第6章汽车覆盖件成形工艺及模具设计Word文档下载推荐.docx
《第6章汽车覆盖件成形工艺及模具设计Word文档下载推荐.docx》由会员分享,可在线阅读,更多相关《第6章汽车覆盖件成形工艺及模具设计Word文档下载推荐.docx(36页珍藏版)》请在冰豆网上搜索。
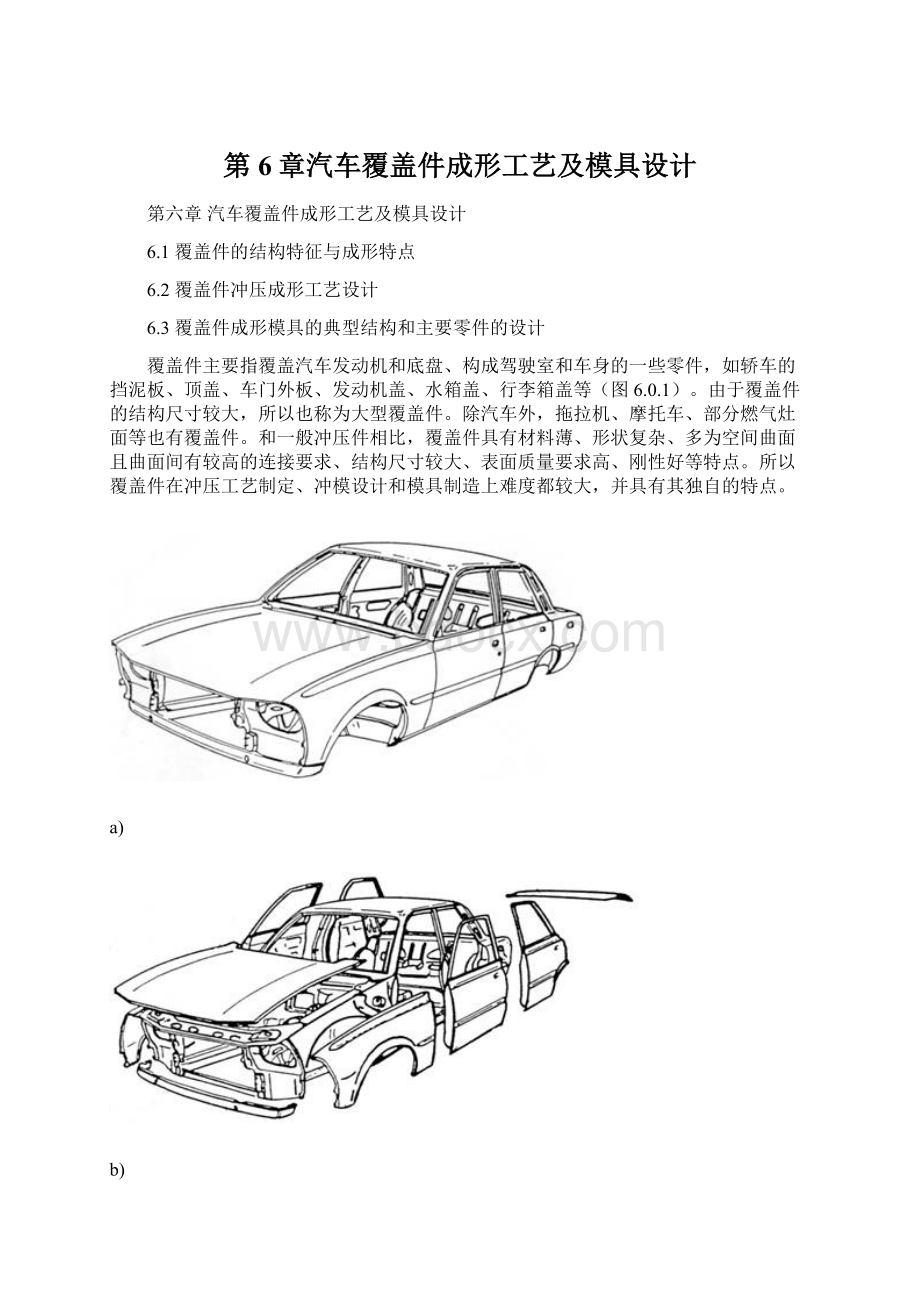
通过对基本形状的零件冲压变形特点的分析,并考虑各基本形状之间的相互影响,就能够分析出覆盖件的主要变形特点,判断出各部位的变形难点。
6.1.2覆盖件的成形特点
覆盖件的一般拉深过程如图6.1.2所示,包括:
(a)坯料放入,坯料因其自重作用有一定程度的向下弯曲;
(b)通过压边装置压边,同时压制拉深筋;
(c)凸模下降,板料与凸模接触,随着接触区域的扩大,板料逐步与凸模贴合;
(d)凸模继续下移,材料不断被拉入模具型腔,并使侧壁成形;
(e)凸、凹模合模,材料被压成模具型腔形状;
(f)继续加压使工件定型,凸模到达下止点;
(g)卸载。
由于覆盖件有形状复杂、表面质量要求高等特点,与普通冲压加工相比有如下成形特点:
(a) (b) (c) (d)
图6.1.1覆盖件的基本形状
(a)法兰形状;
(b)轮廓形状;
(c)侧壁形状;
(d)底部形状
图6.1.2覆盖件拉深过程示意图
)坯料放入;
)压边;
)板料与凸模接触;
)材料拉入;
)压型;
)下止点;
)卸载
(1)汽车覆盖件冲压成形时,内部的毛坯不是同时贴模,而是随着冲压过程的进行而逐步贴模。
这种逐步贴模过程,使毛坯保持塑性变形所需的成形力不断变化;
毛坯各部位板面内的主应力方向与大小、板平面内两主应力之比等受力情况不断变化;
毛坯(特别是内部毛坯)产生变形的主应变方向与大小、板平面内两主应变之比等变形情况也随之不断地变化;
即:
毛坯在整个冲压过程中的变形路径不是一成不变的,而是变路径的。
(2)成形工序多。
覆盖件的冲压工序一般要4~6道工序,多的有近10多道工序。
要获得一个合格的覆盖件,通常要经过下料、拉深、修边(或有冲孔)、翻边(或有冲孔)、冲孔等工序才能完成。
拉深、修边和翻边是最基本的三道工序。
(3)覆盖件拉深往往不是单纯的拉深,而是拉深、胀形、弯曲等的复合成形。
不论形状如何复杂,常采用一次拉深成形。
(4)由于覆盖件多为非轴对称、非回转体的复杂曲面形状零件,拉深时变形不均匀,主要成形障碍是起皱和拉裂。
为此,常采用加工艺补充面和拉深筋等控制变形的措施。
(5)对大型覆盖件拉深,需要较大和较稳定的压边力。
所以,广泛采用双动压力机。
(6)材料多采用如08钢等冲压性能好的钢板,且要求钢板表面质量好、尺寸精度高。
(7)制定覆盖件的拉深工艺和设计模具时,要以覆盖件图样和主模型为依据。
覆盖件图样是在主图样板的基础上绘制的,在覆盖件图样上只能标注一些主要尺寸,以满足与相邻的覆盖件的装配尺寸要求和外形的协调一致,尺寸一般以覆盖件的内表面为基准来标注。
主模型是根据定型后的主图板、主样板及覆盖件图样为依据制作的尺寸比例为1:
1的汽车外形的模型。
它是模具、焊装夹具和检验夹具制造的标准,常用木材和玻璃钢制作。
主模型是覆盖件图必要的补充,只有主模型才能真正表示覆盖件的信息。
由于CAD/CAM技术的推广应用,主模型正在被计算机虚拟实体模型所代替。
传统的由油泥模型到主模型的汽车设计过程,正在被概念设计、参数化设计等现代设计方法所取代,因而从根本上改变了设计制造过程,大大提高了设计与制造周期,提高了制造精度。
6.1.3覆盖件的成形分类
由于汽车覆盖件的形状多样性和成形复杂性,对汽车覆盖件冲压成形进行科学分类就显得十分重要。
汽车覆盖件的冲压成形以变形材料不发生破裂为前提,一个覆盖件成形时,各部位材料的变形方式和大小不尽相同,但通过试验方法定量地找出局部变形最大的部位,并确定出此部位材料的变形特点,归属哪种变形方式,对应于哪些主要成形参数,其参数值范围多大,这样在冲压成形工艺设计和选材时,只要注意满足变形最大部位的成形参数要求,就可以有效地防止废品产生。
同时,有了不同成形方式所要求的成形参数指标大小和范围,薄板冶金生产者就能够有目的地采取相应的冶金工艺措施,保证材料的某一、二个成形参数指标达到要求,从而能实现材料的对路供应,使材料的变形潜力得到最大程度的发挥,而又毋需一味地要求材料的各项力学性能都达到最高级别。
汽车覆盖件的冲压成形分类以零件上易破裂或起皱部位材料的主要变形方式为依据,并根据成形零件的外形特征、变形量大小、变形特点以及对材料性能的不同要求,可将汽车覆盖件冲压成形分为五类:
深拉深成形类、胀形拉深成形类、浅拉深成形类、弯曲成形类和翻边成形类。
6.1.4覆盖件的主要成形障碍及其防止措施
由于覆盖件形状复杂,多为非轴对称、非回转体的复杂曲面形状零件,因而决定了覆盖件拉深时的变形不均匀,所以拉深时的起皱和开裂是主要成形障碍。
另外覆盖件成形时,同一零件上往往兼有多种变形性质,例如直边部分属弯曲变形,周边的圆角部分为拉深,内凹弯边属翻边,内部窗框以及凸、凹形状的窝和埂则为拉胀成形。
不同部位上产生起皱的原因及防止方法也各不相同。
同时,由于各部分变形的相互牵制,覆盖件成形时材料被拉裂的倾向更为严重。
1.覆盖件成形时的起皱及防皱措施
在图6.1.2所示覆盖件的拉深过程中,当板料与凸模刚开始接触,板面内就会产生切向压应力,随着拉深的进行,当压应力超过允许值时,板料就会失稳起皱。
薄板失稳起皱其实质是由板面内的压应力引起的。
但是,产生失稳起皱的原因的直观表现形式是多种多样的,常见的拉深变形起皱有:
圆角凸缘上的拉深起皱、直边凸缘上的诱导皱纹、斜壁上的内皱等。
解决的办法是增加工艺补充材料或设置拉深筋。
除材料的性能因素外,各种拉深条件对失稳起皱有如下影响:
①拉深时板料的曲率半径越小越容易引起压应力,越容易起皱;
②凸模与板料的初始接触位置越靠近板料的中央部位,引起的压应力越小,产生起皱的危险性就越小;
③从凸模与板料开始接触到板料全面贴合凸模,贴模量越大,越容易发生起皱,且起皱越不容易消除;
④拉深的深度越深,越容易起皱;
⑤板料与凸模的接触面越大,压应力越靠近模具刃口或凸模与板料的接触区域,由于接触对材料流动的约束,所以随着拉深成形的进行而使接触面增大,对起皱的产生和发展的抑制作用将增加。
生产实际中,可结合覆盖件的几何形状、精度要求和成形特点等情况,根据失稳起皱的力学机理以及拉深条件对失稳起皱的影响等因素,从覆盖件的结构、成形工艺以及模具设计多方面采取相应的防皱措施。
对于形状比较简单变形比较容易的零件,或零件的相对厚度较大的零件,采用平面压边装置即可防止起皱。
对形状复杂变形比较困难的零件,则要通过设置合理的工艺补充面和拉深筋等方法才能防止起皱。
2.覆盖件成形时的开裂及防裂措施
覆盖件成形时的开裂是由于局部拉应力过大造成的,由于局部拉应力过大导致局部大的胀形变形而开裂。
开裂主要发生在圆角部位、压窝和窗框四角凸模圆角处厚度变薄较大的部位。
同时,凸模与坯料的接触面积过小、拉深阻力过大等都有可能导致材料局部胀形变形过大而开裂。
也有由于拉深阻力过大、凹模圆角过小或凸模与凹模间隙过小等原因造成的整圈破裂。
为了防止开裂,应从覆盖件的结构、成形工艺以及模具设计多方面采取相应的措施。
覆盖件的结构上,可采取的措施有:
各圆角半径最好大一些、曲面形状在拉深方向的实际深度应浅一些、各处深度均匀一些、形状尽量简单且变化尽量平缓一些等。
拉深工艺方面,可采取的主要措施有:
拉深方向尽量使凸模与坯料的接触面积大、合理的压料面形状和压边力使压料面各部位阻力均匀适度、降低拉延深度、开工艺孔和工艺切口(图6.1.3)等。
模具设计上,可采取设计合理的拉深筋、采用较大的模具圆角、使凸模与凹模间隙合理等措施。
对防皱和防裂措施所涉及的一些内容,将在后面的工艺和模具设计内容中介绍。
图6.1.3工艺孔和工艺切口
6.2.1确定冲压方向
覆盖件的冲压工艺包括拉深、修边、翻边等多道工序,确定冲压方向应从拉深工序开始,然后制定以后各工序的冲压方向。
应尽量将各工序的冲压方向设计成一致,这样可使覆盖件在流水线生产过程中不需要进行翻转,便于流水线作业,减轻操作人员的劳动强度,提高生产效率,也有利于模具制造。
1.拉深方向的选择
2.拉深冲压方向对拉深成形的影响
所选的拉深方向是否合理,将直接影响:
凸模能否进入凹模、毛坯的最大变形程度、是否能最大限度的减少拉深件各部分的深度差、变形是否均匀、能否充分发挥材料的塑性变形能力、是否有利于防止破裂和起皱。
同时还影响到工艺补充部分的多少,以及后续工序的方案。
1.拉深方向选择的原则
①保证能将拉深件的所有空间形状(包括棱线、肋条、和鼓包等)一次拉深出来,不应有凸模接触不到的死角或死区,要保证凸模与凹模的工作面的所有部位都能够接触。
如图6.1.4a,若选择冲压方向A,则凸模不能全部进人凹模,造成零件右下部的a区成为“死区”,不能成形出所要求的形状。
选择冲压方向B后,则可以使凸模全部进人凹模,成形出零件的全部形状。
图6.1.4b是按拉深件底部的反成形部分最有利干成形面确定的拉深方向,若改变拉深方向则不能保证90·
角。
图6.1.4拉深方向确定实例
②有利于降低拉深件的深度。
拉深深度太深,会增加拉深成形的难度,容易产生破裂、起皱等质量问题;
拉深深度太浅,则会使材料在成形过程中得不到较大的塑性变形,覆盖件刚度得不到加强。
因此,所选择的拉深方向应使拉深件的深度适中,既能充分发挥材料的塑性变形能力,又能使成形过程顺利完成。
③尽量使拉深深度差最小,以减小材料流动和变形分布的不均匀性。
图6.1.5a深度差大,材料流动性差;
而按图a中所示的点划线改变拉深方向后成为图b,使两侧的深度相差较小,材料流动和变形差减小,有利于成形。
图c所示是对一些左右件可利用对称拉深一次两件成形,便于确定合理的拉深方向,使进料阻力均匀。
图6.1.5拉深深度与拉深方向
④保证凸模开始拉深时与拉深毛坯有良好的接触状态,开始拉深时凸模与拉深毛坯的接触面积要大,接触面应尽量靠近冲模中心。
图6.1.5所示为凸模开始拉深时与拉深毛坯的接触状态示意图。
图a所示上图由于接触面积小,接触面与水平面夹角
大,接触部位容易产生应力集中而开裂。
所以凸模顶部最好是平的,并成水平面。
可以通过改变拉深方向或压料面形状等方法增大接触面积。
图b所示上图由于开始接触部位偏离冲模中心,在拉深过程中毛坯两侧的材料不能均匀拉入凹模,而且毛坯可能经凸模顶部窜动使凸模顶部磨损加快并影响覆盖件表面质量。
图c所示上图由于开始接触的点既集中又少,在拉深过程中毛坯可能经凸模顶部窜动而影响覆盖件表面质量。
同样可以通过改变拉深方向或压料面形状等方法增大接触面积。
图d由于形状上有900的侧壁要求决定了拉深方向不能改变,只有使压料面形状为倾斜面,使两个地方同时接触。
a)
b)
c)
d)
图6.2.5凸模开始拉深时与拉深毛坯的接触状态示意图
还应指出,拉深凹模里的凸包形状必须低于压料面形状,否则在压边圈还未压住压料面时凸模会先与凹模里的凸包接触,毛坯因处于自由状态而引起弯曲变形,致使拉深件的内部形成大皱纹甚至材料重叠。
2.修边方向的确定及其修边形式
(1)修边方向的确定
所谓修边就是将拉深件修边线以外的部分切掉。
理想的修边方向,是修边刃口的运动方向和修边表面垂直。
若修边是在拉深件的曲面上,则理想的修边方向有无数个,这是在同一工序中不可能实现的。
因此,必须允许修边方向与修边表面有一个夹角。
该夹角的大小一般不应小于10°
,如果太小,材料不是被切断而是被撕开,严重的会影响修边质量。
覆盖件拉深成形后,由于修边和冲孔位置不同,其修边和冲孔工序的冲压方向有可能不同。
由于覆盖件在修边模中的摆放位置只能是一个,如果采用修边冲孔复合工序,冲压方向在同一工序中可能有两个或两个以上。
这时,在模具结构上就要采取特殊机构来实现。
(2)修边形式
修边形式可分为垂直修边、水平修边和倾斜修边三种,如图6.2.6所示。
图6.2.6修边形式示意图
a)垂直修边b)水平修边c)倾斜修边
当修边线上任意点的切线与水平面的夹角
小于300时,采用垂直修边。
由于垂直修边模结构最为简单,废料处理也比较方便,所以在进行工艺设计时应优先选用。
拉深件的修边位置在侧壁上时,由于侧壁与水平面的夹角较大,为了接近理想的冲裁条件,故采用水平修边。
凸模(或凹模)的水平运动可通过斜滑块机构或加装水平方向运动的液压来实现。
所以模具的结构比较复杂。
由于修边形状的限制,修边方向需要倾斜一定的角度,这时只好采用倾斜修边。
倾斜修边模的结构也是采用斜滑块机构或加装水平方向运动的液压来实现。
3.翻边方向的确定及其翻边形式
(1)翻边方向的确定
翻边工序对于一般的覆盖件来说是冲压工序的最后成形工序,翻边质量的好坏和翻边位置的准确度,直接影响整个汽车车身的装配和焊接的质量。
合理的翻边方向应满足下列两个条件:
①翻边凹模的运动方向和翻边凸缘、立边相一致;
②翻边凹模的运动方向和翻边基面垂直。
对于曲面翻边,翻边线上包含了若干段不同性质的翻边,要同时满足以上两个条件是不可能的。
对于曲面翻边方向的确定,要考虑下面两个问题:
①使翻边线上任意点的切线尽量与翻边方向垂直;
②使翻边线两端连线上的翻边分力尽量平衡。
因此,对于曲线翻边的翻边方向,一般取翻边线两端点切线夹角平分线,而不取翻边线两端点连线的垂直方向,如图6.2.7所示。
图6.2.7曲线翻边示意图 图6.2.8各种典型的覆盖件翻边
(2)翻边形式
按翻边凹模的运动方向,翻边形式可分为垂直翻边、水平翻边和倾斜翻边三种,如图6.2.8所示。
图a、b为垂直翻边;
图d、e为水平翻边;
图c为倾斜翻边。
6.2.2拉深工序的工艺处理
拉深件的工艺处理包括设计工艺补充、压料面形状、翻边的展开、冲工艺孔和工艺切口等内容,是针对拉深工艺的要求对覆盖件进行的工艺处理措施。
工艺补充部分的设计
图6.2.9工艺补充示意图
为了实现覆盖件的拉深,需要将覆盖件的孔、开口、压料面等结构根据拉深工序的要求进行工艺处理,这样的处理称为工艺补充。
工艺补充是拉深件不可缺少的部分,工艺补充部分在拉深完成后要将其修切掉,过多的工艺补充将增加材料的消耗。
因此,应在满足拉深条件下,尽量减少工艺补充部分,以提高材料的利用率,图6.2.9为工艺补充示意图。
工艺补充设计的原则:
1.内孔封闭补充原则(为防止开裂采用与冲孔或工艺切口除外);
2.简化拉深件结构形状原则(图6.2.10);
3.对后工序有利原则(如对修边、翻边定位可靠,模具结构简单)。
a) b) c)
a)简化轮廓形状;
b)增加局部侧壁高度;
c)简化压料面形状
图6.2.10简化拉深件结构形状
d) e)
图6.2.11常用的几种工艺补充部分
1.修边线在压料面上,垂直修边 b) 修边线在拉深件底面上,垂直修边
c)修边线在拉深件翻边展开斜面上,垂直修边 d) 修边线在拉深件斜面上,垂直修边
e)修边线在拉深件侧壁上,水平修边或倾斜修边
图6.2.11是根据修边位置的不同常采用的几种工艺补充部分。
修边线在压料面上、垂直修边时,如图a所示。
为了在修磨拉深筋时不影响到修边线,修边线距拉深筋的距离
应有一定数值。
一般取
=15~25
,拉深筋宽时取大值,窄时取小值。
修边线在拉深件底面上、垂直修边时,如图b所示。
修边线距凸模圆角半径
的距离
应保证不因凸模圆角半径的磨损影响到修边线,一般取
=3~5
。
=3~10
,拉延深度浅时取小值,深时取大值。
如凹模圆角半径
是工艺补充的组成部分,一般取
=6~10
以外的压料面部分
可按一根拉深筋或一根半拉深筋确定。
修边线在拉深件翻边展开斜面上、垂直修边时,如图c所示。
和图b中的
值相似。
修边方向与修边表面的夹角
不应小于500~600,因
角过小时,在采用垂直修边时,会使切面过尖,且刃口变钝后修边处容易产生毛刺。
修边线在拉深件斜面上、垂直修边时,如图d所示,因修边线距凸模圆角半径
是变化的,一般只控制几个最小尺寸。
为了从拉深模中取出拉深件和放入修边模定位方便,拉深件的侧壁C的侧壁斜度
一般取=30~100。
考虑拉深件定位稳定、可靠和根据压料面形状的需要,一般取C=10~20
水平修边或倾斜修边主要应用在修边线在拉深件的侧壁上时,如图6.2.11e。
当侧壁与水平面的夹角接近或等于直角时,采用水平修边。
而侧壁与水平面的夹角较大时,特别是侧壁与水平面的夹角在450左右时,则采用倾斜修边。
此时,因修边线距凹模圆角半径
由于修边模要采用改变压力机滑块运动方向的机构,为了考虑修边模的凹模强度,修边线距凹模圆角半径
应尽量大,一般取
>
25
2.压料面的设计
压料面是工艺补充部分组成的一个重要部分,即凹模圆角半径以外的部分。
压料面的形状不但要保证压料面上的材料不皱,而且应尽量造成凸模下的材料能下凹以降低拉深深度,更重要的是要保证拉入凹模里的材料不皱不裂。
因此,压料面形状应由平面、圆柱面、双曲面等可展面组成,图6.2.12,图6.2.13所示。
图6.2.12压料面形状
1-平面;
2-圆柱面;
3-圆锥面;
4-直曲面
图6.2.13压料面与冲压方向的关系
1-压边圈;
2-凹模;
3-凸模
压料面有两种:
一种是压料面就是覆盖件本身的一部分;
另一种是由工艺补充部分补充而成。
压料面就是覆盖件本身的一部分时,由于形状是既定的,为了便于拉深,虽然其形状能做局部修改,但必须在以后的工序中进行整形以达到覆盖件凸缘面的要求。
若压料面是由工艺补充部分补充而成,则要在拉深后切除。
确定压料面形状必须考虑以下几点:
降低拉深深度
降低拉深深度,有利于防皱防裂。
如果压料面就是覆盖件本身的一部分时,不存在降低拉深深度的问题。
如果压料面是由工艺补充部分补充而成,必要时就要考虑降低拉深深度的问题。
图6.2.14所示是降低拉深深度的示意图,图6.2.14a是未考虑降低拉深深度的压料面形状,图6.2.14b是考虑降低拉深深度的压料面形状,图中斜面与水平面的夹角
称为压料面的倾角。
对于斜面和曲面压料面,压料面倾角
一般不应大于450;
对于双曲面压料面,压料面倾角
应小于300。
=00时是平的压料面,压料效果最好,但很少有全部压料面全是平的覆盖件,且此时拉延深度最大,容易拉皱和拉裂。
压料面倾角太大,也容易拉皱,还会给压边圈强度带来一定的影响。
图6.2.14降低拉延深度的示意图
1.凸模对毛坯一定要有拉伸作用
这是确定压料面形状必须充分考虑的一个重要因素。
只有使毛坯各部分在拉深过程中处于拉伸状态,并能均匀地紧贴凸模,才能避免起皱。
有时为了降低拉延深度而确定的压料面形状,有可能牺牲了凸模对毛坯的拉伸作用,这样的压料面形状是不能采用。
只有当压料面的展开长度小于凸模表面的展开长度时,凸模才对毛坯产生拉伸作用。
如图6.2.15a所示,只有压料面的展开长度
小于凸模表面的展开长度
时才能产生拉伸作用。
有些拉深件虽然压料面的展开长度比凸模表面的展开长度短,可是并不一定能保证最后不起皱。
这是因为从凸模开始接触毛坯到下止点的拉深过程中,在每一瞬间位置的压料面展开长度比凸模表面的展开长度有长、有短,短则凸模使毛坯产生拉伸作用,长则因拉伸作用减小甚至无拉伸作用导致起皱。
若拉深过程中形成的皱纹浅而少,再继续拉深时则有可能消除,最后拉深出满意的拉深件来;
若拉深过程中形成的皱纹多或深,再继续拉深时也无法消除,最后留在拉深件上。
如图6.2.15b所示的压料面形状,虽然压料面的展开长度比凸模表面的展开长度短,可是压料面夹角
比凸模表面夹角
小,因此在拉深过程中的几个瞬间位置因“多料”产生了起皱。
所以在确定压料面形状时,还要注意使
<
1800。
a) b)
图6.2.15凸模对毛坯产生拉伸作用的条件
3.工艺孔和工艺切口
在制件上压出深度较大的局部突起或鼓包,有时靠从外部流入材料已很困难,继续拉深将产生破裂。
这时,可考虑采用冲工艺孔或工艺切口,以从变形区内部得到材料补充。
如图6.1.3所示。
工艺孔或工艺切口的位置、大小和形状,应保证不因拉应力过大而产生径向裂口,又不能因拉应力过小而形成皱纹,缺陷不能波及覆盖件表面。
工艺孔或工艺切口必须设在拉应力最大的拐角处,因此冲工艺孔或工艺切口的位置、大小、形状和时间应在调整拉深模时现场试验确定。
由于模具制造装配