T型接头双激光束同步焊接热源模型修改后Word文件下载.docx
《T型接头双激光束同步焊接热源模型修改后Word文件下载.docx》由会员分享,可在线阅读,更多相关《T型接头双激光束同步焊接热源模型修改后Word文件下载.docx(10页珍藏版)》请在冰豆网上搜索。
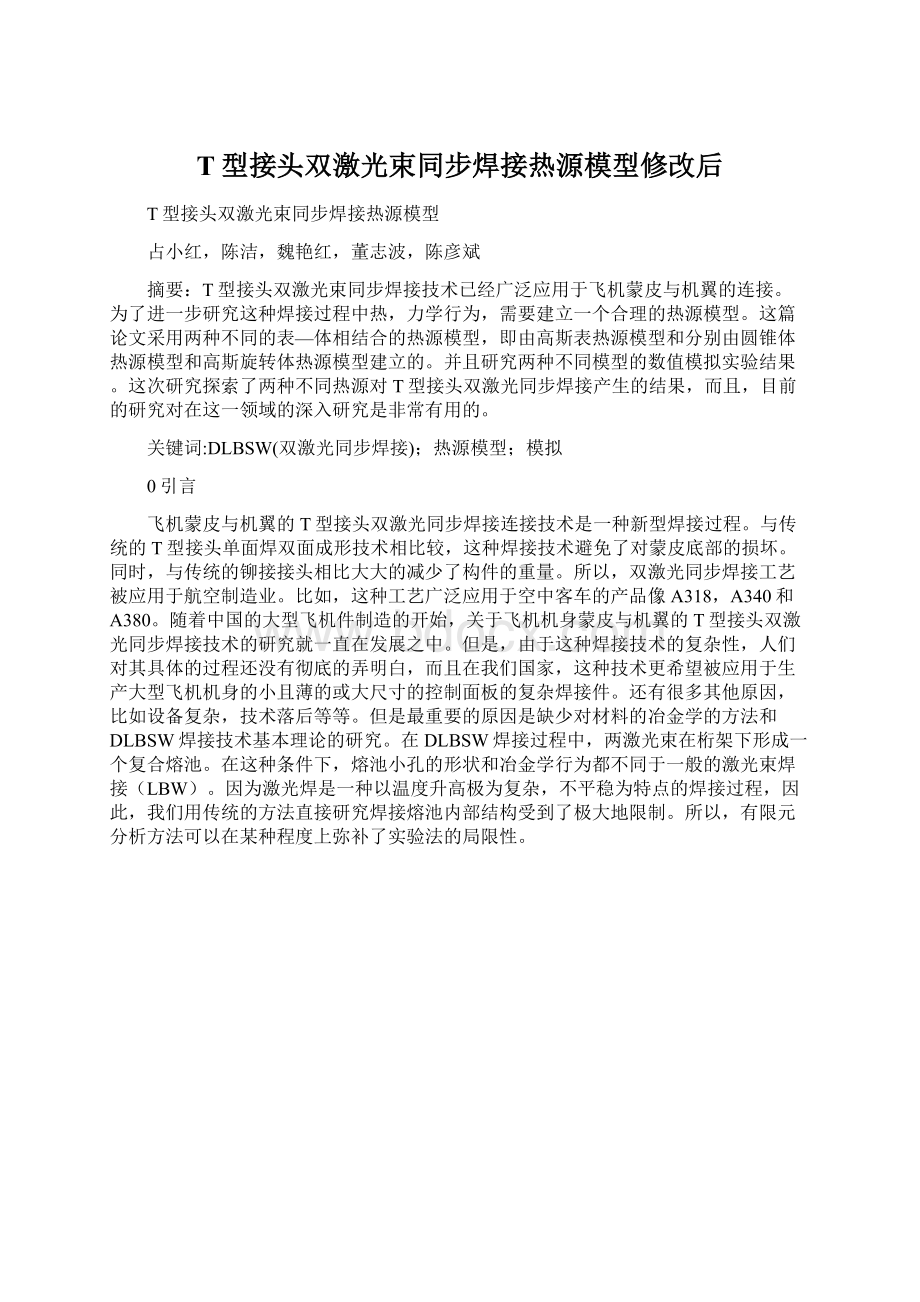
同时,与传统的铆接接头相比大大的减少了构件的重量。
所以,双激光同步焊接工艺被应用于航空制造业。
比如,这种工艺广泛应用于空中客车的产品像A318,A340和A380。
随着中国的大型飞机件制造的开始,关于飞机机身蒙皮与机翼的T型接头双激光同步焊接技术的研究就一直在发展之中。
但是,由于这种焊接技术的复杂性,人们对其具体的过程还没有彻底的弄明白,而且在我们国家,这种技术更希望被应用于生产大型飞机机身的小且薄的或大尺寸的控制面板的复杂焊接件。
还有很多其他原因,比如设备复杂,技术落后等等。
但是最重要的原因是缺少对材料的冶金学的方法和DLBSW焊接技术基本理论的研究。
在DLBSW焊接过程中,两激光束在桁架下形成一个复合熔池。
在这种条件下,熔池小孔的形状和冶金学行为都不同于一般的激光束焊接(LBW)。
因为激光焊是一种以温度升高极为复杂,不平稳为特点的焊接过程,因此,我们用传统的方法直接研究焊接熔池内部结构受到了极大地限制。
所以,有限元分析方法可以在某种程度上弥补了实验法的局限性。
图1三板连接过程的比较
从1973年Swift-Hook和Gic开始研究激光焊温度场到现在,激光焊温度场数值模拟已经有了三十多年的研究了。
许多国外的和国内的学者已经发表了大量的关于深熔透激光焊接数值模拟的学术论文。
本文是从先前的聚焦中心孔和热源模型发展为基于高斯热源分布模型的激光焊温度场数值计算的研究,然后发展为激光深熔焊热流场模拟和形变预测的研究。
近年来,激光焊研究变得越来越深刻,越来越有经验。
在国内,吴川松,徐久华,杜汉斌,吴肃,熊建刚,王宏,陈彦斌,陈曦等人已经对激光深熔焊中心孔和熔池形成动态过程有了研究,并在这一领域取得了一些成就。
但是,到目前为止还没有关于T型接头双激光同步焊接热源模型的研究报告。
为了让T型接头双激光同步焊接有限元分析技术得到应用,应当首先建立T型接头双激光同步焊接热源模型。
这篇论文将论述面—体联合热源模型的发展和研究模拟的结果。
1.模型原理
1.1热源模型
建立热源模型是焊接过程数值模拟中最基本,最重要的一步。
有许多计算机焊接热源模型,主要包括:
罗森塔尔分析模型,高斯热源分布模型,半球分布热源模型,椭球体热源分布模型,双椭球形热源模型等等。
在处理热源模型的方法中,分析法是简单、清晰的一种。
但是,分析法由于需要太多的假设说明,在精确度和有效性方面尤其具有局限性。
数值处理方法采用材料的非线性特征,还可更进一步改善高温区模拟的精确度。
对不同的材料,不同的焊接方法,所有的模型都可以应用,如:
高斯分布的面热源模型,还有球形,椭球形,双椭球形分布的体热源模型。
通过实验的结果反复的修正热源模型参数,使模型更合理,更精确,可用于和有助于深入的更进一步的模拟研究。
圆柱形热源模型,高斯旋转曲面和圆锥体分布热源模型大多应用于激光深熔焊接。
同时,一个面热源模型加上一个体热源模型可以模拟等离子效应和熔池表面状况。
根据不同热源应用范围的综合分析,本文集中研究两种面—体联合热源模型,即:
“高斯面热源与高斯旋转体热源联合的热源模型”和“高斯面热源与锥体热源联合的热源模型”。
当考虑到双激光同步焊接时,就需要两种联合的热源模型。
图2高斯面热源结构
高斯模型的连续热流密度可定义为:
(1)
q(r)是半径r处的面连续热流密度,qmax是热源中心连续热流密度的最大值,热量集中系数c是由焊接方法确定的一个定值。
实际上,锥形体热源模型是由一系列深熔焊高斯面热源模型叠加而成。
热流密度分布区域横截面积的直径随板厚的增加直线减小。
二者的关系可以表示为:
(2)
q(r,z)是半径为r,深度为z处的热流密度,h是热源的有效深度,r是距热源中心的距离,z是研究位置的深度。
高斯旋转体热源沿z方向上的每一个横截面都是圆,且其上的热流密度服从高斯分布。
高斯旋转体热源可以表示为:
(3)
H是热源高度,P是热源功率效率,R0是热源空隙半径。
图3高斯旋转体热源模型
DLBSW焊接过程中,热源协调系统与FEM模型协调系统之间应该有一个补偿角,因为激光束入射角不是很规律。
所以,热源系统的协调或是当地系统的协调的转变必须要有有效的热源路径。
1.2有限元模型
图4是单机翼T型接头几何模型。
用预处理软件或是附加在主处理软件的预处理包可以创建有限元几何模型。
一般的,网格划分的越好,精确度越高,同时计算时间就越长,计算成本就会增加。
相反地,精确度将会下降而且花费时间少。
均匀一致的网格是不适用的,因为焊接过程中的热效应在不同的位置有不同的特点。
也就是说,密集的网格用于焊缝和热影响区,而远离焊缝的区域采用稀疏的网格。
在这篇论文中,不均匀的过度的网格用于T型接头双激光同步焊接有限元模型的建立,其中填充焊丝的部分用起始元件模型。
T型接头网状模型如图5所示:
图4单机翼T型接头几何模型图5T型焊接结构过渡阶段的网格
具有六面体的元件类型应用于网状几何模型。
离中心线不到2mm的区域网格是完整的,而远离焊缝区域的网格是粗糙的。
在以上两种区域之间的区域网格是渐变式的类型。
整个网格是由32300个单元和40704个节点组成。
两个节点之间的空间的大小限制为0.2mm,同时离焊缝3mm处时这个尺寸会改变。
1.3初始条件和边界条件
蒙皮和机翼所用材料分别为6156和6056铝合金。
热传导和热输入都应考虑到边界条件。
由于实际焊接过程的复杂性,所以应当考虑到一些简单的条件。
论文中熔化和模拟过程基于以下假设条件:
(1)工件初始温度为室温(20℃);
(2)忽略焊接熔池中化学反应的影响;
(3)将热传导扩大为熔池内部的热对流;
(4)假设材料均匀各项同性;
(5)忽略填充材料和木材的差异;
(6)考虑潜热的影响是采用相同的比热容量。
2.温度场模拟
根据模型的建立,DLBSW焊接过程中的温度场分布就可以进行模拟了。
而且还可以对不同热源模型的影响进行分析。
图4(a)和图4(b)显示了分别由“高斯面分布与高斯旋转体分布”的联合热源模型和“高斯面分布与锥形体分布”联合热源模型的模拟。
图6说明了联合热源可以应用于获得温度分布合理模拟结果。
这两种不同模型的模拟结果说明了激光束不能穿透金属表面,这对飞机机身的制造是非常有用的,因为飞机外表面的完整性和连续性是非常重要的。
焊接熔池模拟结果显示:
在激光深熔焊接时,熔池在宽度和深度方向的尺寸都比较大。
3.分析和讨论
为了分析不同热源模型热循环曲线的不同,在OH和MN上选择了一系列的样点,如图7所示。
收集三点每一时间段的温度值来生成对温度场可进行量的分析的热循环曲线。
根据模拟结果,OH和MN线上如图7所示的点处的热循环曲线如图8—11所示。
每条热循环曲线表示随着时间的增加每个确定点处温度的变化趋势。
在横向方向上,即垂直于焊接方向,每一点的最高温度随着点距焊缝中心线的距离的增加而降低,如图10和11所示。
很明显的可以看出,当热源靠近时,温度迅速上升为2000℃,而当热源离开时,温度迅速降低。
而且温度降低的趋势比温度上升的趋势要缓和。
当温度降到大约450℃时温度下降的更加缓慢。
同时当温度降至450℃以下时,热循环曲线非常相似。
用高斯体热源模型计算的温度最大值比用圆锥体热源模型计算的稍大一些。
在图9和图11中,极高点的温度不到2000℃但比铝合金的熔点温度高得多。
用不同热源模型计算所得的热循环曲线的不同不仅明显的表现在高温区域。
也就是说,温度场内的位置影响也会造成热源的不同。
模拟结果显示:
距离焊缝中心较远的温度场取决于实际焊接中的焊接参数,而对不同的热流分布模型不敏感。
4.总结
飞机机身的双激光同步焊接技术是一种新型焊接工艺,目前缺少在量上的研究。
这篇研究报告对“高斯面热源+高斯旋转体热源”和“高斯面热源+圆锥体热源”这两种面—体联合热源模型进行了初步的调查研究。
研究报告显示:
激光深熔焊熔池温度场可以用联合热源模型进行模拟。
在相同条件下,用高斯旋转热源模型模拟的极高点的温度值是比较高的。
参考文献:
[1]Swift-Hook.Penetrationweldingwithlaser[J].WeldingJournal,1973,52(11):
492-498
[2]J.G.Andrews,D.R.Atthey.Hydrodynamiclimittopenetrationofamaterialbyahighpowerbeam.J.Phys.D:
Appl.Phys.,1976,9(12):
2181~2194
[3]JohnGoldak.Anewfinitemodelforweldingheatsource[J].MetallurgualTransactiongs,1984,15B
(2):
299~305.
[4]DowdenJandDavisMandKapadiaP,SomeAspectoftheFluidDynamicsoflaserwelding,journalofFluidMechanics,1983,126:
123~146
[5]J.Mazumder,P.S.Mohanty,T.P.Duffy.Challengesinmodelingandmonitoringiflaserweldingprocess.In:
Processingofthe6thInt.Symp.ofJWS.Nagoya,Japan.1996.167~172
[6]WSudnik,DRadajandWErofeev,Computerizedsimulationoflaserbeamwelding,anintroductorysurvey,ComputerTechnologyInWelding9-12,June1996,LanakenBelgium
[7]Wei,Shian,etal.ThreedimensionalanalyticaltemperaturefieldanditsapplicationtosolidificationcharacteristicinhighofLow-power-density-beamwelding.HeatMassTransfer,1997,40(10):
2283-2292
[8]N.Postacioglu,P.Kapadia,J.Dowden.Distortiongeneratedbyamovingweldpoolofellipticalcrosssectionintheweldingofthinmetalsheets.J.Phys.D:
Appl.Phys.,2000,33(14):
1739~1746
[9]N.Postacioglu,P.Kapadia,J.Dowden.Thermalstressgeneratedbyamovingellipticalweldpoolintheweldingofthinmetalsheets,J.Phys.D:
Appl.Phys.,1997,30(16):
2304~2312
[10]Tsirkas,S.A.,Papanikos,P.,Kermanidis,Th.Numericalsimulationofthelaserweldingprocessinbutt-jointspecimens.J.Mater.Proc.Technol,2003,134,59–69.
[11]Darcourt,C.,Roelandt,J.-M.,Rachik,M.,Deloison,D.,Journet,B.Thermomechanicalanalysisappliedtothelaserbeamweldingsimulationofaeronauticalstructures.J.Phys.IV,2004,120,785–792.
[12]Josserand,E.,Jullien,J.F.,Nelias,D.,Deloison,D.Numericalsimulationofwelding-induceddistortionstakingintoaccountindustrialclampingconditions.Math.Modell.WeldPhenom,2007,8,1105–1124.
[13]ChuansongWu.NumericalAnalysisofWeldingHeatTransferProcess.HarbinInstituteofTechnologyPress.Harbin,1990.
[14]JiuhuaXu,YumeiLuo,JingzhouZhang.NumericalStudyforHeatTransferinHighPowerDensityKeyholeWeldingProcess.ChineseJournalOfLasers,2000,27
(2):
174-176.
[15]HanbinDu,LunjiHu,DongchuanWang.Simulationofthetemperaturefieldandflowfieldinfullpenetrationlaserwelding.TransactionsoftheChinaWeldingInstitution,2005,26(12):
65-68.
[16]SuWu,HaiyanZhao,YuWang.Anewheatsourcemodelinnumericalsimulationofhighenergybeamwelding[J].TransactionsofTheChinaWeldingInstitution,2004,25
(1):
91-94.
[17]JiangangXiong.StudyonMathematicalmodelofkeyholeandmoltenpoolgeometryindeeppenetrationlaserweldingandoptimizationofANNparameters.Wuhan:
HuazhongUniversityofScience&
TechnologyLibrary,2001.
[18]HongWang,YaowuShi,ShuiliShi.ModelingoftheKeyholeFormationunderHighIntensityLaserPower[J].ChineseJournalofLasers,2007,34(4):
4-5.
[19]YanbinChen.AdvancedLaserWeldingTechnology.SciencePress.2005,1,Ⅰ.
[20]XiChen,XiaohuYe.ANumericalSimulationStudyofLaserFull-PenetrationWelding.AppliedLaser,2002,Vol.22
(2):
185-187.