甲基叔丁基醚MTBE工艺Word格式.docx
《甲基叔丁基醚MTBE工艺Word格式.docx》由会员分享,可在线阅读,更多相关《甲基叔丁基醚MTBE工艺Word格式.docx(18页珍藏版)》请在冰豆网上搜索。
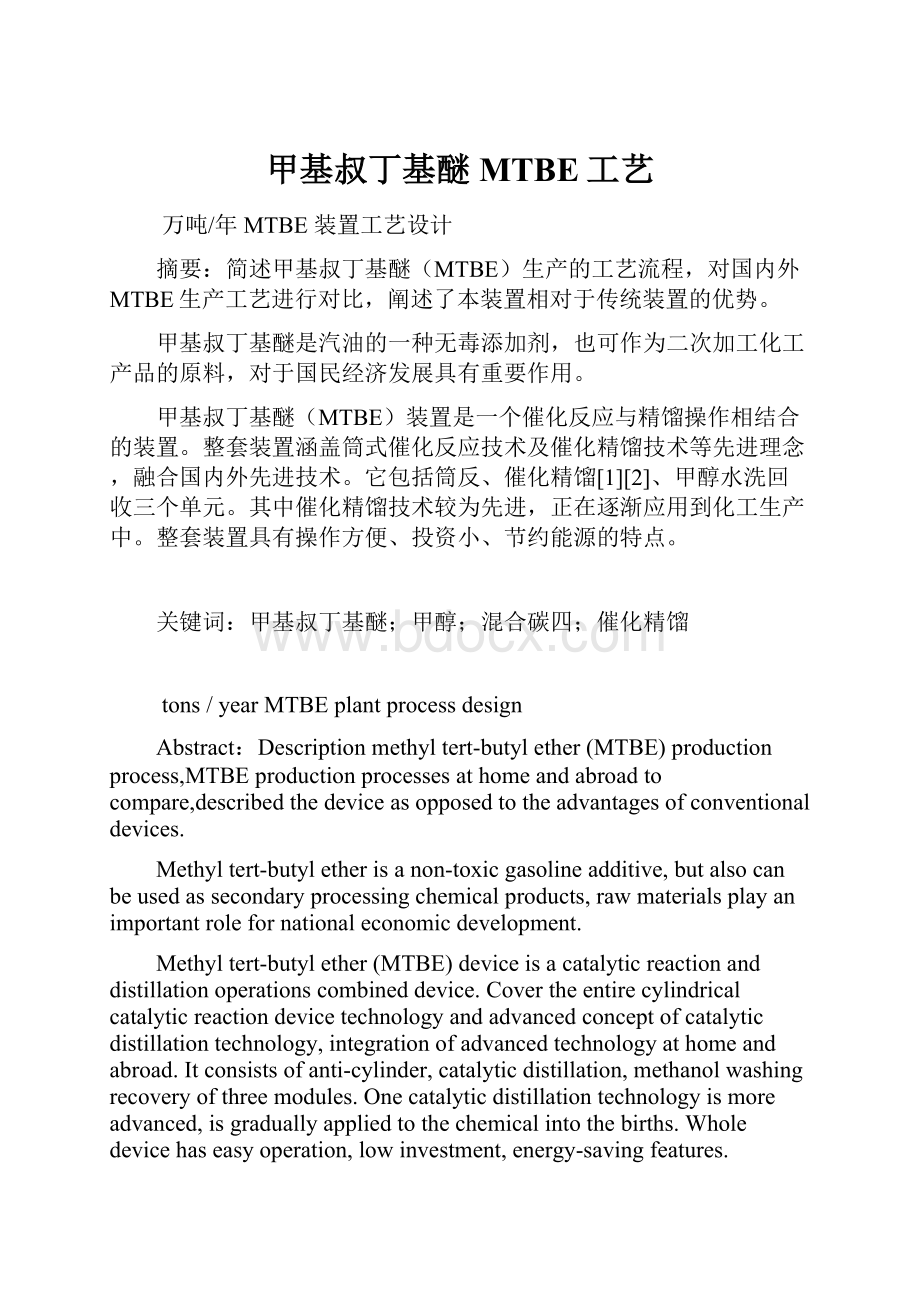
(一)甲醇·
(二)混合碳四·
8
(三)甲基叔丁基醚·
(四)副产物·
9
三、工艺流程及说明·
(一)筒式反应单元工艺流程·
(二)催化精馏单元工艺流程·
(三)甲醇回收单元工艺流程·
10
四、工艺流程图及说明·
五、化学反应·
12
六、物料平衡计算·
13
七、三废治理·
14
八、安全生产特点·
九、总结·
15
十、参考文献·
16
一、绪论:
(一)概况
本甲基叔丁基醚(MTBE)装置是万吨/年生产装置,对石油裂解气中混合碳四深加工项目。
整套装置包括筒式催化反应技术及催化精馏技术等先进理念。
它包括筒式反5E94[3]、催化精馏、甲醇水洗回收三个单元,其中催化精馏技术较为先进,具有操作方便、投资小、节约能源的特点。
MTBE装置自建成以来,又进行了多项改造,包括流程。
设备、仪表改造。
MTBE装置经过设备的改造及工艺流程的部分更改,基本实现计算机远程控制,现在整个装置生产平稳,可控性良好。
本MTBE装置生产能力为1100t/m,碳四进料量为4t/h(以含异丁烯40%~50%抽余碳四为原料进料量为8t/h)。
因碳四原料不足,生产负荷一般在60%左右。
装置最大可按120%负荷生产。
总之MTBE装置的工艺过程较合理,技术较先进,操作方便,产品质量稳定,经济效益较显著。
(二)工艺简介
MTBE装置以含80%异丁烯(40%~50%亦可作为原料)的抽余混合碳四和甲醇为原料。
甲醇和混合碳四按一定醇烯比连续送进筒式反应器和催化精馏塔,在一定压力和温度条件下,混合碳四中的异丁烯和甲醇在催化剂的作用下发生反应,生成MTBE。
MTBE产品从催化精馏塔塔釜采出送出装置。
反应后的剩余碳四和过量的甲醇,从催化精馏塔塔顶蒸出,经冷凝后部分回流入塔,部分采出至甲醇萃取塔,以去除剩余碳四中的甲醇。
剩余碳四从甲醇萃取塔底加入,洗剂水从顶部加入,甲醇含量合格的碳四组分从塔顶采出送出装置。
从甲醇萃取塔塔底排出的含有甲醇的水溶液,靠压差进入甲醇回收塔,常压下精馏,塔顶馏出的甲醇(纯度≥98%)采至甲醇回流罐,作原料循环使用;
塔釜采出(甲醇含量≤0.3%)部分送入甲醇萃取塔循环使用,部分排污出装置。
(三)国外生产工艺
1.意大利SNAM工艺
1973年意大利开发了世界上第一套MTBE工业装置。
早期开发的MTBE生产工艺大多是以许尔斯(HULS)工艺为代表的列管式固定床反应技术,反应温度50–60℃,产品MTBE的含量在98%以上。
催化剂是聚苯乙烯-二乙烯苯离子交换树脂。
反应器外多用冷却水移走反应热,产物用一个或多个分馏塔分离MTBE和甲醇以及剩余的C4馏分。
此工艺的缺点是难以消除反应区中的热点,因此在最近几年新建厂中已较少采用。
2.法国IFP工艺
IFP工艺的主要特点是反应器采用上流式膨胀床,与管式反应器相比,进料是自下而上进入反应器,其中催化剂处于蠕动状态,有利于传质及传热。
它具有结构简单、投资少、能耗低、催化剂装卸方便等优点。
另外,采用上流式操作,可防止催化剂堆集成块,减少压力降,催化剂使用寿命长,副反应少等优点。
3.美国催化蒸馏工艺
催化蒸馏工艺是由美国Chem.Research&
Liecensing公司首先开发成功的,于1987年工业化。
其核心是把反应与共沸蒸馏巧妙地结合起来,使醚化反应和产物分离在同一塔中同时进行,反应放出的热直接用来分馏,既减少了外部冷却设备又控制了反应温度,可最大限度地减少逆向反应和副产品的生成,防止了反应区热点超温现象,降低了能耗,节省了投资。
但该技术也有其不足的地方,主要是中部催化剂的填装比较困难,要严格用玻璃丝布外加不锈钢丝网将催化剂包起来置于反应段中,依靠包与包之间的空隙,使气液两相能够对流通过催化床,减少因催化剂颗粒小造成阻力大的问题。
但由于催化剂置于包中,反应物料必须扩散进入布包中才能与催化剂接触进行反应,反应后产物还要扩散出来,故对反应不利。
4.美国UOP公司的联合工艺
该工艺主要是以油田气或炼厂气中的丁烷为原料,异构化反应转化为异丁烷,进而脱氢生成异丁烯,异丁烯再与甲醇醚化反应生成MTBE。
联合工艺使MTBE生产具有更为广泛的原料来源,且可减低成本,单程转化率高,设备投资低,可靠性好。
(四)国内生产工艺
1.常规工艺
由反应、共沸蒸馏和甲醇回收三部分组成,使用固定床反应器,在强酸性阳离子交换树脂存在下液相合成MTBE。
反应压力0.98-1.47MPa,温度40–80℃,醇烯比为1.0左右,利用外循环方式取出部分反应热来控制反应温度。
异丁烯转化率可达90%-95%,接近平衡转化率。
2.催化蒸馏法工艺
由齐鲁石化公司开发出的一种新催化蒸馏工艺,它克服了美国催化蒸馏工艺催化剂填装的缺陷,采用一种新型的散装筒式催化蒸馏塔,催化剂直接散装入催化床层中,相邻两床层间设至少一个分馏塔盘,且床层中留有气体通道,整个反应段类似若干个重叠放置的小固定床反应器和若干个分设在各床层间的分馏段,反应与分馏交替进行,破坏其平衡组成,使反应不受平衡转化率高的限制。
3.混相床反应蒸馏工艺
该工艺是由齐鲁石化公司研究院、北京石油设计院和上海高桥石化公司炼油厂等单位在混相反应技术基础上开发的合成MTBE新技术,它融合了混相反应技术和催化蒸馏技术的优点。
其特点是将混相反应与分离相结合,在反应塔内设一固定床反应段,控制反应压力使反应在沸点温度下进行,反应热使部分物料汽化而使反应温度衡定,形成汽-液混相状态。
该技术分为炼油型和石油化工型两种类型:
炼油型工艺反应塔的中部是混相反应段,上部和下部分别为精馏段和提馏段。
催化剂装填容易、投资省、能耗和费用低,异丁烯转化率可达90%-98%。
化工型工艺是将炼油型工艺反应塔上部的精馏段改为催化蒸馏反应段,即异丁烯和甲醇先在混相反应段内预反应,异丁烯转化率可达90%-95%,然后再在催化蒸馏反应段进行深度转化,使异丁烯转化率达到99.5%以上[14]。
(五)生产原理及主要影响因素
1.筒式反应单元
抽余碳四与甲醇按照计算配比进行混合(一般醇烯比为1.02)后,通过强酸性阳离子交换树脂[4][5](S型树脂)催化剂床层,在一定温度和压力下,碳四中异丁烯与甲醇发生加成反应,生成MTBE。
反应如下:
反应为放热反应,△H=-37kJ/mol。
反应选择性高,副反应可生成少量异丁烯低聚物、二甲醚以及少量的叔丁醇等。
反应是在筒式反应器的二段床层进行的,通过预热和二段循环,控制在一定反应温度和压力下,异丁烯的转化率可达到95%以上。
2.催化精馏单元
异丁烯与甲醇反应生成MTBE的反应为可逆反应,反应方程式如下:
根据拉乌尔定律,为使可逆反应平衡向正方向(生成MTBE)进行,其一是增加反应一侧的物料浓度,其二是减少生成物的浓度,其三增加反应压力。
在催化精馏塔内装有催化剂填料包,所以在反应过程中生成MTBE的同时通过精馏不断地将生成的MTBE分离出来,使催化剂床层中的MTBE总是处在低浓度状态,从而使反应朝着生成MTBE的方向进行。
由于甲醇和碳四形成共沸物[6][7],所以,从催化精馏塔塔顶分离出来的未反应碳四馏分含有一定量的甲醇,可以通过水洗萃取分离出来,然后通过蒸馏将甲醇与水分离。
催化精馏工艺由于设备少反应热量回收利用较完全,因此基础建设投资少,且可以节约能源。
3.甲醇回收
利用甲醇与碳四在水中的溶解度不同,可用水作萃取剂将甲醇从碳四中除去。
二、物料说明:
(一)甲醇
表1:
甲醇标准
项目
指标
外观
无色透明液体,无可见杂质
色度(铂-钴)
≤5
密度(20℃)
0.790~0.792g/cm3
沸程
64.0~65.5℃
蒸馏量
≥98mL
温度范围(包括64.6±
0.1)
≤0.8℃
高锰酸钾试验
≥50min
水溶性试验
澄清
水分含量
≤0.10%
游离酸含量(以HCOOH计)
≤15×
10-6
游离碱含量(以NH3计)
≤2×
羟基化合物(以HCOH计)
≤20×
蒸发残渣
≤10×
气味
无特殊异气味
乙醇含量
≤0.01%
1.甲醇结构式:
CH3-OH
2.甲醇分子量:
32
3.甲醇物理性质:
化学名称:
甲醇,别名:
甲基醇、木醇、木精。
分子式:
CH3OH,分子量:
32.04,有类似乙醇气味的无色透明,易挥发性液体。
密度(20℃)0.7913克/毫升。
溶点为-97.8℃,沸点为64.65℃。
折射率(n)1.3290,表面张力为22.6达因/厘米,粘度:
0.5945厘泊。
20℃蒸汽压:
96.3mmHg,闪点(闭口)11.11℃,(开口)16℃。
自燃点:
455℃,燃烧热:
5420卡/克,汽化热:
263卡/克,比热:
20℃时为0.599卡/克·
℃。
在空气中甲醇蒸汽的爆炸极限6.0~36.5%(体积)。
(二)混合碳四[9]
表2:
抽余碳四规格
组分
含量
丙烷、丙烯
≤0.772%
正丁烷、异丁烷
≤2.268%
异丁烯
≤39.71%
1-丁烯
≤36.074%
2-丁烯
≤20.856%
1,3-丁烯
≤0.004%
(三)甲基叔丁基醚
表3:
MTBE产品
优等品
一等品
合格品
甲基叔丁基醚(%)
≤98.7
≥98
≥95
甲醇含量(%)
≤0.18
≤1.0
---
碳四含量(%)
≤0.4
≤0.5
二聚异丁烯含量(%)
1.MTBE结构式:
MTBE分子量:
88
2.物理性质
分子式 CH3OC(CH3)3
CAS号 1634–04-4
性质:
无色、低粘度液体,具有类似萜烯的臭味。
沸点55.3℃。
凝固点-108.6℃。
相对密度0.7407(20/4℃)。
折射率nD(20℃)1.3694。
比热0.51。
闪点(闭杯)-28℃。
燃点460℃。
爆炸极限(空气中)1.65%~8.4%(体积)。
蒸气压(25℃)32.664KPa。
临界压力3.43MPa。
临界温度223.95℃。
粘度(20℃)0.36mPa·
s。
微溶于水,但与许多有机溶剂互溶,与某些极性溶剂如水、甲醇、乙醇可形成共沸混合物。
4.主要用途
甲基叔丁基醚是汽油的一种无毒添加剂,可使汽油的辛烷值提高,也可经二次加工作为生产丁基橡胶、叔丁醇、异丁烯等化工产品的原料。
毒性:
有轻度麻醉作用,微毒。
老鼠进口LD50为3865mg/kg,皮肤吸收LD50>10000mg/kg。
对眼有刺激作用,溅入眼睛后应立即用大量水冲洗15分钟以上,并就医诊治。
操作中应戴防护目镜及橡皮手套。
5.包装储运
贮存容器和密封材料与贮存汽油的要求相同,对容器材质无特殊要求,如铁、锌、铝都可应用,也可使用聚乙烯制的容器。
因本品为可燃液体,装载容器应注明“易燃品”字样,按易燃品规定贮运。
6.化学性质
MTBE可发生分解反应,生成甲醇和异丁烯。
(四)副产物
醚后剩余碳四送至罐区,可作为液化燃料气。
三、工艺流程及说明:
(一)筒式反应单元工艺流程
抽余碳四(通过P101进料)与甲醇(通过P102进料)混合,混合物料中的甲醇与抽余碳四中的异丁烯的摩尔比(醇烯比)为1.02,混合后的物料经静态混合器(X101)充分混合,通过预热器(E101)预热进筒式反应器(R101)顶部。
经一段床层反应后的混合物料,部分去一段循环冷却器(E102)冷却,控制其出口温度为50℃,然后经一段循环泵(P104)送筒式反应器顶部,根据一段物料出口温度控制其循环量,循环比一般为3,转化率控制在45%~60%(根据物料具体情况决定);
经二段床层反应器的混合物料,部分去二段循环冷却器(E103)冷却,控制其出口温度为50℃,然后经二段循环泵(P103)送筒式反应器进料口,循环比一般为1或者1.5,转化率控制在90%以上。
反应器温度控制在30~70℃,压力控制在0.95~1.4Mpa,筒式反应器出口物料靠压差连续进催化精馏塔(T101)。
(二)催化精馏单元工艺流程
从二段排出含异丁烯[10]约4%的物料,经流量和调节阀调节流量控制压力,产品经催化精馏进出料换热器(E104)与精馏塔塔釜的MTBE产品换热,进催化精馏塔(T101)。
物料中沸点较高的MTBE流向塔釜,MTBE产品从塔釜排出。
混合碳四及甲醇上升,经催化精馏包催化精馏,气相物料从塔顶馏出,部分进塔顶回流,部分采出去甲醇回收单元。
甲醇通过催化精馏塔甲醇进料泵(P108)输送,经调节阀控制流量分两部分进入催化精馏部分,与上升的碳四中的异丁烯进行反应,生成MTBE,醇烯比根据生产情况调节。
(三)甲醇回收单元工艺流程
从催化精馏单元来的合格醚后碳四(含甲醇约4%左右,含异丁烯小于0.3%)进入萃取水洗塔(T102)的底部,与从塔上部来的软水在塔内逆向萃取洗涤,料水比为1.5~2.0,水洗其中的甲醇。
塔顶得到去烯碳四,送出装置去罐区储存。
水洗塔操作温度为40℃,压力为0.6MPa。
塔釜含甲醇约8%左右的富醇水,通过压差通过调节阀控制流量经甲醇精制塔[11][13]进出料换热器(E107)升温后,从甲醇回收塔塔中(T103)进塔,塔釜由低压蒸汽直接加热(补充损失的水)精馏,分离甲醇和水,该塔在常压下操作,塔顶温度控制在64℃,塔釜温度控制在107℃,塔顶回收的合格甲醇(含量≥98%),一部分回流由回流泵(P107)打回流(回流比为10),一部分返甲醇原料罐循环使用。
塔釜含甲醇不大于0.3%的水循环使用,多余水排污出装置。
四、工艺流程图及说明:
图1:
筒式反应单元
图2:
催化精馏单元
图3:
水洗萃取及甲醇回收单元
表4:
设备编号及名称
标号
名称
R101
筒式反应器
X101
静态混合器
P101
甲醇进料泵
P102
混合碳四进料泵
P103
二段反应循环泵
P104
一段反应循环泵
P105
催化精馏回流泵
P106
水洗萃取塔软水进料泵
P107
甲醇精制塔塔顶回流泵
P108
催化精馏塔甲醇进料泵
T101
催化精馏塔
T102
水洗萃取塔
T103
甲醇精制塔
E101
进料预热器
E102
一段反应冷却器
E103
二段反应冷却器
E104
催化精馏塔进出料换热器
E105
催化精馏塔塔顶冷却器
E106
催化精馏塔塔釜出料冷却器
E107
甲醇精制塔进出料换热器
E108
甲醇精制塔塔釜出料冷却器
E109
甲醇精制塔塔顶冷却器
V101
催化精馏回流罐
V102
甲醇精制塔回流罐
五、化学反应:
本装置涉及化学反应,如下:
1.甲基叔丁基醚合成反应
2.二甲醚合成反应
3.二聚异丁烯合成反应
4.叔丁醇合成反应
六、物料平衡计算:
筒式反应器物料衡算
1.异丁烯、甲醇合成甲基叔丁基醚的反应方程式:
2.原料由混合碳四(含异丁烯39.71%)和98%的甲醇组成,原料中甲醇与异丁烯的摩尔比为1.02(醇烯比)。
异丁烯在一段床层反应的转化率约为50%,在二段床层反应的转化率约为90%。
3.以混合碳四进料量为4000Kg/h来进行反应器的物料衡算。
由已知可知异丁烯的进料量为:
4000×
39.71%=1588.4Kg/h
由醇烯摩尔比为1.02可知反应器中纯甲醇进料量为:
(1588.4/56)×
1.02×
32=925.81Kg/h
则甲醇进料量为:
925.81/98%=944.70Kg/h
4.一段异丁烯转化率以50%计算,反应转化异丁烯量:
1558.4×
50%=794.2Kg/h
5.以两段床层总反应转化率90%计算,则总反应掉的异丁烯量为:
1588.4×
90%=1429.56Kg/h
剩余异丁烯含量:
(1-90%)=158.84Kg/h
6.由反应方程式可求得生成MTBE的量和所用甲醇量:
WS(MTBE)=(1429.56/56)×
88=2246.45Kg/h
WS(甲醇)=(1429.56/56)×
32=816.89Kg/h
剩余甲醇量:
944.70-816.89=127.81Kg/h
7.反应器出料中各组分所占流量:
MTBE的流量为2246.45Kg/h;
甲醇流量为127.81Kg/h;
异丁烯流量为158.84Kg/h,其它为不参加反应物料。
七、三废治理: