铝热焊接作业指导书Word文档下载推荐.docx
《铝热焊接作业指导书Word文档下载推荐.docx》由会员分享,可在线阅读,更多相关《铝热焊接作业指导书Word文档下载推荐.docx(13页珍藏版)》请在冰豆网上搜索。
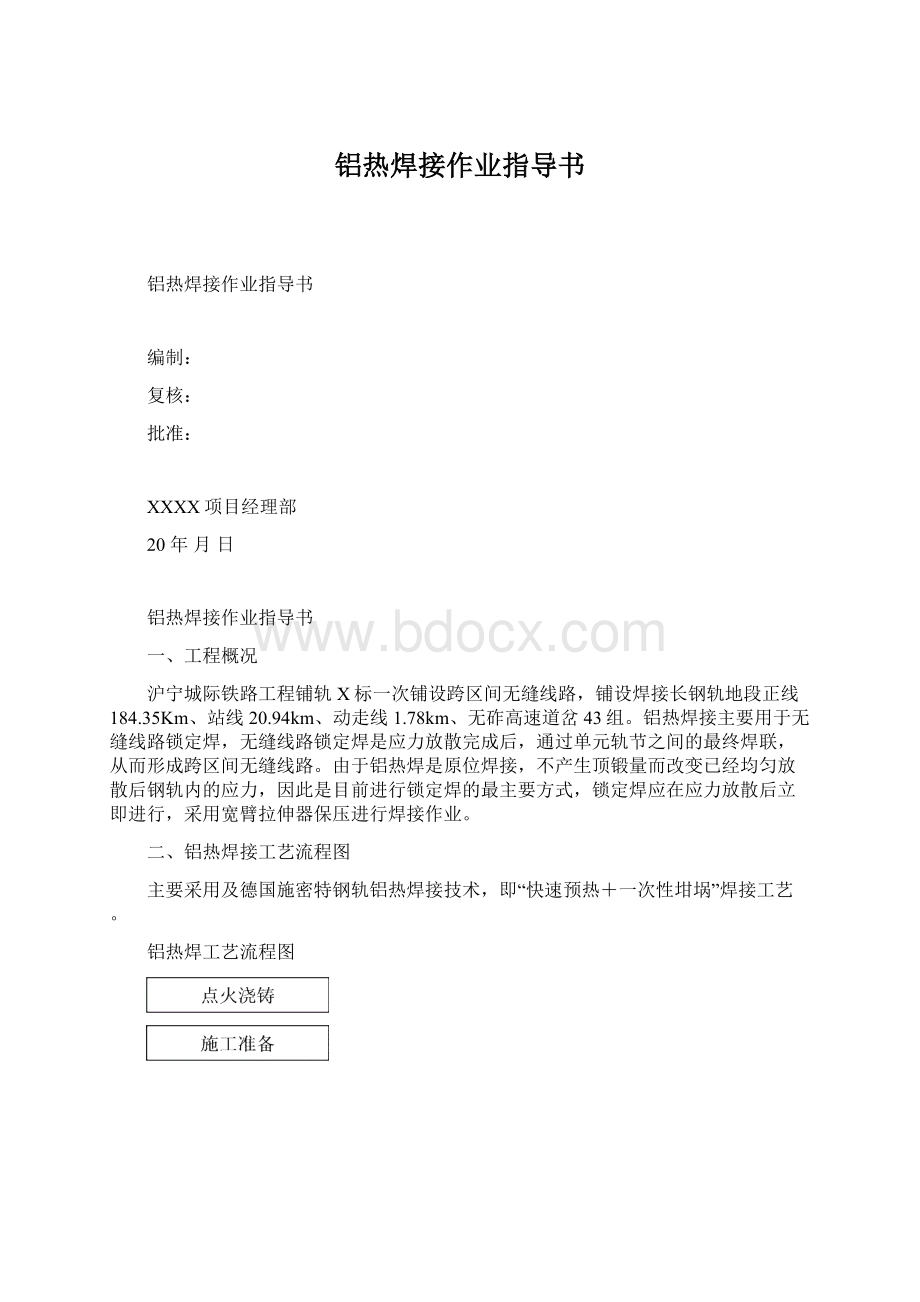
轨缝位置须距轨枕边100mm以上,为了保证钢轨拉伸时接头相错量满足小于100mm的要求,在单元焊时接头相错量按小于50mm掌握。
4.1.5测量轨温。
在钢轨背光的一侧测量轨温,当轨温低于0℃时不进行焊接。
4.1.6轨端200mm范围内的钢轨全断面进行除锈。
4.1.7卸开钢轨接头,卸掉轨缝两侧各10~12根轨枕的扣件(如为曲线或大轨缝则适当延长),取走两侧各2~3根轨枕的绝缘轨距块和胶垫。
4.2端面打磨
轨端打磨用端磨机打磨,轨端不垂直度≤0.8mm,用角磨机或钢丝刷清洁钢轨端头100~150mm范围的钢轨表面。
4.3钢轨端头的对正:
4.3.1轨缝调整:
在轨头和轨底的两侧进行测量,轨缝须满足25mm±
2mm。
焊接过程中保持间隙不变,从对轨开始禁止在焊缝两端各50m范围内松扣件、起拨线路,直至焊接完毕,轨温降至370℃以下为止。
4.3.2尖点对正:
安装对正架,调整对正架使两钢轨端头上拱,保证焊接不产生凹陷,并有一定凸出量供打磨。
4.3.3水平对直:
用型尺分别紧贴钢轨的轨头、轨腰和轨底,一般情况下必须做到三处均密贴方为水平对正。
钢轨内侧纵向要求平直,以1m直尺同时测量两轨平顺度,错动不大于0.2mm。
4.4安装砂模、涂封箱泥
4.4.1检查砂模,应无受潮、无裂纹、无变形,各组件不缺件,状态良好。
4.4.2将侧砂模在轨缝处轻轻摩擦,使其与钢轨密贴,并清除冒口内的浮砂。
4.4.3将底砂模置于金属板中,将密封膏挤入底砂模两侧的槽中,将底砂模与砂模固定夹具板架于轨底,并以轨缝居中,拧紧砂模固定夹具的固定螺丝,同时在砂模固定夹具下侧轻轻敲打,使底砂模与钢轨密贴。
4.4.4将两侧的砂模装入砂模板中,再将侧模置于底板上,并以轨缝居中,带有废渣流出口的侧模位于钢轨的底侧,用一干净纸板将砂模口盖上。
4.4.5先用手指将封箱泥挤入侧模与钢轨内缝隙中一层,外面再抹一层封箱泥进行加固。
在砂模废渣流出口及夹具螺纹处抹上少量封箱泥,以保护工具,放上灰渣盘并在灰渣盘底部垫一层干砂。
4.5调节火焰、钢轨预热
4.5.1将液化气和氧气调压器上的压力完全释放掉(归零),再将预热器上的两个阀门完全打开。
4.5.2通过氧气和液化气的调压阀分别将液化气压力调节至0.07MPa,氧气压力调节至0.49MPa。
4.5.3测量并记录轨温,用预热器加热钢轨。
4.5.4安装预热器支架并调整位置,使预热器处于砂模的中央,预热器离轨面的距离保持在48~55mm范围内。
4.5.5在砂模外,快速打开预热器液化气阀门,点燃火焰并将其稍稍开大,慢慢打开预热器的氧气阀门,交替打开氧气液化气阀门,直至在预热器的喷嘴处获得一个大约12mm的蓝色焰心。
4.5.6将预热器迅速放在预先定位好的预热支架上,并将预热器在砂模中迅速居中定位,此时火焰从砂模两侧冒出,并且均匀对称。
4.5.760kg/m钢轨的预热时间一般掌握在5min以上,具体以钢轨端头颜色发红为标准,既不能预热不足,也不能预热过度。
4.5.8将分流塞放在砂模边缘上进行加热,不间断地注视整个加热过程,确认预热足够后迅速撤走预热器,先关掉氧气阀门,再关掉液化气阀门。
在预热临结束时,注意左右晃动预热器各5秒,以使轨底角加强预热。
4.6检查焊药点火浇注
4.6.1在预热的同时(不宜过早)打开焊药包检查,坩埚不得受潮,无损伤,坩埚内无杂物。
将高温火柴插入焊药内并盖上坩埚盖。
4.6.2当预热结束后,移开预热器,将分流塞放入砂模顶部入口内,把一次性坩埚放置在砂模的中央。
4.6.3点燃高温火柴,将其插入焊药中,埋深为25mm,盖上坩埚盖,此时焊药开始反应浇注。
当废渣停止流出时,按下跑表开始计时。
4.7拆模及推瘤
4.7.1浇注结束5min后,移走灰渣盘和一次性坩埚,拆掉砂模夹具、夹板和金属板。
4.7.2用热切斧在砂模顶部划痕,并将焊头顶部推掉,清理钢轨轨顶变干的封箱泥,同时发动推瘤机。
4.7.3浇注结束6.5s后进行推瘤,推瘤完后除去轨顶面金属,并将金属打弯,放上保温箱进行保温。
4.8拆除对正架、拉伸器
4.8.1浇注结束15min后拆掉对正架。
4.8.2如果使用拉伸器,则浇注结束30min后将其拆掉,不可提前拆除拉伸器。
4.9热打磨
4.9.1打磨焊头使其轮廓与两侧钢轨相同。
4.9.2打磨焊头的内、外侧表面,使其与两侧的钢轨平齐。
4.9.3打磨后,焊头处的焊料凸出量不超过0.5mm。
4.10冷却打磨
4.10.1当轨温降至常温时进行冷打磨,打磨位置包括轨顶及内侧工作面、轨底上表面、轨底。
4.10.2使钢轨表面整体平齐。
4.10.3焊缝两侧100mm范围内不得有明显的压痕、碰痕、划伤等缺陷。
4.11外观及探伤检查
焊缝两侧10mm范围内不得有明显的压痕、碰伤、划伤等缺陷。
当轨温降至50℃以下时进行探伤。
首先清理焊缝两侧各100mm范围,确定无锈、无裂纹、无毛刺等时涂抹机油,进行全端面探伤,不合格者切掉重焊。
编写焊头编号,作好记录。
4.12经打磨后的焊接接头轨头部位满足
4.12.1不应出现裂纹;
4.12.2可出现1个最大尺寸为1mm的气孔;
4.13.3在轨头下鄂与焊筋边缘交界处半径为2mm的区域内,可出现1个最大尺寸为1mm的气孔、夹渣或夹砂;
4.13焊接接头焊筋表面应满足:
4.13.1最多可出现3个最大尺寸不超过2mm的气孔;
4.13.2焊筋表面夹渣或夹砂等缺陷的尺寸应符合下表的规定,这些缺陷不应侵入钢轨的横断面内;
焊筋表面夹渣或夹砂等缺陷的最大尺寸
缺陷面积mm2
缺陷深度mm
≤10
≤3
≤15
≤2
≤20
≤1
4.14收尾工作:
4.14.1检查焊好的接头,做好原始记录并编写焊接序号。
4.14.2清理道床,按标准方枕。
4.14.3将轨道恢复正常,并进一步清理焊接现场。
五、焊接接头直线度和表面质量要求
5.1平直度要求
轨头工作面1m长度平直度允许的最大偏差应符合表1规定。
表1焊接接头平直度标准(mm/1m)
5.2表面质量要求
5.2.1焊接接头的轨头工作面经外形精整后的表面不平度应满足:
在焊缝中心线两侧各100mm范围内,表面不平度不大于0.2mm。
轨顶面及轨头侧面工作边母材打磨深度不应超过0.5mm。
5.2.2焊接接头及其附近钢轨表面不应有裂纹、划伤、碰伤、电极灼伤、打磨灼伤等伤损。
六、探伤
6.1探伤人员资质要求
探伤人员应持有铁道部门无损检测人员技术资格鉴定考核委员会颁发的II级或以上级别的技术资格证书,并经过钢轨焊缝探伤技术培训方能独立上岗作业。
6.2焊接接头探伤要求
6.2.1钢轨焊接后均应对焊接接头进行超声波探伤,并填写探伤记录。
记录应包括仪器、探头、焊接接头编号、测试数据、探伤结果及处理意见。
6.2.2探伤时焊接接头的温度不应高于40℃时,可浇水冷却,浇水冷却时的轨头表面温度应低于350℃。
6.2.3探伤前应对探测系统校准。
6.2.4扫查前检查探测面表面粗糙度,应无锈蚀和焊渣,打磨面应平顺、光滑,打磨范围应能满足探伤扫查的需要。
6.2.5使用双探头或单探头对轨头、轨腰、轨底分别进行探测。
6.2.6发现内、外缺陷要及时向施工人员反映,采取补救措施。
七、焊接记录
焊接操作人员应记录焊接过程,记录内容参照附表1“钢轨铝热焊接操作记录表”,记录应保留5年。
八、检验规则
8.1成品检验
8.1.1应对每个焊接接头(成品)进行成品检验。
8.1.2成品检验的项目包括外观和超声波探伤。
8.2型式检验
8.2.1出现下列情况之一时应进行型式检验:
8.2.1.1焊轨组织初次焊接铁路钢轨。
8.2.1.2采用新型焊剂或调整工艺时;
8.2.1.3钢轨生产厂、或钢轨型号、或钢轨牌号、或钢轨交货状态改变,首次焊接时;
8.2.1.4生产检验结果不合格;
8.2.1.5停产一年后,恢复生产前。
8.2.2型式检验的项目及试件数量见表2
表2型式检验的项目及试件数量单位为个
外观
超声波探伤
静弯
疲劳
拉伸
冲击
硬度
显微组织
断口
轨头受压
轨头受拉
焊缝硬度
软化区宽度
全部试件
8
2
3
1
10(利用静弯试件)
8.2.3型式检验受检试件用钢轨的生产厂、型号、牌号、交货状态应与焊接生产用钢轨相同,受检试件应是相同工艺焊接的接头。
8.2.4不同牌号钢轨之间的焊接,焊接接头的质量要求按照强度级别较低的钢轨执行;
热轧钢轨与热处理钢轨之间的焊接,焊接接头的质量要求按照热轧钢轨执行。
8.2.5型式检验结果符合规定的试件为合格试件。
静弯受检试件、疲劳受检试件应连续试验合格。
一次型式检验中,应在各检验项目全部合格后,方可判定本次型式检验合格。
型式检验合格后方可批量生产。
8.2.6型式检验报告中,应明示以下内容:
焊轨组织名称、焊接材料的型号及生产厂、主要焊接操作人员姓名及操作许可证编号、钢轨生产厂、钢轨型号、钢轨牌号、钢轨交货状态、检验设备、详细的检验结果等。
8.3生产检验
8.3.1出现下列情况之一时应进行生产检验:
8.3.1.1连续焊接100或200个接头;
8.3.1.2两次焊接生产间隔达6个月及以上;
8.3.1.3更换主要焊接操作人员。
8.3.2生产检验的项目及试件数量见表3:
表3生产检验项目及试件数量单位为个
连续焊头数量
100
1(利用静弯试件)
2(利用静弯试件)
200
3(利用静弯试件)
注:
外观和超声波探伤检验合格后的试件作为静弯试件。
8.3.3静弯试件应连续试验合格。
8.3.4生产检验使用随机加焊的试件,生产检验结果应符合相关规定,检验合格后方可继续生产。
8.3.5生产检验有1个及以上试件不合格时应予复验。
第一次复验:
对不合格试件加倍取样复验,经检验合格表示生产检验合格;
若试件中有1个及以上不合格,应再复验。
第二次复验:
若试件中有1个及以上不合格,应判生产检验结果不合格。
九、安全质量措施
9.1各工序工作人员应经过安全技术培训并考试合格后方可上岗。
9.2液化气、氧气瓶、乙炔瓶、控制箱应布置在焊接和切割火焰的上风和铡风向,禁止在火焰的下风下。
9.3加热器发生回火、放炮时,应立即关闭气门、熄灭火焰,防止出现严重事故。
9.4焊接过程对所有气、水胶管严禁压、踩,保证气、水管畅通。
9.5搬运及作业时,各工序严格按操作规程进行操作,以防止发生人身伤害。
9.6焊轨作业时,应配置好必须的劳动防护用品(工作服、眼镜、长皮手套等)。
9.7加热器点火时发现循环水不足时,必须熄灭火焰,待加热器温度降低后,再行供水点火。
施工点附近不应有挥发性气体,易燃易爆物。
如果存在,在设法转换或争取安全保护措施后,方可施工。
9.8水管、气管不要离靠已燃加热器太近,以防爆炸。
9.9加热过后钢轨,严禁身体各部位碰及,以防烫伤。
9.10打磨前应检查端磨机是否漏电,运转是否良好,如有异常应立即联系维修电工进行维修,严禁私拉乱接,避免发生人身事故。
9.11打磨后的钢轨端面严禁再次污染,如有污染要重新打磨。
9.12点火焊接前所需工具摆放齐整,位置合适,禁止闲杂人员进入作业范围内。
附件:
9.13桥上无缝线路焊接严禁采用铝热焊接。
钢轨铝热焊接操作记录表附表1
钢轨铝热焊焊接接头质量要求附表2
附表1
钢轨铝热焊接操作记录表
日期
年月日
序号
里程
行线股公里+米
钢轨编号
钢轨炉罐号
钢轨型号
钢轨材质
操作时间
时分至时分
气温
℃
轨温
拉前轨缝
mm
拉轨压力
MPa
轨缝
上部mm
下部mm
起拱
Mm
氧气
高压Mpa
低压Mpa
流量
L/h
液化气
预热时间
Min
焊剂编号
反应时间
s
平静时间
计时者
对轨者
装卡砂模者
预热者
打磨者
备注
附表2
钢轨铝热焊焊接接头质量要求表
检验项目
60kg/m质量要求
平直度
按5.1的规定
表面质量
按5.2的规定
按第六部分的规定
880Mpa级轨:
F≥1200kN
ƒmax≥10mm
980Mpa级轨:
F≥1300kN
F≥1100kN
4
Fmin=70kN,Fmax=350kN
支距:
1.0m,载荷循环次数:
2×
106,不断
5
拉伸a
880Mpa级轨Rm≥710Mpa,980Mpa级轨Rm≥780Mpa.A≥2%b
6
AKU≥6.0J
7
热轧钢轨Hp±
20(HBW10/3000),热处理钢轨Hp-40~Hp(HBW10/3000)
热轧钢轨W≤20mm,热处理钢轨W≤30mm
焊缝、热影响区不应出现马氏体及魏氏组织等
贝氏体型焊剂:
焊缝显微组织为贝氏体加少量铁素体
珠光体型焊剂:
焊缝显微组织为珠光体加少量铁素体
9
不应出现疏松、缩孔或由焊接引起的裂纹等缺陷
允许出现少量气孔、夹渣或夹砂等缺陷,其尺寸及数量如下:
最大尺寸2mm时,允许数量1个;
最大尺寸1mm时,允许数量2个
a热处理钢轨焊接接头的静弯、拉伸检验项目,按照相应牌号热轧钢轨焊接接头的要求执行。
b断后伸长率A、冲击功AKU不作交货条件。
Hp为焊接接头热影响区外两侧钢轨母材的平均硬度。