碳化工段操作规程Word文件下载.docx
《碳化工段操作规程Word文件下载.docx》由会员分享,可在线阅读,更多相关《碳化工段操作规程Word文件下载.docx(19页珍藏版)》请在冰豆网上搜索。
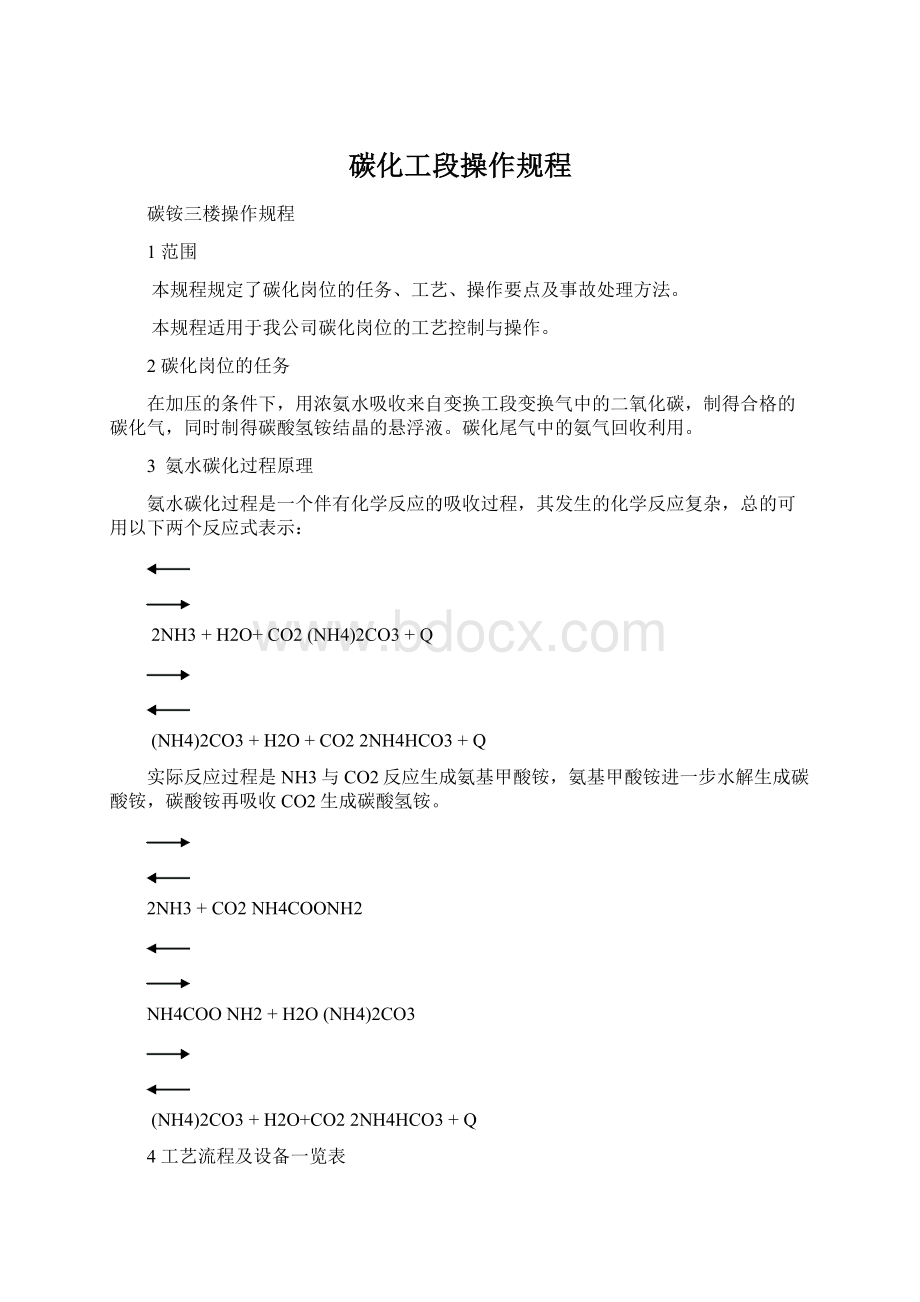
≤20.0g/m3。
5.1.3综合塔CO2%:
≤0.2%;
≤0.10g/m3。
5.2压力
5.2.1气体总入口压力:
≤0.84Mpa;
5.2.2副塔气体入口压力:
≤0.74Mpa;
5.2.3综合塔出口压力:
≤0.66Mpa。
5.3温度
5.3.1主塔:
底温38~45℃;
5.3.2副塔:
底温38-43℃;
5.3.3综合塔出口气体≤30℃;
5.3.4变换气入口温度≤35℃。
5.4液位
5.4.1开五、六机
主塔5灯,副塔4灯,综合塔回收段2灯、清洗段2灯;
5.4.2 全停车
主塔3灯,副塔2灯,综合塔回收段1灯、清洗段1灯。
6操作要点
6.1保证碳铵结晶粒度和碳化气净化质量。
6.1.1根据进主、副塔气体温度、流量及塔内温度情况,及时调节主、副塔温度,提高碳化度,增大结晶颗粒,降低主塔、副塔尾气中的氨与二氧化碳含量。
6.1.2根据生产负荷大小和各塔尾气成分,调节各塔液位。
在保证各塔尾气合格的情况下,尽量将液位控制在低限,以降低系统阻力。
6.1.3调节加液量,控制好塔内的浓氨水成分,在生产负荷小时,采取间歇取出,少取勤取,正常生产负荷下时要连续取出,以稳定操作和提高氨利用率。
6.1.4根据综合塔出口碳化气中CO2及硫化氢含量,及时调节加入的软水量。
6.2在保证碳化气中的氨含量不超指标的条件下,应尽量减少软水加入量,以保证系统的水平衡。
6.3减少系统氨损失
6.3.1在保证碳化气中CO2含量合格的条件下,适当地提高加入塔内浓氨水的CO2含量,以降低清洗塔出口气体的氨含量,以减少氨损失。
6.3.2控制好主塔底部温度,取出液温度不宜过高,以减少取出液中的氨损失。
6.3.3在保证碳化气净化质量的条件下,确定合理的取出量,以减少母液循环量,降低循环过程中的氨损失和动力消耗。
6.3.4及时检查并消除系统设备、管道中的物料跑、冒、滴、漏,以减少氨损失。
6.4调塔操作
调塔时必须保证碳化气成分合格,尽量减少气量、压力的波动;
同时调塔操作要迅速准确。
6.4.1调塔前的准备
6.4.1.1用蒸汽吹洗主、副塔的气体进口阀和出口阀,及有关串阀,使阀门及管道中的结晶溶解。
6.4.1.2适当调节冷却水,加大主塔取出量,减少向主塔加液。
6.4.1.3加高副塔液位,向综合回收段加浓氨水至符合调塔的高度。
6.4.1.4主塔接近取空时,停止取出,并用蒸汽吹通取出管道。
6.4.2变换气体阀门
6.4.2.1开一主一付一综合时
打开新主塔进气阀、关老主塔进气阀、关老主塔尾气串联阀;
开老主塔尾气阀、开老主塔尾气串联阀、关新主塔尾气阀。
6.4.2.2开两主一付一综合时
打开新主塔进气阀、关老主塔进气阀、关老主塔出口串联阀;
关新主塔联通阀、打开老主塔联通阀、开老主塔出口尾气阀、开新主塔出口串联阀、关新主塔出口尾气阀。
6.4.3调节正常。
6.5巡回检查
6.5.1根据操作记录表,按时检查及记录。
6.5.2经常检查回收清洗塔液位。
6.5.3每十五分钟检查一次系统各点压力和温度。
6.5.4每半小时检查一次冷却水箱和冷却水温度及出水中是否带氨。
6.5.5每1小时检查系统设备、管道等的泄漏情况。
7开停车操作
7.1开车
7.1.1接到开车通知后,向各塔加入部分氨水,然后关闭放空阀。
7.1.2待变换通知送气后,开主塔入口,开主塔出口串阀,去副塔底部,进入塔内。
开副塔出口阀,去综合塔底,开放空阀。
7.1.3待副塔CO2结果分析合格后(不超0.4%),开去回收塔入口阀,并通知压缩岗位。
7.1.4待主塔CO2结果达到工艺,通知一楼取出,并开浓氨泵、碳化泵,向主塔加液。
7.2停车
7.2.1短期停车
7.2.1.1系统保压状况下的停车。
a加大主塔取出量,并根据综合塔清洗段出口碳化气成分减少或停止向副塔加入浓氨水。
b与变换、压缩工段联系,切断气源,关闭主塔气体进口阀、主塔气体出口阀与副塔气体进口串联阀、副塔气体出口阀、清洗塔出口阀。
c停各泵,并关闭各塔冷却水阀(冬天注意防冻)。
d利用主塔塔内余压,继续取出,当取出液的固液比降至5%-10%时,停止取出,使系统处于保压状态。
7.2.1.2系统需检修的停车
按长期停车步骤进行。
7.2.2紧急停车
如遇全公司性停电或发生重大设备事故等紧急情况时,须紧急停车,步骤如下:
立即与变换、压缩工段联系,切断气源,迅速关闭主塔气体进口阀和清洗段气体出口阀,然后按短期停车方法处理。
7.2.3长期停车
7.2.3.1按短期停车步骤,加大主塔取出量,塔内结晶悬浮液取完后,切断气源,停各泵。
7.2.3.2利用塔内余压将主、副塔内的液体全部压入母液贮槽,清洗回收段的液体全部压入稀氨水贮槽。
液体压完后,开启清洗塔放空,系统卸压,并排净清洗塔内的液体。
7.2.3.3向主塔、副塔内加软水至2~3米高,开启主塔与副塔底部液体联通阀。
主、副塔内的软水用碳化泵同时打循环1小时左右,洗净塔内残余氨气,同时清理塔内结疤。
然后将塔内的溶液回收稀氨水槽。
7.2.3.4系统从主塔至清洗塔气体出口管止,用清水进行置换。
按流程依次向主塔、副塔、综合塔塔及系统管道加水,直至清洗塔放空管有水溢出为止。
然后拆开各塔底部液体出口阀后法兰,将水排净,如此重复2~3次。
取样分析,氧气含量大于20%,气体中无氨味为合格。
7.2.3.5浓氨水泵、碳化泵进出口管线用水清洗合格。
7.3原始开车
7.3.1开车前的准备
对照图纸,检查和验收系统内所有设备、管道、阀门、分析取样点及电器、仪表等,必须正常完好。
7.3.2单体试车
碳化泵、浓氨水泵、软水泵单体试车合格。
7.3.3系统吹净和清洗
7.3.3.1吹净前的准备
按气、液流程,依次拆开各设备和主要阀门的有关法兰,并插入档板。
开启设备的放空阀、排污阀及倒淋阀,拆除分析取样阀、压力表阀及液位计的气、液相阀。
人工清理碳化塔后,装好冷却水箱及封头。
7.3.3.2吹净操作
用0.2~0.3MPa的压缩空气,按气体流程逐台设备、逐段管道吹净(不得跨设备、管道、阀门及工段、岗位之间的联接管道)。
放空、排污、分析取样及仪表管线同时进行吹净,吹净时用木锤轻击外壁,调节流量,时大时小,反复多次直至吹出气体清净为合格。
吹净过程中,每吹完一部分后,随即抽掉有关挡板,装好有关法兰。
7.3.3.3系统清洗
1)塔系统
分别由塔顶向碳化塔、副塔、综合塔加入清水进行清洗,直至各塔底部出水清净为止。
2)泵进、出口管线
拆开碳化泵、浓氨水泵、清水泵进口阀前法兰和泵出口管道与有关设备的连接法兰。
先将各泵进口总管、支管用清水冲洗干净。
然后装好有关法兰。
7.3.4系统试漏和气密试验
7.3.4.1试漏
关闭主塔气体进口阀和综合塔放空阀。
按流程依次向主塔、副塔、综合塔加清水,待水分出口有水溢出时关闭水分出口阀,让系统充压,并将系统压力控制在0.6MPa。
检查各泄漏点,发现泄漏卸压处理,直至无漏为合格,然后将水从各塔底部液体出口阀法兰拆开处排净。
7.3.4.2空气气密试验
a按流程顺序串联好气体阀门,关闭各放空阀、液体出口阀、倒淋阀及分析取样阀,在综合塔气体出口处装好盲板。
b送空气升压至0.6MPa。
c对设备(包括冷却水箱)、管道、阀门、法兰、分析取样点和仪表接口处及所有焊缝,涂肥皂水进行查漏,发现泄漏,做好标记,卸压处理,直至无泄漏,保压30分钟,压力不下降为合格。
开启水分离器倒淋阀卸压,拆除水分气体出口盲板。
7.3.5系统变换气置换
关闭主塔气体进口阀和综合塔清洗段气体出口阀,按流程依次向各塔加水,待综合塔出口有水溢出时,停止加水,关清洗段放空阀。
然后与变换工段联系送变换气,用变换气依次将各塔内的水依次从各塔底压出。
置换时要按流程逐塔进行,使变换气通过所有设备和管道,将系统内的水排净。
气体由水分倒淋管放空,取样分析,氧气含量不大于进系统变换气中的氧含量为合格。
置换过程中要注意进气和排水速度,以防系统成负压而进入空气。
置换结束后,可转入正常开车。
8不正常现象及处理
发生现象
常见原因
处理方法
取出液中结晶颗粒细小
1.取出量太大
2.主塔底部温度过高或塔温波动太大
3.加入系统浓氨水中的氨浓度低
1.减取出量
2.调节好冷却水量,降低塔底部温度或减少塔温波动
3.与吸氨岗位联系适当提高浓氨水中的氨浓度
碳化气中氨含量高
1.副塔液位过高
2.回收塔水量小,氨浓度高
3.主、副塔塔温高
1.适当降低副塔液位
2.加大回收塔水量,降低稀氨水氨含量
3.加大冷却水量,降低塔温
碳化气中二氧化碳含量高
1.主、副塔有关气体阀门结晶堵塞或阀蕊脱落,关不严,气体走短路
2.加入系统浓氨水中的氨浓度低或碳化度高
3.主塔、副塔、综合塔液位低
4.主、副塔塔温高
1.用蒸汽吹洗后,关紧有关阀门或停车检修阀门
2.与吸氨岗位联系,适当提高浓氨水中氨浓度或降低碳化度
3.适当加大有关塔的加液量,提高液位
4.加大冷却水量,降低塔温
碳化气中硫化氢含量高
1.脱硫效率低,脱硫后半水煤气硫化氢偏高
2.配制浓氨水所用的母液中硫化氢含量高
1.与脱硫工段联系,提高脱硫效率,降低半水煤气硫化氢含量
2.适量更换母液
碳化气
带水
1.清洗段液位过高
2.清洗段结垢严重
3.清洗段系统添加剂含量低,系统起泡带液
1.适当降低清洗塔液位
2.停车清理清洗塔
3.把添加剂调到工艺指标范围内
6
系统压
差大
1.气体管道、阀门有结晶
3.主塔内结疤严重
4.各塔液位过高
1.用蒸汽吹洗管道、阀门
2.停车处理清洗塔
3.用蒸汽吹洗或调塔清洁
4.适当降低各塔液位
7
浓氨水泵不打液
1.进口管有结晶或杂物堵塞
2.浓氨水贮槽液位低
3.泵内有气
4.电机反转或故障
5.叶轮脱落或损坏
6.泵回路阀内漏
1.倒泵,用蒸汽吹洗或疏通进口管
2.与吸收岗位联系,提高氨水贮槽液位
3.关闭泵出口阀排气
4.倒泵,与电工联系处理
5.倒泵,检修叶轮
6.倒泵,检修回路阀
离心机岗位操作规程
本规程规定了离心机岗位的任务、工艺、操作要点及事故处理方法。
本规程适用于我公司离心机岗位的工艺控制及操作。
2离心机岗位的任务
在离心力的作用下,从来自碳化岗位的碳铵结晶县浮液中分离出合格的碳酸氢铵成品。
3工艺流程及设备一览表
3.1流程简述
来自碳化岗位的碳铵结晶悬浮液,从稠厚器底部进入离心机布料斗,在离心力的作用下,结晶浮在筛网上,推料推出结晶为干成品;
分离出的母液同稠厚器顶部溢流出的母液一起流入晶液分离器,静止沉降分层,清母液流至母液槽,细结晶液由泵送入稠厚器二次分离。
3.2设备一览表
名称
离心机
WH-800推料次数每分钟42次
通风机
EFB-72NO6C7.5KW
4工艺指标
4.1碳铵含水量:
≤3.5%。
4.2碳铵含氮量:
≥17.1%。
4.3油工作压力:
≤4.0MPa。
4.4油箱油位不低于油标尺1/2处。
4.5主电机温度:
≤65℃。
4.6主电机电流:
≤35A。
4.7油泵电机电流:
≤24A。
5操作要点
5.1提高分离效果,降低碳铵含水量。
5.1.1加入离心机的悬浮液应保持均匀,并根据固液比高低和结晶颗粒大小,及时调节离心机加料量,保证碳铵含水量不超指标。
5.1.2每次分离结束,应对离心机及其进出口管道、阀门进行清洗,以保证下次分离效果。
5.2注意安全运行
经常注意离心机的振动和响声、电机电流及温升、油箱油位及各润滑点润滑等情况。
5.3巡回检查
5.3.1根据操作记录表,按时检查及记录。
5.3.2每小时检查一次晶液泵运转情况。
5.3.3经常观察离心机转动部件的运转及润滑情况,油压系统的工作情况。
6开停车操作
6.1正常开车
6.1.1开车前的准备
6.1.1.1检查各设备、管道、阀门和电器、仪表及离心机油箱的油位、油质等,必须正常完好。
6.1.1.2检查系统所有阀门的开关位置,应符合开车要求。
6.1.1.3与供水、供电、供汽部门及碳化、吸收、包装岗位联系,作好开车准备。
6.1.1.4开车
开启水箱冷却器冷却水阀,并调节好冷却水量。
检查筛篮内外有无杂物,松开刹车带,用手盘动筛篮应转动灵活,无磨擦现象。
启动油泵,待油压系统运行正常后,启动主机,空负荷运转。
待离心机空负荷运转正常后,开启加料阀均匀加入悬浮液进行分离。
6.2停车
6.2.1短期停车
6.2.1.1系统不需检修的停车
1)悬浮液分离完毕,关闭离心机加料阀,开启稠厚器出料管旁路阀,放母液,待稠厚器中母液放完后,开启蒸汽阀,吹洗加料阀和旁路阀。
然后将其关闭。
2)停主机,并用刹车带在2~3分钟内将其制动,主机停转后,停油泵。
3)用木铲或铝铲铲净筛篮内滤饼。
4)按正常开车步骤重新启动油泵、主机,待运转正常后,用回收清洗塔的稀氨水清洗筛篮及其后腔。
5)清洗结束后,按b的步骤停主机、油泵。
6)停车时间较长,则关闭油冷却器冷却水阀。
6.2.1.2系统检修的停车
按6.2.1.1的步骤停车后,系统再用清水置换2~3次,取样分析,氧含量大于20%为合格。
6.2.2紧急停车
如遇全公司停电或运转过程中发生故障时,须紧急停车。
步骤如下:
6.2.2.1立即关闭离心机加料阀。
6.2.2.2迅速按停车按钮,停主机、油泵,并制动主机。
同时与碳化、包装岗位联系。
6.2.2.3稠厚器内未分离完的悬浮液应根据具体情况处理,以防结晶沉淀堵塞。
6.3离心机空负荷试车
6.3.1检查机体安装,应符合要求,机内无杂物。
6.3.2检查电机绝缘及运转方向,应符合要求。
6.3.3盘车检查传动部件转动正常。
6.3.4油箱加油至正常油位。
6.3.5按正常开车步骤启动离心机,进行空负荷试车,检查离心机的振动和各传动部件的响声,磨擦发热情况及油压系统的工作情况等,第一次运转时间约一分钟,停车检查无问题后,再次启动离心机,并依次延长运转时间至十分钟、三十分钟、两小时,经检查各方面都正常后,即可开启加料阀加负荷运行,转入正常生产。
7不正常现象及处理
离心机身及筛篮振动
1.加料不均匀,引起滤饼厚度不均匀或冲破滤饼
2.轴承损坏
3.地脚螺栓松动
4.筛篮同心度偏差大,不平衡
5.筛网破损,转动失去平衡
1.加料要均匀,情况严重时停车铲除滤饼
2.停车更换轴承
3.拧紧地脚螺栓
4.停车、校正筛篮平衡
5.停车、更换筛网
油压低,推料器推料速度不正常
1.油温过高,粘度不够
2.滤网堵塞,泵吸油量不正常
3.油泵故障
4.油路系统漏油
1.加大油冷却器、冷却水量,降低油温
2.停车清洗滤油网
3.停车检修油泵
4.停车、检修油路
离心机电流突然升高
1.母液管有结晶堵塞,母液流出困难
2.筛篮后腔有结晶堵塞
3.加料量太大
1.停车用蒸汽吹洗母液管
2.用软水清洗筛管后腔
3.减少加料量
碳铵成品含水量高
1.加料量太大,推料速度快
2.结晶颗粒细
3.筛网间隙过小或堵塞
4.筛篮前环密封不严,漏母液
5.密封圈漏母液
6.母液管有结晶堵塞,母液流出困难
1.减少加料量,降低推料速度
2.与碳化工段联系,增大结晶颗粒
3.停车更换或用软水冲洗筛网
4.停车检修筛篮前环
5.停车检修密封圈
6.停车用蒸汽吹洗母液管
漏晶多
1.结晶颗粒细
2.筛网间隙过大或破坏
1.与碳化岗位联系,增大结晶颗粒
2.停车更换筛网
氨吸收岗位操作规程
本规程规定了氨吸收岗位的任务、工艺、操作要点及事故处理方法。
本规程适用于我公司氨吸收岗位的工艺控制与操作。
2氨吸收岗位的任务
用稀氨水或碳化母液吸收合成工段送来的气氨,制得合格的浓氨水,供碳化岗位使用。
3.1.1来自碳化岗位固定付塔的稀氨水和离心机岗位的母液进入氨吸收岗位的母液槽,再由吸氨泵打入高位吸氨器,吸收来自合成工段的气氨,再经冷排冷却后制成合格的浓氨水,然后送碳化岗位。
3.1.2浓氨水的制备可一次吸收或多次循环吸收气体,多次循环时将氨水打入循环槽,与母液槽的母液一起经吸氨泵打到高位吸氨器去吸收气氨。
循环槽
Φ4200mm×
4500mmV=62m2
母液槽
浓氨槽
Φ4000mm×
5500mm
Φ5000mm×
6000mm
蒸发冷
F=82m2
高位吸氨器
Φ400mm×
700mm
1#碳化泵
Q=50m3/hN=15kW
8
2#碳化泵
9
3#碳化泵
10
4#碳化泵
Q=25m3/hN=7.5kW
11
1#浓氨泵
Q=45m3/hN=45kW
12
2#浓氨泵
Q=45m3/hN=37kW
13
3#浓氨泵
Q=55m3/hN=55kW
14
1#、3#吸氨泵
Q=104m3/hN=22kW
15
2#吸氨泵
Q=54m3/hN=11kW
16
1#软水泵
Q=6.5m3/h扬程91米N=7.5kW
17
2#软水泵
Q=25m3/h扬程125米N=22kW
18
晶液泵
65-40-200 7.5KW
19
晶液分离器
Φ1600mm×
3700mm
20
1#一次水泵
IS65-50-160 7.5KW
21
2#一次水泵
IS65-80-160 15KW
22
吸氨冷排
铝Φ108*4
1组
4工艺指标
4.1液位
4.1.1母液槽液位:
≥6m3;
4.1.2循环槽液位:
≥20m3;
4.1.3浓氨槽液位:
≥40m3。
4.2浓度
4.2.1浓氨水浓度:
冬季190~200tt;
夏季200~220tt;
4.2.2循环槽氨水浓度:
≥180tt。
4.3浓氨水中添加剂活性物含量:
(0.1-0.5)g/L。
4.4压力
4.4.1氨气压力:
≤0.1MPa;
4.4.2吸氨泵压力:
≥0.25MPa;
4.4.3碳化泵压力:
≥1.0MPa;
4.4.4浓氨泵压力:
≥1.5MPa;
4.4.5软水泵压力:
≥1.0MPa。
4.5电流
4.5.1吸氨泵电流:
1#、3#≤42A;
2#≤21A;
4.5.2碳化泵电流:
1#-3#:
≤28.4A;
4#≤15A;
4.5.3浓氨泵电流:
1#≤83A;
2#≤68A;
3#≤101A;
5.1经常与合成工段联系,要求送气氨量均匀、压力稳定,同时根据负荷大小及气氨压力变化,及时调节吸收液流量,保证浓氨水浓度及供应量。
5.2控制好稀氨水和母液的配比,保证浓氨水碳化度符合工艺要求。
5.3当浓氨水中的硫化氢含量过高或污物太多时,应适当更换母液。
5.4根据生产负荷变化及浓氨水中添加剂活性物的高低,及时补充皂化液,保证浓氨水中的添加剂符合工艺要求。
5.5经常检查吸氨冷排进、出口浓氨水温度,控制好冷却水用量,保证吸氨效果。
5.6及时检查并消除系统设备管道的跑、冒、滴、漏,防止氨水和母液的损失。
5.7经常注意气氨压力和吸氨泵出口压力变化,以及系统管道有无堵塞,阀芯有无脱落等情况发生,防止液体倒入气氨管。
5.8巡回检查
5.8.1每十五分钟检查一次系统各点压力和温度。
5.8.2每半小时检查一次各贮槽液量。
5.8.3经常检查吸氨泵运转情况。
5.8.4经常检查吸氨冷排冷却水淋洒情况。
6.1.1.1检查各设备、管道、阀门、分析取样点及电器仪表等,必须正常完好。
6.1.1.2检查系统所有阀门的开、关位置,应符合开车要求。
6.1.1.3与供水、供电、供汽部门及合成工段联系,做好开车准