加氢裂化开工过程事故汇编.docx
《加氢裂化开工过程事故汇编.docx》由会员分享,可在线阅读,更多相关《加氢裂化开工过程事故汇编.docx(15页珍藏版)》请在冰豆网上搜索。
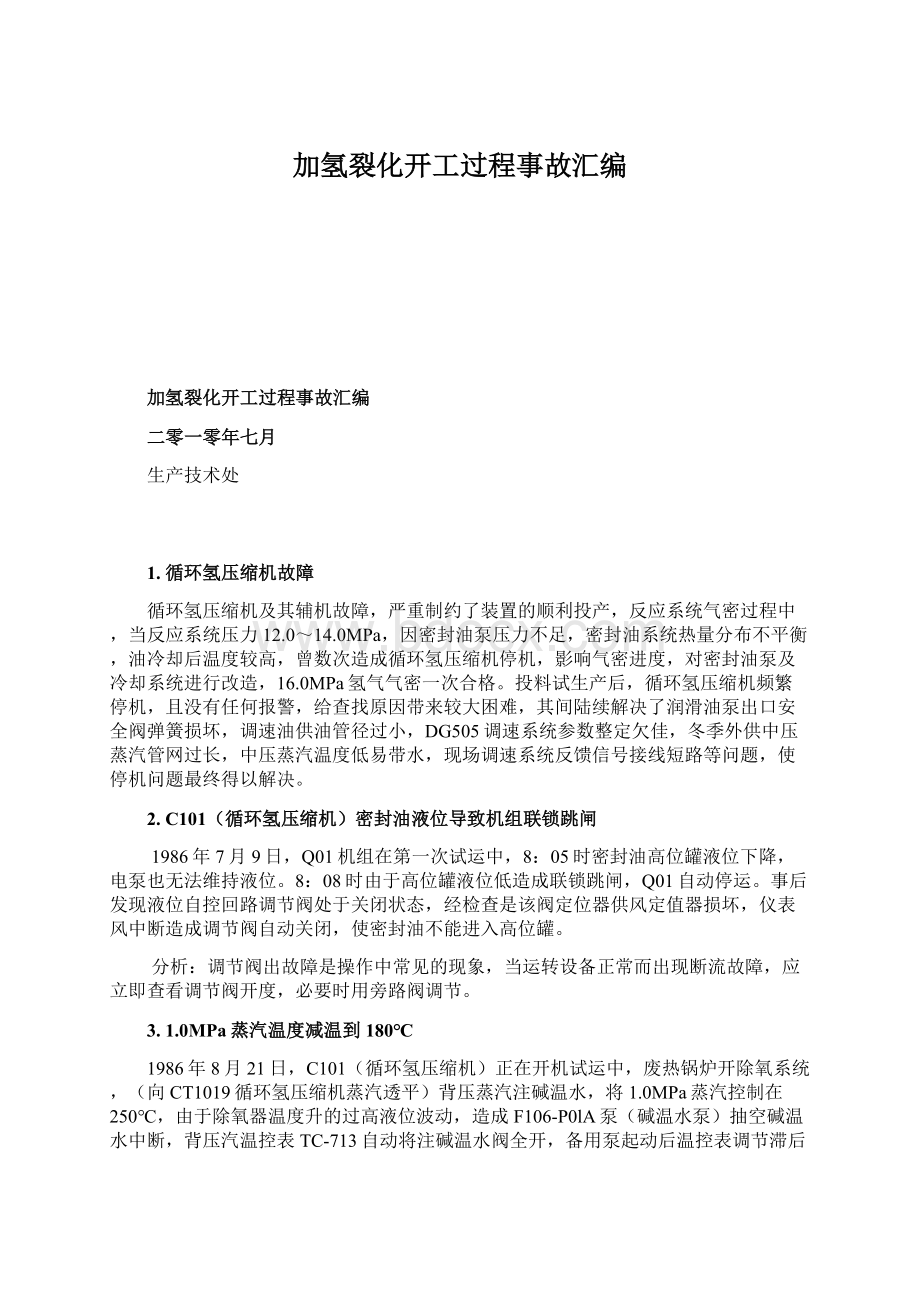
加氢裂化开工过程事故汇编
加氢裂化开工过程事故汇编
二零一零年七月
生产技术处
1.循环氢压缩机故障
循环氢压缩机及其辅机故障,严重制约了装置的顺利投产,反应系统气密过程中,当反应系统压力12.0~14.0MPa,因密封油泵压力不足,密封油系统热量分布不平衡,油冷却后温度较高,曾数次造成循环氢压缩机停机,影响气密进度,对密封油泵及冷却系统进行改造,16.0MPa氢气气密一次合格。
投料试生产后,循环氢压缩机频繁停机,且没有任何报警,给查找原因带来较大困难,其间陆续解决了润滑油泵出口安全阀弹簧损坏,调速油供油管径过小,DG505调速系统参数整定欠佳,冬季外供中压蒸汽管网过长,中压蒸汽温度低易带水,现场调速系统反馈信号接线短路等问题,使停机问题最终得以解决。
2.C101(循环氢压缩机)密封油液位导致机组联锁跳闸
1986年7月9日,Q01机组在第一次试运中,8:
05时密封油高位罐液位下降,电泵也无法维持液位。
8:
08时由于高位罐液位低造成联锁跳闸,Q01自动停运。
事后发现液位自控回路调节阀处于关闭状态,经检查是该阀定位器供风定值器损坏,仪表风中断造成调节阀自动关闭,使密封油不能进入高位罐。
分析:
调节阀出故障是操作中常见的现象,当运转设备正常而出现断流故障,应立即查看调节阀开度,必要时用旁路阀调节。
3.1.0MPa蒸汽温度减温到180℃
1986年8月21日,C101(循环氢压缩机)正在开机试运中,废热锅炉开除氧系统,(向CT1019循环氢压缩机蒸汽透平)背压蒸汽注碱温水,将1.0MPa蒸汽控制在250℃,由于除氧器温度升的过高液位波动,造成F106-P0lA泵(碱温水泵)抽空碱温水中断,背压汽温控表TC-713自动将注碱温水阀全开,备用泵起动后温控表调节滞后,大量碱温水注入C101背压汽中,使1.0MPa蒸汽温度降到180℃。
故障出现后,紧急将TC-713改手动将温度提回到250℃。
分析:
加氢裂化装置的低压汽是排放到厂管网,1.0MPa蒸汽饱和温度为170℃,接近170℃时会造成蒸汽带水事故。
我厂热裂化装置和瓦斯压缩站使用以1.0MPa蒸汽为动力的汽轮机,蒸汽带水会造成汽轮机损坏,对蒸汽温度的控制万不可大意。
4.C102向制氢返回氢中断
1986年9月2日,C102B机(新氢压缩机)由于一级入口滤网堵需更换到C102A机。
启动C102A机后,由于新氢管路太脏,一级和二级入口滤网立即堵塞,被迫紧急停机,造成制氢返回氢中断,制氢装置被迫切断进料。
分析:
制氢反应炉需要加氢C102提供返回氢作反应配氢,返回氢中断制氢将被迫切断进料,反之又影响加氢,这是一个联系两个装置的重要环节,换机时一定要注意将返氢线打开,此次故障产生于试运阶段,所以影响不大。
正常生产操作则会产生重大波动。
5.C101更换转子
1989年7月4日装置第12周期开工,18时当循环氢压缩机C101转速由3000rpm向8000rpm提速时,机组出现严重振动,厂部决定进行检修。
经检查发现,迷宫密封磨损,蜂窝密封磨损,平衡鼓镀层有剥落现象,转子叶轮有结垢现象,吸入口与级间扩压器内存有蜡油,原转子已不能再用,厂部决定更换国产新转子,以后运转情况表明,国产转子的性能优于进口转子。
分析:
因循环油进料孔板FRC-157法兰泄漏,装置进行21巴/分紧急放空降压时,部分较重的油冲进入C101入口管道,当C101重新启动时循环气体带液造成机组振动,损伤转子与密封件,这种现象车间已估计到,但是当时条件不允许进行处理,而是“抓紧时间开工”,结果是相反的。
此次教训应牢牢记住,不能盲目执行上级命令。
6.循环氢压缩机喘振
4月11日装置停工准备进行第二次催化剂再生,4月24日开C101循环氢压缩机循环升温,15:
50时接班完毕后,岗位人员发现温控表TIC-210输出在50%以上,B阀处于全开的位置,E101与E103循环氢/反应产物换热器换热流程短路。
为提高循环气换热温度,用仪表手动将B阀关闭,此刻C101入口流量立刻下降产生喘振,机岗位反应迅速立即将反飞动控制阀全开,没有造成机组损坏。
事后查明TIC-210回路A阀手动轮开在关闭位置上,调节器信号对该阀无作用,当B阀关闭时实际上造成反应流程中断C101断流,故障当时的瞬间C101入口压力2.7MPa出口压力5.3MPa。
这是一起严重的未遂事故,幸亏机岗位反应快否则C101转子非损坏不可。
上一班开机流程检查不细,恰巧停工冷却时TIC-210的手动输出使B阀打开,反应流程畅通顺利开机,但却埋下了事故隐患。
接班的检查不细。
当发现与正常不同现象应追问清楚,但没有那样做。
开工期间要特别注意流程正确,如发现异常一定要弄清楚再调整。
7.新氢机出口超压现象
1994年开工切换机组过程中,此时系统压力已达到6.OMPa,新氢机由意大利机切换至沈阳机。
按规程,先开三回一线机组自身循环,在未关小三回一阀的情况下,开启出口阀,此时系统压力经三回一反窜至入口,入口压力超高经机压缩后,出口压力猛增至12.OMPa,出口震动极大,经紧急停机后,幸未发生事故。
吸取本次经验后,在开出口阀前,先开出口放空阀开机,在开启出口阀同时,关闭出口放空,避免了上述问题。
8.循氢机调速过快,造成循氢带液
1995年,检修后的开工,进油后,循氢机手动提速,转速由7000转/分向9000转/分提,由于提速过快,造成循氢大量带液,瞬时,高分液面满。
循氢罐液面达到高位报警线,经迅速降低转速、降量,及时脱液后,避免了一次可能发生的严重事故。
经验教训,在循氢机提速过程中,首先应通知反应岗位,并按规程提速,以免发生循氢带液,甚至带入循氢机,造成毁机的重大问题。
9.齐鲁石化缓和加氢裂化开工中出现的问题及处理方法
90年1月3日凌晨循环氢压缩机突然停机,精制反应器入口温度失控超温,压力超高。
紧急泄压重新开工后,精制反应器床层压差由停机前的0.25MPa升至0.3MPa。
15日又进一步升至0.49MPa。
25日又突然降回到0.24MPa,与此同时精制油氮含量节节升高,虽不断提高精制床层温度,但氮含量仍升高到143ppm,在这段时间内裂化床层的温度也相应提高,2月2日温度已经升到380℃方能维持大于350℃馏分的转化率在35%左右。
2月1日发现精制反应器一床层中上部外壁出现过热点,过热区不断扩大,2月9日超温区中心壁温已经达到320℃,故停工检查处理。
经过开盖检查和再生卸出催化剂的观测,发现一床层上部到顶分配器塔盘均已被焦炭堵塞,并且在贴近器壁处有一深1.2米以上的洞穴直通超温中心部,内保温表面有一主裂纹和多条小裂纹汇集在超温中心部,另外再生后一床层催化剂大约粉碎25%,床层水平断面的中心部位粉化的更为严重,这也是压差增大的一个原因。
10.3.GAT-183齿轮箱轴烧坏
92年7月19日22:
30分启动GAT-183(密封油蒸汽透平泵),准备开循环氢压缩机,在开GAT-183前做好了开泵前的一切准备工作;开启后发现此泵振动较大,立即向上级有关部门汇报并来人查看未做任何处理,交接班时下个班也未发现任何问题,到1:
30分发现GAT-183齿轮箱轴烧坏。
事后进行事故分析,主要原因是检修不过关造成烧轴,另一方面有可能是润滑油少的原因造成烧轴。
经验教训:
(1)此泵检修完后未进行认真检查。
(2)操作人员对事故判断能力较差。
(3)没有严格按操作规程执行,润滑油位低。
(4)有关上级部门对此事不够重视,岗位人员应继续向上级汇报。
11.反应转化率过高
1986年10月28日8:
30时反应提量,19:
00时反应提量到80吨/时,反应温度控制过高,单程转化率高达82.5%,引起分馏操作波动。
20:
00时T103(产品分馏塔)油过轻,P108(塔底抽出泵)泵抽空,F104被迫熄火,反应被迫降温降量,产品转不合格罐,影响正常生产达6小时。
分析:
反应单程转化率设计为60%,过高或过低均造成分馏不正常,特别是反应温度超高时,深度转化的反应生成油进入分馏系统后,轻者造成冲塔,严重会产生超压事故。
转化率是反应岗位重要控制指标,调节中应缓慢进行把握好与进料量相适应的反应温度。
12.反应深度过大影响分馏
1987年10月22日第四周期开工,反应进油后Pll2(分馏单元最后一分馏塔底泵即尾油泵)处于半抽空状态,21:
00时各塔液面指示全满,21:
30时反应被迫降量,但由于降量过急温度降得慢,造成反应深度大,单程转化率达87.5%,造成T101(脱丁烷塔)冲塔,D104(T101回流罐)满,液态烃放人火炬时形成火雨将火炬下烧着,报火警。
分析:
反应深度是反应岗位的关键指标,绝不能出差错,处理应本着先降温后降量的原则进行。
13.反应器大盖发生泄露着火
1987年9月9日,四套加氢精制开工期间,反应器大盖发生泄露着火,使反应器顶部框架钢梁烧毁,装置紧急停工。
分析:
泄露系检修时反应器大盖卡扎里密封半丝装反,致使筒体及半丝螺纹未紧到位。
经验教训:
检修拆装设备要认真严谨,否则可能引发重大事故。
14.催化剂床层发生严重飞温
1993年7月,二套加氢裂化开工期间,使用RT-1新催化剂,进油时催化剂床层发生严重飞温,床层最高温度达820℃,装置紧急停工。
分析:
进油温度为240℃,略高,后调整为200℃,开工正常。
经验教训:
新鲜催化剂初进油时,温度不能太高,否则极易发生超温事故。
15.废热炉入口负压超高
1986年9月2日,反应炉F101和F102正在升温,废热锅炉开C104(烟道气引风机)引烟气煮炉。
操作人员在进行烟气切换时,烟道旁路挡板DA-6关得太快,废热锅炉入口负压过高,将F101和F102两炉火抽熄。
分析:
废热锅炉入口负压控制着五台工艺炉负压,它的激烈波动将造成五台工艺炉负压波动,严重时会产生熄火,炉膛爆炸等恶性事故。
锅炉操作人员调整负压时,应与反应和分馏岗位联系,三方人员到现场严密监视各炉负压变化情况,必须缓慢调节。
16.F102(循环氢加热炉)干烧
1986所9月15日15:
15时,反应系统正处于开工高压气密阶段,由于高分液位D102超高报警跳闸联锁表LS/LAILH-01因表件松动造成误动作,C101(循环氢压缩机)紧急停车7巴/分自动放空,F102自动熄火。
当班人员在没有将主火嘴手阀关闭情况下将XCV-104A联锁控制阀复位,有四个火嘴又自动点燃。
车间干部从中控室CRT显示发现F102管壁温度最高点已升到512℃,责成岗位人员立即检查才发现此问题,立即将火嘴熄火。
分析:
不管加热炉出现什么原因造成熄火,操作人员应首先关闭火嘴阀门,否则可能造成干烧、爆炸等事故。
我厂曾经因为类似情况火嘴复燃,之后又不检查造成炉管烧坏,甚至整台加热炉报废的重大事故,此事反映了操作人员对事故的处理过程不熟悉。
需要进一步加强训练,提高技术素质。
17.分馏炉回火爆燃
1986年10月4日9:
40时,突然F104(产品分馏塔底重沸炉)发生回火爆燃,接着F103(脱丁烷塔重沸炉)也回火,F104又发生第二次回火。
由于不明回火原因,当班人员立即在中控室紧急停炉,反应降温降量,对操作产生很大波动。
分析:
这是一起严重的回火爆炸事故,由于初次开工现场比较乱,其原因当时也没能调查清楚,经分析和以下原因有关:
(1)、燃料油压力控制过高。
装置内总线在1.0MPa,比正常高出0.2MPa。
(2)、雾化蒸汽压力没有投自动,各炉没按规定将蒸汽与燃料油差压控制在0.15MPa,F104差压仅有0.07MPa。
原因可能是蒸汽压力波动,燃料油雾化不良,部分火咀熄火。
司炉员发现之后将烟道挡板开大,大量空气进人炉膛后产生爆燃。
要强调的是,加热炉蒸汽压控必须投入自控,否则蒸汽压力波动十分容易产生熄火、爆炸等事故。
18.F103(脱丁烷塔重沸炉)熄火造成馏分波动
1987年9月8日准备开液力透平,仪表检查LIC-103控