LF精炼渣脱硫能力优化与循环利用Word文档下载推荐.docx
《LF精炼渣脱硫能力优化与循环利用Word文档下载推荐.docx》由会员分享,可在线阅读,更多相关《LF精炼渣脱硫能力优化与循环利用Word文档下载推荐.docx(19页珍藏版)》请在冰豆网上搜索。
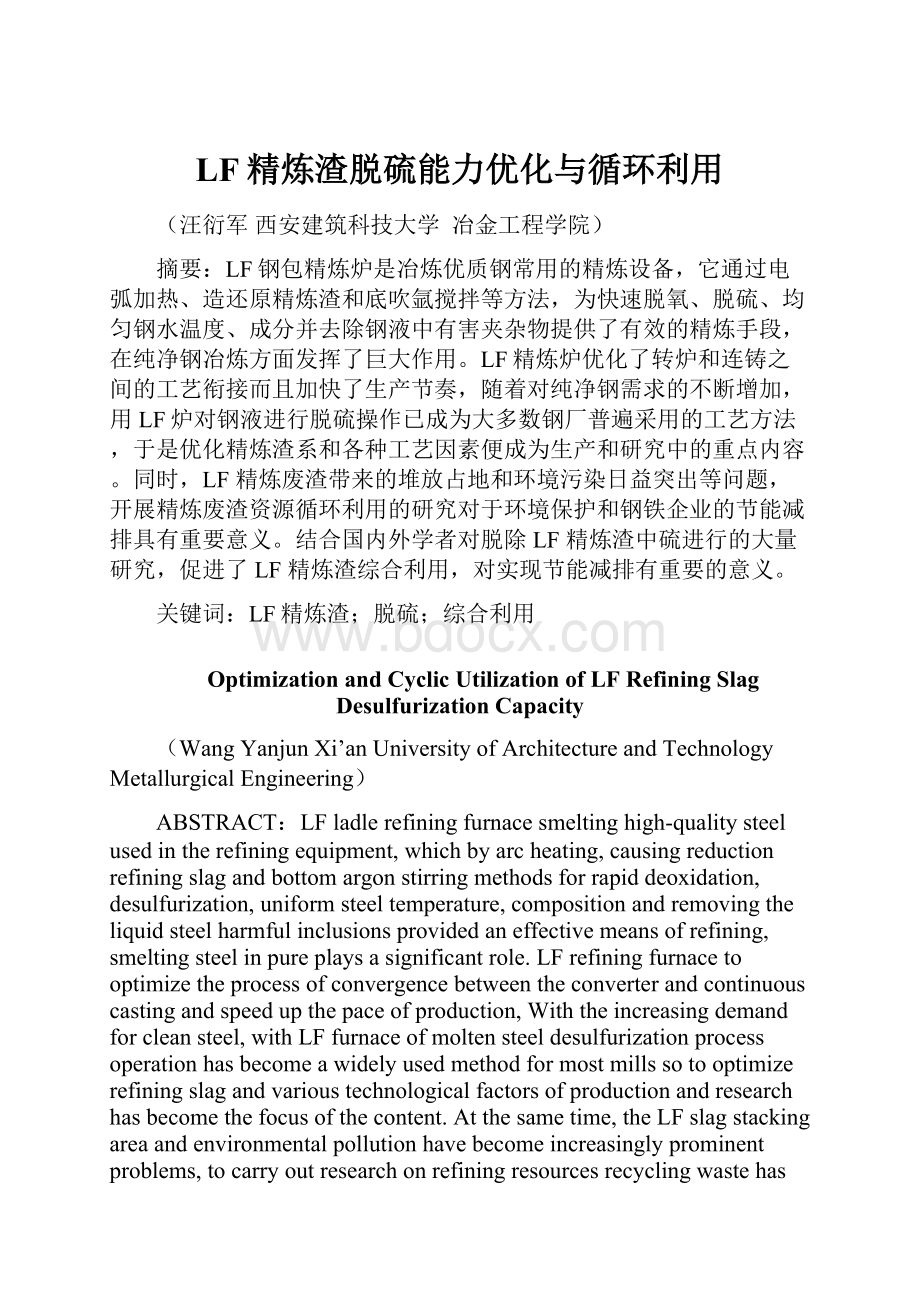
FeS的熔点为1190℃,而且在900-1200℃的温度范围内,还会形成低熔点的共晶体,这种低熔点的共晶体是应力集中点,这样,硫在铁中作用导致钢的热脆性。
γ-Fe晶界表面上形成低熔点相,但是硫在固溶体中以各种硫化物析出,从而产生晶内应力集中,这加强晶界表面上的裂纹倾向。
除对钢材的热加工性能、焊接性能、抗腐蚀性能有较大影响外,对力学性能也有影响,而且会显著降低钢材的抗氢致裂纹(HIC)的能力。
近年来开发出的一些高性能洁净钢,如管线钢、取向硅钢、汽车面板等,w(S)都要求控制在50×
10-6甚至更低的水平。
为此,通过优化LF工艺,提高精炼过程脱硫能力,可实现低硫钢的稳定生产。
LF精炼是脱硫的最有效工艺,可以达到深脱硫的目的,在铁水预处理—转炉—LF炉工艺过程中钢水硫的含量可以控制在10×
10-6~20×
10-6,好的可以控制到10×
10-6以下。
因此,研究LF脱硫精炼渣对炼钢工艺的发展具有重要意义。
脱硫的主要标准
目前,世界上许多大型钢铁企业都在努力提高自己钢材产品质量,其中大部分通过降低钢中杂质含量特别是硫含量的途径来实现的。
欧洲生产的钢材产品中大批量ω[S]≤%,小批量ω[S]≤%,少数特别优质钢ω[S]≤%。
在1994~1995年度时,欧洲70%的钢材ω[S]≤%,50%的钢材ω[S]≤%,28%的钢材ω[S]≤,10%的钢材ω[S]≤%。
我国生铁产品质量与国外工业发达国家相比,还有很大差距,生铁一级品的质量标准保持在ω[S]≤%,但即使铁水硫含量达到一级品的质量标准,对转炉炼钢来说还是偏高,炼钢过程中还要不断经过脱硫处理,这导致炼钢时渣量大、冶炼周期长、炼钢工序产量低、消耗高。
LF炉(钢包精炼炉)
LF(LadleFurnace)是1970年在日本首先发展起来的钢包型精炼炉外设备。
在70年代初期,日本大同特殊钢公司的大森厂,研究人员自己总结和消化ASEA一SKF、VOD和VAD等精炼技术方法的基础上,开发研究了LF精炼法。
LF精炼法的应用和发展极大地推动了新工艺研究开发和新钢种的生产需要,促进了世界上钢铁工业的发展和炉外精炼技术的很大进步。
虽然LF设备结构比较简单和技术容易掌握,但它拥有许多有效的炉外精炼方法,例如合成渣应用处理、合金成分调整、加热和搅拌等。
LF具有氩气搅拌、保持炉内还原气氛和合成渣精炼等独特的精炼功能,不但可以为连铸稳定持续的提供温度成分准确均匀钢水和协调缓和转炉或电炉炼钢与连铸节奏,还可开发特殊合金含量较高的新钢种。
其中LF合成渣精炼可以更好完成脱硫、脱氧、去除有害夹杂物的作用。
影响LF脱硫的主要因素
a.炉渣成分:
炉渣碱度的和CaO含量;
Al2O3含量;
SiO2的含量;
CaF2的含量;
MgO含量;
BaO的含量;
不稳定氧化物;
b.炉渣物理性质:
炉渣黏度和其他物理性质;
炉渣熔化温度;
c.冶炼工艺条件:
LF操作温度;
渣量;
钢中全氧量;
底部吹氩搅拌;
总的来说,由于炉渣成分、物理性质、冶炼工艺条件等在一定程度上影响了脱硫过程过程热力学和反应动力学。
导致LF精炼时石灰消耗量过大且不稳定,且由于氩气流量控制未经优化,渣中氧化铁含量偏高且不稳定等。
本文通过对生产现场收集到的大量原始数据进行计算、分析。
力求找出各工艺因素对脱硫影响的特征,得出优化结果、稳定脱硫工艺。
LF精炼产生大量固废
LF精炼工艺可以冶炼出优质的低硫钢,然而随着我国LF精炼工艺的快速发展,每年产生的LF精炼废渣大约为1500万t,LF精炼废渣中含有大量的CaO,SiO2,Al2O3和MgO等物质,这些组分和冶金生产中使用的部分原料成分相近。
如果这些有效组分可以加以利用,不但能够提高LF精炼废渣的循环利用率,还可以节约资源、缩短冶炼时间。
目前,大多数钢铁企业选择将精炼废渣和普通转炉渣混在一起,用于铺路和生产水泥,该方式利用价值低,造成了资源的浪费。
同高炉渣和转炉渣相比,精炼渣的利用率较低,LF精炼渣的碱度高、硬度大,不能像转炉钢渣那样可以回收含铁的原料;
且由于渣中CaO活性较高和自由CaO的水化活性较低等原因,容易引起LF精炼渣的体积膨胀,所以不能大量用于建筑材料和水泥的生产。
研究表明,LF精炼后的废渣仍具有一定的硫容量,而实践证明,只有当废渣的硫容量小于时,废渣才表现出脱硫速率较慢的现象。
针对LF精炼渣循环利用出现的很多问题,有必要进一步开展LF精炼渣的高效循环利用研究。
LF固态精炼炉弃渣在结晶凝固过程中形成不同的矿物组织、将其中的有益部分用于炼钢生产,是规模化利用LF精炼炉弃渣潜在价值的有效途径。
2精炼渣系综述
目前常用的精炼渣渣系
迄今为止,人们已经研究了很多种精炼渣渣系,其中应用最为广泛的要数Ca0基合成渣,这是由于Ca0自身具有很强的脱硫能力,而且其原料非常丰富,价格低廉。
Ca0基渣系有以下几种:
渣系
Ca0-CaF2渣系在1500℃下的硫容量可以高达,具有很强的脱氧、脱硫能力,其硫容量在二元渣系中是最高的。
在Ca0-CaF2渣系中,CaF2的主要作用是改善渣的流动性,降低渣的熔点,增大脱硫产物的扩散速度,改善脱硫动力学条件。
成渣中Ca0与CaF2的比例要适当,比值若过高,则渣中Ca0含量较高,使合成渣熔点过高,流动性较差,从而影响精炼效果;
比值过低,则渣中CaF2含量较高,对Ca0起了稀释作用,不利于脱硫。
但是由于在这种渣系中CaF2含量相对较高,对炉衬侵蚀严重,同时这种渣系粘度较小,不利于埋弧操作,导致电弧对包衬的辐射侵蚀。
此外CaF2还会与渣中其它组元反应,生成含氟气体对污染环境。
OguchS等人测定了Ca0-A1203-CaF2渣系在1550℃时的硫含量,结果表明,渣中的硫含量主要取决于Ca0/A1203的大小,而CaF2含量对其影响很小。
当Ca0/A1203的比值增加,lgKs(渣中硫含量)显著增加。
由于原料中不可避免会带入部分Si02,因而Cad-Al203-CaF2渣系实际上为Ca0-A1203-CaF2-Si02四元渣系。
对该渣系进行研究后得出w(Ca0)/w(Si02)大于后,脱硫效果比较理想。
Ca0-Si02-Mg0-A1203渣系是当前应用最为广泛也最常见的精炼渣系。
实验研究表明当R<
时,随着碱度增加,LS随之增加,而当R>
时,若再继续增加碱度R反而下降。
提高渣中Ca0的含量,可以显著降低钢中的硫含量,但当(Ca0%)>
60%后,由于Ca0含量过高,增大了炉渣粘度,使流动性变差,脱硫效果反而会降低,不利于脱硫。
Ca0-A1203渣系实际上是Ca0-A1203-Si02渣系,也具有很强的脱氧、脱硫能力。
实验结果表明,随着Ca0/A1203值增大CaS的饱和溶解度也随着增大。
Ca0-Al203脱硫渣的成本昂贵,为了降低成本,前苏联研究了用石灰石—粘土砖或者石灰高岭土渣代替CaO-A1203合成渣,并进行了相关的工业实验。
结果表明,用石灰石—粘土砖渣洗的钢与用Ca0-A1203渣洗的钢相比,脱硫率都在50%-70%左右,高的可达80%。
该渣系吸收夹杂能力强,不含氟,适应环保的要求。
文献表明,该渣系的脱硫率可以维持在70%以上,同时也可以应用于超低硫钢的冶炼。
多用于铝镇静钢,取代CaO-CaF2渣系,可减弱高含量CaF2的危害;
维持较高的CaO/Al2O3对也能具有良好的脱硫能力,研究认为,钙铝酸盐与钙硅酸盐相比,对硫的吸收速度和硫化物的允许容量更大;
对夹杂物吸收能力强于CaO-CaF2渣系,生成C12A7低熔点夹杂易于上浮排除;
实际生产中充分发挥好CaO-Al2O3渣系的脱硫和去夹杂能力关键在于控制渣中较低的SiO2。
国外LF精炼渣的特点是高碱度(有时渣中的Ca0含量高达65%),并能获得较好的精炼效果;
而国内普遍采用的是中(R=,低(R=水平碱度的精炼渣,在这种碱度范围内,也同样显著提高了钢液的质量。
实验中发现,碱度越高反而越不易于脱硫,一般将碱度控制在之间,硫的分配比较高,精炼结束时可达到80以上。
据相关文献介绍渣的碱度控制在时熔渣具有最强的脱硫能力,碱度过高,渣中的Ca0会使流动性变差,不利于生成的(CaS)在渣中扩散。
渣指数(=Ca0/Si02:
A1203比值)反映了精炼渣在一定的碱度下,炉渣的流动性。
研究表明,当渣指数为时,硫的分配比超过80。
精炼渣的主要成分和作用
表1精炼渣的主要成分和作用
精炼渣白渣理论
精炼渣的基础渣一般多选CaO-SiO2-Al2O3系三元相图的低熔点位置的渣系。
基础渣最重要的作用是控制渣的碱度,而渣的碱度对精炼过程的脱氧脱硫均有较大影响。
碱度提高可使钢中平衡氧降低。
精炼渣可以利用白渣(不加脱氧剂)精炼,达到降低钢中氧、硫和夹杂物含量的目的;
也可以在钢中加入脱氧剂,如铝粒、Si-Fe、RE等,提高渣的精炼能力;
熔渣碱度和氧化性是熔渣的重要指标。
熔渣的碱度表示它去除钢液中硫、磷的能力,同时保证炉渣对钢包炉衬的化学侵蚀性最低。
熔渣的氧化性高低取决于渣中最不稳定的氧化物-氧化铁活度(αFeO)的高低。
熔渣的碱度对αFeO数值的影响起着重要的调整作用。
当w(FeO+MnO)<
%时,还原很充分,很利于反应进行。
由于钢渣之间的扩散关系,氧在钢渣间存在着平衡分配关系。
但在初炼时期两者并没有立即平衡,需要搅拌和反应时间。
通过钢渣接触、氩气搅拌,钢中[Al]也直接同渣中的(FeO)起反应。
更有效的办法是将颗粒状的Al粒直接加到渣中,直接降低(FeO)。
硫的分配比与精炼渣中(FeO+MnO)成反比关系,即随着(FeO+MnO)含量的提高,硫的分配比降低,对炉渣脱硫不利。
因此要求合成精炼渣中还原性要强,(FeO+MnO)的含量应控制在%以下。
设计精炼渣的基本原则
(1)要有较高的硫容量
(2)(FeO+MnO)含量低,具有强还原性
(3)P2O5应尽量低
(4)必须有较好的流动性,即合适的熔点及粘度
(5)吸收非金属夹杂物能力强
(6)有较好的绝热性能
(7)对包衬耐火材料侵蚀轻微即要求有良好的泡沫渣
(8)有一定的比电导,在加热时可以埋弧工作
钢包炉(LF)精炼用渣的功能和配制
钢包精炼炉已成为现代化钢铁生产短流程中不可缺少的一道工序。
在世界钢包精炼装置中,钢包炉(LadleFurnace2LF)约占%。
LF除了采用还原气氛埋弧加热、真空脱气、透气砖吹氩搅拌等3项二次精炼较成熟的技术外,还引用了合成渣精炼技术,因此,LF用精炼渣的研究日益受到广泛重视。
LF精炼渣的基本功能为:
(1)深脱硫;
(2)深脱氧;
(3)起泡埋弧;
(4)可去除钢中非金属夹杂物,净化钢液;
(5)改变夹杂物的形态;
(6)防止钢液二次氧化和保温作用。
LF精炼渣根据其功能由基础渣、脱硫剂、还原剂、发泡剂和助熔剂等部分组成。
渣的熔点一般控制在1300~1450℃,渣1500℃的粘度一般控制在~·
s。
精炼渣的基础渣一般多选CaO-2SiO2-2Al2O3系三元相图的低熔点位置的渣系。
基础渣最重要的作用是控制渣的碱度,而渣的碱度对精炼过程脱氧、脱硫均有较大的影响。
提高渣的碱度可使钢中平衡氧降低,而且可提高硫在渣钢之间的分配比,即利于脱氧和脱硫。
但是,精炼渣的碱度也不能过大,如果碱度过大,例如大于5,精炼渣熔化困难,渣的粘度过大,流动性不好,也将影响脱氧和脱硫效果。
通常精炼渣分为高碱度渣和低碱度渣,一般碱度(CaO/SiO2)大于2为高碱度渣,高碱度渣适用于一般铝镇静钢二次精炼,在钢水脱硫等方面具有较好的效果。
对于具有特殊要求的钢种,如帘线钢、钢丝绳钢、轴承钢等,需采用低碱度渣,例如碱度在1左右的中性渣。
在这些钢中,为了避免在脱氧过程中生成过多氧化铝夹杂,大多采用Si2Mn脱氧,采用中性精炼渣、甚至于酸性渣,精炼后形成较低熔点的圆形或椭圆形复合夹杂物,在加工时可以变形,危害较小。
精炼渣可以利用白渣(不加脱氧剂)精炼,达到降低钢中氧、硫及夹杂物含量的目的;
也可以在渣中加入脱氧剂,如Al粒、Si2Fe、RE等,提高渣的精炼能力;
还可以在渣中加入硅钙合金等,清除镇静钢中Si或Al脱氧后的产物,即将单一的脱氧固态产物改变成复合低熔点液态夹杂,渣中Ca发生下列反应:
X[Ca]+YAl2O3(s)=[X(CaO)·
(Y-1Π3X)Al2O3](s)+2Π3X[Al]
生成的铝酸盐夹杂浮出钢液,达到Al2O3变性处理的目的。
精炼渣的脱硫反应受渣中FeO+MnO含量的影响很大,它与硫分配常数K的关系见图3。
因此,精炼渣中MnO、FeO要尽量的低。
配制精炼渣常用的基础渣原料、脱硫剂、发泡剂、还原剂、助熔剂及其作用见表1。
精炼渣通常有粉剂和颗粒状剂。
粉剂多为机械混合物,使用过程中粉尘大。
颗粒状剂加入钢包时,不会产生粉尘飞扬而污染环境和使物料损失。
另外,颗粒状物料流动性好,可以迅速在钢水表面形成覆盖层。
目前有的连铸生产线LF精炼时间不允许太长,为了使精炼渣加入钢包后快速均匀熔化,以缩短精炼时间,也常常采用预熔型精炼渣,但成本有所提高。
3精炼过程脱硫热力学及动力学分析
钢液脱硫的热力学
渣-钢间的脱硫反应渣-金属间脱硫反应,根据炉渣的分子理论,可以用下式表示:
[S]+(CaO)=(CaS)+[O]lgKCaS=lgaCaSaO/aSaCaO=-5650/T+
考虑一般情况下渣中的成分是以离子状态存在,也可表示为:
[S]+(O2-)=[O]+(S2-)
式中as,ao——用质量分数计算的金属液中硫和氧的亨利活度;
aCaS,aCaO——以纯固体状态作为基准的活度,用摩尔分数表示。
由反应式可知,渣中的CaO(O2-)的活度越大,CaS(S2-)的活度越小,且钢水中的氧含量低,硫的活度大一些,脱硫反应易于进行。
选择碱度高且硫溶解度大的渣,保持渣金反应体系低的氧位,以利于进行金属液的脱硫。
氧含量低,[C]和[Si]含量高的铁水,与钢水相比易与脱硫,这正是铁水预处理脱硫的优势所在。
为了生产低硫钢,必须做到铁水脱硫后的渣不能进入下一工序的炼钢炉内,需要进行扒渣处理铁水,由于前一工序的渣子混入在某种程度上不可避免,因此还需在钢包精炼中进行钢水脱硫。
图所示,表示了各种渣共存条件下的钢水成分和硫的浓度的平衡关系。
碳含量高的铁水中硫的平衡浓度低,可知铁水脱硫是有效的。
钢水条件下,铝镇静钢的石灰饱和(aCaO=1)的CaO-Al2O3渣中的平衡硫浓度最低。
这是钢包精炼法脱硫之所以对铝镇静钢使用CaO-Al2O3系渣的主要原因。
炉渣的脱硫能力一般用硫在渣-金属间的分配比(LS=ω(S)/ω[S])表示。
在脱硫操作中要求由分配比大的渣组成。
为了推算分配比,必须求出渣中成分的活度。
因为实际测量渣中各成分的活度比较困难,引入硫容量(CS)来表示炉渣脱硫能力的指标。
在硫分配比和硫容量之间,存在以下关系:
lgLS=lgCS+lgƒS-lgaO-465/T-964
为了用少量的渣制造极低硫钢,要选择硫容量大的渣系,进行强脱氧,并在高温下进行脱硫。
实际操作中钢包精炼后的LS值比热力学计算预测值低得多。
原因是从气体和耐火材料中供氧,钢水中的氧活度增高。
钢包精炼中为了有效地进行脱硫,保持惰性气氛和耐火材料中低的氧位是重要的。
具体地来说,希望是真空或者氩气气氛,而且采用碱性氧化物作为钢包耐火材料。
脱硫反应动力学
采用CaO基精炼渣对钢水脱硫,其反应可用如下方程式表示:
(CaO)+[S]=(CaS)+[O]
(O2-)+[S]=(S2-)+[O]
由脱硫反应知,LF精炼过程中脱硫反应的限制性环节为硫和氧在钢中的传质过程。
但是由于氧在钢液中的扩散系数比硫高出一个数量级,即氧在钢中的传质速度比硫快几十倍,不对硫的传质形成限制,所以硫的传质是脱硫的限制性环节。
吹氩搅拌可改善炉内脱硫动力学条件,增加渣-钢界面接触面积,促进硫在渣钢中的传质,提高界面反应速度,强化还原精炼进程。
LF精炼过程中炉内传质方程用下式所示:
式中J为物质扩散通量,A为渣-钢接触面积,D为物质扩散系数;
δ为边界层厚度;
为物质浓度梯度。
可知看到,增大渣-钢界面的接触面积A,减小边界层厚度δ及增大浓度梯度,均可增大物质扩散通量,提高物质扩散速度,促进反应进行。
LF精炼过程中的吹氩搅拌可极大改善上述动力学参数,强化反应动力学条件,提高还原精炼效率。
炉渣脱硫是降低钢中硫含量使之达到规格的主要手段。
炉渣脱硫的热力学条件是:
炉渣碱度,渣中不稳定氧化物的含量,以及渣料和温度。
一般情况下,碱度越高,渣中不稳定氧化物含量越低,越有利于脱硫。
炉渣脱硫的动力学条件是:
渣与钢接触面积的大小有关,以及反应物和产物在钢和渣中的传质速度。
一般情况下,搅拌钢液可以使上述动力学条件得到改善。
4LF精炼渣脱硫工艺优化方法与精炼渣循环利用
攀钢LF精炼渣脱硫工艺优化
攀钢目前有5座LF,之前在生产过程中主要承担加热升温和调整合金成分任务。
由于对脱硫、去除夹杂等功能考虑较少,LF造渣工艺相对简单,主要考虑其埋弧效果。
而要发挥其脱硫功能,造渣工艺存在以下不足:
1)造渣过程未加入还原剂,钢包渣氧化性偏高;
2)渣量仅保证基本埋弧加热要求,加入量较小;
3)渣料种类单一,未对钢包渣成分进行准确控制。
为此,对LF精炼过程脱硫的工艺进行了以下改进。
开发还原剂
为提高LF的脱硫效果,在转炉出钢过程和LF工序加入钢包渣还原材料,来降低钢包渣氧化性,形成白渣精炼。
为此,开发出含铝的钢水调渣剂和含CaC2的复合精炼渣,其理化指标分别见表2和表3,用于对不同钢种的钢包渣进行改性处理,以达到白渣精炼的目的。
针对含铝钢种,在LF处理前加入10~20kg铝粒,来进一步降低钢包渣的氧化性。
表2调渣剂化学成分(%)
表3复合精炼渣理化指标
提高钢包渣碱度
根据图2的分析,将LF钢包渣碱度控制在7左右,可获得较高的脱硫能力。
为此,通过在出钢过程中向钢包内加入活性石灰和萤石,以及在LF处理过程增加高碱度渣料的加入,控制钢包渣中w(CaO)=55%~65%,w(SiO2)≈10%,将碱度控制在较高区间。
为保证在钢包渣碱度提高的情况下,炉渣熔化良好,LF高碱度渣料采用多批次少量加入的方式,并加入少量萤石,渣料加入后确保足够的加热化渣时间和吹氩搅拌时间,以保证其脱硫效果。
控制钢包渣Al2O3含量
在冶炼低硫钢时,通过加入铝粒和调渣剂来调整钢包渣中的Al2O3含量。
在每批次加入了高碱度渣料后,均对应加入10%左右的调渣剂8%左右的铝粒,来调整钢包渣的氧化性和渣中的Al2O3含量。
过程控制及吹氩操作
LF在处理开始,先采用大流量吹氩方式吹开表面的渣层,加入第1。
随后采用高供电档位进行化渣,化渣期间适当调低吹氩流量,并加入第1批铝粒,确保高碱度的钢包渣熔化良好。