冲压模课程设计Word文档格式.docx
《冲压模课程设计Word文档格式.docx》由会员分享,可在线阅读,更多相关《冲压模课程设计Word文档格式.docx(17页珍藏版)》请在冰豆网上搜索。
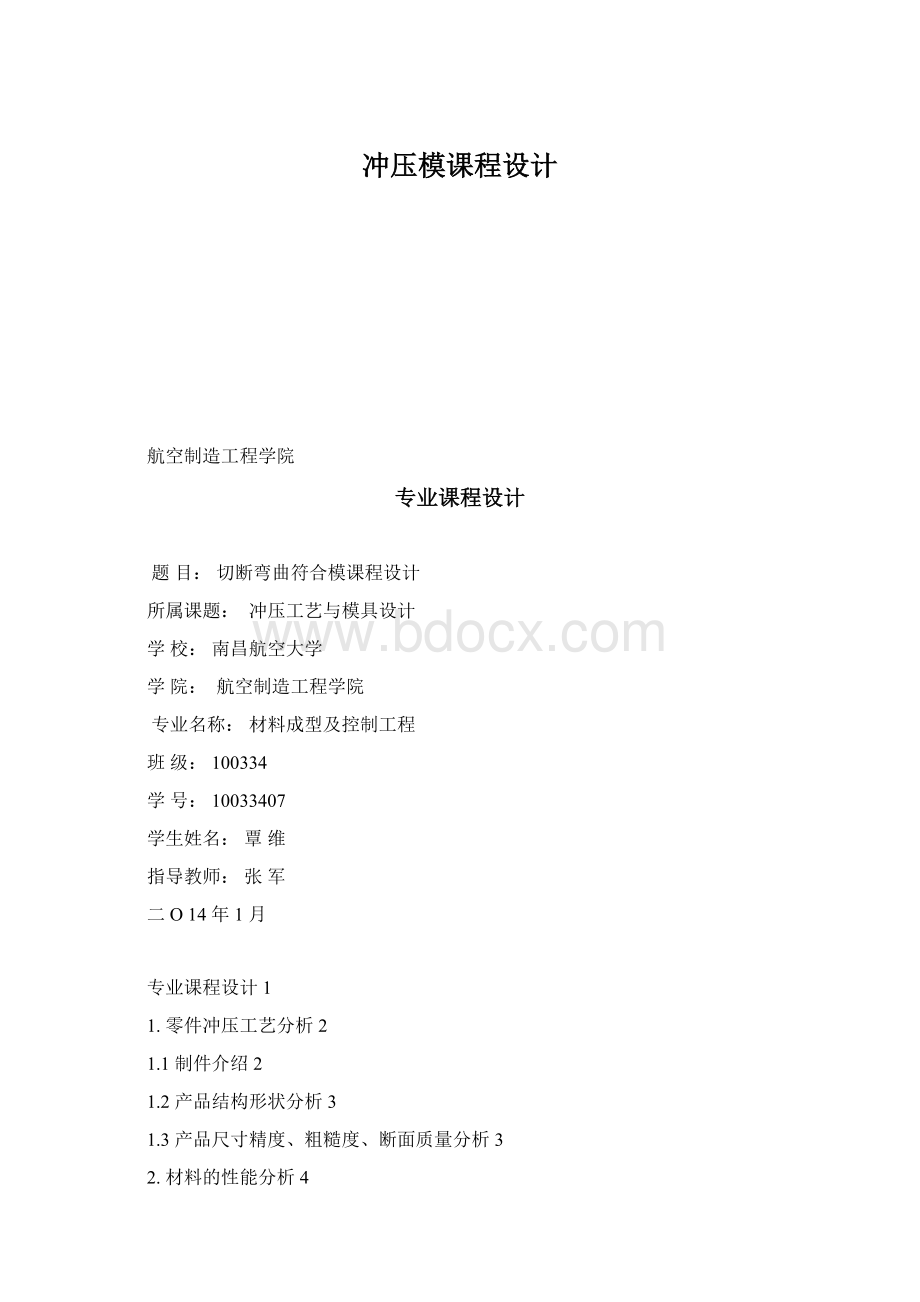
4.2模具结构的选择5
5.主要工艺计算5
5.1零件毛坯尺寸计算5
5.2排样6
5.3剪切力和弯曲力的计算6
5.4剪切凸模和凹模间隙的计算7
5.5计算模具刃口尺寸7
5.6计算模具其它尺寸7
5.6.1凸模设计7
5.6.2凹模设计8
5.6.3定位零件9
5.6.4卸料及出件装置9
5.6.5模柄10
5.6.6模座10
5.6.7导柱和导套11
6.选用标准模架11
6.1模架的类型11
6.2模架的尺寸11
7.模具的装配12
7.1模具装配的特点和内容12
7.2模具的装配过程13
7.3模具的装配图14
8.试模和校验15
8.1试模15
8.2校验16
9.参考文献16
1.零件冲压工艺分析
1.1制件介绍
零件名称:
几字形垫片
材料:
Q235
料厚:
1.5mm
批量:
中小批量
零件图:
如图1所示
图1产品零件图
1.2产品结构形状分析
由图1可知,产品为长条形状切断并弯曲的零件,产品结构简单对称,产品厚度均匀,极易成型,而且产品尺寸要求很低。
1.3产品尺寸精度、粗糙度、断面质量分析
(1)尺寸精度
产品主要起到垫片的作用,功能简单,结构单一,所以对外在尺寸要求低,尺寸精度也是要求很低。
只要达到IT12即可。
(2)冲裁件断面质量
板料厚度为1.5,查阅相关书籍得知,生产时毛刺允许高度为≤0.15mm,本产品在断面质量和毛刺高度上没有严格的要求,所以只要模具精度达到一定要求,冲裁件的断面质量可以保证。
(3)产品材料分析
对于冲裁件材料一般要求的力学性能是强度低,塑性高,表面质量和厚度公差符合国家标准。
本设计产品所用的材料是Q235,为普通碳素结构钢,其力学性能是强度、硬度和塑性指标适中,经热处理后,用冲裁的加工方法是完全可以成形的。
另外产品对于厚度和表面质量没有严格要求,所以采用国家标准的板材,其冲裁出的产品的表面质量和厚度公差就可以保证。
(4)生产批量
产品生产批量为中小批量生产,适于采用冲压加工的方法,最好是采用复合模或级进模,这样将很大地提高生产效率,降低生产成本。
2.材料的性能分析
2.1Q235的机械性能
在板材里,Q235是最普通的材质,属普板系列。
是一种钢材的材质。
Q代表的是这种材质的屈服度,后面的235,就是指这种材质的屈服值,在235MPa左右。
并会随着材质的厚度的增加而使其屈服值减小。
由于含碳适中,综合性能较好,强度、塑性和焊接等性能得到较好配合,用途最广泛。
常轧制成盘条或圆钢、方钢、扁钢、角钢、工字钢、槽钢、窗框钢等型钢,中厚钢板。
大量应用于建筑及工程结构。
用以制作钢筋或建造厂房房架、高压输电铁塔、桥梁、车辆、锅炉、容器、船舶等,也大量用作对性能要求不太高的机械零件。
C、D级钢还可作某些专业用钢使用。
2.2Q235热处理
可以退火,一般用于焊接件毛坯的制造,由于焊接应力所以应当消除内应力,所以可以采用退火处理。
Q235板材一般出场为正火状态。
Q235截面不大时,可以进行淬火+低温回火处理。
另外进行渗碳淬火等表面处理也是可以的。
由于这个产品对各方面性能的要求都不是很高,所以就不用进行热处理了。
3.零件冲压工艺方案的确定
2.1冲压方案
完成此工件需要切断和弯曲两道工序。
其加工方案分为以下2种:
(1)方案一:
先弯曲后切断。
(2)方案二:
先切断后弯曲。
3.2各工艺方案特点分析
方案一和方案二都是采用复合模的形式,主要是因为产品零件外形简单,尺寸精度要求低,模具也是相对简单,模具制造简单,维修方便,生产效率还相对比较高。
方案一是先弯曲后切断,弯曲之后的切断工步所需要设计的模具外形相对于方案二来说更加复杂一点,而方案二先切断后弯曲就没有方案一的这个问题。
3.3工艺方案的确定
结合本零件的设计要求,方案二模具形状非常简单,容易设计,容易生产,节约成本,所以综合考虑,决定采用方案二。
4.冲模结构的确定
4.1模具的结构形式
复合模可分为正装式和倒装式两种形式。
(1)正装式的特点:
工件和冲孔废料都将落在凹模表面,必须清除后才能进行下一次冲裁,造成操作不方便、不安全,但冲出的工件表面比较平直。
(2)倒装式的特点:
冲孔废料由冲孔凸模落入凹模洞口中,积聚到一定的数量,由下模漏料孔排出,不必清除废料,但工件表面平直度较差,凸凹模承受的张力较大。
4.2模具结构的选择
经分析,若工件表面平直度较差,影响零件的使用,而工件和冲孔废料在有气源车间可以方便地清除。
综合比较两种方式,决定采用正装式复合模。
5.主要工艺计算
5.1零件毛坯尺寸计算
确定外形尺寸
制件要有切断和弯曲工序,切断工序的话就要求选择的条料宽度尺寸已经满足产品零件的要求,零件的宽度公称尺寸为10mm,上下偏差都为0.1mm。
5.2排样
(1)单排(如图2)
图2产品拍样图
(2)板料利用率
板料的利用率为100%。
5.3剪切力和弯曲力的计算
5.3.1切断工序
F=KLtτ
式中L——冲裁件周边长度mm
t——材料厚度mm
τ——材料抗剪强度MPa
K——系数。
考虑到模具刃口的磨损,模具间隙的波动,材料力学性能的变化及材料厚度偏差等因素,一般去K=1.3。
故
F=KLtτ=1.3×
10×
1.5×
150=2925N
5.3.2弯曲工序
F=(CKBt*t)/(r+t)*σ
式中C——与弯曲形状有关的系数,对于U形件C取0.7
K——安装系数,一般取1.3
B——料宽mm
t——料厚mm
r——弯曲半径mm
σ——材料强度极限MPa
故
=(0.7×
1.3×
1.5)/(1+1.5)×
235
=1924N
5.4剪切凸模和凹模间隙的计算
切断间隙是指模具凸模和凹模刃口之间的间隙。
剪切间隙分单边间隙和双边间隙,单边间隙用C表示,双边间隙用Z表示。
间隙值的大小对零件质量、模具寿命、剪切力的影响很大,是剪切工艺与模具设计中的一个机器重要的工艺参数。
根据零件的制造精度和材料厚度,查阅相关书籍得到冲模的制造精度为IT9。
凹模和凸模的单边间隙为0.2mm。
5.5计算模具刃口尺寸
(1)剪切模刃口尺寸
查表可得
=0.36mm,
=0.50mm
-
=0.50-0.36=0.14mm
=+0.03mm,
=-0.02mm
由此可得
故能满足分别加工的要求。
查表可得磨损系数X=0.5,剪切件基本尺寸为58mm,取精度为IT12,则其公差
,上偏差和下偏差分别为=0.23mm和-0.23mm。
由此可得
L落凹=(Lmax-XΔ)+
=58.03mm
L落凸=(Lmax-XΔ)-
-Δ=57.56mm
5.6计算模具其它尺寸
5.6.1凸模设计
剪切部分的凸模刃口尺寸方形,为了便于凸模和固定板的加工,将剪切凸模设计成台阶式。
将冲孔凸模设计成台阶式。
小端方形部分,是具有锋利刃口的工作部分,采用台肩式固定。
凸模材料采用T10A,凸模工作端(即刃口)淬硬至HRC56~60,凸模外形尺寸如图3所示
图3凸模
5.6.2凹模设计
凹模的结构形式和固定方法:
凹模采用矩形板状结构,通过螺钉、销钉与下座连接固定。
凹模刃口的结构形式:
因冲件的批量不大,考虑凹模有磨损和保证冲件的质量,凹模刃口采用直刃壁结构,刃壁高度取7mm。
凹模材料和技术要求:
凹模的材料选用T10A。
工件部分淬硬至HRC58~62。
外轮廓棱角要倒钝。
凹模的形状及尺寸如图4所示:
图4凹模
5.6.3定位零件
定位零件的作用是使坯料或工件在模具上相对凸、凹模有正确的位置。
选用挡料销一个。
挡料销的作用是挡住条料搭边或冲件轮廓以限定条料送进的距离,挡料销固定在位于下模的固定板上,材料45号钢,硬度为43~48HRC
选用导料两块,前面一块后面一块。
导料板的作用是保证条料送料的准确,在条料的两侧各一块
5.6.4卸料及出件装置
卸料采用弹性卸料装置,由,卸料板,卸料螺钉,弹性元件(这里是弹簧)组成。
出件装置由打杆、推板、连接推杆、顶件块组成。
。
5.6.5模柄
模柄的作用是把上模固定在压力机滑块上,同时使模具中心通过滑块的压力中心,模柄的直径与长度与压力机滑块一致,模柄的尺寸规格选用凸缘模柄。
用模柄肩的形式固定在上模座上。
模柄的形状尺寸如图5所示:
图5模柄
5.6.6模座
标准模座根据模架类型及凹模同界尺寸选用,
上模座:
130mm×
130mm×
25mm;
下模座:
30mm;
模座材料采用灰口铸铁,它具有较好的吸震性,采用牌号为HT200。
5.6.7导柱和导套
导柱选用A型导柱,A20h5×
120 GB2861.1-81。
材料为20钢,热处理要求:
渗碳深度为0.8~1.2,硬度HRC58~62。
导套选用A型导套,A20H6×
65×
23 GB2861.6-81。
6.选用标准模架
6.1模架的类型
模架包括上模座、下模座、导柱和导套。
冲压模具的全部零件都安装在模架上,为缩短模架制造周期,降低成本,我国已制定出模架标准。
根据模架导向用的导柱和导套间的配合性质,模架分为滑动导向模架和滚动导向模架两大类。
每类模架中,由于导柱安装位置和数量的不同,由有多种模架类型,如:
后侧导柱式、中间导柱式、对角导柱式和四角导柱式。
选择模架结构时,要根据工件的受力变形特点、坯料定位和出件方式、板料送进方向、导柱受力状态和操作是否方便等方面进行综合考虑。
在此选用滑动导向型的后侧导柱式模架。
6.2模架的尺寸
选择模架尺寸时要根据凹模的轮廓尺寸考虑,一般在长度及宽度上都应比凹模大30~40mm,模版厚度一般等于凹模厚度的1~1.5倍。
选择模架时,还要考虑模架与压力机的安装关系,例如模架与压力机工作台孔的关系,模座的宽度应比压力机工作台的孔径每边约大40~50mm。
在本设计中,凹模采用方形的结构,其工作部分基本尺寸为60mm,壁厚为30mm,所以其长度为125mm,厚度为h=30mm。
模具的闭合高度H应介于压力机的最小装模高度
与最小装模高度
之间,其关系为:
+10≤H≤
-5
由上面压力机的选择可知道
=300mm,
=
-70=230mm。
所以H应介于225mm~310mm之间。
查阅冲模手册可知,选用的模架为、上模座、下模座分别为:
模架:
250×
250×
(240~285)GB/T2851.3
上模座:
50GB/T2855.5
下模座:
65GB/T2855.6
由此可知其最大装模高度为285mm,最小装模高度为240mm,符合H的要求。
下模座周界尺寸为250×
250,而凹模的长度为125mm,所以周界尺寸符合要求。
下模座厚度为30mm,而凹模的厚度为30mm,也符合要求。
工作台孔尺寸为150mm,模座的宽度也比工作台孔尺寸大,也符合要求。
根据模具的结构,可知其闭合高对为
式中:
-模具的闭合高度,mm;
-上模座厚度,mm,由前可知
=50mm;
-上垫板厚度,mm,此处选
=5mm;
-凸模固定板厚度,mm,由前可知
=25mm;
-上凸凹模长度,mm,由前可知
=65mm;
-制件厚度,mm,此处
=2.5mm;
-下推板厚度,mm,由前可知
=21mm;
-下凸凹模固定板厚度,mm,由前可知
-下垫板厚度,mm,选取
-下模座厚度,mm,由前可知
=65mm。
综上可得
介于225mm和310mm之间,符合设计要求。
7.模具的装配
7.1模具装配的特点和内容
模具的装配属单件小批装配生产类类型,特点是工艺灵活性打,工序集中,工艺文件不详细,设备、工具尽量选通用的。
组织形式一固定式为多,手工操作比重达,要求工人有较高的技术水平和多方面的工艺知识。
模具装配的内容有:
(1)选择装配基准件选择基准件的原则是按照模具主要零件加工的依赖关系来确定的。
可做基准件的主要有凸模、凹模、导向板及固定板等。
(2)组件装配组件的装配是指模具在总装前,将两个以上的零件按照规定的技术要求连接成一个组件的装配工作。
(3)总体装配总体装配是将零件盒组件结合成一幅完整的模具过程。
在总装前,应选好装配基准件和安排好上、下模的装配顺序,然后以基准件为准,按工艺顺序装相应的零件。
(4)调整凸、凹模间隙在装配模具时,必须严格控制及调整凸、凹模间隙的均匀性。
间隙调整合格后,才能固紧螺钉并打入销钉。
(5)检验、调试模具装配完毕后,必须保证装配精度,满足规定的各项技术要求,并按照模具的验收技术条件,检验模具各部分的功能。
7.2模具的装配过程
(1).组件装配
模具总装前,将主要零件如模架、模柄、凸模进行组装。
1)将模柄装配与上模座内,并磨平上平面。
2)将凸模装入凸模固定板内,成为凸模组件。
3)将凸凹模装入凸凹模固定板内,成为凸凹模组件。
4)将导柱、导套压入上下模板,成为模架。
(2).确定装配基准件
落料冲孔复合模应以凸凹模为基准件,首先确定去凹模在模架中的位置。
安装凸凹模组件,加工下模座漏料孔。
(3).安装上模部分
1)检查上模各零件尺寸是否能满足装配技术条件要求。
2)安装上模,调整冲裁间隙。
3)钻铰上模销孔和螺孔。
(4).安装弹性卸料部分
将弹性卸料板套在凸凹模上,安装弹簧和鞋料螺钉。
7.3模具的装配图
模具的装配图如图7和图8所示:
图7装配图
1-下模座帮;
2-导柱;
3-圆柱销;
4-推杆;
5-推板;
6-导料板;
7-导套;
8-挡料销;
9-凸模固定板;
10-上模座板;
11-内六角螺钉;
12-圆柱销;
13-模柄;
14-打杆;
15-凸凹模;
16-压料板;
17-螺钉;
18-垫板;
19-弹簧;
20-卸料板;
21-凹模;
22-内六角螺钉;
23-内六角螺钉
其工作原理为:
该模具由导料板6和挡料销8控制条料的送进方向和步距。
上模下行,进行冲裁,导柱、导套对上、下模的运动起到可靠的导向作用。
冲裁过程中,弹性卸料板20对板料起着压平作用,冲才出的工件精度高。
冲裁完毕,上模回程,上模部分的弹性卸料装置将卡在凸凹模外的废料卸下,最后包裹在弯曲凸模上的零件由推板5和推杆4推出。
图8装配图俯视图
8.试模和校验
8.1试模
模具安装完毕之后,必须要通过试冲对制件的质量和模具的性能进行综合考查与检测。
对试冲中出现的各种问题应作全面、认真的分析。
找出其产生的原因.并对冲模进行适当的调整与修正,以得到合格的制品零件。
在模具生产中.试模的主要目的是确定制品零件的质量和模具的使用性能好坏。
这是由于制品零件从设计到批量生产需经过产品设计、工艺设计、模具设计、模具零件加工、模具组装等若干工艺过程。
在这些过程中,任何一项的工作失误,都会引起模具性能不佳和难以生产出合格的制品零件来。
因此,冲模组装后,必须首先经过在生产条件下的试冲,并根据试冲后的成品,按制品零件设计图.检查其质量和尺寸是否符合图样规定的要求,其所制造的模具动作是否合理可靠。
根据试冲时出现的问题,分析产生的原因,并设法加以修正,使所制造的模具不仅能生产出合格的零件,而且能安全稳定地投人生产使用。
8.2校验
模具试模完成之后,如果加工出来的产品不合格,那就要对模具进行校验,对症下药,模具的哪一部分出了问题就要及时的进行修复与调整,保证加工出来的零件是符合标准的。
9.参考文献
[1]周本凯.冲压模具设计实践100例[M].北京:
化学工业出版社,2008.3.
[2]薛啟翔.《冲压模具设计和加工计算速查手册》.北京:
化学工业出版社,2007.10
[3]朱立义.冷冲压工艺与模具设计.重庆大学出版社.2006
[4]周玲.冲模设计实例详解[M].北京:
化学工业出版社,2007.3.
[5]周本凯.冲压模具设计实践100例[M].北京: