煤气操作规程Word格式.docx
《煤气操作规程Word格式.docx》由会员分享,可在线阅读,更多相关《煤气操作规程Word格式.docx(29页珍藏版)》请在冰豆网上搜索。
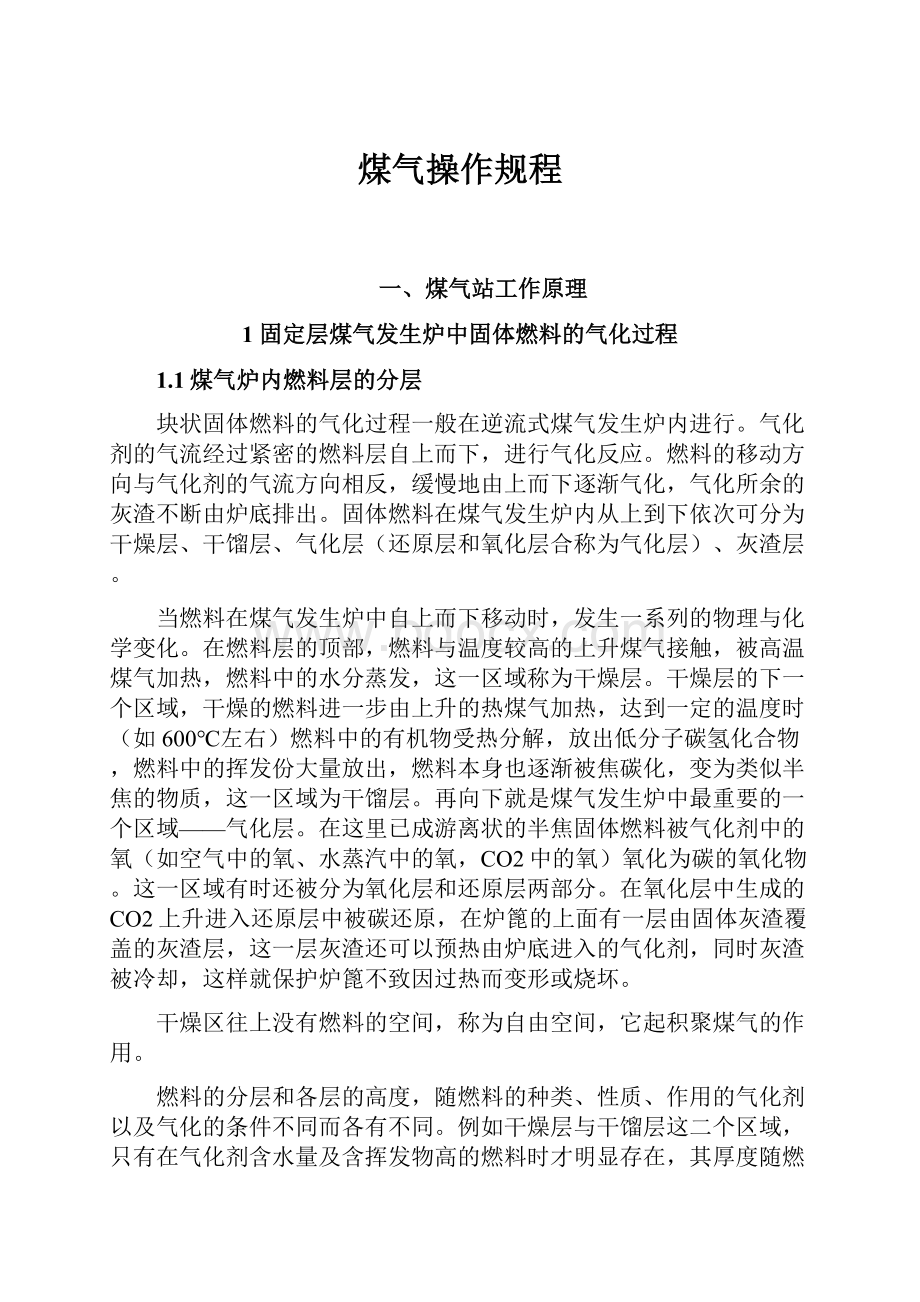
H2O+C=CO+H2
H2O+CO=CO2+H2
3
还原层
CO2还原成CO,燃料依靠与热气体换热而被预热
CO2+2C=2CO
4
干溜层
燃料依靠热气体换热进行热分解,并析出下列物质。
水分、醋酸、甲醇、甲醛、苯酚、树脂、气体CO、CO2、H2S、CH4、乙烯、氨、氢、氮
C+O2=CO2
2C+O2=2CO
C+2H2=CH4
H2+S=H2S
5
干燥层
依靠气体与燃料的换热来蒸发燃料中的水分
6
上部空间
起积聚煤气的作用
少量CO+H2O=CO2+H2
1.2沿燃料层高度气体组成及其变化
当用空气为气化剂时,在炉底的一小段距离内,即灰渣层,氧浓度保持不变。
因在灰渣层中的碳已基本上消失,且温度较低,空气中的氧不能反应。
进入氧化层后由于氧与碳的剧烈反应,氧的浓度迅速下降,CO2的浓度达到最高值。
气流进入还原层后CO2大部分被碳还原,CO2浓度逐渐下降而CO的浓度逐渐上升。
氧化层中气体的特点是:
其中还有一定量的未反应的游离氧(含氧2-5%),CO2的浓度很高(可达10-16%),CO的浓度很低。
氧化层中CO与CO2相应量的多少,与燃料活性与颗粒大小有关。
当燃料颗粒小活性好时,气体中的CO量增多而CO2量减少,温度也相应的降低,反之亦然。
氧化层是燃料层中温度较高的区域,在这层所进行的反应属放热反应。
氧化层中所进行的反应速度极快,所以氧化层厚度较薄,一般在100-120㎜。
氧化层的上部(与还原层相邻的部分)是以CO2的浓度达到最高后急剧下降和相应的CO浓度急剧上升为特征的。
此时气流中氧含量的多少,将随燃料品种和性能的不同而有差别。
还原层的特点是:
除了开始很少的一部分,该层的绝大部分不含游离氧。
这一层进行的主要是吸热反应,而且还原层的温度随反应进行逐渐降低,所以还原层的厚度远远超过氧化层。
用水蒸汽作为气化剂时,灰渣层中水蒸汽未分解,浓度不变。
进入氧化层后在高温下水蒸汽与碳剧烈反应,根据温度计算,在900℃时,碳与氧的反应速度接近碳与水蒸汽的反应速度。
而在1100℃时,碳与水蒸汽的反应速度大于碳与氧的反应速度。
因此,在氧化层中水蒸汽迅速分解,生成大量和CO、H2、CO2。
温度较高时,CO的生成量较CO2生成量大。
由于反应需要吸热,氧化层温度逐渐降低,反应速度减慢。
气体进入还原层时仍有相当量水蒸汽继续与碳反应,但主要是由氧化层来的CO2与碳反应还原成CO。
因此,在还原层中氢与CO含量在继续增加而CO2逐渐减少。
由于还原层中仍有碳与水蒸汽中的氧化反应,因此氧化层与还原层无明显界限。
氧化层的主要特征是气体中含氢迅速增加,水蒸汽含量迅速下降,还原层的主要特征则是CO2含量逐渐降低。
当以空气、水蒸汽同时为气化剂时的气化过程与单独用空气,或单独用水蒸汽进行气化时的气化过程有所不同。
在空气与水蒸汽同时进入燃料层时,首先接触的还是氧化层(仍以游离氧的存在为特征)。
但此时该层的反应比单独通入空气时要复杂得多。
由于氧化层的温度很高,所以在碳与氧反应的同时水蒸汽也必然会与碳反应。
所以氧化层中碳的氧化速度要比单独用水蒸汽或空气时为快。
以水蒸汽与空气同时作为气化剂时,由于通过氧化层的气流中尚有部分游离氧,氢和氧的反应在高温下,速度很快,因此在氧化层中未发现氢的存在。
在氧化层中,开始时气化剂中O2量急剧下降,水蒸汽含量不变,其后,在氧含量下降到接近零时,CO2又迅速下降,大量CO迅速生成。
氧化层的上面是还原层,还原层的反应情况与单独通入水蒸汽时无原则上的区别,只是气体中除H2外。
还有相当多的CO2和N2。
N2的存在,降低了水蒸汽和CO2的分压,从化学平衡的角度来看,对生成氢和CO的反应有利。
从反应的热平衡角度来看,水蒸汽与空气同时通入燃料层的气化过程,是热效应相互抵消的过程,这样就有得于维持燃料层温度的恒定。
为了进一步分析各反应进行的部位和相互关系,须明确燃料层中各层之间量之间的关系。
我们称H2/(H2+H2O)为水蒸汽的分解量,(CO+CO2)/N2为碳氧化物量,CO/CO2为碳氧化物转移量。
在氧化层上约20-60㎜的部分,上述三层同时激增。
由此可以认为这主要是下列三个反应在起作用。
H2O+C=CO+H2,H2O+CO=CO2+H2,CO2+2C=2CO,这部分称为第一还原层。
在此层几乎没有CO和水蒸汽的反应,否则(CO+CO2)/N2值应无变化,CO/CO2值应有所下降。
在第一还原层往上,即氧化层上约60-100㎜部分,(CO+CO2)/N2值保持不变,而H2/(H2+H2O)值有所增加,CO/CO2值也略有增加,这主要是由于下列两个反应起作用的缘故。
即H2O+CO=CO2+H2,CO2+2C=2CO,这部分称为第二还原层。
由于CO和水蒸汽的反应继续进行,在燃料层的上部,H2/(H2+H2O)值稍有增加,CO/CO2值稍有增加。
沿煤气发生炉内燃料层高度温度分布与燃料层内的反应、气流与燃料的换热情况相适应,亦与气化剂的流速有关。
2混合发生炉煤气工艺原理
以块煤或煤棒为原料,采用蒸汽和空气的混合物作为气化剂由炉底送入。
气化剂与煤逆流接触,气化过程进行得比较完全,灰渣中残炭少。
碳与氧的反应是放热反应,其放出的热量供给碳与水蒸气的反应。
由于碳与水蒸气的反应是吸热反应,就可以降低气化层中温度,使灰渣维持在不熔融状态,而煤气发生炉就可以采用固态排渣。
同时水蒸气与碳的反应能产生CO和H2,使煤气热值提高。
这种煤气称为混合发生炉煤气。
由于产物气体的显热中的相当部分供给煤气化前的干燥和干馏,煤气出口温度低,而且灰渣的显热又预热了入炉的气化剂,因此气化效率高。
目前,混合发生炉煤气在工业上应用很广。
理论上,制取混合发生炉煤气是按下列两个主反应进行:
2C+O2+3.76N2=2CO+3.76N2+246435KJ
C+H2O=CO+H2-118821KJ
由热平衡条件可知,每2kmol碳与空气起反应则与水蒸气起反应的碳应为2.07kmol,则反应方程式可写为:
2C+O2+3.76N2+2.07C+2.07H2O=4.07CO+2.07H2+3.76N2
按照理论计算气化效率可达100%,但是实际上,制取发生炉煤气时,不可避免有许多热损失(煤气带走的显热和煤气炉外壳的热损失等),另外由于水蒸气分解和CO2的还原反应进行得不完全,使实际的气化指标(煤气组成、气化效率等)与理论计算值有显著差别。
实际上我们的工艺就是围绕以上几个方面展开,也就是追求最少的热损失、提高CO2的还原程度,合理的蒸汽分解率,尽可能高的气化效率和气化强度等。
二、煤气发生炉
煤气发生炉是煤气站的最主要设备之一,是煤与气化剂进行气化反应的场所。
煤从煤气炉顶部入料口由自动加煤机加入,气化剂(空气与蒸汽)从炉底中心管线进入煤气炉。
气化剂与煤气炉的灼热的碳发生反应生成煤气,煤被气化并形成煤渣。
煤气炉的要完成的任务就是:
均匀分布气化剂、发生气化反应生成煤气、排出炉渣、水夹套产生蒸汽(热水)。
1煤气发生炉
炉上体、炉体裙座灰仓、炉底总成、炉篦、传动机构、出灰机构、炉体支撑。
炉上体:
由炉顶盖和水夹套组成,炉顶顶部有进煤口、出气口、看火孔、量碳孔装置。
水夹套主要用于产生蒸汽,同时防止炉内挂壁。
炉底总成:
由炉底盘、灰盘、大齿轮、上下导轨组成。
炉底盘用于支挂炉内部件;
灰盘用于装灰,转动与灰犁配合出灰;
大齿轮用于灰盘传动;
上下导轨用于灰盘传动,内装钢球。
下导轨安装于炉底盘上,上下导轨成对安装,灰盘安装于上导轨上,大齿轮安装于灰盘上,大齿轮与炉条机小齿轮成对。
炉篦:
炉篦是煤气炉的核心部件。
起到均匀分布气化剂的作用,同时起破渣排渣的作用,炉篦安装于灰盘上,与灰盘同时转动。
选择性能较优的炉篦,煤气炉内气化层温度高,气化层均匀不偏炉,煤气热值高,煤耗低,炉内不结焦不需要打钎。
传动机构:
煤气炉传动机构主要作用是为煤气炉灰盘转动提供动力并实现减速。
主要由电机、减速机、小链轮、大链轮、封闭式炉条机等组成。
封闭式炉条机内装有蜗轮、蜗杆、立轴、小齿轮。
小齿轮与炉内大齿轮配对。
出灰机构:
由灰犁、下灰插板阀(南北各一)、下灰圆盘阀、灰渣箱等组成。
炉体支撑:
由四根支柱、炉体支撑框架、炉体支腿等组成。
1.1主要性能参数表
参数名称
炉型单位
J-28
炉膛
内径
mm
Ф3000
横截面积
m2
7.07
水套
工作压力
MPa
0.1
受热面积
≈31
蒸汽产量
kg/h
800-1200
水耗量
880-1330
气化剂
空气+水蒸汽
煤气出口直径
Ф820
加煤机加煤量
kg/次
200-300Kg
炉篦传动
减速机
型号
JZQ350-23.34-1
电机
YDX132M-4
功率
kW
7.5
水套用软化水
悬浮物
mg/l
<
20
酸碱度
PH(25℃)
6.5~9.6
总硬度
毫克当量/升
2.1
1.2煤气炉示意图
三、煤气站操作规程
1岗位任务
1、调节煤气炉生产负荷(通过炉底风机变频器频率调节入炉空气流量),确保煤气量满足后工序的要求。
2、调节煤气发炉入炉饱和温度(通过蒸汽调节阀开关调节入炉蒸汽流量),确保煤气炉炉况稳定,煤气热值满足后工序的要求。
3、操作控制自动加煤机正常均匀加煤,检查煤质,确认煤棒硬度,长度大小。
4、操作控制下灰装置正常均匀排出灰渣。
观察两边灰斗出渣量是否均匀和渣块大小、含碳量。
5、操作控制软水箱进水,确保软水箱不干水。
操作控制软水泵正常供水,确保汽包液位正常。
6、操作控制液压泵站,检查液压泵站油位、油温、油压,确保正常生产。
7、操作循环水泵,控制循环水量平衡,煤气冷却后的温度在正常范围内。
8、操作控制加压风机(通过加压风机变频器频率调节煤气流量),确保煤气压力稳定。
9、每班定期清理旋风除尘器、废热锅炉排水水封煤灰。
10、每班定期对加压风机、捕滴器进行排水。
11、每小时测量料层高度一次,每小时对所辖区域内设备进行一次巡回检查,检查内容见后面章节。
每小时记录报表一次。
12、每班统计加煤量、出渣量,并按交接班制度进行交接班。
13、定期按要求对设备进行润滑管理。
2试车
2.1煤气炉试车条件
1.试车前必须完成一切安装工作。
2试车操作现场地面应清扫干净。
3设备及附属仪器表应齐全,并经校准合格。
4试车及初开车应由技术熟练有经验的专人负责。
5试车前应有必须的防护用品及安全防火等设施,如灭火器,消防水等.
2.2试车质量要求
1炉条机及传动系统运转正常,电流稳定。
2煤气炉夹套锅炉部分用0.20MPa进行水压试验。
3微机运行稳定,仪表及联锁试车符合要求。
2.3炉条机试车
2.3.1单体试车
A拆开电动机和减速机的靠背轮,由电工全面检查设备确认是否可用
B盘动电动机
C启动电动机,注意电动机运转方向及电流情况。
D全速运转2h即可停车。
2.3.2联动试车
A连接好电动机靠背轮。
B检查并补足变速箱及轴承的油量。
C灰盘轴承加黄油
D将蜗杆的油盒内加足油量。
E启动电动机,留意电流不得超负荷,检查整套炉条机系统减速机传动装置的运转情况,不得有摩擦声及其他异常情况,电流指示应稳定,黄油注油情况应稳定。
F运转4h如一切正常即可分段加速试车,各种转速运行2h。
G试车过程如发现电流超负荷或炉条机运转发生异常情况等,应立即停车检查原因。
H联动试车2h后停车,并全面检查炉条机各部件。
2.3.3负荷试车
A炉条机的负荷试车应在开车生产前夕进行
B炉膛内装入炉渣,高出夹套锅炉即可。
C其试车步骤与联动试车步骤相同,炉条机加速试车时间即可适当减短。
D负荷试车1h即合格。
2.4炉底风机试车
1、试车准备条件:
(1)试车前必须结束一切土建及安装工作,并将操作现场全部清扫干净,风机进口管道清理干净。
(2)设备所属全部仪表及安全联锁装置应齐全,并经校验确定是否灵敏好用。
(3)设备电机及电气线路检查(由电气专业人员负责)。
①清除电动机及配电盘周围的杂物,使环境及电气设备本身达到清洁干燥。
②检查电动机绝缘电阻是否合格,有无接地线。
③在无电情况下试按电动机开停车按纽数次,检查动作是否正常。
④测量电源电压。
(4)安装后的试车及初开车过程中要指派有经验的专人负责。
(5)试车前应备有劳动保护用品及安全防火等设施。
(6)试车前必须检查电动机转动方向是否与鼓风机相一致。
2、试车的质量要求:
(1)鼓风机所产生之压力要符合技术要求。
(2)设备机座地脚螺丝的震动情况,螺丝不能松动。
(3)机体各部的震动情况及轴承等摩擦部分的温度要符合操作指标的要求。
(4)电动机及附属开关等的工作情况应处于正常状态,电流指示数不得超过规定值。
(5)管道、支架等同定设备的联结应牢固。
(6)设备及管道阀门等应无漏现象。
(7)所属仪表、空气压力调节器等灵敏好用。
3、单体试车与负荷试车:
电机先进行单体试车,运转方向正确并正常后转入空运转试车。
空运转试车:
在空运转时,吸入管和压出管拆开,空气不受压缩,此时主要试其装配质量及鼓风机、电动机之运转情况。
发现并消除其故障。
(1)推上鼓风机电机三相电闸。
(2)由电工启动电机,当电机能转动时立即停止,检查转动方向是否正确,有无其他不正常情况。
当电机达到正常转速后立即停车,此时检查倾听机体各部有无杂音及其他异常情况。
(3)如此反复3—4次如无异常现象,即可正式运转起来并加强各处检查,如发现下列情况时应立即停车检查处理:
①轴承或机体温度过高,或发生突涨。
②机体发生剧烈振动。
③机体发生金属碰撞或其他杂音。
④附属电气设备发生故障,或有冒烟着火等。
(4)鼓风机空运转1小时后即可停车。
负荷试车:
负荷试车为检查鼓风机在正常负荷情况下的工作情况,是否符合设计要求。
(1)负荷试车前的准备工作。
①联结好吸入管及压出管。
②检查仪表。
③关鼓风机出口阀。
④各炉空气支管阀门应关闭。
(2)鼓风机开车及负荷试车。
①由电工启动鼓风机电机,并注意运转情况。
②如鼓风机运转正常,即可缓开出口阀,使空气压入空气总管,此时应注意如下几点:
鼓风机马达的电流,不得超负荷。
鼓风机出口压力应符合所试风机规范要求。
发现异常情况应立即停车。
如一切正常,运转2小时后即可停车。
(3)、鼓风机的停车:
①关鼓风机出口阀。
②停鼓风机电机。
4、安全措施及注意事项:
(1)严格遵守试车规程,并按其步骤进行。
(2)参加试车人员应熟知试车操作规程及安全规程。
(3)电气设备应由电工操作,其他人不得任意乱动。
(4)电器设备着火应先切断电源,然后用干粉灭火器扑灭。
(5)试车人员应穿规定的工作服。
(6)机器在运转情况下不得进行任何修理工作。
(7)安全罩保护网及其他安全设施应符合试车要求。
(8)操作环境应有足够的亮度,夜间应有足够照明。
(9)试车人员不得离开操作地点,需要离开时,应交待给专人。
2.5夹套锅炉试压
1.开汽包放空阀,将软水加入汽包内进入夹套锅炉直至加满关闭放空阀。
2.检查液位计是否畅通,各处有无泄漏。
3.缓开进水管注意压力表读数上升至0.2Mpa关死进水阀,保持几分钟后无泄漏即可
2.5煤气炉烘炉
第一种方案(无耐火砖)
1.按煤气炉开车步骤操作(见后面正常开车)。
2温度控制在200-350左右,烘炉2天即可
第二种方案(有耐火砖)
2温升控制要求:
点火至110℃之间,每小时温升小于10℃,110℃恒24h;
110℃至240℃之间,每小时温升小于20℃,240℃恒温24h;
240℃至450℃之间,每小时温升小于30℃,450℃恒温8h,烘烤完毕。
3煤气站开停车
3.1煤气炉点火
1、煤气炉点火前准备:
煤气炉检修已完成,炉内脚手架已拆除,空气系统、软水系统、循环水系统、蒸汽系统、加煤系统、排渣系统、煤气系统、液压系统已全部具备开车条件方可进行煤气炉点火。
2、检查阀门开关状态:
确认液压系统不漏油的情况下,开启液压系统。
确认以下阀门处于开启状态:
汽包放空阀、汽包至水夹套的连通阀、水夹套至汽包的连通阀、汽包蒸汽出口阀、余热汽包至废热锅炉的连通阀、废热锅炉至余热汽包的连通阀、汽包蒸汽出口阀、水夹套两边的人孔、两边灰斗手孔、炉底中心管圆门。
确认以下阀门处于关闭状态:
南北下灰插板阀、南北下灰阀、两边灰斗加水阀、蒸汽调节阀、炉底中心管排水导淋、水夹套排水阀、自动加煤机插板阀、圆盘阀、大布料器阀。
3、煤气炉填渣:
筛渣:
用30㎜筛网筛子筛炉渣4吨左右粗渣。
填渣:
可先填细渣1-2吨左右在煤气炉内,填满炉篦以下的部位。
放完细渣后,必须将炉篦上的炉渣全部清理至炉篦下面,确认炉篦上面无细渣。
再填粗渣3-4吨在煤气炉内。
炉渣高出炉条帽200mm左右比较均匀为合格。
底煤:
均匀地加一吨左右块煤或煤棒至灰渣上,最好在中间位置铺设呈十字型油棉布。
柴浇废油:
从水夹套人孔处往炉内均匀铺设200-300mm高的木材,并浇上适量的废油。
4、检查以下水封状态:
确认放散管水封、旋风除尘器水封、低压总管水封、加压风机前后水封,处于正常水封状态。
5、将水夹套两边的人孔封好。
6、加水:
开启软水泵,使水夹套(看夹套锅炉汽包液位)、废热锅炉液位处于正常位置(看余热汽包液位)。
7、点火:
开启油泵,手动提起加煤机大布料器,并确认集散管水封阀处于开的位置。
打开加煤机大布料器快开门。
开下位机、上位机并确认通讯正常。
从加煤机大布料器快开门和炉顶看火孔将点燃油棉纱投入炉中,确认燃烧均匀正常。
8、自燃:
点火初期可通过开关南北灰斗插板及下灰阀调节空气量,待木材燃烧稳定后关闭中心管线园门,灰斗园门。
9、鼓风:
开炉底风机,逐渐向炉内鼓风,使空气流量约400~600m3/h。
10、加煤:
从看火孔观察,木材基本烧完时,可少量多次加煤,开始加煤约5分钟后用蒸汽调节饱和温度至65度左右。
11、调节火层:
打开南北灰斗插板阀,点火两小时后启动炉篦低速运行10分钟(不大于5HZ)。
关探火孔,逐步提高炉底压力,并用蒸汽调节饱和温度至正常,按正常炉出口温度加煤。
炉篦須适当低速运行(灰斗温度不高于80度),并适时出渣。
11、气体分析:
当料层至量碳杆70cm高时,温度大于400摄氏度取样分析,待煤气成分O2<
1%,热值大于1000大卡后可送入系统,煤气炉可转入正常开车。
3.2煤气站正常开车
1、检查阀门开关状态
放散阀,汽包放空阀(根据汽包进行调节)、汽包至水夹套的连通阀、水夹套至汽包的连通阀、汽包蒸汽出口阀、余热汽包至废热锅炉的连通阀、废热锅炉至余热汽包的连通阀、余热汽包蒸汽出口阀、南北下灰插板阀、两边灰斗加水阀、蒸汽调节阀、炉底中心管排水导淋。
低压总管水封、加压风机前后水封、南北下灰阀、水夹套排水阀、水夹套两边的人孔、两边灰斗手孔、炉底中心管圆门、自动加煤机插板阀、圆盘阀、大布料器阀。
2、旋风除尘器水封溢流正常,放散管水封加好,放散管水封阀落下。
汽包正常供水。
3、开下位机、上位机并确认通讯正常。
启动泵站油泵,调节油压为4.0—5.0Mpa。
4、检查并开启各油压考克,检查油压系统各处是否漏油。
5、检查炉子情况,炉温过高(大于450度)应手动补煤,炉温过低还应升温。
6、炉底先通入蒸汽约3分钟、然后将空气手动调节阀开一部分(约为平时生产时的一半),调节好饱和温度,取样分析煤气合格(O2<
1%,煤气热值大于1000大卡)后进行下一步。
7、启动循环水泵,洗气塔上水、排水正常,加压风机盘车正常,机壳排水。
8、开微机驱动电源,输入开车指令或按开车键开车,解除低压总管水封和加压风机前后水封,开加压风机。
9、调节饱和温度和空气的流量,满足煤气炉生产需要。
10、检查各阀门是否处于正常开车位置(旋风除尘器水封、低压总管水封和加压风机前后水封解除、左右灰斗插板阀开,其余均为关闭状态)。
3.3煤气站正常生产转热备(或短停)
1、停加压风机,加压风机前后水封。
2、开放散阀,在微机上停炉底风机。
低压总管水封。
3、关空气蒸汽混合器下部排污阀。
入炉蒸汽调节阀约10分钟后再关。
汽包放空阀视汽包压力决定打开。
4、热备时间长须加强检查,必要时小量加煤,确保不熄火。
5、停油泵(停车时间长时)。
如停电或停油泵需拉开集散管水封放空阀。
停油泵前,须先将灰斗内灰渣排净,并关闭南北下灰插板阀,关闭下灰圆门的油管球阀。
如要停电,关上位机、下位机并断通讯。
6、如需开看火孔须点火。
。
3.4煤气站热备(或短停)转正常生产
1、检查确认煤气炉各园门、人孔处于关闭状态,各水封溢流正常。
2、开下位机、上位机并确认通讯正常。
启动泵站油泵,调节油压为4