十一五期间医药行业优秀科技创新案例Word文档下载推荐.docx
《十一五期间医药行业优秀科技创新案例Word文档下载推荐.docx》由会员分享,可在线阅读,更多相关《十一五期间医药行业优秀科技创新案例Word文档下载推荐.docx(8页珍藏版)》请在冰豆网上搜索。
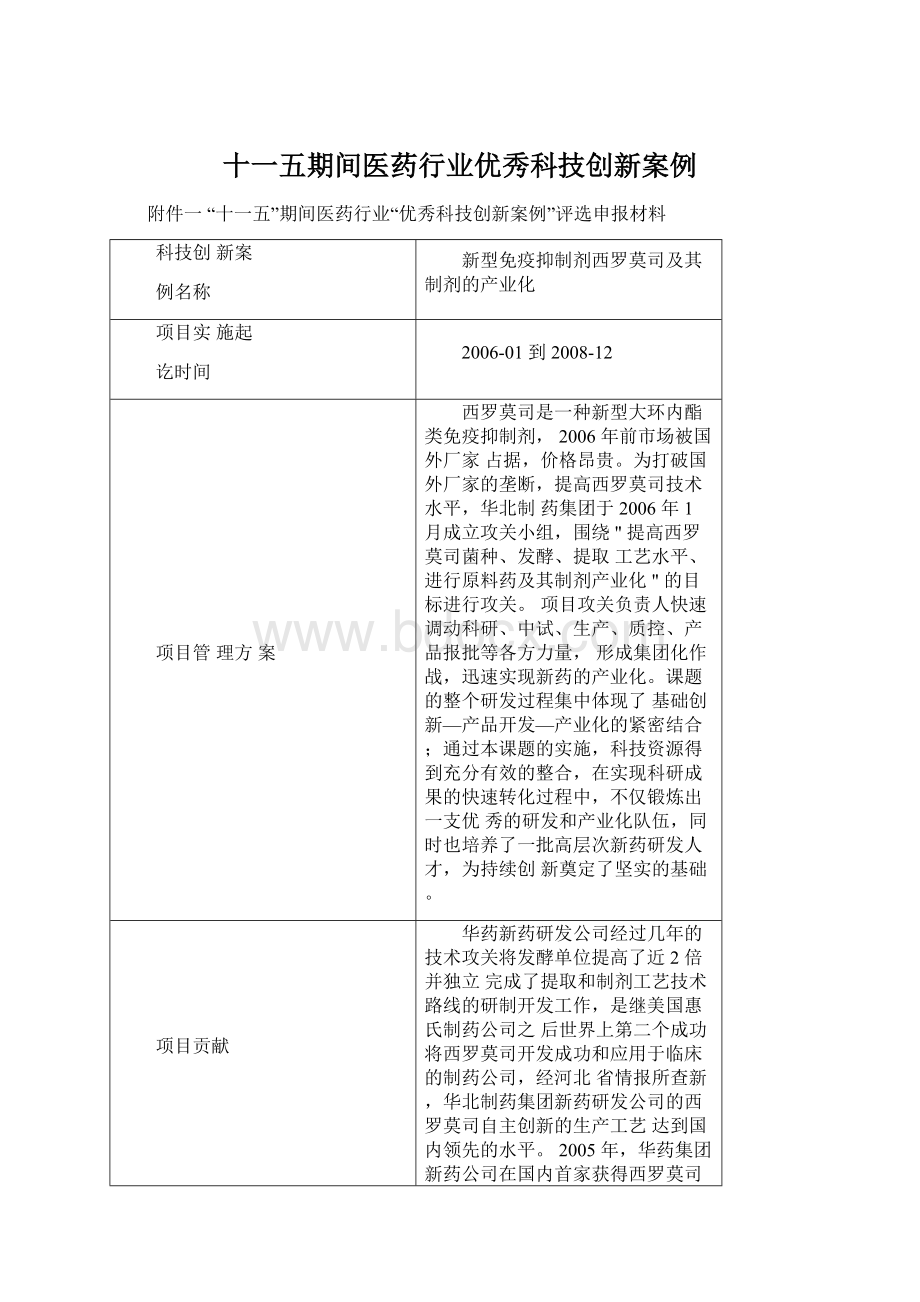
通过本课题的实施,科技资源得到充分有效的整合,在实现科研成果的快速转化过程中,不仅锻炼出一支优秀的研发和产业化队伍,同时也培养了一批高层次新药研发人才,为持续创新奠定了坚实的基础。
项目贡献
华药新药研发公司经过几年的技术攻关将发酵单位提高了近2倍并独立完成了提取和制剂工艺技术路线的研制开发工作,是继美国惠氏制药公司之后世界上第二个成功将西罗莫司开发成功和应用于临床的制药公司,经河北省情报所查新,华北制药集团新药研发公司的西罗莫司自主创新的生产工艺达到国内领先的水平。
2005年,华药集团新药公司在国内首家获得西罗莫司及其制剂的新药证书及生产批文,填补了国内空白。
该项目完全自主创新,具有全部自主知识产权。
项目经济与社会效益
我公司西罗莫司上市仅三年多,国内市场份额已占据10%,销售收入逐
年提高。
我公司在西罗莫司原料药、制剂的生产方面,已经形成了一定的生产成本竞争优势并实现了出口,随着我公司生产技术水平的不断进步,竞争优势将会更加明显。
完善了我公司的免疫抑制剂的品种线,提高了我公司在该领域的竞争实力。
随着工艺水平提高、生产成本的降低,口服剂市场价格也随之降低,减轻了患者的用药负担,受到了医院和患者的一致好评。
临床证实该产品是一种强有效的新型免疫抑制剂,可以更有效地预防术后急性排斥反应的发生和有利于术后移植肾功能的恢复。
是否存在知识产权纠纷风险
否
企业推荐意见
同意推荐
华北制药集团有限责任公司
“十一五”期间医药行业“优秀科技创新案例”评选申报材料
一、单位基本情况介绍
华北制药集团有限责任公司(以下简称:
华北制药)是目前中国最大的化学制药企业之一,是最大的抗生素和半合成抗生素基地。
其前身华北制药厂1953年筹建,1958年建成投产,结束了我国青霉素、链霉素依赖进口的局面,开创了我国大规模生产抗生素的历史,并支援了全国数十家制药企业建设。
目前,华北制药拥有子分公司四十多家,现有抗生素原料药(中间体)、维生素及营养保健品、生物农兽药、现代生物技术药物和制剂五大系列600多个品种,其中青霉素、硫酸链霉素、阿莫西林、7-ADCA、头孢拉定、维生素C、维生素B12等品种的产销量居世界前列。
集团拥有资产总额100亿元。
2009年6月,经省委、省政府批准,冀中能源集团重组华北制药。
未来几年,华北制药将以科学发展观为统领,继续秉承“人类健康至上,质量永远第一”的企业宗旨,按照“统筹整合、力主创新、优化升级、做精做强”的发展战略,努力实施“三步走”,实现“一二三”(第一步,到2011年销售收入达到100亿元;
第二步,到2013年销售收入达到200亿元;
第三步,到2015年销售收入达到300亿元)目标,把华北制药建设成为“创新领先、集约高效、开放共赢、和谐富裕”的新华药,建设成为紧密型、高效能、可持续的国内领先世界一流的现代制药集团。
二、科技创新及其创新团队工作
华北制药历来重视科技创新工作,坚持创新促发展的理念。
集团公司总经理张千兵,副总经理王永维作为创新团队的领军人物,在科研创新中不断开拓,锐意进取,主持并完成了多项国家、省级重大科研课题,取得了优异成绩。
华北制药有近4000人的专业技术人员队伍,有中高级工程技术职称的接近2000人,研发人员接近500人,其中多人被评为国家级和省级优秀专家和有突出贡献的中青年专家。
集团公司领导运用其出色的组织领导能力和协调管理能力组建了研发中心创新团队,团队有博士、硕士60余人、高级技术人员50余人。
团队的平均年龄35岁,知识结构合理,创新意识强、学术气氛活跃,技术实力雄厚,在团队的带领下,充分发挥人财物的优势,合理配臵资源,通过在团队内部建立自由学术交流平台,使每一个成员产生了更多的新观点和新理念,获得更大的创新动力,充分发挥了团队的整体合力和团队优势。
经过团队多年的努力,已建成了成熟具有自主知识产权的核心技术的研发平台,建成与完善了自主创新体系。
1.技术平台建设
(1)天然药物筛选技术平台该平台形成了微生物菌种资源采集、发酵、活性化合物筛选、活性化合物分离纯化、结构解析等一系列核心技术,为我省目前唯一达到国内领先和国际先进水平的微生物来源的完整的新药筛选研究和新产品开发技术创新体系。
承接了科技部十五重大专项《国家药物微生物菌种资源标准化整理、整合及共享试点》和“国家药物筛选平台”,共计构建了40余个高通量筛选模型,包括抗真菌、抗代谢、抗癌、抗炎、降胆固醇、免疫调节等,年筛选量达到20万样次以上,所保存的药用微生物菌种的数量居国内制造企业之最;
所分离的微生物来源的活性化合物中,80多个为世界首次发现的全新结构的有药用活性的化合物;
定向筛选得到了多个具有产业化价值的菌种,部分已实现产业化,获得显著的经济效益。
(2)利用现代生物技术改造传统产业技术平台
承担完成了国家“十一五”科技攻关项目“青霉功能基因组研究”和863“高产量、低氧耗产黄青霉基因工程菌的构建、筛选及工业生产”,利用基因组学、基因芯片、生物信息学等手段,对青霉素、吗替麦考酚酸、环孢素等品种生物合成相关的代谢网络及其调控机制进行分析,克隆一批与产量、品质密切相关的关键基因,获得一批具有自主知识产权的发明专利,为菌种理性筛选模型构建及生产菌种的基因工程改造提供依据。
(3)微生物药物发酵和提取中试及产业化技术平台与上述平台相配合,将科研成果迅速产业化,承担的国家高技术产业化项目免疫抑制剂药物产业化项目在2006年河北省发展和改革委员会组织的全省申报国家高技术产业化项目的评审中,该项目获得了全省医药领域总分第一名。
(4)生物技术药物研发技术及生物技术药物中试及产业化技术平台
通过平台研发的基因重组白蛋白项目申请了国家“十五”重大专项课题,建立了大剂量公斤级蛋白的生产技术平台和质量检测平台,解决了重组蛋白克级用药产品的诸多生产关键问题,成功进行了大规
模公斤级蛋白产品的制备,该课题在菌株构建、蛋白表达和产业化等方面居国际先进水平,技术成果得到了专家的一致好评和认可。
在哺乳动物细胞高效表达的技术领域已经获得突破性进展,为蛋白药物的产业化打下了坚实的基础,公司自主研发的国内第一个全人源抗体、一类新药基因重组人抗狂犬病毒抗体注射液的获得了国家批准
进入临床,确保了华药在该领域已取得的优势地位。
(5)合成药物研发平台
通过与国外合作,进行药物合成技术方面的培训,提升了研发队伍的整体实力,无论从合成技术还是新化合物的结构设计都达到国内领先水平,目前有多个新药正在进行研发,已有一个一类新药已申报临床。
(6)药物分析研究技术平台作为其他平台工作的有力保障,药物分析研究技术平台拥有一批高级技术人员,及先进的实验仪器设备,如500M的核磁共振、液-质联用、20余台的HPLC(其中包括一部分的制备用HPLC),为新药研发提供了有效的物质保障。
2.立足于“产-学-研”,发展后劲和创新潜力强劲经几年的实践,团队掌握了创新药物开发的设计原理、思维方式、开发流程、项目管理等重要开发理念,建成与完善了自主创新体系,取得了丰硕的成果。
承担并完成了多个国家科技部、发改委的技术创新项目,技术水平居国内领先和国际先进,均得到验收专家的好评。
近年来共完成包括化学药物、生物技术药物和保健品在内的重大新产品科研项目几十项并进行了产业化生产;
特别是在免疫抑制剂产品研发方面,在国内首家拿到西罗莫司(二类新药)的生产批件,后续品种的开发使公司成为世界上唯一一家掌握全部微生物来源免疫抑制剂药物研发及生产核心技术的公司,打破了国外公司的技术垄断,大幅度降低我国患者的用药成本。
随着新产品的不断投放市场产生的新的经济增长点,公司的销售收入也逐年攀升,同时也产生了良好的社会效益,为省会的经济社会发展做出了贡献。
另外,研发中心团队利用自身成熟的平台技术为省内院校、制药企业提供技术服务,在解决他们的实际问题时,也树立了公司良好的形象。
团队从多方面入手不断提高手成员科研水平,使团队的骨干始终站在本领域的前沿,使团队保持着持续旺盛的创造力。
团队与国内外20多家研究院所进行了广泛的合作,先后与北京大学、中科院等联合培养博士硕士多名。
团队的骨干被多所大学聘为兼职教授,每年都招收硕士研究生和博士后科研人员进站工作,为团队补充新的活力。
通过多方位、多层次、开放式的科研体系的建立,为团队在新药研究开发领域开展国际竞争奠定了坚实的基础。
新药开发正在从以“仿”为主向以“创”为主转变。
由于团队的出色的创新能力,2004年被国家发改委授予”微生物药物国家工程研究中心”,2008年,在发改委组织的工程中心评估中,综合评价位居国内医药企业之首。
同时也成为河北省和全国医药行业中唯一2006、2007年连续两年获得“自主创新能力全国总分第
一名”的单位。
三、所获国家称号及荣誉
通过团队的努力也使企业得到了国家相关领导部门的认可,华北制药的研发中心被授予:
国家首批6家技术创新试点企业、中国制药企业首批国家级企业技术中心、国家高技术产业化示范工程、微生物药物国家工程研究中心、国家863高技术产业化基地、中国青年科技创新行动示范基地、国家级高新技术企业、国家科技部创新型企业、河北省“五一劳动奖状”、河北省明星企业等称号,综合技术创新能力居国内医药行业领先水平。
由于在国际合作中的出色业绩,2009年8月获得国家科技部“微生物和生物技术创新药物研发国际科技合作基地”称号。
迄今为止,集团公司共获得5项国家发明奖。
“七五”、“八五”期间华药承担并组织了多项国家级重大科技攻关项目,与华东理工大学、清华大学、天津大学、中国科学院等进行联合攻关,取得了大量科技成果,其中获得国家科技进步二等奖5项,三等奖13项。
省部级以上奖项110多项。
多年来,我们申报多项国家重大科技项目,其中14项列入科技部国家“863”和“973”项目计划、26项列入国家经贸委技术创新项目计划、25项列入国家发展改革委高技术产业化项目、重大专项及科技部重大新药创制、科技支撑项目计划等。
华北制药在创新的同时,注重知识产权的保护,将创新的成果申请专利。
迄今为止,华北制药共申请专利180余项,授权专利60余项。
集团公司在连续两年全国知识产权示范创建的基础上,2010年又被国家知识产权局列为第二批全国知识产权示范创建单位。
四、优秀创新案例情况
1、新型免疫抑制剂西罗莫司及其制剂的产业化项目
集团公司十一五期间承担的国家高技术产业化项目新型免疫抑制剂西罗莫司及其制剂的产业化项目在2006年河北省发展和改革委员会组织的全省申报国家高技术产业化项目的评审中,该项目获得了全省医药领域总分第一名。
西罗莫司上市仅三年多,国内市场份额已占据10%,销售收入逐年提高。
我公司在西罗莫司原料药、制剂的生产方面,已经形成了一定的生产成本竞争优势并实现了出口,随着我公司生产技术水平的不断进步,竞争优势将会更加明显。
目前国内西罗莫司用量逐年提高,但2006年前市场被国外厂家所占据,价格昂贵,为打破国外厂家的垄断,提高西罗莫司技术水平,进行原料药及其制剂产业化为目标,公司于06年1月成立攻关小组,围绕"
提高西罗莫司菌种、发酵、提取工艺水平、进行原料药及其制剂产业化"
项目攻关负责人可快速调动科研、中试、生产、质控、产品报批等各方力量,形成集团化作战,迅速实现新药的产业化。
我公司是国内第一家,世界范围内第二家取得西罗莫司原料药生产批件的企业。
经河北省情报所查新,公司的西罗莫司自主创新的生产工艺达到国内领先的水平。
我公司生产的西罗莫司在产品质量上具有明显优势。
原料药内控质量标准高于国外同类产品,制剂内控质量标准高于国外同类产品。
在市场上,我公司产品价格优势明显。
在成本上,我们目前的生产成本只有销售价的几分之一,产品质量好于国内外的同类产品。
本产品完全可替代进口产品。
其销售网络遍布全国各地及欧美市场。
仰仗我公司已有的免疫抑制剂完善的销售网络,我们的优质、低价产品必将迅速占领市场,与国外同类产品抗衡,市场占有率将得到保证。
实现年销售额1200万元以上、利润330万元和20%以上的市场占有率是可以预计的。
经河北省科学技术情报研究院(国家一级科技查新咨询单位)查新,本课题进行的雷帕霉素原料及制剂研发过程中,具有:
1、在发酵过程中添加外源芳香族氨基酸,摇瓶发酵水平达到500μg/ml。
2、原粉含量达99%,制备收率达40%。
3、口服液采用自乳化技术。
以上特点,在国内外文献中未见报道,工艺达到国际先进水平。
此产品完善了我公司的免疫抑制剂的品种线,提高了我公司在该领域的竞争实力。
随着工艺水平提高、生产成本的降低,口服剂市场价格也随之降低,减轻了患者的用药负担,受到了医院和患者的一致好评。
临床证实该产品是一种强有效的新型免疫抑制剂,可以更有效地预防术后急性排斥反应的发生和有利于术后移植肾功能的恢复。
2、年处理150万吨维生素C废水超低排放关键技术开发项目本项目是我公司和南京大学与南京大学、河北科技大学、华北制药集团环保研究所共同申请的国家高技术研究发展计划(863计划)重点项目“工业含糖废水超低排放技术”中的一个子项目,项目研究内容基于维生素C废水水质特点,重点开展深度处理工业化技术研发及集成创新,解决难降解污染物与色度共生等制约维生素C废水超低排放的关键技术难题,研究开发集成降解COD、脱色、脱氮功能的维生素C废水超低排放成套技术,开发出年处理150万吨维生素C废水超低排放成套技术,在年产7500吨以上的维生素C生产线上建成高标准水质回用工业化示范装臵并完成运行考核。
本项目主要研究内容包括:
1、废水处理设施生物强化技术低温稳定控制技术开发:
研究碳源结构分布规律对废水中COD降解、脱氮效果的影响,研究低温条件下(<
15℃)生物硝化与反硝化行为,开发基于废水处理设施稳定降碳、脱氮、脱色季节性控制技术开发;
2、
维生素C废水经过二级生化处理后尾水脱色技术开发:
利用现代分析手段解析废水中发色物质的结构特征,筛选并开发出以脱色为核心的废水脱色处理反应器;
3、以水回用为目标的废水超低排放关键技术研究与开发:
研究以间歇式曝气生物颗粒床为核心、结合电催化氧化预处理和膜分离后处理技术的组合工艺集成效果与适应性,获得满足包括生活杂用水、工业用水水质等多用途回用水质标准的成套技术。
目前本课题进展顺利,现已完成了中期考核目标,主要工业化研发内容如下:
满足超低排放和低标准回用水质工程化示范研究:
为了适应行业和河北省的废水超低排放的要求,首先对河北维尔康制药有限公司原有污水处理工程进行了技术升级改造,将部分活性污泥池改造成新型生物膜反应池,于2009年12月8000吨/日维生素C废水处理工程改造完毕,实现了提标排放,解决了企业因废水排放标准大幅度的提标高压控制下的超低排放的提标要求。
2)高标准水回用集成技术工业化示范研究:
运用各种现代分析手段,建立了维生素C废水中发色物质的特征解析方法,并根据发色物质特征,开发了经过生化处理后尾水脱色技术和高标准回用技术,出水满足回用水质要求,并在河北维尔康制药有限公司开展工业化示范研究,已建成(50000吨/年)高标准水质回用工业化示范装臵,经过调试已进入稳定运行阶段。
工业化示范装臵的工艺流程:
来自维生素C废水处理装臵二沉池出水用泵提升进入前臵过滤器去除废水中的悬浮杂质,出水分别进入催化氧化反应塔与电解催化氧化反应器,将废水中难以生物降解的有机大分子链打开,以有利于下一步生化装臵的深度处理。
电解催化氧化、催化氧化装臵出水分别自流进入中间水箱1、中间水箱2,用泵提升进入至生物强化高效流动床一体化反应器、内循环曝气生物滤池,进行深度处理试验比较;
出水各自流入中间水箱3、中间水箱4后用泵提升后进入活性炭过滤器、保安过滤器进行两级过滤处理,出水分别进入超滤—反渗透装臵、电吸附脱盐装臵,进行脱盐工艺对比试验,出水进入生物监测池后排放或回用。
过滤反冲洗水、一体化反应器的排泥装臵、曝气生物滤池反冲洗出水、脱盐装臵浓水及反冲洗水均流入现装臵的排水管道外排。
流程中:
“高级催化氧化+生物强化处理”的出水70%经过臭氧消毒后可满足《生活杂用水水质标准》用于绿化用水;
剩余30%进入
双膜脱盐装臵,纳滤产水率为70%,其产水的50%可用于工业用水,50%作为反渗透进水;
反渗透产水率为60%,高混后可满足循环冷却水水质要求,因此本套工业化装臵的水回用能力为87%(4.35万吨/
年)。
本课题已实现了三项重大技术突破1)维生素C废水经过生化处理后尾水脱色技术,采用凝胶过滤色谱、超滤、傅里叶红外光谱和紫外光谱对维生素C废水厌氧、好氧出水中的发色化合物进行了特征解析,并据此开发了高效的高级催化氧化脱色技术。
2)废水处理设施的生物强化技术,开发了新型上流式一体化生物强化反应器和高效节能内循环曝气生物滤塔(HPES生物滤塔),反应器集成降解COD、脱色、脱氮的功能。
3)以水回用为目标的废水超低排放关键技术,开发了“高级催化氧化+生物强化处理+双膜脱盐”维生素C废水提标排放和分质回用技术,实现高标准水质回用。
截至目前课题进展顺利,工业化示范装臵运行稳定,正在开展工业化示范装臵运行稳定稳定运行和控制效果研究,考察工程影响因素,进一步完善工业化示范装臵等工作。
中国是世界维生素C生产大国,2007年全国维生素C的年产量约在10万吨以上,按《发酵类制药工业水污染物排放标准》(GB21903-2008)规定的指标,年取水量约3000万吨以上,年排水量达2700万吨。
根据国家发改委发布的《产业结构调整指导目录(2007年本)》中,维生素C原料药已被划入限制发展类项。
到目前为止世界范围内主要平均取水定额300吨/吨产品(维生素C),最先进水平取水定额为150吨/吨产品(维生素C)。
本项课题实施后,其成果可望达到国际先进水平,并填补国内空白,其预期主要技术经济指标如下:
(1)开发出年处理150万吨的维生素C废水超低排放关键技术,可实现年减排COD240吨以上;
(2)建成(50000吨/年)高标准水质回用工业化示范装臵,水回用能力不低于80%,示范装臵正常运行半年以上,可实现吨维生素C产品的综合废水排放量不大于40吨,吨维生素C的COD直接排放量不大于3.2公斤;
(3)直接处理费用:
吨产品的废水处理成本不高于708元。
课题完成后,如按20-30%的比例在维生素C生产企业进行推广,其废水排放减少量可达到约500万吨/年,节约用水420万吨/年,将产生巨大的社会和经济效益。
公司课题的整个研发过程集中体现了基础创新—产品开发—产业化的紧密结合,通过课题的实施,科技资源得到充分有效的整合,在实现科研成果的快速转化过程中,不仅锻炼出一支优秀的研发和产业化队伍,同时也培养了一批高层次研发人才,为持续创新奠定了坚实的基础。