表处车间工艺喷粉Word格式文档下载.docx
《表处车间工艺喷粉Word格式文档下载.docx》由会员分享,可在线阅读,更多相关《表处车间工艺喷粉Word格式文档下载.docx(19页珍藏版)》请在冰豆网上搜索。
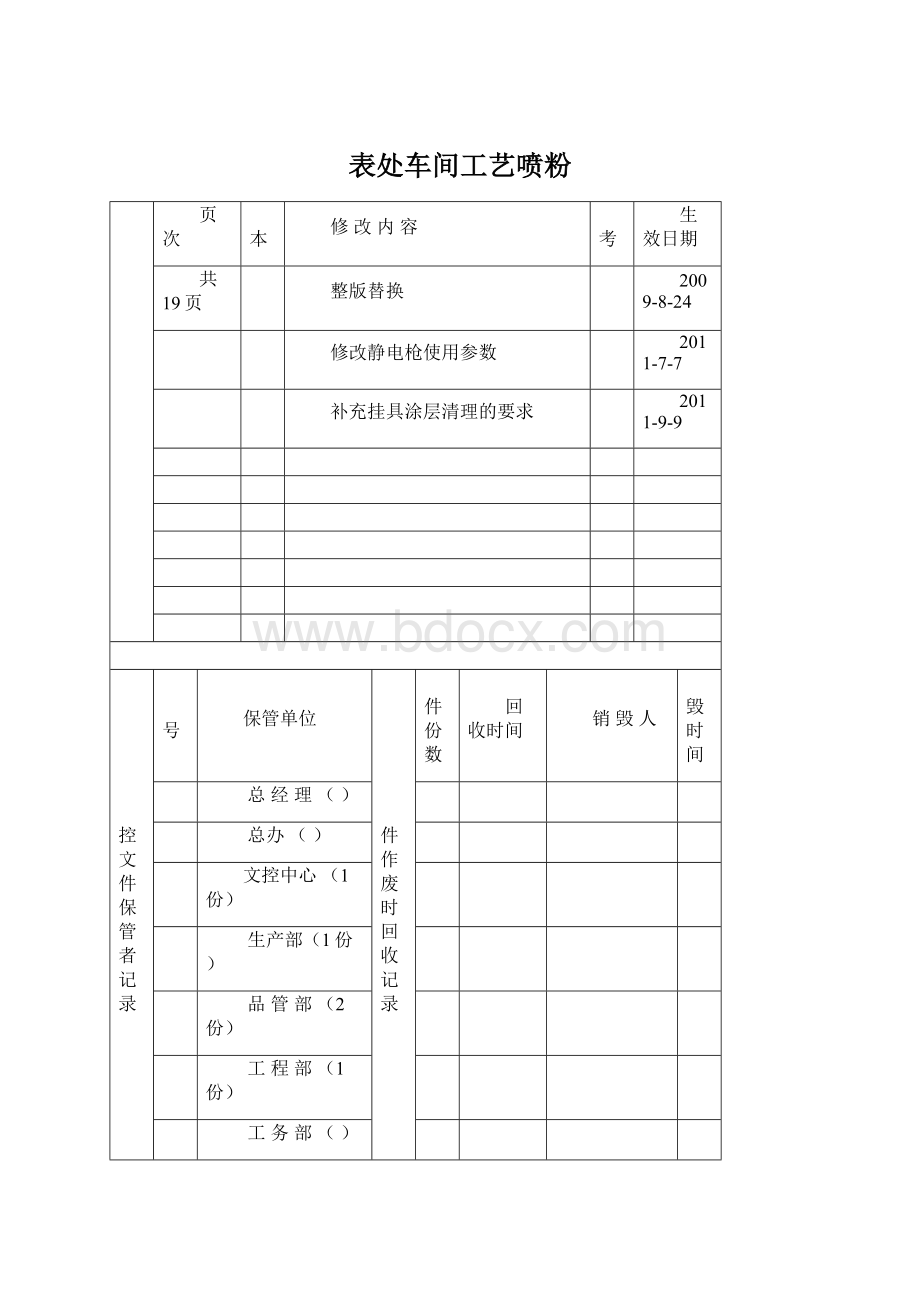
5
品管部(2份)
6
工程部(1份)
7
工务部()
8
业务部()
9
资材部()
签署栏
批准张宁
日期2011-9-9
审核______________
日期______________
编制﹕彭湘源
日期﹕2011-9-9
一、粉末固化的基本原理
环氧树脂中的环氧基、聚酯树脂中的羧基与固化剂中的胺基发生缩聚、加成反应交联成大分子网状体,同时释放出小分子气体(副产物)。
固化过程分为熔融、流平、胶化和固化4个阶段。
温度升高到熔点后工件上的表层粉末开始融化,并逐渐与内部粉末形成漩涡直至全部融化。
粉末全部融化后开始缓慢流动,在工件表面形成薄而平整的一层,此阶段称流平。
温度继续升高到达胶点后有几分短暂的胶化状态(温度保持不变),之后温度继续升高粉末发生化学反应而固化。
工件经过前处理除掉冷轧钢板表面的油污和灰尘后才能喷涂粉末,同时在工件表面形成一层锌系磷化膜以增强喷粉后的附着力。
前处理后的工件必须完全烘干水分并且充分冷却到35℃以下才能保证喷粉后工件的理化性能和外观质量。
二、静电喷涂原理
静电粉末静电喷涂首先要有产生直流高压的高压静电发生器,和把粉末喷射出来的喷枪。
通常情况下,工件接地,喷枪尖就接负高压,负高压是高压静电发生器供给的。
当喷枪尖端靠近工件,就产生电晕放电现象,粉末从喷枪口喷射出来,经过电晕放电就带上了负电荷。
这带负电荷的粉末微粒在静电力和压缩气流的作用下到达工件表面,在粉末微粒的其它部分的负电荷与工件之间具有静电吸引力,使粉末微粒吸附在工件表面上,然后经过高温烘烤,塑料颗粒就会融化成一层致密的均匀、连续平滑的保护层牢牢附着在工件表面,变成效果各异的最终涂层。
三、静电喷涂
1、喷粉作业流程
坯料检查→上挂具(挂钩)→除杂尘→喷涂→转件→上烤车→烘烤→下架→自检→补漆→摆放
注:
下架及后续工序带白手套作业
2、各流程的作业方法与作业要求:
2.1坯料检查
2.1.1作业方法:
作业员工在上挂具前检查工作表面是否有明显的不良现象,不符合喷涂要求,如脱焊、凹坑、生锈、变形等,将此类不良品挑出后由组长级以上人员处理。
2.1.2作业要求:
由车间组长确认所喷涂的工件型号规格是否正确,所喷涂的粉体颜色是否正确。
2.1.3品质要求:
品检员在上挂具前检查工件表面是否有明显的不良现象,如脱焊、凹坑、生锈、变形等,确认所喷涂的工件型号规格是否正确,所喷涂的粉体颜色是否正确。
2.2上挂具(挂钩)
2.2.1作业方法:
上挂具、挂钩是将工件按一定方式悬挂排列,以方便喷涂、提高效率。
挂具分专用挂具与普通挂钩,如本公司有玻璃刮挂具(配合铁线钩使用)、管件类挂具、带夹子窗帘环挂具、带夹子锌合金窗帘环外环挂具;
普通铁线挂钩,见下图
2.2.2作业要求:
A、尽量采用外表无挂点方式悬挂工件,若无法避免则要求挂点尽量小并在隐蔽处。
如插在管内的方式,表面无挂点;
铁线架则挂在铁线背面交焊处,且挂钩不能碰到工件其他表面;
工件有孔处,则挂在孔处较适宜。
B、上挂具或挂钩后的产品要求平稳,工件不可在挂具上随意滑动。
C、除专用挂具外,工件之间的间隔距离一般为6-10cm,实际以工件之间在转移时不相互碰撞为原则,但不可过大,避免造成烤箱的空间浪费,生产效益低。
D、挂具要保持良好的通电效果,并经常进行保养,挂具上的涂层厚度大于1.5mm时就要敲掉涂层,避免烘烤时产生涂层对产品的流挂。
2.3除杂尘
2.3.1作业方法:
用气枪吹净表面杂志与灰尘,若表面有较多难吹落的杂质,则用碎布擦拭干净工件表面。
2.3.2作业要求:
A、工件表面干净。
B、若喷涂容易被污染的颜色(如白色)需要用碎布擦拭干净工件,以免气吹造成颜色被污染。
2.3.3品质要求:
B、若喷涂容易被污染的颜色(如白色),颜色无污染。
2.4喷涂
2.4.1作业方法:
严格按相关《设备安全操作规程》进行喷涂作业。
2.4.2作业要求:
A、走抢需均匀,不可漏喷、变速喷、随意加喷。
B、大工件喷涂距离为15~30cm,小工件喷涂距离10~20cm。
C、有死角的工件,先喷薄死角处,再均匀喷涂各面。
D、正常喷涂参数:
小体积工件:
静电电压为60~80KV,静电电流10~20uA,主气压为0.1~0.3Mpa,雾化气压为0.05~0.15Mpa,清枪压力0.05~0.15Mpa,粉筒流化压力0.04~0.1Mpa。
大体积工件:
静电为60~90KV,静电电流10~20uA,主气压为0.2~0.4Mpa,雾化气压为0.05~0.2Mpa;
清抢压力0.05~0.2Mpa,粉筒硫化压力0.04~0.1Mpa。
E、加(返)喷工件时,喷枪的静电电压40~50KV;
①电压过高容易造成粉末反弹和边缘麻点;
电压过低上粉率低。
②电流过高容易产生放电击穿粉末涂层;
电流过低上粉率低。
③流速压力越高则粉末的沉积速度越快,有利于快速获得预定厚度的涂层,但过高就会增加粉末用量和喷枪的磨损速。
④适当增大雾化压力能够保持粉末涂层的厚度均匀,但过高会使送粉部件快速磨损;
适当降低雾化压力能够提高粉末的覆盖能力,但过低容易使送粉部件堵塞。
⑤清枪压力过高会加速枪头磨损,过低容易造成枪头堵塞。
⑥供粉桶流化压力过高会降低粉末密度使生产效率下降,过低容易出现供粉不足或者粉末结团。
⑦喷枪口至工件的距离过近容易产生放电击穿粉末涂层,过远会增加粉末用量和降低生产效率。
F、不同颜色的粉体不可混放,以避免相互污染;
G、极容易被污染的粉体如白色,需要集中、单独地分开放置;
H、若工件磷化后表面灰尘、杂质较多且难于擦拭干净,可先将工件烘烤至200℃×
15分钟,再进行擦灰,然后按正常喷涂工艺作业;
I、若锌合金产品喷涂时,需先将工件烘烤至200℃×
15分钟,再按正常的工艺作业。
2.5转件、上烤车
2.5.1作业方法:
将喷涂好的工件转移到烤车,准备烘烤。
2.5.2作业要求:
A、转移时需轻拿轻放,不可剧烈晃动,避免碰伤产品;
B、手拿挂具时,防止粉堆掉落在工件上,造成粉堆现象;
C、上烤车时,挂具间隔合理,注意手不可触碰工件,工件间亦不可互相碰撞,工件如有碰撞、触碰,需重新喷粉。
2.6烘烤:
2.6.1作业方法:
将烤车推至烤箱内进行烘烤。
2.6.2作业要求:
A、参数设置:
一般为200℃×
15分钟(具体按供应商提供的粉体参数设置)。
B、烘箱的启动、设置、运行关闭均由组长负责。
C、烤车推进烤箱时,避免工件剧烈晃动,导致工件碰伤。
2.7下架
2.7.1作业方法:
工件烤好后,表面温度降至室温时,将成品从挂具上取下。
2.7.2作业要求:
A、要轻拿轻放,避免工件掉落,工件碰伤、刮花、变形;
B、白色或易脏工件下架后需尽快包装或用报纸、纸板做好防尘工作,以保护产品不受污染;
C、下架后产品需要放在干净台面上或框内,摆放整齐、有序,并注意产品不可积压过高。
对易刮花、碰伤的产品每层用报纸或纸板隔开。
2.8品质要求(自检/品管抽检)
2.8.1品检方法:
A、摩擦力测试:
工件间用1kg的力互相摩擦一次,无可见划痕为合格。
B、对照色版,一般接近95%为合格,包括光泽与色泽。
C、涂层厚度:
50-90um。
D、表面品质:
表面无粉堆、流挂、喷薄、杂质、阴阳色、桔皮、沙眼等,轻微不良现象,参考样板做次品处理:
严重不良经品检主管确认后做返工处理。
2.8.2品检要求:
作业方法中的A、B项,需有车间主管确认,测试时间:
每班首件产品;
每批领用新粉以及有任何加工条件改变时,必须进行测试。
B、作业方法中的C项,需由车间主管确认,测试时间,每烘箱需从四个角落抽四件进行核对,以便及时指导枪手进行调整。
C、作业方法中的D项,需由车间员工进行检查,车间组长进行核查。
2.9补漆
2.9.1作业方法:
带手套作业,对挂点、喷薄、露底处补漆(自干漆)。
2.9.2作业要求:
补漆颜色与工件喷涂后色泽相近,补漆处光滑、平整、无漏补,面积不可过大,对产品外观无明显影响。
3.0产品堆放要求
A、管类产品:
3分管—30pcs/扎;
4、5、6分管—20pcs/扎;
7、8分管—10pcs/扎;
用栈板堆放时每层用报纸或拷贝纸隔开,最高不能超过8层(栈板上不可有钉凸起),板面需垫干净报纸或纸板。
B、小件类产品:
如J钩、天花板挂钩、托架、带夹子窗帘环外环等产品,用胶框放置,每层用报纸或拷贝纸隔开,产品注意轻拿轻放。
C、大件类产品:
如展示架、旋转架、9984落地式杂志架用栈板摆放时,以不压坏产品为原则,但堆放最高不超过100cm,堆放高度不压坏产品为限,每层需要用拷贝纸(易脏的工件,如白色浴帘管)、报纸或纸板(用于质量较重,体积较大工件,如300001800加强型、9438落地式杂志架)隔开;
同层产品摆放要留间隙,防止产品碰伤、刮花。
4其它工艺补充事项:
4.1试产
每班生产前或使用新粉以及其他条件改变时,必须先安排小批量试喷并确认粉体、设备、品质、喷手喷涂方式是否正常。
4.2喷粉柜
4.2.1每天生产前,检查回收器是否旋到位,风机运转是否有异常声音。
4.2.2生产过程中,一般每隔半个小时敲击回收器一次,以保证风机抽风效果良好。
4.2.3下班后,需要关闭柜门并盖好粉筒,每天生产结束后,需简单清理粉房一次,换粉时需彻底清理粉房、地面、喷粉设备,(简单清理粉房指将粉房内绝大部分积粉收集起来,允许有少量粉层附在粉房壁内)。
4.3烤箱
4.3.1每天生产前,需检查煤气、烤箱的启动、设置参数、运行是否正常。
4.3.2温控主表显示与四角温度显示表的数值需相近,最高不可相差±
10℃。
4.3.3烤箱每半个月需用气枪清杂一次,并用拖把拖干净。
4.4回收粉的利用
4.4.1黑色、白色粉体生产时回收粉比列不超过总量的50%(在不影响喷涂质量的情况下可适当添加比例)。
4.2银色、古金铜、裂纹、金属镍色粉体生产时回收粉比列不超过总量的20%左右(在不影响喷涂质量的情况下可适当添加比例)。
4.5环境卫生
经常清扫地面,保持良好的喷涂环境,防止粉体受到污染。
5、悬挂方式:
5.2挂架方式
5.3摆放方式
粉末涂料喷涂常见问题和解决措施
涂膜缺陷
造成原因
解决措施
1、沙粒或粒子
1、粉末本身有粒子
1、降低使用要求或过筛或更换粉末
2、前处理不彻底
2、加强前处理的检查与管理
3、挂具杂物污染
3、清洁挂具
4、回收粉末未过筛
4、过100-160目筛后加入使用
2、杂点
1、换粉末时喷粉系统清洁不干净
1、重新清洁喷粉系统
2、同时喷几种颜色的粉末造成粉末污染
2、加强回收系统的回收效果及隔离装置
3、粉末质量不合格
3、降低使用要求或更换粉末
4、环境太差、地面粉尘多
4、清洁喷粉环境
3、色差
1、粉末本身有色差
1、降低使用要求或更换粉末
2、粉膜太薄或太厚
2、调整涂膜厚度
3、烤炉内不同部位温差较大
3、整改设备
4、粉末固化条件改变如烘烤温度和时间
4、调整粉末固化条件
5、涂膜多次烘烤
5、提高喷涂质量减少烘烤次数
6、回收粉比例不稳定
6、加强稳定回收粉的添加比例
7、前处理不合格
7、加强前处理
4、光泽不足或失光
1、粉末烘烤条件不当如温度过高或时间过长
1、调整粉末烘烤条件
2、粉末使用过程中被污染
2、重新清洁喷粉系统,加强喷粉管理
3、回收粉比例添加不当
3、调整回收粉的添加比例
4、回收粉被污染
4、不加回收粉
6、高光粉与无光粉或半光粉同时烘烤
6、高光粉尽量避免与无光粉或半光粉同时混合使用
7、粉末配方的改变造成粉末交叉污染
7、稳定配方或避免不同配方的粉末同时混合使用
8、前处理不合格
8、加强前处理
5、针孔
1、喷涂环境较差,粉末被污染
1、加强喷涂现场的环境管理
2、喷强的静电电压过高或距工件的距离太近造成涂层被击穿。
2、调低静电电压或调缘喷枪与工件的距离
3、涂膜太薄或太厚
3、调整涂膜厚度
4、压缩空气油水含量高不干净
4、加强压缩空气的处理质量
5、前处理不合格
5、加强前处理
6、粉堆
1、喷枪堵塞或气流不畅
1、疏通供粉管道
2、喷枪雾化不佳
2、调整稳定雾化气压
3、喷粉室或挂具上有粉末滴落
3、清洁喷粉室及挂具
4、有异物吸附于工件表面
4、加强喷粉前质量管理
5、粉末流化不理想
5、加强粉末流化
7、缩孔
1、粉末质量不合格
1、更换粉末
2、使用过程中被环境或不相容物体污染
2、加强现场管理及重新清洁喷粉系统更换新粉喷涂
3、压缩空气除油或除水不干净
3、检查气源必要时整改除油和除水设备
4、工件前处理不合格及工件本身的影响
4、加强前处理及工件本身的检查
8、桔皮
1、粉末烘烤升温太快或太慢
1、调整烘烤条件
2、粉末粒径太粗
2、调整粉末粒径
3、涂膜厚度不当
4、粉末在烘烤前受热
4、改善粉末喷涂工艺条件
5、粉末质量不合格
5、更换粉末或降低要求使用
9、涂层脱落
1、高压静电不足
1、检查高压静电设备,调整静电电压
2、喷粉空气压力过高
2、调整喷粉空气压力
3、粉末本身配方设计问题
3、调整配方
4、工件处理不合格
4、加强前处理
10、流挂
1、涂膜太厚
1、调整控制涂膜厚度
2、粉末流平不好
2、调整粉末流平
3、工件挂掉不理想
3、改变挂掉方式
11、物力机械性能差(冲击力、附着力、硬度)
1、粉末质量不理想
1、更换粉末或降低要求使用
2、烘烤温度过高或过低,时间过场或过短
2、调整烘烤固化条件
3、前处理不合格
3、加强前处理
12、耐腐蚀性
2、烘烤温度过高或过低,时间过长或过短
13、工件不上粉或上粉率不好
1、工件未接地或接地不良
1、检查维修工件接地
2、静电电压不够
2、调整静电电压
3、无静电电压或时有时无
3、检查维修静电发生电路
4、粉末粒径太幼
4、调整粉末粒径
5、空气气压不稳而影响粉末雾化问题
5、检查维修供气系统