造气岗位操作要点Word格式文档下载.docx
《造气岗位操作要点Word格式文档下载.docx》由会员分享,可在线阅读,更多相关《造气岗位操作要点Word格式文档下载.docx(19页珍藏版)》请在冰豆网上搜索。
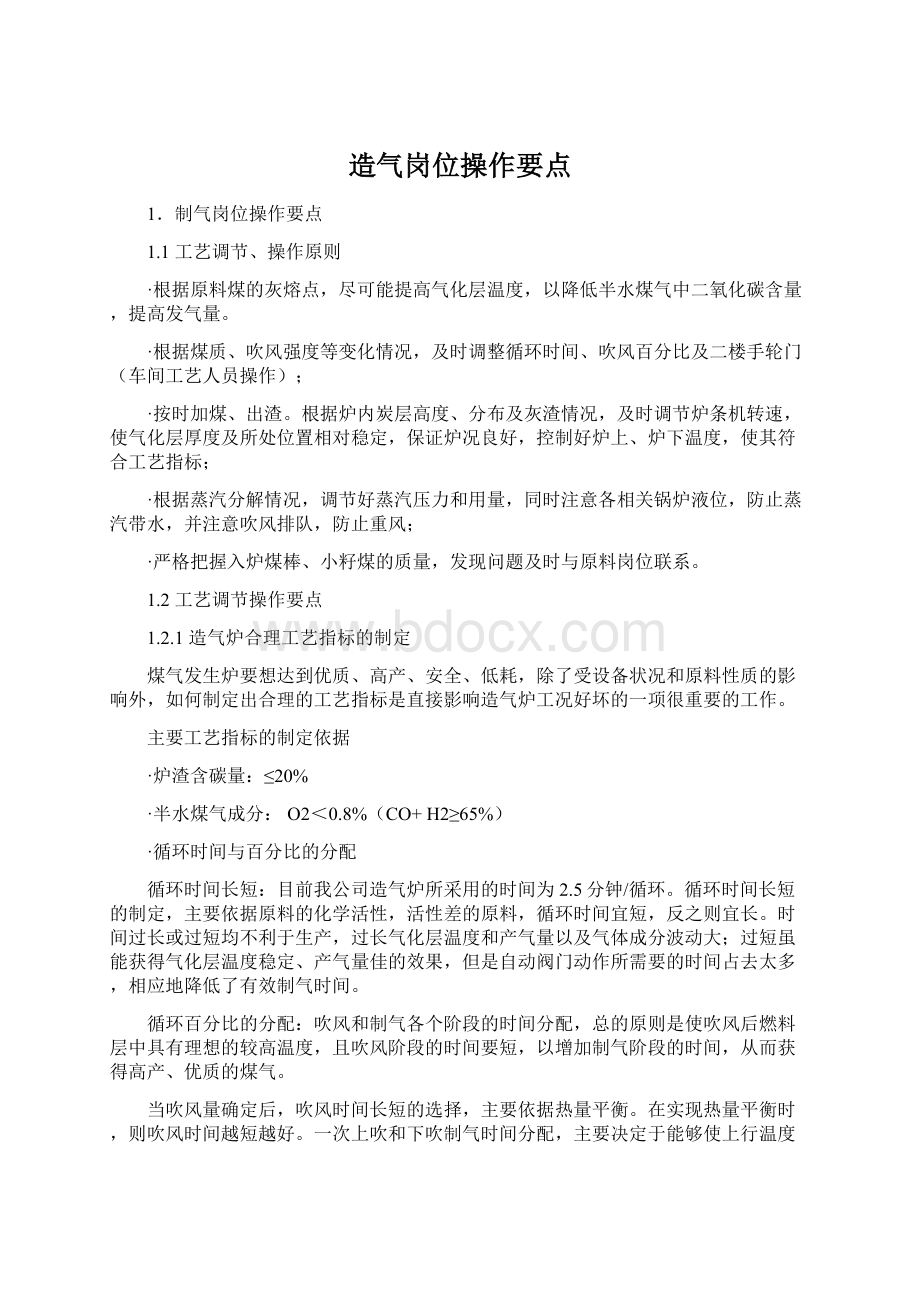
二次上吹和空气吹净无较高要求,只要能达到安全生产和回收余气的目的就可以。
温度
上行温度:
原料化学活性和灰熔点是制定上行温度的重要依据。
煤球和煤棒的冷、热强度差,不宜高,一般在300~400℃。
下行温度:
下行温度的制定,主要防止炉下温度过高而烧坏设备,其温度高低也决定于气化层上下移动的变化。
一般下行温度在200~300℃为宜。
气化层温度(火层):
在实际生产中气化层温度目前还无法用仪表直接测量出,只能通过炉上、下温度和用探测炉内火层情况来推测。
根据不同的炉型,有两种方法:
一种使用钢钎垂直插入炉内,钢钎在炉内烧2~3分钟后拔出,烧红部分在200~300毫米为宜,另一种是钢钎(俗称火棍)水平方向查入炉内2~3分钟,烧红部位在200~400毫米为宜。
在制定工艺指标时切忌盲目追求大火层,虽然火层大,气化层温度高,产气量高,气体成分好,但是火层大易造成炉内结大块,烧坏炉篦和灰盘,给生产带来更大损害。
流量
空气流量:
根据不同的炉型和燃料性质来选择造气炉的理想吹风强度,应在不破坏固定床层的条件下,送入的空气量达到最大值,使炭的燃烧达到最佳状态。
从节能角度考虑,吹风气中CO含量要求越低越好,可减少能量损失。
在燃烧较好的情况下,吹风气中CO和O2含量应在1.0%以下较为合理。
入炉蒸汽流量:
入炉蒸汽流量适中与否是决定造气炉气化效率高低的一项重要因素。
入炉蒸汽量过少,造成炉内气化层温度过高,结疤结块,严重影响煤气的产量和质量;
入炉蒸汽量过多,蒸汽分解率下降,气化层温度下降过快,燃料气化不完全,炉渣含炭量过高,也同样影响到煤气的产量和质量。
半水煤气中CO2含量:
半水煤气中CO2含量指标,是诊断造气炉气化情况正常与否的脉搏,也是判断入炉蒸汽用量是否恰当的一个重要指标。
控制好上、下吹半水煤气中CO2指标,是调节蒸汽流量的主要依据。
灰盘转速
灰盘转速指标的制定,主要决定于燃料本身灰份含量的多少、造气炉负荷的高低以及灰盘本身转速的快慢。
平时的调节主要依造气炉火层和炭层下降情况而加以调节。
炭层高度
合理的炭层指标,大都是通过生产实践不断摸索出来的。
要根据炉型和所使用原料性质及系统阻力而定。
一般认为,燃料层的阻力不宜太大,在炉内风量达到最大时,以不破坏气化层为宜,我公司一般控制在见夹套为宜。
1.2.2造气炉理想生产负荷的选择
煤气发生炉的负荷,实质上是指吹风强度,理想的吹风强度是在炉内燃料层不被吹翻原则下,尽量加大吹风量(燃料层的总高度也要在理想高度范围内,不宜太高或太低)。
高风量的目的是在较小的吹风百分比的条件下,能保持气化层有较高的温度。
在高风量、高炉温的条件下,气化反应速度快,生成的吹风气能迅速地离开燃料层表面,炭和氧接触时间短,不利于吹风气中的CO2还原成CO,有利于降低能耗。
高负荷生产能使气化层温度迅速上升,可以缩短吹风阶段时间,增加制气时间。
另外,由于高负荷条件下气化层温度升高,入炉蒸汽用量也相应地增加,故发气量也大。
需要说明的是,因使用的原料性质不同,其最佳吹风强度也不同,要根据本企业自己实际情况选择造气炉最佳负荷,不可盲目追求造气炉高负荷。
值得注意的是,造气炉处于高负荷生产时,许多工艺条件大都处于临界状态,要求高度集中精力操作,一旦疏忽,即会造成气化层情况恶化,出现结疤、结块、风洞等异常情况。
1.2.3造气炉合理吹风率的调节
吹风率(即单位时间内吹风空气流量)的选择,主要依据燃料的特性及燃料层的控制高度的变化。
粒度比较小或热稳定性比较差的燃料,一般应选择比较低的吹风率,反之,应选择较高的吹风率。
当造气炉所用燃料的粒度和品种变更时,吹风率也要及时进行调整。
另外,燃料层的控制高度比较高时,其燃料层的阻力也相应增加,会使吹风率降低,此时如果盲目提高吹风率,容易造成燃料层吹翻。
如果保持或提高气化层温度,只宜增加吹风百分比。
燃料层的控制高度较低时,一般由于燃料层的阻力相应减少,会使吹风率增高,其燃料层温度会相应增高,可适当提高燃料高度,或适当降低吹风率,否则会使燃料吹翻。
1.2.4吹风百分比的最佳选择
最佳吹风时间的分配,以使燃料层具有较高温度为主要原则,即利用较短的时间达到最高温度。
实现这个目的,决定于空气鼓风机能否提供较高的空气流速和燃料层是否能承受较高的空气流速。
原料煤性质与吹风时间分配随燃料的机械强度、热稳定性及化学活性的不同而有差别。
一般而言,上述三种性质较好,燃料层阻力小,有利于提高空气流速,只要用较少的时间就能使燃料层达到高温,反之则相反。
燃料层的阻力,除了受燃料的机械强度和热稳定性的影响外,与燃料层的高度和煤的粒度都有很大的关系。
此外,气化剂在燃料层的分布均匀与否与炉篦结构也有关系。
我厂吹风百分比大都在24~26%之间,利用高强度风机后,吹风百分比可下降到20%左右。
1.2.5造气炉一个工作循环内各阶段产气量的变化
吹风阶段结束后,炉内气化层温度最高,一次上吹制气初期是气化最佳时期,产气量和煤气质量好。
随着制气时间的推移和阶段的转化,产气量逐渐下降,气体质量也随之下降,至二次上吹结束前,是一个工作循环中制气最差阶段。
1.2.6上下吹蒸汽用量不当的危害
上、下吹入炉蒸汽用量不当会影响炉内工况的正常,严重时还会使炉内气化层恶化,甚至于迫使炉子熄火,进入炉内打疤打块。
上、下吹蒸汽用量同时过大,炉内气化层温度低,产气率低,蒸汽分解率低,灰渣中返炭高。
有些企业所谓开太平炉,就是这种状况,不挂壁、不结疤、不结块,但产气量低,而且能耗很高;
上、下吹蒸汽用量同时都过少,则会出现炉上挂壁结疤,炉下结大块,虽然蒸汽分解率高,但是因炉况恶化无法维持生产,最终只有熄火处理;
上吹蒸汽用量大于下吹蒸汽用量太多,会出现气化层严重上移,炉上表面因温度过高,而造成结疤挂壁。
炉下则出现温度低返炭高,整个气化层上移到炉面气化,无疑气化效率相当低;
下吹蒸汽用量大于上吹蒸汽用量过多,则会出现气化层严重下移,炉上温度低,炉下温度高,严重时会出现烧坏炉篦和灰盘等设备,此种情况,一般炉篦传动机构因炉下温度高灰盘膨胀无法启动,也就是人们常说的“造气炉变成了炼铁炉了”。
1.2.7上下吹蒸汽用量差值的选择
一般来说,下吹蒸汽用量要大于上吹蒸汽用量,因为下吹蒸汽用量大,可使气化层集中在比较理想的位置,不会造成炉上温度偏高而发亮挂壁;
上下吹蒸汽用量的差值究竟多大为宜,主要根据造气炉使用原料品种而定,一般烧优质原料的蒸汽差值在1.0~1.5吨/时范围内,如果烧劣质原料其差值就可以小些,可在0.8~1.0吨/时之间,有时因为所用的原料熔点过低,还会出现上吹蒸汽用量大于下吹蒸汽用量的现象。
1.2.8制定造气炉上下吹时间和蒸汽用量的依据
一般是根据造气炉所使用的原料性质和以往的实践经验订出百分比和上、下吹蒸汽用量,然后根据分析测定数据加以调整。
如果造气炉所使用的原料灰熔点低,灰份高,固定碳低,则上吹蒸汽用量适当加大些,上吹制气时间适当加长些,同时灰盘转速适当加快,使气化层稳定在规定的位置上;
对那些粒度或机械强度差的原料煤,炉内床层阻力大,吹风时空气中的氧与炭的燃烧反应往往集中在炉下部,所以上吹制气时间要长些,上吹蒸汽用量也应放大些,反之则相反;
在理论上还可通过原料的发热值和吹风时间的长短来决定上、下吹百分比和蒸汽用量之差。
一般使上吹时间的蒸汽用量与炭起反应所吸收的热量,基本上等于下吹时间的蒸汽用量与炭起反应所吸收的热量;
造气炉使用任何不同品种的原料都要通过实践摸索,逐步达到最佳制气条件。
通常调节上、下吹百分比和蒸汽用量多少的主要依据是根据单炉上、下吹气体成分中CO2含量多少和蒸汽分解率高低来决定的;
实践证明下吹CO2<
上吹CO21~1.5%为宜,一般而言,蒸汽用量改变0.25吨/时,相当于改变1%制气百分比,在调节两者之间的分配时,以改变百分比的效果更好些。
造气炉一次产气量增加1500m3/时左右,则需要增加上、下吹蒸汽各0.25吨/时。
1.2.9正确调节造气炉上下吹入炉蒸汽用量
上、下吹入炉蒸汽用量的多少,是直接影响气化炉炉内工况好坏的重要因素之一。
当上、下吹百分比分配比较合理时,一般都采用上、下吹蒸汽来维持造气炉的正常工况,调节上、下吹蒸汽用量的主要依据如下:
根据炉上、炉下温度高低变化情况进行调节;
视单炉上、下吹半水煤气成份CO2含量高低进行调节,在炉况正常的情况下CO2偏高,则说明蒸汽用量过多,反之则蒸汽用量太少;
根据炉内出灰渣情况进行调节,排出渣中块度太大且又硬,应适当增加上吹蒸汽用量,如排出渣较碎而且返炭高,则应适当减少上吹蒸汽用量。
1.2.10炉渣含炭量高的原因
造气炉操作失控,造成气化层下移或偏移,致使未燃尽的炭进入灰渣区;
灰盘转速过快;
蒸汽用量过大;
造气炉负荷太低,致使气化层温度低;
气化床被破坏,出现漏炭或炉下有大块;
原料粒度不均,大小悬殊太大;
原料含粉量太多,致使床层阻力增加;
原料中煤矸石过多,影响气化层温度提高;
灰盘排灰口过高或灰犁过长,易形成漏炭和排渣强度增大;
炉篦通风不均或通风面积过小,炉篦无破渣力;
加煤不匀,截面炭层高低悬殊过大,造成床层阻力偏差。
1.2.11造气炉正常生产时加减负荷
加负荷的步骤
炉温维持不变,适当提高炭层(即增加入炉煤量);
加大吹风量,如果入炉风量到了极限值时,可增加吹风百分比;
炉温上涨后,适当加大上下吹蒸汽用量。
减负荷的步骤
减小吹风量或吹风百分比;
炉温维持不变,炭层高度适当降低;
如果炉温开始下降即减少入炉蒸汽用量。
加减负荷时均不能过猛,要慢慢进行,另外蒸汽用量要及时进行调整;
加减负荷一段时间之后,要注意及时调整灰盘转速。
1.3炉况控制操作要点
1.3.1炉温控制操作要点
1.3.1.1造气炉负荷不变的情况下影响炉温波动的因素
原料性质改变
原料的发热值和固定碳含量减少,水分和煤矸石增加,都会影响炉温下降,反之则升高;
入炉原料过分潮湿,致使水分在炉内蒸发时吸收的热量较多,另外因煤湿,过筛不干净,带入炉内的粉煤过多,增加炉内阻力,致使风量下降,炉温也下降;
入炉原料粒度变化对炉温也有影响,炉温随着粒度逐渐变大而升高,反之则会下降;
人工加煤时入炉煤量波动大,炉温波动也大。
炉内压力的变化
气柜高低之影响,气柜高时气柜内部压力大,气流阻力大,制气时蒸汽入炉量会减少,炉温会升高;
入炉原料粒度的变化,炭层高低波动,煤量多少、含粉率的高低等都会影响炉内压力的变化而造成炉温波动;
入炉蒸汽压力波动太大(蒸汽来源处故障或蒸汽压力波动,调节阀失灵等原因),则也会影响到炉温波动。
阀门失常
加氮阀开关过快或过慢,流量过大过小以及由于加氮时空气流量的变化而影响吹风时空气流量的变化(因为吹风、加氮空气管是并联的)等原因都会导致炉内温度波动;
下行煤气阀泄漏,吹风时有部分空气由下行煤气阀漏入煤气系统,实际入炉风量减少,也会使炉温下降;
此外吹风阀及上、下吹蒸汽阀、蒸汽总阀、三气阀、水封阀出现故障,不开或不关都会影响炉温波动。
操作失误方面的原因
炉子吹风排队没有安排好,时而单炉吹风,时而多炉同时吹风,造成入风量紊乱,风量无法稳定而影响炉温波动;
炉内气化层出现异常情况,如结大块、结疤、风洞、吹翻、滑炭、火层失常等原因都能引起炉温波动;
在正常制半水煤气时,因处理循环氢需要,改加减氮或打回收,都会影响炉温波动;
人工加煤的炉子,多做循环或少做循环、煤棒烘炉时间长短也易引起炉温波动。
1.3.1.2控制造气炉上行温度的意义及方法
造气炉的上行温度,一般指炉子上部煤气出口温度和炉面温度,其温度高低根据使用燃料品种和粒度不同以及炉膛直径大小而有所区别。
炉上温度过高,不但使煤气带出的热量过多,增加煤的消耗,而且稍有不慎会造成炉上四周发亮挂壁。
炉上温度过低,则说明气化层温度也低。
其原因可能是入炉风量太少或下吹蒸汽太大,也可能是气化层(火层)严重下移,它直接影响造气炉的发气量和质量。
因此,控制好上行温度的意义十分重要。
要想控制好上行温度,首先要了解造气炉所使用燃料的性质;
根据燃料性质,制定出上行温度的工艺指标;
分配好微机上下吹阶段百分比,一般而言,下吹阶段稍大于上吹阶段;
在确保炉况正常的情况下,选择最大吹风强度;
上、下吹蒸汽用量适当,一般可通过上、下吹半水煤气中CO2含量来加以验证。
经过多年实践表明上吹半水煤气(不含回收吹风气)中CO2含量比下吹半水煤气中CO2的含量要大1.0~2.0%。
1.3.1.3影响上行温度变化的因素
影响上行温度变化的原因很多,情况也较复杂,发现上行温度变化时,需要通过其它仪表来对照判断寻找出影响变化的主要原因,并加以消除。
影响上行温度升高的原因有:
吹风阶段,吹风电磁阀卡或阀门不落,造气炉长期处于吹风阶段,致使炉上温度猛涨;
上行煤气阀不落,使下吹制气时下吹蒸汽未全部入炉;
由于某种原因入炉蒸汽总管内的压力在下吹制气阶段变低,致使下吹入炉蒸汽减少;
空气流量瞬间过大,致使炭层吹翻或吹成风洞;
气化层(火层)上移造成炉面发亮(发白);
人工加煤时,入炉炭量减少。
影响上行温度下降(人工加煤时上行温度上升幅度减少)的原因有:
-空气阀或加氮阀不开,造成无风入炉;
-下行煤气阀关不严或不到位,致使吹风阶段的空气不能全部入炉,部分空气走短路直接经下行煤气阀入煤气总管(同时还会造成半水煤气中氧高);
-吹风阶段百分比紊乱,致使吹风百分比减少;
-在下吹制气阶段,下行煤气阀电磁阀卡或不落,造气炉长期下吹制气,造成炉上温度骤降;
-改做水煤气的时间过长;
-入炉炭量过多,炭层增高,致使炉内阻力增加,风量相应减少;
-下吹蒸汽量过大。
1.3.1.4造气炉下行温度的控制及对发气量的影响
正常生产时下行温度控制范围在200~300℃为宜,下行温度过高,则说明气化层下移,不但影响造气炉发气量,而且会烧坏炉篦及灰盘等设备。
温度过低,则说明气化层上移,也会影响造气炉发气量,同时因炉下温度过低还会造成燃烧不完全,致使灰中返炭高燃料消耗增高。
1.3.2炉况异常的判断及处理操作要点
1.3.2.1控制好造气炉气化层的意义及方法
意义:
造气炉“火层”是“气化层”的俗称,它包括氧化层(也叫燃烧层)和还原层,造气炉内工况好坏的各种迹象表现,实际上都为火层的分布状态所决定。
因为炉内主要气化反应都在这一区域中进行,火层分布均匀和火层厚薄与否,对制出气体的质量和数量起着决定性的作用。
因此,维持造气炉正常火层是节能增产的有效途径。
方法:
要想控制好造气炉内火层,首先要订出合理的火层指标。
操作中要做到两勤:
勤观察:
经常注意造气炉工艺条件的变化,一旦出现异常要及时处理。
勤调节:
使造气炉气化所生成的渣要基本上等于排渣强度。
此外,调节好上、下吹百分比也很重要,其比例不当亦能使火层失常。
下行温度是判断火层正常与否的重要依据之一,一般来说,温度过低是火层上移的表现,因此控制好下行温度(我厂为250~300℃为宜)也是十分重要的。
对影响火层正常的设备,应及时检修、改进和更换。
气化层失常的原因及处理
火层不正常的情况比较复杂,其原因也是多方面的,现分述如下:
火层上移
造气炉火层上移,一般可分为一般上移和严重上移两种。
造成一般上移的原因是由于灰盘转速过慢,造气炉排灰强度下降,灰层逐步积厚,造成火层上移。
处理方法是加快灰盘转速,提高排渣能力,待火层恢复正常后,再将灰盘转速减慢到比原来转速稍快点即可。
如不及时减速又会出现火层下移现象。
造成火层较长时间严重上移的原因就比较复杂,除了操作上的失误因素之外,还有设备和原料方面的问题。
如造气炉排灰装置中的灰筋(推灰器)磨损及灰犁磨损、弯曲、脱落和排灰口的高度过小等情况均会影响排渣能力下降。
一般属于原料方面的原因,大都是因原料劣质煤含灰份较高,由于灰份过高致使造气炉排灰能力跟不上,因而造成火层上移。
当出现火层严重上移时,首先分析其主要原因是什么,然后逐一加以解决。
如系设备原因就要及时检修和更换损坏设备,如系原料问题,就要认真研究,或改变原料品种,或改进炉子排灰结构,加快排渣能力。
火层下移
造成火层下移的原因大都是灰盘转速过快,使正常的灰渣层遭到破坏并消失,气化层进入灰渣层位置。
这种情况一般可以从炉篦和炉下温度迅速上升及炉条机系统负荷增大(炉下超温设备膨胀致使负荷增大)等方面发现,一般的处理方法是:
迅速减慢灰盘转速,或者在慢速的情况下将炉条机开开停停;
加大负荷使下移的气化层尽快燃尽,已达到早些恢复正常的灰渣层的目的;
必要时可采取临时性减少下吹制气时间,增加上吹制气时间,避免下移时间过长而烧坏设备。
其方法可用加大上吹蒸汽或减少下吹蒸汽用量,也可短期地变动上下吹百分比。
火层偏移
火层偏移的情况比较复杂,其中因偏移的程度不同而差别很大。
包括:
一边火层正常而另一边无火层;
一边火层短而另一边火层正常;
一边无火层而另一边火层短;
火层两边均偏向炉篦及两边火层均薄。
上述这些情况均属于火层偏移范围,但由于情况不完全一样,故其处理方法亦不同。
造成火层偏移的原因有:
因某一边的灰犁损坏或脱落而使该边排渣能力下降,从而导致该边火层短或无火层;
两边排灰口的高度不一样,排灰口高度过低的一侧则排灰量少,同样影响火层正常;
炉内有大疤块将某一边排灰口堵塞,被堵塞的这边排灰量少或不排灰,火层必然受到影响;
因炉篦结构不合理,气化层不能均匀的向下移动,同时气流分布不匀。
这两种因素均能引起火层偏移;
造气炉加煤时分布不匀,造成炉内燃料层阻力不均匀,炭层低阻力小的一边则气化剂走得多,气化得快,灰层易增厚而导致火层短或无火层。
火层偏移的处理方法:
如果属于设备问题,应及时进行检修或更换有缺陷的设备;
如果是操作失误而造成火层偏移,应对无火层或火层差的一边加强临时性的人工排渣(即扒块),直至两边火层厚度相等为止;
如果是一边无火层,一边火层短,除对无火层一边稍加人工排渣之外,还可适当加快灰盘转速,使之尽快达到平衡;
火层两边均偏向炉篦的情况就较难处理,虽然两边属于火层短现象,但是火层偏移均靠向炉篦,此情况持续时间长易烧坏炉篦,所以处理时要慎之。
尽管火层短,还不宜加快灰盘转速,一般应采取减慢灰盘转速或暂维持现状的情况下采取适当加负荷的方法,使靠近炉篦的燃料尽快燃尽,以达到消除炉篦周围的高温区。
待两边均无火层时再加快灰盘转速,使燃料层稳步下移。
一边无火层,但另一边火层也是靠近炉篦的情况在处理时亦可参照此方法进行处理。
其他情况
两边火层薄的情况,其处理方法较简单,只要稍加快灰盘转速即可;
还有一种情况是炉上、下温度都高的反常情况,也就是人们常说的“两头发烧”。
像这样既是火层下移,又是火层上移的现象,在生产中亦是常见的,其主要原因是操作失误造成的。
出现这种情况应该是抓住主要矛盾,首先处理火层下移,即加大负荷,加快灰盘转速,使灰盘上的燃料层尽快燃尽排掉,待正常火层慢慢形成后再减慢灰盘转速。
“两头发烧”是难处理的,在处理过程中往往会碰到一个棘手的问题,就是当灰盘上温度较高时,会出现熔融状红软块,这种红软块即使加快灰盘转速也无济于事。
它会严密地堵塞住两边排灰口,此时应当加大上吹蒸汽增加蒸汽对红软块的接触,使之尽快变黑变脆,已达到尽早排出的目的。
另外也可人工扒块协助早些正常。
通过以上处理措施使火层即将恢复正常时,一定要注意灰盘速度及时调节,使之调节在最佳范围内,否则会大起大落,火层难以较快恢复正常。
1.3.2.2从床层阻力来判断炉内工况是否正常
炉内出现异常时,床层阻力就会发生变化,因此,平时操作中只要经常注意阻力的变化就可以判断炉内工况的好坏。
如炉内阻力突然下降,则说明气化层遭到破坏,炉内则可能出现风洞或吹翻等异常现象;
如果阻力慢慢下降,则说明整个燃料层高度在逐渐降低;
如果阻力逐渐增加则说明燃料层高度慢慢高起来;
如果床层阻力突然增加较多,而且导致炉系统阻力也增加较大,出现炉底水封冲破,吹风气防爆门大量泄漏等现象,此现象很可能是系统中出现故障,如洗气塔堵塞导致煤气送不出去等原因。
在正常生产时吹净阶段炉下阻力最高,吹风时次之,上、下吹制气时再次之。
另外使用燃料中的焦炭、块煤、煤球、煤棒及粒度大小、含粉量多少、机械强度、热稳定性高低等情况,其床层阻力有所区别。
影响造气炉阻力降的因素
影响造气炉阻力的因素较多,常见的有:
原料的品种不同;
原料的粒度大小和粒度大中小未分级使用;
原料的机械强度和热稳定性好坏;
炉篦的结构功能;
系统流程中各设备堵塞情况;
流程设计的繁简。
1.3.2.3从灰渣判断炉况的正常
从造气炉内排出的灰渣好坏,可以判断造气炉气化层温度的高低和工况是否正常。
如果蒸汽用量过大,上下吹百分比失调,灰盘转速过快,则会出现炉渣中粒度过碎及返炭高的现象。
气化层温度过低,炭燃烧不完全也会出现这种现象。
反之,因灰盘转速过慢,炉内负荷过大,蒸汽用量过小导致气化层温度过高。
当超过灰熔点时,极易结成大块渣,严重时大块堵住排灰口影响炭层下降(有时出现两侧灰斗排灰量不等情况),表明炉内工况处于失常状况。
造气炉内结大块的原因及处理
常见的结块原因有:
-原料煤(焦)质量差,灰熔点低,煤矸石多,固定碳低,灰份和含粉率高;
-蒸汽用量太少或上下吹蒸汽用量失调,下吹蒸汽过量致使气化层严重下移;
-造气炉负荷过大,加负荷时蒸汽用量未及时跟上;
-雨雪天气原料煤含粉量高,未筛干净,影响气化床层的阻力不匀,局部过热;
-灰盘转速控制不当,造成气化层严重下移,炉下温度过高;
-上下吹百分比调节不当,下吹时间过长,造成炉下温度过高;
-炉篦结构设计不合理,气化剂分布不匀,炉下有局部过热现象。
首先找出结大块的原因,并加以消除,使炉内不要再结新块,一般处理方法是:
-加大上吹蒸汽用量,用蒸汽吹