车床主轴箱箱体组合钻床设计Word文档格式.docx
《车床主轴箱箱体组合钻床设计Word文档格式.docx》由会员分享,可在线阅读,更多相关《车床主轴箱箱体组合钻床设计Word文档格式.docx(35页珍藏版)》请在冰豆网上搜索。
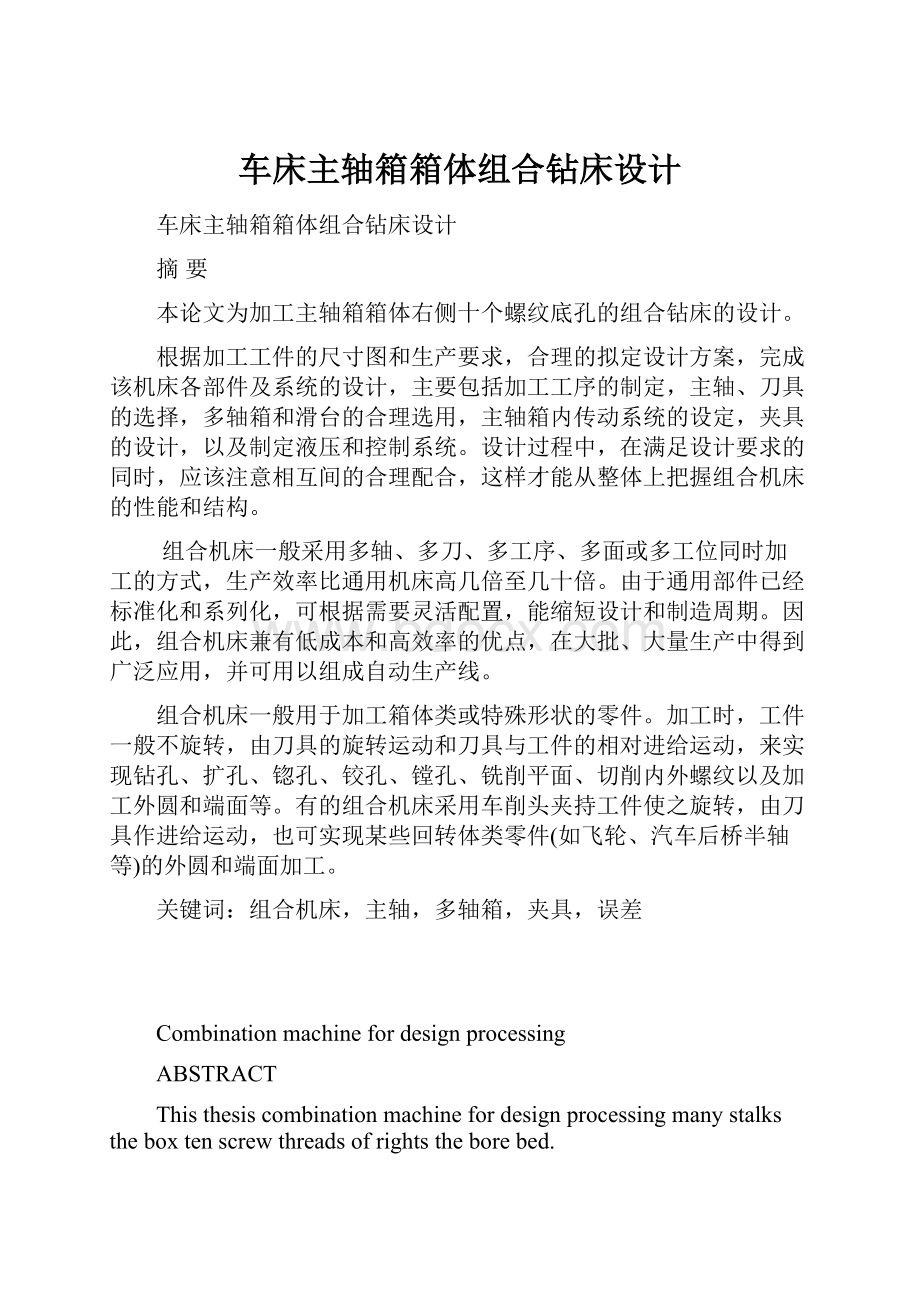
1.1.1了解有关产品的设计的一般程序和方
1.1.2综合运用所学知识
1.1.3初步具备调查研究,收集资料、分析方面的能力
1.1.4围绕毕业设计课题一步一步加深和扩大知识领域
1.1.5逐步树立真确的设计思想和认真的设计作风。
1.2毕业设计的有关内容及计算:
1.2.1选择材料
该加工件为主轴箱箱体,由表3-1灰铸铁的牌号和力学性能,可知HT300型号的铸铁适于制造多轴机床主轴箱。
1.2.2计算硬度
硬度242HBS:
查表3.2-3灰铸铁铸件预计的机械性能及应用举例,有σb=290MPa,由硬度与抗拉强度间对应的经验公式,当σb>
196MPa时
HB=RH(100+0.438σb)
灰铸铁相对硬度RH=0.8~1.20
所以HBmax=272HBS,
HBmin=182HBS,
查表7-24组合机床设计中推荐的切削力、扭矩及功率计算公式的注解中HB=HBmax-(HBmax-HBmin)/3
从而HB=272-(272-182)/3=242HBS
1.2.3重量估算
M=
=38Kg
第2章方案讨论及总体设计
组合机床是由大量的通用部件为基础,配以少量专用部件组成的一种高效专用机床。
它能对一种或几种零件进行多刀、多轴、多面、多工位加工,在组合机床上可以完成钻孔、扩孔、铰孔、镗孔、攻丝、车削、铣削、磨削及滚压等工序;
生产效力高,加工质量稳定。
其组成是:
床身(侧底座)、底座(中间底座、立柱底座)、动力滑台、夹具、动力箱、多轴箱、立拄、垫铁、液压装置、电器控制设备、刀具等。
总体方案设计主要包括制定工艺方案(确定零件在组合机床完成的工艺内容及加工方法,选择定位基准和夹紧部位,决定工步和刀具结构形式、种类及切削用量等)、确定机床装配形式、制定影响机床总体布局和技术性能的主要部件的结构方案。
2.1组合机床工艺方案的制定
2.1.1综合运用所学知识
根据题目要求,该组合机床采用液压滑台驱动,实现进给运动。
本设计为钻10个M8的螺纹底孔,分析可知,其加工为单工位的平面加工,且其加工的精度要求不是不高,生产需要为大批大量生产,故该组合机床的通用部件使用大型部件。
(1)由工序集中的原则
考虑该工件加工孔间相对位置有严格的精度要求,所以应该在一次工序中集中加工,以免2次安装产生的误差影响和便于机床精度调整与找正
(2)孔间中心距的限制
查表7-37通用主轴最小间距对于滚针轴承主轴dmin>
35.5mm
由加工工序图可有主轴7和9之间距离最小,因此
dmin=
=41.5mm>
(3)生产批量要求
该组合机床要求能够满足大批量工件的加工需求,其通用部件因该使用大型部件。
2.1.2定位基准和夹压部位的选择
组合机床一般为工序集中的多刀加工,不但切削负荷大,而且工件受力方向变化。
因此,正确选择定位基准和夹压部位是保证加工精度的重要条件。
对于毛坯基准选择要考虑有关工序加工余量的均匀性;
对于光面定位基准的选择要考虑基面与加工部位间位置尺寸关系,使它利于保证加工精度。
定位夹压部位的选择应在有足够的夹紧力下工件产生的变形最小,并且夹具易于设置导向和通过刀具。
该螺纹底孔分别以孔Ⅱ、Ⅲ、Ⅳ的轴线为中心作为定位基准,而孔Ⅱ、Ⅳ的轴线又以孔Ⅲ的轴线为平行基准,考虑到夹紧问题,选择孔Ⅱ、Ⅲ的轴线为加工件的定位基准,另一侧面为定位面,加工面作为夹紧面。
2.1.3工序间余量的确定
2.1.4刀具结构的选择
2.2切削用量的确定
切削用量选择是否合理,对组合机床的加工精度、生产率、刀具耐用度、机床的结构型式及工作可靠性均有较大影响。
由于钻孔要求较高的切削速度和较小的进给量,查表7-19高速钢钻头切削用量有刀具切削速度为v=(10~18)m/min,进给量为f=(0.1~0.18)mm/r,现取v=18m/min、f=0.15mm/r。
2.3确定切削力、切削转矩、切削功率
根据选定的切削用量(主要指切削速度v及进给量f),确定进给力作为选用动力滑台及设计夹具的依据;
确定切削转矩用以确定主轴及其他传动件的尺寸;
确定切削功率用作选择主传动电机功率。
根据表7-24组合机床设计中推荐的切削力、扭矩及功率计算公式有
M8的孔:
切削力F=
=
=
(N)
切削转矩T=
(N*mm)
切削功率P=Tv/(9740ΠD)=
=0.2KW
2.4组合钻床主轴箱体上的10个M8螺纹底孔的加工工序图
根据加工工序图上加工部位的尺寸、精度、表面粗糙度及技术要求,加工用的定位基准、夹压部位以及被加工零件的材料HT300,其布氏硬度为242HBS,加工部位壁厚20mm来制定工艺方案。
加工工序图如图2-1:
图2-1
2.5液压滑台的设计计算
为了完成主轴箱体侧面10个螺纹底孔的加工,液压滑台工作循环如图2-2所示:
图2-2
为实现上述工作循环,可以采用液压系统和电气系统操纵行程开关来实现快进——工进——快退的工作循环。
其工作过程为:
液压滑台快进后,当摆杆碰到中间行程开关时,经液压系统转换为工作进给,动力头以慢进速度完成加工循环,当碰到终点行程开关时,延时一段时间,动力头再变为快退,到碰到原位的行程开关后快退结束,动力头停止。
在加工终了,压下终点行程开关,同时发出信号切断主轴旋转的信号即可,也既当液压滑台在快退到压下开始的限位开关,主轴旋转停止。
由F总=10745N,查表7-151HY系列液压滑台主要技术性能,选择1HY40M型液压滑台以及相配套的侧底座,其行程为630mm,台面宽度为400mm,台面长度为800mm,最大进给力为20000(N),工进速度为12.5~500mm﹒min-1,快进速度为8m﹒min-1。
液压滑台与其附属部件配套,通过电气、液压联合控制实现自动循环。
根据零件的尺寸图,选用一次工作进给,这种工作循环主要用于对工作进给速度要求不变的情况下,如:
钻孔、扩孔、镗孔等。
当孔加工深度要求较高精度时,可采用死挡铁停留来保证。
附属部件、支承部件配套表:
表2-1
滑台型号
行程(mm)
二级进给及压力
导轨防护
分级进给装置
滑台侧底座
立柱
立柱侧底座
1HY40
630
1HY40-F51
1HY40-F81
1CC401M
1CL40M
1CD40M
查表5-31HY系列液压滑台卧式配置时联系尺寸:
液压滑台的尺寸为:
B=400mB1=400
B2=96B360.5
B4=330B5=85
b1=355L=630
L1=1470L2=800
L3=307l=100~180
e=120~90取e=110
H1=320H2=245
n=7m=0
d0=M16
侧底座的尺寸为:
B6=600B7=85
L4=1580L5=250
L6=60H3=560
H4=210H5=110
H6=40d1=M20*70
d2=¢20d3=¢24
d4=G1d5=G1/4
根据加工工件的尺寸,可以按
快进(264mm),
工进(36mm),
快退(300mm)。
的过程来放置行程开关,完成工件的加工。
2.6加工示意图2-3
图2-3
2.6.1加工示意图的作用和内容
加工示意图是在工艺方案和机床总体方案初步确定的基础上绘制的。
是表达工艺方案具体内容的机床工艺方案图。
它是设计刀具、辅具、夹具、多轴箱和液压、电气系统以及选择动力部件、绘制机床总联系尺寸图的主要依据;
是对机床总体布局和性能的原始要求;
也是调整机床和刀具所必须的重要技术文件。
见加工示意图II表达和标注的内容用:
机床的加工方法,工作循环和工作行程;
工件、刀具及导向、托架及多轴箱之间的相对位置及其联系尺寸;
主轴结构类型、尺寸及外伸长度;
刀具类型、数量和结构尺寸(直径和长度);
接杆(包括镗杆)、浮动卡头、导向装置、等结构尺寸;
刀具、导向套间的配合,刀具、接杆、主轴之间的连接方式及配合尺寸等。
2.6.2选择刀具、导向及有关计算
(1)刀具的选择
根据工件的材质、加工精度、表面粗糙度、排屑及生产率等要求,刀具选用高速刚。
只要条件允许,应尽量选用标准刀具。
刀具插入接杆孔内的长度,在绘制加工示意图时应注意从刀具的总长度中减去。
由表5-2普通螺纹基本尺寸可以查得螺距为1的M8螺纹孔小径D1=6.917mm,根据工件的加工及材料特点,宜选用高速钢型的直柄麻花钻,通过表2-106直柄麻花钻,选择d=7.00上偏差为0下偏差为-0.22的刀具。
其尺寸联系图2-4:
图2-4
(2)导向结构的选择
组合机床加工孔时,除采用刚性主轴加工方案外,零件上孔的位置精度主要是靠刀具的导向装置来保证的。
因此,正确选择导向结构和确定导向类型、参数、精度,是设计组合机床的重要内容,也是绘制加工示意图时必须解决的问题。
查表7-26导向装置的布置与参数选择及表7-27导向装置的配合来确定,
其尺寸见图2-5:
图2-5
(3)确定主轴类型、尺寸、外伸长度
主轴类型主要依据工艺方法和刀杆与主轴的联结结构进行确定。
主轴轴颈及轴端尺寸主要取决于进给抗力和主轴——刀具系统结构。
如与刀杆有浮动联接或刚性联接,主轴则有短悬伸镗孔主轴和长悬伸的钻孔主轴。
主轴轴颈尺寸规格应根据选定的切削用量计算出切削转矩T总=23.8N
根据表7-28轴能承受的扭矩可以得传动轴直径为20mm.
综合考虑加工精度和具体工作条件,按表7-31通用主轴的系列参数选定主轴外伸长度L,外径D和内径d1及配套的刀具接杆莫氏锥度或攻螺纹靠模规格代号等。
对于卧式类钻削类主轴:
有主轴外伸长度L=115mm,
外径D=32mm,
内径d1=20mm,
(4)选择接杆、浮动卡头
除刚性主轴外,组合机床主轴与刀具间常用接杆连接(称刚性连接)和浮动卡头连接(称浮动连接)。
在钻、扩、铰、锪孔及倒角等加工小孔时,通常都采用接杆。
因多轴箱各主轴的外伸长度和刀具长度都为定值,为保证多轴箱上各刀具能同时到达加工终了位置,须采用轴向可调整的接杆来协调各轴的轴向长度,以满足同时加工完成各孔的要求。
为使工件端面至多轴箱端面为最小距离,首先应按加工部位在外壁、加工孔深最浅、孔径又最大的主轴选定接杆(通常先按最小长度选取),由此选用其它接杆。
接杆已标准化,通用标准接杆号和弹簧卡头可根据刀具尾部(莫氏号)和主轴头部内孔径直径按图5-38弹簧卡头、图5-39接杆来选取。
为提高加工精度、减少主轴位置误差和主轴振摆对加工精度的影响,在采用长导向或双导向和多导向进行镗、扩、铰孔时,一般孔的位置精度靠夹具来保证。
为避免主轴与夹具导套不同轴而引起的刀杆“别劲”现象影响加工精度,均可采用浮动卡头连接。
(5)标注联系尺寸
首先从同一多轴箱上所有刀具中找出影响联系尺寸的关键刀具,使其接杆最短,以获得加工终了时多轴箱前端面到工件端面之间所需的最小距离,并据此确定全部刀具、接杆、导向托架及工件之间的联系尺寸。
主轴端部须标注外径和孔径(D/d)、外伸长度L;
刀具结构尺寸须标注直径和长度;
导向结构尺寸应标注直径、长度、配合;
工件至夹具之间须标注工件离导套端面的距离;
还必须标注托架与夹具之间的尺寸、工件本身以及加工部位的尺寸和精度等。
多轴箱端面到工件端面之间的距离是加工示意图上重要的联系尺寸。
为使所设计的机床结构紧凑,应尽量缩小这一距离。
这一距离取决于两方面:
一是多轴箱上刀具、接杆、主轴等结构和互相联系所需的最小轴向尺寸;
二是机床总布局所要求的联系尺寸。
这两个方面是互相制约的。
(6)标注切削用量
各主轴的切削用量应标注在相应的主轴后端。
其内容包括:
主轴转速n、相应刀具的切削速度v、每转进给量f。
同一多轴箱上各主轴的每分钟进给量是相等的,等于动力滑台的工进速度v,即fM=vf。
(7)动力部件工作循环及行程的确定
动力部件的工作循环是指加工时,动力部件从原始位置开始运动到加工终了位置,又返回原位的动作过程。
一般包括快速引进、工进进给和快速退回等动作。
有时还有中间停止、多次往复进给、跳跃进给、死挡铁停留等特殊要求。
a.工作进给长度LI的确定组合机床上有第一工作进给和第二工作进给之分。
前者用于钻、扩、铰和镗孔等工序;
后者常用于钻或扩孔后需要进行锪平面、倒大角等工序。
工作进给长度LI,应等于加工部位长度L(多轴加工时按最长孔决定)与刀具切入长度L1和切出长度L2之和,即LI=L+L1+L2
切入长度一般为5~10mm,取L1=10mm。
根据端面的误差情况确定。
切出长度查表3-7有:
L2=1/3d+(3~8)=2.3+(3~8)=5.3~10.3mm,
取L2=6mm
则:
LI=L+L1+L2=10+20+6=36mm
b.快速引进长度的确定快速引进是指动力部件把刀具送到工作进给位置,其长度按具体情况确定,考虑到安装工件的必要尺寸取L快进=264mm。
c.快速退回长度的确定快速退回的长度等于快进长度和工进进给长度之和。
一般在固定式夹具钻孔或扩孔的机床上,动力部件快速退回的行程,只要把所有刀具都退回导套内,不影响工作的装卸就行了。
但对于夹具需要回转或移动的机床,动力部件快速退回行程必须把刀具、托架、活动钻模板及定位销都退离到夹具运动可能碰到的范围之外,L快退=36+264=300mm。
d.动力部件总行程的确定动力部件的总行程除了满足工作循环向前和向后所需的行程外,还要考虑因刀具磨损或补偿制造、安装误差,动力部件能够向前调节的距离(即前备量)和刀具装卸以及从接杆中或接杆连同刀具一起从主轴孔中取出时,动力部件需后退的距离(刀具退离夹具导套外端面的距离应大于接杆插入主轴孔内或刀具插入接杆孔内的长度,即后备量)。
因此,动力部件的总行程为快退行程与前后备量之和。
2.7机床联系尺寸总图2-6
图2-6
2.7.1刀具结构的选择
机床联系尺寸总图是以被加工零件工序图和加工示意图为依据,并按初步选定的主要通用部件以及确定的专用部件的总体结构而绘制的。
是用来表示机床的配置型式、主要构成及各部件安装位置、相互联系、运动关系和操作方式的总体布局。
用以检验各部件相对位置及尺寸联系能否满足加工要求和通用部件选择是否合适;
它为多轴箱、夹具等专用部件设计提供重要依据;
它可以看成是机床总体外观图。
由其轮廓尺寸、占地面积、操作方式等可以检验是否适应用户现场使用环境。
2.7.2绘制机床联系尺寸总图之前应确定的主要内容
(1)选择动力部件
动力部件的选择主要是确定动力箱(或各种工艺切削头)和动力滑台。
动力箱规格要与滑台匹配,其驱动功率主要依据多轴箱所需传递的切削功率来选用。
在不需要精确计算多轴箱功率或多轴箱尚未设计出来之前,可按下列简化公式进行估算:
P多轴箱=P切削/η
式中P切削——消耗于各主轴的切削功率的总和,单位为KW;
计算公式查表6-20计算。
η——多轴箱的传动效率,加工黑色金属时取0.8~0.9,加工有色金属时取0.7~0.8;
取η为0.8。
P多轴箱=P切削/η=2/0.8
=2.5KW
查表7-91TD32-1TD50动力箱性能,多轴箱选用1TD40Ⅲ型动力箱,其内部电动机型号为Y132M-4,电动机功率为3.0KW,电动机转速为960r·
min-1。
驱动轴转速为480r·
(2)确定机床装料高度H
装料高度一般是指工件安装基面至地面的垂直距离。
在确定机床装料高度时,首先要考虑工人操作的方便性;
对于流水线要考虑车间运送工件的滚道高度;
对于自动线要考虑中间底座的足够高度,以便允许内腔通过随行夹具返回系统或泠却排屑系统。
其次是机床内部结构尺寸限制和刚性要求。
如工件最底孔位置h2、多轴箱允许的最底主轴高度h1和通用部件、中间底座及夹具底座基本尺寸的限制等。
考虑上述刚度、结构功能和使用要求等因素,新国家标准装料高度为1060mm,与国际标准ISO一致。
实际设计时常在850~1060mm之间选取。
本课题取装料高度为H=930.5mm。
(3)确定夹具轮廓尺寸
主要确定底座的长、宽、高尺寸。
工件的轮廓尺寸和形状是确定夹具底座轮廓尺寸的基本依据。
具体要考虑布置工件的定位、限位、夹紧机构、刀具导向装置以及夹具底座排屑和安装等方面的空间和面积需要。
加工示意图中已确定了一个或几个加工方向的工件与导向间距离以及导向套的尺寸。
这里主要是合理确定设置导向的钻模架体尺寸,可初步确定它在加工方向的尺寸一般不小于导向长度,取L长503mm,至于宽度尺寸可据导向分布尺寸及工件限位元件安置需要确定,取L宽480mm,工件夹紧高度L=1072.5mm,夹具底座的高度尺寸,一方面要保证其有足够的刚度,同时要考虑机床的装料高度、中间底座的刚度、排屑的方便性和便于设置定位、夹紧机构,一般不小于240mm。
本课题高度为240mm。
对于较复杂的夹具,绘制联系尺寸总图之前应绘制夹具夹具结构草图,以便于确定夹具的主要参数、基本结构方案及其外形控制尺寸。
(4)确定中间底座尺寸
中间底座的轮廓尺寸,在长宽方向应满足夹具的安装需要。
它在加工方向的尺寸,实际已由加工示意图所确定,图中已规定了机床在加工终了时工件端面至多轴箱前端面的距离。
由此,根据选定的动力箱、滑台、侧底座等标准的位置关系,并考虑滑台的前备量,通过尺寸链就可以计算确定中间底座加工方向的尺寸(本课题选前备量为30mm,计算长度为740mm)。
算出长度通常应圆整,并按R20优选数系选用。
应注意,考虑到毛坯误差和装配偏移,中间底座支承夹具底座的空余边缘尺寸。
当机床不用泠却液时不要小于10~15mm;
使用冷却液时不小于70~100mm。
还须注意:
当加工终了时,多轴箱与夹具体轮廓间应有足够的距离,以便于调整和维修,并应有一定的前备量。
确定中间底座的高度方向尺寸时,应注意机床的刚性要求、冷却排屑系统要求以及侧底座连接尺寸要求。
装料高度和夹具底座高度确定后,中间底座高度就已确定,本课题中高度为560mm。
(5)确定多轴箱轮廓尺寸
标准通用钻、镗类多轴箱的厚度是一定的、卧式为325mm,立式为340mm。
因此,确定多轴箱尺寸,主要是确定多轴箱的宽度B和高度H及最底主轴高度h1。
见图多轴箱宽度B、高度H的大小主要与被加工零件孔的分布位置有关,可按下式确定:
B=b+2b1
H=h+h1+b1
式中b——工件在宽度方向相距最远的两孔距离,单位为mm;
b1——最边缘主轴中心至箱体外壁距离,单位为mm;
h——工件在高度方向相距最远的两孔距离,单位为mm;
h1——最底主轴高度,单位为mm。
b和h为已知尺寸,从加工工序图中查得:
b=197.5mm,
h=192mm。
为保证多轴箱内有足够安排齿轮的空间,推荐b1>
70~100mm。
取b1=100mm,多轴箱最底主轴高度h1必须考虑与工件最低孔位置h2、机床装料高度H、滑台总高h3、侧底座高度h4等尺寸之间的关系而确定。
推荐h1>
85~140mm,取h1=108mm。
H、B的计算如下:
B=b+2b1=197.5+2*100=397.5mm
H=h+h1+b1=192+108+100=400mm
查表5-401TD25-1TD80动力箱与多轴箱、滑台的联系尺寸及表7-3多轴箱体规格尺寸及动力箱法