黄岩天材模具厂总结模具的种类Word格式文档下载.docx
《黄岩天材模具厂总结模具的种类Word格式文档下载.docx》由会员分享,可在线阅读,更多相关《黄岩天材模具厂总结模具的种类Word格式文档下载.docx(22页珍藏版)》请在冰豆网上搜索。
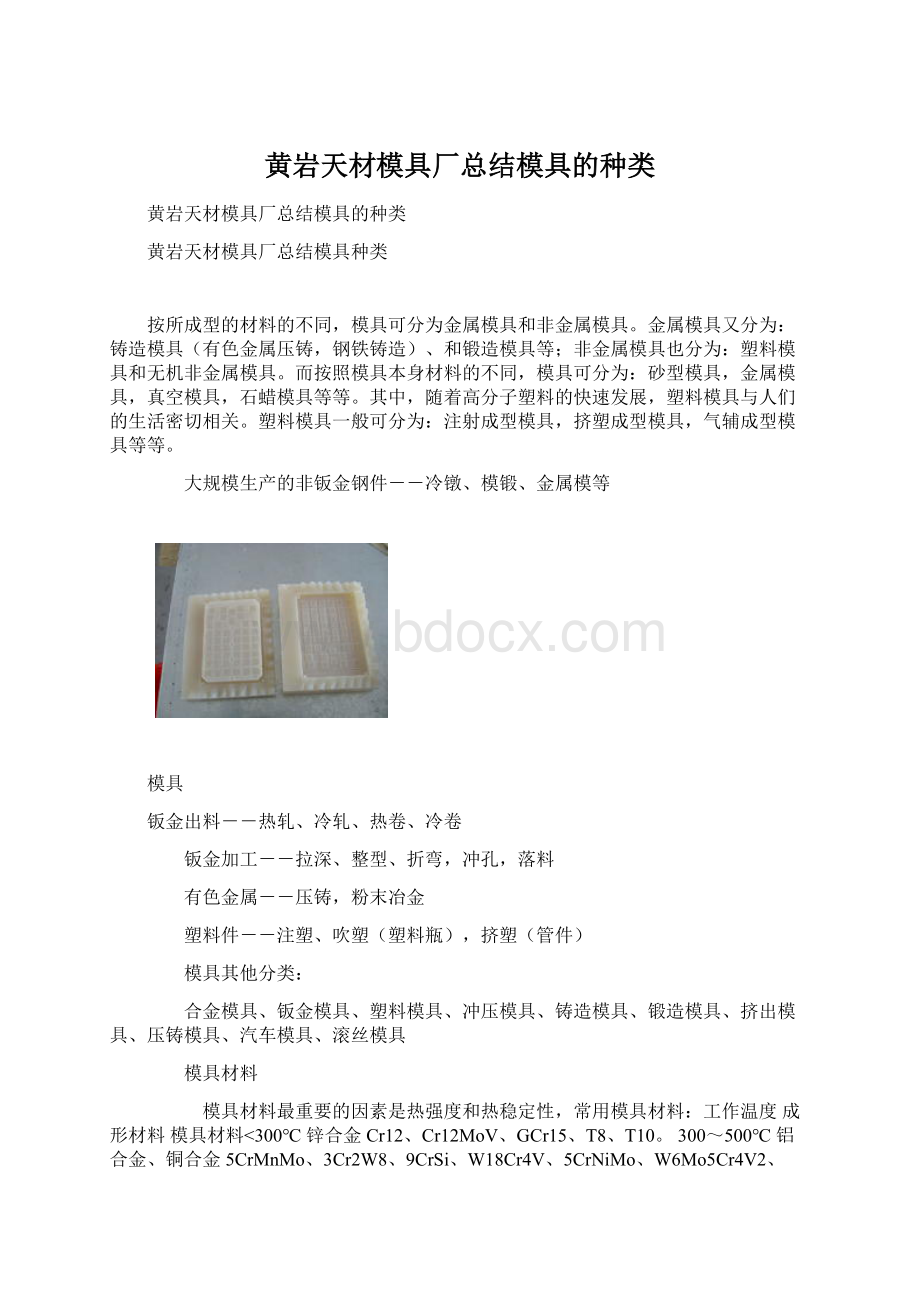
1000℃镍合金铜基合金模具
编辑本段塑料模具
一般模具类别
(1)两板模具
又称单一分型面模,是注塑模中最简单的一种,它以分型面为界面将整个模具分为两部分:
动模和定模。
一部分型腔在动模,另一部分型腔在定模。
主流道在定模;
分流道开设在分型面上,开模后,制品和流道留在动模,动模部分设有顶出系统。
(2)三板模或细水口模
有两个分型面将模具分成三部分,比两板增加了浇口板,适用于制品的四周不准有浇口痕迹的场合,这种模具分成采用点浇口,所以叫细水口模,这种模具结构相应复杂些。
启动动力用山打螺丝或拉板。
按成型方法分类
(1)注射成型
是先把塑料加入到注射机的加热料筒内,塑料受热熔融,在注射机螺杆或柱塞的推动下,经喷嘴和模具浇注系统进入模具型腔,由于物理及化学作用而硬化定型成为注塑制品。
注射成型由具有注射、保压(冷却)和塑件脱模过程所构成循环周期,,因而注射成型具有周期性的特点。
热塑性塑料注射成型的成型周期短、生产效率高,熔料对模具的磨损小,能大批量地成型形状复杂、表面图案与标记清晰、尺寸精度高的塑件;
但是对于壁厚变化大的塑件,难以避免成型缺陷。
塑件各向异性也是质量问题之一,应采用一切可能措施,尽量减小。
(2)压缩成型
俗称压制成型,是最早成型塑件的方法之一。
压缩成型是将塑料直接加入到具有一定温度的敞开的模具型腔内,然后闭合模具,在热与压力作用下塑料熔融变成流动状态。
由于物理及化学作用,而使塑料硬化成为具有一定形状和尺寸的常温保持不变的塑件。
压缩成型主要是用于成型热固性塑料,如酚醛模塑粉、脲醛与三聚氰胺甲醛模塑粉、玻璃纤维增强酚醛塑料、环氧树脂、DAP树脂、有机硅树脂、聚酰亚胺等的模塑料,还可以成型加工不饱和聚酯料团(DMC)、片状模塑料(SMC)、预制整体模塑料(BMC)等。
一般情况下,常常按压缩膜上、下模的配合结构,将压缩模分为溢料式、不溢料式、半溢料式三类。
(3)挤塑成型
是使处于粘流状态的塑料,在高温和一定的压力下,通过具有特定断面形状的口模,然后在较低的温度下,定型成为所需截面形状的连续型材的一种成型方法。
挤塑成型的生产过程,是准备成型物料、挤出造型、冷却定型、牵引与切断、挤出品后处理(调质或热处理)。
在挤塑成型过程中,注意调整好挤出机料筒各加热段和机头口模的温度、螺杆转数、牵引速度等工艺参数以便得到合格的挤塑型材。
特别要注意调整好聚合物熔体由机头口模中挤出的速率。
因为当熔融料挤出的速率较低时,挤出物具有光滑的表面、均匀的断面形状;
但是当熔融物料挤出速率达到某一限度时,挤出物表面就会变得粗糙、失去光泽,出现鲨鱼皮、桔皮纹、形状扭曲等现象。
当挤出速率进一步增大时,挤出物表面出现畸变,甚至支离和断裂成熔体碎片或圆柱。
因此挤出速率的控制至关重要。
(4)压注成型
亦称铸压成型。
是将塑料原料加入预热的加料室内,然后把压柱放入加料室中锁紧模具,通过压柱向塑料施加压力,塑料在高温、高压下熔化为流动状态,并通过浇注系统进入型腔逐渐固化成塑件。
此种成型方法,也称传递模塑成型。
压注成型适用于各低于固性塑料,原则上能进行压缩成型的塑料,也可用压注法成型。
但要求成型物料在低于固化温度时,熔融状态具有良好的流动性,在高于固化温度时,有较大的固化速率。
(5)中空成型
是把由挤出或注射制得的、尚处于塑化状态的管状或片状坯材趋势固定于成型模具中,立刻通入压缩空气,迫使坯材膨胀并贴于模具型腔壁面上,待冷却定型后脱模,即得所需中空制品的一种加工方法。
适合中空成型的塑料为高压聚乙烯、低压聚乙烯、硬聚氯乙烯、软聚氯乙烯、聚苯乙烯、聚丙烯、聚碳酸酯等。
根据型坯成型方法的不同,中空成型主要分为挤出吹塑中空成型和注射吹塑中空成型两种。
挤出吹塑中空成型的优点是挤出机与挤出吹塑模的结构简单,缺点是型坯的壁厚不一致,容易造成塑料制品的壁厚不匀。
右图是挤出吹塑中空成型原理示意图。
注射吹塑中空成型的优点是型坯的壁厚均匀、无飞边,由于注射型坯有底面,因此中空制品的底部不会产生拼和缝,不仅美观而且强度高。
缺点是所用的成型设备和模具价格贵,故这种成型方法多用于小型中空制品的大批量生产上,在使用上没有挤出吹塑中空成型方法广泛。
按其它分类
(1)热流道模
借助加热装置使浇注系统中的塑料不会凝固,也不会随制品脱模,所以又称无流道模。
优点:
1)无废料2)可降底注射压力,可以采用多腔模3)可缩短成型周期4)提高制品的质量适合热流道模塑料的特点:
5)塑料的熔融温度范围较宽。
低温时,流动性好,高温时,具有较好的热稳定性。
6)对压力敏感,不加压力不流动,但施加压力时即可流动。
7)比热性好,以便在模具中很快冷却。
可用热流道的塑料有PE,ABS,POM,PC,HIPS,PS。
我们现在常用的热流道有两种:
1)加热流道模2)绝热流道模。
(2)硬模
3.成型设备:
(1)各射出料缸的射出量,决定那一色用那一支料缸.
(2)打击棒的位置及打击行程.
(3).旋转盘上水路,油路,及电路的配置问题.
(4).旋转盘的承载重量.
4.模座设计:
模仁配置设计
首先考虑到模具公模侧必需旋转180度,模仁设置必需交叉对称排列,否则无法合模成型.
(1).导柱:
具有导引公模与母模的功能.在多色模中必需保持同心度.
(2).回位销:
由于模具必需旋转的动作,所以必需将顶出板固定,在回位销上加弹簧使顶出板保持稳定.
(3).定位块:
确保两模座固定于大固板时不因螺丝的间隙问题而造成偏移.
(4).调整块(耐磨块):
主要用于合模时模具高度z坐标值误差时可以做调整.
(5).顶出机构:
顶出方式的设计与一般模具相同.
(6).冷却回路设计:
模具一与模具二的冷却回路设计尽量相同.
编辑本段金属模具
模具按加工金属的加工工艺分类,常用的有:
冲压模,包括冲裁模、弯曲模、拉深模、翻边模、缩口模、起伏模、胀形模、整形模等;
锻模,包括模锻用锻模、镦锻模等;
以及挤压模和压铸模。
用于加工非金属和粉末冶金的模具则按加工对象命名和分类,有塑料模、橡胶模和粉末冶金模等。
1.冲压模用于板料冲压成形和分离的模具。
成形用的模具有型腔,分离用的模具有刃口。
最常用的冲压模只有一个工位,完成一道生产工序。
这种模具应用普遍,结构简单,制造容易,但生产效率低。
为提高生产率,可将多道冲压工序,如落料、拉深、冲孔、切边等安排在同一模具上,使坯料在同一工位上完成多道冲压工序,这种模具称为复合模。
另有将落料、弯曲、拉深、冲孔和切边等多工序安排在同一模具的不同工位上,这种模具称为级进模(又称连续模)。
2.锻模用于热态金属模锻成形的模具。
模锻时,坯料往往经过多次变形才能制成锻件,这就需要在一个模块上刻有几个型腔。
金属依次送至各个型腔,并在型腔内塑性流动,最后充满型腔制成锻件。
在模锻成形中,坯料很难与终锻时型腔体积相等,为了避免废品,坯料选用稍大一些。
为此,在终锻模的上、下模分界面的型腔四周设有飞边槽,以存贮多余的金属,成形后将飞边切去。
型腔中应尽量减少尖角、深槽,以利于金属塑性流动和充填,减少模具磨损和开裂,提高模具寿命。
3.挤压模用于将金属挤压成形的模具。
正挤压模有一个静止的凹模和放置坯料的挤压筒和对坯料施加压力的冲头。
挤压空心件时,冲头前端带有芯棒。
反挤压模的挤压筒为凹模,冲头成为凸模。
金属需要在很大的压强下才能从凹模挤出成形,在冷态下所需压强可高达2000千牛/毫米(200千克/毫米)以上。
为此,挤压筒和反挤压的凹模需要有很高的强度,常采用多层预应力组合结构。
冲头和凸模的工作长度宜短,避免在高的压应力下发生不稳和弯曲。
4.压铸模安装在压铸机上,液态金属在高压下注入型腔、保压至金属凝固和成形的模具。
它主要用于铝、锌、铜件,也可用于钢件。
压铸模的结构与塑料注射模类似。
它由动模与定模构成型腔,用型芯形成铸件的孔腔。
金属在型腔内冷却、凝固后抽出型芯,分开模具,由顶杆推出铸件。
压铸件一般壁薄中空,有众多台、筋,形状结构复杂,尺寸要求较精确,表面较光洁,金属在熔融的高温下成形。
因此压铸模需要采用耐高温的材料制造。
5.粉末冶金模将固体金属粉末压制成形的模具。
将金属粉末定量地倒入下模,然后上模压下、闭合、成形,再用顶料装置顶出预制坯。
将预制坯送入烧结炉内烧结,遂制成粉末冶金零件。
一般粉末冶金件的空隙很大,占总体积的15%左右,成形压力不大,模具结构较简单,精度、表面粗糙度要求一般,所以对模具无特殊要求。
为了减少空隙、提高密度和强度,对烧结后的坯件,再进行一次热锻,通称粉末锻造。
所用的模具与模锻模相似。
编辑本段模具生产的流程
模具就是一个模型,按照这个模型做出产品来,但是模具是怎样生产出来的呢,可能除了模具专业人士大多数回答不出来.模具已经在我们生活当中起了不可替代的作用,我们的生活用品大部分离不开模具,如,电脑,电话机,传真机,键盘,杯子等等这些塑胶制品就不用说了,另外像汽车和摩托发动机的外罩也是用模具做出来的,光一个汽车各种各样的模具就要用到2万多个.所以说现代生活模具的作用不可替代.只要批量生产就离不开模具,至少在最近50年内离不开。
那么模具是怎样做成的呢?
下面对现代模具生产流程做一个简单的介绍。
1)ESI(EarlierSupplierEvolvement供应商早期参与):
此阶段主要是客户与供应商之间进行的关于产品设计和模具开发等方面的技术探讨,主要的目的是为了让供应商清楚地领会到产品设计者的设计意图及精度要求,同时也让产品设计者更好地明白模具生产的能力,产品的工艺性能,从而做出更合理的设计。
2)报价(Quotation):
包括模具的价格、模具的寿命、周转流程、机器要求吨数以及模具的交货期。
(更详细的报价应该包括产品尺寸重量、模具尺寸重量等信息。
)
3)订单(PurchaseOrder):
客户订单、订金的发出以及供应商订单的接受。
4)模具生产计划及排工安排(ProductionPlanningandScheduleArrangement):
此阶段需要针对模具的交货的具体日期向客户作出回复。
5)模具设计(Design):
可能使用的设计软件有Pro/Engineer、UG、Solidworks、AutoCAD、CATIA等
6)采购材料
7)模具加工(Machining):
所涉及的工序大致有车、锣(铣)、热处理、磨、电脑锣(CNC)、电火花(EDM)、线切割(WEDM)、座标磨(JIGGRINGING)、激光刻字、抛光等。
8)模具装配(Assembly)
9)模具试模(TrialRun)
10)样板评估报告(SER)
11)样板评估报告批核(SERApproval)
编辑本段模具的基本设计原理
因为不同的成型模具已应用很多领域,加之专业模具的制造技术在这些年也有了一定的变化发展,因此在这部分,总结了真空吸塑成型模具的一般设计规则。
真空吸塑成型模具的设计包括了批量大小、成型设备、精度条件、几何形状设计、尺寸稳定性及表面质量等内容。
1、批量的大小实验用,模具产量小时,可采用木材或树脂进行制造。
但是,如果实验用模具是为了获得制品有关收缩、尺寸稳定性及循环时间等的数据时,应该使用单型腔模具来实验,且能保证其能在生产条件下运用。
模具一般用石膏、铜、铝或铝-钢合金制造,很少用到铝-树脂。
2、几何形状设计,设计时,经常要综合考虑尺寸稳定性及表面质量。
例如,制品设计和尺寸稳定性要求采用阴模(凹模),但是表面要求光泽度较高的制品却要求使用阳模(凸模),这样一来,塑件订购方会综合考虑到这两点,以使制品能在最佳条件下进行生产。
经验证明,不符合实际加工条件的设计往往是失败的。
3、尺寸稳定,在成型过程中,塑件与模具接触的面要比离开模具部分的尺寸稳定性更好。
如果日后由于材料刚度的需要要求改变材料厚度,可能导致要将阳模转换为阴模。
塑件的尺寸公差不能低于收缩率的10%。
4、塑件表面,就成型材料能够包住的范围而言,塑件可见面的表面结构应在与模具接触处成型。
如果可能的话,塑件的光洁面不要与模具表面接触。
就像采用阴模制造浴盆和洗衣盆的情况。
5、修饰,如果使用机械式水平锯锯掉塑件的夹持边,在高度方向上,至少要有6~8mm的余量。
其他的修整工作,如磨削、激光切削或射流,也必须留有余量。
刀口模切割线间的间隙最小,冲孔模修整时的分布宽度也很小,这些都是要注意的。
6、收缩和变形,塑料易收缩(如PE),有些塑件易变形,无论如何预防,塑件在冷却阶段都会发生变形。
在这种条件下,就要改变成型模具的外形来适应塑件的几何偏差。
例如:
尽管塑件壁保持平直,但其基准中心已偏离10mm;
可以抬高模具底座,以调整这种变形的收缩量。
7、收缩量,在制造吸塑成型模具时一定要考虑到下列的收缩因素。
①成型制品收缩。
如果不能清楚地知道塑料的收缩率,则必须取样或用相似形状的模具通过试验来得到。
注意:
通过这种方法只能得到收缩率,不能得到变形尺寸。
②中间介质的不利影响造成的收缩,如陶瓷、硅橡胶等。
③模具所用材料的收缩,如铸造铝时的收缩。
编辑本段设计
按国家职业定义,模具设计是:
从事企业模具的数字化设计,包括型腔模与冷冲模,在传统模具设计的基础上,充分应用数字化设计工具,提高模具设计质量,缩短模具设计周期的人员。
单元化设计之概念
冲压模具整体构造可分成二大部分:
(1).共通部分
(2).依制品而变动的部分。
共通部分可加以标准化或规格化,依制品而变动的部分是难以规格化。
模板之构成及规格
1.模板之构成
冲压模具之构成将依模具种类及构成及相异,有顺配置型构造与逆配置型构造二大类。
前者是最常使用的构造,后者构造主要用于引伸成形模具或配合特殊模具。
从事的主要工作包括:
(1)数字化制图--将三维产品及模具模型转换为常规加工中用的二维工程图;
(2)模具的数字化设计--根据产品模型与设计意图,建立相关的模具三维实体模型;
(3)模具的数字化分析仿真--根据产品成形工艺条件,进行模具零件的结构分析、热分析、疲劳分析和模具的运动分析;
(4)产品成形过程模拟--注塑成形、冲压成形;
(5)定制适合本公司模具设计标准件及标准设计过程;
(6)模具生产管理。
2.模具之规格
(1).模具尺寸与锁紧螺丝
模板之尺寸应大于工作区域,并选择标准模板尺寸。
模板锁紧螺丝之位置配置与模具种类及模板尺寸有关。
其中单工程模具最常使用锁紧螺丝配置于四边角,最标准形式工作区域可广大使用。
长形之模具及连续模具最常使用锁紧螺丝配置于四边角及中间位置。
(2).模板之厚度
模板之厚度选择与模具之构造、冲压加工种类、冲压加工加工力、冲压加工精度等有绝对关系。
依据理论计算决定模具之厚度是困难的,一般上系由经验求得,设计使用的模板厚度种类宜尽量少,配合模具高度及夹紧高度加以标准化以便利采购及库存管理。
模板之设计
连续模具之主要模板有冲头固定板、压料板、母模板等等,其构造设计依冲压制品之精度、生产数量、模具之加工设备与加工方法、模具之维护保养方式等有下列三种形式:
(1)整块式,
(2)轭式,(3)镶入式。
1.整块式
整块式模板亦称为一体构造型,其加工形状必须是封闭的。
整块式模板主要用于简单结构或精度不高的模具,其加工方式以切削加工为主(不需热处理),采用热处理之模板必须再施行线切割加工或放电加工及研磨加工。
模板尺寸长(连续模具)之场合将采用两块或多块一体型并用之。
2.轭式
轭式模板之中央部加工成凹沟状以组装块状品。
其构造依应用要求,凹沟部可以其他模板构成之。
此轭式模板构造之优点有:
沟部加工容易,沟部宽度可调整之,加工精度良好等。
但刚性低是其缺点。
轭式模板之设计注意事项如下:
(1).轭板构部与块状部品之嵌合采中间配合或轻配合方式,如采强压配合将使轭板发生变化。
(2).轭板兼俱块状部品之保持功能,为承受块状部品之侧压及面压,必须具有足够的刚性。
还有为使轭板沟部与块状部品得到密着组合,其沟部角隅作成逃隙加工,如轭板沟部角隅不能作成逃隙加工,则块状部品须作成逃隙加工。
(3).块状部品之分割应同时考虑其内部之形状,基准面必须明确化。
为使冲压加工时不产生变形,亦要注意各个块状部品之形状。
(4).轭板组入许多件块状部品时,由于各块状部品之加工累积误差使得节距产生变动,解决对策是中间块状部品设计成可调整方式。
(5).块状部品采并排组合之模具构造,由于冲切加工时块状部品将承受侧压使各块状部品间产生间隙或造成块状部品之倾斜。
此现象是冲压尺寸不良、冲屑阻塞等冲压不良之重要原因,因此必须有充分的对策。
(6).轭板内块状部品之固定方法,依其大小及形状有下列五种:
A.以锁紧螺丝固定,B.以键固定,C.以揳形键固定,D.以肩部固定,E.以上压件(如导料板)压紧固定。
3.镶入式
模板中加工圆形或方形之凹部,将块状部品镶合嵌入于模板中,此种模板称为镶入式构造,此构造之加工累积公差少、刚性高,分解及组立时之精度再现性良好。
由于具有容易机械加工、加工精度由工作机械决定、最后调整之工程少等优点,镶入式模板构造已成为精密冲压模具之主流,但其缺点是需要高精度的孔穴加工机。
连续冲压模具采用此模板构造时,为使模板具有高刚性要求,乃设计空站。
镶入式模板构造之注意事项如下所述:
(1).嵌入孔穴之加工:
模板之嵌入孔穴加工使用立式铣床(或治具铣床)、综合加工机、治具镗床、治具磨床、线割放电加工机等。
嵌入孔穴之加工基准,使用线割放电加工机时,为提高其加工精度乃进行二次或以上之线割加工。
(2).嵌入件之固定方法:
嵌入件固定方法之决定因素有不变动其加工的精度、组立及分解之容易性、调整之可能性等。
嵌入件之固定方法有下列四种:
A.以螺丝固定,B.以肩部固定,C.以趾块固定,D.其上部以板件压紧。
母模板之嵌入件固定方法亦有采用压入配合,此时应避免因加工热膨胀而产生的松弛结果,使用圆形模套嵌入件加工不规则孔穴时应设计回转防止方法。
(3).嵌入件组立及分解之考量:
嵌入件及其孔穴加工精度要求高以进行组立作业。
为得到即使有稍微的尺寸误差亦能于组立时加以调整,宜事先考虑解决对策,嵌入件加工之具体考虑事项有下列五项:
A.设有压入导入部,B.以隔片调整嵌入件之压入状态及正确位置,C嵌入件底面设有压出用孔穴,D.以螺丝锁紧时宜采用同一尺寸之螺丝,以利锁固及松开,E.为防止组立方向之失误,应设计防呆倒角加工。
单元化之设计
1.模具对准单元
模具对准单元亦称为模具刃件之对合引导装置。
为确实保持上模与下模之对准及缩短其准备时间,依制品精度及生产数量等条件要求,模具对准单元主要有下列五种:
(1).无导引型:
模具安装于冲床时直接进行其刃件之对合作业,不使用引导装置。
(2).外导引型:
此种装置是最标准的构造,导引装置装设于上模座及下模座,不通过各模板,一般称为模座型。
(3).外导引与内导引并用型
(一):
此种装置是连续模具最常使用之构造,冲头固定板及压料板间装设内导引装置。
冲头与母模之对合利用固定销及外导引装置。
内导引装置之另一作用是防止压料板倾斜及保护细小冲头。
(4).外导引与内导引并用型
(二):
此种装置是高精密度高速连续模具之使用构造,内导引装置贯穿冲头固定板、压料板及母模固定板等等。
内导引装置本身亦有模具刃件对合及保护细小冲头作用。
外导引装置之主要作用是模具分解及安装于冲床时能得到滑顺目的。
(5).内导引型:
此构造不使用外导引装置,内导引装置贯穿冲头固定板、压料板及母模固定板等等,正确地保持各块板之位置关系性以保护冲头。
2.导注及导套单元
模具之导引方式及配件有导注及导套单元之种类有两种:
(A).外导引型(模座型或称主导引),(B).内导引型(或称辅助引)。
另行配合精密模具之要求,使用外导引与内导引并用型之需求性高。
(1).外导引型:
一般上使用于不要求高精密度之模具,大多与模座构成一单元贩卖之,主要作用是模具安装于冲床时之刃件对合,几乎没有冲压加工中之动态精度保持效果。
(2).内导引型:
由于模具加工机之进展,最近急速普及。
主要作用除了模具安装于冲床时之刃件对合外,亦有冲压加工中之动态精度保持效果。
(3).外导引与内导引并用型:
一副模具同时使用外导引与内导引装置。
3.冲头与母模单元(圆形)
(1).冲头单元:
圆形冲头单元依其形状(肩部型及平直型)、长度、维修之方便性,使用冲头单元宜与压料板导套单元配合。
(2).母模单元:
圆形母模单元亦称为母模导套单元,其形式有整块式及分开式,依生产数量、使用寿命及制品或冲屑之处理性,母模单元之组合系列有:
(A).使用模板直接加工母模形状,(B).具有二段斜角之逃隙部,(C).是否要使用背板,(D).不规则母模形状必须有回转防止设计。
4.压料螺栓与弹簧单元
(1).压料螺栓单元:
压料板螺栓之种类有:
(A).外螺丝型,(B).套筒型,(C).内螺丝型。
为保持压料板于指定位置平行状态,压料螺栓之停止方法(肩部接触部位):
(A).模座凹穴承受面,(B).冲头固定板顶面,(C).冲头背板顶面。
(2).压料弹簧单元:
可动式压料板压料弹簧单元可大致分为:
(A).单独使用型,(B).与压料螺栓并用型
选择压料弹簧单元时最好考虑下列要点再决定之:
(A).确保弹簧之自由长度及必要的压缩量(压缩量大之弹簧宜置于压料板凹穴)。
(B).初期的弹簧压缩量(预压缩量)或荷重之调整有无必要。
(C).考量模具组立或维护保养之容易性。