设备稼动率一般是多少 设备稼动率Word格式文档下载.docx
《设备稼动率一般是多少 设备稼动率Word格式文档下载.docx》由会员分享,可在线阅读,更多相关《设备稼动率一般是多少 设备稼动率Word格式文档下载.docx(13页珍藏版)》请在冰豆网上搜索。
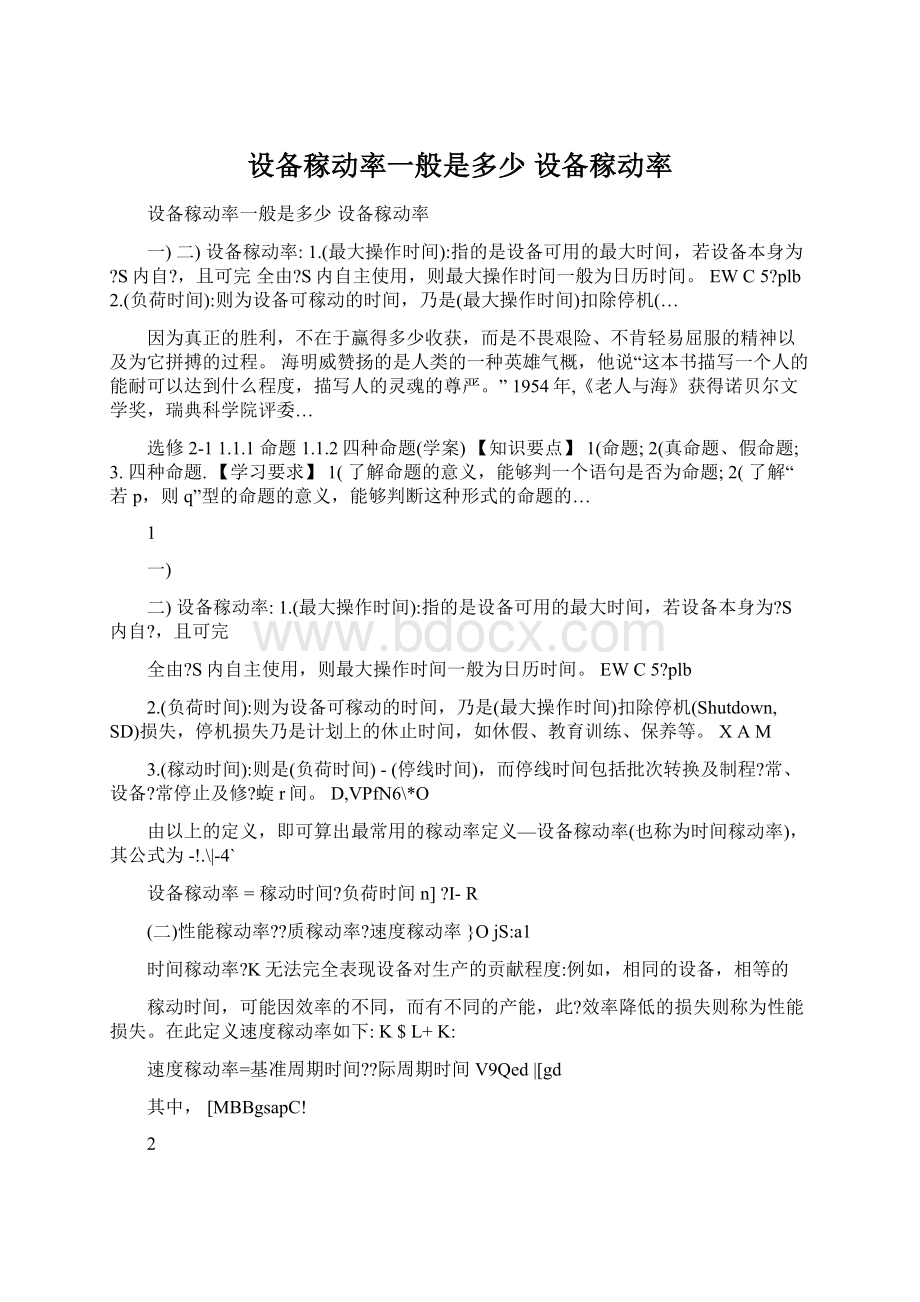
质稼动率?
速度稼动率}OjS:
a1
时间稼动率?
K无法完全表现设备对生产的贡献程度:
例如,相同的设备,相等的
稼动时间,可能因效率的不同,而有不同的产能,此?
效率降低的损失则称为性能损失。
在此定义速度稼动率如下:
K$L+K:
速度稼动率=基准周期时间?
际周期时间V9Qed|[gd
其中,[MBBgsapC!
2
基准周期时间:
设备原设计产出单位产量所需的时间。
z-Q
G02
际周期时间:
目前设备?
际产出单位产量所需的时间。
?
K定义?
质稼动率与性能
稼动率如下:
]$Z_T’
质嫁动率=生产量*?
际周期时间?
稼动时间G7pV>
性能稼动率=速度稼动率*?
质稼动率R5?
G#0
性能稼动时间=稼动时间*性能稼动率=稼动时间-性能损失时间&
yAn其中性能损失包括速度低落的损失与短暂停机的损失。
由以上定义可知,若性能
稼动率变小,则可判定生产相关设备的效率降低。
{)&
n7-Y/]
(三)价值嫁动时间与设备总合效率#4Cok性能稼动时间表示设备产出产品的时间,但无法表示设备产出良率的好坏,因此
定义「价值稼动时间」?
肀硎菊嬲?
墚a出良品的有价值时间,其定义如下:
K9D,U8r
价值稼动时间=性能稼动时间*良品率c84-TQ
而设备的有效使用程度则以「设备总合效率」?
砼卸ǎ?
涠
x如下:
VfLb!
设备总合效率=时间稼动率*性能稼动率*良品率
3
(一)想办法缩短换线时间,如果你的产品属于多产品少批量的话.换线时间将成为
影响稼动率的杀手.1.提前备料,如果是Panasert及Fuji这类转塔式的机器的话,你可以在另一个FeederBank先装料.2.换线前技术人员需把下一个产品的程序先准备好.3.换线时人员的分配,如果一条线多机的话,每台机最好有一个技术人员.{\G]&
(
(二)生产过程中,提前备料尤为重要.作业人员要主动查看哪些材料快用完了,要提
前把料上到备用的Feeder上,当停机时马上把用完料的Feeder取下,把上好料的
Feeder换上.如果是长批量的产品,而你的料又不多于一个FeederBank的Slot数的
话,最好两个FeederBank上都放同样的料,把机器设置为自动切换模式,缺料时,机器会自动切换到另一个FeederBank,然后作业换料,不影响停机时间.OZRuB0ei
(三)管理,分为现场作业员管理和设备管理.这就见仁见智了/
在生产过程中,大家如何去优化生产线呢,也许各有各的招,各有各的办法,是
否大家可以拿出来和大家分享一下,这里是小弟的一点资
4
料,以求更多良策良方。
生产线的优化
如何优化生产线?
1.优化生产线第一站的作业时间,及多久放一片板子,此为满足生产计划量所必
须的投入cycle时间。
但在实际上,瓶颈站的作业时间必然大于第一站,第一站一定不是瓶颈站,所以
第一站不一定会完全依要求的cycle时间去投入,因为瓶颈站已脱拖慢他的速度,故从现场管理者的角度来看,要确实要求第一站作业者依规定速度投入。
输送带的速度也可反推算出日产量,下面为输送带速度的公式:
输送带的pitch时间=整日的上班时间/日产量*(1+不良率)
输送带的速度=记号间隔距离/输送带的pitch时间
所谓记号间隔距离,在皮带线上所做的记号间的距离,希
5
望作业者依记号流经的
速度完成作业并放置在皮带线上;
但炼条线并没有做记号,就以板子的长度当做
记号间隔距离。
为何要用输送带?
除了运送物品外,还有半强制作业者依计划完成作业的功能,但不是一味地加快去试试看,而应依上述公式去计算求得。
2.观察那一站是瓶颈站:
I.永远忙个不停的站
II.老是将板子往后拉的站
III.从该站开始,原本一片接着一片的板子,中间出现了间隔
上面三点是目视就可察觉的,再来就是用秒表量,作业时间是所有站中最长的。
瓶颈站的作业时间就变成了整条线实际产出的cycle时间,而日产量公式如下:
6
日产量=实整日的上班时间/际cycle时间
故现场干部只要减少其作业时间,就可明显提升产量,如将零件拿一些给别站做、使用治工具以节省动作、改善作业域的配置等等。
但在解决瓶颈站后,可能会出
现新的瓶颈站,所以又要对此新的瓶颈站进行改善,因此持续盯着瓶颈站改善,整条线的效率就会日日提升。
3.观察最后一站收板子的cycle时间,也就是实际产出的cycle时间,这站的cycle
时间必相等于瓶颈站。
从这站可推算出这条线的效率如何,公式如下:
效率=投入cycle时间/实际cycle时间=第一站的作业时间/最后一站的作业时间
当然也可用瓶颈站的作业时间来算,不过观察最后一站总是较简单、实际。
在线上的在制品数量就等于:
7
(最后一站的作业时间-第一站的作业时间)*(整日的上班时间/最后一站的作业时间)
在制品太多表示容易发生问题:
所需空间大以容纳在制品、品质易有问题、东西
遗失机会大,物料管理不易。
从这可看出干部对「物」的管制能力。
4.稼动率的观察
稼动率=在作业的时间/整日的上班时间
所谓稼动就是有效的在工作,作业者坐在位子上并不表示他有在工作,有在工作
才能做出产品来,所以要观察作业者在作业的时间。
但在实妹上,不可能全天对每个作业者进行测量,所以有种「工作抽查」的手法来
仿真测量,其实说穿了就是不时去看作业者在做什么,干部在巡视现场时,总会
看看作业者在做什么,如果常看到某人在做事,就会认为他很好,反之就不好,这就是「工作抽查」的基本概念,以「观
8
察次数」取代「观测时间」。
从这可看出干部对「人」的管制能力。
5.作业者坐在位子上并不表示他有「认真」在工作,所以最后就是观察每一个作
业者的作业速度,速度是一个很抽象的概念,光从目视很难来比较跟量化,所以
在心里建立起一个标准速度,快过它就算好,动作精简、固定而有节奏地进行,往往有较好的作业速度,反之不佳,如此来观察就比较简单。
不过不是快就是好,其动作必须是「有附加价值」的,所以还要看其动作是否简单扼要,所以要求「动作经济原则」的观念,简单地说,人类手部的动作可分为移动、握取、放开、前置、组立、使用、分解,还有一种心理的「精神作用」,其中严格来说只有两种动作有附加价值:
组立、使用,所以在能满足生产要求的条件下,尽量排除或简化其它的动作。
其原则如下:
I.移动:
使物料自动到达所要的位置、缩短移动距离、减少需移动物品的重量、
移动路径周围避免有东西会妨碍移动、让料盒斜置以缩短
9
绕过边缘的距离等。
II.握取:
料盒里的物料尽可能整齐排放,不要杂乱堆积、不方便拿取的东西能先
预留握取的空间等。
III.前置:
同握取一样,料盒里的物料尽可整齐排放,不要杂乱堆积等。
IV.组立:
以治工具代替手作业等。
V.使用:
使机械全自动化等。
VI.精神作用:
利用机械取代人为判断、减少作业者目光的移动等。
GQAL1.1钱在哪里
企业经营的最终目的,就是要获取最大的利润。
用什么样的方法来达到这个目的,就成为经营上最重要的课题。
每一个人都知道,将售价减去成本就是利润来源,所以,要增加利润,就必须提高售假货降低成本。
我们可以将售价、成本及利润用数学的公式便显出来:
(A)售价=成本+利润
10
(B)利润=成本-售价
(C)成本=售价-利润
就数学的意义来说,以上三个公式是完全相同的。
但就企业经营的思想来说,确实打不相同。
一下举例说明。
]
第(A)式的例子是:
生产的成本是100元,利润定为成本的20%,即20元,售价就定为120元。
此种思想称之为“成本主义”。
这种产品大都属于独占性的商品,消费者没有选择的余地,要不要随您变,也就是所谓的卖方市场,这种市场未来建越来越小。
第(B)式的例子是:
商品的售价是100元,现在的成本是90元,那么利润就是10元。
售价若降低至95元,但是成本仍在90元,或也降低到88元,利润就都跟着降低。
利润取决于市场价的高低。
此种思想方式称之为“售价主义”
第(C)式的例子是:
公司的目标利润是20元,现在是产的价格是100元,那么目标成本就是80元。
如果市场的售价降至90元,但目标利润仍是20元,因此必须加倍努力将目标成本降到70元。
这种以营利为目标来设定目标成本的思想方式,就称之为“利润主义”。
新生产方式的思想观念一利润主义为推动企业改革的原动力。
在自由竞争的市场下,商品的售价受市场供需的影响,所
11
以受价的高低不是企业自己决定,而是由市场决定的。
这也就是买方市场。
因此,要达到目标利润就必须努力达到目标成本。
就成本而言,简单地说是由材料、人工、设备、与管理成本所构成。
材料是由外面买进来的,也有一定的市场行情,同业间买进相同材料,价格理当不会有太大的差异。
因而,材料的价格也就如商品的售价一样,都不是企业自己可以决定的,而是受到买方市场的影响的。
如此一来,要降低成本,就必须从企业内部所能掌握到的部分,如人工、设备及管理成本作为改善的对象。
简言之,企业要赚取更多的钱,就必须将人工、设备及管理上的浪费彻底消除。
1.2真的不浪费了吗,
消除浪费并不是新的思想,甚至可以说是老生常谈,每一个人几乎从小就接受了节俭、不要浪费的训诫。
所以,说企业要赚钱,就必须先消除浪费,许多人一听,总是觉得没什么新鲜感,当作耳旁风。
然而NPS(新生产技术)里,对浪费的认识,就与以往大有不同。
也就是说,在传统的思想里,认为是不浪费的地方,在NPS的思想里却被认为是浪费。
这是最大的差别。
什么是NPS所认定的浪费呢,他的意义又是如何呢,请看下面的两个图。
12
看看左边这头牛,一直在绕着圆圈走动,但是不能产生有附加价值的动作,只是在活动筋骨而已。
这种不产生附加值的动作,就是浪费。
在工厂里常常可看到搬运、寻找、取放、翻转等等的动作,作业人员们个个汗流浃背,看起来像是很卖力地在做事,但是冷静地想一想,做这些动作都是必需的吗?
会赚钱吗,答案是不会的。
所以,凡是不会赚钱的动作就是浪费。
然后再看另一幅图。
同样的牛,也是一直在走动着,但是没走完一圈就能摸出一些面粉来,把麦子变成面粉,从而提高了产品的价值,因而可以赚取更多的利润。
这就是由附加值的动作。
生产过程的目的就是要将购入的原材料经过人工、设备的投入,而使得物品的价值能更为提高。
对浪费的意义,有了新的认识之后,再回头看看我们自己的工作现场,一定可以发现每一个作业人员的作业,也可以分为又浪费存在的动作以及会产生附加值的动作。
现场管理优良的公司,他的作业里无效的浪费动作所占的比例就少。
反之,则相反。
NPS改善的出发点就是要能在现场中分辨出两种不同动作的所在,然后努力将浪费的动作逐步的消除掉而转变成会赚钱的动作。
1.3劳动改善胜过劳动强化
现场作业员的工作中,包含了不会赚钱的浪费动作以及会
13
赚钱的动作。
改善的重点就是要增加会赚钱的动作的分量。
然而,一般增加的方法,都是采用所谓“劳动强化”的做法。
此种做法没有将现场工作中的浪费排除掉,而只是增加额外的动作,或者只是一味的要求作业员上班的八小时内,做出更多的产品,很容易招致作业员的抵触情绪:
认为已经很卖力地在工作了,还要增加这么多的工作,简直是没有人性,虐待劳工嘛~此时,管理者就的要费尽心思与作业员沟通。
最后如不识字方让步,增加津贴,就是劳资双方造成长久的对立。
这种现象,如果经常发生的话,那么公司早晚会亏本关门的。
从NPS的眼光来看,大部分的工厂里,若以优秀的作业员来说,作业员上班的八小时中,其产生有附加值的动作。
大约只有一小时,其余的七小时可以说都在做浪费的动作。
而普通的作业员其工作的内容或许仅有百分之一左右,才是赚钱的动作,要使公司能够赚钱就必须以“劳动改善”的做法代替“劳动强化”的做法,才能剔除浪费。
“劳动改善”与“劳动强化”是全然不同的东西,劳动强化没有将作业员的浪费剔除,仅是增加作业员的工作量。
浪费仍然存在。
产量增加有限。
与劳动强化相对的就是劳动改善。
劳动改善的做法首先要从派出作业员工作中的浪费开始,通过现场观察,了解作业的整个过程,分辨出动作的差别,然后彻底地将浪费的动作
14
排除掉。
比方说,从2-3米的放置场所,取一张铜片到冲床去做冲压的工作。
往返之间作业员走6米的路。
假如,在工厂里走1米必须花1秒,走6米那就表示浪费了6秒的时间。
这走路的6秒如果能够排除掉,作业员就可以减少走路的体力消耗,感到更舒适,生产量也就自然跟着提高。
这种自然的改善非常的重要,依照这种方法做下去的话,既增加了劳动密度,同时也增加了有附加值的动作。
NPS改善的终极目的就是要赚取更多的利益。
以劳动改善的方式所能获取的利益远大于劳动强化的方式。
所以NPS的改善绝对要以“劳动改善”的方式来进行。
1.4七种浪费
打劳动强化与劳动改善中已提到,NPS强调要排除浪费的动作,但我们必须先认识哪些是无附加价值的浪费动作。
了解它,才能想办法把它消除掉。
就如同我们要打敌人,必先知道谁是敌人,敌人在哪里,对敌人越了解,打起仗来就越有胜算。
NPS将所有浪费归纳成七种:
(1)等待的浪费;
(2)搬运的浪费;
(3)不良品的浪费;
(4)动作的浪费;
(5)加工的浪费;
(6)库存的浪费;
(7)制造过多(早)的浪费。
其中
(1)~(5)浪费,一般说起来比较容易被了解与接受,第(6)与(7)种浪费就是NPS与众不同的看法与见解了。
15
以下依序加以介绍。
七种浪费之一:
等待的浪费
等待就是闲着没事,等着下一个动作的来临,这种浪费是无庸置疑的。
造成等待的通常有;
作业不平衡、安排作业不当、待料、品质不良等。
另有一种就是“监视机器”的浪费,有些工厂买了一些速度快、价格高的自动化机器,为了使其能正常运转或其他原因,例如:
排除小故障、补充材料等等,通常还会另外安排人员站在旁边监视。
所以,虽是自动设备,便仍需人员在旁照顾,特称之为“闲视”的浪费。
七种浪费之二:
搬运的浪费
大部分人皆会主同搬运是一种无效的动作,也有人会认为搬运是必须的动作,因为没有搬运,如何做下一个动作,笔者曾经问过很多人,都有这种想法。
正因为如此,便有很多人默许它的存在,而不设法消除它。
有些人想到用输送带的方式来克服这种方式仅能称之为花大钱减少体力的消耗,但搬运本身的浪费并没有消除,反而被隐藏了起来。
搬运的浪费若分解开来,又包含放置、堆积、移动、整理等动作的浪费。
通常造成搬运浪费主要是由于工厂布置采用批量生产、依工作站为区别的集中的水平式布置所致。
缺乏NPS流线生产的观念。
七种浪费之三:
不良品的浪费
16
产品制造过程中,任何的不良品产生,皆造成材料、机器、人工等的浪费。
任何修补都有是额外的成本支出。
NPS的生产方式,能及早发掘不良品,容易确定不良的来源,从而减少不良品的产生。
七种浪费之四:
动作的浪费
要达到同样作业的目的,会有不同的动作,哪些动作是不必要的呢,是不是要拿上、拿下如此频繁,有没有必要有反转的动作、步行的动作、弯腰的动作、对准的动作、直角转弯的动作等,若设计得好,有很多动作皆可被省掉
七种浪费之五:
加工的浪费
在制造过程中,为了达到作业的目的,有一些加工程序是可以省略、替代、重组或合并的,若是仔细地加以检查,你将可发现,又有不少的浪费,等着你去改善。
七种浪费之六:
库存的浪费
NPS大胆地断言:
“库存是万恶的根源”。
这是NPS对浪费的见解与传统见解最大不同的地方,也是NPS能带给企业很大利益的原动力。
NPS中几科所有的改善行动皆会直接或间接地和消除库存有关。
NPS为什么将库存看做是万恶之根源,而要想尽办法来降低它呢,因为库存会造成下列的浪费:
——产生不必要的搬运、堆积、放置、防护处理、找寻等浪费。
17
——使先进先出的作业困难。
——损失利息及管理费用。
——物品的价值会减低,变成呆滞品。
——占用厂房空间、造成多余的工场、仓库建设投资的浪费。
另外,因库存所造成的无形损失绝不亚于上述的有形损失,NPS认为库存会隐藏问题点,而“问题”在NPS中被认为是宝藏,问题如果能不断地被发现解决,则利益便会不断地产生。
库存隐藏问题点,造成下列后果:
——没有管理的紧张感,阻碍改进:
库存量一多,因机械故障、不良产品所带来的不利后果不能马上显现出来,因而也不会产生对策,同样地,换模时间的缩短也永远排不到优先解决之列。
——设备能力及人员需求的误判:
由于库存量的存在,设备能力不平衡时也看不出(库存越多,越不容易看出来)。
人员是否过剩,也无法了解。
到底为什么要有库存量,最大的理由是“怕出问题”——机器故障怎么办,不良品产生怎么办,换模时间太长怎么办,会不会因部分设备出问题,而影响整条生产线式工厂的生产呢,于是乎为了不使影响扩大,库存便成了必需,众多的问题也被隐藏了起来,所有进步、赚钱(发现问题、解决问题就是赚钱)的步调自然变慢了。
18
无怪乎NPS称库存为万恶的根源,绝对不允许它存在,如果现在已经有了库存,也要想尽一切办法,将之降低,力争零库存。
(注:
零库存的“零”并非指数学意义上的“完全没有”的意思,而是指把库存“尽量减到最少的必要程度”。
)
七种浪费之七:
制造过多(早)的浪费
上文提到库存是万恶之根源,而制造过多或提早完成,在NPS中则被视为最大的浪费。
NPS所强调的是“适时生产”,也就是在必要的时候,做出必要数量的必要的东西。
此外都属于浪费。
而所谓必要的东西和必要的时候,就是指顾客已决定要买的数量与时间。
在前面,我们提过售价-利润=成本,而这售价必须是在有顾客需求的前提下才会产生,假设客户只要100个,而每个1元,若我们生产了150个,这售价就不会是150元,因为多余的50个并没有卖出去,仅是变成库存,因此利润也就无从产生,换句话说,多做了是浪费。
而制造过早同样也是浪费,但为什么有很多工厂会一而再地过多与过早制造呢,最大的原因在于他们不明白这是一种浪费,反而以为多做能提高效率,提早做好能减少产能损失。
(不做白不做,机器还不是一样停着,)显然这是一种极大的误解。
认为制造过多与过早能够提高效率或减少产能的损失,是
19
见树不见林的看法,因为真正利润的产生是从售货而来,而不是效率与产能。
为了看到更多的效率与产能制造过多与过早而销售并没增加,仅是增加了库存量,你说这合算吗,
因此,NPS强调,绝无理由制造过多(早),因为:
——它只是提早用掉了费用(材料费、人工费)而已,并不能得到什么好处。
——它也会把“等待的浪费”隐藏起来,使管理人员漠视等待的发生和存在。
——它会自然而然地积压在制品,其结果不但会使制程的时间变长(无形的),而且会使现场工作的空间变大,机器间的距离因此加大,这些在不知不觉中,将逐渐地吞蚀我们的利润。
——它也会产生搬运、堆积的浪费,并使得先进先出的作业产生困难。
以上七种浪费,都是横亘在我们面前的敌人,我们对它了解得越多,将来获得的利益也越多。
对于这七种浪费,绝对不能半信半疑,否则效果便会打折扣。
敌人就是敌人,一定要想尽一切办法消灭它~要知道,消灭它的同时,利益就产生了。
在竞争激烈的环境中,我们要比别人赚取更多的利润,才能够顺利地生存下去。
我们不能有丝毫的浪费。
NPS不但归纳出这七种浪费,在往后的内容里还会详细介绍各种消除浪费的方法。
20
设备稼动率
1.询问观察时间内是否有停机损失、现有稼动率情况、现有稼动率的计算方式(9/29武、姚、
周):
观察时间为10/8-10/21(14天,24H/天);
停机损失为计划休止时间,如休假、教育培训、保养。
计划上的休息时间(如一天工作多久,具体的时间安排,有没有周末休息或节假日休息等)、保养时间(机器多久保养一次,分哪几种保养,怎么保养,责任人是谁)。
武与WBL课课长将此确认,周、姚与机长确认,并将我们的安排、目的与对方说明。
2.对741M/C进行工程分解的确认(9/29姚、周):
排气机与点灯机是否需要分开的确认;
周、姚、机长共同将工程进行分解,确认最终的工程分解情况
3.741M/C的工作状况划分(9/29姚、周):
参考现有机器工作状况的划分情况,制订最终的机器工作状况划分方法。
4、制表(9/29-9/30姚、周):
根据工程的划分、工作状况的划分、工作时间的安排制订跟踪表格及整理分析图表
跟踪表参考以前的机器稼动率统计表,考虑:
开停机的起讫时间,为哪个工程,停机原因,在开机时间内的产能、良品数
整理表参考
21
原因停机时间
故障354
补换材料84
更换部件14
机器调整288
其他152
5.按不同的工程对741M/C的运转与停机情况进行跟踪(10/8-10/21姚、周):
按跟踪表记录统计现状的设备运停情况,产能统计,不良品统计。
期间注意多与机长沟通,针对具体的问题询问他们的改善方案。
时间安排为:
姚8:
00-20:
00,周20:
00-8:
00,14天内无休息日。
6.根据非稼动率找出瓶颈工程:
数据表的形成,整理分析图表的完成,现状工程分析表的完成。
参考整理分析图表的要求找出瓶颈
7.针对瓶颈工程制订改善方案:
改善照眼点
1)设备故障原因检讨、排除;
2)确保材料供应的及时、流畅,减少因待料、补料的停机;