汽车最新暴晒标准Word文档格式.docx
《汽车最新暴晒标准Word文档格式.docx》由会员分享,可在线阅读,更多相关《汽车最新暴晒标准Word文档格式.docx(13页珍藏版)》请在冰豆网上搜索。
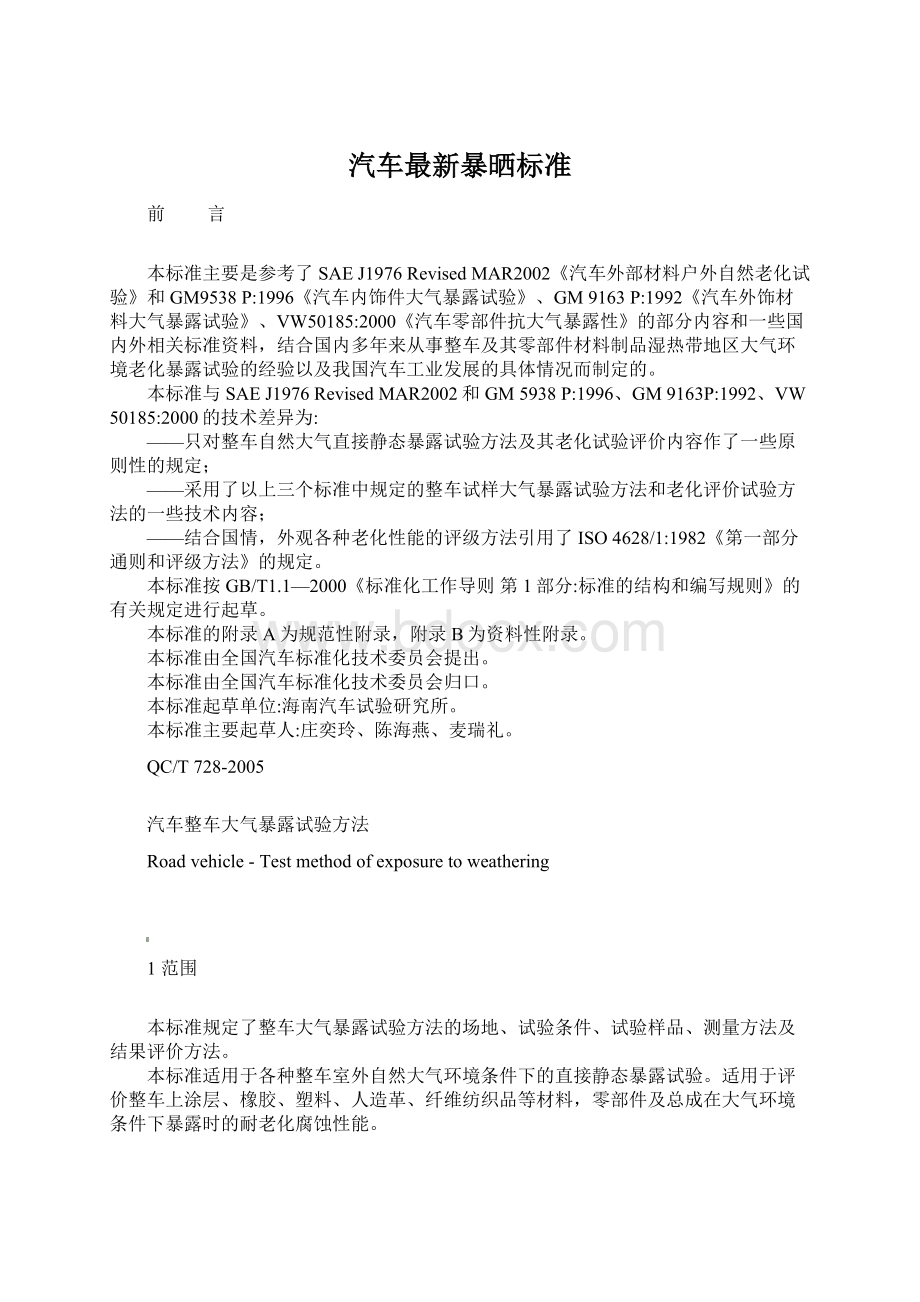
本标准规定了整车大气暴露试验方法的场地、试验条件、试验样品、测量方法及结果评价方法。
本标准适用于各种整车室外自然大气环境条件下的直接静态暴露试验。
适用于评价整车上涂层、橡胶、塑料、人造革、纤维纺织品等材料,零部件及总成在大气环境条件下暴露时的耐老化腐蚀性能。
2规范性引用文件
下列文件中的条款通过本标准的引用而成为本标准的条款。
凡是注日期的引用文件,其随后所有的修改单(不包括勘误的内容)或修订版均不适用于本标准,然而,鼓励根据本标准达成协议的各方研究是否可使用这些文件的最新版本。
凡是不注日期的引用文件,其最新版本适用于本标准。
GB250评定变色用灰色样卡(GB250---1995,idtISO105/A02:
1993)
GB/T1766色漆和清漆涂层老化的评级方法(GB/T1766--1995,neqISO4628—1:
1980)
GB/T3681塑料大气暴露试验方法(GB/T3681—2000,neqISO877:
1994)
GB/T6739涂膜硬度铅笔测定法(GB/T6739---1996,eqvJISK5400:
1990)
GB/T8807塑料镜面光泽试验方法
GB/T9276涂层自然气候曝露试验方法(GB/T9276--1996,eqvISO2810)
GB/T9286色漆和清漆漆膜的划格试验(GB/T9286--1998,eqvISO2409:
1992)
GB/T9754色漆和清漆不含金属颜料的色漆漆膜元20°
、0和85°
镜面光泽的测定(GB/T9754--1988,eqvISO2813:
1978)
GB/T11186涂膜颜色的测定方法[GB/T1186--1989,eqvISO7724:
1984(所有部分)]
GB/T15596塑料暴露于玻璃下日光或自然气候或人工光后颜色和性能变化的测定(GB/T15596--1995,eqvISO4582:
1980)
GB/T16996硫化橡胶暴露于自然气候或人工光后性能变化的评定(GB/T16996--1997,eqvISO4665—1:
1985)
SAEJ1976RevisedMAR2002汽车外部材料户外自然老化试验
3术语和定义
下列术语和定义适用于本标准。
3.1
涂层coatsforautomobile
涂装在汽车各部位表面上的装饰性涂膜或保护性涂膜体系。
3.2
标准样件standardsamplepiece
指在特定环境条件下保存,作为曝晒试验过程中比对评价用的基准参照试样。
3.3
自然气候老化naturalweathering
指试样在室外自然大气环境条件下暴露,受到环境因素的作用发生的各种不可逆的化学和物理变化过程而使其各种性能劣化的总称。
3.4
环境因素ambientfactors
在暴露试验环境中的气象因素与大气环境污染因素的总称。
4原理
将整车试样置于能代表某一气候类型区域的室外自然大气环境条件下进行暴露试验,让其经受阳光、温度、湿度、雨水、氧、臭氧及其他环境因素的综合作用。
按规定的暴露试验期限,定期检测整车用非金属材料制品的外观、力学、电学、化学或其他性能变化和金属材料制品的腐蚀变化,从而评价整车试样耐大气环境老化腐蚀性能及操作使用性能。
整车外观各种老化破坏现象的定义描述、检测项目与评价原则按附录A的规定进行。
5试验条件
5.1暴露场地
5.1.1暴露场地选择
暴露场地应选择在能代表各种气候类型的典型的有苛刻环境气候条件的区域内或在受试产品实际使用的环境条件下建立,也可以按SAEJ1976RevisedMAR2002的有关规定进行选择。
根据气候条件对非金属材料大气老化腐蚀性能的影响来确定,我国的气候可分为六种类型(见附录B)。
注:
特殊需要的工业暴露场应设在厂矿密集区内;
盐雾气候暴露场应设在空气盐分浓的海边或海岛上。
5.1.2标准暴露场地要求
场地应平坦空旷,远离建筑物和树木,周围障碍物与场地边沿的距离至少为该障碍物高度的3倍。
场地附近应无工厂烟囱、通风口或其他能散发大量腐蚀气体和杂质的设施。
最好远离厂矿区和闹市区,或设在该地区主导风向的上方。
场地应保持当地的自然植被状态,不积水,有植物生长则应该经常割短,要求草高不应超过200mm。
根据试验目的要求,也可采用水泥地板,需在报告中注明。
5.2暴露场设备
暴露场内或邻近要求设置气象要素观测和大气介质分析设备,以长期连续观测记录主要的气象要素和定期测定环境周围的大气成分。
环境因素测量仪器要求符合GB/T3681的有关规定或相关国际标准的有关规定。
6试验样品
6.1整车
每种车型至少有一辆样车,根据不同的配置与试验目的也可以是多辆。
要求试验车辆是新开发的产品或是批量生产线上抽取的标准配置的合格产品,并配有随车工具、备胎、灭火器、使用说明书及零部件目录等附件。
6.2标准样件
试验整车要求配备与其上装配是同批生产的合格标准样件。
标准样件要求是单个零部件制品或是特制的标准样件。
标准样件主要包括前(后)保险杠、散热器罩、各种灯具、转向盘、仪表板总成、车标、车内装饰件等或是重点考核的零部件。
6.3标准样件贮存
标准样件要求贮存在空气温度为23℃±
20℃、相对湿度为50%±
5%、气压为86kPa—106kPa的标准环境条件下的避光处,如果不具备该条件也可以贮存在正常的试验条件(即环境空气温度为1O℃~35℃、相对湿度为45%~75%)下的避光处。
注:
标准样件贮存处环境(包含空气)应保持清新、干净,无任何污染物质存在。
7暴露期限
7.1期限设定方法
7.1.1期限设定除考虑试样类型、用途及试验目的外,还要考虑能够正确地掌握试样性能老化的历程。
7.1.2暴露期限设定可以选择以时间为单位(如月、年),但在考核内饰件的光老化性能时,要求选择以试样表面接收太阳辐射量为单位(如MJ/m2);
也可以选择以试样性能变化(如损耗、破坏的程度)到规定的某一极限值为单位。
7.1.3产品研制阶段或生产例行试验要求以试样性能老化下降至规定限值时其所接收的太阳辐射量或经过的时间为期限,产品鉴定或是验收试验至少一年以上,暴露研究试验至少要两年以上。
也可以按SAEJl976RevisedMAR2002的有关规定进行设定。
7.2暴露期限的表示
7.2.1以时间设定期限的时候,原则上取日、月及年为单位。
7.2.2以太阳辐射量为期限时,即以试样表面接收太阳辐射量达到规定的某一数值为单位,这时要明确记录暴露开始的日期及结束日期。
如无特殊规定,以总日射表接收器平面朝正南方、在偏离水平面45°
的透明回火玻璃下,测定出的总太阳辐射量作为暴露整车接收的太阳辐射能量来确定期限。
7.2.3以试样性能变化为期限时,即以达到所规定的变化限值为期限,这时除明确记录暴露开始的日期及结束日期外,还要记录试样所接收的太阳总辐射能量与太阳紫外辐射总能量。
7.3暴露开始日期
7.3.1要求少于一年的暴露期限,为了正确掌握试样各种性能的历时变化,原则上应把暴露开始的日期分为下面两种来实施:
即湿热带气候暴露试验建议以每年的3月或4月开始;
干燥气候的暴露试验推荐以秋季的9月或10月为开始日期。
7.3.2超过一年以上的暴露期限,一般不特别规定暴露试验开始的日期。
8试验程序
8.1试验准备
8.1.1试验样品验收
清洁新到试验样品、晾干,检查装运损伤、装配缺陷与其他表面状态缺陷,做好原始记录,必要时应拍照或摄像记录;
然后对试样进行试验处理,配备标准样件的贮存要求按6.3的规定进行。
8.1.2测量位置的确定
要求颜色、鲜映性、光泽度测量的表面及部件总成,其测量位置要选择在最显眼、接收太阳总辐射能量最多的平面上并用不褪色记号笔做出永久性标记标识,使每次测量位置、方向顺序不变,以保证测量值的准确。
要求测量温度的部件,要在晴天的中午12—15点间用便携式测温仪在不同部位进行多次测量以确定其最高积温点位,然后在其上做出标识作为试验过程中部件的温度测量点。
要求划痕腐蚀、划格附着力与划痕硬度测量的涂层表面,其测量位置要选择在颜色、鲜映性、光泽度测量位置的下部。
注1:
光泽与颜色的测量点位应尽可能靠近或重叠。
注2:
测量点位的确定除按8.1.2的规定外,也可以按客户的要求进行。
8.1.3暴露前检测
试验前按8.4、8.5的要求进行清洁与状态调节,然后根据选择的项目按8.3.2—8.3.8的规定进行检测。
8.1.4划痕处理
如果选择了涂层划痕腐蚀项目,整车投入试验时,应在确定的测量位置划出长为100mm的垂直方向(Y)与水平方向(x)的“+”痕,痕深度为穿过表面涂层到达钣金,并测出“+”划痕的宽度;
也可以按GB/T9276的相关规定进行涂层划痕。
垂直车身板面上的水平划痕从左到右,垂直划痕从上到下;
水平或接近水平车身板面上的水平划痕从左到右,垂直划痕从前到后。
8.1.5温度传感器安装
如果要求温度测量,整车投入试验前,建议在确定的温度测量点上安装热电偶。
软表面试样的热电偶应安装在软表层/填充物叠层的分界面处,即刺穿软表层把热电偶插入至少13mm并使其平行于表面,以确保温度感应点嵌入在分界面内;
其他表面试样的热电偶安装应用如环氧类的耐高温灰色不透明粘合剂粘接在试样表面,必须小心操作以确保热电偶连接点与试样表面接触并被粘合剂覆盖,在保证热电偶粘接到试样表面的前提下,粘接面积应尽量做到最小。
8.2投入试验
8.2.1暴露方式
室外大气暴露试验一般应南北朝向自然放置于暴露场内。
在北半球,试验车的前风挡玻璃朝正南方向;
在南半球,试验车的前风挡玻璃朝正北方向。
为了适应特殊的试验目的,也可以朝向任何方向放置。
8.2.2暴露状态
试验时,要求试验车的所有车门、车窗和通风系统都要紧密关闭,同时要保证每辆试验车之间的放置空间通风自由且不相互遮挡阳光。
试验车的放置距离至少为其相邻车辆高度的3倍。
8.3检测周期与方法
8.3.1检测周期
整车按8.2规定进行暴露后,在整个试验期限中,各种性能变化的检测周期为:
新产品要求暴露初期三个月内,每半个月一次;
三个月至一年内,每月一次;
超过一年后,每三个月一次。
如果是批量生产的鉴定或验收试验,检测的间隔时间可以相对延长即检测次数相对减少。
也可以按试样表面接受一定的总太阳辐射量作为检测周期。
当天气骤变时,应随时检查,如有异常变化现象应做记录或拍照。
8.3.2外观目测检查
如无特殊要求,根据选择的检测周期,在不受阳光直射,自然光线充足、明亮、干燥的地方,按附录A规定的整车外观检测内容进行各种老化现象的目测检查。
检查时可采用5—10倍放大镜,对试样进行观察。
渗析物、长霉、起霜等老化现象的目测检查应在试样清洁前进行预观察。
8.3.3光泽度的测量
根据选择的测量周期,涂层表面光泽度测量按GB/T9754的有关规定进行,也可以按相关光泽仪操作说明进行测量;
塑料表面光泽的测量按GB/T8807的有关规定进行。
整车装饰部件有纹理表面光泽的测量方法是在测量位置上任意标出0°
位,然后从0°
位开始依次顺时针旋转如0°
、180°
和270°
等4个方向进行测量,读取每一测量方向的光泽数据,光泽测量几何角度的选择按GB/T9754或GB/T8807的有关规定进行。
8.3.4颜色与鲜映性(DOI)的测量
根据选择的测量周期,涂层表面颜色的测量按GB/T11186的有关规定选择标准照明体D65和观察者视域角为10°
视场下进行,鲜映性(DOI)或(PGD)值的测量按相关鲜映性仪的使用操作说明进行;
塑料、橡胶表面颜色的测量按GB/T15596、GB/T16996的有关规定进行。
8.3.5涂层划痕腐蚀检测
根据选择的测量周期,观察“十”痕的腐蚀出现时间、状态及腐蚀产物,测量垂直划痕(Y)两侧涂层区域与水平划痕(x)两侧涂层区域的最大腐蚀点间垂直于原始划痕的距离,以mm为单位记录测量数据。
8.3.6涂层铅笔硬度检测
如无特殊要求,规定试验开始时与结束后,按GB/T6739规定的手工操作法测定其铅笔硬度。
也可选用相关的硬度测量仪(如DUR—O—Test)进行测定。
8.3.7涂层附着力检测
如无特殊要求,试验开始时与结束后,按GB/T9286规定进行涂层的附着力划格试验检测。
8.3.8整车操作检查
在暴露试验中,整车每周启动一次并运行40min,运行前后分别对以下功能件进行检查。
a)检查所有电器功能件的工作情况是否正常。
b)检查刮水器、风窗洗涤器、除霜装置、玻璃升降器、门锁、内锁提钮、行李箱门及发动机盖等性能是否正常。
c)检查发动机、变速器、悬挂及转向系统等工作情况是否正常及电池充电性能等。
8.3.9车体温度测量
投放试验后,有温度测量跟踪设备应在温度测量点上安装探头及连接记录仪。
如果不能对选定的温度测量点进行每天跟踪测量,要求每月必须挑选4至5天气温高、太阳辐射强、最好无云彩影响的良好日期进行车体温度测量,测量出选择点的相对最高受热温度。
8.3.10拍照
在试验过程中,要求对出现特殊老化现象的部位及时拍照。
拍照时要求标上标识和日期。
8.4样品清洁
如无特殊要求,试验样品规定每月或每次检测前应进行清洁。
清洁时要求用干净水(即水质:
pH值为6—8,固体含量小于1ppm,硅土小于0.2ppm)和柔软棉布对车辆外表面进行彻底清洗、晾干,用吸尘器清洁车内灰尘及用干净柔软湿棉布清洁内饰件及玻璃表面;
若涂层试验表面用干净水没有清洗干净,可用中性汽车(液体)清洁剂清洗后再用干净水清洗干净,晾干。
清洁时注意保护试验表面不受任何污染与损伤。
在清洁过程中,不要清除任何的老化产物如粉化、渗析物、长霉、起霜等。
8.5状态调节
试验样品清洁、晾干后一般要求在标准环境状态条件下停放24h以上,才能进行各项外观性能的检测。
如果没有标准环境状态调节试验室,也可以在常规试验条件下停放24h以上。
8.6环境因素的监测
整车投入曝晒试验的同时,要求按GB/T3681或相关国际标准的有关规定记录所有的气象条件因素和会影响试验结果的大气环境因素。
9数据处理
9.1涂层外观老化
9.1.1光泽
以试验前测出的光泽度为原始值。
按式
(1)计算出其在各个暴露阶段的光泽损失率即失光率(%)。
失光率(%)=(Ao-Ai)/Ao×
100……………………………………
(1)
式中:
Ao——老化前光泽测定值;
Ai——老化后光泽测定值。
9.1.2颜色与鲜映性(DOI)
以试验前测出每个试样的色空间坐标L*、a*、b*和c*的平均值为原始值,按式
(2)计算其在各试验时间的色差
三值,根据需要也可以按式(3)计算其在各试验时间的色相差ΔH*值;
测量点位鲜映性值在各个试验阶段的变化率(%)按式(4)计算。
鲜映性值变化率(%)=(Po-Pi)/Po×
Po——老化前的(DOI)或(PGD)值;
Pi——老化后的(DOI)或(PGD)值。
9.1.3外观目测结果
按GB/T1766的有关规定对粉化、变色、失光、裂纹、长霉、沾污、斑点、生锈、泛金、脱落、起泡等外观老化现象进行等级评定表示。
也可以根据附录A.3的有关规定进行表示。
9.1.4划痕腐蚀检测结果
划痕涂层区域最大腐蚀深度的算法如式(5)和式(6)所示:
hY=y-y0…………………………………………………………………………(5)
hX=x-x0…………………………………………………………………………(6)
hY、hX——垂直和水平划痕的最大腐蚀深度,mm;
y、x——垂直和水平划痕两侧涂层区域最大腐蚀点间的垂直距离;
mm;
y0、X0——垂直和水平划痕口原始宽度,mm。
9.1.5涂层硬度检测结果
按GB/T6739的规定进行硬度测量结果表示。
9.1.6涂层划格检测结果
涂层划格试验结果按GB/T9286的有关规定进行表示。
9.2橡胶、塑料、人造革纤维和纺织品等外观老化结果
仪器测量结果表示:
光滑表面的失光率按式
(1)计算,有纹理表面的失光率按式(7)计算;
颜色结果表示与9.1.2同,目测结果按GB250的有关规定表示;
其他外观老化现象,按附录A的有关规定表示。
根据要求也可按GB250、GB/T 16996、GB/T15596的有关规定表示。
失光率(%)=(Bo-Bi)/Bo×
100……………………………………………(7)
Bo——老化前4个方向的光泽平均值;
Bi——老化后4个方向的光泽平均值。
9.3整车使用操作检测结果
对功能件的破坏程度推荐用“轻微、中等、严重与完全失效”等术语描述。
9.4整车车体温度测量结果
绘制每个测量点的月/年最高温度曲线与车体空气的月/年最高温度曲线,或统计整个暴露试验过程中每个测量点积热的最大温度值,以℃表示。
9.5环境因素的监测结果
按GB/T3681或相关国际标准的规定对监测的各种环境因子数据进行结果统计与表示。
10结果评价
10.1涂层外观性能老化评定
根据试验结果按GB/T1766的有关规定进行涂层外观各性能老化等级的评定,划痕腐蚀、硬度、划格附着力等试验结果按相关标准或附录A的有关规定进行等级评定。
10.2橡胶、塑料、人造革纤维和纺织品等外观老化评定根据试验结果按附录A或GB/T16996、GB/T15596的有关规定进行各材料试样外观性能老化等级的评定。
附录A
(规范性附录)
老化定义、检测项目及评价原则
A.1老化定义
暴露试验车辆常出现的老化现象及其定义详见表A.1。
表A.1各种老化现象的定义描述
A.2整车外观检测项目
暴露试验整车外观变化检测项目详见表A.2。
表A.2暴露试验车辆外观检测内容表
A.3老化评价原则
A.3.1老化分级
试样外观老化变化分级均采用统一的方法,即以0—5的数字级别来表示老化程度。
“0”表示无老化,“5”表示严重老化,必要时可采用中间的半级来对所观察到的老化现象做更详细的记录。
A.3.2老化程度、数量、大小的评定
A.3.2.1评定试样外观可见的均匀老化,用老化的程度评级,详见表A.3。
表A.3均匀老化程度评定表
A.3.2.2评定试样外观非连续性或局部不规则的老化现象,按试验有效面内出现老化的破坏密度程度进行评级,详见表A.4;
对一些有大小意义的分散老化现象应同时以老化大小程度(即最大老化处大小)进行评级,老化大小表示的评级原则,详见表A.5。
表A.4分散老化密度评定表
表A.5分散老化大小评定表
A.3.3等级表示方法
表示方法应包括下列内容:
老化类型:
均匀老化程度等级按表A.3;
分散老化密度等级按表A.4。
若表示老化大小等级按表A.5,则在括号内注明。
如:
均匀老化中的变色等级表示——变色:
2,即表示试样外观2级变色。
分散老化中的起泡等级表示——起泡:
3(S2),即表示试样表面起泡密度为3级,起泡大小为2级。
应在等级的前面标出老化部位名称。
如发动机盖外表面涂层失光2级;
顶篷中间外表面涂层生锈3(S4)级或左前
门塑料护板边缘涂层脱落2(S3)级。
附录B
(资料性附录)
我国主要的气候类型
我国主要的气候类型详见表B.1。
表B.1我国主要的气候类型