机器人焊接智能化技术.docx
《机器人焊接智能化技术.docx》由会员分享,可在线阅读,更多相关《机器人焊接智能化技术.docx(10页珍藏版)》请在冰豆网上搜索。
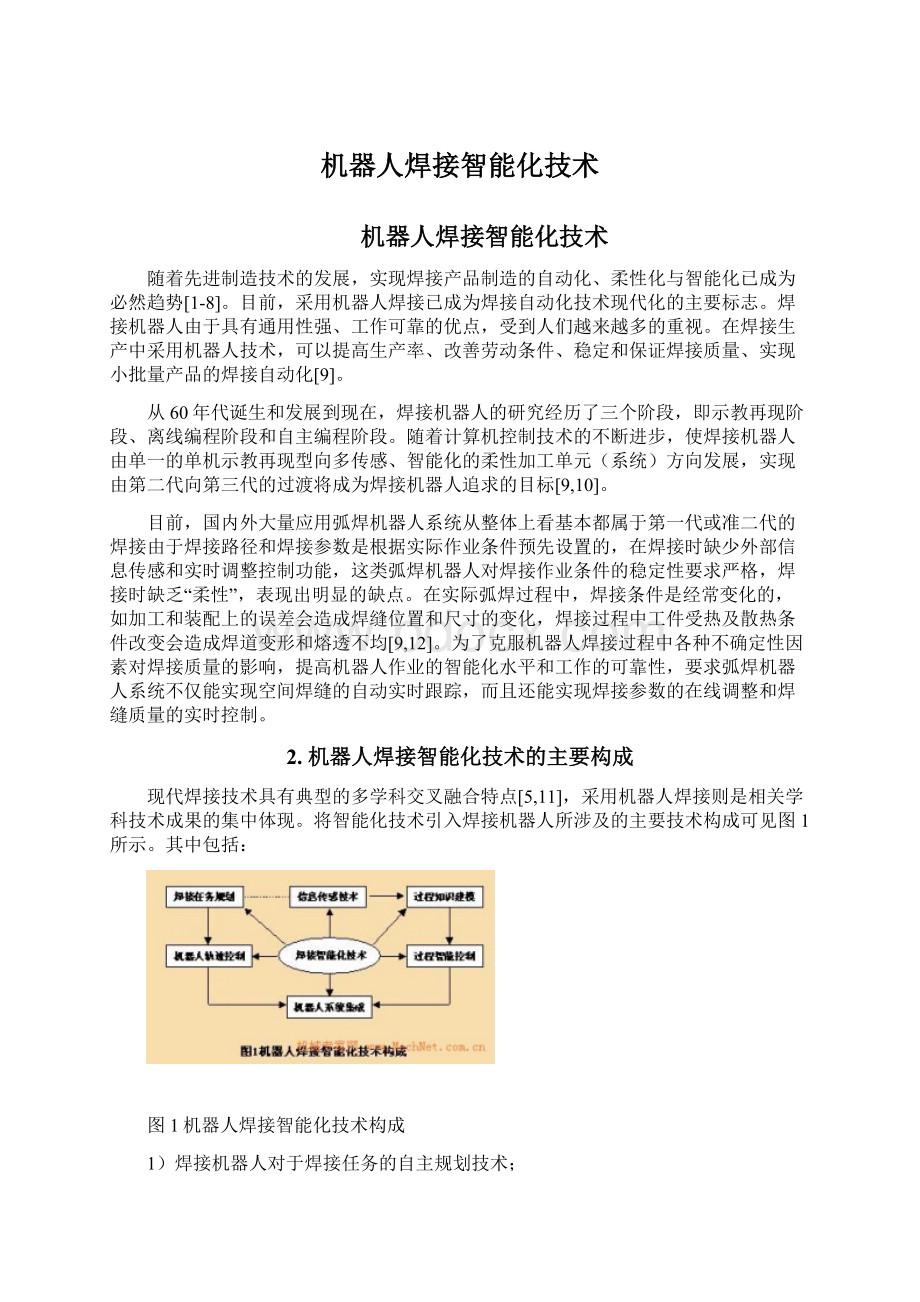
机器人焊接智能化技术
机器人焊接智能化技术
随着先进制造技术的发展,实现焊接产品制造的自动化、柔性化与智能化已成为必然趋势[1-8]。
目前,采用机器人焊接已成为焊接自动化技术现代化的主要标志。
焊接机器人由于具有通用性强、工作可靠的优点,受到人们越来越多的重视。
在焊接生产中采用机器人技术,可以提高生产率、改善劳动条件、稳定和保证焊接质量、实现小批量产品的焊接自动化[9]。
从60年代诞生和发展到现在,焊接机器人的研究经历了三个阶段,即示教再现阶段、离线编程阶段和自主编程阶段。
随着计算机控制技术的不断进步,使焊接机器人由单一的单机示教再现型向多传感、智能化的柔性加工单元(系统)方向发展,实现由第二代向第三代的过渡将成为焊接机器人追求的目标[9,10]。
目前,国内外大量应用弧焊机器人系统从整体上看基本都属于第一代或准二代的焊接由于焊接路径和焊接参数是根据实际作业条件预先设置的,在焊接时缺少外部信息传感和实时调整控制功能,这类弧焊机器人对焊接作业条件的稳定性要求严格,焊接时缺乏“柔性”,表现出明显的缺点。
在实际弧焊过程中,焊接条件是经常变化的,如加工和装配上的误差会造成焊缝位置和尺寸的变化,焊接过程中工件受热及散热条件改变会造成焊道变形和熔透不均[9,12]。
为了克服机器人焊接过程中各种不确定性因素对焊接质量的影响,提高机器人作业的智能化水平和工作的可靠性,要求弧焊机器人系统不仅能实现空间焊缝的自动实时跟踪,而且还能实现焊接参数的在线调整和焊缝质量的实时控制。
2.机器人焊接智能化技术的主要构成
现代焊接技术具有典型的多学科交叉融合特点[5,11],采用机器人焊接则是相关学科技术成果的集中体现。
将智能化技术引入焊接机器人所涉及的主要技术构成可见图1所示。
其中包括:
图1机器人焊接智能化技术构成
1)焊接机器人对于焊接任务的自主规划技术;
2)焊接机器人的运动轨迹控制技术;
3)焊接动态过程的信息传感、建模与智能控制技术;
4)机器人焊接系统的集成与控制,将上述焊接任务规划、轨迹跟踪控制、传感系统、过程模型、智能控制等子系统的软硬件集成设计、统一优化调度与控制,涉及焊接柔性制造系统的物料流、信息流的管理与控制,多机器人与传感器、控制器的多智能单元与复杂系统的控制等。
下面对以上相关方面的主要技术研究与发展现状分别作简要叙述。
3.机器人焊接任务自主规划技术[13-16]
如前所述,国内外弧焊机器人多属示教--再现型,它无法满足焊接生产日益复杂的需要,还存在许多问题有待研究。
有关弧焊机器人的研究逐步向自主化过渡,出现了弧焊机器人的离线编程技术,一个较为完整的弧焊机器人离线编程系统应包括焊接作业任务描述(语言编程或图形仿真、操作手级路径规划、运动学和动力学算法及优化、针对焊接作业任务的关节级规划、规划结果动画仿真、规划结果离线修正、与机器人的通讯接口(downloading、利用传感器自主规划路径及进行在线路径修正等几大部分组成。
其关键技术通常包括视觉传感器的设计以及焊缝信息的获取问题、规划控制器的设计问题。
在1987年的自动化及机器人焊接国际会议上,专家对离线编程的发展进行了总结,其中最有代表性的工作是WRAPS系统。
K.H.Goh等人在一个焊接工作站FANUC/WESTWOOD上建立了基于专家系统的焊接机器人自适应离线编程和控制系统—WRAPS,它包括焊接数据库、离线编程、计算机仿真和焊接专家系统。
它还配有视觉传感器进行焊前接头检测和焊后缺陷检测,从而构成了一个完整的专家焊接机器人系统。
国内哈工大研究人员对焊接机器人的无碰路径规划、具有冗余度弧焊机器人自主规划以及焊接工艺参数联合规划问题的研究工作[14-16],设计开发了离线规划与仿真系统模块结构如图2所示。
图2离线规划及仿真系统的结构
弧焊机器人规划系统都包含了CAD输入系统、焊接专家系统、自主规划系统以及模拟仿真系统等。
从更广泛的意义上讲,一个更完善的弧焊机器人规划系统应该还包括反馈控制系统、焊前传感系统以及焊后检测系统。
4.机器人焊接的焊缝跟踪与导引技术
就机器人焊接作业而言,焊接机器人的运动轨迹控制主要指初始焊位导引与焊缝跟踪控制技术。
在弧焊机器人的各种应用领域,适应能力都是影响焊接质量和焊接效率的最重要因素。
弧焊机器人的适应能力即采用从焊接工件检测到的传感器的输入信号实时控制和修正机器人的操作,以适应变化了的焊接条件和环境。
瑞典和美国公司曾先后研制出激光扫描和结构光视觉传感器用于焊缝跟踪系统。
国内哈工大的吕伟新、张炯博士研制了基于激光扫描和高性能线阵CCD敏感器的视觉系统,见图4,实现实时视觉控制[13]。
在初始焊位机器人视觉导引技术研究方面,吕伟新博士基于激光扫描视觉系统,设计了局部搜索算法,实现了对一定工件焊缝特征在一定范围的自主导引[13]。
郭振民和李金泉分别采用视觉伺服和图象识别技术探讨了机器人焊接初始焊位导引和焊缝识别与实时跟踪问题。
5.焊接熔池动态过程的视觉传感、建模与智能控制技术
机器人焊接的高质量关键在于实现对于焊接动态过程的有效精确的控制。
由于焊接过程的复杂性,实践表明经典的控制方法有效性受到较大的限制。
受熟练焊工操作技艺的启发,近年来,模拟焊工操作的智能控制方法已被引入焊接动态过程,主要涉及熔池动态视过程的视觉传感、建模与智能控制。
5.1焊接过程的传感技术
焊接过程的传感,是实现焊接过程质量控制的关键环节。
未来焊接发展的趋势是焊接自动化、机器人化及智能化,而传感技术是这一发展中最重要的部分。
焊接传感器按其使用目的可分为测量和检测操作环境、检测和监控焊接过程两大类。
在传感原理方面,主要分为声学、力学、电弧、光学传感等。
声学传感器主要用于GMAW过程熔滴过渡的检测、等离子穿孔焊等。
力学传感主要指近年来发展起来的熔池振荡法。
电弧传感器由于直接检测电弧自身的特性(电流,弧压,不需要外加传感器以及外加传感器所需的保护和去噪装置,使应用变得简单。
目前的应用领域主要是焊缝跟踪和熔敷控制。
与其它传感方法相比,光学传感器不与焊接回路接触,信号的检测不影响正常焊接过程,是将来最有发展前景的传感技术之一。
利用焊接区的红外热辐射传感焊接过程信息是光学传感中一种自成体系的方法,这方面的研究成果也较多[16]。
5.2焊接熔池的视觉传感
对于焊接过程,直接视觉是一种最好的非接触式传感形式。
直接视觉传感技术的主要优点是不接触工件,不干扰正常的焊接过程,获取的信息量大,通用性强。
并且由于它可以得到焊接过程动态熔池的二维或三维信息,与其它焊接过程信息检测方法相比,这种方法检测到的熔池信息直接反映焊接过程熔化金属的动态行为,更适合焊接过程的质量控制。
直接视觉传感在焊接中的应用包括离线确定被焊工件的位置;在线补偿由于固定精度、机器人各部分的容差、焊接过程中的焊件变形引起的焊接路径偏差;焊接过程控制中的焊接接头和熔池几何形状的实时传感;熔滴过渡形式的监测等。
近年来,随着计算机视觉技术的发展,利用机器视觉正面直接观察焊接熔池,通过图象处理获取熔池的几何形状信息对焊接质量进行闭环控制,已成为重要的研究方向[17-21]。
根据视觉检测系统中成像光源是辅助光源还是焊接区自身产生的光源,直接视觉检测系统可分为主动式和被动式两大类。
(1)主动式直接视觉传感
为了减小弧光对图象质量的影响,主动式直接视觉检测方法采用激光等辅助光源对焊接区进行人工照明,以提高图象的质量。
由于激光具有单波长,方向性好,相干性好等特点,所以采用激光作为辅助光源可以获得较清晰的图象。
主动视觉由于其所需设备较为昂贵,系统较为复杂,常常限制了其应用推广。
这里不作详细介绍。
可见文[14,15]的参考文献。
(2)被动式直接视觉传感
目前作为焊接过程视觉图象传感的一种实用技术,研究较多的是不另加辅助光源,而是利用弧光本身照明焊接区,即被动式直接视觉检测方法。
对被动式直接视觉传感较为深入的研究起步于八十年代中期,国内外研究工作者曾直接利用电弧光照射熔池前方的工件间隙获取焊接区焊缝信息,根据熔池前方不同远近处电弧光强度的闪烁来实现焊接过程中的焊缝跟踪;利用带有CCD摄像机的微型计算机控制系统对脉冲MIG/MAG焊熔池行为进行了观察和控制的研究;美国Ohio大学开发了一套放置在焊炬内部与电极同轴观测焊接熔池的集成化视觉传感系统,在TIG焊熔池观察和MIG焊焊缝跟踪等方面进行了初步的研究。
文献[19]设计了熔池正反两面视觉图象同时同幅传感系统图3,获得了脉冲GTAW熔池正反两面的清晰图象图4,并对图象二维特征尺寸提取进行了较深入的研究。
文献[21]在上述系统的基础上,获取了脉冲GTAW填丝熔池图象图5。
并对图象进行了三维形状特征恢复的处理算法研究。
文献[19-21]的结果可以认为是近期计算机视觉传感技术在焊接熔池动态过程中的较为系统和成功应用研究工作。
a凸出型b下塌型
图5熔池正面图象类型区分
5.3焊接熔池动态过程的建模
由于焊接熔池动态过程的非线性、不确定性、时变性和强耦合性,采用传统的过程建模方法建立的数学模型不可能作为有效的可控模型,这也是长期以来焊接过程控制成为困扰着焊接界和控制界的一大难题的主要原因。
目前认为,对焊接熔池动态过程的建模方法一般有如下几种:
(1基于对焊接熔池金属热传导理论推导的解析数学模型,这种模型一般是由若干偏微分方程组描述,与实际过程偏差较大,最主要的问题是难以用于焊接过程控制系统设计。
一般只用于焊接热过程的数值模拟与分析;
(2采用经典或现代控制理论的系统辨识方法获得的数学模型,如传递函数、差分方程等形式。
一般可用于限定范围的焊接过程实时控制;
(3基于神经网络逼近理论的人工神经网络建模方法获得焊接过程的神经网络模型,这种建模方法对过程的知识要求较少,通常只根据过程的输入输出数据就可以进行网络模型的学习,得到的模型便于系统的在线学习与控制;
(4基于模糊集合、粗糙集合理论的知识建模方法,这种方法可以借助于焊工经验,也可以直接基于实验数据测量的处理提取知识规律,给出以人类知识形式描述的模型,有助于对焊接过程变化规律的理解和智能系统的应用。
文献[22]对脉冲GTAW熔池动态过程传统数学模型进行了辨识与分析。
文献[20]对脉冲GTAW熔池动态过程进行了模糊逻辑和神经网络的建模方法研究,给出了相应的模型如图所示,并验证了模型用于过程实时控制的有效性。
1)脉冲GTAW对接过程模糊控制规则的提取[20]:
模糊控制规则是模糊控制系统设计的基础.控制对象模糊控制规则的提取属于模糊系统辨识问题,文[20]采用C-均值动态聚类算法来提取脉冲GTAW对接过程模糊控制规则。
选取脉冲GTAW对接过程的被控变量为熔池反面最大熔宽,控制量为脉冲占空比,根据过程动态实验结果[20],采用C-均值动态聚类方法提取模糊控制规则如表1:
表1脉冲GTAW对接模糊控制规则
NB
NM
NS
ZO
PS
PM
PB
NB
PB
PB
PB
PM
PS
ZO
ZO
NM
PB
PB
PM
PM
PS
ZO
ZO
NS
PB
PM
PM
PS
ZO
NS
NS
ZO
PM
PM
PS
ZO
NS
NM
NM
PS
PS
PS
ZO
NS
NM
NM
NB
PM
ZO
ZO
NS
NM
NM
NB
NB
PB
ZO
ZO
NS
NM
NB
NB
NB
2)脉冲GTAW熔池背面熔宽神经网络模型BNNM[19],其输入向量包括当前时刻熔池正面最大熔宽Wfmax(t和最大半长Lfmax(t以及工艺参数等17个输入参数,模型的输出为熔池反面最大宽度Wbmax(t。
确定BNNM模型的隐含层处理单元个数为24。
所得的BNNM模型结构如图6所示,图7是训练样本的期望输出值与B