装过程中,应注意以下事项:
①转体球铰运抵现场后,在安装前的放置期间应使用防水塑料布将球铰整体严密包好,并将上下球铰边缘的缝隙、中心销轴套管口也用防水塑料布密封,以防止雨水、沙尘、杂物等进入球铰工作面。
②在整个安装吊装过程中,应注意平稳起吊,对准位置后再放置,放置时要轻慢。
吊装过程应避免球铰与其他物件的碰撞,特别要注意保护上球铰凸球面,不得磕碰、划伤。
③安装上球铰之前,应注意保护好上球铰。
可将上球铰凸球面涂抹黄油后,用防水塑料布将整个上球铰严密包起来,放置于在厚木块上。
使用时,将上球铰吊起,去除防水塑料布,用纱布将凸球面擦拭干净,检查凸球面上有无生锈,如有,可用布轮抛光方法清除。
④上球铰安装完毕后,用宽胶带纸将上下球铰边缘的缝隙密封,待上盘混凝土浇筑完毕,球铰转体之前,用刀片将宽胶带纸划开。
5.2.1.5牵引体系的设计
本桥的转体牵引力体系由牵引力系统、牵引索、反力架、锚固构件组成。
转体施工设备采用全液压、自动、连续运动系统。
具有同步,牵引力平衡等特点,能使整个转体过程平衡,无冲击颤动,该设备是一种较为理想的转体设备。
(1)转体的牵引动力系统
由两台套ZLD100型连续牵引千斤顶,两台ZLDB液压泵站及一台主控台(QK~8)通过高压油管和电缆连接组成。
每台ZLD100型连续牵引千斤顶公称牵引力1000KN,由前后两台千斤顶串联组成,每台千斤顶前端佩有夹持装置。
助推千斤顶采用YCW150A型穿心式千斤顶6台(配备ZB4-500电动油泵6台)。
将调试好的动力系统设备运到工地进行对位安装后,往泵站油箱内注满专用液压油,正确连接油路和电路,重新进行系统调试,使动力系统运行的同步性和连续性达到最佳状态。
ZLD100自动连续转体系统由千斤顶、泵站和主控台3部分组成。
其主要特点是能够实现多台千斤顶同步不间断匀速顶进牵引结构旋转到位,以主控台保证同步加压。
本系统兼具自动和手动控制功能,手动控制主要用于各千斤顶位置调试和距离运动,自动控制作为主要功能用于正常工作过程。
(2)牵引索
转盘设置有2处每束由9根强度为1860MPa的钢绞线组成。
预埋的牵引索经清洁各根钢绞线表面的锈斑、油污后,逐根顺次沿着既定轨道排列缠绕后,穿过ZLD100型千斤顶。
先逐根对钢绞线预紧,再用牵引千斤顶整体顶紧,使同一束牵引索各钢绞线持力基本一致。
牵引索的另一端设锚,已先期在上转盘灌注时预埋入上转盘砼体内,出入处不能死弯;
预留的长度要足够并考虑4m的工作长度。
牵引索安装完到使用期间应注意保护,特别注意防止电焊打伤或电流通过,另外要注意防潮、防淋,避免锈蚀。
(3)
反力座预埋钢筋
反力座
牵引反力座采用钢筋混凝土结构,反力架预埋钢筋深入下部承台内,反力架混凝土与下转盘混凝土同时浇注,牵引反力座槽口位置及高度准确定位,与牵引索方向相一致。
转体的左右幅分别单独成为一套牵引体系。
为保证转体梁精确就位在设置反力架的同时预埋限位架。
详见下图:
(3)转体技术参数计算
转体过程的计算按两种工况进行,A状态:
支撑腿没有和滑道接触;
B状态:
由于梁体两端产生不平衡重量,且根据一端平均每米梁段多浇筑砼0.3立方,支撑腿和滑道接触产生摩阻。
A工况计算:
①动力储备系数的计算
转体总重量W为68720KN,其摩擦力计算公式为F=W×
μ
启动过程中的静摩擦系数按μ=0.1,静摩擦力F=W×
μ=6872.0KN;
转体过程中的动摩擦系数按μ=0.06,动摩擦力F=W×
μ=4123.2KN。
转体拽拉力计算:
T=2/3×
(R·
W·
μ)/D
其中:
R—球铰平面半径,R=1.5m;
W—转体总重量,W=68720KN;
D—转台直径,D=8.0m;
μ—球铰摩擦系数,μ静=0.1,μ动=0.06;
计算结果:
启动时所需最大牵引力T=2/3×
μ静)/D=480KN<2000KN
转动过程中所需牵引力T=2/3×
μ动)/D=250KN<2000KN
动力储备系数:
2000KN/480KN=4.17
钢绞线的安全系数:
9×
1860×
0.75×
140÷
1000=1757.7KN/240=7.323
B工况计算:
根据假设的工况,超重一端梁段每米超重0.3立方砼,即q=0.3*25=7.5KN,且只有一个支撑腿和滑道接触并产生摩阻,现计算摩阻的大小如下:
FA=7.5×
3.5÷
2(1+61.55÷
3.5)2=4533.75KN
支撑腿和滑道之间的摩擦系数按u=0.08计算则钢绞线需要增加的牵引力为F=4533.75×
0.08=362.5KN
μ静)/D+F=480+362.5=842.5KN<2000KN
μ动)/D=250+362.5=612.5KN<2000KN
2000KN/842.5KN=2.374
1000=1757.7KN/421.25=4.172
从此计算结果可以看出千斤顶动力储备和钢绞线的安全已达到工程的设计要求。
故本桥转体选用两台套ZLD100型液压,同步、自动连续牵引系统(牵引系统由连续千斤顶、液压泵站及主控台组成),形成水平旋转力偶,通过拽拉锚固且缠绕于直径8.0m的转台周围上的9φ15.24钢绞线,使得转动体系转动。
5.2.2墩身及梁部施工时的上下承台的固结措施
为了防止在施工墩身和梁部时出现的外力导致上承台发生扭动致使梁部线形发生变化,在施工上承台之时将上下承台预埋的限位架焊接牢固,并在支撑腿走板和滑道间楔入钢楔防止了上承台以上部分在施工中受外力的影响而发生转动。
5.2.3卸架支撑体系的施工
满堂支架拆除的次序由悬臂端向根部展开,由于考虑到在支架拆除过程中悬臂端将下挠,将直接造成未拆除的临界支架受力剧增而导致支架变形,对后续的拆架造成极大的困难,因此为了有利于支架拆除,为了防止在支架拆除过程中发生变形扭曲,在T构转体梁距两端部各0.80米处设置一个临时支墩,每个支墩均采用四根φ529螺旋钢管,待拆除梁体支架时在每根钢管柱顶各安装一个350t千斤顶对梁体进行支撑。
临时支墩的底座采用预埋钢板,并在安装支墩时将支墩顶钢板和预埋钢板焊接牢固。
具体详见布置详见右图:
支墩的受力计算
(1)计算参数:
纵梁:
采用4根I30工字钢;
立柱:
立柱采用φ529螺旋钢管,壁厚10mm,长10.08m。
根据设计提供的支座反力为400T,即千斤顶顶力每端按400T计算,则每钢管桩受到的最大压力为1000KN
(2)Φ529×
10mm钢管柱计算
①钢管柱回转半径:
i=1/4×
529=132.25mm
②计算长细比λ=L/i=9.92×
1000/132.25=76.219
③轴心受压构件稳定系数ф1=0.674
④A3钢材轴向允许应力[σ]=140MP
⑤支墩钢管受力截面积为:
A=π(D2-d2)/4=0.0163M2
支墩受力为:
[N]=ф1×
A×
[σ]=0.674×
0.0163×
103×
140=1538.1KN>
N=1000KN满足要求。
(3)地基处理计算
钢管柱位于满堂支架硬化场地上,原地基已将软土挖除并检测其承载力均超过220kpa,并换填隧道洞碴1.5米,承载力较好,直接在混凝土面上浇筑钢筋混凝土做方型基础(C30),基础设置为:
1.0米(厚)×
3.0米(宽)×
8.8米(长)。
钢筋布置如下图:
地基承载力验算:
①支撑力:
400T
②钢管即相关焊接件千斤顶等:
5T
③钢筋砼基础:
68.64T
即合计总重为:
T=400+5+68.64=473.64吨
④基础面积:
A=26.4m2(不含扩散面积)
P=N/A=4736.4÷
26.4=179.4Kpa<
220Kpa满足承载力要求
5.2.4转体施工
5.2.4.1称重
该桥桥梁施工采用平转法施工,跨度为64+64m,单悬臂实际跨度64.9m。
与既有沪昆铁路交叉,斜交角度为122度,转体角度为58度。
T构转体梁实际重量6390吨,上转盘设计直径8m,下方设置8个直径60cm的撑脚来提供安全保护。
称重有两种方式,分别为应力称重和千斤顶顶推称重两种:
a、应力称重是在墩身和0#块施工是已埋设应力感应器,在卸架之前用仪器对转体梁预埋的应力感应器开始进行量测,待支架完全卸架后再进行量测,并根据量测的结果经计算得出两端不平衡重所需的配重值,指导配重施工;
b、千斤顶顶推称重法是用千斤顶在上下承台之间的梁纵轴位置分别顶起并根据力矩计算所需配重,此次配重采用的是平衡配重的方案,该配重方案的基本思想是,转体梁在静力状态下保持平衡,通过配重使转体梁的重心线通过球铰竖轴线。
本工法重点介绍千斤顶顶推称重法。
a、千斤顶测点布置
根据撑脚实际设置情况如图所示,在1#和5#撑脚的两侧27cm处对称放置两个350吨的千斤顶进行对称顶升。
在1,3,5,7#撑脚设置四个百分表,并编号为①③⑤⑦,用以判断转动体在称重试验过程中是否发生转动。
千斤顶外边缘距上转盘外边缘约为25cm,千斤顶直径为42cm。
千斤顶中心距上转盘圆心即顶升力矩为3.53m。
b、测试方法
转动体支架全部拆除,梁体两端悬空,观察百分表转动情况,
百分表变化表(单位:
mm)
测点
工况
①
③
⑤
⑦
成桥阶段
6.3
4.6
11.3
落梁
8.12
4.68
2.53
11.6
升1.82
升0.08
降2.07
升0.3
从以上数据可知,顺桥向长沙方向下降2.07mm,杭州方向上升1.82mm,撑脚全部悬空且与滑道没有接触。
由此可知转动体球铰摩阻力矩大于转动体不平衡力矩。
横桥向百分表变化在0.5mm,即横桥向未发生偏转,较为平衡。
计算球铰摩阻力矩和不平衡力矩:
由百分表的转动可知,梁体重心偏向大里程侧。
在长沙侧承台实施顶力
当顶力
逐渐增加到使球铰发生微小转动的瞬间,有:
在杭州侧承台实施顶力
不平衡力矩:
摩阻力矩:
c、测试结果分析
分别对上转盘的大小里程方向进行顶升。
大里程侧顶力
为1908.964
为3.53m,小里程侧顶力
为1274.88
为3.53m。
。
使用四氟乙烯片并用黄油填充的球铰静摩阻系数和偏心距可用下列各式表示:
球铰静摩阻系数:
转动体偏心距:
式中,R——球铰中心转盘球面半径
N——转体重量
计算得球铰静摩擦系数0.0149,偏心距为0.0174m。
在小里程侧距离梁端8m处增加配重20kN。
撑脚到滑道的设计高度为6mm,四氟乙烯板的厚度为4mm,撑脚距四氟乙烯板的距离较小,在转动过程中较为安全。
需要配重=不平衡力矩/(悬臂长度—配重距两端距离)
需要配重=1112.775÷
(64.9-8)=19.6KN(2吨)
配重计算结果
不平衡力矩
(
)
摩阻力矩
初始偏心距e(m)
静摩擦系数
配重(T)
配种作用位置
1112.775
5625.868
0.0174
0.0149
2
距小里程侧梁端8m
5.2.4.2配重
按称重结果,在预定位置吊装配重。
配重采用沙袋进行,吊装沙袋的吊车应采用有称重系统的吊车进行吊装达到初步配重的效果,同时经过预埋的应力感应器再次进行精确配重,做到转体梁两端重量平衡,杜绝发生因不平衡重而引发的梁体倾斜。
当各撑脚与环道间隙差值太大时,为了便于放置四氟板,可用竖向千斤顶调好各撑脚与环道间隙后再配重。
5.2.4.3转体结构的索引力、安全系数及转体时间的计算
(1)转体索引力、安全系数计算
转体总重量W为68000KN
其磨擦力计算公式:
F=W×
启动时静磨擦系数按μ=0.1,静磨擦力F=W×
μ=6800KN
转动过程中的动磨擦系数按μ=0.06
动磨擦力F=W×
μ=4080KN
转体牵引力计算:
(R×
W×
R为球铰平面半径,R=1.5m
D为转台直径,D=9m
μ为球铰磨擦系数,μ静=0.1,μ动=0.06
计算结果:
启动时所需最大索引力T=2/3×
μ静)/D=755KN
转动过程中所需牵引力T=2/3×
μ动)/D=453KN
动力储备系数1000KN/755KN=1.32
9根/台×
26T/根/75.5T=3
计算结果表明千斤顶动力储备和钢绞线的安全系数均达到了本类型工程施工的要求。
(2)转体时间及各项参数的计算
千斤顶的牵引理论速度(mm/min)=泵头流量(L/min)/(伸缸面积)
ZLDB泵站流量设为2.7L(可根据工况调节溢流阀改变流量)
根据转体角度58°
及上转盘半径4.5m,计算出钢绞线牵引长度L=4.55m。
64米梁端转过弧线长度为64.75m。
计算出千斤顶动作速度V=(2.7÷
0.)×
60=5.2m/h。
a、转体所用时间:
转体角度为58°
其中起转从0°
至58°
,58÷
1.09=51分钟,点转2°
,经验耗时6分钟,合计用时间37分钟,临时限位用时15分钟。
b、牵引钢绞线速度:
0.09m/min。
c、转体角速度:
1.09°
/min,即0.019rad/min;
d、转体悬臂端线速度:
1.09÷
360×
(2×
64.7×
3.1415)=1.23m/min。
根据《高速铁路桥涵工程施工技术指南》(铁建设【2010】241号文)相关规定,转体角速度不宜大于0.02rad/min,且桥体悬臂端线速度不大于1.5m/min。
上述计算数据均满足规范要求。
5.2.4.4转体前准备工作
(1)将设备安装和试运行:
连接好主控台、泵站、千斤顶间的信号线,接好泵站与千斤顶间的油路,连接主控台、泵站电源;
平转千斤顶、牵引索、锚具、泵站配套安装、调试。
要求各束钢绞线平直、不打绞、纽结。
然后设备空载试运行。
根据千斤顶施力值(启动牵引力按静磨擦系数μ=0.1,转动牵引力,按动磨擦系数μ=0.06考虑)反算出各泵站油压值,按此油压值调整好泵站的最大允许油压,空载试运行,并检查设备运行是否正常;
空载运行正常后再进行下一步工作。
设备运行流程:
1)自动运行前,1#、2#连续千斤顶的前、后顶的活塞都在行程开关的
位。
2)控制系统给泵站及阀本柜的电磁阀通电信号,前顶前进。
3)前顶前进到行程开关的②号位,行程开关反馈信息给控制系统,控制系统给1#、2#顶的电磁阀通电信号,后顶前进、前顶停,前顶延时回程,前顶回到
号位停止。
4)后顶前进到行程开关的②号位,行程开关反馈信息给控制系统,控制系统给1#、2#顶的电磁阀通电信号,前顶前进、后顶停,后顶自动延时回程,后顶回到
经过前、后顶的交叉运行,使转盘连续地,无冲击的运行。
(2)助推千斤顶安装。
根据需要,将2台YCW250B辅助转体千斤顶对称、水平地安放到合适的反力座上,根据需要在启动、止动、姿态微调时使用。
(3)安装牵引索。
(4)安装微调及控制设备,作好各种测控标志,标明桥梁轴线位置。
各关键部位再次检查,确认签字。
(5)梁体精确就位的准备工作
A、转提前做一张转体刻度表,贴在上转盘上,并用钢筋焊一个指针,方便读数。
刻度盘分两个区,分别为:
①转动区,为56.5°
;
②点转区,为1.5°
并指针对准0刻度,在转体过程作为初步控制。
B、在梁端梁体分中位置准确的贴上刻度标,作为标尺,并在和转体梁边墩相近的墩顶架设仪器