13龙川135MW机组调节保安系统调试措施Word格式.docx
《13龙川135MW机组调节保安系统调试措施Word格式.docx》由会员分享,可在线阅读,更多相关《13龙川135MW机组调节保安系统调试措施Word格式.docx(63页珍藏版)》请在冰豆网上搜索。
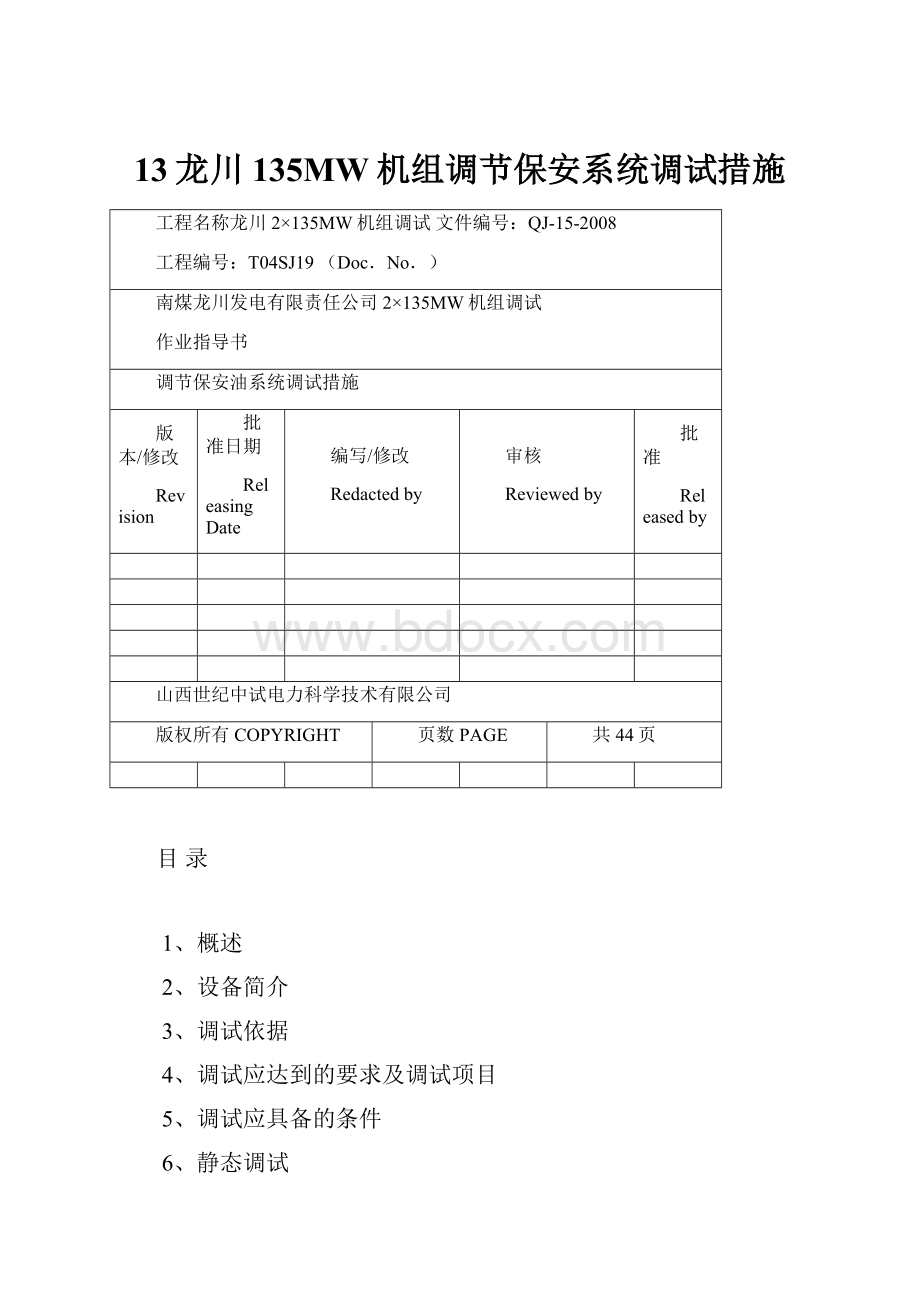
名称
功率kW
电压V
频率Hz
电流A
数量
流量L/min
主油泵
30
380
50
60
2
100
电加热器
3
15
蓄能器
2*10L
10MPa
抗燃油系统参数:
工作介质
三芳基磷酸酯抗燃油
EH系统油压
14.0±
0.5
MPa
工作油泵
工作温度
35-45
℃
油箱油位
500-730
mm
过滤器压降
<
0.35
冷却水压力
0.3
油箱有效容积
900
L
2.6调节系统性能指标
2.6.1转速控制精度:
≤3r/min
2.6.2负荷控制精度
2.6.2.1稳态误差:
<
0.25%ECR
2.6.2.2动态误差:
3%
2.6.2.3振荡:
在与5至8个振幅之后动态误差小于1%
2.6.2.4限制频率影响的死区:
可调(典型+/20mHz)
2.6.2.5限制频率影响:
可调(典型+0.5Hz)
2.6.2.6响应的滞后时间:
滞后时间小于等于100ms
2.6.2.7控制阀的响应时间(开到关):
偏差<
25%时为1.5s
快关方式:
150~200ms
2.6.3主汽门、调汽门关闭时间:
小于300ms
3调试依据
3.1《电力建设施工及验收技术规范》
3.2《火电施工质量检验及评定标准》
3.3《火电工程整套试运质量检验及评定标准》
3.4合同及制造厂技术文件
3.5上汽提供调试指导文件
3.6设备设计制造依据的相关标准
3.7油清洁度检验ISO4460标准
4调试应达到的要求及调试项目
4.1调试应达到的要求
4.1.1检查系统设备的设计,符合合同的要求。
4.1.2检查系统设备的安装质量,符合设计图纸及制造厂技术文件的要求。
4.1.3试验调整及检查调节、保安、油系统各设备部件的特性,符合制造厂的要求。
4.1.4抗燃油系统油循环冲洗符合油清洁度检验标准要求。
4.1.5DEH系统工作性能正常,可保证机组安全经济运行;
。
4.1.6根据调试结果,对本机调节保安系统的性能作出全面的评价。
并作为机组正常运行维持的依据。
4.2调试项目
序号
项目
内容
结果
时间
备注
1
系统检查
根据流程图进行
系统清洗
油箱管路人工清理
油系统循环
清洁度检查
系统严密性
部件出厂压力试验
管路工作压力试验
油箱注油检查
4
电气调试
电气回路调试
电气马达试转调试
5
热控调试
测量及热控信号
联锁保护回路
功能组调试
自动调节回路
6
油系统设备部件单体调试
液压控制阀
手动门检查
安全门
再生油泵
循环泵
7
热控系统试验
信号、联锁试验
功能功试验
8
抗燃油系统
调整
系统油压调整
蓄能器投运
油系统工作性能检查
9
汽门伺服阀单体试验调整
主汽门控制器
调汽门控制器
10
调节保安系统静止试验
启动装置试验
掉闸系统试验
主、调汽门关闭时间测定
特性曲线测定
控制回路参数整定
11
机组空负荷下的试验
控制参数优化
超速试验
汽门严密性试验
12
机组带负荷下的试验
调节系统各控制回路投运检查
自动试验装置试验
甩负荷试验
CCS系统投运试验
13
油系统运行
设备切换
系统维护
5调试应具备的条件
5.1抗燃油系统有关设备及部件及主汽门、调汽门控制器各部件出厂试验合格,抗燃油系统组装试验试运正常,各汽门伺服阀出厂调试合格,有关技术文件齐全。
5.2抗燃油供油单元安装工作结束,验收合格,管路系统连接正确,布置合理,工艺符合厂家要求。
5.3系统循环冲洗油质化验合格,各转动机械分步试运结束。
5.4系统管路,设备部件清理工作结束,检查符合要求。
5.5I∝C系统有关信号,表计及联锁保护调试工作结束。
5.6安装现场清理工作结束,现场有关条件满足调试要求。
5.7调试仪器准备齐全,各表计经校验合格,测试仪器精度满足要求。
5.8已制定调试安全防范措施,可确保人身、设备安全
6静态调试
6.1抗燃油系统调试
6.1.1单体调试
6.1.1.1主油泵调试
操作步骤
要求
测试记录
准备
a.用补油设备经滤网向油箱补油,至高油油位。
b.蓄能器流入合格氮汽至正常压力(10MPa)。
c.系统操作检查,开启系统截止阀(压力释放阀至最低压力位置)。
a.油型号、油质符合要求
b.油位指示正确
a.补油量
b.蓄能器充入
压力
油泵空载运行
a.启动油泵,空载运行
b.进行系统排空及检查
c.连续试运30min
a.运行正常
b.无刺耳的噪音
c.无系统泄漏
d.油箱远过多汽泡
见附表1
保持5MPa
油泵升压试验
a.调整释放阀,逐渐分档升压
b.每档变化2-3Mpa,每档运行10min
c.直到调整释放阀至压力17MPa
d.稳定压力运行30min
e.必要时进行滤网清理
a.承上
b.限制油液温升在允许规定值内
c.控制滤网差压不超限
见附表2
调整油压
调整泵出口压力调整阀,使泵出口压力维持在额定范围内
油量变化试验调整
a.必要时投入冷却系统
b.进行原出口压力—流量控制阀的调整
b.泵不得过负荷
c.泵流量平稳
d.控制阀按厂家要求调整
6.1.1.2冷却再生泵及系统
泵试运检查
a.再生装置旁路门开启
b.启动
c.泵运行检查
b.无刺耳噪声
分别启动
转向正确无异音
风机电流
系统调试
a.安全阀整定
b.再生装置投运
c.进行检查清理
a.安全阀动作压力正常
b.再生装置工作正常
6.1.1.3液压阀
安全阀压力限制阀整定
a.至各阀门控制阀油路关闭。
b.按厂家要求,对系统安全阀及压力限制阀进行逐级逐路调整。
c.升压过程中,注意油泵工作应正常,系统严密性检查。
a.动作值,回座值。
b.系统严密性良好。
c.注意设备人身安全。
各控制阀动作压力回座压力。
6.1.1.4蓄能器
蓄能器充(补)氮及严密性检查
a.用专业充氮装置充气,在压力0.2MPa以下,应缓慢充入,并停留检查
b.压力达0.2MPa后,可适当加快速度充气,边充氮边切换观察氮气压力,充压至5MPa后,停留检查,并进行排汽试验。
c.充氮至10MPa。
d.充完后检查接头处严密。
e.严密性检查。
a.充氮时,操作要平稳。
b.压力超过规定值,应放气。
c.必要时,再进一步充气。
d.24h后及一周后检查严密性,符合厂家要求。
初始氮气压力24小时后压力,一周后压力。
注油
a.关回油,开进油门向系统注油,并进行排空。
b.当油侧压力达到充氮压力,关闭注油门,停油泵,进行严密性试验。
严密性符合厂家要求。
内部气压检查
a.关进油门,缓慢开启回油门,油压将逐渐下降。
b.当油压到某一值时,油压会迅速下降,此时油压值可间接反映氮气压力值。
c.当氮气压力不足时应补氮气并查明原因。
要求充氮气运行后,氢气压力应无明显变化。
a.原充气压力
b.检查试验压力
6.1.2控制油系统试运
控制油系统投运
各控制器通油
a.逐一开供中控制器供油门,进行检查。
b.注意系统严密性。
a.系统无泄油。
b.通油后压力无明显变化。
a.通油前后系统压力。
b.通油前后油箱油位。
ΔP=
ΔL=
蓄能器投运试验
a.投运前检查蓄能器油压。
b.开启各蓄能供油阀。
c.蓄能器投入运行。
d.开油泵,检查系统压力变化。
e.蓄能器充放油清洗数次。
f.蓄能器内部气压检查。
a.蓄能器工作正常。
b.停泵5分钟,系统压力在允许范围内。
c.内部气压正常。
a.投入前后油位变化。
b.内部压力
c.停泵后,系统压力变化过程。
见附
表3
系统试验调整
调整各油泵释放阀使系统油压至14MPa
调整后,把锁母锁死。
调整后压力
P0=
系统动态性能测试
a.分别在蓄能器投/退下进行。
b.调节、保安系统试验时进行。
a.系统油压变化范围正常。
b.油位正常。
详见调节保安系统试验
同左
系统运行维护
a.调试过程中持续检查。
b.投运后定期检查。
—油泵启停前后
—运行定时巡检
a.系统油位保持正常。
b.油系统无泄漏。
油滤网
a.系统调试过程持续检查清理。
b.投运后的定期检查和清理。
—运行巡回检查
—滤网差压偏大时进行清理。
c.利用停机机会,进行滤网内部检查。
a.保持滤网差压在正常范围。
b.滤网无堵塞、破损。
油质
a.油箱补油前及试运各阶段进行油质化验。
b.系统调试过程中持续进行油的外观检查。
c.系统正常投运后定期进行外观检查。
a.油质清澈透明。
b.各阶段化验油质稳定。
充气压
力检查
a.蓄能器充油前后检查。
b.运行期间定期检查。
c.系统停运后检查。
a.充气压力无明显变化。
b.检查时排进蓄能器充油。
蓄能器汽压
切换
a.系统滤网压差大时进行切换。
b.试运期定期切换。
a.切换过程系统油压正常。
b.严防因逆止门不严和拒动引起系统倒油。
切换前后压力
循环冷却油泵
同上
运行参数测试
a.系统投运前后。
b.稳定运行定期记录。
按附表3进行
6.2静止状态下调节保安系统试验调整
6.2.1汽门控制器特性试验调整
试验步骤
记录测试
准
备
及
条
件
a.油系统投运。
b.油系统检查。
系统工作正常,油温油压符合要求。
仪器准备
a.试验传感器安装。
b.试验仪器准备。
a.校验工作完毕。
b.仪器试验正常。
热控回路检查
a.控制回路。
b.跳闸系统回路。
a.调试工作完毕。
b.调试记录齐全。
设备情况检查
a.安装情况。
b.出厂试验情况。
a.安装、记录齐全。
b.出厂记录齐全。
表5
部件检查
各电磁阀检查
a.电磁阀名称、型号
b.带电操作,揭开防尘盖检查动作情况。
a.符合设计要求
b.回路正确,行程正常。
用小杆检查行程
伺服阀
检查
a.各伺服阀处于断油状态。
b.伺服阀名称、型式。
按厂家要求检查,符合设计要求。
用多功能测量仪器检查。
调
门
控
制
器
试
验
整
静态特性调整
a.油系统投入
b.掉闸电磁阀断电
c从电调阀位控制单元加模拟电压信号进行试验
d.当输入信号断路时,调整电液伺服阀,使调门刚开,测量调整反馈信号应与“0”位值对应。
e.输入信号从“0”开始,每变化5%,进行测量
f.进行反馈信号调整,使特性满足设计要求
a.油系统运行正常
b.各调门同时断电
c.信号测量装置精度满足要求
d.阀门行程符合设计值
e.阀门特性符合设计要求
a.系统油压油温
b.输入信号
c.反馈信号
d.阀门行程
表6
关闭时间整定
a.1#跳闸电磁阀动作时间
—全开调汽门
—使1#跳闸电磁阀失电,调汽门关闭
b.2#跳闸电磁阀动作试验
c.1#、2#跳闸电磁阀动作试验
d.通过调整关闭时间节流孔使关闭时间符合要求。
a.蓄能器投运
b.关闭过程平稳
c.关闭时间符合要求
d.动态记录仪记录
a.电磁阀动作信号
b.调门开度
c.时间
附表7
节
开关响应试验
a.给定阀位开关阶跃扰动信号
b.进行调门全开、全关试验
c.测量动态特性
d.求取动态参数
a.信号变化]幅度符合要求
b.开关时间1.5±
0.1S
c.动态记录仪记录
a.扰动信号
b.时间
c.阀门开度
附表9
性能测试
小幅扰动响应试验
a.给定阀位阶跃扰动信号范围
b.连续扰动数次
c.测取动态特性
a.扰动幅度10%
b.动态参数符合要求
附表10
主
汽
阀
控制阀开关特性调整
a.开启主汽门
b.进行开关接点整定
c.开关数次排空,并检查开关信号状态
a.主汽阀开关平稳,无冲击
b.开关信号状态正确
c.操作过程各掉闸电磁阀应在联锁状态
a.各主汽阀行程
b.开关状态信号
a.1#跳闸电磁阀动作时间;
→全开主汽门;
→使1#跳闸电磁阀失电,主汽门关闭
b.主汽门开度
附表8
控制器性能检查
a.导向阀通、断电,
b.进行阀门全开、全关试验
c.测量动态特性,求取动态参数
a.开关时间1.5—15S
b.动态记录仪记录
a.导向阀开、关信号
b.主汽门开动及时间
6.2.2调节保安系统静止试验
测试
工
作
油系统
a.启动油系统,进行系统循环
b.全面检查系统,正常
油质、油压、油温正常,油系统工作稳定
油温、油压、油位
控制回路检查
a.进行系统检查,有关回路送电
b.模拟试验条件准备就绪
a.热工仪表,信号正确
b.回路工作正常
c.模拟方法正确
测量仪器
投入测量就绪
工作
启
动
装
置
功
能
功能初步检查
a.利用启动装置进行主汽阀、调汽门开关试验
b.开关数次,检查系统可靠性
a.动作顺序正确
b.状态反馈正确
c.调节、保安系统工作稳定
启动装置自动升降试验
a.按启动装置自动
b.自动升过程完成,主跳闸回路复位,各ESV、CV阀、跳闸电磁阀复位,ESV、CV阀开启。
c.自动降过程完成,EV、ESV关闭,CV、ESV阀跳闸阀跳闸,主跳闸回路掉闸
b.动作点符合要求
c.动作过程符合要求
a.启劝装置实际动作点
b.动作时间
附表11
特
性
关
系
定
汽机调节器与启动装置关系
a.抗燃油系统停用
b.调节器下限期作点调整
—启动装置
—调整调节器输出
c.调节器上限工作点调整
—给定启动装置定值
d.特性关系测定
—启动装置从0%开始,每变化5%,测量一次试验参数至启动装置100%
—反向操作,至启动装置至40%,绘制特性曲线
a.上、下限工作点符合设计要求
b.特性关系线性度良好
a.启动装置信号
b.调节器输出
附表12
阀门行程与汽机调节器关系
a.启动抗燃油系统
b.用启动装置控制汽机调节器输出信号
c.各阀门零位同步调整;
→当调节器输出为时,高调门开始开启;
→当调节器输出为%时,中调门开始开启
d.各阀门全开位置调整;
→当调节器为%中调门全开→当调节器为%高调门全开
e.特性线拐点检查
f.特性关系测定
—调节器输出-10%开始每变化5—10%(同时测拐点值)直到输出至最大值
—反向操作至调节器输出-10%
g.绘制特性曲线
a.各高调门同步
b.各中调门则步
c.特性关系符合设计要求
a.调节器调出
b.各调门行程
附表13
启动装置特性试验
测取汽机调节自各调门行程与启动装置关系
a.特性关系测定
b.启动装置从0%开始每变化5%,进行记录,直至启动装置100%,反向操动至启动装置40%
c.绘制特性曲线
特性关系
a.启动装置位置
b.调节再输出
c.各调门行程
附表14
保
安
统
跳闸系统跳闸试验
a.1#跳闸通道试验
b.2#跳闸通道试验
c.1#、2#通道跳闸试验
a.汽门动作正确
b.信号状态正确
a.动作情况
b.状态信号
跳闸系统失电试验
a.单供电回路失电
b.双供电回路失电
a.单回路汽门不动作
b.双回路汽门不动作
保护信号试验
a.主汽门,调汽门全开
b.模拟各保护信号
主汽门正常动作
见热控试验措施
调节系统开关响应试验
投运
a.给定汽机调节器,开关阶跃扰动
b.进行调门全开、关试验
a.信号变化幅度(-10—105%)
c.动态记录
d.油压变化符合要求
a.时间
b.信号
d.油压
附表15
不投运
b.油泵工作正常
汽门关闭时间测定
a.1#跳闸通道跳闸
b.2#跳闸通道跳闸
c.1#、2#跳闸通道跳闸
关闭时≤0.15s
b.跳闸信号
c.阀开度
附表16
1#、2#跳闸通道跳闸
关闭和时≤0.15s
电调系统试验
系统信号试验
见热工措施
符合设计及运行要求
功能检查
参数整定
6.2.2系统整定值
代号/参数
功能
挂闸电磁阀
复位
超速保护电磁阀
103%转速或甩负荷,关调速汽门
机械飞锤式危急遮断器和危急遮断滑阀
109%-110%额定转速动作,卸掉保安油,停机
停机电磁阀
保护停机
溢油阀
17±
0.2MPa时动作
抗燃油泵联锁
报警、联动备用油泵
油箱温度控制器
控制油温
20℃,自动加热
高压油出口滤网
差压变送器
>
0.35MPa,报警
EH液位
高680mm
报警
低450mm
低320mm
停加热器
低220mm
停