1精益师基础知识Word格式.docx
《1精益师基础知识Word格式.docx》由会员分享,可在线阅读,更多相关《1精益师基础知识Word格式.docx(19页珍藏版)》请在冰豆网上搜索。
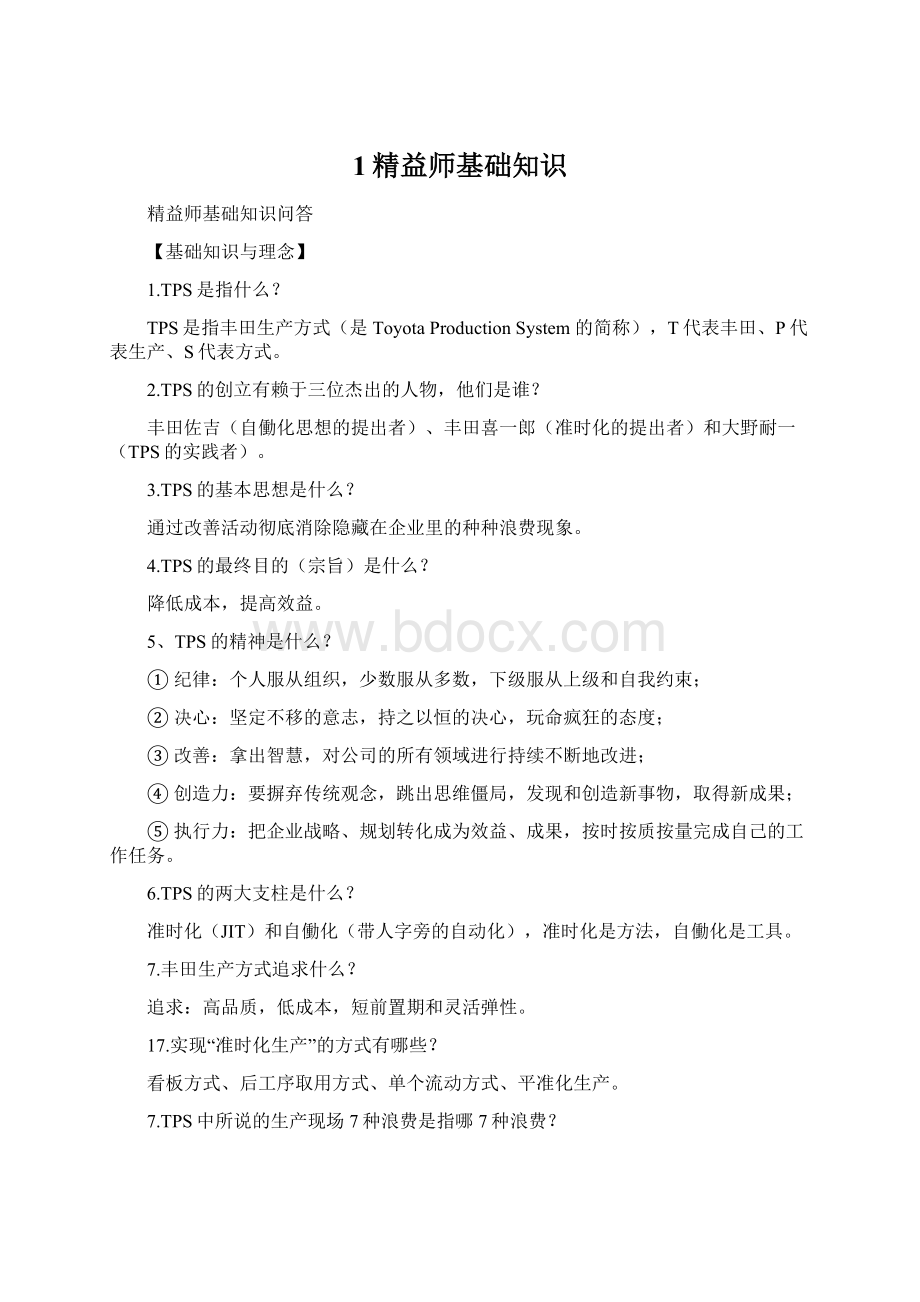
戴明环又叫PDCA循环(P—plan,计划;
D--do,执行,实施;
C--check,检查;
A-act,处理)。
是美国质量管理专家戴明博士首先提出的,它是全面质量管理所应遵循的科学程序。
全面质量管理活动的全部过程,就是质量计划的制订和组织实现的过程,这个过程就是按照PDCA循环,不停顿地周而复始地运转的。
13.丰田发现和解决问题的八个步骤是什么?
P计划:
①明确问题,②分解问题,③设定目标,④把握真因,⑤制定对策;
D执行/实施:
⑥贯彻实施对策;
C检查:
⑦评价结果和过程;
A处理:
⑧巩固成果。
7.评价合格工位的五项内容。
作业区域、作业干涉、部品的放置区域、作业部位、往返次数 。
14.解决问题的十条训言
第一训:
“没有问题就是最大的问题”。
问题无处不在,所以要积极地寻找问题。
第二训:
百个直觉不如一个正确数据。
要认真观察现场、现物,使用数据正确的把握实际情况。
第三训:
赤手空拳无法取胜。
要认真学习改善工具,有效彻底的充分利用。
第四训:
还是专业技能最重要。
要充分掌握专业技巧、技能、技术并随时磨练提高。
第五训:
欲速则不达。
要确实地按解决问题的顺序逐步解决。
第六训:
不要光盯在对策上。
要清醒地分析原因、找到真正原因后再采取措施。
第七训:
电脑再好也不会出主意想办法。
所以要注意创意功夫。
第八训:
想法合理但不具体进行推进的话会停止不前。
第九训:
不要只要求部下去做。
要自己迎难而上积极推进。
第十训:
不要轻易灰心,要锲而不舍坚持到成功。
15.改善的十种精神
第一条:
摒弃制造工艺的固有观念;
第二条:
与其解释不能干的理由,不如考虑实施的方法;
第三条:
别找借口,首先要把握现状;
第四条:
好的事情马上做,不好的事情马上停止;
第五条:
开始别追求完美,从60分做起,一点一点地进步;
第六条:
是错误就要当场改正;
第七条:
如果遇到困难就不会有好的智慧产生;
第八条:
反复问5个为什么来找到真正的原因;
第九条:
与其发挥一个人的智慧,不如发挥10个人的智慧;
第十条:
改善无止境。
16.丰田的十个基本意识
1客户至上;
——在为本部门或公司工作时,应始终将客户的利益放在第一位,后道工序也被看作是“客户”。
2经常自问自答“为了什么”;
——不要将当前的手段混淆为目的。
常常自问“真正的目的是什么?
”
3当事者意识;
——只有认识到自己是当事者,才能理解自己工作的使命和价值,产生自豪感。
才会思考“我想要做什么”,“我一定要达成这个”。
4可视化;
——问题、信息、计划和对情况的认识和意见等需要共有的信息,都要进行目视,已达到信息共享。
5依据现场和事实进行判断;
——摒弃先入为主的观念,以无拘无束之心,看待事物的真实方面。
不将臆测和事实混淆。
亲临现场、自己去看,去听,去感受。
6彻底的思考和执行;
——深入思考、怀着“不到最后决不放弃”的强大意志和坚韧不拔的精神,将工作进行到最后。
7速度·
时机;
——迅速对应客户需求,贯彻实施对策。
避免错失做事的良机。
8诚实·
正直;
——即使在没人监督的时候也按照既定顺序确实推进工作,虚心听取别人的意见。
对自己的行为负起责任。
9实现彻底的沟通;
——诚心诚意与客户或相关人员努力沟通,直至他们给与理解并能够主动积极提供协助。
10全员参与。
——从项目的最初阶段起,动员一切可动员的力量,及时提供相关信息,引领团队以及相关人员,集思广益,以达到效果和效率的最大化。
17.“三现主义”中“三现”是指什么?
三现是指现地(发生问题的地点)、现物(对发生问题的对象进行确认)、现实(摒弃完全凭经验和感觉进行判断的习惯,注重数据和事实,对问题进行分析,找出真正原因)。
三现主义要求我们在解决问题时要到问题发生的现场去,针对现物进行调查和分析,掌握现状,制定解决问题的对策,杜绝仅仅依靠主观想象进行判断。
18.真实效率和表面效率
能力提升是效率的基础。
但效率必须建立在有效需求的基础上,以【是否创造利润】为标准。
假如市场需求100件/天,10个人1天生产100件产品,为单纯提升效率,达到10人1天生产120件,则这种没有基于需求的改善,将不会创造效益甚至会造成在库,则此种效率是假效率。
“省人化”是效率的关键。
只有在满足需求的情况下,达到8人1天生产100件,则此种效率为真效率。
19.省力化和省人化和少人化
◆如果导入高性能的大型设备,可以省人力,即实现「省力化」。
但是更重要的是通过其设备减去人手,将其安排到所需要的部门。
进行「省力化」比如说即使减了0、9的人也是毫无意义的。
因为只有减了一个人才能同降低成本挂钩,所以必须实现「省人化」。
◆丰田汽车进一步设定了新的目标,即「少人化」。
虽然为了做「省人化」,进行了「自働化」,但减产的时候,却不能按产量减少的比例减人。
这是因为「自働化」是定员制。
在低速增长的时候,需要使用智慧打破定员制,建立一条能够对应所需生产数量,无论是几个人都能进行生产的生产线。
这就是「少人化」的目的。
20.稼动率(利用率)和可动率
◆稼动率是指相对于生产时间(负荷时间),实际生产物品的时间(稼动时间)所占的比率,即1台设备计划生产数量与实际生产数量的比值。
市场的需求量是变动的,在生产销量下降的情况下仍然追求设备高利用率的话,会生产出销售不出去的多余库存,造成浪费,因此稼动率并非越高越好,而是基于需求。
◆可动率是指想要生产时,设备、模具随时都处于可以正常使用状态的比率,即指在需要使用设备的负荷时间内,机器设备能按标准定额完成合格品制造的可以动用的时间。
可动率与设备的保养状态息息相关。
设备故障、设备调整、机型切换等都将降低设备可动率,100%可动率是理想状态。
21、拉动与推动
传统生产采用上道工序向下道工序送货,加工过程由第一道工序向最后一道工序推进。
这样的生产方式造成库存的积压过多、产品的批量不良产生。
精益生产遵循内部客户原则,由后工序向前工序取货。
通过看板调节和控制各工序在必要时间生产出必要产品,达成拉动式生产方式。
【术语与定义】
1.什么是品质?
就是物品为达到其使用目的而必须具备的性质,即物品的“作用”、“功效”、“机能”。
2.什么是准时化(JIT)?
准时化,简称JIT(Just
In
Time),是指在仅仅在必要的时候生产必要数量的必要产品。
平准化生产是实现“准时化生产”的前提,“一个流”是准时化生产的核心。
3.什么是平准化?
把产品的流量波动尽可能控制到最小程度,即实现总量和品种数量的均衡。
均衡化和同步化是实现平准化的基础。
4.什么是自働化(Jidoka,带人字旁的自动化)?
在TPS里面说的“自働化(带人字旁的自働化)”是指对设备赋予人的智能,当出现异常情况(例如生产出不合格品时)时设备能够自动停止。
5.什么是目标管理MBO(ManagementbyObjective)?
目标管理是以目标为导向,以人为中心,以成果为标准,而使组织和个人取得最佳业绩的现代管理方法。
目标管理亦称“成果管理”,俗称责任制。
是指在企业个体职工的积极参与下,自上而下地确定工作目标,并在工作中实行“自我控制”,自下而上地保证目标实现的一种管理办法。
6.什么是SMART原则?
①S(Specific)——明确性:
目标必须是具体的;
②M(Measurable)——衡量性:
目标必须是可以衡量的;
③A(Attainable)——可实现性:
目标必须是可以达到的;
④R(Relevant)——相关性:
目标必须和其他目标具有相关性;
⑤T(Time-based)——时限性:
目标必须具有明确的截止期限。
7.什么是生产现场浪费?
生产中只会额外增加成本的各种要素,即对产品来源不提高任何附加价值的各种现象。
它包括勉强(Muri)、浪费(Muda)、不均(Mura)。
8.什么是安东?
安东(Andon)又称故障显示板,是在生产管理系统中通过声、光、电的自动控制,及时传递生产中的异常信息,使异常显现化,以便相关人员及时了解信息,并进行及时处理。
9.什么是A3报告?
A3报告是一种由丰田公司开创的方法,通常用图形把问题、分析、改正措施、以及执行计划囊括在一张(A3)纸上。
在丰田公司,A3报告已经成为一个标准方法,用来总结解决问题的方案,进行状态报告以及绘制价值流图。
要求员工将报告的精华浓缩到一页纸上,把问题搞清楚,把事情搞透彻,去掉冗繁的不必要的内容,直截了当写明“题目、问题、方案、风险、结论和审批”,改变写长篇总结的习惯。
10.什么是看板?
看板是用来发布生产指示、领取指示或作为目视化管理的工具。
看板主要有两种类型:
领取看板和生产指示看板。
11.什么是改善?
发现问题点,找出发生原因,将原因一追到底,直到找到解决方案而反复进行的过程。
12.什么是“一个流”?
是指将作业场地、人员和设备(作业台)合理配置,使产品在生产时,每个工序最多只有一个在制品或成品,从生产开始到完成之前,没有在制品放置场地和入箱包装的作业。
13.什么是标准作业?
指在节拍时间内,以有效的操作顺序,在同一条件下反复进行的操作。
即以人的动作为中心,将高品质的产品(无不良)安全、有效地(无浪费)进行生产的做法。
14.什么是换型时间?
在同一条生产线或同一台设备生产的前一种产品的最后一件良品与下一种产品的第一件良品之间的间隔时间,主要包括内部作业转换和外部作业转换。
15.什么是生产线编成效率?
用来评价一条生产线上各工位所需时间的均衡状态,若失去均衡,则会发生在制品的停滞或延缓工程,劳动力得不到充分利用等。
评价此生产线的好坏即是编成效率。
16.什么是5W2H?
①Why——为了什么目的;
②What——做什么事情或课题;
③Who——由谁负责;
④When——什么时候,包括什么时候开始、什么时候结束;
⑤Where——什么地点,即在哪里实施;
⑥How——如何做,即实施的方法;
⑦How
Much——需要花费多少时间和费用。
17.什么是4M?
生产系统为顾客创造价值的4M。
前3M代表资源,第4个M代表使用资源的方法。
4M――人(man)、设备(machine)、材料(maternal)、方法(method)。
同时丰田4M作为现场变化点进行管理。
18.什么是变化点管理?
在工序内,当4M发生变化后,可能会造成工序内品质的波动或异常,为确保工序内品质稳定,在一定期间内对变化点进行的一系列控制和管理的活动称为变化点管理。
19.什么是生产节拍(T/T)?
生产节拍Takttime(takt是一个德语,原意是乐队的指挥棒),是指生产一个产品所需的时间,即一天的工作时间除以一天所生产的必要数量。
这里一天的所需生产数量是根据生产计划来确定的,而生产计划是基于市场预测和订单情况制定的。
因此,每天的生产数量并不是一定的,而是不断变动的。
20.什么是循环时间?
一名工人在其负责的工序上按照作业顺序操作一个周期所需要的时间。
21.什么是标准手持?
是指为了每个作业人员能够持续进行标准作业,而必须的生产制程内的在制品数量。
22.什么是物流?
物流是物品从供应地向接收地的实体流动过程。
根据实际需要,将运输、储存、装卸、搬运、包装、加工、配送、信息处理等基本功能实施有机结合。
23.什么是定量不定时搬运?
当达到决定的数量时开始进行零部件的搬运,如果生产停滞,零部件消耗没有达到预定的数量,则不进行零部件的搬运,搬运的时间不确定。
24.什么是定时不定量搬运?
当达到决定的时间时进行零部件的引取,如果生产停滞,则领取数量减少,搬运的数量不确定。
25.什么是顺引?
指零部件供货厂家按照整车厂发布的车辆装配的确定顺序,将零部件排序,在规定的时间内将排好序的零部件送到整车厂的物流方式。
26.什么是顺建?
指工厂内部在零部件运送时,按照车辆装配的确定顺序,将零部件排列,在规定的时间内按顺序送到线侧的物流方式。
27.什么是SPS?
SPS是SetPartsSupply的简称,意指成套零部件供应,是将单台车所需的成套部品组合在专用容器中,为车辆生产提供供给的物流方式。
28.什么是物和信息的流程图?
物和信息的流程图是通过直观图的形式明确生产过程中物和信息流动的具体状况,并通过该图寻找出在何处存在何种停滞的浪费,分析生产系统和物流系统中存在的问题,从而作为生产及物流改善的道具。
29.什么是安全库存(最小库存)?
为了防止由于不确定性因素(如大量突发性订货、交货期突然延期等)而准备的缓冲库存,通常定义为在物流或生产过程出现异常时,因需要增加物流时间和异常处置时间而消耗的零件数量。
30.什么是多能工?
多能工是指具有操作多种机器设备能力或具有多种工作技能的作业人员。
5.什么是自主保全?
每个操作者以“维护自己所操作的设备为己任”,做好自己所操作设备的日常点检、加油、更换部件及修理,提早发现异常、检查设备精度等的活动。
6.什么是作业区域?
从最初与车身有关的作业位置开始,1个作业循环结束,到离开车身为止。
【精益生产基础工具】
·
5S及目视化·
1.5S的定义?
①整理:
区分要与不要的物品,把不要品扔掉;
②整顿:
将要的物品按需要时便于使用的原则,整齐地放置,明确标示,以便无论是谁都能清楚明白;
③清扫:
经常扫除保持清洁;
④清洁:
不断地保持整理、整顿、清扫的成果并将成果标准化;
⑤素养:
具有经常正确地遵守已经决定了的事情的习惯。
2.整顿的3定3要素?
3定:
定容、定量、定位;
3要素:
场所、方法、标识。
3.红牌作战的作用?
红牌作战是指在工厂内,找到问题点,并悬挂红牌,让大家都明白并积极地去改善,从而达到整理、整顿的目的,它是5S推进中常用的现场暴露问题的方法,是一种进行整理和整顿的目视化管理工具。
4.推行5S的目的?
①改善和提高企业形象;
②促成效率的提高;
③改善零件在库周转率;
④减少直至消除故障,保障品质;
⑤保障企业安全生产;
⑥降低生产成本;
⑦改善员工精神面貌,使组织活力化;
⑧缩短作业周期,确保交货期。
5.目视管理的定义?
目视管理就是通过视觉传递管理信息,使各种管理一目了然的管理方法。
6.目视管理的要点?
无论是谁都能判断是好是坏;
能迅速判断,准确度高;
判断结果不会因人而异。
7.目视管理的用途(目的)?
使异常及问题显现化;
把应该管理、控制的项目明确表示出来;
提高管理效率。
8.推行目视管理的基本要求?
①统一,即目视管理要实行标准化,消除五花八门的杂乱现象;
②简约,即各种视觉显示信号应易懂,一目了然;
③鲜明,即各种视觉显示信号要清晰,位置适宜,现场人员都能看得见、看得清;
④实用,即不摆花架子,少花钱、多办事,讲究实效;
⑤严格,即现场所有人员都必须严格遵守和执行有关规定,有错必纠,赏罚分明。
价值流图分析·
1.价值
价值是指企业有利于客户的活动,它是由终端客户所确定的,也就是说,只有以一定产品价格在适当时间内满足客户需求时,价值才能体现出来。
从价值的角度来判别企业所有活动,其基本构成主要有三种:
一是必要但不增值的活动,二是不必要的不增值的活动,三是增值活动。
2.价值流
价值流是指在企业经营和生产过程中,把原材料转变为成品,并赋予价值的全部活动,这就包括从供应商处购买的原材料到到企业,企业对产品进行开发设计、加工转变为成品,再交付给客户的全过程。
3.价值流图
价值流图是以铅笔和纸为工具,用一些规范的符号和流线,以确定一个产品族,并从头到尾描绘其每一个工序状态、工序间的物流、信息流和价值流的当前状态图,在找出需要改善的地方后,再描绘一个未来状态图,以显示价值流需要改善的方向和结果。
4.价值流图分析
价值流图分析就是先对运作过程中的现状进行分析,即对“当前状态图”进行分析,从顾客一端开始,首先了解顾客的需求情况和节拍,然后研究运作流程中的每一道工序,从下游追溯到上游,直至供应商。
分析每个工序的增值和非增值活动,包括准备、加工、库存、物料的转移方法等,记录对应的时间,了解分析物流信息传递的路径和方法,然后根据分析情况来判别和确定出浪费所在及其原因,为消灭浪费和持续改善提供目标。
最后根据企业的实际情况,设计出新的价值流程,为未来的运作指明方向。
TPM——设备精益化·
1.什么是TPM?
TPM是从美国的生产性设备保全发展而来,是英文TotalProductiveMaintenance的缩略语,中文译为全面生产维护或全员生产保全。
2.TPM的七大损失?
故障损失;
准备、调整损失;
器具调整损失;
加速损失;
检查停机损失;
速度下降损失;
废品修正损失。
3.TPM发展的5个阶段?
事后保全(BM)、改良保全(CM)、预防保全(PM)、保全预防(MP)和生产维护(PM)。
4.设备的劣化有哪几种形式?
设备的劣化有自然劣化和强制劣化两种形式。
5.设备润滑的5定是指哪5定?
①定时:
按规定周期给设备注油或换油;
②定点:
明确规定或用图显示出设备需要注油的润滑点;
③定量:
按规定的注油量加油,并有消耗定额;
④定质:
按不同设备的规定使用不同品种规格的润滑油,不得擅自改变;
⑤定人:
落实到专人负责。
6.自主保全的定义?
7.自主保全中防止设备劣化的三要素?
清扫、加油、紧固。
8.推行自主保全有什么益处?
①单一技能向多种技能扩展展;
②激发一线员工的能力;
③发现一线员工的潜力;
④更加安全有效的生产。
9.全员生产保全涵盖四大内容。
预防保全、事后保全、改良保全、设备设计。
55.保全活动的三要素是什么?
防止老化、测定老化、恢复劣化。
62.通过开展TPM,将所有损失实现什么?
做到哪三“零”?
通过开展TPM,将所有损失实现预防,做到“零”故障、“零”灾害、“零”不良。
9.什么是“三懂、四会”?
三懂:
懂结构、懂性能、懂原理;
四会:
会使用、会维护保养、会检修、会排除故障;
IE——现场精益化·
1.所有的现场作业都可以分成哪三类?
纯粹的浪费、无附加价值的作业和提高附加值的实质性作业。
2.改善的目标是什么?
工作轻松(减轻劳动强度)、质量变好(提高产品质量);
速度加快(缩短生产时间)、成本降低(节减经费)。
3.改善四要法ECRS指什么?
取消(Eliminate)、合并(Combine)、重排(Rearrange)、简化(Simplify)。
4.动作改善的八大经济原则是什么?
①重心不变;
②方向不变;
③位置不移;
④伸手可及;
⑤容易取放;
⑥借用重力;
⑦双手并用;
⑧利用夹具。
5.IE七大手法是什么?
①流程分析法;
②动作分析法;
③动作经济原则;
④时间研究;
⑤工作抽查法;
⑥人机配置法;
⑦工作简化法(ECRS)。
6.合格工位的作用是什么?
使生产线工位工艺的排布更为合理,减少作业过程中的等待、作业改善、作业不均衡以及无效劳动等浪费现象,并可作为生产线工位改善的基准,通过分析评价以及不间断的改善,从而提高生产效率,实现精益生产。
合格工位评价主要围绕作业区域、部品区域、作业干涉、作业部位、往返次数等方面进行评价。
7.合格工位的描述。
答:
①员工在固定的区域内作业,没有溜线赶线的现象;
②每次的作业路线都一样,没有走动及搬运的浪费;
③作业均衡,员工作业如履平地,而不像爬山一样忽紧忽慢;
④相互间作业无干涉;
标准作业·
1.标准作业适用于什么样的作业?
标准作业适用于循环式的作业和以人的动作为中心的作业,循环式的作业是指有规律的、重复的操作,以人的动作为中心是指作业主要依靠人进行操作。
2.四大名表是指什么?
工程能力表、时间观测表、标准作业组合票、标准作业票。
3.标准作业的三要素是指什么?
生产节拍、作业手顺和标准手持。
4.标准作业的作用是什么?
不同的操作者执行标准作业,都可以用相同的时间,按相同的作业顺序,生产出相同品质的产品。
即:
同一时间、同一手顺、同一品质。
5.我们为什么要推行标准作业?
①标准作业是作业的依据,是管理的基准,是目前最好、操作更容易、安全的工作方法。
②执行标准作业能够有效地保证产品质量。
③标准作业是改善的基础。
④执行标准作业可以有效地监督和防止异常的发生。
⑤执行标准作业可以对新人进行有效的指导,培养多技能工。
6.时间观测中三点一线的“三点”指什么?
眼、秒表、观测点。
60.要素作业的分割难点在于什么?
在于要素作业的大小和分割方法。
6.标准作业原则上应该由谁来制定?
标准作业原则上应该由现场监督人员(班组长)制定。
7.基于标准作业进行改善的六个着眼点分别是什么?
降低工时数、降低工序间在制品库存、降低不合格品、生产能力的增强、目视化管理、设备布局的改善,其中降低工时数是指减少加工单件产品所需要的劳动时间。
8.标准作业表(四大名表)的制作顺序是什么,简述每个步骤的作用?
1工程能力表:
明确各工程的生产瓶颈,适用于以机械作业为主的生产线。
2时间观测表:
实测实际作业时间,观测循环时间及差异,比较循环时间与节拍时间。
3标准作业组合票:
比较作业者的循环时间与节拍时间的差异。
4标准作业票:
对应节拍时间来决定作业者“责任作业范围”,包括走动路线、标准手持、安全注意等。
9.三书一表是指什么?
作业手顺书、作业指导书、作业要领书、QC工程表。
10.标准作业常用的改善