磁化方法Word文档格式.docx
《磁化方法Word文档格式.docx》由会员分享,可在线阅读,更多相关《磁化方法Word文档格式.docx(12页珍藏版)》请在冰豆网上搜索。
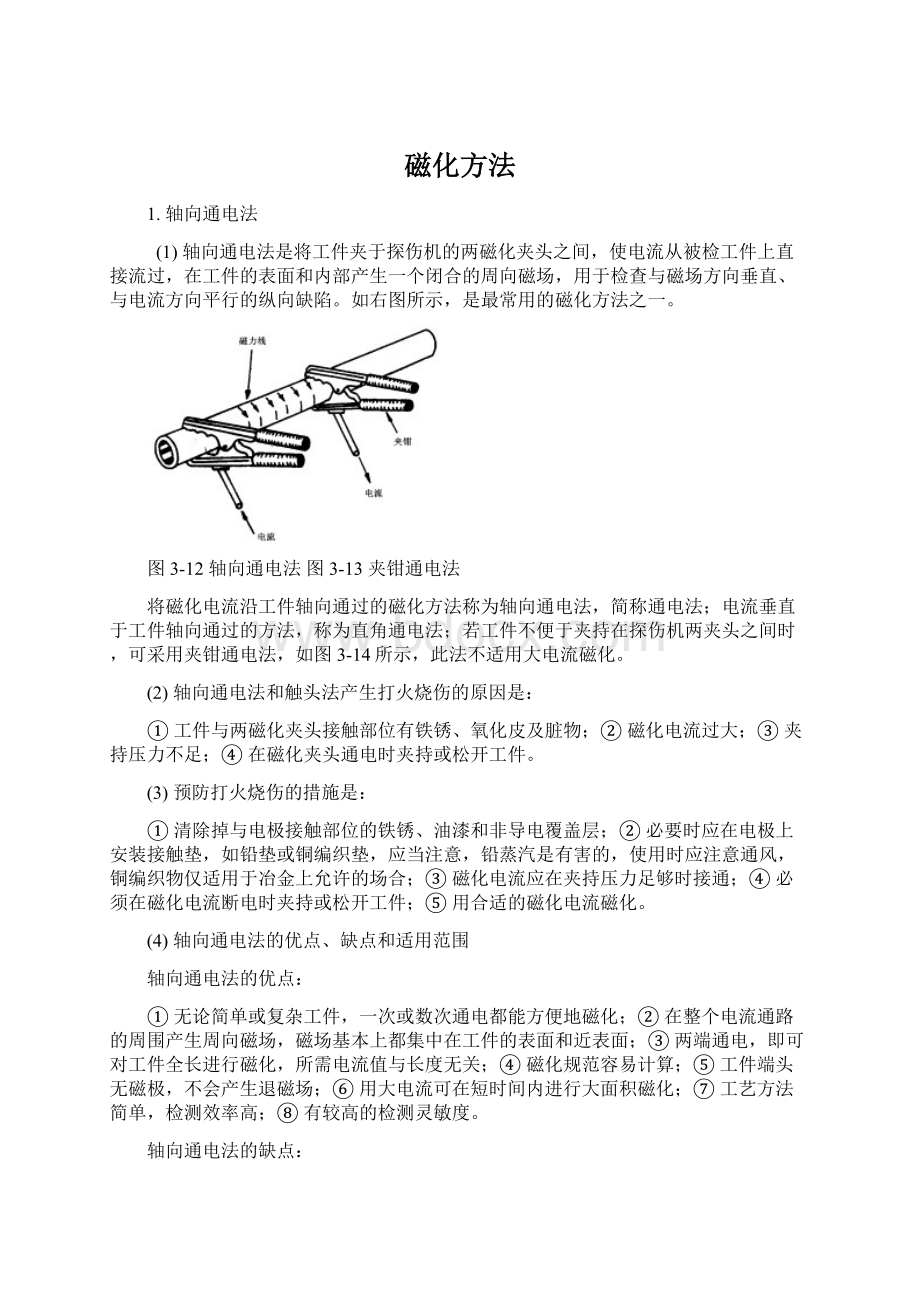
③两端通电,即可对工件全长进行磁化,所需电流值与长度无关;
④磁化规范容易计算;
⑤工件端头无磁极,不会产生退磁场;
⑥用大电流可在短时间内进行大面积磁化;
⑦工艺方法简单,检测效率高;
⑧有较高的检测灵敏度。
轴向通电法的缺点:
①接触不良会产生电弧烧伤工件;
②不能检测空心工件内表面的不连续性;
③夹持细长工件时,容易使工件变形。
轴向通电法适用于:
承压设备实心和空心工件的焊缝、机加工件、轴类、管子、铸钢件和锻钢件的磁粉检测。
图3-14中心导体法
2.中心导体法
(1)中心导体法是将导体穿入空心工件的孔中,并置于孔的中心,电流从导体上通过,形成周向磁场。
所以又叫电流贯通法、穿棒法和芯棒法。
由于是感应磁化,可用于检查空心工件内、外表面与电流平行的纵向不连续性和端面的径向的不连续性,如图3-15所示。
空心件用直接通电法不能检查内表面的不连续性,因为内表面的磁场强度为零。
但用中心导体法能更清晰地发现工件内表面的缺陷,因为内表面比外表面具有更大的磁场强度。
(2)中心导体法用交流电进行外表面检测时,会在筒形工件内产生涡电流ie,因此工件的磁场是中心导体中的传感电流It和工件内的涡电流ie产生的磁场叠加,由于涡电流有趋肤效应,因此导致工件内、外表面检测灵敏度相差很大,对磁化规范确定带来困难。
国内有资料介绍,对某一规格钢管分别通交、直流电磁化,为达到管内、外表面相同大小的磁场,通直流电时二者相差不大,而通交流电时,检测外表面时的电流值将会是检测内表面电流值的2.7倍,因此,用中心导体法进行外表面检测时,一般不用交流电而尽使用直流电和整流电。
(3)对于一端有封头(亦称盲孔)的工件,可将铜棒穿入盲孔中,铜棒为一端,封头作为另一端(保证封头内表面与铜棒端头有良好的电接触),被夹紧后进行中心导体法磁化。
(4)对于内孔弯曲的工件,可用软电缆代替铜棒进行中心导体法磁化。
(5)中心导体材料通常采用导电性能良好的铜棒,也可用铝棒。
在没有铜棒采用钢棒作中心导体磁化时,应避免钢棒与工件接触产生磁写,所以最好在钢棒表面包上一层绝缘材料。
(6)中心导体法的优点、缺点和适用范围:
中心导体法的优点:
①磁化电流不从工件上直接流过,不会产生电弧;
②在空心工件的内、外表面及端面都会产生周向磁场;
③重量轻的工件可用芯棒支承,许多小工件可穿在芯棒上一次磁化;
④一次通电,工件全长都能得到周向磁化;
⑤工艺方法简单、检测效率高;
⑥有较高的检测灵敏度。
因而是最有效、最常用的磁化方法之一。
中心导体法的缺点:
①对于厚壁工件,外表面缺陷的检测灵敏度比内表面低很多;
②检查大直径管子时,应采用偏置芯棒法,需转动工件,进行多次磁化和检验;
③仅适用于有孔工件的检验。
中心导体法适用于:
承压设备的管子、管接头、空心焊接件和各种有孔的工件如轴承圈、空心圆柱、齿轮、螺帽及环形件的磁粉检测。
3.偏置芯棒法
对于空心工件,导体应尽量置于工件的中心。
若工件直径太大,探伤机所提供的磁化电流不足以使工件表面达到所要求的磁场强度时,可采用偏置芯棒法磁化,即将导体穿入空心工件的孔中,并贴近工件内壁放置,电流从导体上通过形成周向磁场。
用于局部检验空心工件内、外表面与电流方向平行和端面的径向缺陷,如右图所示。
适用于中心导体法检验时,设备功率达不到的大型环和压力管道管子的磁粉检测。
偏置芯棒法采用适当的电流值磁化,有效磁化范围约为导体直径d的4倍。
检查时要转动工件,以检查整个圆周,并要保证相邻检查区域有10%的重叠。
4.触头法
(1)触头法是用两支杆触头接触工件表面,通电磁化,在平板工件上磁化能产生一个畸变的周向磁场,用于发现与两触头连线平行的缺陷,触头法设备分非固定触头间距如图3-17所示(承压设备常用)和固定触头间距两种。
触头法又叫支杆法、尖锥法、刺棒法和手持电极法。
触头电极尖端材料宜用铅、钢或铝,最好不用铜,以防铜沉积被检工件表面,影响材料的性能。
图3-17触头法的磁力线
图3-18触头法磁化的有效磁化区(阴影部分)
(2)触头法用较小的磁化电流值就可在工件局部得到必要的磁场强度,灵敏度高,使用方便。
最短不得小于75mm,因为在触头附近25mm范围内,电流密度过大,产生过度背景,有可能掩盖相关显示。
如果触头间距过大,电流流过的区域就变宽,使磁场减弱,磁化电流必须随着间距的增大相应地增加。
JB/T4730.04-2005规定:
“采用触头法时,电极间距应控制在75mm~200mm之间。
磁场的有效宽度为触头中心线两侧1/4极距,通电时间不应太长,电极与工件之间应保持良好的接触,以免烧伤工件。
两次磁化区域间应有不小于10%的磁化重叠区”。
欧洲标准EN1290也规定,触头法磁化的有效磁化区如图3-18的阴影部分所示,面积约为(L-50)×
(L/2)mm2。
有效磁化区范围还可以通过实测工件表面磁场强度或用标准试片上的磁痕显示来验证。
(3)为了保证触头法磁化时不漏检,必须让两次磁化的有效磁化区相重叠不小于10%,如图3-19所示。
图3-19有效磁化区的重叠区
(4)触头法的优点、缺点及适用范围
触头法的优点:
①设备轻便,可携带到现场检验,灵活方便;
②可将周向磁场集中在经常出现缺陷的局部区域进行检验;
③检测灵敏度高。
触头法的缺点:
①一次磁化只能检验较小的区域;
②接触不良会引起工件过热和打火烧伤;
③大面积检验时,要求分块累积检验,很费时。
触头法适用于:
承压设备平板对接焊缝、T型焊缝、管板焊缝、角焊缝以及大型铸件、锻件和板材的局部磁粉检测。
5.感应电流法
感应电流法是将铁芯插入环形工件内,把工件当作变压器的次级线圈,通过铁芯中的磁通的变化,在工件内产生周向感应电流。
用感应电流磁化工件产生闭合磁场的方法称为感应电流法或磁通贯通法。
如图3-20和3-21所示,用于发现环形工件圆周方向的缺陷。
图3-20感应电流法图3-21感应电流法
感应电流与磁通量的变化率成正比。
只有激磁线圈容量大,铁芯面积也足够大,才能感应产生足够的磁化电流,在工件表面产生足够大的磁化场。
工件表面的磁场强度与环形工件径向尺寸成反比,与宽度关系不大。
感应电流法的优点:
①非电接触,可避免烧伤工件;
②工件不受机械压力,不会产生变形;
③能有效地检出环形工件内、外圆周方向的缺陷。
感应电流法适用于:
直径与壁厚之比大于5的簿壁环形工件、齿轮和不允许产生电弧烧伤的工件的磁粉检测。
6.环形件绕电缆法
图3-22环形件绕电缆法
在环形工件上,缠绕通电电缆,也称为螺线环,如图3-22所示。
所产生的磁场沿着环的圆周方向,磁场大小可近似地用下式计算:
…………(3-7)
式中:
H——磁场强度(A/m)
N——线圈匝数
I——电流(A)
R——圆环的平均半径(m)
L——圆环中心线长度(m)
环形件绕电缆法是用软电缆穿绕环形件,通电磁化,形成沿工件圆周方向的周向磁场,用于发现与磁化电流平行的横向缺陷,如图3-22所示。
环形件绕电缆法的优点是:
①由于磁路是闭合的,无退磁场产生,容易磁化。
②非电接触,可避免烧伤工件。
缺点是效率低,不适用于批量检验。
环形件绕电缆法适用于:
承压设备尺寸大的环形件的磁粉检测。
7.线圈法
(1)线圈法是将工件放在通电线圈中,或用软电缆缠绕在工件上通电磁化,形成纵向磁场,用于发现工件的周向(横向)缺陷。
适用于纵长工件如焊接件、轴、管子、棒材、铸件和锻件的磁粉检测。
(2)线圈法包括螺管线圈法和绕电缆法两种,如图3-23和图3-24所示。
图3-23螺管线圈法图3-24绕电缆法
(3)线圈法纵向磁化的要求
①线圈法纵向磁化,会在工件两端形成磁极,因而产生退磁场。
工件在线圈中磁化与工件的长度L和直径D之比(L/D)有密切关系,L/D愈小愈难磁化,所以L/D必须≥2,若L/D<2,应采用与工件外径相似的铁磁性延长块将工件接长,使L/D≥2。
②工件的纵轴应平行于线圈的轴线。
③可将工件紧贴线圈内壁放置进行磁化。
④对于长工件,应分段磁化,并应有10%的有效磁场重叠。
⑤工件置于线圈中开路磁化,能够获得满足磁粉检测磁场强度要求的区域称为线圈的有效磁化区。
线圈的有效磁化区是从线圈端部向外延伸150mm的范围内。
超过150mm以外区域,磁化强度应采用标准试片确定。
ASTME1444-94a对于低和高充填因数线圈的有效磁化区分别规定如下:
对于低充填因数线圈,在线圈中心向两侧延伸的有效磁化区大约等于线圈的半径R,如图3-25所示。
对于高充填因数线圈和绕电缆法从线圈中心向两侧分别延伸9英寸(229mm)为有效磁化区,如图3-26所示。
可供试验和应用时参考。
对于不能放进螺管线圈的大型工件,可采用绕电缆法磁化。
图3-25低填充因数线圈有效磁化区图3-26高填充因数线圈有效磁化区
(4)快速断电的影响
三相全波整流电磁化线圈,磁化长条形工件时,磁场在线圈横截面上分布不均匀,在其轴线附近变化较为平缓,靠近内壁变化增大。
在线圈端部和端部外附近,磁场的径向分量很大,对工件磁化时,这部位的磁力线外溢较严重,有可能造成工件端部(有效磁化区端部)磁化不足。
此时,可采用快速断电的方法来补偿。
磁化电流的快速切断,意味着磁化场的快速切除,这样在工件的横截面上将感生闭合的电流(即涡流),该电流产生的磁场与原磁场的轴向分量同向,同时在工件端部建立一个封闭的环形磁场,称为“快速断电效应”,如图3-27所示。
只要断电速度足够快,感生电流的磁场也可以足够大,使缺陷能够被检测出来。
利用这种效应,有利于检测工件端面的横向不连续性。
图3-25快速断电和慢速断电的磁场分布
(5)线圈法的优点、缺点及适用范围:
线圈法的优点:
①非电接触;
②方法简单;
③大型工件用绕电缆法很容易得到纵向磁场;
④有较高的检测灵敏度。
线圈法的缺点:
①L/D值对退磁场和灵敏度有很大的影响,决定安匝数时要加以考虑;
②工件端面的缺陷,检测灵敏度低;
③为了将工件端部效应减至最小,应采用“快速断电”。
线圈法适用于:
承压设备对接焊缝、角焊缝、管板焊缝以及纵长工件如曲轴、轴、管子、棒材、铸件和锻件的磁粉检测。
8.磁轭法
(1)磁轭法是用固定式电磁轭两磁极夹住工件进行整体磁化,或用便携式电磁轭两磁极接触工件表面进行局部磁化,用于发现与两磁极连线垂直的缺陷。
在磁轭法中,工件是闭合磁路的一部分,用磁极间对工件感应磁化,所以磁轭法也称为极间法,属于闭路磁化,如图3-28和图3-29所示。
图3-28电磁轭整体磁化图3-29电磁轭局部磁化
(2)整体磁化
用固定式电磁轭整体磁化的要求是:
①只有磁极截面大于工件截面时,才能获得好的探伤效果。
相反,工件中便得不到足够的磁化,在使用直流电磁轭比交流电磁轭时更为严重;
②应尽量避免工件与电磁轭之间的空气隙,因空气隙会降低磁化效果;
③当极间距大于1m时,工件便不能得到必要的磁化。
④形状复杂而且较长的工件,不宜采用整体磁化。
(3)局部磁化
用便携式电磁轭的两磁极与工件接触,使工件得到局部磁化,两磁极间的磁力线大体上平行两磁极的连线,有利于发现与两磁极连线垂直的缺陷。
图3-30便携式磁轭磁化的有效磁化区(阴影部分)
便携式电磁轭,一般做成带活动关节,磁极间距L一般控制在75mm-200mm为宜,但最短不得小于75mm。
因为磁极附近25mm范围内,磁通密度过大会产生过度背景,有可能掩盖相关显示。
在磁路上总磁通量一定的情况下,工件表面的磁场强度随着两极间距L的增大而减小,所以磁极间距也不能太大。
“磁轭的磁极间距应控制在75mm~200mm之间,检测的有效区域为两极连线两侧各50mm的范围内,磁化区域每次应有不少于15mm的重叠”。
欧洲标准EN1290也规定便携式电磁轭磁化的有效磁化区如图3-30的阴影部分,面积约为(L-50)×
交流电具有趋肤效应,因此对表面缺陷有较高的灵敏度。
又因交流电方向在不断地变化,使交流电磁轭产生的磁场方向也不断地变化,这种方向变化可搅动磁粉,有助于磁粉迁移,从而提高磁粉检测的灵敏度。
而直流电磁轭产生的磁场能深入工件表面较深,有利于发现较深层的缺陷。
因此在同样的磁通量时,探测深度越大,磁通密度就越低,尤其在厚钢板中比在薄钢板中这种现象更明显,如图3-31所示。
尽管直流电磁轭的提升力满足标准要求(>177N),但测量工件表面的磁场强度和在A型试片上的磁痕显示都往往达不到要求,为此建议对厚度>6mm的工件不要使用直流电磁轭探伤。
ASME规范第V卷也特别强调“除了厚度小于等于6mm的材料之外,在相等的提升力条件下,对表面缺陷的探测使用交流电磁轭优于直流和永久磁轭。
”
a)在薄钢板中的磁通分布b)在厚钢板中的磁通分布
图3-31直流电磁轭在钢板中的磁通分布
一般说来,承压设备的表面和近表面缺陷的危害程度较内部缺陷要大的多,所以对锅炉、压力容器的焊缝进行磁粉检测,一般最好采用交流电磁轭。
但对于薄壁(<6mm)的压力管道来说,利用直流电磁轭既可发现较深层的缺陷,又兼顾表面及近表面缺陷能检测出来,这样也弥补了交流电磁轭的不足,所以对于<6mm的薄壁压力管道应采用直流电磁轭。
(4)磁轭法的优点、缺点及适用范围:
磁轭法的优点:
②改变磁轭方位,可发现任何方向的缺陷;
③便携式磁轭可带到现场检测,灵活,方便;
④可用于检测带漆层的工件(当漆层厚度允许时);
⑤检测灵敏度较高。
磁轭法的缺点:
①几何形状复杂的工件检验较困难;
②磁轭必须放到有利于缺陷检出的方向;
③用便携式磁轭一次磁化只能检验较小的区域,大面积检验时,要求分块累积,很费时;
④磁轭磁化时应与工件接触好,尽量减小间隙的影响。
磁轭法适用于:
整体磁化适用于零件横截面小于磁极横截面的纵长零件的磁粉检测。
9.永久磁轭法
永久磁铁可用于对工件局部磁化,适用于无电源和不允许产生电弧引起易燃易爆的场所。
它的缺点是:
在检验大面积工件时,不能提供足够的磁场强度以得到清晰的磁痕显示,磁场大小也不能调节。
永久磁铁磁场太大时,吸在工件上难以取下来,磁极上吸附的磁粉不容易清除掉,还可能把缺陷磁痕弄模糊,所以使用永久磁铁磁化一般需要得到批准。
10.交叉磁轭法
电磁轭有两个磁极,进行磁化只能发现与两极连线垂直的和成一定角度的缺陷,对平行于两磁极连线方向缺陷则不能发现。
使用交叉磁轭可在工件表面产生旋转磁场,如图3-30所示。
国内外大量实践证明,这种多向磁化技术可以检测出非常小的缺陷,因为在磁化循环的每个周期都使磁场方向与缺陷延伸方向相垂直,所以一次磁化可检测出工件表面任何方向的缺陷,检测效率高。
1—工件2—旋转磁场3—缺陷4、5—交流电6—焊缝7—交叉磁轭
图3-30交叉磁轭法
(1)交叉磁轭的正确使用方法是:
①交叉磁轭磁化检验只适用于连续法。
必须采用连续移动方式进行工件磁化,且边移动交叉磁轭进行磁化,边施加磁悬液。
最好不采用步进式的方法移动交叉磁轭。
②为了确保灵敏度和不会造成漏检,磁轭的移动速度不能过快,不能超过标准规定的4m/min的移动速度,可通过标准试片磁痕显示来确定。
当交叉磁轭移动速度过快时,对表面裂纹的检出影响不是很大,但是,对近表面裂纹,即使是埋藏深度只有零点几毫米,也难以形成缺陷磁痕。
③磁悬液的喷洒至关重要,必须在有效磁化场范围内始终保持润湿状态,以利于缺陷磁痕的形成。
尤其对有埋藏深度的裂纹,由于磁悬液的喷洒不当,会使已经形成的缺陷磁痕被磁悬液冲刷掉,造成缺陷漏检。
④磁痕观察必须在交叉磁轭通过后立即进行,避免已形成的缺陷磁痕遭到破坏。
⑤交叉磁轭的外侧也存在有效磁化场,可以用来磁化工件,但必须通过标准试片确定有效磁化区的范围。
⑥交叉磁轭磁极必须与工件接触好,特别是磁极不能悬空,最大间隙不应超过1.5mm,否则会导致检测失效。
(2)交叉磁轭磁化的优点、缺点及适用范围
交叉磁轭磁化的优点:
一次磁化可检测出工件表面任何方向的缺陷,而且检测灵敏度和效率都高。
交叉磁轭磁化的缺点:
不适用于剩磁法磁粉检测,操作要求严格。
交叉磁轭磁化的适用于:
锅炉压力容器的平板对接焊缝的磁粉检测。