利用落孔式连接梁降低装后高度的设想与实现Word下载.docx
《利用落孔式连接梁降低装后高度的设想与实现Word下载.docx》由会员分享,可在线阅读,更多相关《利用落孔式连接梁降低装后高度的设想与实现Word下载.docx(10页珍藏版)》请在冰豆网上搜索。
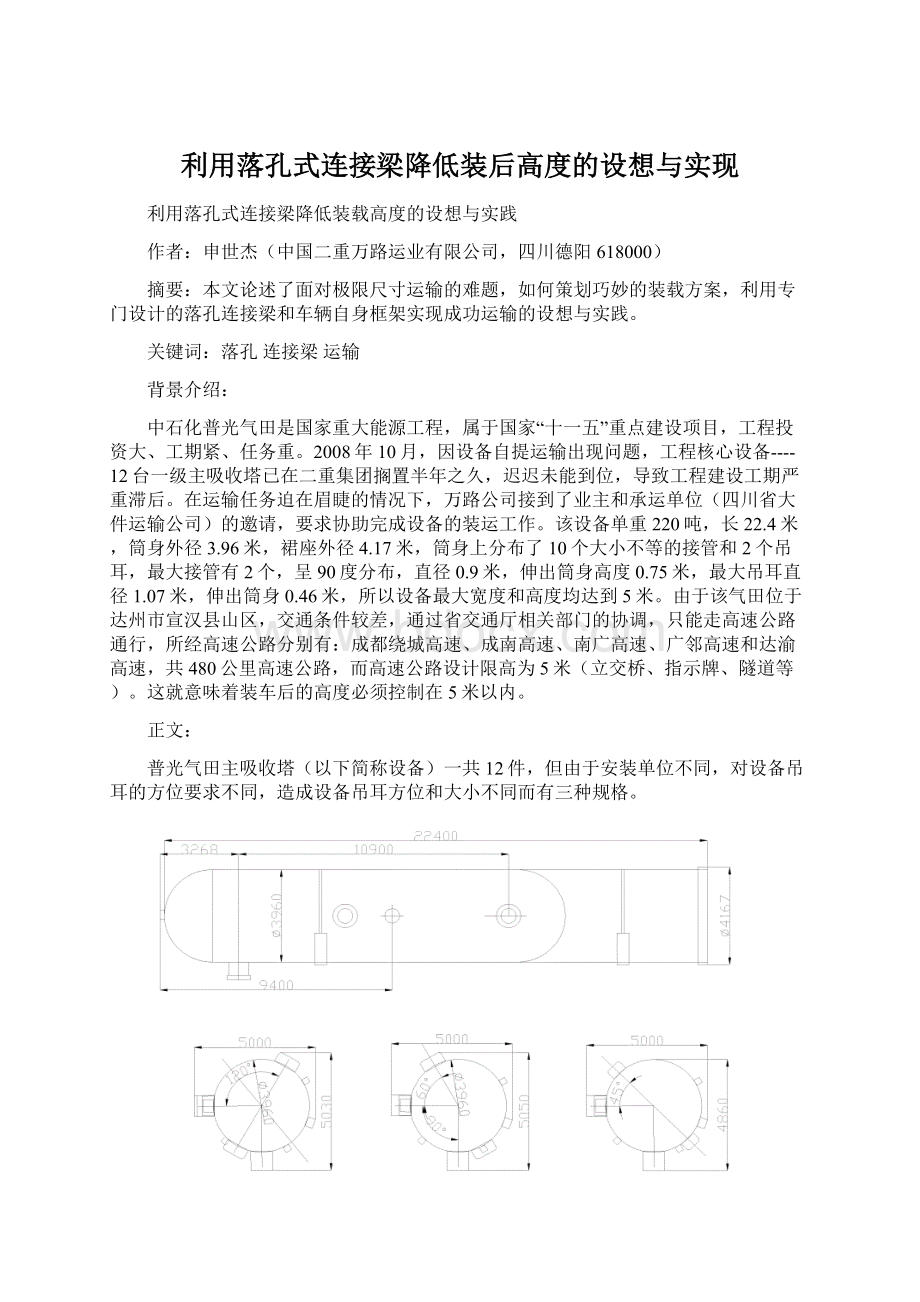
该设备单重220吨,长22.4米,筒身外径3.96米,裙座外径4.17米,筒身上分布了10个大小不等的接管和2个吊耳,最大接管有2个,呈90度分布,直径0.9米,伸出筒身高度0.75米,最大吊耳直径1.07米,伸出筒身0.46米,所以设备最大宽度和高度均达到5米。
由于该气田位于达州市宣汉县山区,交通条件较差,通过省交通厅相关部门的协调,只能走高速公路通行,所经高速公路分别有:
成都绕城高速、成南高速、南广高速、广邻高速和达渝高速,共480公里高速公路,而高速公路设计限高为5米(立交桥、指示牌、隧道等)。
这就意味着装车后的高度必须控制在5米以内。
正文:
普光气田主吸收塔(以下简称设备)一共12件,但由于安装单位不同,对设备吊耳的方位要求不同,造成设备吊耳方位和大小不同而有三种规格。
图1:
设备规格示意图(注:
主视图相同,因三种吊耳规格有三种端视图)
从以上图形可以看出,设备最大端面尺寸全都接近甚至超过5米,液压平板车的正常运行高度为1070±
210mm,要完成装车高度控制在5米以内的任务其难度可想而知。
装车方案策划:
经过仔细分析以后,我们选择了可升降的水工窄系列液压平板车作为承载平台,该车承载高度最低可降至830mm,这是当时我们所能利用的条件最好的车辆。
理论上,倘若能通过旋转设备避开接管,将筒身直接装载于车板上,裙座最低高度为4.9米。
下一步,就是如何避开接管的问题了。
首先考虑的是两个最大的接管,直径900mm,伸出筒身750mm,一个在筒身前部,一个在筒身中部,两个接管呈90度分布。
这两个接管中任一个向上方都是不可能的,只有向下或向两侧摆放。
最理想的是两个接管左右对称向斜下方摆放,如图:
图2
很显然,这种摆放方式虽然避开了大接管,但小接管无法回避,设备高度达到4.45米,加上车板高0.83米,还是超过了5米。
这表明,仅就避开大接管的条件来考虑,常规网状框架结构的平板车难以满足装载要求,所以,我们决定采用组合式车辆为大接管留出空档,将大接管朝下以降低装车高度。
由于在端视图上,吊耳有三种不同的布置,所以在端视方向用一种方案不能满足全部设备三种规格的装车要求,需要分别加以考虑。
首先考虑图1中,最左侧的端视图,其吊耳与大接管的夹角为120度,通过旋转端视图,找到该视图高度最低的2种摆放角度。
如图3所示
图3
其中,图3左图需要设计“日”字形连接梁,右图需要设计“Ⅱ”字形连接梁。
连接梁俯视示意图如图4:
图中椭圆示意大接管的位置
图4
其次,考虑图1中间的端视图,其吊耳位置与大接管夹角为60度,通过旋转视图,找到该视图高度最低的摆放角度。
如图7所示:
图5
此种规格的设备所需的连接梁为“Ⅱ”字形连接梁,如图6所示,图中椭圆示意大接管的位置。
图6
最后考虑图1中,最右侧的端视图,其吊耳与大接管的夹角为45度,通过旋转端视图,找到该视图高度最低的摆放角度。
如图7所示
图7
此种规格的设备所需的连接梁为“Ⅱ”字形连接梁,如图8所示,图中圆圈示意大接管的位置。
图8
为了降低成本和方便操作,我们考虑三种规格的设备都使用“Ⅱ”字形连接梁的方案,因为这种连接梁通过优化设计有可能实现通用,即设计一种连接梁,适用于三种设备的不同装载方式。
为了验证这个设想的可行性,我们考虑了两种装车方案:
1、全挂车的装车方案
图9
2、鹅颈车的装车方案
图10
从两种方案的比较来看,全挂车的车辆长度较长(比鹅颈车的长6米),相比之下,鹅颈车转弯性能较好;
而且鹅颈车将裙座吊在车板之外,相比全挂车方案,裙座离地高度降低了0.1米。
再加之,虽然两种方案的车辆都是接近满载,但是鹅颈车的牵引车不需要额外的配重,比较而言,鹅颈车的车货总重比全挂车的小30吨左右,对于减少沿途桥梁负荷更为有利。
全挂车的优势是可以双向牵引,在坡度较大的路段便于采用前拉后顶的方式牵引。
综合比较后,认定鹅颈车方案的优势明显,所以最后选择了鹅颈车的装车方案。
方案实现:
1、连接梁的设计
首先是“Ⅱ”字形连接梁横截面范围的确定,这关系到能否同时适用于三种设备的装车需要。
由图4、图6、图8可以看出,三种规格的设备对连接梁的要求各不相同,对应大接管在连接梁空档的位置也各不相同,分别在连接梁左、中、右。
通过对这三种大接管位置组合到一张图上,可以确定连接梁的横截面尺寸范围。
如图11中虚线框所示:
图11
很显然,虽然这个横截面范围左右不对称,大小也不同,但范围是足够大了。
留给设计的余地也是比较大了,只需再从制造工艺和多功能要求等方面加以调整,完全能够得到满意的连接梁截面。
其次是连接梁长度的选择。
连接梁长度的选择牵涉到三个方面的因素:
一是要能将大接管容下,大接管的直径是0.9米,考虑装车余量,空档长度大于1.2米就够了。
二是要考虑鹅颈车的整体载荷分布,由于整车负荷接近满载,连接梁长了,鹅颈负载不足,后面挂车超载,而且还会造成牵引车附着力不足的问题;
连接梁短了,鹅颈负荷过重,鹅颈容易受损,牵引车也承受不了。
通过建立数学模型进行验算,我们得到在鹅颈整车负载均衡的条件下,最佳连接梁长度值为4.4米,此时鹅颈车前后液压缸负载相同。
三是要考虑鹅颈车的转向问题,该车型轴距1.55米,从3~30轴线,在每种轴线数的状态下,都对应有最佳的横直拉杆调整位置,如果车辆长度不是1.55米的倍数,很难在转向拉杆的配置上与之适应,容易产成转向失控和轮胎异常磨损等问题。
所以综合以上三点考虑,最终我们选择了4.65米(即轴距1.55米的三倍)作为连接梁的长度。
最后是连接梁承载面高度的选择。
单纯就这三种设备的运输来讲,连接梁承载面的高度可以与后面的车板高度相同,我们考虑到便于增设辅助支点和便于以后其它类型的超高设备运输,在保证该连接梁与车板等强度的条件下,尽量将承载面降低,最后,通过计算,确定了承载面高度比车板低0.2米。
最终结构图如下:
图12
大接管的问题解决了,下面是小接管的问题。
从图5、图7中可以看出,虽然避开了大接管,但是小接管还是与车板发生了干涉。
图13
如图13,通过仔细分析车板结构可以看出,车板上有3根纵梁,与每一轴线的横梁组成了网状框架结构,设备的现实条件迫使我们考虑:
能否将小接管摆放到车板框架结构的空档之中?
特别是图5所示的设备上,沿纵线有两个相同尺寸的小接管,车板空档的距离能否正好满足将这两个接管都摆放进去的条件?
这些都是方案顺利实施的前提条件。
经过测算,小接管都可以摆放到车板框架结构的空档中。
如图14所示:
图14
但是,车板降到最低时,小接管与轮胎可能发生干涉,通过调整小接管在框架中的位置,只有1个小接管的设备可以避开轮胎,有2个小接管的设备只能避开1个,不能避开的最后采取了卸掉轮胎的办法。
如图15所示:
图15
2、装车操作
由于装车方案考虑的因素较多,而且很多因素都达到了理论极限,如车板最低高度,设备最佳角度等,给装车操作带来不少困难,要求装车操作更加精确才能实现设计目标。
第一关是旋转角度。
由于方案设计时考虑的是最佳角度,所以装车时必须达到理论上的最佳角度,否则,稍有偏差,不是装不上车,就是高度超标。
我们采取了多重参照的方式来确定设备的角度,在设备裙座的端面上,均匀分布着24个螺栓孔,这是一个比较精细的参照;
另外,根据设备的最佳理论角度,我们测算了大接管的离地高度,然后通过在滚轮架上测量大接管的离地高度来控制旋转角度。
两个参照互相印证,确保设备旋转至最佳角度。
第二关是起吊。
虽然在滚轮架上,把旋转角度控制好了,但在以往的装车过程中,时常发生起吊时设备发生微小转动的情况,这时由于起吊钢丝绳在吊挂时不可能做到长度、角度等绝对均衡,钢丝绳在起吊收紧时力量不均造成设备的不确定性转动。
在装车精度要求不高的情况下,这种微小的转动可以忽略,但在本次装车时必须考虑,在起吊前,提前与起重工沟通好,明确控制要求;
起吊时,要求起重工对钢丝绳的吊挂长度、角度精细调整,钢丝绳拉紧并提升后(设备刚刚离开滚轮架),再次对设备角度进行确认,发现偏差,则落回滚轮架,重新旋转调整,再次起吊,确保起吊后的角度仍在最佳位置。
第三关是落钩。
落钩是实现装载方案的关键环节,特别是有2个小接管落在车辆空档中的设备,前部有大接管必须落在落孔式连接梁里,中部和后部有小接管必须落在车辆空档中,落钩时前后左右的位置都必须非常精确。
我们采取了多人多点监控的办法,配合起重工共同完成落钩动作。
为了保证车板受力均衡,我们在连接梁部位增加了一个辅助支点(如图4所示),辅助支点采用钢梁和楔形木结合的方式,落钩时,在设备刚刚与液压车板上的刚性支座接触时,就将楔形木与设备靠紧,再继续落钩,待设备全部重量落在车板上后,楔形木与设备的接触已经非常紧密了。
这样,既保证了辅助支点的可靠受力,又不致让辅助支点受力过大,确保了车板受力的均衡。
3、装载效果
装载后,检查液压表读数,左支点:
14Mpa,右支点:
15Mpa,前支点(鹅颈):
18Mpa。
对应鹅颈承载:
35t,液压车板前支点每轴线载荷:
20t,液压车板后支点每轴线载荷:
23t。
可以说,整个车辆的承载达到了均衡合理的状态,既发挥了车辆的装载能力,又没有产生个别轴线超载偏载的问题。
对于重车过桥也起到了技术保障作用。
装后车辆最低高度控制在4.97米以内,成功实现了装后高度控制在5米以内的目标。
从2008年12月16日至2009年2月9日,普光气田的12台一级主吸收塔均采用该装车方案成功装载,顺利通过高速公路运输至达州。
结束语:
本方案的大胆设想与成功实施,为类似多接管容器设备的装载运输提供了成功的经验,本方案的创新点在于设计一种落孔式连接梁适应三种装载方式的要求,以及将设备多个接管同时落在连接梁框架和车辆结构的空档之中。
可以说是充分挖掘了车辆的潜力,最大限度地降低了装载高度,实现了看似不可能的装载运输。
2011年10月