大桥防腐涂装工艺Word格式.docx
《大桥防腐涂装工艺Word格式.docx》由会员分享,可在线阅读,更多相关《大桥防腐涂装工艺Word格式.docx(22页珍藏版)》请在冰豆网上搜索。
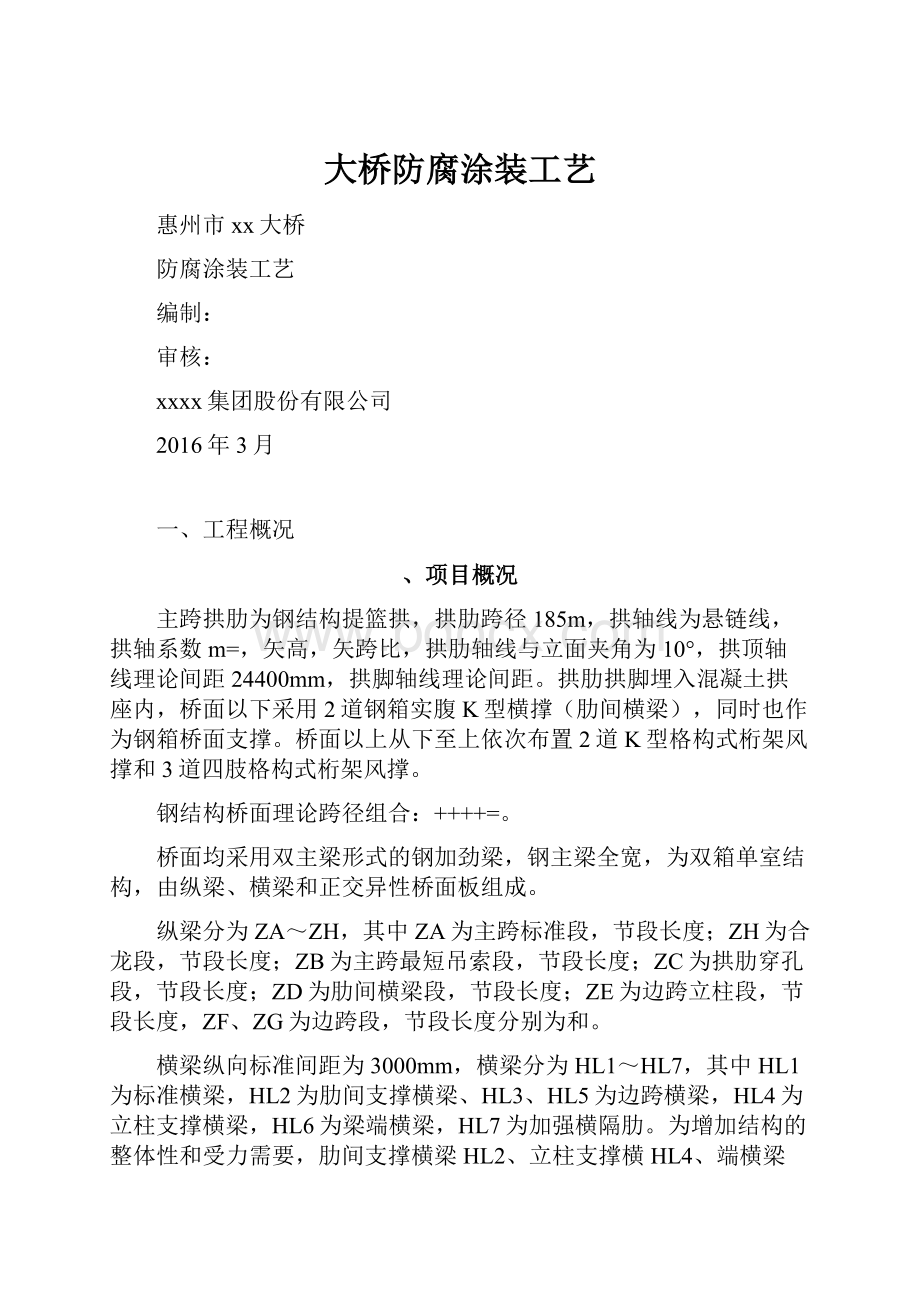
钢主梁外表面
拱肋外表面
(包括箱形杆件
内位于端隔
板以外的面积)
无机硅酸锌车间底漆
1×
25μm
厂内
表面净化处理
无油、干燥
二次表面处理
Sa3级,Rz60-100μm
电弧喷铝
≥150μm
环氧封闭漆1道
无厚度要求
环氧云铁漆中间漆2道
≥2×
60μm
聚氨脂面漆1道
≥1×
40μm
氟碳面漆1道
现场
钢主梁内表面
拱肋钢箱内表面
(不含桁架拱肋内表面)
级,Rz25-60μm
环氧富锌底漆2道
环氧云铁漆中间漆1道
100μm
环氧厚浆漆2道
钢桥面
环氧富锌底漆1道
80μm
U肋封闭内部
主桁箱形杆件内端隔板以内部分喷砂除锈,并涂一道40μm环氧富锌底漆+200μm环氧厚浆漆。
箱梁截面形成后,对端隔板以内部分立即采用封闭式措施,端隔板所有缝隙、孔洞使用弹性密封材料封堵严密,防止水汽进入引起钢板锈蚀。
箱形杆件端隔板外侧未密封部位腻封前,需对密封部位除绣。
密封后,密封表面按与钢结构外表面相同的工艺进行涂装。
高强螺栓摩擦面:
表面处理:
喷砂除锈等级达到级,表面粗糙度Rz60μm~100μm。
高强螺栓连接部分摩擦面涂装采用电弧喷涂铝,涂层厚度为150μm,工厂涂层的抗滑移系数不小于,工地安装时抗滑移系数不小于。
栓接点外露的铝表面与涂料涂层搭接处应涂装特制环氧富锌防锈底漆。
钢梁组装后,栓接点外露的铝涂层用环氧类封孔剂进行封孔,封孔层厚度无要求,涂覆的封孔剂至不被吸收为止。
封孔后应加涂相应的配套涂料。
栓接点螺栓、螺栓头处涂装特制环氧富锌防锈底漆,涂装前螺栓应除油,螺母和垫片应水洗清除皂化膜。
二、钢板预处理
所有钢板表面,应进行两次处理,即钢板预处理和构件正式涂装前处理。
钢板预处理时即可涂刷1道干膜厚度为25μm的无机硅酸锌车间底漆。
涂刷油漆时应注意预留焊道。
钢板进场经辊板机矫平达到要求后,进入生产车间。
三、涂装施工工艺要求
、结构处理
二次涂装前须对构件表面进行检查,并作出标识。
、表面清理
梁段进入喷砂房前,在临时存放点清扫钢结构表面的浮沉和附着物;
清除表面油污、盐分及杂质。
、喷砂
(1)喷砂作业环境要求(见表)
表喷砂作业环境要求
控制要求
检测方法
空气相对湿度
涂装房内<80%
干湿球温度计测量再查表换算,或直接用仪器测量空气湿度
钢板表面温度
≥空气露点温度3℃
钢板温度仪测量
空气露点
露点测试仪或由空气温度和空气相对湿度表求出
(2)喷砂、喷漆压缩空气要求
要求无油、干燥、无杂物,全部采用进口大功率空压机,空气出口压力达以上,以提高喷砂质量和喷砂效率。
(3)喷砂作业工艺参数(见表)
表喷砂工艺参数
压缩空气(无油、无水)
~
喷距
200~300mm
喷角
65~70°
(杜绝90°
喷砂)
(4)喷砂前准备
根据工艺试验选用可以满足规范中清洁度和粗糙度要求的磨料,喷砂施工中适时补充新磨料;
测量施工环境的温度和湿度以及钢板表面温度,如不符合上述施工环境要求,应使用除湿、加温等环境控制。
喷砂开始前开启空压机,同时有质检员检测出气口压缩空气清洁度,并将检验结果记录于钢结构喷砂除锈质量记录表中。
(5)喷砂
在喷砂过程中,对内外表面同时进行喷砂处理,喷砂时严格按喷砂工艺参数进行施工。
在喷砂过程中,每天至少进行一次环境检测,并根据实际情况安排除湿、加温。
磨料使用过程中应定期进行检查,并采用过筛、除灰、补充等处理,以保证磨料正常使用。
如果受潮,则应停止使用,更换新砂或干燥达到要求后再使用。
对于钢梁内表面、钢桥面要求表面达到GB/标准规定的级的要求,钢梁外表面、高强螺栓摩擦表面达到GB/标准规定的级的要求。
(6)吸砂、吸尘
喷砂后吸砂、吸尘对工件进行清洁处理。
由大功率吸砂机、人工辅助清除砂、尘;
并用大功率吸尘机进行真空吸尘,使工件表面彻底清洁。
此后进入箱梁内部时必须穿戴干净的手套、鞋套。
、高强螺栓摩擦面
惠州市xx大桥高强螺栓摩擦面的喷涂采用电弧喷铝。
经喷砂清理后的钢梁应在4小时以内进行摩擦面涂装。
钢梁内表面涂装范围为最边缘螺栓孔中心外延100mm。
涂装完成后,用直尺和记号笔,在涂装面上,边缘螺栓孔中心外延100mm处划出喷铝面和其它油漆面的分界线,并在喷铝完成后用牛皮纸或者塑料膜对分界线处的喷铝面进行保护。
摩擦面涂装工作应在涂装底漆之前完成。
高强螺栓摩擦面电弧喷铝:
在喷砂合格后,测试环境,达到工艺要求,安装好电弧喷涂机,喷涂机应处于完全良好的状态;
压缩空气通过冷却干燥机净化不得有油、水、杂质等。
电弧喷涂施工要求:
A、绕丝
电弧喷涂前首先进行铝丝的盘丝,盘丝要求丝盘和绕丝机的中轴要同心,绕丝机尽量靠近丝盘,绕丝中丝与丝要紧挨着,不要有压、折、弯等情况发生。
B、人员配备
每套电弧喷涂设备配备两名喷涂操作工,操作工穿戴好劳保用品,呼吸供气正常后进入涂装车间操作,其中一名操作喷涂枪进行喷涂,另一名照看喷涂机并配合操作工工作。
C、喷涂施工
喷涂开始时首先先合上喷涂机电源,打开喷涂机供气开关,调剂电流和电压到要求的工艺参数,喷枪对着非喷涂面试喷,喷涂正常后再对需喷涂面进行正式喷涂。
为了驱除潮气和消除应力,在热喷涂前,对工件进行预热,预热温度一般控制在95℃。
预处理和喷涂工序之间,需中间停留时,应对经预处理的有效表面采用牛皮纸、塑料膜等进行保护。
、喷漆
表喷漆作业环境及检测方法
项目
备注
环境温度
氟碳面漆温度不得低于5℃,环氧富锌底漆温度不得低于10℃,其余涂装温度环境温度在5℃~38℃之间
温度计测量
当与油漆说明书不符合时,应执行油漆相应产品施工说明书
相对湿度仪、干湿度摇表
钢板温度仪、露点测试仪
涂装施工前,制造厂和油漆供应商应进行专项涂装工艺试验,涂装工艺试验报监理工程师确认,工艺试验合格后方可进行正式涂装施工。
试板按钢梁外表面涂装体系进行涂装施工和检查,试验方案及检验方法见附件一。
1)应按设计规定涂层配套进行喷涂,涂装材料、工艺及性能要求等亦应符合设计要求。
施工方案必须符合油漆厂商提供的使用说明所规定的要求。
2)涂装前应仔细确认涂料的种类、名称及施工位置。
3)对双组份涂料要明确混合比例,并搅拌均匀、熟化后使用。
混合后如超过使用期,则不得使用。
4)首次进行油漆喷涂工作时,应该在油漆供应商技术代表的指导下进行,以熟悉所用油漆的施工性能。
5)涂料应按涂装方法(喷涂或刷涂)、工作温度、湿度,用规定的稀释剂。
如变动稀释剂的品种和用量,必须经监理工程师的批准,否则不得使用。
6)按涂料供应商提供的资料,根据施工的实际温度、湿度等环境因素,确定喷涂的时间间隔,并严格执行;
正确记录施工环境条件、油漆品种、数量、涂装部位等参数。
7)涂装前应对构件自由边进行倒角,倒弧半径为r=。
8)喷漆施工前须对构件表面或前涂层表面进行清理,除去污物,修理缺陷。
经喷砂清理后的钢梁应在12小时以内进行涂装。
第一道漆未实干前不得涂第二道油漆,两道底漆的间隔时间应该在24h-168h内完成,若超过168小时,必须将第一道油漆用细砂纸打磨成细微毛状方可施工。
9)对于钢梁结构复杂或不易喷涂到的部位应先用刷子进行预涂,然后再进行大面积的油漆喷涂工作。
10)应留出工地焊缝处不涂油漆,以免影响焊接质量。
11)若出现油漆起泡严重、色差较大,应立即停止施工。
并即使反应到相关部门,由相关部门会同油漆供应商一并解决所发生的问题。
12)喷枪所用压缩空气管路必须装有油水分离器,在喷砂除锈或喷涂油漆时,每次都应将空气压机里油水分离器中的水排干净。
13)油漆喷涂工作和喷砂除锈同时进行时,油漆喷涂杆件应远离砂房,避免钢梁表面油漆被灰尘污染。
14)刚做好油漆的钢梁应避免雨水冲刷,特别是面漆,应及时将钢梁转移到可以避雨的地方。
15)当环境温度超过38℃或钢梁表面温度过高时,容易发生干喷现象,此时应将钢梁移至阴凉处进行涂装作业。
16)构件在运输和安装过程中。
对损坏的油漆应进行补涂,对大面积损伤的,必须重新砂磨按层修补。
局部小面积损伤者用手工打磨,进行修补。
17)喷涂时压缩空气的压强保证在/cm2。
、钢梁的标号
涂装后应在规定的位置,涂刷钢梁标记,并核对钢印号。
、杆件的密封
箱形杆件端隔板外侧未密封使用手工焊条进行焊堵。
密封施工时,环境温度应在5~35℃之间,相对湿度不大于80%,下雨不能施工,表面有水不能施工。
四、厂内及工地涂装施工工艺
、厂内涂装
(1)表面清理
钢梁拼焊完成并检查合格后,进行表面清理,彻底清除表面的油污、杂质。
(2)喷砂除锈
钢梁整体喷砂除锈,严格按喷砂工艺参数进行施工,在喷砂过程中,经常进行环境检测,并根据实际情况安排除湿、加温。
使外表面及摩擦面钢板清洁度等级为Sa3级,粗糙度为60-100μm;
内表面和钢桥面钢板清洁度等级为级,粗糙度为25-60μm。
(3)吸砂吸尘
用大功率吸砂机进行吸砂吸尘处理,使工件表面彻底清洁。
(4)喷铝
在合适喷涂条件下,对喷砂报检合格后的外表面及栓接面严格按工艺参数进行电弧喷铝,要求涂层均匀,不得漏喷,喷涂养护后其摩擦系数及现场施工时摩擦系数均应满足大于相关规范要求。
厚度为150μm。
喷铝结束后采用白铁皮或牛皮纸进行防护,防止涂料污染。
(5)环氧富锌底漆的涂装
对钢主梁、箱型拱肋内表面摩擦面进行保护,预涂、喷涂2道后,要求涂层均匀,不得漏喷,喷后防护,喷涂施工中随时用湿膜卡检测湿膜厚度,使干膜厚度达到80μm。
对钢桥面进行1道环氧富锌底漆的喷涂,要求涂层均匀,不得漏喷,喷涂施工中随时用湿膜卡检测湿膜厚度,使干膜厚度达到80μm。
对桁架拱肋内表面进行1道环氧富锌底漆的喷涂,要求涂层均匀,不得漏喷,喷涂施工中随时用湿膜卡检测湿膜厚度,使干膜厚度达到40μm。
(6)环氧封闭漆的涂装
对外表面喷铝面进行检查清理,检测膜厚。
合格后进行1道环氧封闭漆的喷涂,要求涂层均匀。
(7)环氧云铁中间漆的涂装
对外表面环氧封闭漆层进行检查清理后进行2道环氧云铁中间漆的预涂、喷涂,要求涂层均匀,喷涂施工中随时使用湿膜卡检测湿膜厚度,使干膜厚度达到120μm。
累计膜厚达到270μm。
对钢主梁、箱型拱肋内表面环氧富锌底漆层进行检查清理,检测膜厚。
合格后进行1道环氧云铁中间漆的喷涂,要求涂层均匀,喷涂施工中随时使用湿膜卡检测湿膜厚度,使干膜厚度达到100μm。
累计膜厚达到180μm。
(8)环氧厚浆漆的涂装
对钢主梁、箱型拱肋内表面环氧云铁中间漆层进行检查清理,检测膜厚。
合格后进行2道环氧厚浆漆的喷涂,要求涂层均匀,喷涂施工中随时使用湿膜卡检测湿膜厚度,使干膜厚度达到120μm。
累计膜厚达到300μm。
对桁架拱肋内表面环氧富锌底漆层进行检查清理,检测膜厚。
合格后进行环氧厚浆漆的喷涂,要求涂层均匀,喷涂施工中随时使用湿膜卡检测湿膜厚度,使干膜厚度达到200μm。
累计膜厚达到240μm。
(9)聚氨酯面漆的涂装
对外表面环氧云铁中间漆层进行检查清理,检测膜厚。
合格后进行1道聚氨酯面漆的喷涂,要求喷涂均匀,喷涂施工中随时用湿膜卡检测湿膜厚度,使干膜厚度达到40μm。
累计膜厚达到310μm。
、工地涂装
(1)所有构件在出厂前均经过抛丸除锈,并涂了一定道数的油漆,因此对已涂油漆的部位只需清理灰尘、泥土、油污等。
(2)对现场拼装焊缝处,须用砂轮打磨焊缝区域,清理焊渣、焊瘤、毛刺、焊接飞溅物及污垢等。
(3)在现场拼装焊缝处,如在涂底漆前已返锈,需重新除锈,除锈采用电动钢丝刷处理达到St3级,经除锈后的钢结构表面,应用毛刷等工具清扫,或用干净的压缩空气吹净锈尘和残磨料,然后方可进行下道工序。
(4)构件在装车、运输、卸车、堆放时,对构件涂层造成局部损伤,引起局部返锈的,需要重新除锈,除锈采用电动钢丝刷理达到St3级,同样也需经清理后,才可涂底漆、中间漆、面漆。
(5)按照油漆说明书和油漆技术服务人员的现场指导,根据施工时的实际温度、湿度等环境因素及涂层的实际干燥(或固化)情况,确定下道油漆的重涂间隔时间,并严格执行。
如遇下雨等不适喷涂的环境,禁止继续喷涂。
(6)针对施工现场特点,高处作业人员必须备戴安全带,穿防滑鞋。
风速如超过3m/s时则停止施工。
此部分油污、杂质较多,清理过程中要认真仔细,确保表面无油污、杂质。
(2)封孔
栓接点外露的铝涂层用环氧类封孔剂进行封孔,封孔层厚度无要求,涂覆的封孔剂至不被吸收为止。
(3)涂装
在合适的环境条件下按所在部位补涂各涂层。
外表面施工至聚氨酯面漆,氟碳面漆的涂装和外表面最后一道面漆的涂装同时进行。
清除表面存在的油污、杂质。
(2)表面除锈
用打磨机对清理干净的外表面打磨,达到级。
在合适环境条件下按焊缝所在部位补涂各涂层。
(1)损伤面修复
对未损伤至底材的区域:
去油后对周边涂层实施保护,对损坏区域采用打磨机打磨;
周围涂层打磨成坡度,磨出不同漆层的层面,用刷涂方法补涂相应涂层的涂料。
对损伤至底材的部位:
去油后打磨除锈达到级,周围涂层打磨成坡度,磨出不同漆层的层面,周边涂装层进行保护,进行外表面相应涂层的涂料涂装。
(2)外表面最后一道面漆的涂装
为保证大桥建成后整体外观色彩一致、漂亮美观,在整桥安装完成,焊缝防腐处理结束后对整桥涂装最后一道氟碳面漆。
A、全桥修补涂装结束后,对全桥外表面涂层进行清理、活化处理。
用毛刷等工具清除钢结构表面的污物残渣等,然后用稀释剂擦洗掉钢结构表面的油污,用砂纸打毛油漆表面,再用抹布擦净表面灰尘。
B、面漆涂装
对钢结构进行拉毛和活化处理后,尽快涂装氟碳面漆,先对焊缝、边角等小部位不平处用毛刷先预涂面漆,再用高压无气喷涂机整体喷涂面漆。
a、根据工程量、天气状况适时适量配制涂料,严格按配比进行调配,并根据气温等情况加入适量稀释剂,均匀搅拌后进行施工。
b、对边角处预喷涂面漆,预涂结束后进行大面积的喷涂,喷涂过程中用湿膜卡随时检测湿膜厚度,使干膜厚度达到要求,外观颜色均匀,美观大方。
c、钢结构外表面整体喷涂氟碳面漆一道,使干膜厚度达到40μm。
五、涂装质量要求与检测
、涂料的质量控制
每个涂装材料品种按不同生产批号各抽取一个样品送国家检验机构进行检验。
检验结果应满足《钢结构防护涂装通用技术条件》(GB/T28699-2012)附录要求,检验合格后方能进行涂装工作;
若检验结果中有某项指标存在争议时,允许在该批涂装材料中再随机抽取一个样品,重新进行检验。
环氧富锌底漆应满足GB/T28699-2012附录D的要求,见附录二。
环氧封闭漆、环氧云铁中间漆、环氧厚浆漆应满足GB/T28699-2012附录E的要求,见附录三、四、五。
聚氨酯面漆、氟碳面漆应满足GB/T28699-2012附录F的要求,见附件六、七。
环氧富锌底漆500小时耐盐雾试验,环氧云铁中间漆贮存稳定性和聚氨酯面漆、氟碳面漆500小时耐人工加速老化性能试验为涂料供应商保证项目,涂料供应商须提供权威方的试验报告。
环氧富锌底漆性能指标:
流出时间、不挥发物含量、黏度、干燥时间、弯曲性能、耐冲击性、附着力、适用期、施工性能。
环氧封闭漆性能指标:
不挥发物含量、黏度、干燥时间、弯曲性能、耐冲击性、附着力、适用期、施工性能。
环氧云铁中间漆性能指标:
流出时间、不挥发物含量、干燥时间、弯曲性、耐冲击性、附着力、适用期、施工性能。
环氧厚浆漆性能指标:
流出时间、不挥发物含量、干燥时间、弯曲性、耐冲击性、附着力、耐磨性、适用期、施工性能。
聚氨酯面漆性能指标:
流出时间、不挥发物含量、黏度、细度、干燥时间、弯曲性、耐冲击性、附着力、硬度、耐碱性、耐酸性、耐磨性、适用期、施工性能。
氟碳面漆性能指标:
氟含量、流出时间、不挥发物含量、黏度、细度、干燥时间、弯曲性、耐冲击性、附着力、硬度、耐碱性、耐酸性、耐磨性、适用期、施工性能。
(1)涂料的采购
所有构成防腐体系的油漆都应满足招标文件及设计要求。
(2)涂料的封装和运输
所有涂料应装在密闭容器内,容器的大小应方便运输。
每个容器应在侧面贴说明书,表明用途(例如是底漆、中间漆还是面漆)、颜色、批号、生产日期和生产厂。
(3)涂料的验收入库
仓库保管员应对进库前的涂料验证其合格证、质保书,检查是否与相应合格样品相同,相同时方可入库,否则拒绝入库,并退回供方更换。
(4)涂料应存放在专用库房内,库房应防止漏水,有安全、灭火设施。
除非另有说明,超过贮存期的涂料应予废弃,不得用于永久性工程。
、涂装质量控制与检测
(1)漆膜的外观要求平整、均匀、无气泡、裂纹,无严重流挂、脱落、漏涂等缺陷,面漆颜色与比色卡相一致。
(2)涂膜厚度按设计规定,采用《色漆和清漆漆膜厚度的测定》(GB/进行测量。
(3)漆膜附着力的检验采用《色漆和清漆漆膜拉开法附着力试验》(GB/T5210-2006)进行拉开法试验。
(4)钢梁构件外部涂装体系干膜最小总厚度和每一涂层干膜平均厚度不得小于设计要求厚度。
(5)钢梁出厂后,高强度螺栓连接面(喷铝)涂层的保质期为6个月。
(6)涂装质量检验符合下表:
表各工序质量检验要求表
工序
检测项目
检测手段
检验要求
检测数量
标准
除油
油污、杂质
目测
清除可见油污、杂质
全面
喷砂
清洁度
图谱对照
或Sa3级要求
GB/
粗糙度
表面粗糙度比较样板或粗糙度测量仪
Rz=25~60μm或Rz=60~100μm
每10m2内至少均匀的选择3个测点,取平均值
涂层
铝涂层及漆膜厚度
用磁性测厚仪
达到规定漆膜厚度
每10m2至少应有三个基准面,基准面为10cm2平面,基准面内取3处测点取平均值,每基准面相距50cm
GB/T28699-2012
GB/T4956-2003
附着力
油漆涂层
拉开法
≥
抽检
GB/T5210-2006
铝涂层
外观
漆膜颜色与色卡一致,漆膜无流挂、针孔、气泡、裂纹等缺陷;
铝涂层均匀、致密,无未熔化大颗粒,无漏喷现象
在每种涂层干后全面检查
注:
漆膜厚度测量值必须满足必须90%以上的测值达到规定的厚度要求,另10%厚度不达标的测值其厚度不得低于规定厚度的90%。
六、高强螺栓连接表面抗滑移系数实验
1)钢梁出厂时栓接表面抗滑移系数试验值应不小于,安装前不小于,抗滑移系数试验应符合《铁路钢桥栓接面抗滑移系数试验方法》(TB2137-1990)的规定。
试验结果报监理工程师确认。
2)抗滑移系数试件与钢梁同材质、同工艺、同批制造,随钢梁批次发运及存放。
3)根据设计图规定:
抗滑移系数试件以钢拱肋和钢主梁制作批为单位,钢拱肋检验两批,钢主梁检验三批。
七、环境及安全
1)进场油漆应该按品种、批号放置在避光位置,并远离明火。
2)配置油漆需要搅拌时,应采用气动搅拌,杜绝采用电力搅拌。
3)各工序工作人员必须配备相应的工作装备,如:
手套、防尘面罩、口罩等,禁止不穿戴装备进行操作,以免灰尘、有毒气体对工作人员造成伤害。
4)喷砂除锈时要关闭砂房大门,并开启除尘设备,以减少灰尘对周边环境的污染。
5)使用过的废油漆桶、过期的油漆都应集中处理,存放到指定位置,禁止将稀料、油漆倒入下水道或搁置在饮水源旁。
6)禁止工作人员在油漆施工场地吸烟,以免引起火灾或爆炸。
附件一涂装试验方案及检验方法
试验目的:
检验涂装体系的配套性及涂层的附着力。
试验器材:
250mm×
300mm钢板一块、磁性测厚仪、粗糙度仪、拉力试验机、无气喷枪、涂装体系中规定的油漆。
试验人员:
监理工程师、油漆供应商技术代表、制造单位相关人员、油漆施工队代表。
试验步骤:
1)将准备好的钢板的一个面用专用稀释剂清洗,除去表面的油污后进行喷砂处理,使钢板表面达到GB/标准规定的Sa3级的要求。
2)喷砂完毕后,用粗糙度仪测量钢板表面的粗糙度,并做记录,检验参照标准GB/。
3)喷制试板:
采用电弧喷涂机在钢板表面喷涂铝层,完毕后存放在干净处。
4)按比例配制环氧封闭漆,并加适量稀释剂,使所配油漆达到合适的喷涂黏度。
配制油漆时应注意油漆的活化期、使用期及使用量。
5)在试板长度方向两端分别标注“上”“下”字样,并从距试板上端50mm处喷制环氧封闭漆漆膜,不做油漆的地方采用胶带保护。
6)待漆膜实干后,重复步骤4配制环氧云铁中间漆,并从距试板上端100mm处喷制环氧云铁中间漆漆膜,不做油漆的地方采用胶带保护。
7)待漆万实干后,重复步骤4配制聚氨酯面漆,并从距试板上端150mm的地方开始喷制聚氨酯面漆漆膜,不做油漆的地方采用胶带保护。
8)待漆万实干后,重复步骤4配制氟碳面漆,并从距试板上端200mm的地方开始喷制氟碳面漆漆膜,不做油漆的地方采用胶带保护。
9)漆膜制备完毕后,将所制试板放在恒温、干净的地方保持一个星期,以便漆膜都能彻底干燥。
10)漆膜彻底