电风扇旋钮注射模设计说明书Word格式文档下载.docx
《电风扇旋钮注射模设计说明书Word格式文档下载.docx》由会员分享,可在线阅读,更多相关《电风扇旋钮注射模设计说明书Word格式文档下载.docx(31页珍藏版)》请在冰豆网上搜索。
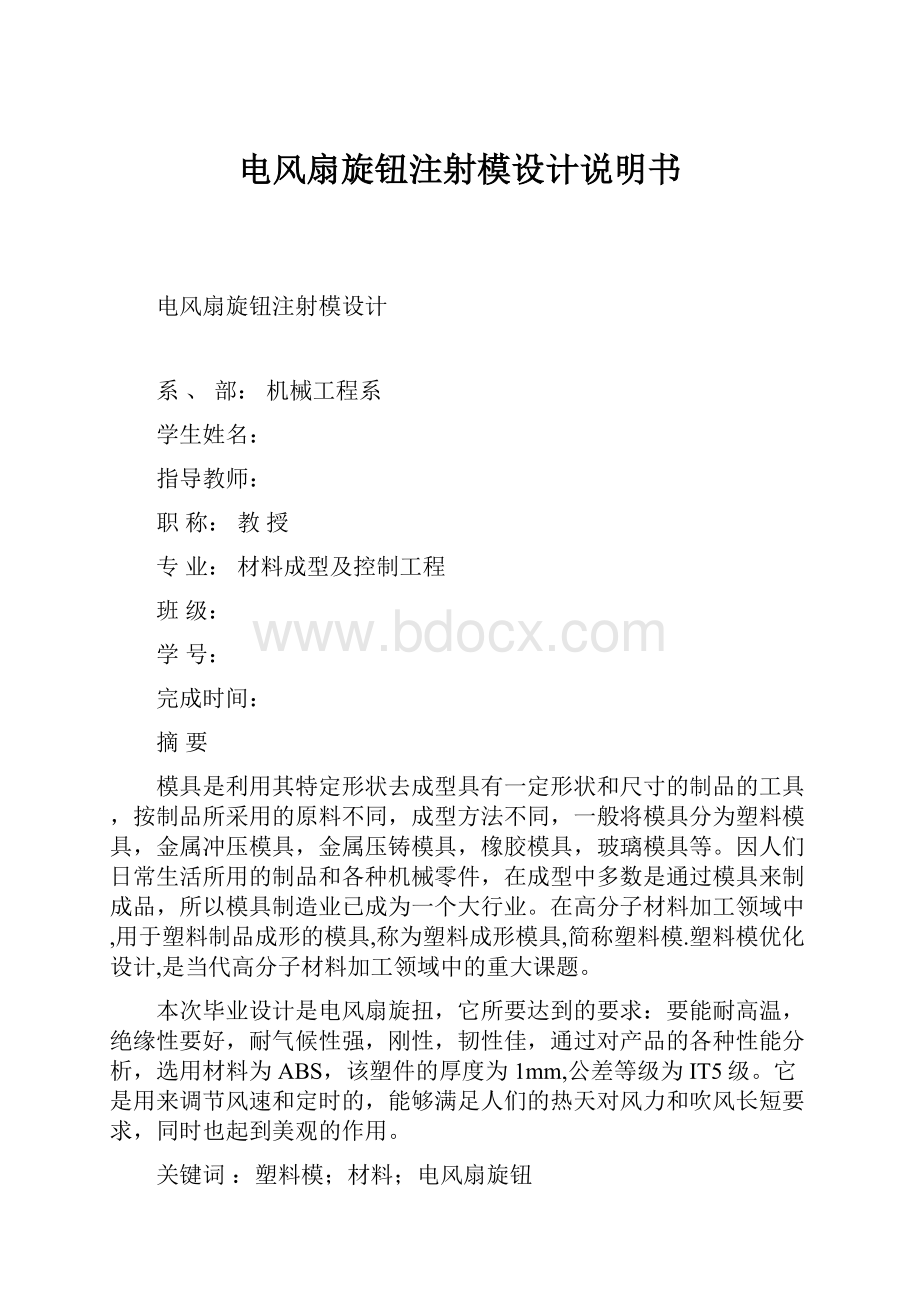
光阴似箭,在校的大学四年的学习一晃而过,为具体的检验这四年来的学习效果,综合检测理论在实际应用中的能力,除了平时的考试、实验测试外,更重要的是理论联系实际,即此次设计的课题为电风扇旋钮塑料模具设计。
本次毕业设计课题来源于生活,应用广泛,模具结构较为简单,对模具工作人员提高理论联系实际的能力是一个很好的练习。
它能加强对塑料模具成型原理的理解,同时锻炼对塑料成型模具的设计和制造能力。
本次设计以电风扇旋钮注射模具为主线,综合了成型工艺分析,模具结构设计,最后到模具零件的加工方法,模具总的装配等一系列模具生产的所有过程。
能很好的学习致用的效果。
在设计该模具的同时总结了以往模具设计的一般方法、步骤,模具设计中常用的公式、数据、模具结构及零部件。
把以前学过的基础课程融汇到综合应用本次设计当中来,所谓学以致用。
在设计中除使用传统方法外,同时引用了CAD、Pro/E等技术,使用Office软件,力求达到减小劳动强度,提高工作效率的目的。
由于本人才疏学浅,知识根底不牢,缺少经验,在模具结构设计计算和编写设计说明书的过程中,得到刘先兰老师以及其他机械、模具基础课老师的细心指导,同时也得到同学的热情帮助和指点,在此谨以致谢。
敬请各位老师和同学批评指正,以促我在以后的工作中减少类似的错误,做出成绩,以报恩师的淳淳教诲和母校的培养。
设计说明书中详细分析了设计中的一些必要计算,并附图分析,所有数据经过核算,该查表的数据在《机械设计手册》、《塑料模设计手册》等丛书中查得。
1塑件的工艺性分析
图1塑件图
注塑模按结构分为单分型、双分型和多分型面,此塑件是采用侧浇口工件较简单,因此采用单分型面的模具,又因为该工件属于薄壁塑件,当采用推杆,会把塑件容易顶坏。
所以该工件采用推件板推出,容易保证塑件的质量。
注塑模包括:
成型零部件、合模导向机构、浇注系统、侧向分型与抽芯机构、推出机构、加热和冷却系统、排气系统、支承零部件。
只有处理好各个环节的制约关系,才能设计出一副较好的模具出来,一副模具设计出来,把它装在注塑机上,还要通过校核,才能投入生产。
因此注塑模与注塑机的关系也是至关重要。
塑件首先选用材料为ABS塑料,它是属于热塑性塑料,该产品是通过注塑成型的。
ABS的主要技术指标:
密度g/cm³
1.02—1.16
弹性模量MPa1.8×
10³
比体积dm³
/g0.86—0.98
弯曲强度MPa80
吸水率%(24h)0.2—0.4
硬度HB9.7R121
收缩率%0.4—0.7
体积电阻率Ωcm6.9e+16
熔点°
C130—160
热变形温度°
C0.46MPa90—108
0.185MPa85—103
冲击强度kJ/m²
无缺口49
缺口6.5
抗拉屈服强度MPa50e
ABS成型塑件的主要缺陷及其消除措施:
成型前要干燥,容易产生熔接痕,浇口处不好看。
以上这些缺陷均可以采取以下措施消除:
(1)分流道及浇口截面要加大,
(2)注意浇口位置,
(3)防止熔接纹,
(4)在成型时的脱模斜度
2°
,
(5)收缩率
0.5%。
ABS塑料的原理是将颗粒或粉状塑料从注塑机的料中送进加热器中,经加热熔化,在受压的情况下,把它注到成型的型腔中,再冷却成型。
注塑成型它的周期短,能成型复杂的、尺寸精确的制件。
它的成型工艺过程包括如下:
成型前的准备,注塑过程,塑件后处理。
由于ABS料它是属于易湿的塑料,所以在加工前要把它进行充分的干燥。
注塑过程它是一个比较关键的进程,各个步骤都要控制好,这对塑件的质量和形状起着至关重要的作用。
注塑成型的核心问题是:
就是采用措施得到良好的塑料熔体,并把它注塑到型腔中去,在控温下,使塑件达到所求的质量。
温度、注塑压力、时间是其关键的工艺参数。
2分型面位置分析和确定
打开模具取出塑件或浇注系统凝料的可分离的接触表面,称之为分型面。
分型面的设计它受到塑件的形状、壁厚、和外观、尺寸精度、及模具型腔的数目等诸多因素的影响。
2.1型腔数目的确定
根据塑件的精度确定型腔的数目。
根据经验每增加一个型腔,塑件的精度就要下降4%左右,该塑件它要求它的精度比较高,根据《塑料模具技术手册》,得到经验公式:
n=(x-δL/100)÷
[(δL/100)x(4/100)]…………
(1)
=2500x/δL-24
=(2500x0.013)/(0.05x25)-24
=26-24
=2
所以确定模具的型腔为2。
其中x是塑件尺寸的公差,δ%是料的收缩率,ABS料取0.05%,L是塑件的基本尺寸。
2.2型腔的布局
由于型腔的排布与浇注系统布置密切相关,因而型腔的排布在设计中加以综合考虑。
型腔的排布应使每个型腔都通过浇注系统从压力中等分所得的足够压力,以保证塑件熔体同时均匀地充满每个型腔。
该模具采用的平衡式,其结构如装配图所示。
2.3分型面设计
该模具采用的是单分型面的模具,其分型分面的设计原则满足以下几项原则:
(1)塑件的脱模;
(2)保证的塑件的质量。
该模具采用在最大圆周上,保证了塑件的外观;
(3)便于模具加工,该模具采用在圆周上分型,模具的型腔容易在电火花上加上,型芯也易于加工;
(4)对成型面积的影响;
(5)对排气效果的影响;
该模具的分型面的设计可以见装配图,它基本符合上述要求。
3注射机的选择及工艺参数校核
3.1注塑机的选择
根据型腔的数量的确定和校核,此副模具选用的是SZ-320/1250的注射机。
其中技术规格见《塑料模具设计手册》中的235页。
这是由上海第一塑料机械厂生产的。
现详述如下:
理论注射量为335cm3,
螺杆直径D=48mm,
注射压力145Mpa,
注射速率v=140g/s,
塑化能力19g/s,
螺杆转速v=10~200r/min,
锁模力F=1250KN,
拉杆内间距d=415x415mm,
移模行程s=360mm,
最大模具厚度d=550mm,
最不模具厚度d=150mm,
锁模形式为双曲肘,
模具定位孔直径为D=φ160mm,
喷嘴球半径d=SR15。
3.2工艺参数的校核
由注射机料筒塑化速率确定型腔数量n得:
n=2≤(KMt/3600-m2)/m1………
(2)≤(0.8x19x3600x6/3600-40)/15
≤3.4
其中n是型腔数目,K是注射机的最大注射量的利用系数,取0.8,M是注射机的额定塑化量,t是成型周期,此时取6s(因为在上面算了塑件的冷却时间为4s,它占整个周期的2/3.)m2是浇注系统的塑料的质量体积。
型腔数为2符各要求。
注射量的校核:
由公式得:
nm1+m2≤80%m………(3)
2x15+40≤80%x335/1.02
70≤262
其中:
m是注射机充许的最大注射量,1.02是ABS的密度。
所以能保证注射模内所需熔体总量在注射机的最大注射范围内。
塑件在分型面上的投影面积与锁模力的校核;
经算得,塑件在分型面的投影面积和浇注系统在模具分型面的投影面积之和最多不超过5500mm2,在此就作5500mm2。
由锁模力的校核公式得:
(nA1+A2)P<
F............(4)
5500x10-6x116x106<
1250KN
638KN<
A1是塑件在分型面上的投影面积,A2是浇注系统在分型面上的投影面积。
P是塑料熔体对型腔的成型压力,其大小一般为注射机的80%左右。
由上式可得它也是符合要求。
注射压力的校核:
ABS料它是综合力学性较好的塑料,粘度不是很高的,精度要求也不是高精度的,根据《塑料模具技术手册》中的经验,它所需的压力一般选70~100Mpa即可。
经查得此注射机的注射压力为145Mpa,所以由此可得它的压力也是足够的。
喷嘴尺寸的查表得它的球面半径为SR15,符合R2=SR+0.5,这样有利于主流道的凝料脱出。
模具厚度的校核:
Hmin<
H<
Hmax
150mm<
269mm<
550mm
由此也符合要求。
开模行程的校核:
此副模具采用是单分型面的注射模具,且采用的是推件板的推出机构,因此它的开模行程为:
Smax≥S=25+10…………(5)
360mm≥35mm
所以也是符合的,25是塑件的高度。
由上述可各个数据可以得到,选择SZ-320/1250的注射机是合适的。
选择好的注射机是得良好的塑件的重要的因素之一,因此这个步骤是必不可少的。
4成型零件的设计
成型零件是决定塑件的几何尺寸和形状的关键。
成型零件因直接与高温、高压的塑料流接触,因此成型零件要求具有较高的强度、刚度和耐磨性能。
成型零部件,它包括:
型腔、型芯、成型杆、和成型环等。
该产品是IT5级精度制造的,产品外表面要求比较光滑,因此要求成型零件的抛光性能要好,表面应该光滑美观。
表面粗糙度要求Ra0.4以下。
型腔的材料选40Cr。
淬火处理,使其达到硬度40HRC以上。
4.1型腔的结构设计
由于该塑件结构比较简单,但要求其精度也要较高,要求其塑件不允许产生拼接线痕迹,经过仔细的参考,该型腔采用整体式较为合理。
其结构和尺寸如下图所示:
图2型腔结构图
查阅资料可得塑件的理想的外壁圆角半径为塑件的壁厚的1.5倍。
即R=1.5Xt,即R=1.5mm,该型腔的加工,先下料一块为400X400X50mm的40Cr,然后在磨床上进行磨削,使其达到应有的光洁度,然后热处理,使其达到硬度达到40HRC以上。
成型的型腔可以在电火花机上加工得到所要的尺寸和精度,最后通过精磨和抛光,得到所要的型腔。
4.2型腔的工作尺寸计算
所谓工作尺寸就是指成型零件上直接用以成形塑件部位的尺寸。
它主要包括型腔的径向尺寸、型腔的深度、中心距等尺寸。
它受到塑件的尺寸精度的影响。
型腔的计算公式如下:
型腔的径向尺寸计算(LM)0δz=[(1+Scp)Ls-3/4△]0δz…………(6)
=[(1+0.55/100)x52-3/4x0.013]0δz
=[52.286-0.00975]0δz
=[52.2765]0δz。
(L)0δz=[(1+Scp)Ls-3/4△]0δz…………(7)
=[(1+0.55/100)x15-0.75x0.008]0δz
=[15.0765]0δz
其中LM是型腔的径向尺寸,Scp是塑料的平均收缩率,△是塑件的公差值。
查表得ABS塑料的最小收缩率为0.3%,最大的收缩率为0.8%,由公式得Scp=(0.3%+0.8%)/2得Scp为0.55,至于塑件的精度,在此到△的系数为0.75,当塑件的精度不同时会有变化。
型腔的深度尺寸计算:
(HM)0δz=[(1+Scp)Hs-2/3△]0δz…………(8)
=[(1+0.55/100)x26-0.009x2/3]0δz
=[26.143-0.006]0δz
=[26.136]0δz
其中HM为型腔的深度尺寸,△的系数取2/3。
塑件的字体是通过在型腔上做相反的字,它的深度为0.3mm,它是通过金雕工艺,把它雕到上面的,因此在这里不详细说明是怎么样生产出来的。
4.3型芯的结构设计
型芯是成型塑件的内表面的的零件。
此塑件它有两个小孔,它是用小型芯来成型,主型是用来成型塑件的内壁,塑件的内表面精度要求要稍微低一些,因此型芯的加工可以稍稍粗糙点。
该芯采用整体式,它结构牢固,它固定在动模固定板上。
其形状和尺寸如下图:
所示:
图3型芯
其工件角度都是通过核算而得到的。
型芯选40Cr,淬火处理,使其硬度达到40HRC以上,以保证其硬度,不使它在加工时,变弯、变软。
它的加工过程是,先取一段φ60x40的一块圆棒料,开始在车床上车削,然后进行热处理,再进行电火花加工,使其达到所要求的形状和尺寸,最后进行磨和抛光。
型芯的尺寸计算
型芯的径向尺寸:
(LM)-δz0=[(1+Scp)Ls+3/4△]-δz0………(9)
=[(1+0.55)x50+0.75x0.011]-δz0
=[50.2835]-δz0
(LM)-δz0=[(1+Scp)Ls+3/4△]-δz0………(10)
=[(1+0.55/100)x13+0.75x0.008)]-δz0
=[13.0775]-δz0
其上面字母所表示的意义和型芯的字母是一样的。
型芯的高度尺寸计算如下:
(HM)=[(1+Scp)Hs+2/3△]-δz0…………(11)
=[(1+0.55/100)25+2/3x0.006]-δz0
=[25.1425]-δz0
塑件中心距的尺寸计算:
(LM)-δz0=(1+Scp)Ls±
δ/2…………(12)
=(1+0.55/100)x26±
δ/2
塑件理想的内角圆半径应为塑件壁厚的1/3以上。
所以取内角圆半径为0.5mm.
型腔由于受到熔体的高压作用,应具有足够的强度和刚度。
如果型腔侧壁和厚度过下,则会引起溢料和出现飞边,这样就降低了塑件的精度,严重时还会影响脱模。
因此还要计算侧壁和底板的厚度。
模具型腔的壁厚的计算,应以最大的压力为准。
此塑件是属于小尺寸塑件,为了防止其弹性变形,其内应力超过许用应力,强度不足是主要原因,因此应以强度计算。
这个零件可以近似看作圆形件。
型腔侧壁的计算如下:
S=r{{([σ]/([σ]-2P))}1/2}…………(13)
S是侧壁厚度。
P是型腔压力,[σ]模具材料的许用应力。
r型腔半径。
经算得,图中型腔的壁厚已经足够。
型腔的厚度计算公式如下:
h=1.1rx(p/[σ])1/2…………(14)
h型腔的高度,r型腔的半径。
经算得15mm已经满足要求了。
型腔动模支承板的厚度的计算。
因为该型腔是采用整体式型腔,动模垫块厚度的选择显得较为自由。
S=3.14xR2…………(15)
=3.14x26x26
=21.22cm2
本副模具厚度可选为25mm.
5模架的设计
模架技术的标准,是指在模具设计和制造中所应遵循的技术规范、基准、和准则。
它具有以下要求:
(1)减少了模具设计者的重复性工作;
(2)改变了模具制造行业“大而稀,小而全”的生产局面,转为专业生产;
(3)模具的标准化是采用CAD/CAM技术的先决条件;
(4)有利于模具技术的国际交流和模具出口。
该模具的模架采用A3型,它适应于单分型面的模具的推件板的推出机构,且可以用潜伏式浇口。
其图可见其装配图。
根据《塑料模具技术手册》表9-16的中小型模架的尺寸组合系列:
选A3型中的编号为17号的它的各个参数如下:
采用A3-355459-17-Z1GB/T12556-90:
模宽B=355mm,模长L=459mm;
模板A=40mm,材料45钢;
模板B=25mm,材料45钢;
垫块C=100mm,材料45钢;
推件板的厚度为20mm,T8A,前面已经说明了,型芯固定板的厚度为20mm,采用45钢。
动模座板的高度为32mm,它的材料为45钢,定模座板的高度为32mm,它的材料也为45钢。
模架的总高度计算得:
H=32+32+20+20+A+B+C…………(16)
=32+32+20+20+40+25+100
=269mm
经校核模具的强度和刚度都是足够的。
且模架的大小也适中,经核算选用该模架是较为合理的。
6合模导向机构的设计
导向机构是保证动模或上下模合模时,正确定位和导向的零件。
本副模具是采用导柱、导套导向。
导向机构它起到的作用有:
定位作用、导向作用、承载作用、保持运动平稳的作用。
6.1导柱的设计
导柱导向通常是由导柱和导套的间隙配合而组成的。
导柱分带头导柱和有肩导柱。
因为该产品是成批量的生产,导柱经常运动,容易磨损,所以采用导套,这样导套坏了,可以随时更换。
小型模具采用带头导柱。
导柱的技术要求包括:
导柱的长度、形状、材料、数量及布置。
此副模具把导柱设在动模一侧,这样有利于推杆的运动。
导柱固定端与模板之间采用H7/m6,而导柱与导套采用H7/f7的间隙配合。
导套也分直导套和芾头导套。
其用法与导柱的用法一样。
导套的技术要求的技术要求包括:
导套的形状、导套的材料、及固定形式及配合精度。
导套采用H7/r6配合镶入模板。
导柱结构和尺寸如下图所示:
图4导柱结构图
取导柱的长度为100mm,导柱的材料选T8A,淬火处理到55~60HRC,导柱的前端做成锥台形,这样是为了导柱顺利进入导套,导柱固定端粗糙度Ra为0.8,导向部分Ra为0.4该导柱的布置采用等直径导柱对称分布,但是为了在合模时要注意。
6.2导套的设计
导套采用直导套,这样简单易制作,而且也适用。
其结构和形状如图所示:
图5导套结构图
导套的前端倒圆角,是为了让导柱顺利进入导套。
材料通常也采用T8A,热处理,使其硬度达到一定硬度,以利于耐磨。
粗糙度为Ra为0.8,固定采用H7/r6配合镶入模板。
7推出机构的设计
使塑件从成型零件上脱出的机构称之为推出机构。
本副模具是通过注塑机的合模机构,把力传给推板,然后通过通过固定板,再通过推杆,最后传给推件板,把塑件推出的。
推出零件常分为推件板、推杆、推管、成型推杆等。
此副模具所设计的塑件是属于薄壁塑件,而且在推出时不允许有推出痕迹,所以该模具采用推件板推出,这样有利于保证塑件的精度。
此模具的设计也要满足一般推出机构的设计原则:
塑件滞于动模一侧,这样有利于设计推出推出机构,以致于使模具结构简单、防止塑件变形、力求良好的塑个外观、结构可靠、脱模时工作可靠,运动平稳,制造方便,更换容易。
脱模力的计算:
Ft=Fb………(17)
Fb=AP
=3500x10-9x3x107
=105N
其中Ft是脱模力,Fb是塑件对型芯的包紧力,P为塑件对型芯的单位面积的包紧力。
模外冷却取P约为2.4~3.9x107Pa,模内冷却约取0.8x1.2x107Pa,由此式可以得到,当塑件越大,对型芯的包紧面也越大,因此脱模力也越大,在模内脱出所需的脱模力要少于模外脱出的脱模力。
但模内脱模容易使塑件容易变形,因此该模选用模外脱模。
此副模具采用简单推出机构。
它需要设计推杆、推件板、推杆固定板、推板等的设计。
推杆的设计:
此模具由于塑件是圆形件,各处的脱模力是一样的,为了各处平衡,设计推杆时应均匀布置推杆。
这样使系统就显得比较平衡了,增加了推杆的寿命。
推杆的直径的设计,其尺寸和结构如下图:
图6推杆结构图
推杆在推推件板时,应具有足够的刚性,以承受推出力,条件充许的话,尽可以把推杆的直径设得大一点。
经过仔细的推算,选推杆的直径为10,为了保持推杆在工作时具有一定的稳定性,把它进行校核。
由公式:
直径d=φ(L2Q/nE)1/4………(18)
=1.5(1202105/4x2.2x105)<
10
取直径为10mm,已经足够了。
进行强度校核:
σ=4Q/nx3.14d2≤σs…………(19)
=4x105/4x3.14x102
=410/1256<
σs
说明它的强度是满足的。
其中d是推杆直径,φ是安全系数,通常取1.5,L是推杆长度,Q是脱模阻力,E弹性模量,n是推杆的根数,σs是推杆的屈服极限,推杆的材料选用T8A,淬火处理。
推杆的固定形式,推杆直径与模板上的推杆孔采用H8/f7r的间隙配合。
推杆的工作端面的配合部分的表面粗糙度Ra为0.8。
推件板是由一块与型芯按一定的配合精度相配合