漏斗注塑模具设计Word文档格式.docx
《漏斗注塑模具设计Word文档格式.docx》由会员分享,可在线阅读,更多相关《漏斗注塑模具设计Word文档格式.docx(17页珍藏版)》请在冰豆网上搜索。
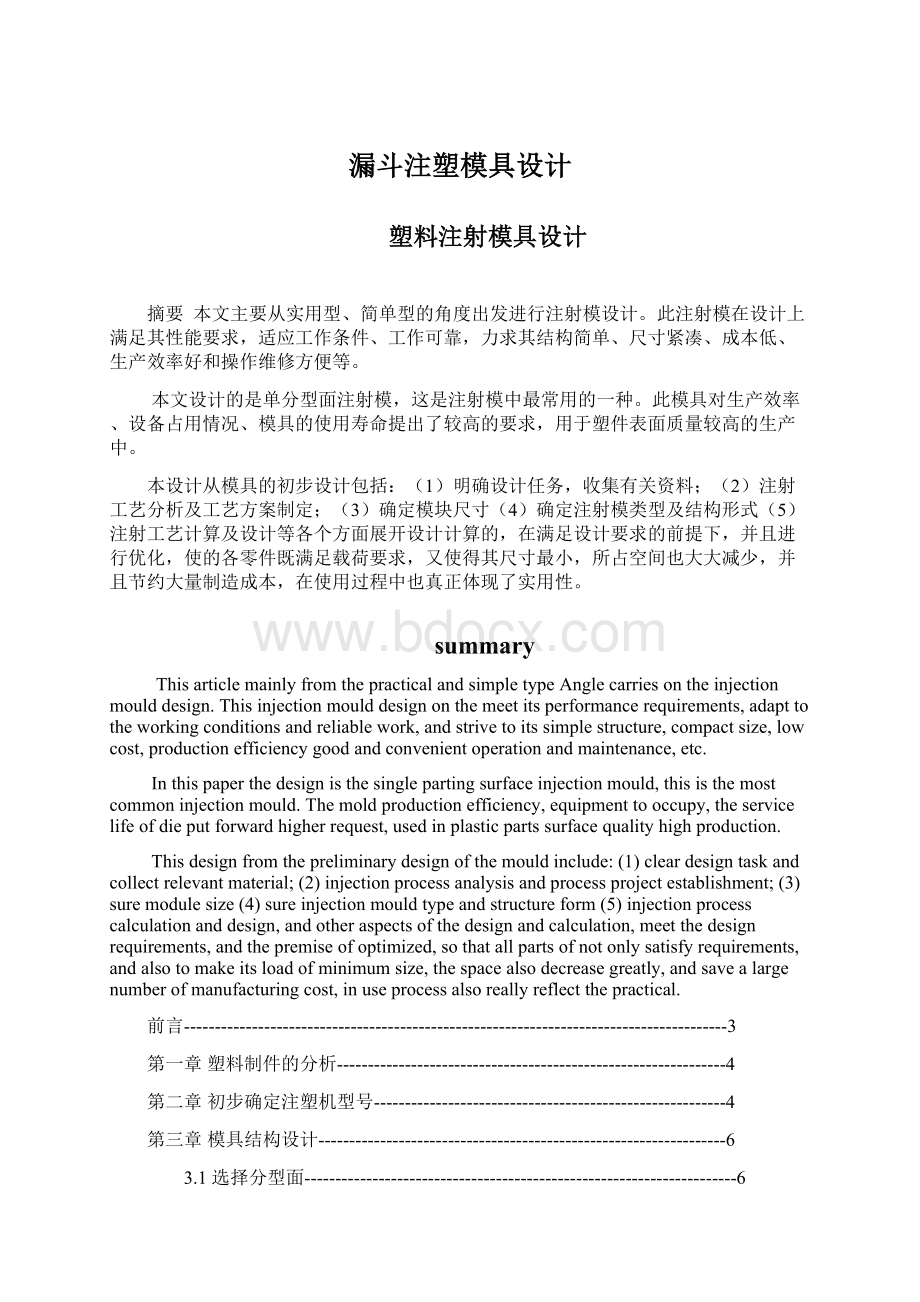
4.2型腔侧壁厚度和底板厚度计算---------------------------------------------20
4.3注射机与模具有关参数及尺寸的校核------------------------------------22
第五章绘制模具总装图--------------------------------------------------------------24
结论---------------------------------------------------------------------------------------24
致谢辞---------------------------------------------------------------------------------25
参考文献---------------------------------------------------------------------------------25
前言
国民经济的高速发展对模具工业提出了愈来愈高的要求,促使模具技术迅速发展,作为生产各种工业产品和民用产品的重要工艺装备,模具已发展成为一门产业。
20世纪80年代以来,中国模具工业的发展十分迅速。
近20年来,产值以每年15%左右的速度增长。
2010年我国模具工业消费额约11120亿人民币。
在模具工业的总产值约占50%,塑料模具约占33%,压铸模具约占6%,其它各类模具约占11%。
目前,从事模具技术研究的机构和院校已达3000余家。
华中科技大学模具技术国家重点实验室、上海交通大学模具CAD国家工程研究中心等,在模具CAD/CAE/CAM技术、精冲模CAD软件、模具的电加工和数控加工技术、快速成行和快速制模技术、新型模具材料等方面都取得了显著的进步和多项的成果。
中国模具发展前景将十分广阔。
模具行业的发展趋势:
(1)模具市场全球化,模具生产周期进一步缩短;
(2)模具CAD/CAM向集成化、智能化和网络化发展。
本书的主要内容为塑料注射模设计。
对于塑件变形的基本概念、注射机设备、注射常用的材料以及其它注射工艺及其模具也作了概要的介绍。
图—1
第一章塑料制件的工艺性分析
图—1塑料制件图
1)制件质量为18.35g,材料为PE,收缩率为1.5%~5.0%,平均收缩率为3.25%,体积20cm3,密度为0.910~0.925g/cm3,平均密度为0.9175g/cm3。
2)该塑件尺寸较小,未注精度等级,为降低成本推荐一模多腔,并对制件进行后加工。
3)为满足制品的要求和提高成型效率采用轮辐式浇口。
4)为了方便加工、热处理和降低制造成本,型腔与型芯部分采用拼镶结构。
第二章初步确定注射机型号
根据制品的生产批量及尺寸精度的要求,采用单型腔模,即一模一腔。
模具设计时,必须使制品所需注射的塑料容积或质量在注射机额定注射量的85%以内。
在一个注射成型周期内,需注射入模具内的塑料溶体的容量或质量,应为制品和浇注系统两部分容量或质量之和,即
W=nWz+Wj≤Wg
式中:
W—一个成型周期内所需注射的塑料质量(g);
Wz—单个制品的质量(g);
Wj—浇注系统冷凝料和飞边所需的塑料质量(g);
为制品质量的10%;
Wg—注射机额定注射量;
W=1x18.35+18.35x10%=20.185g;
根据计算结果,并查阅塑料注塑机技术规格表和PE材料注射成型的工艺参数,初步确定选用SZA-YY60型注射机。
PE注射成型的工艺参数
注射机类型:
螺杆式
螺杆转数:
30~60r/min
喷嘴形式:
关式
喷嘴温度:
170~180°
C
料筒温度:
均化端:
170~210°
C 压缩段:
160~170°
C 加料端:
130~140°
模具温度:
40~70°
注射压力:
40~80MPa
预塑背压:
0.1~2.0MPa
保压压力:
50~70MPa
注射时间:
3~5s
保压时间:
20~30s
冷却时间:
成型周期:
50~70s
SZA-YY60注射机的主要技术参数
一次注射量:
62cm3
螺杆直径:
Ф35mm
138.5MPa
注射方式:
锁模力:
440kN
最大注射面积:
160cm2
最大开(合)模行程:
mm
模具最大厚度:
250mm
模具最小厚度:
150mm
拉杆空间:
330x300
定位圈尺寸:
Ф100mm
推出形式:
中心推出
第三章模具结构设计
3.1选择分型面
分型的位置直接影响模具使用、制造及塑件质量。
根据分型面的选择原则:
1)分型面应选择在塑件外形轮廓最大处2)分型面的选择应有利于塑件的留模方式,便于塑件顺利脱膜3)保证塑件的精度要求4)满足塑件外观的要求5)便于模具的制造6)减小成型面积7)增强排气效果。
制件留在动模上,分型面选择如下图所示。
图—2分型面选择
3.2确定型腔的布局
本塑件在注射时采用一模一腔的模具结构。
因为是回转体零件,所以型腔置于模具中心位置上。
另外塑件为空心管状形式,故采用轮辐式浇口形式。
其浇口的典型尺寸为:
深h=0.5~1.5mm,宽b=1.6~6.4mm,长L=1~2mm。
如下图所示。
图—3轮辐式浇口
3.3浇注系统设计
3.3.1、主流道设计
在卧式或立式注射机使用的模具中,主流道一般垂直于模具分型面。
其设计要点如下:
1)为了便于拉出流道中的冷凝料,通常将主流道设计成圆锥形,锥角α为2°
~6°
,内壁粗糙值Ra为0.08μm。
2)圆锥孔小头直径D为4~8mm,但必须比注射喷嘴d大0.5~1mm。
3)主流道的长度由定模板的厚度来确定,一般不大于60mm。
根据XS-ZY-125型注塑机喷嘴的有关尺寸
喷嘴前端孔径:
d0=Ф4mm
喷嘴前端球面半径:
R0=12mm
根据模具主流道与喷嘴的关系:
R=R0+(1~2)mm
D=d0+(0.5~1)mm
取主流道的球面半径:
R=13mm
取主流道的小端直径:
d=Ф4.5mm
图—4主流道衬套
3.3.2、分流道设计
1)分流道的形状
分流道连接主流道和浇口,其主要作用是在压力损失最小的条件下,将来自主流道的熔料以较快的速度送至浇口进行充模。
同时,在保证充满型腔的条件下。
要求分流道容积要小,以减少回收的冷凝料。
所以分流道截面要大小适宜。
分流道截面形状可以是圆形、半圆形、矩形、梯形和U形等。
根据塑件的实际情况,这里选用半圆形为分流道截面。
图—5分流道截面形状
2)分流道的尺寸
分流道尺寸根据塑料品种、塑件的大小及流道长度确定。
对于重量在200g以下、壁厚在3mm以下的塑件可用下面的经验公式计算分流道的直径。
D=0.2654M1/2L1/4
D—分流道的直径(mm);
M—塑件的质量(g);
L—分流道的长度(mm)。
D=0.2654×
16.391/2×
61/4=1.6mm
根据经验值,分流道直径取3mm
3.3.3、冷料井和拉料杆设计
注射机喷嘴前端要和温度较低的模具接触,所以喷嘴前端部位的熔融料温度也较低,在注射模具时应防止这部分材料(冷料)进入型腔,否则将影响塑件质量。
为此,在主流道的末端开设冷料井,使这部分冷料停留在此处。
当分流道较长时,料流的前端又会产生新的冷料,最好在分流道的末端也开设冷料井。
冷料井内的冷凝料和整个浇注系统的冷凝料是连成一体的,利用冷凝井的冷凝料脱出整个浇注系统的形式有拉料杆脱料式和推板脱料式两种类型。
根据制件的成型要求、脱膜要求和浇口布置形式,本制件采用拉料杆脱料式。
图—6冷料井与拉料杆形式
3.4、脱膜机构设计
3.4.1、推出机构设计
制品成型后,由于其体积的收缩,对型芯产生包紧力,制品要从型芯中脱出,就必须克服因包紧力而产生的摩擦阻力。
对于不带同孔的壳体类制品,脱膜时还要克服大气压力。
所以为了克服塑件因冷却收缩产生的包紧力,方便脱膜,塑件内外表面在脱膜方向应设计一定的脱膜斜度。
塑件上脱膜斜度的大小与塑件的性质、收缩率、摩擦系数、塑件壁厚及几何形状有关。
查表得脱膜斜度为型腔35′~1°
30′型芯30′~40′。
(1)推件力的计算
推件力 F=AxP
A—塑件包络型芯的面积(mm2);
p—塑件对型芯单位面积上的包紧力,p取0.8×
107~1.2×
107MPa;
a—脱膜斜度;
q—大气压力0.09MPa;
μ—塑件对钢的摩擦系数,μ约为0.1~0.3;
A1—制件垂直于脱膜方向的投影面积(mm2)。
A≈1658.76+188.49≈1846.49mm2
Ft=1846.49×
1.2×
107(0.3cos40′-sin40′)/106+0.09×
1649.34=6355N=6.3kN
(2)确定顶出方式及顶杆位置
推出方式选用推杆推出,推杆设计时应注意以下事项:
1)推杆直径不宜过细,以防顶出时受力弯曲。
2)在成型孔旁边设置推杆孔时,两孔壁不能靠的很近,否则成型压力将使孔壁变形。
3)推杆应尽量设置在塑件脱膜阻力大的部位。
如果各处阻力相同时,推杆应均匀对称设置,使塑件在脱膜时受力均匀。
4)推杆在塑件上留下的痕迹,应尽量不影响塑件的外观。
所以应尽可能地设置在制件的非主要表面,而且推杆端面应和型腔在同一表面,或比型腔的平面高0.1mm,但不可低于型腔表面,否则塑件平面上有凸出点,可能会影响使用。
根据上述条件及本模具的实际情况,推杆数量选用4根。
如图7所示。
推杆与动模板推杆孔的配合一般为H8/f7,配合长度约为推杆直径的1.5~2倍。
推杆与推杆固定板径向应留有0.5mm的间隙。
图—7顶出方式及顶杆位置
(3)推出直径的确定
根据压杆稳定公式,可得推杆直径的公式:
d—推杆的最小直径(mm);
k—安全系数,一般为1.5;
L—推杆的长度(mm);
n—推杆的数目;
F—脱膜力(N);
E—钢材的弹性模量。
推杆的直径:
==3.73mm
推杆直径确定后,还应进行强度校核,其公式为
—推杆所受的应力(MPa);
—推杆材料的许用应力(MPa)。
强度校核:
根据上述条件,推杆直径选用4mm。
3.4.2、导向机构设计
根据塑件特点和实际成型要求,选用导柱导向机构。
(1)导柱的结构及要求
图—8导柱结构
对导柱的要求:
1)长度导柱的有效长度一般应高出凸模端面6~8mm,以保证凸模进入凹模之前导柱先进入导向孔以避免凸凹模碰撞而损坏模具。
2)配合导柱和模板固定孔之间的配合为H7/k6,导柱和导向孔之间的配合为H7/f7。
(2)导向孔的结构及对导套的要求
图—9导套结构
对导套的要求:
1)配合直导套和模板固定孔之间的配合为H7/n6。
3.5、冷却系统设计
因制件外形较平直,故直接打冷却水孔冷却。
由于制品平均厚度为3mm,制件尺寸又较小,确定管道直径Ф8mm。
由于冷却水道的位置、结构形式、孔径、表面状态、水的流速、模具材料等很多因素都会影响模具的热量向冷却水传递,精确计算比较困难。
实际生产中,通常都是根据模具的结构确定冷却水路,通过调节水温、水速来满足要求。
冷却系统的设计原则:
1)冷却水孔数量多、孔径尽量大。
2)冷却水孔至型腔表面距离相等。
为使塑件均匀冷却,当塑件的壁厚均匀时,冷却水孔与型腔表面的距离最好相等,分布尽量与型腔轮廓相吻合。
当壁厚不均匀时,壁厚处应加强冷却。
冷却水孔至型腔表面的距离应适应,一般可为12~15mm,过大则影响冷却效果,过小会导致型腔表面温差增大。
冷却水孔间距离不宜太大或太小,一般在(1.7~3)d之间。
3)浇口处加强冷却。
当塑料溶体刚充满型腔时,浇口附件温度最高,离浇口越远处,温度越低,为保证冷却均匀,对浇口处应加强冷却。
4)降低进出口水的温差。
为使整个塑件冷却均匀一致,提高塑件质量,当型腔各处温度要求均匀时,则必须尽量降低冷却水进出口的温差,一般情况下冷却水进出口的温差应在5°
C以下,精密塑件应控制在2°
C左右。
一般可通过并联水道或改变水孔的排列方式来降低进出口水的温差。
5)冷却水孔避开熔接缝。
冷却水孔不宜设在靠近熔接缝处,以免影响熔接牢固。
6)便于加工处理。
冷却水通道要易于加工,便于清理,水孔直径不宜过小,一般可为8~12mm。
7)密封可靠。
当冷却水道设在模具零件的结合面上或穿过模具零件的结合面时,应密封可靠,不能在结合面上产生泄漏现象。
另外进出口处、堵头处也应有很好的密封。
冷却水路布置如下图所示。
图—10冷却水道布置
3.6、排气系统设计
3.6.1、排气方式
由于制件的顶出杆较多,再利用分型面间隙进行排气即可。
3.6.2、排气槽设计要点
排气槽位置和大小的确定主要依靠经验。
1)排气槽一般设在分型面上凹模一侧,以便模具制造与清理。
2)排气槽应设在料流末端。
3)排气槽出口方向不应朝向操作人员,并最好呈曲线状,以防注塑时熔料或高温气体喷出烫伤工人。
4)排气槽尺寸一般为宽1.5~6mm,深0.02~0.05mm,以塑料不从排气槽溢出为宜,即应小于塑料的溢料间隙。
3.7、成型零件结构设计
本塑件成型件结构相对简单,需大型芯两个,压入固定板固定。
3.7.1、凹模的结构设计
凹模是成型塑件外表面的部件,按其结构形式可分为整体式、整体组合式和组合式三类。
这里根据塑件本身的结构特点,选用组合式凹模。
图—11组合式凹模
组合式凹模的设计要求:
1)便于加工、装配和维修。
尽量把复杂的内形加工变为外形加工,配合面配合长度不宜过长,易损件应单独成块,便于更换。
2)保证组合结构的强度、刚度,避免出现薄壁和锐角。
3)尽量防止产生横向飞边。
4)尽量避免在塑件上留下镶嵌缝痕迹,影响塑件外观。
5)各组件之间定位可靠、固定牢固。
3.7.2、型芯的结构设计
据型芯是成型塑件内表面的部件,按其结构形式同样可以分为整体式、整体组合式和组合式三类。
这里根塑件的结构特点,选用整体组合式。
图—12组合式型芯
3.8、确定标准模架型号与规格
根据以上分析,计算并考虑型腔的尺寸,可以初步确定标准模架的结构和规格。
查设计手册选用标准模架为A2-100160-41-Z2(GB/T12556.1-1990),其参数如下:
定模板厚度A=40mm
动模板厚度B=12.5mm
垫块厚度C=40mm
定模固定板厚度=16mm
动模固定板厚度=16mm
支承板厚度=20mm
推杆固定板=10mm
推板=12.5mm
模具厚度=52+A+B+C=144.5mm。
3.9、模具材料的选用
3.9.1、塑料模具钢材的性能要求
1)加工性能良好,热处理变形小2)抛光性良好3)耐磨性良好4)芯部强度高5)耐蚀性良好6)有一定的热硬度。
3.9.2、塑料模钢材的选用
根据制件的大小、材料、产量等因素进行选择。
成型零件:
CrWMn;
定模座板、动模座板、垫板、推杆固定板、推板:
20~55钢,锻造、压延或拉拔,淬火回火或正火,硬度HB123~235。
定模板、动模板、支承板:
50、55、42CrMo、T8,正火、退火或淬火回火,硬度HB183~235。
其它标准件根据国标选用
3.10、绘制模具的结构草图(见附图)
第四章、模具的设计计算
4.1、成型零件工作尺寸计算
所谓工作尺寸是指成型零件上直接用以成型塑件部分的尺寸,主要有型腔和型芯的径向尺寸(包括矩形或异形型芯的长和宽),型腔和型芯的深度尺寸,中心距尺寸等。
任何塑料制品都有一定的尺寸要求,在使用或安装中有配合要求的塑料制品,其尺寸精度常要求较高。
在设计模具时,必须根据制品的尺寸和精度要求来确定相应的成型零件的尺寸和精度等级。
影响塑料制品精度的因素较为复杂,主要有以下几方面:
首先与成型零件制造公差有关,显然成型零件的精度愈低,生产的制品尺寸或形状精度也愈低。
其次是设计模具时,估计的塑料收缩率与实际收缩率的差异和生产制品时收缩率的波动值,成型收缩率包括设计选取的计算收缩率与实际收缩率的差异,以及生产制件时由于工艺条件波动,材料批号发生变化而造成制件收缩值的波动,前者造成塑料制品的系统误差,后者造成偶然误差,收缩率波动值δs随制件尺寸增大而成正比的增加。
制造误差δz随制件尺寸成立方根关系增大,型腔使用过程中的总磨损量δc随制件尺寸增大而增加的速度也比较缓慢。
生产大尺寸塑料制件时因收缩率波动对制件公差影响较大,若单靠提高模具制造精度来提高塑件精度是很困难的和不经济的,而应着重稳定工艺条件