锻造实习教案Word格式.docx
《锻造实习教案Word格式.docx》由会员分享,可在线阅读,更多相关《锻造实习教案Word格式.docx(14页珍藏版)》请在冰豆网上搜索。
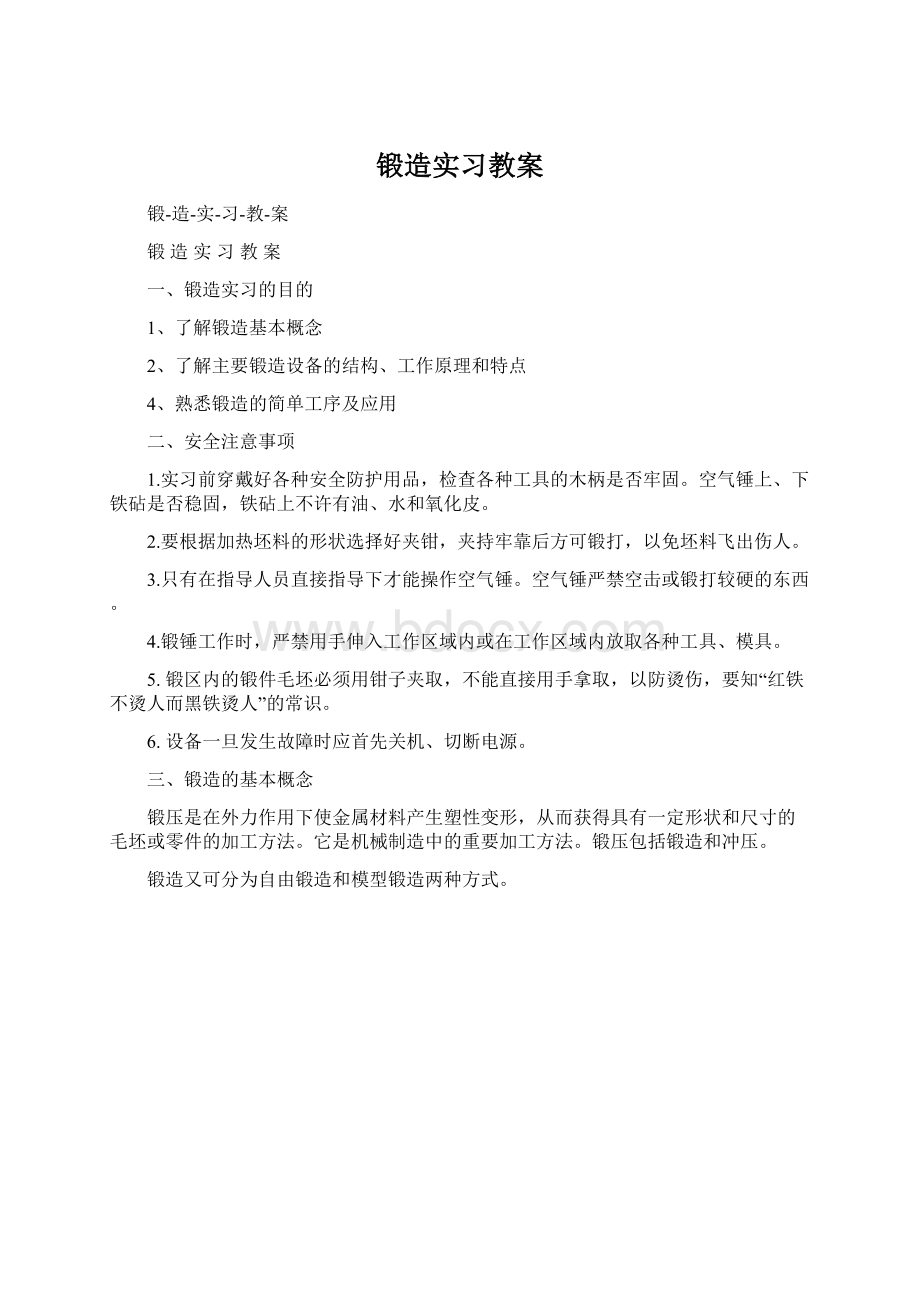
1.镦粗
镦粗是使坯料的截面增大,高度减小的锻造工序。
镦粗有完全镦粗、局部镦粗和垫环镦粗等三种方式。
局部镦粗按其镦粗的位置不同又可分为端部镦粗和中间镦粗两种。
如图所示。
镦粗主要用来锻造圆盘类(如齿轮坯)及法兰等锻件,在锻造空心锻件时,可作为冲孔前的预备工序,镦粗可作为提高锻造比的预备工序。
镦粗的一般规则、操作方法及注意事项如下:
⑴被镦粗坯料的高度与直径(或边长)之比应小于2.5~3,否则会镦弯(图a)。
工件镦弯后应将其放平,轻轻锤击矫正(图b)。
局部镦粗时,镦粗部分坯料的高度与直径之比也应小于2.5~3。
⑵镦粗的始锻温度采用坯料允许的最高始锻温度,并应烧透。
坯料的加热要均匀,否则镦粗时工件变形不均匀,对某些材料还可能锻裂。
(a)(b)(a)(b)
镦粗镦弯的产生和矫正
a)完全镦粗b)局部镦粗a)镦弯的产生b)镦弯的矫正
⑶镦粗的两端面要平整且与轴线垂直,否则可能会产生镦歪现象。
矫正镦歪的方法是将坯料斜立,轻打镦歪的斜角,然后放正,继续锻打。
如果锤头或抵铁的工作面因磨损而变得不平直时,则锻打时要不断将坯料旋转,以便获得均匀的变形而不致镦歪。
⑷锤击应力量足够,否则就可能产生细腰形,如图a所示。
若不及时纠正,继续锻打下去,则可能产生夹层,使工件报废,如图b所示。
(a)(b)(c)(a)(b)
镦歪的产生和矫正细腰形及夹层的产生
a)细腰形b)夹层
2.拔长
拔长是使坯料长度增加,横截面减少的锻造工序,又称延伸或引伸,如图所示。
拔长用于锻制长而截面小的工件,如轴类、杆类和长筒形零件。
(a)(b)(c)
拔长
a)拔长b)局部拔长c)心轴拔长
拔长的一般规则,操作方法及注意事项:
⑴拔长过程中要将毛坯料不断反复地翻转90°
,并沿轴向送进操作,如图a所示。
螺旋式翻转拔长如图b所示,是将毛坯沿一个方向作90°
翻转,并沿轴向送进的操作。
单面顺序拔长如图c所示,是将毛坯沿整个长度方向锻打一遍后,再翻转90°
,同样依次沿轴向送进操作。
用这种方法拔长时,应注意工件的宽度和厚度之比不要超过2.5,否则再次翻转继续拔长时容易产生折叠。
(a)(b)(c)
拔长时锻件的翻转方法
a)反复翻转拔长b)螺旋式翻转拔长c)单面顺序拔长
⑵拔长时,坯料应沿抵铁的宽度方向送进,每次的送进量应为抵铁宽度的0.3~0.7倍(图a)。
送进量太大,金属主要向宽度方向流动,反而降低延伸效率(图b)。
送进量太小,又容易产生夹层(图c)。
另外,每次压下量也不要太大,压下量应等于或下于送进量,否则也容易产生夹层。
拔长时的送进方向和进给量
a)送进量合适b)送进量太大、拔长率降低c)送进量太小、产生夹层
⑶由大直径的坯料拔长到小
直径的锻件时,应把坯料先锻成
正方形,在正方形的截面下拔长,
到接近锻件的直径时,再倒棱,
滚打成圆形,这样锻造效率高,
质量好。
大直径坯料拔长时的变形过程
⑷锻制台阶轴或带台阶的方形、矩形截面的锻件时,在拔长前应先压肩。
压肩后对一端进行局部拔长即可锻出台阶。
(a)(b)
压肩
a)方料压肩b)圆料压肩
⑸锻件拔长后须进行修整,修整方形或矩形锻件时,应沿下抵铁的长度方向送进,如图a所示,以增加工件与抵铁的接触长度。
拔长过程中若产生翘曲应及时翻转180°
轻打校平。
圆形截面的锻件用型锤或摔子修整。
如图b所示。
(a)(b)
拨长后的修整
a)方形、矩形面的修整b)圆形截面的修整
3.冲孔
冲孔是用冲子在坯料冲出透孔或不透孔的锻造工序。
一般规定:
锤的落下部分重量在0.15~5t之间,最小冲孔直径相应为Φ30~Φ100mm;
孔径小于100mm,而孔深大于300mm的孔可不冲出;
孔径小于150mm,而孔深大于500mm的孔也不冲出。
根据冲孔所用的冲子的形状不同,冲孔分实心冲子冲孔和空心冲子冲孔。
实心冲子冲孔分单面冲孔和双面冲孔。
⑴单面冲孔:
对于较薄工件,即工件高度与冲孔孔径之比小于0.125时,可采用单面冲孔(图)。
冲孔时,将工件放在漏盘上,冲子大头朝下,漏盘的孔径和冲子的直径应有一定的间隙,冲孔时应仔细校正,冲孔后稍加平整。
⑵双面冲孔:
其操作过程为:
镦粗;
试冲(找正中心冲孔痕);
撒煤粉;
冲孔,即冲孔到锻件厚度的2/3~3/4;
翻转180°
找正中心;
冲除连皮;
修整内孔;
修整外圆。
(a)(b)
单面冲孔双面冲孔
冲孔前的镦粗是为了减少冲孔深度并使端面平整。
由于冲孔锻件的局部变形量很大,为了提高塑性,防止冲裂,冲孔应在始锻温度下进行。
冲孔时试冲的目的是为了保证孔的位置正确,即先用冲子轻冲出孔位的凹痕,并检查孔的位置是否正确,如果有偏差,可将冲子放在正确的位置上再试冲一次,加以纠正。
孔位检查或修正无误后,向凹痕内撒放少许煤粉或焦炭粒,其作用是便于拔出冲子,因可利用煤粉受热后产生的气体膨胀力将冲子顶出,但要特别注意安全,防止冲子和气体冲出伤人,对大型锻件不用放煤粉,而是冲子冲入坯料后,立即带着冲子滚外圆,直到冲子松动脱出。
冲子拔出后可继续冲深,此时应注意保持冲子与砧面垂直,防止冲歪,当冲到一定深度时,取出冲子,翻转锻件,然后从反面将孔冲透。
⑶空心冲子冲孔:
当冲孔直径超过400mm时,多采用空心冲子冲孔。
对于重要的锻件,将其有缺陷的中心部分冲掉,有利于改善锻件的机械性能。
4.切割
切割是使坯料分开的工序,如切去料头、下料和切割成一定形状等。
用手工切割小毛坯时,把工件放在砧面上,錾子垂直于工件轴线,边錾边旋转工件,当快切断时,应将切口稍移至砧边处,轻轻将工件切断。
大截面毛坯是在锻锤或压力机上切断的,方形截面的切割是先将剁刀垂直切入锻件,至快断开时,将工件翻转180°
再用剁刀或克棍把工件截断,如图a所示。
切割圆形截面锻件时,要将锻件放在带有圆凹槽的剁垫上,边切边旋转锻件,如图b所示。
(a)(b)
切割
a)方料的切割b)圆料的切割
5.弯曲
使坯料弯成一定角度或形状的锻造工序称为弯曲。
弯曲用于锻造吊钩、链环、弯板等锻件。
弯曲时锻件的加热部分最好只限于被弯曲的一段,加热必须均匀。
在空气锤上进行弯曲时,将坯料夹在上下砥铁间,使欲弯曲的部分露出,用手锤或大锤将坯料打弯,如图a所示。
或借助于成型垫铁、成型压铁等辅助工具使其产生成型弯曲,如图b所示。
弯曲
a)角度弯曲b)成形弯曲
六、螺母的锻造过程
锻造前要根据锻件的形状、尺寸大小及坯料形状等具体情况,合理选择基本工序和确定锻造工艺过程。
螺母的锻造过程
序号
火次
操作工序
工具
备注
1
下料
剪床
按锻件图尺寸,考虑料头烧损计算坯料尺寸并使H。
/d。
<
2.5
2
镦粗
尖口钳
3
冲孔
圆钩钳
冲子
4
锻六角
心棒
用心棒插入孔中,锻好一面转60°
锻第二面,再转60°
即锻好
5
罩圆
倒角
罩圆凹模
6
修整
平锤
修整温度可略低于800℃
(先示范,学生再实际操作。
)
机加工前,锻件要进行热处理,目的是均匀组织,细化晶粒,减少锻造残余应力,调整硬度,改善机械加工性能,为最终热处理做准备。
(实习的目的和意义、实习的内容及操作步骤、实习小结)
1、金属锻造前为什么要加热?
2、自由锻造有哪些基本操作工序?
各有何用途?
3、指出空气锤各组成部分的名称。
4、冲压的主要特点是什么?
冲压有哪些基本工序?
板料冲压
一、冲压生产概述
利用冲压设备和冲模使金属或非金属板料产生分离或变形的压力加工方法称冲压,也称为板料冲压。
这种加工方法通常是在常温下进行的,所以又称冷冲压。
板料冲压的原材料是具有较高塑性的金属材料,如低碳钢、铜及其合金、镁合金等。
非金属(如石棉板、硬橡皮、胶木板、皮革等)的板材、带材或其他型材。
用于加工的板料厚度一般小于6mm。
冲压生产的特点。
①可以生产形状复杂的零件或毛坯。
②冲压制品具有较高的精度、较低的表面粗糙度,质量稳定,互换、性能好。
③产品还具有材料消耗少、重量轻、强度高和刚度好的特点。
④冲压操作简单,生产率高,易于实现机械化和自动化。
⑤冲模精度要求高,结构较复杂,生产周期较长,制造成本较高,故只适用于大批量生产场合。
在一切有关制造金属或非金属薄板成品的工业部门中都可采用冲压生产,尤其在日用品、汽车、航空、电器、电机和仪表等工业生产部门,应用更为广泛。
二、板料冲压的主要工序
按板料在加工中是否分离,冲
压工艺一般可分为分离工序和变形
工序两大类。
分离工序是在冲压过
程中使冲压件与坯料沿一定的轮廓
线互相分离;
而变形工序是使冲压
坯料在不破坏的条件下发生塑性变
形,并转化成所要求的成品形状。
冲裁
在分离工序中,剪裁主要是在剪床上完成的。
落料和冲孔又统称为冲裁,如上图所示,一般在冲床上完成。
弯曲示意图拉深示意图
在变形工序中,还可按加工要求和特点不同分为弯曲、拉深(又称拉延)和成形等类。
其中弯曲工序除了在冲床上完成之外,还可以在折弯机(如电气箱体加工)、滚弯机(如自行车轮圈制造等)上实行。
弯曲的坯料除板材之外还可以是管子或其他型材。
变形工序又可分为缩口、翻边、扩口、卷边、胀形和压印等。
翻边
a)内孔翻边b)外缘翻边
三、冲压主要设备冲压所用的设备种类有多种,但主要设备是剪床和冲床。
1.剪床
剪床的用途是将板料切成一定宽度的条料或块料,以供给冲压所用,剪床传动机构如图5-5所示。
剪床的主要技术参数是能剪板料的厚度和长度,如Q11-2×
1000型剪床,表示能剪厚度为2mm、长度为1000mm的板材。
剪切宽度大的板材用斜刃剪床,当剪切窄而厚的板材时,应选用平刃剪床。
剪床传动机构示意图
1-电动机2-带轮3-制动器4-曲柄5-滑块6-齿轮7-离合器8-板料
9-下刀片10-上刀件11-导轨12-工作台13-挡铁
2.冲床
冲床是曲柄压力机的一种,可完成除剪切外的绝大多数基本工序。
冲床按其结构可分为单柱式和双柱式、开式和闭式等;
按滑块的驱动方式分为液压驱动和机械驱动两类。
机械式冲床的工作机构主要由滑块驱动机构(如曲柄、偏心齿轮、凸轮等)、连杆和滑块组成。
下图为开式双柱式冲床的外形和传动简图。
电动机经V带减速系统使大带轮转动,再经离合器使曲轴旋转。
当踩下踏板后,离合器闭合并带动曲轴旋转,再通过连杆带动滑块沿导轨作上下往复运动,完成冲压加工。
冲模的上模装在滑块上,随滑块上下运动,上下模闭合一次即完成—次冲压过程。
踏板踩下后立即抬起,滑块冲压一次后便在制动器作用下,停止在最高位置上,以便进行下一次冲压。
若踏板不抬起,滑块则进行连续冲压。
通用性好的开式冲床的规格以额定标称压力来表示,如100kN(10t)。
其他主要技术参数有滑块行程距离(mm)、滑块行程次数(次/min)和封闭高度等。
冲床
a)外观图b)传动简图
1-电动机2-小带轮3-大带轮4-小齿轮5-大齿轮6-离合器7-曲轴8-制动器
9-连杆10-滑块11-上模12-下模13-垫板14-工作台15-床身16-底座17-脚踏板
3.冲模结构
冲模是板料冲压的主要工具,其典型结构如下图所示。
一副冲模由若干零件组成,大致可分为以下几类:
工作零件如凸模l和凹模2,为冲模的工作部分,它们分别通过压板固定在上下模板上,其作用是使板料变形或分离,这是模具关键性的零件。
定位零件如导料板9,定位销10。
用以保证板料在冲模中具有准确的位置。
导料板控制坯料进给方向,定位销控制坯料进给量。
卸料零件如卸料板8。
当冲头回程时,可使凸模从工件或坯料中脱出。
亦可用弹性卸料,即用弹簧、橡皮等弹性元件通过卸料板推下板料。
模板零件如上模板3,下模板4和模柄5等。
上模借助上模板通过模柄固定在冲床滑块上,并可随滑块上、下运动;
下模借助下模板用压板螺栓固定在工作台上。
导向零件如导套11、导柱12等,是保证模具运动精度的重要部件,分别固定在上、下模板上,其作用是保证凸模向下运动时能对准凹模孔,并保证间隙均匀。
固定板零件如凸模压板6、凹模压板7等,使凸模、凹模分别固定在上、下模板上。
此外还有螺钉、螺栓等联接件。
以上所有模具零件并非每副模具都须具备,但工作零件、模板零件、固定板零件等则是每副模具所必须有的。
冲裁模
1-凸模2-凹模3-上模板4-下模板5-模柄6-压板7-压板
8-卸料板9-导料板10-定位销11-导套12-导柱
冲床操作安全规范:
⑴冲压工艺所需的冲剪力或变形力要低于或等于冲床的标称压力。
⑵开机前应锁紧所有调节和紧固螺栓,以免模具等松动而造成设备、模具损坏和人身安全事故。
⑶开机后,严禁将手伸入上下模之间,取下工件或废料应使用工具。
冲压进行时严禁将工具伸入冲模之间。
⑷两人以上共同操作时应由一人专门控制踏脚板,踏脚板上应有防护罩,或将其放在隐蔽安全处,工作台上应取尽杂物,以免杂物坠落于踏脚板上造成误冲事故。
⑸装拆或调整模具应停机进行。