耐火材料中间包用技术Word格式.docx
《耐火材料中间包用技术Word格式.docx》由会员分享,可在线阅读,更多相关《耐火材料中间包用技术Word格式.docx(19页珍藏版)》请在冰豆网上搜索。
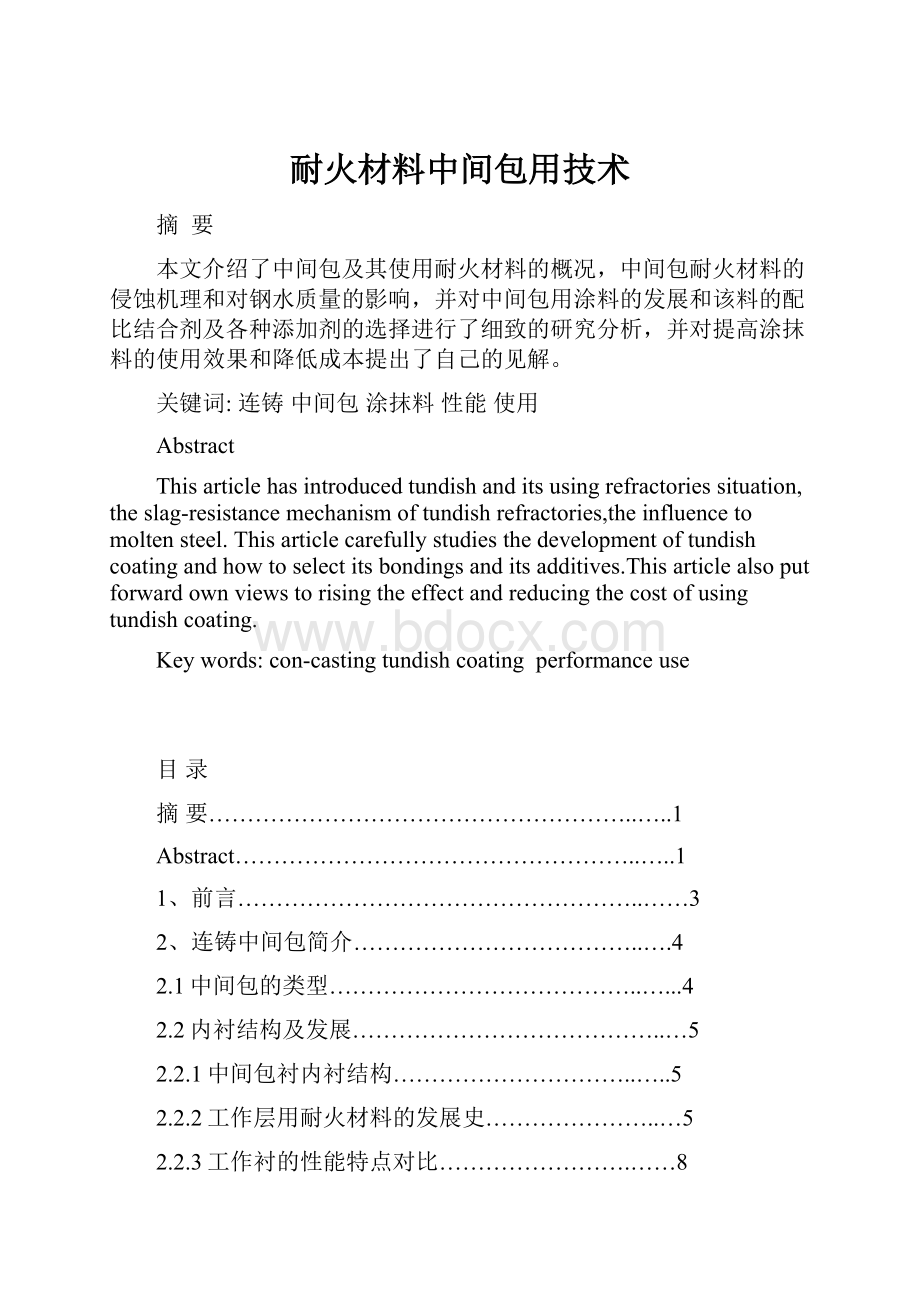
本文就对涂抹料的应用、发展与研究做些阐述。
2连铸中间包简介
中间包是连铸工艺的重要设备之一。
在连铸过程中,中间包不仅起着均匀钢水温度的作用,而且是钢包与结晶器之间的缓冲器。
随着冶金工艺的不断发展,还赋予中间包新的功能,如在中间包中进行的钢水精炼和非金属夹杂物的消除等冶金过程。
图1 中间包示意图
2.1中间包的类型
按浇铸钢种冶炼方式和是否需烘烤等条件,中间包大体分以下几种类型:
(1)高温中间包,为某一特定的冶金过程所设置,采用镁砖内衬,预热至1500℃左右;
(2)热中间包,是常见的中间包,采用烧成砖或不烧砖或浇注料作内衬,浇铸前预热至800-1100℃;
(3)冷中间包,采用绝热板作内衬,在浇铸前不经预热即可使用。
2.2内衬结构及发展
2.2.1中间包衬内衬结构
中间包衬一般由隔热层(材料为轻质砖或隔热材料)、永久层(粘土砖或浇注料)和工作衬(绝热、板涂料或干式料)组成。
其中工作衬有多种,而涂料内衬目前使用比较普遍。
(1)保温层(10~30mm),该层紧挨着中间包钢壳,通常砌石棉板、保温砖或轻质浇注料。
效果最好的为隔热纤维板,厚约12mm,热导率低,也易砌筑。
(2)永久层(100~200mm),该层与保温层相接触,其材料一般为粘土砖。
整体永久衬最为普遍,浇注料一般为高铝质。
(3)工作层(20~50mm),该层与钢水接触,是关键部位。
该内衬材料有半硅质、蜡石质、粘士砖、高铝砖、碱性砖(如镁质砖等)、锆英石砖;
或用绝热板:
硅质绝热板、镁质绝热板、镁橄榄石质绝热板;
或用涂料:
镁质、镁铬质及镁钙质涂料等。
目前也有用浇注料作中间包内衬。
2.2.2工作层用耐火材料的发展史
(1)第一代工作衬
即无下作衬阶段(连铸工艺出现在20世纪70年代。
欧洲可能延长到8O年代末)。
把日前的永久衬直接当工作衬或钢水直接接浇在永久衬上。
此方法只可用于无需洁净炼钢的低质钢的生产。
工作衬的维修费用很高,而且清除使用后的渣壳也很困难。
典型的高铝质低水泥浇注料内衬,其氧化铝含量在70%左右。
其理化性能如表1所示(日新钢铁公司五厂65t中间包永久衬浇注料)
表1日新钢铁公司五厂65t中间包永久衬浇注料理化性能
化学成分(%)
永久衬浇注料
Al2O3
61
SiO2
36
体积密度(g/cm3)
110℃,24h
2.52
1000℃,3h
2.50
1400℃,3h
2.48
线变化率(%)
-0.07
+0.07
抗折强度(MPa)
7.8
7.6
11.5
耐压强度(MPa)
34
69
83
(2)第二代工作衬
即绝热板阶段(20世纪70-80年代),材质大部分为镁质。
典型的镁质板成分如表2所示(瑞典研究的无机结合橄榄石基泡沫绝热板),此绝热板是保证洁净炼钢的有效方法。
该板以中间连锁板安装,与永久衬之间有填充砂支撑,并采用真空成型。
它绝热性能良好,但安装时劳动强度大,而且在使用过程中容易造成钻钢变形从而导致寿命下降,影响到连铸阶段的正常生产。
表2瑞典研究的无机结合橄榄石基泡沫绝热板理化性能
化学组成(%)
MgO
60
30
FeO
7
CaO
1
体积密度(g/cm3)
1.0
抗折强度(MPa)
2.0
导热系数(W/m·
k)
0.5
寿命(浇注次数)
(3)第三代工作衬
为了提高中间包内衬的使用寿命,降低耐火材料消耗,便于清除内衬上的残渣和残钢,许多国家采用耐火涂抹料(手工)或喷涂料(机械喷涂)作保护层。
涂料衬兴起于日本,瑞典、俄罗斯等欧洲国家也相继研究并以投入工业应用,而我国于20世纪90年代才相继推出试验。
涂料的材质有镁质和镁钙质,从施工方法来看有:
人工湿法涂抹、人工半干法机械喷涂、人工湿法机械喷涂、机械全自动化半干法喷涂等。
涂料衬采用湿法人工涂抹或机械喷涂时,需加入20%~30%的水。
因而中间包使用前需要2~6h,甚至更长时间的干燥以便除去水分。
涂料衬虽然有比绝热板有更好的整体使用性能,且解体性更好,便于清除渣壳,并且寿命还能满足现阶段连铸生产的需要,但是涂料衬无法满足更长连续浇钢工作环境的需要。
(4)第四代工作衬
为了适应高效连铸工艺的发展,国内的莱钢炼钢厂对连铸中间包定径水口快速更换与中间包长寿技术进行了研究,并率先开发成功。
由于中间包对其工作衬使用寿命提出了更高的要求,因此第四代干式料于20世纪90年代末应运而生,现有逐步取代涂料的趋势。
由美国UniversalRefractoryCompany率先研制使用的中间包干式工作衬已投入使用,其理化性能与喷涂料的性能比较,如表3所示:
表3中间包干式料与喷涂料的性能比较
Universal干式料
典型喷涂料
化学成分%(MgO)
85~92
80~85
烧碱%
2.5~3.0
1.0~3.0
所需水分%
20~30
处理后密度(g/cm3)
2.1~2.2
1.4
典型干燥处理时间h
1.25
1521.8
典型衬厚度mm
10~15
15~20
最多连浇炉数及时间/包,h
162(95)
8~16(8~16)
2.2.3工作衬的性能特点对比
每一代工作衬都是不同历史发展阶段的产物,而且后一代相对于前一代都有其独特的优势,以下从八个方面分别比较了它们各自不同的性能特点,如表4所示:
表4不同代工作衬的性能特点比较
浇注料衬(无工作衬)
绝热板
涂料
干式料
材质
高铝质
硅质或镁质
镁质或镁钙质
施工方法
振动
真空机压
涂抹或喷涂
振捣
加热方式
慢
较慢
较快
迅速
抗侵渗性
抗渗好但抗侵差
均好
抗侵好但抗渗差
抗蚀性突出
解体性
无法解体
好
较好
优异
保温性
最差
一般
洁净性
差
连浇时间
长且维护难
长且易钻钢
短且维护易
长且维护易
从表4中可以清楚地看出,总体趋势是随着连铸生产工艺的不断进步,从第一代逐渐过渡到第四代工作衬,其综合性能是逐渐优化的,尤其中干式料衬显示出了其它三代衬与其无法相比拟的优越性能。
2.2.4连铸中间包涂料的发展趋势
随着连铸工艺的发展,研究开发长寿耐用、具有洁净钢水功能的连铸中间包涂料成为今后耐火材料研究开发的主要课题之一。
“长寿化”和“洁净化”是连铸中间包涂料的两大发展趋势。
1、涂料的长寿化
随着冶金工艺的发展,降低吨钢涂料消耗增加连浇炉数、提高生产效率、有效地降低生产成本,是众多的冶金企业追求的目标。
而提高中间包的使用寿命,可以很好地满足这些要求。
目前,国内普遍使用的是镁质涂料,其主体原料大多采用中档镁砂。
为了使涂料的使用寿命能有较大幅度的提高,可考虑采取以下几个措施。
(1)尽量降低Na20、K20、SiO2、Fe0等杂质的含量,以最大限度地降低高温下易形成低熔点相的可能性。
(2)改善并强化基质,提高基质的抗侵蚀性和抗渗透性,从而提高涂料的高温性能。
(3)引入添加剂,改善其施工性能。
(4)采用高档主原料(这同时也提高了原料的纯度),从根本上提高涂料的整体耐侵蚀性。
2、涂料的洁净化
(1)洁净化的意义
虽然我国的钢产量位居世界第一,但普通钢种占了相当大的比例,每年仍需花费大量外汇从国外进口相当数量的各种优质钢材,以满足经济建设的需要。
在优质钢材的生产过程中,要求尽量降低夹杂物的含量,因而涂料的“洁净化”功能显得尤为重要。
在连铸过程中,利用涂料与钢液接触时对钢液中的A1203、SiO2、Fe0等的化学作用,可进一步除去钢中的非金属杂质成分,这对制造优质特种钢十分有利。
(2)“洁净化”的含义
涂料的“洁净化”就是利用其本身所含有的Ca0与钢液中的夹杂成分反应进而降低其含量的冶金过程。
例如:
A1203+3Ca0→3Ca0·
A1203
(1)
上述反应生成的铝酸钙从钢液中上浮与钢液分离,从而达到了净化钢液的目的。
(3)研制“洁净化”涂料的主要措施
通过近几年的摸索,专家认为在镁质涂料的基础上,设法引入尽可能高含量的Ca0,可达到净化钢液的目的,担须保证涂料的抗侵蚀性能不受太大的影响。
随着冶金工艺的技术进步,为了满足用户降低耐火材料消耗、提高生产效率的需要,研制“长寿化”涂料是连铸中间包涂料的一大发展趋势。
为适应冶炼高级洁净钢的需要,研制“洁净化”涂料是它的另一趋势。
3中间包用涂抹料
中间包涂抹料由镁砂、纤维、结合剂、防裂剂、减水剂等混合均匀装袋,使用时需要加入搅拌机中,并加水搅拌成可塑泥料状,通过人工涂抹或机械喷涂到中间包永久层上,此后自然养护24小时以上即可投入使用。
使用前要烘烤到1000℃左右,之后在装入钢水进行连铸。
3.1中间包对涂抹料质量的要求
a.具有良好的黏结性和一定的可塑性,使材料便于涂抹施工;
b.凝固时间适当,要求施工后快速凝固,凝固时间过长会使包壁垮料,同时料裂纹也会增加,一般凝固时间一小时左右为宜;
c.在常温或50~150℃温度条件下黏结性好,附着率高;
d.常温下无裂纹,快速烘烤到使用温度后不剥落、无炸裂、不与永久层脱离;
e.抗侵蚀性、抗冲刷性好;
f.隔热、保温性能好;
g.使用完毕易于翻包清理。
3.2原料准备
在涂抹料性能达标的前提下,其生产成本应尽可能的低,涂抹料所用的镁砂有:
电熔镁砂、烧结镁砂、高纯镁砂、中挡镁砂等不同档次,价格差异也很大;
结合剂和添加剂有:
磷酸盐、硅酸盐、硫酸盐、氯化镁、软质粘土、高铝水泥、各类纤维等价格差异也很大。
因此,选择合适的结合剂对提高产品质量和降低成本具有很重要的意义。
a.镁砂:
表5不同镁砂各个组分含量比
MgO(%)
CaO(%)
SiO2(%)
Al2O3(%)
Fe2O3(%)
中档镁砂
95
1.51
1.07
1.16
0.41
重烧镁砂
91.86
2.17
2.24
1.09
1.65
b.三聚磷酸钠:
采用工业用一级品:
P2O5≥56.5%,Na5P2O10≥90%,PH9.2-10.0,白色粉状
c.硅酸钠:
采用工业一等品:
可溶团体含量≥97.0%;
模数(u)3.5-3.7,
白色粉状
d.硫酸镁:
主含量≥98.0%,水不溶物≤0.10%,白色粉状
e.氯化镁:
采用普通一级品:
MgCl2≥45.0%;
,白色粉状
f.软质粘土:
采用河南焦作软质粘土:
Al2O328.50%,SiO269.16%
Fe2O31.21%,CaO0.22%,MgO0.43%
j.高铝水泥:
采用电熔铝酸盐925﹟水泥
3.3粒状料选择
中间包涂抹料要求使用时有一定的保温隔热作用,因此用其他耐火材料配比不能达到一定的体积密度。
需要考虑涂抹性能,烘烤性能和抗裂爆性能,因此,做了5个配方进行试验:
表6试样配方
重
烧
镁
砂
1﹟
2﹟
3﹟
4﹟
5﹟
3-5(mm)%
26
10
/
3-1(mm)%
24
38
1-0(mm)%
20
200目%
22
28
软质粘土%
2.5
三聚磷酸钠%
1.5
硅酸钠%
高铝水泥%
纸纤维%
用5种配方配制5Kg试样,加水18%,搅拌均匀进行涂抹性能比较试验。
涂抹性能:
1﹟﹤2﹟﹤3﹟﹤4﹟﹤5﹟。
细粉料少不易涂抹,2﹟相对于3﹟、4﹟、5﹟配方颗粒比较大,塌落严重。
5﹟配方凝固过快。
分析后认为镁砂粉过多由于镁砂细粉和水反应后使涂料水分减少,使涂料过早凝固。
MgO+H2O→Mg(OH)2
(2)
另外细粉过多,涂料自然养护过程中产生裂纹也越多,综上分析,最终选择3#配方比较合适。
3.4结合剂的选择
根据作为镁质材料的结合剂很多,从原料来源和市场价格来考虑,目前比较常用的结合剂有:
三聚磷酸钠、六偏磷酸钠、硅酸钠、硫酸镁、氯化镁。
高铝水泥既是涂抹料的结合剂又是磷酸盐和硅酸盐的促进剂。
软质粘土只要作用是提高涂抹料的可塑性和涂抹性能,也有一定的结合作用。
因此,用高铝水泥和软质粘土一并进行试验。
(配方见表7、表8)
表7结合剂的选择试样配方
1#
2#
3#
4#
5#
6#
重烧镁砂
3-1(mm)%
120目%
200目%
3.0
三聚磷酸钠%
3.5
六偏磷酸钠%
硫酸镁%
氯化镁%
加水量(外加)
16.0
17.0
18.0
19.0
凝固时间(分)
42
45
75
70
40
2.08
1.95
1.90
2.25
抗折强度(Mpa)
1.10
1.05
1.00
0.85
0.90
800℃,3h
2.00
1.94
1.93
1.89
2.15
2.30
2.26
1.83
1.55
2.21
1500℃,3h
2.05
1.97
1.98
1.91
2.03
2.10
1.56
1.82
表8结合剂的选择试样配方
7#
8#
9#
10#
11#
12#
120目%
200目%
软质粘土%
三聚磷酸钠%
六偏磷酸钠%
硅酸钠%
硫酸镁%
氯化镁%
高铝水泥%
纸纤维%
65
90
50
110℃,24h
0.98
0.82
0.80
1.01
0.94
1.92
抗折强度(Mpa)
1.96
2.06
2.04
2.01
2.22
2.40
从以上数据分析可以看出:
a.随着热处理温度的提高,涂料中水分进一步排出,纸纤维300℃以上开始碳化燃烧,涂料体密逐渐降低1500℃×
3h烧后体密和800℃×
3h烧后体密变化不大,在与1500℃烧后体密有关。
b.110℃×
24h和800℃×
3h处理后的抗折强度来看,磷酸盐和硅酸盐为主结合的涂料显著提高了。
这是由于水分蒸发,结合剂进一步将水与镁砂反应生成高强度磷酸盐,磷酸盐的反应物、硫酸镁和氯化镁结合的涂抹料抗折强度相对提高而密度比较小,分析是由于具有结合作用的Mg(OH)2随温度的提高而分解,抵消了一部分强度。
c.三聚磷酸钠的减水作用比较明显,加入0.5~1.0%就具备了减水作用。
三聚磷酸钠结合的涂料,烘干后和800℃烧后强度相对较高,但1500℃烧后强度有所降低,分析是部分硅酸盐在高温下分解而失去结合强度。
d.六偏磷酸钠的减水效果不如三聚磷酸钠,且涂料的强度和体密不如三聚磷酸钠结合的涂料。
e.硅酸钠结合的高温涂料烘干强度不是太高,但由于它具有高温烧结作用,因此高温烧后强度比较高。
f.高铝水泥具有很强的促凝作用,特别对于磷酸盐和硅酸盐结合的涂抹料促凝作用更强。
g.氯化镁和硫酸镁的作用主要是促进镁砂水化生成Mg(OH)2,而Mg(OH)2具有胶凝作用,从而起结合作用,强度相对较低。
h.随着黏土加入量的增加,有利于涂抹料施工,从试验中得知附着效果1#、2#、3#依次提高,3#自然养护后裂纹比较多,分析是由于黏土脱水收缩引起,因此加入黏土不能过多。
综上所述:
选择11#、12#涂抹料比较合适,12#涂抹料更佳。
3.5纸纤维加入量
纸纤维的作用主要是调节涂抹料的体积密度,随着纸纤维加入量的增加体积密度降低,同时隔热、保温效果加强,相应抗侵蚀性能降低。
一般加入量0.5~1.5%。
3.6镁砂的选择
根据连铸时间相选择相应档次的镁砂,一般连铸10小时以下的涂抹料选用中档镁砂做颗粒和细粉;
一般连铸15小时以下的涂抹料选用烧结镁砂做颗粒和中挡镁砂做细粉。
3.7中间包涂抹料的生产与使用
3.7.1中间包涂抹料的生产
按照12#配方的配比要求,选用重烧镁砂作颗粒和细粉生产30t,选用重烧镁砂作颗粒和中挡镁砂做细粉生产30t。
分别运到成都钢厂和南京梅山钢厂进行使用试验。
生产用250号强制搅拌机搅拌涂抹料。
各物料称量好后先加入颗粒料,然后加入纸纤维,混匀后再加入镁砂细粉和其他结合剂、外加剂。
混合均匀后出料,人工装