铸造大赛设计说明书路铝合金框架课件文档格式.docx
《铸造大赛设计说明书路铝合金框架课件文档格式.docx》由会员分享,可在线阅读,更多相关《铸造大赛设计说明书路铝合金框架课件文档格式.docx(48页珍藏版)》请在冰豆网上搜索。
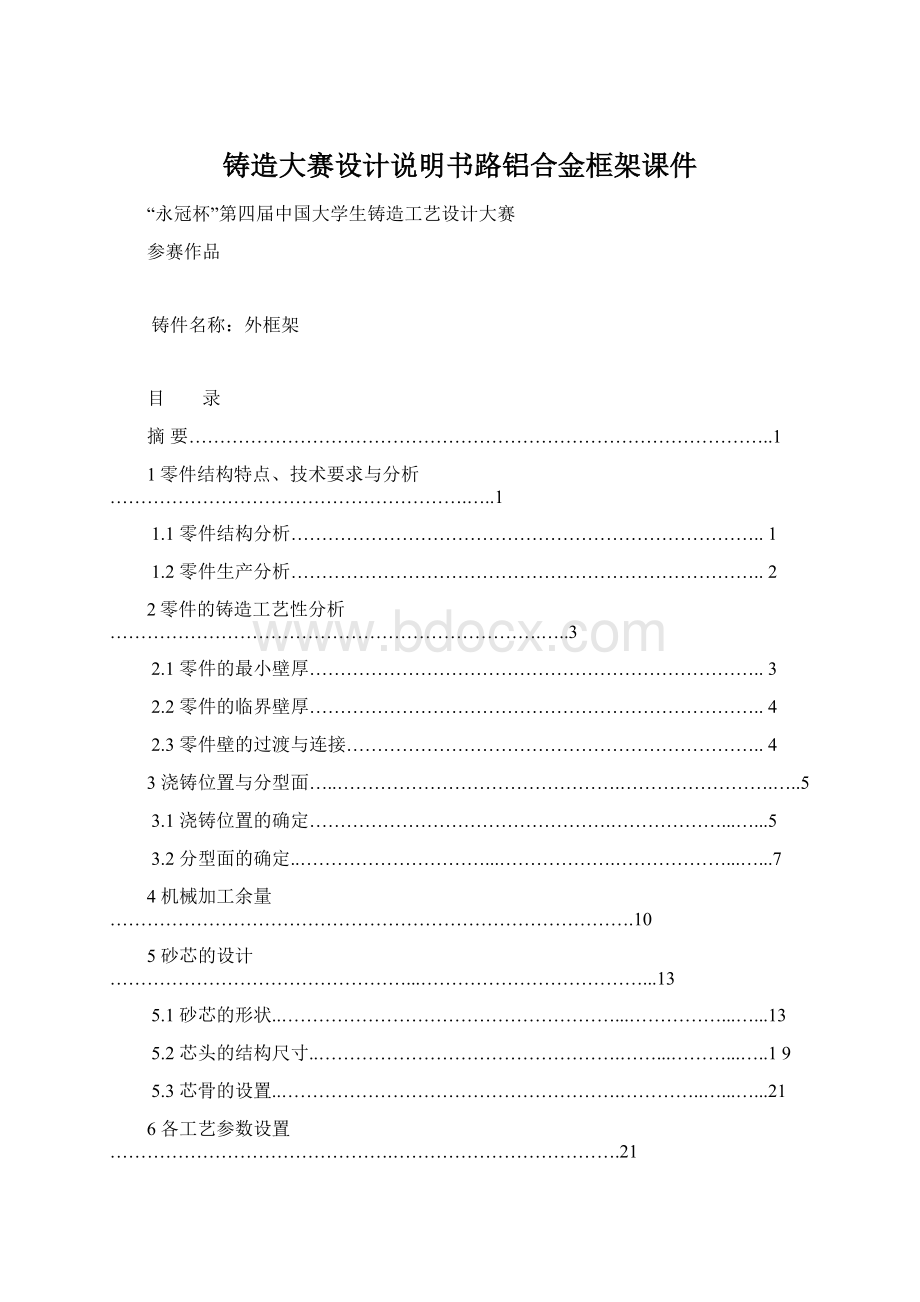
10.1原始工艺方案中铸件的充型和凝固分析…………………….……….…….34
10.2铸件的优化方案…………………….……………………………………36
11砂箱…………………………………………………………………………….….….37
11.1砂箱的结构尺寸……………………………….………………….........….38
11.2砂箱的定位…………………………………….…………………..…...….39
参考文献…………………………………..……………………………………….....…...40
附图………………………………..………………………………………...….....…41
摘要:
铸造是通过熔炼金属,制造铸型,并将熔炼金属液浇入铸型,凝固后获得一定形状、尺寸和性能金属零件毛坯的成型方法。
在机器制造业中用铸造方法生产的毛坯零件,在数量和吨位上迄今仍是最多的。
而铸造工艺(造型、制芯、浇注、落砂、清理及其后处理等)是铸造生产的核心,是能否生产优质铸件的关键。
重力铸造是指金属液在地球重力作用下注入铸型的工艺,砂型铸造所用的造型材料价廉易得,铸型制造简便,对铸件的单件生产、成批生产和大量生产均能适应,长期以来,一直是铸造生产中的基本工艺。
采用树脂砂造型造芯能获得高精度表面光洁的铸件,铸型不用烘干、强度高而且溃散性好,易于实现机械化生产。
由于树脂砂铸造的多种优点,作者对“C件—外框架”采用树脂砂型铸造,用CATIAV5创建模型,通过对铸件结构、形状和尺寸的详细分析,设计了铸造生产时的“浇注位置”、“分型面”,设计了砂芯的形状和数量等铸造工艺方案内容以及铸造生产时涉及到的“加工余量”、“拔模斜度”、“铸造收缩率”等工艺参数,采用了大孔流出的方法设计了浇注系统的类型、内浇口的开设位置以及浇注系统各组元的截面形状和尺寸。
应用Hypermesh软件剖分网格,采用ProCAST软件对铸件进行充型及凝固过程的数值模拟,优化工艺,减少或消除铸造缺陷,缩短新产品的试制周期,降低成本,提高生产效率。
关键词:
铸造,工艺设计,铝合金铸件,呋喃树脂自硬砂,数值模拟
1、零件结构特点、技术要求与分析
1.1零件结构分析
1、零件名称:
2、材质:
ZL114A
3、零件用途:
支撑,传动扭矩
4、零件特点:
件的轮廓尺寸为1466mm×
870mm×
619mm,结构左右对称,壁厚均匀,最厚大部位30mm,最小壁厚15mm,最大孔径Φ210mm,最小孔径Φ5mm。
5、零件的形状:
如图1.1所示三维实体。
图1.1零件结构三维实体图
铸件材料为ZL114A,钢套材料为45号钢,铸件重量为253.98千克,内部结构较复杂,属于中大型铸件,适合单间小批量生产。
圆柱上下表面和框架顶端为工作表面;
圆盘上表面有4个ф125mm的铸造孔,下表面有一个Φ210mm的铸造孔,钢套上有10个ф35mm的铸造孔,圆柱空腔里有10个ф60mm的铸造孔,其它孔过小不宜铸出,均为加工孔。
技术要求:
1、铸件不得有气孔、沙眼、缩松等缺陷,且须经时效处理。
2、未注倒角1×
45°
,未注倒圆R1~3。
3、内径ф275钢套应与框架铸造牢固,保障传递10000Nm较大扭矩。
4、加工时保证尺寸439及619一致。
1.2铸件生产分析
零件“C—外框架”净重达到253.986kg,零件尺寸为1466mm×
619mm,属于大型铝合金铸件。
中大型零件的铸造生产不易采用机械化流水线生产,而应该采用手工造型生产方式。
砂型包括湿型、干型、表干型和树脂砂型等。
采用粘土砂造型方法,无论是普通湿型造型还是表面干型或者是干型造型,由于粘土的粘结性能比较低,铸型的强度受到影响,生产中大型铸件时容易造成铸件夹砂、多肉、气孔、缩孔、铸件尺寸和铸件重量偏差大等铸造缺陷,难以获得内部质量和外部质量优良的铸件,所以很少采用。
对于中大型铸件,可以采用树脂自硬砂型,水玻璃砂型以及黏土干砂型。
采用水玻璃粘结剂CO2气体硬化方法制作铸型,由于水玻璃砂出砂性差,增加了铸件的清理工作;
黏土干砂型需要烘干,增加了人力和成本;
而树脂砂造型造芯能获得高精度、表面光洁的铸件,铸型不用烘干、强度高且溃散性好。
目前,多数铸造企业为了提高铸件的尺寸精度、重量精度以及铸件的内部质量和表面质量,并且为改善铸造车间的生产环境,对于单件小批量生产的中大型铸件一般都采用树脂自硬砂造型、树脂砂制芯方式生产铸件。
采用树脂粘结剂作为型砂和芯砂的粘结剂能够获得高强度的砂型和砂芯,对于保证铸件的质量是有保证的。
本次设计采用呋喃树脂自硬砂作为型砂和芯砂,另外,由于采用单件小批量生产,设计使用芯盒手工造芯。
图1.2砂型铸造流程图
2、零件的铸造工艺性分析
零件的工艺性分析包括考察零件的合理壁厚和铸孔尺寸,铸件壁的连接和过渡,肋的设计,铸件的结构斜度等内容。
合理的金属零件铸造结构可以消除许多铸造缺陷。
该零件的结构及主要尺寸如图2.1所示。
零件轮廓尺寸为1466mm×
,619mm,整体结构对称,内部结构较为复杂,壁厚均匀,最大壁厚30mm,最小壁厚15mm,最大孔径为Φ210mm,最小孔为M5螺纹孔。
图2.1零件整体结构及尺寸
2.1铸件的合理壁厚
从保证金属液充型能力看,在设计铸件壁厚时,要考虑金属液的流动性和铸件的轮廓尺寸。
在一定的铸造条件下,铸造合金液能充满铸型的最小厚度称为该铸造合金的最小壁厚。
为了避免铸件产生浇不到和冷隔等缺陷,应使铸件的设计壁厚不小于最小壁厚。
如果铸件的壁厚小于其最小壁厚的限制,则容易使铸件形成“浇不足”、“冷隔”等缺陷。
对于砂型铸造铝合金铸件,参照资料
(1)铸造手册表3-3列表格如下表2.1:
表2.1砂型铸造铝合金铸件的最小壁厚(mm)
合金种类
当铸件最大轮廓尺寸为下列值时
<
100
100~200
200~400
400~800
800~1250
铝合金
3
4~5
5~6
6~8
8~12
由表中数据可推出,铸件最大轮廓为1250~1800mm时,铝合金最小壁厚为12~16mm,对于零件“C—外框架”,铸件最大轮廓尺寸为1466mm,最小壁厚为15mm,接近铝合金铸件的容许的最小壁厚,浇注时应该特别注意,防止产生“冷隔”和“浇不足”的缺陷。
2.2铸肋的合理分析
布置肋的时候,要尽量分散与减少热节点,肋的布置尽量避免十字交叉。
但是考虑到该零件的设计要求,如图2.2所示的交叉肋,只能设计成十字交叉型铸出。
交叉肋
图2.2零件十字交叉肋位置
2.3铸件壁的过渡和连接
一般情况下,铸件壁的断面尺寸不可能完全相同,同时,铸件有类型各异的连接。
任何零件都是由不同尺寸的“壁”相互连接构成,通常构成零件的各“壁”其“壁厚”应该接近一致,不能差别过大,否则其铸造工艺也属于不合理。
同时,铸件各个壁的连接和过渡应该满足铸造工艺性要求,即铸件“壁”的连接、过渡应该是平缓的。
分析该零件的连接过渡,均运用合理的圆角过渡,过渡平缓,因此零件满足铸造工艺性要求。
3、铸造工艺方案设计
3.1浇注位置的确定
浇注位置是指浇注金属液时铸件在铸型中所处的位置,浇注位置是根据铸件的结构特点、尺寸、重量、技术要求、铸造合金特性、铸造方法和铸造生产车间的条件决定。
正确的浇注位置应该能保证获得健全的铸件,并使造型、制芯和清理方便。
要依据浇注位置的确定原则选取合理的浇注位置,本铸件不能满足所有的原则,但是在解决主要矛盾的同时兼顾其他次要矛盾。
本铸件共有4种浇注位置,分析如下:
AB
CD
图3.1浇注位置
如图3.1所示,A位置铸件的加工面放在侧面,防止加工面产生砂眼、气孔、夹渣等铸造缺陷,缺点是需使用悬臂砂芯;
B位置与A位置优缺点相似,但B位置难以取出模样,同时,竖放使得砂箱的高度大大增加,给铸造生产带来更大的困难;
C位置下芯相对简单,但是加工面被放置在上表面,容易产生铸造缺陷;
D位置除了有C的缺点外,需大量使用吊芯,使得砂芯安放困难。
综合考虑以上4种浇注位置,A和C各有优缺点,设计小组人员考虑应把铸件的质量放在第一位,尽量不让加工面产生砂眼、气孔、夹渣等铸造缺陷,所以选择A浇注位置。
3.2分型面的确定
铸造分型面是指铸型组元间的结合面。
合理的选择分型面,对于简化铸造工艺、提高生产率、降低成本、提高铸件质量等都有直接关系。
分型面的选择应尽量与浇注位置一致,尽量使两者协调起来,是铸造工艺简便,并易于保证铸件质量。
对于铸件“C件—外框架”,综合以上原则,位置分型面放在最大截面方起模,如下图:
图3.2.分型面
分型面选在铸件的最大截面处,保证从铸型中取出模样,不损坏铸型,铸件上下对称分布,避免上沙箱过大。
4铸造工艺参数的设计
4.1铸件尺寸公差
铸件尺寸公差是指铸件公称尺寸的两个允许极限尺寸之差。
在两个允许极限尺寸之内,铸件可以满足加工、装配和使用要求。
根据资料
(1)《铸造手册》GB/T6414—1999《铸件尺寸公差和机械加工余量》的规定,铸件尺寸公差等级分为16级,表示为CT1~CT16。
铸件“C-外框架”需满足CT12级要求,具体公差数值见下表4.1:
表4.1单件小批量生产铸件的尺寸公差等级
方法
造型材料
公差等级CT
铸钢
灰铸铁
球墨铸铁
可锻铸铁
铜合金
轻金属合金
镍基合金
钴基合金
砂型铸造
手工造型
粘土砂
13~15
11~13
化学粘结剂砂
12~14
10~12
铸件“C-外框架”材料为ZL114A,属于轻金属合金,采用呋喃树脂砂手工造型,根据表4.1数据,选用尺寸公差等级为CT11。
根据公差等级,根据表4.2选用合理的公差数值:
表4..2铸件尺寸公差数值(摘自GB/T6414—1999)单位:
mm
毛坯铸件
基本尺寸
铸件尺寸公差等级CT
1
2
4
5
6
7
8
9
10
11
12
13
>
400~630
——
0.64
0.9
1.2
1.8
2.6
3.6
14
630~1000
0.72
1.0
1.4
2.0
2.8
4.0
16
1000~1600
0.80
1.1
1.6
2.2
3.2
4.6
18
铸件毛坯最大长度为1466mm,公差等级为CT11,所以采用的尺寸公差数值为9mm。
4.2铸件重量公差
铸件的重量公差,是以占铸件公称重量的百分比表示的铸件重量变动的允许范围。
铸件重量的公差等级应根据铸件的生产方式、铸造合金种类和铸造工艺方法选取。
一般来说,铸件的重量公差等级与铸件的尺寸公差等级应该对应选取。
因此“C-外框架”选择MT11。
表4.3铸件重量公差数值(%)
公称重量
重量公差等级MT
100~400
由表4.3可知,铸件的重量公差数值为12%,即30.4kg。
4.3铸件机械加工余量
根据资料
(1)《铸造手册》GB/T6414—1999《铸件尺寸公差与机械加工余量》规定,机械加工余量应适用于整个毛坯铸件,且该值应根据最终机械加工后成品铸件的最大轮廓尺寸和相应的尺寸范围选取。
铸件的某一部位在铸态下的最大尺寸应不超过成品尺寸与要求的加工余量及铸造总公差之和,有斜度时斜度另外考虑。
要求的机械加工余量等级共有10级,称之为A、B、C、D、E、F、G、H、J和K级共10个等级。
根据《铸造工艺手册》要求,轻金属合金手工造型砂型浇铸应选公差等级为F~H级。
处于浇注位置“底部”和“侧面”的选用“高”的等级,本次设计对于底面采用F级,侧面选择G级;
;
处于浇注位置“顶部”的选用“低”的等级,本次设计对于顶面选择H级;
根据《铸造工艺手册》GB/T6414—1999所要求的机械加工余量如下表:
表4.4要求的机械加工余量(RAM)(mm)
最大尺寸
要求的机械加工余量等级
E
F
G
H
2.5
3.5
5.5
根据铸件的尺寸公差等级、要求的机械加工余量级铸件的最大轮廓尺寸确定加工余量的数值。
铸件需要加工的表面如下:
(1)单侧加工
铸件单侧加工面如图4.1所示,编号为1、2、3:
单侧加工面尺寸计算公式为:
δ=RMA+CT/2(公式4.1)
式中:
δ—加工余量(mm)
RMA—要求的铸件加工余量(mm)
CT—铸件尺寸公差(mm)
图4.1单侧加工面示意图
(2)双侧加工面:
铸件双侧加工面如图4.2所示,编号4、5、6、7:
图4.2双侧加工面示意图
双侧加工面尺寸计算公式为:
δ=RMA+CT/4(公式4.2)
各符号意义同上。
(3)内侧加工面
铸件内侧加工面如图4.3所示,编号8、9、10、11、12
图4.2内侧加工面示意图
内部加工的加工余量公式为:
δ=RMA+CT/4(公式4.3)
各符号意义同上。
根据零件技术要求,铸件公差等级应满足GB/T6414—1999《铸件尺寸公差和机械加工余量》的规定。
铸件尺寸公差等级分为16级,表示为CT1~CT16。
铸件“C—外框架”需满足CT11级要求,具体公差数值见下表4.5:
表4.5尺寸公差数值(mm)
毛坯铸件基本尺寸
铸件毛坯最大尺寸为1466mm,尺寸公差等级满足CT11级要求,由上表查得本铸件的尺寸公差数值为9mm。
综上所述,将各个表面加工余量计算结果列在表4.6中如下:
表4.6各面机械加工余量(最大尺寸1466mm)
加工面编号
加工余量等级
RMA值
CT值
加工余量δ
6.25
7.75
根据零件图,考虑以上机械加工余量后,将后续加工结构去掉,在编号为1、3、5、7的面加上拔模斜度,再把钢套装配上,即可得到铸件图。
此外,有些圆面相隔C≤3mm,在铸件上难以铸出,决定把间隔过小的两个面合成一个面铸出,在后续加工中再把它们加工出来。
图4.4铸件实体图
5砂芯的设计
砂芯用来形成铸件的内腔、各种成形孔及外形不易起模的部分。
砂芯要满足的基本要求是:
砂芯的形状、尺寸和在砂型中的位置应与铸件的要求相适应,有足够的强度和刚度,在浇注后铸件凝固过程中砂芯所产生的气体能及时排出型外,铸件收缩时砂芯不给予大的阻力,容易清砂。
砂芯设计的主要内容:
确定砂芯的形状和个数(砂芯分块)、下芯顺序、芯头结构、核算芯头大小等。
本铸件采用呋喃树脂自硬砂造芯。
5.1砂芯的形状
砂芯的设置应满足以下几个基本原则:
(1)尽量减少砂芯的数量;
(2)复杂的砂芯分块设计;
(3)选择合适的砂芯形状,便于填砂、舂砂、安放芯骨和采取排气措施;
(4)砂芯的分盒面应尽量与砂型的分型面一致;
(5)便于下芯和合型;
(6)被分开的砂芯每段要有良好的固定条件;
对于本题目,采用呋喃树脂砂自硬化制芯,涉及不到砂芯的烘干,而保证铸件的成型、保证铸件的精度则是重要的环节。
分析铸件结构,需要用到多个砂芯成型,铸件共有16处需要用到砂芯,如下图5-1所示,15处编号1~16:
图5.1需要砂芯形成的部位
15个砂芯的形状如下图5.2所示:
砂芯2
砂芯1
砂芯4
砂芯3
砂芯6
砂芯5
砂芯8
砂芯7
砂芯10
砂芯9
砂芯12
砂芯11
砂芯14
砂芯13
砂芯15
砂芯16
图5.2各砂芯的形状
砂芯说明:
铸件的位置需要大量的悬臂砂芯,所以悬臂砂芯的安放特别的重要。
我们设计1号砂芯、2号砂芯和16号砂芯是加大加高的芯头,三个砂芯中分别放置一个钢结构芯盘。
悬臂砂芯用芯骨连接到上述钢结构芯盘中,其中,3号、4号、13号和14号砂芯的芯骨插入1号砂芯的钢结构芯盘中,7号、8号、9号、10号砂芯用芯骨插入到2号砂芯的钢结构芯盘中,5号、6号、11号、12号和15号砂芯用芯骨插入到16号砂芯的钢结构芯盘中。
由于本铸件砂芯比较复杂,我们采用组合砂芯,即在下芯之前将多个砂芯组合为一个整体砂芯,再把组合砂芯一次性放到砂箱里,这样便于砂芯装配、检查和下芯。
为了使钢套与铝合金框架连接牢固,在浇注之前把钢套装到砂芯15上。
图5.2砂芯组合图
5.2芯头的结构尺寸
砂芯主要靠芯头固定在砂型中。
对于垂直芯头,必须要有足够的尺寸,以保证其轴线垂直、牢固地固定砂型上。
对于水平砂芯,必须有足够的芯头长度,以承受砂芯的重力和金属液的浮力。
芯头与芯头座之间有适宜的间隙,以使砂型与砂芯既能保证装配,又能确保铸件的尺寸精度。
本次设计所采用的砂芯芯头共有2种,。
其中,Ⅰ型属于悬臂砂芯芯头,Ⅱ型是用芯骨连接的水平砂芯。
Ⅰ型用于砂芯1和砂芯2,Ⅱ型用于砂芯15和16。
Ⅰ型属于悬臂芯头,采用加大加长芯头的方法,将砂芯的重心移入芯头的支撑面内。
根据资料
(1)《铸造工艺手册》公式,当D或h>
150mm时,h1=(1.5~1.8)h,l>
L,芯头尺寸与斜度如图5.2所示。
图5.2Ⅰ型悬臂芯头尺寸
Ⅱ型水平芯头,右端圆柱芯头削去一部分,用于芯头的定位,左边芯头较大,用于承载其他砂芯的重量。
图5.3Ⅱ型水平芯头尺寸
为了下芯和合型的方便,芯头应有一定的斜度,心头与芯座之间应有一定的间隙,水平芯头示意图如下图5.6所示:
图5.6水平芯头示意图
参照资料1铸造手册,设置各芯头S1、S2、S3数值如下表所示:
表5.1芯头参数设置
芯头编号
S1
S2
S3
Ⅰ型悬臂砂芯
6.0
Ⅱ型承载砂芯
5.0
8.0
Ⅱ型圆柱砂芯
3.0
为了快速下芯,合型以及保证铸件的质量,方便砂芯中产生气体的排出,在砂芯的顶部应该设置“压环”;
为了防止由于造型时没有完全吹净的极少沙粒引起的砂芯位置的不准确,需要在砂芯的底部设置“集砂槽”。
压环、防压环和集砂槽的示意图如下图5.7所示,压环、防压环和集砂槽的尺寸列入下表5.2:
图5.7压环、防压环、集砂槽示意图
表5.2:
压环,防压环,集砂槽尺寸
a
b
c
r
1.5
25
40