涂料生产企业安全生产培训班讲座资料Word格式.docx
《涂料生产企业安全生产培训班讲座资料Word格式.docx》由会员分享,可在线阅读,更多相关《涂料生产企业安全生产培训班讲座资料Word格式.docx(27页珍藏版)》请在冰豆网上搜索。
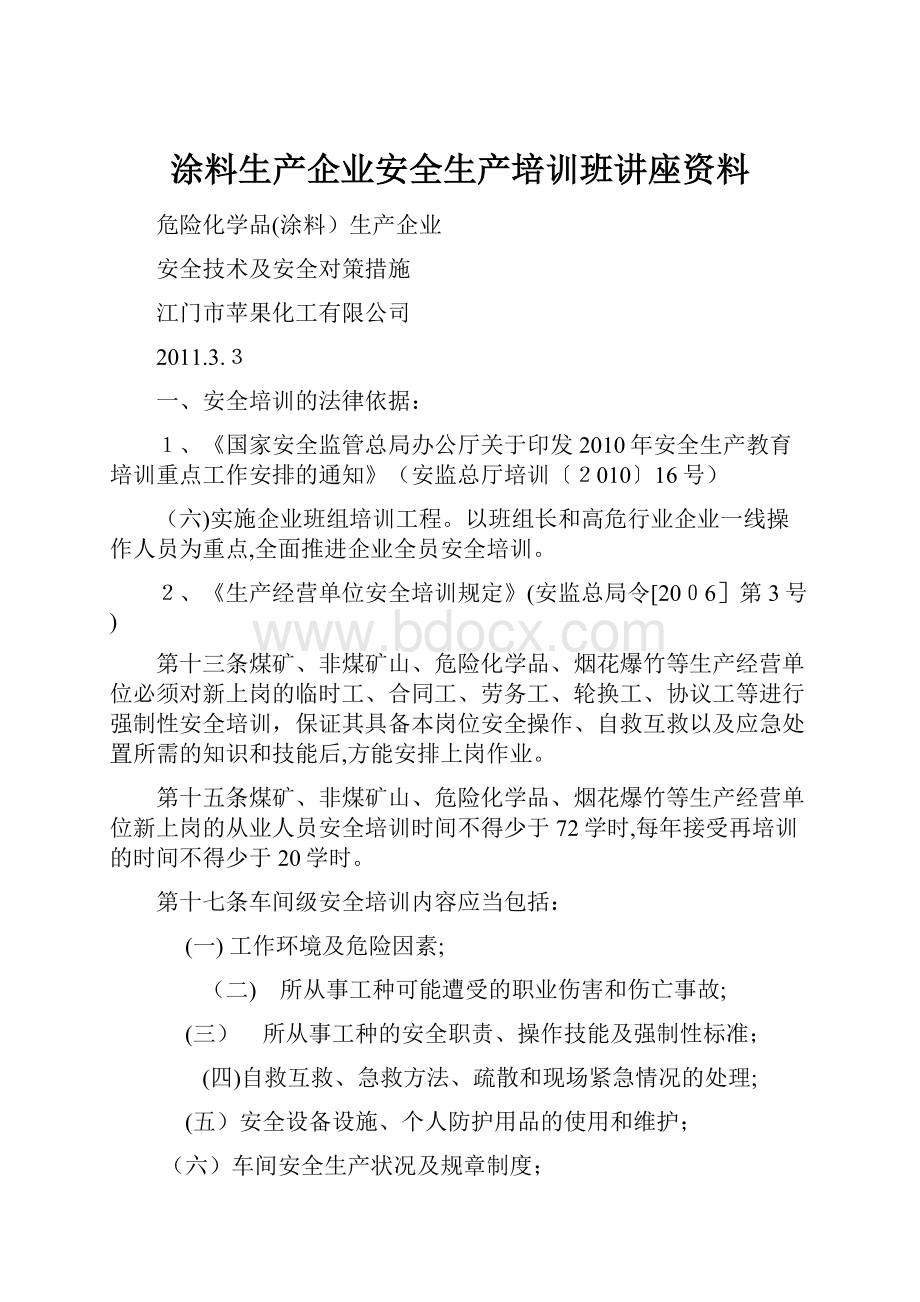
按危险化学品的主要危险特性分为八类:
第1类爆炸品;
第2类压缩气体和液化气体;
第3类易燃液体;
第4类易燃固体、自燃物品和遇湿易燃物品;
第5类氧化剂和有机过氧化物;
第6类有毒品;
第7类放射性物品;
第8类腐蚀品。
分类标准为《常用危险化学品的分类及标志》(GB13690-92)
什么是危险化学品的涂料:
《涂料生产企业安全技术规程》(AQ5204-2008)(2009年1月1日实施)
3术语和定义
3.1涂料 coating
涂于物体表面能形成具有保护、装饰或特殊性能(如绝缘、防腐、标志等)的固态涂膜的液体或固体材料之总称。
早期大多数以植物油为主要原料,故有“油漆”之称。
现在合成树脂已大部分或全部取代了植物油,故称为“涂料”。
注:
在具体的涂料品种名称中可用“漆”字表示“涂料”,如调和漆、厚漆等。
3.2危险化学品的涂料产品CoatingofDangerous Chemicals
符合GB6944危险货物特征的涂料产品,列入GB12268《危险货物名录表》。
注1:
如涂料产品中(包括涂料用树脂),在其闭杯试验闪点不高于60.5℃,或开杯试验不高于65.6℃的产品,属于危险化学品第3类易燃液体。
危险化学品的涂料产品判据见GB6944。
注2:
不符合本条特征的涂料产品不属于危险化学品,即非危险化学品的涂料产品。
三、车间安全生产状况及规章制度;
车间安全生产技术方面要求:
危险化学品涂料生产企业其车间生产过程中存在着使用和生产危险化学品,这是生产所需要的原材料;
也要使用到生产设备,如分散机、三辊机、研磨机、搅拌釜、反应釜等。
这些原料从配(投)料到设备进行生产再到出产品的过程,就是生产工艺的过程。
危险化学品涂料生产企业在生产过程中常使用的原料有甲苯、二甲苯、乙酸乙酯、乙酸丁酯、溶剂油、固化剂、稀释剂等,而产品有不干性醇酸树脂、聚氨酯固化剂、醇酸树脂清漆、硝基木器清漆、硝基底漆、聚酯树脂清漆、聚氨酯树脂清漆和稀释剂等。
这些原料及产品都属于《危险化学品名录》中的笫3类易燃液体;
另外还有使用到第8类腐蚀品如苯酐(邻苯二甲酸酐);
笫6类毒害品如TDI、防白水(单丁醚乙二醇)等。
都具有易燃易爆、有毒、有腐蚀性等危险特性,其中最主要的危险因素是易燃易爆。
危险化学品第3类 易燃液体
易燃液体:
指闭杯闪点等于或低于61℃的液体、液体混合物或者含有固体物质的液体,但不包括由于其危险性已列入其它类别的液体。
本类物质在常温下易挥发,其蒸汽与空气混合物能形成爆炸性混合物。
闪点:
液体表面挥发的蒸气与空气混合物发生瞬间燃烧的最低温度。
易燃液体分类:
3.1项 低闪点液体:
闪点<
-18℃ 如:
乙醚(-45℃)汽油(-48℃)
3.2项中闪点液体:
-18℃≤闪点<
23℃如:
苯(-11℃)乙醇(12℃)
3.3项高闪点液体:
23℃≤闪点≤61℃如:
丁醇(35℃)
易燃液体的危险特性:
①易挥发性:
易燃液体大部分属于沸点低、闪点低、挥发性强的物质。
随着温度的升高,蒸发速度加快,当蒸气与空气达到一定浓度时遇到火源极易发生燃烧爆炸。
②易燃性:
闪点越低,越容易点燃,火灾危险性就越大。
③易产生静电性:
大部分易燃液体为非极性物质,在管道、储罐、槽车、油船的输送、灌装、摇晃、搅拌和高速流动过程中,由于摩擦会产生静电。
当所带的静电荷聚积到一定程度时,就会产生静电火花有引起燃烧和爆炸的危险。
④流动扩散性:
易燃液体具有流动和扩散性,大部分黏度较小,易流动,有蔓延和扩大火灾的危险。
⑤毒害性:
大多数易燃液体都有一定的毒性,对人体的内脏器官和系统有毒性作用。
对工作场所的安全要求:
根据其危险特性,车间安全生产技术要求就必须符合国家有关的安全标准。
①针对其易燃易爆的特性,生产车间及仓库等建筑物的耐火等级、安全间距、消防设施等条件必须达到《建筑设计防火规范》(GB50016-2006)的要求。
②树脂生产车间、危险化学品的涂料产品生产及包装车间、粉末涂料的粉碎、包装车间及仓库、危险化学品仓库等易燃易爆甲、乙类作业场所使用的电动机、低压变压器、低压开关和控制器(开关、断路器,控制开关及按钮,配电盘,控制箱,操作箱等)、照明灯具、信号报警装置等应使用防爆型(EXdⅡBT3)电气设备。
电线套管应采用镀锌焊接钢管,不应采用绝缘导线或塑料管明设。
所有电气设备应进行有效接地。
电气线路及用电设备的防爆必须符合《爆炸和火灾危险环境电力装置设计规范》(GB50058﹣92)的要求;
③甲、乙类仓库内宜使用低温照明灯具,并应对灯具的发热部件采取隔热等防火保护措施;
不应设置卤钨灯等高温照明灯具。
配电箱及开关宜设置在仓库外。
④可燃气体泄漏检测报警装置应符合《石油化工企业可燃气体和有毒气体检测报警设计规范》(SH3063-1999)的要求;
⑤工厂建筑物的防雷装置必须符合《建筑物防雷设计规范》(GB50057﹣94,2002年版)的要求;
⑥有产生静电的生产设备及贮罐、装卸区等的防静电措施《化工企业静电接地设计规程》(HG/T20675-1990)的要求;
⑦工作场所的采光、照明、通风、护栏、噪声、振动、高温、安全警示标志、工作通道等应符合《工业企业设计卫生标准》﹙GBZ1-2010﹚的要求。
安全生产管理方面的要求:
规章制度和操作规程的建立
《危险化学品从业单位安全标准化通用规范》(AQ3013-2008)
第5.3.3条安全生产规章制度至少包括:
1)安全生产职责;
2)识别和获取适用的安全生产法律法规、标准及其他要求;
3)安全生产会议管理;
4)安全生产费用;
5)安全生产奖惩管理;
6)管理制度评审和修订;
7)安全培训教育;
8)特种作业人员管理;
9)管理部门、基层班组安全活动管理;
10)风险评价;
11)隐患治理;
12)重大危险源管理;
13)变更管理;
14)事故管理;
15)防火、防爆管理,包括禁烟管理;
16)消防管理;
17)仓库、罐区安全管理;
18)关键装置、重点部位安全管理;
19)生产设施管理,包括安全设施、特种设备等管理;
20)监视和测量设备管理;
21)安全作业管理,包括动火作业、进入受限空间作业、临时用电作业、高处作业、起重吊装作业、破土作业、断路作业、设备检维修作业、高温作业、抽堵盲板作业管理等;
22)危险化学品安全管理,包括剧毒化学品安全管理及危险化学品储存、出入库、运输、装卸等;
23)检维修管理;
24)生产设施拆除和报废管理;
25)承包商管理;
26)供应商管理;
27)职业卫生管理,包括防尘、防毒管理;
28)劳动防护用品(具)和保健品管理;
29)作业场所职业危害因素检测管理;
30)应急救援管理;
31)安全检查管理;
32)自评等。
《涂料生产企业安全生产标准化实施指南》(AQ3040-2010)
每个生产操作岗位都应编制岗位安全操作规程,至少应包括下列内容:
1.正常开、停车操作程序;
2.各种操作参数、指标的控制;
3.安全注意事项和异常处理方法;
4.事故应急处理措施;
5.紧急停车操作程序;
6.接触化学品的危险性;
7.个体安全防护措施。
仓库装卸车安全操作:
严禁在仓库(堆场)内进行卸车桶装、转(过)桶、分装等作业。
在进行卸车桶装、转(过)桶、分装等作业时,必须在仓库(堆场)外面进行,并做好防静电措施,必须有安全人员配备应急器材在场监控。
四、工作环境及危险因素
《生产过程危险和有害因素分类与代码》(GB/T13861-92)
按导致伤亡事故和职业危害的直接原因进行分类。
1、物理性危险和有害因素:
设备、设施缺陷;
防护缺陷(无防护、防护装置、设施缺陷、防护装置、设施和防护用品不符合要求、使用不当);
电危害(漏电、静电、电火花);
噪声危害(机械性噪声、电磁性噪声、流体动力性噪声);
振动危害(机械性振动、电磁性振动、流体动力性振动);
电磁辐射;
非电离辐射(包括紫外线、激光、射频辐射、超高压电场);
运动物危害(固体飞甩、液体飞溅、坠落物、反弹物、料堆(垛)滑动);
明火;
高温物质;
低温物质;
粉尘与气溶胶;
作业区环境不良(地面滑、场地狭窄、地面高低不平、场地杂乱、安全过道缺陷、采光照明不良、通风不良、空气质量不良、信号缺陷、标志缺陷等)。
2、化学性危险和有害因素:
易燃易爆性物质;
自燃性物质;
有毒物质;
腐蚀性物质。
(包含气体、液体、固体、粉尘)。
3、生物性危险和有害因素:
致病微生物;
细菌、病毒、传杂病媒介物、致害动物、致害植物等。
4、心理、生理性危险和有害因素:
负荷超限(指易引起疲劳、劳损、伤害等的负荷超限)、健康状况异常(指伤、病期)、从事禁忌作业;
心理异常(情绪异常;
冒险心理;
过度紧张);
辨识功能缺陷(感知延迟、辨识错误)。
5、行为性危险和有害因素:
指挥错误(指挥失误、违章指挥);
操作错误(误操作、违章作业);
监护失误。
《企业职工伤亡事故分类》(GB6441-86)
事故类别分为20类:
物体打击、车辆伤害、机械伤害、起重伤害、触电、淹溺、灼烫、火灾、高处坠落、坍塌、冒顶片帮、透水、放炮、火药爆炸、瓦斯爆炸、锅炉爆炸、容器爆炸、其他爆炸、中毒和窒息、其他伤害。
涂料生产主要危险场所及主要危险、危害因素
涂料生产危险场所主要有:
生产车间、原材料仓库、成品仓库及装卸场所等。
涂料生产工艺流程相对简单,涂料生产工艺操作过程中的危险、有害因素有:
火灾、爆炸、机械伤害、触电、物体打击、起重伤害、车辆伤害、接触性毒物危害、噪声危害等。
其中最主要的危险因素是火灾、爆炸危险,最主要的危害因素是毒物危害。
危险、有害物质辨识结果
根据《危险化学品名录》、《危险货物品名表》、《建筑设计防火规范》、《易制毒化学品管理条例》和《职业性接触毒物危害程度分级》《工作场所有害因素职业接触限值化学有害因素》等有关规定,涉及的危险化学品主要有易燃性物质、剧毒物质等,如甲苯、二甲苯、乙酸乙酯、乙酸丁酯、溶剂油、固化剂、稀释剂、醇酸树脂、聚氨酯固化剂、醇酸树脂清漆、硝基木器清漆、硝基底漆、聚酯树脂清漆、聚氨酯树脂清漆、TDI等,这些物质具有易燃性、刺激性、毒害性、流动性、静电聚集性、腐蚀性、挥发性和粉尘等危险特性。
工艺过程危险有害因素分析结果
各种生产工艺有不同的危险特性。
(1)乳液生产工艺:
反应在一定温度条件和常压条件性进行,生产过程为聚合反应,属于放热反应,且需要在密闭条件,其中涉及到的物质中还有剧毒物质,可能发生爆聚和沸腾。
其工艺危险度为Ⅱ级中度危险。
(2)醇酸树脂生产工艺:
本工艺过程为醇和酸的酯化反应和缩聚反应,反应条件为240℃和常压条件下进行,反应过程为放热反应。
反应过程需要通氮气。
且反应过程部分物料需要滴加,其工艺危险度为Ⅱ级中度危险。
(3)固化剂生产工艺:
固化剂生产过程为各物料的聚合过程,在生产过程中需要控制一定的温度和反应速度,且聚合反应属于放热反应,且聚合反应中加入的引发剂化学活泼性很强的过氧化物,一旦配料比控制不当,容易引起爆聚,反应器压力骤增易引起爆炸;
聚合反应热未能及时导出,如搅拌发生故障、停电、停水,由于反应釜内聚合物粘壁作用,使反应热不能导出,造成局部过热或反应釜飞温,发生爆炸。
(4)油漆生产工艺:
生产过程中属于物理混合过程,在常温常压下进行,其工艺危险为Ⅲ低度危险。
(5)稀释剂生产工艺:
稀释剂的生产为各种物料按照比例简单的混合过程,其反应条件为常温常压条件下进行,其工艺的主要危险性来源于物料的危险性。
其工艺危险度为Ⅲ级轻度危险。
(6)水性漆生产工艺:
生产过程中属于混合过程,在常温常压下进行,其工艺的主要危险性来源于物料的危险性。
设备设施危险有害因素分析结果
根据车间使用生产设备情况可知,其主要的设备设施有反应釜、分散机、各种物料泵、电动葫芦等,这些设备设施缺陷可能造成设备故障,进而造成物料泄漏等事故。
作业环境危险有害因素分析结果
根据《企业职工伤亡事故分类》(GB6441-86)和《职业病范围和职业病患者处理办法的规定》,通过对企业工艺过程、生产装置、仓库场所等生产场所危险有害因素进行分析,危险有害因素可能造成的事故有:
物体打击、车辆伤害、机械伤害、起重伤害、触电、灼烫、火灾、高处坠落、坍塌、锅炉爆炸、容器爆炸、其他爆炸、中毒和窒息、其他伤害和职业病。
生产单元
类别
详细名录
生产车间
危险因素
火灾爆炸、机械伤害、起重伤害、灼烫伤害、触电伤害、容器爆炸、化学灼伤、物体打击。
有害因素
职业中毒、粉尘危害、噪声危害、窒息
甲类乙类
仓库
火灾爆炸、机械伤害、触电伤害、车辆伤害
职业中毒
溶剂
储罐区
火灾爆炸、触电伤害、车辆伤害、物体打击
职业中毒、窒息
公用工程间
机械伤害、火灾、锅炉爆炸、容器爆炸、触电伤害、灼烫伤害
噪声危害、窒息
丙类仓库
(含TDI仓库)
火灾、触电伤害
堆场
火灾爆炸、机械伤害、触电伤害、车辆伤害、化学灼伤
五、所从事工种可能遭受的职业伤害和伤亡事故;
可能发生的事故有:
火灾、爆炸、机械伤害、触电、灼烫伤害、高空坠落、起重伤害、碰撞伤害、物料泄漏、中毒和窒息等。
发生生产事故的原因分析
在储存、运输及生产过程中所发生的各种事故,都有其必然的原因。
ﻫ
直接原因是导致事故即酿成事故的前提条件,是在基础原因和间接原因的基础上,发生事故或扩大成灾的直接诱发原因。
事故原因可归纳为如下三个方面。
ﻫ
1、物的原因(物的不安全状态)
(1)危险物质、设备处于危险状态:
如储存的危险物质(易燃液体:
甲苯、二甲苯、醋酸乙酯、醋酸丁酯等)、分散缸没盖好、储存装置的接管发生变形、破裂或阀门被打开;
造成了化学反应热或潜热的蓄积;
运转机械的零部件损坏,或仪表失灵,设备损伤;
形成了可燃物、助燃物和点火源相互作用的条件等。
(2)装置现场的设施不良:
如照明不良;
通风不良;
工具、材料不良;
装修、整修不良;
空地狭小;
地面太滑;
绝缘不良;
安装不牢固等。
(3)缺少防火、防爆安全装置和设施:
如消防、疏散、急救设施不全,或设置不当等;
压力容器没有或缺少安全阀、没有或缺少阻火器等防爆、防火安全装置等。
(4)缺少警戒设备:
如缺少自动检测报警设备;
缺少防护遮罩、防护堤;
避雷、防静电(设备、物体和人体上积累静电,其放电时便容易引燃易燃蒸气、粉尘和纤维而导致火灾爆炸。
这可根据具体情况,通过接地、连接、电离、增湿、工作人员不穿容易产生静电的工作服等一系列防静电的措施来防止。
)等设备失效;
没有安全标志或安全标志不清等。
(5)缺少保护性装具:
如防护服、眼镜、面罩、头盔、靴鞋等不齐备。
2、人的原因(人的不安全行为)
(1)操作机械、装置失误:
如操作程序、顺序有误;
操作动作错误;
岗位之间沟通、协调不够;
确认不准,甚至误认;
超负荷或带病运转等。
(2)工作态度不端正:
如注意力不集中,操作不认真;
不适当的动作、不按照安全操作规程进行操作等。
(3)误用防护设备和器具:
如不会使用或错误使用防护设备和器具;
设备、装具等管理不善,零件缺损等。
(4)监督检查不够:
如发现异常和隐患未能及时制止和整改;
不按科学办事,瞎指挥、蛮干等。
⑸ 安全教育培训不足:
没有执行三级教育,安全操作培训不足,操作不熟练等。
3、管理缺陷的原因
⑴安全生产管理机构不健全,没有配备安全生产管理人员。
⑵安全生产管理人员的不落实,管理人员的管理水平不高,安全生产知识不足。
⑶安全生产管理制度不健全,安全生产管理制度不落实、不执行。
⑷生产操作岗位的安全操作规程没有或不完善。
⑸ 安全生产教育和岗位安全知识宣传、安全操作培训不足。
特别是新员工的教育培训。
⑹安全检查没有落实,检查不到位,流于形式。
⑺检查中发现的事故隐患没有及时处理。
⑻在生产过程没有对生产人员的思想情况、人的精神状态的变化进行及时了解和掌握,并及时地进行调整。
事实上,管理上的缺陷,也是人的因素所为。
通常人的不安全行为是指操作工人所为,而管理上的缺陷则指管理人员的所为。
六、所从事工种的安全职责、操作技能及强制性标准
《涂料生产企业安全技术规程》(AQ5204-2008)
涂料生产安全
1一般规定
1.1企业应根据所生产的涂料产品编制生产工艺技术规程、安全操作规程和安全技术规程。
涂料生产应按照工艺技术规程、安全操作规程和安全技术规程执行。
工艺技术指标和中间控制指标的更改应有生产技术部门会同安全技术部门审核同意,企业负责人的批准。
1.2生产车间应根据生产需要规定原料的存放时间、地点和最高允许存放量。
相禁忌的原料不应存放在同一区域,应划定区域分类隔开或分离贮存。
生产车间的生产物料、产品、半成品的堆放,应用黄色和白色标记在地面上标出存放地点,堆放整齐,保证通道畅通。
1.3树脂生产设备、加热设备、分散设备、辅助设备(过滤机、离心机、各类泵、空气压缩机、通风机、电动葫芦)等生产设备应按照设备安全操作规程进行操作。
1.4生产含有易燃液体色漆的研磨设备应使用封闭式砂磨机,分散机(搅拌机)使用的配料缸、调漆缸、拉缸等敞开式设备应加盖防止易燃液体挥发。
1.5当生产树脂的反应釜、稀释罐(釜)等生产设备属于压力容器的,其安全附件、安全保护装置、测量调控装置及有关附属仪器应定期校验、检修,并记录。
1.6树脂生产设备(包括反应釜、稀释罐(釜)、过滤机、冷却(凝)器、放空管等)、加热设备、制漆分散设备、辅助设备(离心机、各类泵、空气压缩机、通风机、电动葫芦等)等生产设备及其所属管线及附件均应有防静电接地。
对拉缸等移动式设备及工具的静电接地连接,应采用连接器与接地支线(接地干线)相连接。
不应采用接地线与被接地体相缠绕等方法进行连接。
1.7设备在灌装、循环或搅拌等工作过程中,不应对易燃液体进行取样、测温等现场操作。
设备停止工作后,应静置一段时间才允许进行上述操作。
2色漆(清漆)生产
2.1配料
2.1.1配料时投料量应准确。
分散机开机前,料缸必须先做好防静电措施,夹好静电夹才能开机。
在搅拌机运行时,不应用手打捞容器里的杂物,避免引起机械伤害事故。
配料缸、调漆缸、拉缸等敞开式设备应加盖防止易燃液体挥发。
2.1.2 当班配料应当班研磨,未经研磨的色浆不应在车间存放。
当班配置的华兰、炭黑、甲苯胺红、铬黄(绿)等颜料的色浆不能进行研磨时,应在下班前对配好料的色浆采取防聚热措施,单独存放,以防自燃引起火灾。
2.2研磨
2.2.1应熟悉易燃液体的安全使用和设备的安全操作规程。
2.2.2轧制硝化纤维素(简称硝化棉,下同)漆片时,应使用含水量不小于25%、不含乙醇的硝化棉,并应控制炼胶机滚筒冷却水出水温度,以防自燃。
3 硝化棉溶解
3.1硝化棉溶解岗位生产作业不应使用铁器类撞击易产生火花的工具,应使用铜、铝或木质工器具等不易产生火花的工具,以防止铁器撞击产生火花引起火灾。
溶解罐等设备应采取有效防静电接地,硝化棉溶解罐周围的地面应采用不发火花的地面(如敷设铝板等),以防止静电火花引发火灾爆炸。
3.2硝化棉溶解时,配料计量应准确,应控制好加料速度,应轻拿、轻放,做到边加料边溶解,投料不应过快,以防止投料过快,使未溶硝化棉与搅拌桨摩擦产生静电起火爆炸。
3.3硝化棉要做到随用随领,剩余的生产用硝化棉应用包装盖密闭,不应在车间存放,应及时送回仓库。
4 树脂生产
4.1投料
4.1.1投料前所用的原料应检验合格,不合格的原料不允许投料。
投料计量应准确,应按工艺技术要求注意投料顺序和加料速度,轻拿轻放,防止液体物料四溅或固体粉料飞扬,保持岗位的环境卫生。
4.1.2反应釜的装料量应根据所生产树脂品种的工艺技术要求和物料性质来确定装料量,但不应大于釜体容积的70%,以防物料外溢出釜。
反应釜最低液面应高于反应釜壁的加热面,搅拌时液面应有效淹没温度仪接触点。
反应釡应导线接地,以防止加料时产生静电。
4.2 加热与温度控制
4.2.1树脂生产过程的反应温度应按生产树脂的工艺技术要求控制,不应超过所用主要原料的自燃点温度。
应定时采样测定树脂的酸值和粘度值等工艺控制指标,以防止胶化、自燃。
4.2.2发生物料溢锅时,应立即进行处理。
轻者可加适量硅油消泡剂等,降低其表面张力,使生产恢复正常。
物料溢锅严重时,应立即停止加热,降温进行处理。