最新管道检验Word文档下载推荐.docx
《最新管道检验Word文档下载推荐.docx》由会员分享,可在线阅读,更多相关《最新管道检验Word文档下载推荐.docx(10页珍藏版)》请在冰豆网上搜索。
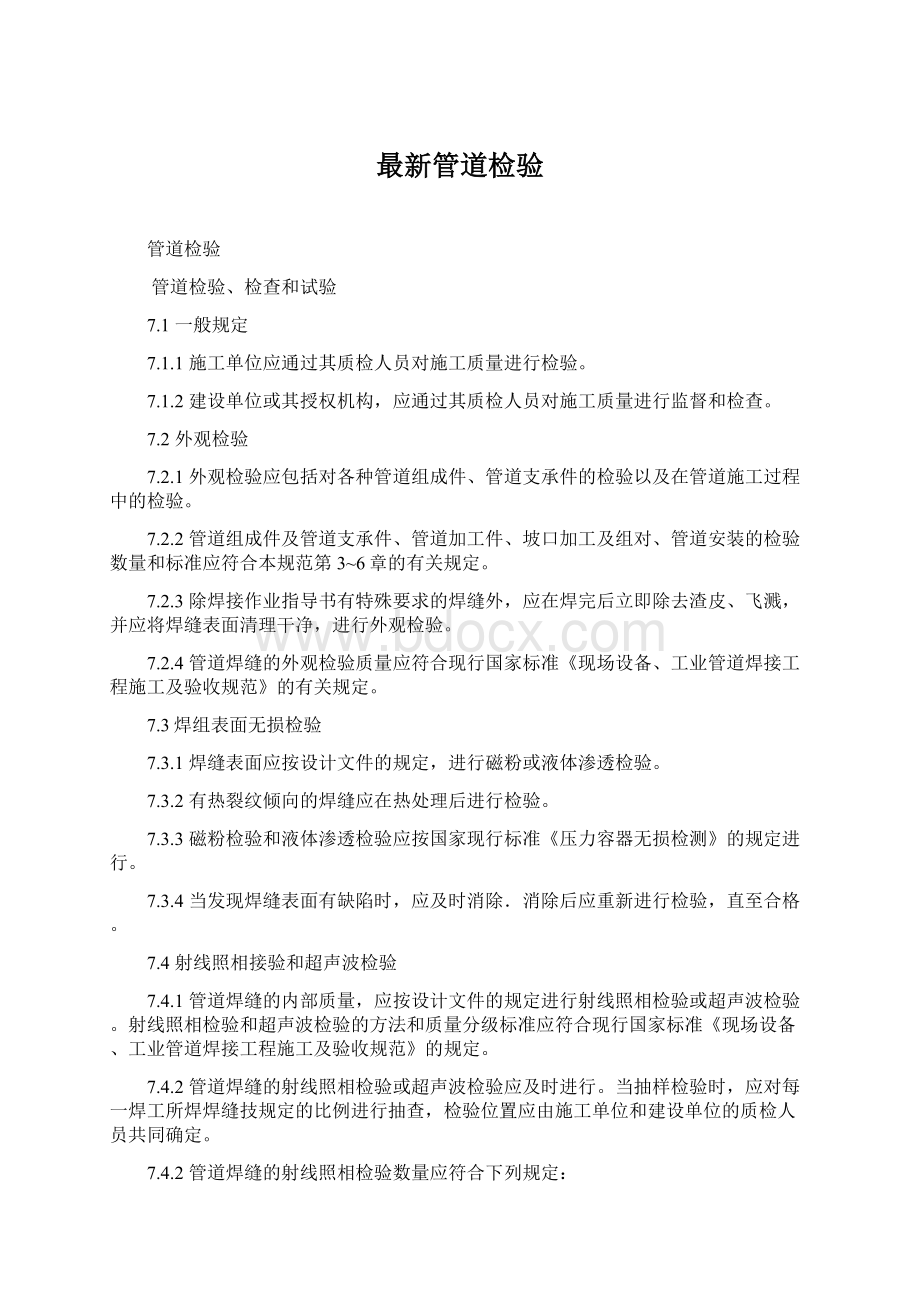
7.4.3.1下列管道焊缝应进行100%射线照相检验,其质量不得低于Ⅱ级:
(1)输送剧毒流体的管道;
(2)输送设计压力大于等于10MPa或设计压力大于等于4MPa且设计温度大于等于400℃的可燃流体、有毒流体的管道;
(3)输送设计压力大于等于10MPa且设计温度大于等于400℃的非可燃流体、无毒流体的管道;
(4)设计温度小于-29℃的低温管道。
(5)设计文件要求进行100%射线照相检验的其他管道。
7.4.3.2输送设计压力小于等于1MPa且设计温度小于400℃的非可燃流体管道、无毒流体管道的焊缝,可不进行射线照相检验。
7.4.3.3其他管道应进行抽样射线照相检验,抽检比例不得低于5%,其质量不得低于Ⅲ级。
抽检比例和质量等级应符合设计文件的要求。
7.4.4经建设单位同意,管道焊缝的检验可采用超声波检验代替射线照相检验,其检验数量应与射线照相检验相同。
7.4.5对不要求进行内部质量检验的焊缝,质检人员应按本章第7.2节的规定全部进行外观检验。
7.4.6当检验发现焊缝缺陷超出设计文件和本规范规定时,必须进行返修,焊缝返修后应按原规定方法进行检验。
7.4.7当抽样检验未发现需要返修的焊缝缺陷时,则该次抽样所代表的一批焊缝应认为全部合格;
当抽样检验发现需要返修的焊缝缺陷时,除返修该焊缝外,还应采用原规定方法按下列规定进一步检验:
7.4.7.1每出现一道不合格焊缝应再检验两道该焊工所焊的同一批焊缝。
7.4.7.2当这两道焊缝均合格时,应认为检验所代表的这一批焊缝合格。
7.4.7.3当这两道焊缝又出现不合格时,每道不合格焊缝应再检验两道该焊工的同一批焊缝。
7.4.7.4当再次检验的焊缝均合格时,可认为检验所代表的这一批焊缝合格。
7.4.7.5当再次检验又出现不合格时,应对该焊工所焊的同一批焊缝全部进行检验。
7.4.8对要求热处理的焊缝、热处理后应测量焊缝及热影响区的硬度值,其硬度值应符合设计文件规定。
当设计文件无明确规定时,碳素钢不宜大于母材硬度的120%;
合金钢不宜大于母材硬度的125%。
检验数量不应少于热处理焊口总数的10%。
7.4.9需要热处理的管道焊缝,应按本规范附录A第A.0.7条规定的格式填写“热处理报告”。
7.5压力试验
7.5.1管道安装完毕,热处理和无损检验合格后,应进行压试验。
压力试验应符合下列规定:
7.5.1.1压力试验应以液体为试验介质。
当管道的设计压力小于或等于0.6MPa时,也可采用气体为试验介质,但应采取有效的安全措施。
脆性材料严禁使用气体进行压力试验。
7.5.1.2当现场条件不允许使用液体或气体进行压力试验时,经建设单位同意,可同时采用下列方法代替:
(1)所有焊缝(包括附着件上的焊缝),用液体渗透法或磁粉法进行检验。
(2)对接焊缝用100%射线照相进行检验,
7.5.1.3当进行压力试验时,应划定禁区,无关人员不得进入。
7.5.1.4压力试验完毕,不得在管道上进行修补。
7.5.1.5建设单位应参加压力试验。
压力试验合格后,应和施工单位一同按本规范附录A第A.0.8条规定的格式填写“管道系统压力试验记录”。
7.5.2压力试验前应具备下列条件:
7.5.2.1试验范围内的管道安装工程除涂漆、绝热外,已按设计图纸全部完成,安装质量符合有关规定。
7.5.2.2焊缝及其他待检部位尚未涂漆和绝热。
7.5.2.3管道上的膨胀节已设置了临时约束装置。
7.5.2.4试验用压力表已经校验,并在周检期内,其精度不得低于1.5级,表的满刻度值应为被测最大压力的1.5~2倍,压力表不得少于两块。
7.5.2.5符合压力试验要求的液体或气体已经备齐。
7.5.2.6按试验的要求,管道已经加固。
7.5.2.7对输送剧毒流体的管道及设计压力大于等于10MPa的管道,在压力试验前,下列资料已经建设单位复查:
(1)管道组成件的质量证明书。
(2)管道组成件的检验或试验记录。
(3)管子加工记录。
(4)焊接检验及热处理记录。
(5)设计修改及材料代用文件。
7.5.2.8待试管道与无关系统已用盲板或采取其他措施隔开。
7.5.2.9待试管道上的安全阀、爆破板及仪表元件等已经拆下或加以隔离。
7.5.2.10试验方案已经过批准,并已进行了技术交底。
7.5.3液压试验应遵守下列规定:
7.5.3.1液压试验应使用洁净水,当对奥氏体不锈钢管道或对连有奥氏体不锈钢管道或设备的管道进行试验时,水中氯离子含量不得超过25×
10 ̄6(25ppm)。
当采用可燃液体介质进行试验时,其闪点不得低于50℃。
7.5.3.2试验前,注液体时应排尽空气。
7.5.3.3试验时,环境温度不宜低于5℃,当环境温度低于5℃时,应采取防冻措施。
7.5.3.4试验时,应测量试验温度,严禁材料试验温度接近脆性转变温度。
7.5.3.5承受内压的地上钢管道及有色金属管道试验压力应为设计压力的1.5倍,埋地钢管道的试验压力应为设计压力的1.5倍,且不得低于0.4MPa。
7.5.3.6当管道与设备作为一个系统进行试验,管道的试验压力等于或小于设备的试验压力时,应按管道的试验压力进行试验;
当管道试验压力大于设备的试验压力,且设备的试验压力不低于管道设计压力的1.15倍时,经建设单位同意,可按设备的试验压力进行试验。
7.5.3.7当管道的设计温度高于试验温度时,试验夺力应按下式计算:
Ps=1.5P[σ]1/[σ]2(7.5.3)
式中Ps——试验压力(表压)(Mpa);
P——设计压力(表压)(MPa);
[σ]1——试验温度下,管材的许用应力(MPa);
[σ]2——设计温度下,管材的许用应力(MPa)。
当[σ]1/[σ]2大于6.5时,取6.5。
当Ps在试验温度下,产生超过屈服强度的应力时,应将试验压力Ps降至不超过屈服强度时的最大压力。
7.5.3.8承受内压的埋地铸铁管道的试验压力,当设计压力小于或等于0.5MPa时,应为设计压力的2倍;
当设计压力大于0.5MFa时,应为设计压力加0.5MPa。
7.5.3.9对位差较大的管道,应将试验介质的静压计入试验压力中。
液体管道的试验压力应以最高点的压力为准,但最低点的压力不得超过管道组成件的承受力。
7.5.3.10对承受外压的管道,其试验压力应为设计内、外压力之差的1.5倍,且不得低于0.2MPa。
7.5.3.11夹套管内管的试验压力应按内部或外部设计压力的高者确定。
夹套管外管的试验压力应按第7.5.3.5款的规定进行。
7.5.3.12液压试验应缓慢升压,待达到试验压力后,稳压10min,再将试验压力降至设计压力,停压30min,以压力不降、无渗漏为合格。
7.5.3.13试验结束后,应及时拆除盲板、膨胀节限位设施,排尽积液。
排液时应防止形成负压,并不得随地排放。
7.5.3.14当试验过程中发现泄漏时,不得带压处理。
消除缺陷后,应重新进行试验。
7.5.4气压试验应遵守下列规定:
7.5.4.1承受内压钢管及有色金属管的试验压力应为设计压力的1.15倍,真空管道的试验压力应为0.2MPa,当管道的设计压力大于0.6MPa时,必须有设计文件规定或经建设单位同意,方可用气体进行压力试验。
7.5.4.2严禁使试验温度接近金属的脆性转变温度。
7.5.4.3试验前,必须用空气进行预试验,试验压力宜为0.2MPa。
7.5.4.4试验时,应逐步缓慢增加压力,当压力升至试验压力的50%时,如未发现异状或泄漏,继续按试验压力的10%逐级升压,每级稳压3min,直至试验压力。
稳压10min,再将压力降至设计压力,停压时间应根据查漏工作需要而定。
以发泡剂检验不泄漏为合格。
7.5.5输送剧毒流体、有毒流体、可燃流体的管道必须进行泄漏性试验。
泄漏性试验应按下列规定进行:
7.5.5.1泄漏性试验应在压力试验合格后进行.试验介质宜采用空气。
7.5.5.2泄漏性试验压力应为设计压力。
7.5.5.3泄漏性试验可结合试车工作,一并进行。
7.5.5.4泄漏性试验应重点检验阀门填料函、法兰或螺纹连接处、放空阀、排气阀、排水阀等。
7.5.5.5经气压试验合格,且在试验后未经拆卸过的管道可不进行泄漏性试验。
7.5.6真空系统在压力试验合格后、还应按设计文件规定进行24h的真空度试验,增压率不应大于5%。
7.5.7当设计文件规定以卤素、氦气、氨气或其他方法进行泄漏性试验时,应按相应的技术规定进行。
8管道的吹扫与清洗
8.1一般规定
8.1.1管道在压力试验合格后,建设单位应负责组织吹扫或清洗(简称吹洗)工作,并应在吹洗前编制吹洗方案。
8.1.2吹洗方法应根据对管道的使用要求、工作介质及管道内表面的脏污程度确定。
公称直径大于或等于600mm的液体或气体管道,宜采用人工清理,公称直径小于600mm的液体管道宜采用水冲洗;
公称直径小于600mm的气体管道宜采用空气吹扫;
蒸汽管道应以蒸汽吹扫;
非热力管道不得用蒸汽吹扫。
对有特殊要求的管道,应按设计文件规定采用相应的吹洗方法。
8.1.3不允许吹洗的设备及管道应与吹洗系统隔离。
8.1.4管道吹洗前,不应安装孔板、法兰连接的调节阀、重要阀门、节流阀、安全阀、仪表等,对于焊接的上述阀门和仪表,应采取流经旁路或卸掉阀头及阀座加保护套等保护措施。
8.1.5吹洗的顺序应按主管、支管、疏排管依次进行,吹洗出的脏物,不得进入已合格的管道。
8.1.6吹洗前应检验管道支、吊架的牢固程度,必要时应予以加固。
8.1.7清洗排放的脏液不得污染环境,严禁随地排放。
8.1.8吹扫时应设置禁区。
8.1.9蒸汽吹扫时,管道上及其附近不得放置易燃物。
8.1.10管道吹洗合格并复位后,不得再进行影响管内清洁的其他作业。
8.1.11管道复位时,应由施工单位会同建设单位共同检查,并应按本规范附录A第A.0.9条及第A.0.4条规定的格式填写“管道系统吹扫及清洗记录”及“隐蔽工程(封闭)记录”。
8.2水冲洗
8.2.1冲洗管道应使用洁净水,冲洗奥氏体不锈钢管道时,水中氯离子含量不得超过25×
10-6(25PPm)。
8.2.2冲洗时,宜采用最大流量,流速不得低于1.5m/S。
8.2.3排放水应引入可靠的排水井或沟中,排放管的截面积不得小于被冲洗管截面积的60%。
排水时,不得形成负压。
8.2.4管道的排水支管应全部冲洗。
8.2.5水冲洗应连续进行,以排出口的水色和透明度与入口水目测一致为合格。
8.2.6当管道经水冲洗合格后暂不运行时,应将水排净,并应及时吹干。
8.3空气吹扫
8.3.1空气吹扫应利用生产装置的大型压缩机,也可利用装置中的大型容器蓄气,进行间断性的吹扫。
吹扫压力不得超过容器和管道的设计压力,流速不宜小于20m/S。
8.3.2吹扫忌油管道时,气体中不得含油。
8.3.3空气吹扫过程中,当目测排气无烟尘时,应在排气口设置贴白布或涂白漆的木制靶板检验,5min内靶板上无铁锈、尘土、水分及其他杂物,应为合格。
8.4蒸汽吹扫
8.4.1为蒸汽吹扫安设的临时管道应按蒸汽管道的技术要求安装,安装质量应符合本规范的规定。
8.4.2蒸汽管道应以大流量蒸汽进行吹扫,流速不应低于30m/s。
8.4.3蒸汽吹扫前,应先行暖管、及时排水,并应检查管道热位移。
8.4.4蒸汽吹扫应按加热—冷却—再加热的顺序,循环进行。
吹扫时宜采取每次吹扫一根,轮流吹扫的方法。
8.4.5通往汽轮机或设计文件有规定的蒸汽管道,经蒸汽吹扫后应检验靶片。
当设计文件无规定时,其质量应符合表8.4.5的规定。
吹扫质量标准表8.4.5
项目质量标准
靶片上痕迹大小田0.6mm以下
痕深<0.5mm
粒数1个/cm2
时间15min(两次皆合格)
注:
靶片宜采用厚度5mm,宽度不小于排汽管道内径的8%,长度略大于管道内径的铝板制成。
8.4.6除本规范第8.4.5条规定的蒸汽管道检验外,蒸汽管道还可用刨光木板检验,吹扫后,木板上无铁锈、脏物时,应为合格。
8.5化学清洗
8.5.1需要化学清洗的管道,其范围和质量要求应符合设计文件的规定。
8.5.2管道进行化学清洗时,必须与无关设备隔离。
8.5.3化学清洗液的配方必须经过鉴定,并曾在生产装置中使用过,经实践证明是有效和可靠的。
8.5.4化学清洗时,操作人员应着专用防护服装.并应根据不同清洗液对人体的危害佩带护目镜、防毒面具等防护用具。
8.5.5化学清洗合格的管道,当不能及时投入运行时,应进行封闭或充氮保护。
8.5.6化学清洗后的废液处理和排放应符合环境保护的规定*
8.6油清洗
8.6.1润滑、密封及控制油管道,应在机械及管道酸洗合格后、系统试运转前进行油清洗。
不锈钢管道,宜用蒸汽吹净后进行油清洗。
8.6.2油清洗应以油循环的方式进行,循环过程中每8h应在40-70℃的范围内反复升降油温2~3次,并应及时清洗或更换滤芯。
8.6.3当设计文件或制造厂无要求时,管道油清洗后应采用滤网检验,合格标准应符合表8.6.3的规定。
油清洗合格标准表8.6.3
机械转速(r/min)滤网规格(目)合格标准
≥6000200目测滤网,无硬颗粒及粘稠物,每平方厘米范围内,软杂物不多于3个
<6000100
8.6.4油清洗应采用适合于被清洗机械的合格油,清洗合格的管道,应采取有效的保护措施。
试运转前应采用具有合格证的工作用油。
9管道涂漆
9.0.1管道及其绝热保护层的涂漆应符合本章和国家现行标准《工业设备、管道防腐蚀工程施工及验收规范》的规定。
9.0.2涂料应有制造厂的质量证明书。
9.0.3有色金属管、不锈钢管、镀锌钢管、镀锌铁皮和铝皮保护层,不宜涂漆。
9.0.4焊缝及其标记在压力试验前不应涂漆。
9.0.5管道安装后不易涂漆的部位应预先涂漆。
9.0.6涂漆前应清除被涂表面的铁锈、焊渣、毛刺、油、水等污物。
9.0.7涂料的种类、颜色,涂敷的层数和标记应符合设计文件的规定。
9.0.8涂漆施工宜在l5—30℃的环境温度下进行,并应有相应的防火、防冻、防雨措施。
9.0.9涂层质量应符合下列要求:
9.0.9.1涂层应均匀,颜色应一致。
9.0.9.2漆膜应附着牢固,无剥落、皱纹、气泡、针孔等缺陷。
9.0.9.3涂层应完整,无损坏、流淌。
9.0.9.4涂层厚度应符合设计文件的规定。
9.0.9.5涂刷色环时,应间距均匀,宽度一致。
10管道绝热
10.0.1管道绝热工程的施工及质量要求应符合本章和现行国家标准《工业设备及管道绝热工程施工及验收规范》的规定。
10.0.2管道绝热工程的施工应在管道涂漆合格后进行。
施工前,管道外表面应保持清洁干燥。
冬、雨季施工应有防冻、防雨雪措施。
10.0.3管道绝热工程材料应有制造厂的质量证明书或分析检验报告,种类、规格、性能应符合设计文件的规定。
10.0.4管道绝热层施工,除伴热管道外,应单根进行。
10.0.5需要蒸汽吹扫的管道,宜在吹扫后进行绝热工程施工。
11工程交接验收
11.0.1当施工单位按合同规定的范围完成全部工程项目后,应及时与建设单位办理交接手续。
11.0.2工程交接验收前、建设单位应对工业金属管道工程进行检查,确认下列内容:
11.0.2.1施工范围和内容符合合同规定。
11.0.2.2工程质量符合设计文件及本规范的规定。
11.0.3工程交接验收前,施工单位应向建设单位提交下列技术文件:
11.0.3.1管道组成件及管道支承件的质量证明书或复验、补验报告。
11.0.3.2施工记录和试验报告:
(1)阀门试验记录。
(2)高压管件加工记录。
(3)隐蔽工程(封闭)记录。
(4)安全阀最终调试记录。
(5)管道补偿装置安装记录。
(6)热处理报告。
(7)管道系统压力试验记录。
(8)管道系统吹扫及清洗记录。
(9)射线照相检验报告。
(10)超声波检验报告。
(11)磁粉检验报告。
(12)渗透检验报告。
(13)其他检验报告。
11.0.3.3设计修改文件及材料代用报告。
11.0.3.4要求100%射线照相检验的管道,应在单线图上准确标明焊缝位置、焊缝编号、焊工代号、无损检验方法、焊缝补焊位置、热处理焊口编号。
对抽样射线照相检验的管道,其焊缝位置、焊缝编号、焊工代号、无损检验方法、焊缝补焊位置、热处理焊口编号等应有可追溯性记录。
11.0.4工程交接验收时确因客观条件限制未能全部完成的工程,在不影响安全试车的条件下,经建设单位同意,可办理工程交接验收手续、但遗留工程必须限期完成。
11.0.5工程交接验收应按本规范附录A第A.0.14条规定的格式填写“工程交接检验书”。